一种异型筏板扇形网片式钢筋绑扎施工方法与流程



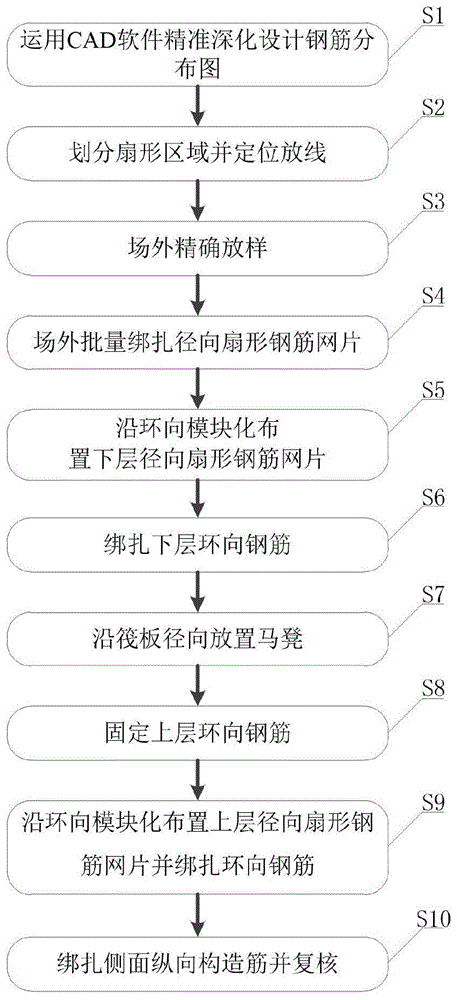
本发明属于特种设备基础施工技术领域,具体涉及一种异型筏板扇形网片式钢筋绑扎施工方法。
背景技术:
随着国防工程建设的日趋完善,各类大型设备不断涌现,异型的设备筏板基础越来越多,传统的钢筋绑扎施工方法存在钢筋长度型号繁多、下料分料费时、施工周期长、耗费大量的时间和人工成本,难以满足快速抢建国防工程施工任务的要求。因此,如何高效、经济地完成异型筏板钢筋绑扎工作,成为有待解决的问题。
技术实现要素:
(一)要解决的技术问题
本发明提出一种异型筏板扇形网片式钢筋绑扎施工方法,以解决如何保证异型筏板钢筋绑扎效率和质量的技术问题。
(二)技术方案
为了解决上述技术问题,本发明提出一种异型筏板扇形网片式钢筋绑扎施工方法,该绑扎施工方法包括如下步骤:
s1、运用cad软件深化设计钢筋分布图;
s2、将环形筏板划分为多片扇形区域并定位放线;
s3、根据确定的扇形分区、钢筋分布及间距,进行场外精确放样;
s4、场外批量绑扎径向扇形钢筋网片;
s5、沿环向模块化布置下层径向扇形钢筋网片;
s6、由外环至内环绑扎下层环向钢筋,完成筏板下层钢筋绑扎;
s7、根据扇形分区位置,在单个扇形分区内沿环形筏板径向布置马凳以支撑上层钢筋;
s8、由外环至内环将上层环向钢筋固定于马凳上;
s9、沿环向模块化布置上层径向扇形钢筋网片并绑扎环向钢筋;
s10、绑扎侧面纵向构造筋并复核。
进一步地,步骤s2包括:将环形筏板上、下层径向钢筋沿环向分别等分为多份,形成多片径向扇形钢筋网片,单片扇形分区包括外环混凝土边界、内环混凝土边界以及两侧的扇形钢筋分区边界。
进一步地,步骤s2中,采用两种不同净长的钢筋沿环向间隔分布;其中,多根大净长钢筋沿环向分布,两端分别至外环钢筋边界和内环钢筋边界;多根小净长钢筋沿环向分布,外侧至外环钢筋边界,内侧置于两根大净长钢筋中间。
进一步地,步骤s2中,扇形钢筋网片的钢筋间距不超过100mm,双层双向拉通;下料时钢筋长度最大偏差为10mm。
进一步地,步骤s3包括:在进行步骤s2的同时进行钢筋下料、分料、放样及扇形钢筋网片绑扎;首先根据确定的扇形分区画出内弧、外弧;其次根据钢筋数量及间距进行均分画出每根钢筋的位置;然后在每根钢筋的两端钉上钉子做好标记,确保每根钢筋位置准确无误,放样精确。
进一步地,步骤s4包括:根据场外精确放样的结果进行场外批量绑扎径向扇形钢筋网片。根据钢筋分布图分别布置相应型号钢筋,并使用临时固定钢筋进行固定,逐片完成单片扇形钢筋网片的绑扎。
进一步地,步骤s5包括:扇形钢筋网片绑扎完成后进行模块化钢筋绑扎,根据定位放线的结果,在环形筏板区域内均匀布置同等标号的混凝土保护层垫块,确保能够支撑起径向扇形钢筋网片;然后利用塔吊将固定好的径向扇形钢筋网片逐片吊起放入下层相应的扇形分区内,调整角度确保位置准确,完成下层径向扇形钢筋网片的模块化布置。
