复合承载式浅水自安装风电基础及其制造、下水和安装方法与流程



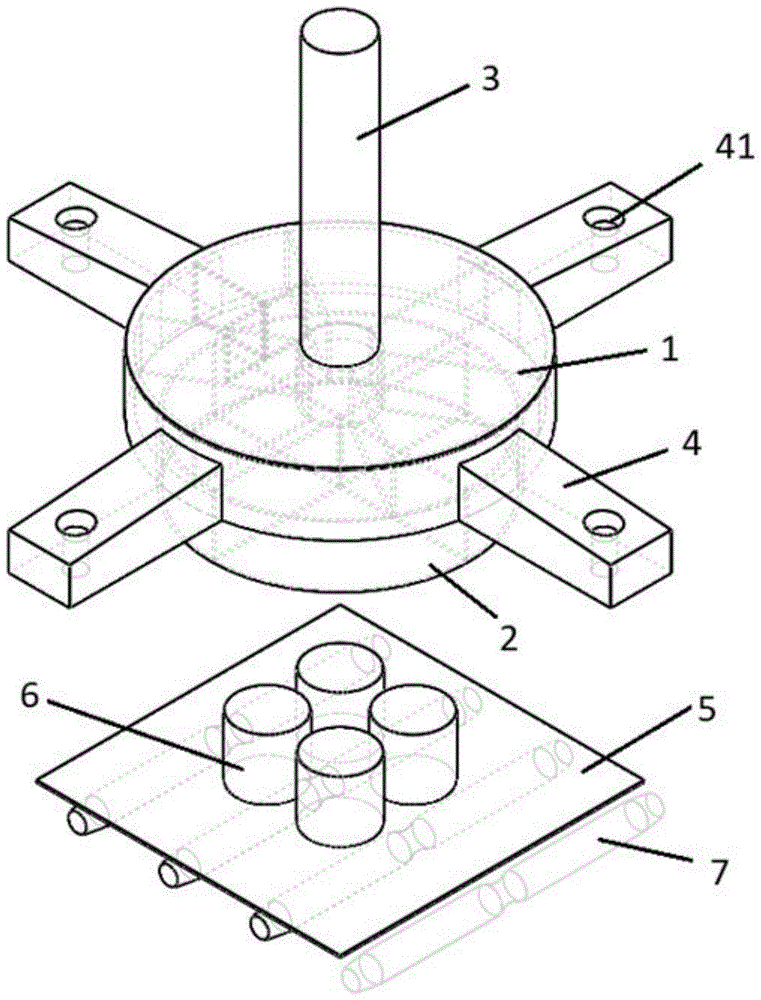
本发明涉及一种海上风电基础及其制造、下水和安装方法,尤其涉及一种浅海可实现自安装的风电基础及其制造、下水和安装方法,属于海上风电领域。
背景技术:
在许多海上风电项目中,无论是基于浮式基础还是固定式基础,其安装费用已接近总包费用的30%,这里面包括打桩船、大型浮吊等专用船舶的租金,并且海上打桩施工周期长,对于窗口期短的海域来说,更加增加了施工的不确定性。
针对海上风电项目中风电基础在安装时需要耗费巨额安装费的情况,需要设计一种不需要依托打桩船、大型浮吊等专用船舶海上风电基础才能有效降低安装费用。
技术实现要素:
本方案所要解决的技术问题是设计一种海上风电基础,该风电基础不需要依托打桩船及大型浮吊等专用船舶既可实现在浅海范围内安装。
为了解决上述技术问题,本方案的复合承载式浅水自安装风电基础,包括盘型底座,所述盘型底座下底面设置有柱形吸力桩和通海口,所述盘型底座上顶面设置有柱体段和注气口,还包括通气管,所述通气管的下端口设置在吸力桩内,所述通气管的上端口设置在柱体段上端,所述盘型底座、柱型吸力桩和柱体段均在同一轴线上。所述盘型底座是一个粗短的柱体结构,可以采用圆柱体结构,也可以采用正六边形或正八边形等多边形柱体结构,也可以采用花边型柱体结构。
上述方案中,所述盘型底座侧边均匀设置有3至8个支脚。支脚之间的间隔相等,设置3个支脚时,相邻两个支脚间间隔120°;4个支脚时,相邻两个支脚间间隔90°;6个支脚时,相邻两个支脚间间隔60°;8个支脚时,相邻两个支脚间间隔45°,以此类推,支脚之间等分角度固定在盘型底座的侧面上。支脚用于辅助盘型底座抵御风电基础上部风电设施带来的倾覆力矩。
上述方案中,所述盘型底座内部沿中轴面分隔成6至12个扇形隔离间,所述扇形隔离间的上顶面均设置有注气口,所述扇形隔离间的下底面均设置有通海口。盘型底座可以作为压载舱使用。通海口平时封住,在安装时打开,供海水进入扇形隔离间,对应的注气口用于向扇形隔离间注入压缩空气。
上述方案中,所述柱体段插入至盘型底座内底面,柱体段的下端设置在盘型底座内可以增加结构强度。
上述方案中,所述盘型底座直径不小于25米且高度与直径比小于1:3;所述吸力桩直径不超过20米。盘型底座必须要有足够的直径才可以抵御风电基础上部风电设施带来的倾覆力矩。
上述方案中,所述吸力桩内部沿中轴面分隔成4至8个相等的扇型柱体,每个扇型柱体内均独立设置有通气管。吸力桩主要功能之一为承受风电基础以及上部风机的重量,功能之二为贡献部分抗倾覆力矩。吸力桩内部设置扇型柱体以便安装时,调节内部负压。
上述方案中,所述支脚为长方形盒体结构,增大基础的倾覆力臂。所述支脚的下底面与盘型底座下底面在同一水平面上。
上述方案中,所述扇形隔离间之间采用水密结构,从而不同的扇形隔离间之间海水是无法通过的。所述扇形隔离间内纵向分隔至少两个隔离块,所述隔离块之间采用非水密结构,海水可以在一个扇形隔离间内自由流动,隔离块的上顶面上设置有排水孔和注入孔。其中注入孔用于注入铁矿砂压载,排水孔用于注入铁矿砂时,将隔离块内的海水排出。
上述方案中,所述支脚上还设置有通孔,所述通孔设置在支脚外侧端,所述通孔上部为喇叭口。支脚一侧短面焊接在盘型底座侧面,对应另一侧短面附近设置通孔,供固定桩打入,圆孔上部做成喇叭口,以便固定桩导入。固定桩可采用组合式吸力桩。组合式吸力桩也是采用抽真空使吸力桩打入海底。
复合承载式浅水自安装风电基础的制造方法,包含如下步骤:
(a)先建造一个胎架,所述胎架由平面钢板和支柱组成,所述支柱垂直设置在平面钢板上,平面钢板上表面还设置有龙骨。平面钢板下表面光滑减少摩擦力,上表面上布置龙骨以保证强度,上表面支柱的数量和吸力桩内分隔的扇形柱体数量一致且位置相匹配,以便支柱插入吸力桩内。
(b)将胎架放置于支墩上。支墩将平面钢板顶起,平面钢板下方有镂空间隔。
(c)在平整场地上反向建造盘型底座,完成盘型底座内部结构以及侧壁支脚的建造。
(d)此时反向建造完毕的盘型底座的下底面朝上,在盘型底座的下底面上完成吸力桩的建造,确保吸力桩和盘型底座在同一轴线上。
(e)将建造完成的盘型底座、支脚和吸力桩起吊翻转并放置在胎架上,使支柱插入吸力桩。
(f)在盘型底座的上顶面上完成细长柱体段的建造,至此风电基础主体建造完成。
复合承载式浅水自安装风电基础的下水方法,在风电基础建造完成后,还包含如下步骤:
(g)将胎架通过结构件点焊在风电基础主体上。
(h)在胎架下,支墩之间放置气囊,气囊打气,顶起胎架,撤走支墩。
(i)在滑坡上布置打完气的气囊,胎架及风电基础主体通过气囊滑入水中并浮起。
(j)回收气囊,并在胎架上绑上数个气囊,烧断胎架与风电基础主体之间连接的结构件,胎架下沉至一定深度后停止,打捞上岸,待下次利用。
(k)至此风电基础主体下水完毕并拖至码头处。
复合承载式浅水自安装风电基础的安装方法,包含如下步骤:
(a)在码头对风电基础主体布置气囊,风电基础主体的整个盘型底座的正上方布置满气囊,将气囊充气并捆绑在柱体段上,在柱体段顶部舾装风机塔体、机舱及叶片;完成舾装后的风电基础主体、风机和气囊,湿拖至现场海域安装;
(b)将辅助船舶上的压缩空气管口连接至盘型底座中每个扇形隔离间的注气孔口;
(c)打开盘型底座中每个扇形隔离间的通海口,通过调整每个扇形隔离间内部的压载水来调整风电基础主体及风机下沉时的姿态;
(d)风电基础主体下沉时,气囊保持在水面,辅助风电基础主体及风电的下沉;
(e)当吸力桩接触至海床,利用通气管调节吸力桩中每个扇形柱体中的负压,从而可以调节吸力桩插入时整体基础与风机的姿态,保证竖直向下;