进一步地,步骤s9包括:利用塔吊将径向扇形钢筋网片逐片吊起放入上层相应的扇形分区内,调整角度确保位置准确;然后将环向钢筋与径向扇形钢筋网片绑扎一起,完成筏板上层钢筋绑扎。
进一步地,步骤s10包括:先将上下层径向钢筋弯拐逐根搭接并绑牢,最后绑扎侧面构造纵筋并复核钢筋绑扎的质量情况。
(三)有益效果
本发明提出一种异型筏板扇形网片式钢筋绑扎施工方法,包括运用cad软件深化设计钢筋分布图,划分扇形区域并定位放线,场外精确放样,场外批量绑扎径向扇形钢筋网片,沿环向模块化布置下层径向扇形钢筋网片,绑扎下层环向钢筋,沿筏板径向布置马凳,固定上层环向钢筋,沿环向模块化布置上层径向扇形钢筋网片并绑扎上层环向钢筋,绑扎侧面纵向构造筋并复核。本发明将模块化、装配式的思想运用到钢筋绑扎施工过程中,能够解决异型筏板钢筋绑扎难的问题,保证异型筏板钢筋绑扎的效率和质量,缩短施工周期,减少人工和时间成本,为解决异型筏板钢筋绑扎难的问题提供新的解决思路。
附图说明
图1为本发明实施例异型筏板扇形网片式钢筋绑扎施工方法的流程图;
图2为本发明实施例异型筏板上下层钢筋分布深化设计图;
图3为本发明实施例异型筏板钢筋扇形分区图;
图4为本发明实施例径向扇形钢筋网片的钢筋分布图。
图中,a-单片扇形分区,31-外环混凝土边界,32-扇形钢筋分区边界,33-内环混凝土边界,41-外环钢筋边界,42-内环钢筋边界,43-净长4m(不含弯拐)钢筋,44-净长5.5m(不含弯拐)钢筋,45-扇形网片临时固定钢筋,46-最大钢筋间距,47-最小钢筋间距。
具体实施方式
为使本发明的目的、内容和优点更加清楚,下面结合附图和实施例,对本发明的具体实施方式作进一步详细描述。
本实施例提出一种异型筏板扇形网片式钢筋绑扎施工方法,该异型筏板为环形筏板,筏板内弧半径2550mm,外弧半径8150mm。设计要求:混凝土保护层厚度50mm,混凝土强度等级为c40高抗硫混凝土,配筋为φ14mm的hrb400带肋钢筋,钢筋间距100mm,双层双向拉通;侧面构造纵筋为3根φ16mm的hrb400带肋钢筋,钢筋间距200mm。
如图1所示,扇形网片式钢筋绑扎施工方法具体包括如下步骤:
s1、运用cad软件深化设计钢筋分布图
运用cad软件深化设计钢筋分布图,如图2所示,保证钢筋间距、长度准确无误,符合环形筏板的设计要求。
s2、划分扇形区域并定位放线
根据深化设计的钢筋分布图,同时考虑现场施工条件,将环形筏板上、下层径向钢筋沿环向分别等分为20份,共计40片径向扇形钢筋网片,每层钢筋分区如图3所示。单片扇形分区a包括外环混凝土边界31、内环混凝土边界33以及两侧的扇形钢筋分区边界32。
根据划分的扇形区域,使用全站仪进行精确定位放线,以提高后续钢筋网片模块化拼装质量。
扇形钢筋网片的钢筋间距根据设计要求不超过100mm,双层双向拉通。根据设计钢筋间距要求,同时为了减少钢筋搭接、方便下料分料,采用净长5.5m(不含弯拐)钢筋44和净长4m(不含弯拐)钢筋43沿环向间隔分布,下料时钢筋长度最大偏差为10mm。单块扇形钢筋网片中钢筋分布如图4所示,径向方向共计26根钢筋,其中14根净长5.5m(不含弯拐)钢筋44沿环向分布,两端分别至外环钢筋边界41和内环钢筋边界42;12根净长4m(不含弯拐)钢筋43沿环向分布,外侧至外环钢筋边界41,内侧置于两根钢筋44中间,钢筋最大间距46为97.8mm,最小间距47为51.5mm,符合设计要求,钢筋余料用作临时固定钢筋45,减少钢筋废料。
s3、场外精确放样
根据上述确定的扇形分区、钢筋分布及间距,进行场外精确放样,具体包含以下步骤:充分考虑现场工序交叉,在进行步骤s2的同时进行钢筋下料、分料、放样及扇形钢筋网片绑扎。首先根据确定的扇形分区画出内弧、外弧;其次根据钢筋数量及间距进行均分画出每根钢筋的位置;然后在每根钢筋的两端钉上钉子做好标记,确保每根钢筋位置准确无误,放样精确。
s4、场外批量绑扎径向扇形钢筋网片
根据场外精确放样的结果进行场外批量绑扎径向扇形钢筋网片。根据钢筋分布图分别布置相应型号钢筋,并使用临时固定钢筋45进行固定,逐片完成单片扇形钢筋网片的绑扎。
在进行模块化钢筋绑扎前,完成40片扇形钢筋网片绑扎待用,减少施工时间、提高施工效率、降低人工成本。
s5、沿环向模块化布置下层径向扇形钢筋网片
扇形钢筋网片绑扎完成后进行模块化钢筋绑扎,根据定位放线的结果,在环形筏板区域内均匀布置同等标号的50mm厚混凝土保护层垫块,确保能够支撑起径向扇形钢筋网片;然后利用塔吊将固定好的径向扇形钢筋网片逐片吊起放入下层相应的扇形分区内,调整角度确保位置准确,完成下层径向扇形钢筋网片的模块化布置。
s6、绑扎环向钢筋
根据设计要求,按100mm间距由外环至内环绑扎下层环向钢筋,搭接长度不少于600mm,完成筏板下层钢筋绑扎,并布置侧面构造纵筋待用。
s7、沿环形筏板径向布置马凳
根据扇形分区位置,在单个扇形分区内沿径向布置不少于两排马凳以支撑上层钢筋,马凳间距不宜过大以保证上层钢筋平直不弯曲。
s8、固定上层环向钢筋
根据设计要求,按100mm间距由外环至内环将上层环向钢筋固定于马凳上,搭接长度不少于600mm。
s9、沿环向模块化布置上层径向扇形钢筋网片并绑扎环向钢筋
利用塔吊将径向扇形钢筋网片逐片吊起放入上层相应的扇形分区内,调整角度确保位置准确;然后将环向钢筋与径向扇形钢筋网片绑扎一起,完成筏板上层钢筋绑扎。
s10、绑扎侧面纵向构造筋并复核
根据设计要求,先将上下层径向钢筋弯拐逐根搭接并绑牢,最后绑扎侧面构造纵筋并复核钢筋绑扎的质量情况。
以上所述仅是本发明的优选实施方式,应当指出,对于本技术领域的普通技术人员来说,在不脱离本发明技术原理的前提下,还可以做出若干改进和变形,这些改进和变形也应视为本发明的保护范围。
起点商标作为专业知识产权交易平台,可以帮助大家解决很多问题,如果大家想要了解更多知产交易信息请点击 【在线咨询】或添加微信 【19522093243】与客服一对一沟通,为大家解决相关问题。
此文章来源于网络,如有侵权,请联系删除