(f)当吸力桩安装到位后,通过注入孔向扇形隔离间内的隔离块内注入铁矿砂;
(g)铁矿砂注入完成后,将支脚安装固定桩,自此安装完毕。
上述方法中,所述盘型底座内部沿中轴面分隔成6至12个扇形隔离间,所述扇形隔离间的上顶面均设置有注气口,所述扇形隔离间的下底面均设置有通海口;所述扇形隔离间之间采用水密结构,所述扇形隔离间内纵向分隔至少两个隔离块,所述隔离块之间采用非水密结构,隔离块的上顶面上设置有排水孔和注入孔。
上述方法中,所述吸力桩内部沿中轴面分隔成4至8个相等的扇型柱体,每个扇型柱体内均独立设置有通气管,所述通气管的下端口设置在扇型柱体内,所述通气管的上端口设置在柱体段上端,所述扇型主体的数量及位置与胎架的柱体数量及位置相匹配。
上述方法中,所述盘型底座侧边均匀设置有3至8个支脚,所述支脚上还设置有通孔,所述通孔设置在支脚外侧端,所述通孔上部为喇叭口。
本方案的复合承载式浅水自安装风电基础,可以解决海上风电项目中风电基础安装需要巨额安装费等不利条件,提出的一种可以实现自安装的海上风电基础形式,该风电基础形式有着如下几个优点:首先,复合承载式浅水自安装风电基础,由于不含压载时本身质量不大,所以支持在简易场地建造,不需要船坞、轨道及船台,只需建造现场与开放式水域有滑坡衔接即可,也不要求场地强度,泥质场地也可。建造时置于胎架上,下水时通过气囊辅助下水即可;其次,复合承载式浅水自安装风电基础,支持码头舾装,舾装时可以基于气囊辅助增大干舷,现场完成风机塔桶、机舱及叶片的安装;再次,舾装完毕的复合承载式浅水自安装风电基础,可以满足湿拖要求,仅需普通拖轮就能完成运输;最后,复合承载式浅水自安装风电基础支持现场自安装,无需大型辅助船舶,只需普通的海洋工程辅助船即可,极大的减少了运输与安装费用。
附图说明
图1为复合承载式浅水自安装风电基础、胎架及气囊组合结构图。
图2为风电基础中圆盘型底座内部结构及支脚结构图。
图3为吸力桩内部结构图。
图4为风电基础中圆盘型底座及支脚固定状态结构图。
图5为复合承载式浅水自安装风电基础利用胎架及气囊运输至海中过程示意图。
图6为复合承载式浅水自安装风电基础利用胎架及气囊在海中运输过程示意图。
图7为复合承载式浅水自安装风电基础在海中利用气囊辅助自安装过程示意图,方向从左至右。
上述图示中对圆盘型底座上通海口、注气口、注入孔和排水孔进行了省略,对连接吸力桩内部的通气管进行了省略;通海口、注气口、注入孔和排水孔使圆盘型底座与外部能够导通,通气管使吸力桩内部与外部能够导通,在结构上都很简单,故不进行详细标注。
具体实施方式
参见图1至4,一种复合承载式浅水自安装风电基础实施方式,包括圆盘型底座1,所述圆盘型底座下底面垂直焊接有吸力桩2,吸力桩2下端为敞口,所述圆盘型底座1上顶面垂直焊接有细长的柱体段3,所述柱体段3插入至圆盘型底座内并焊接在圆盘型底座内底面,以便增加柱体段3和圆盘型底座1之间连接强度。柱体段的直径略大于风机底座。所述圆盘型底座1、吸力桩2和柱体段3采用同轴设置。所述圆盘型底座的侧边焊接有4个支脚4,相邻支脚4之间间隔90度。所述支脚4为长方形盒体结构,靠圆盘型底座侧较外侧略厚,所述支脚的下底面水平且与圆盘型底座下底面在同一水平面上。所述支脚4外侧上还设置有通孔41,通孔41轴向和圆盘型底座1轴向平行,所述通孔41上部为喇叭口,便于固定桩42插入通孔41。
所述圆盘型底座1内部沿中轴面分隔成6个扇形隔离间11,所述扇形隔离间11之间采用水密结构,确保相邻的扇形隔离间11之间水不相互流通,每个扇形隔离间11内纵向分隔成4个隔离块111,所述隔离块111之间采用非水密结构,确保相邻的隔离块111之间水能相互流通。每个扇形隔离间的上顶面和下底面均分别设置有注气口和通海口。每个隔离块的上顶面上设置有排水孔和注入孔。也就是说注气口、排水孔和注入孔均设置在圆盘型底座上顶面上并对应相应的区域,通海口设置在圆盘型底座下底面上并对应相应的区域。
所述吸力桩2内部沿中轴面分隔成4个相等的扇型柱体21,每个扇型柱体21内均独立设置有通气管。所述通气管的下端口设置在吸力桩2顶部,所述通气管穿过圆盘型底座1和柱体段3并穿出柱体段的上顶面。这种结构的风电基础适合水深介于20米至50米的海域。
参见图5至7,复合承载浅水自安装风电基础的制造、运输及安装方法。
第一步,在简易场地建造一个胎架,胎架可重复利用。胎架由一个平面钢板5和数个支柱6组成,平面钢板5下表面光滑,上表面上布置龙骨以保证强度,上表面上垂直焊接固定有数个支柱6,支柱6将来用于穿过风电基础的吸力桩2,支撑在风电基础的圆盘型底座的下表面上。
第二步,在简易场地上建造风电基础的底座部分,注意这时候采用反向建造法,即圆盘型底座1、支脚4与吸力桩2是反向建造的,即将来面朝上的圆盘型底座的上表面在这次建造中处于最下端,而吸力桩的开口则处于最上端,这样建造是为了不破坏吸力桩2。在圆盘型底座1内建有主结构件将圆盘型底座1划分成六至十二个扇形区域,在每个扇形区域里,还建有次结构件将该扇形区域分为数个二级区域。主结构件是水密的,从而不同的扇形区域之间海水是无法通过的,次结构件是非水密的,这样海水可以在一个扇形区域内自由流动。在每个扇形区域中,都建有一对通海口和注气口,通海口位于圆盘型底座的下表面,在本步骤中,因为反向建造其位于上方表面,通气口位于圆盘型底座的上表面,在本步骤中,因为反向建造其位于下方表面,在每个二级区域,建有一对注入孔和排水孔,其位于圆盘型底座的上表面,在本步骤中,因为反向建造其位于下方表面。
第三步,在建造完圆盘型底座1后,建造支脚4。支脚4为长方形盒体,用途为增大风电基础的倾覆力臂。支脚4个数为三个或四个,三个支脚就以120°的等分布置在圆盘型底座的圆柱状侧面上,四个支脚就以90°的等分布置在圆盘型底座的圆柱状侧面上。支脚的底部与圆盘型底座下表面处于同一平面上,支脚的一端焊接在圆盘型底座侧面,对应另一端附近设置有通孔41,供固定桩42打入,通孔41上部做成喇叭口,以便固定桩42导入。注意这个步骤时是反向建造的。
第四步,为建造吸力桩2,吸力桩2上表面是圆盘型底座的下表面,注意这个步骤时是反向建造的,此时圆盘型底座的下表面还位于上方,吸力桩2被分隔成四至八个扇形,每个扇形都有一个通气管至细长圆柱型柱体段的上端,注意此时还未建造细长圆柱型柱体段,要预留接口。
第五步,为翻转建造完毕的圆盘型底座1、支脚4与吸力桩2。首先在场地上布置支墩,然后将胎架吊放在支墩上,平面钢板5置于支墩上,支柱6朝上。然后起吊建造完毕的圆盘型底座1、支脚4与吸力桩2,翻转180°,将胎架的支柱6穿入吸力桩2,支撑在风电基础的圆盘型底座的下表面上。
第六步,为建造细长圆柱型柱体段3,注意细长圆柱型柱体段3上有通气管,与吸力桩2预留的通气管相连。
第七步,为下水,基于气囊7下水。首先使用临时固定结构件将胎架与圆盘型底座1和支脚4点焊在一起。然后在平面钢板5下,支墩之间放置气囊7,给气囊7打气,顶起胎架,撤走支墩。同时在滑坡8上布置打完气的气囊7,胎架及风电基础在气囊上滑入水中9并浮起。
第八步,为回收胎架。首先回收气囊7,然后在胎架上绑上数个气囊7,烧断胎架与圆盘型底座1和支脚4的临时固定结构件,胎架下沉,鉴于胎架上绑着气囊7,其下沉至一定深度后停止,打捞上岸,待下次利用。
第九步,为码头舾装。将风电基础拖至码头系泊好,此时直接安装风机塔桶等设备稳性不够,需要借助气囊7辅助。将下水气囊7充气并捆绑在细长圆柱型柱体段3上,整个圆盘型底座的正上方都必须布置满气囊7,这样相当于增加了基础的干舷,能够满足稳性需求,并完成风机塔桶、机舱与叶片的安装。
第十步,为湿拖。保持第九步捆绑的气囊7,将舾装好的风电基础与风机湿拖至指定海域。
第十一步,为自安装。首先将辅助船舶上的压缩空气管口连接至每个扇形区域的注气孔口,然后打开每个扇形区域的通海口,通过调整每个扇形区域内部的压载水来调整风电基础及风机下沉时的姿态,当风电基础下沉时,气囊7保持在水面,可以辅助风电基础及风电的下沉,当吸力桩2接触至海床91,通过通气管可以调节吸力桩2中每个扇形中的负压,从而可以调节吸力桩插入时风电基础与风机10的姿态,保证竖直向下,当吸力桩2安装到位后,向每个二级区域内注入压载的铁矿砂,注入完成后,再安装固定桩42,自此安装完毕。
起点商标作为专业知识产权交易平台,可以帮助大家解决很多问题,如果大家想要了解更多知产交易信息请点击 【在线咨询】或添加微信 【19522093243】与客服一对一沟通,为大家解决相关问题。
此文章来源于网络,如有侵权,请联系删除


