一种钢管桩静轴向承载力检测装置及检测方法与流程



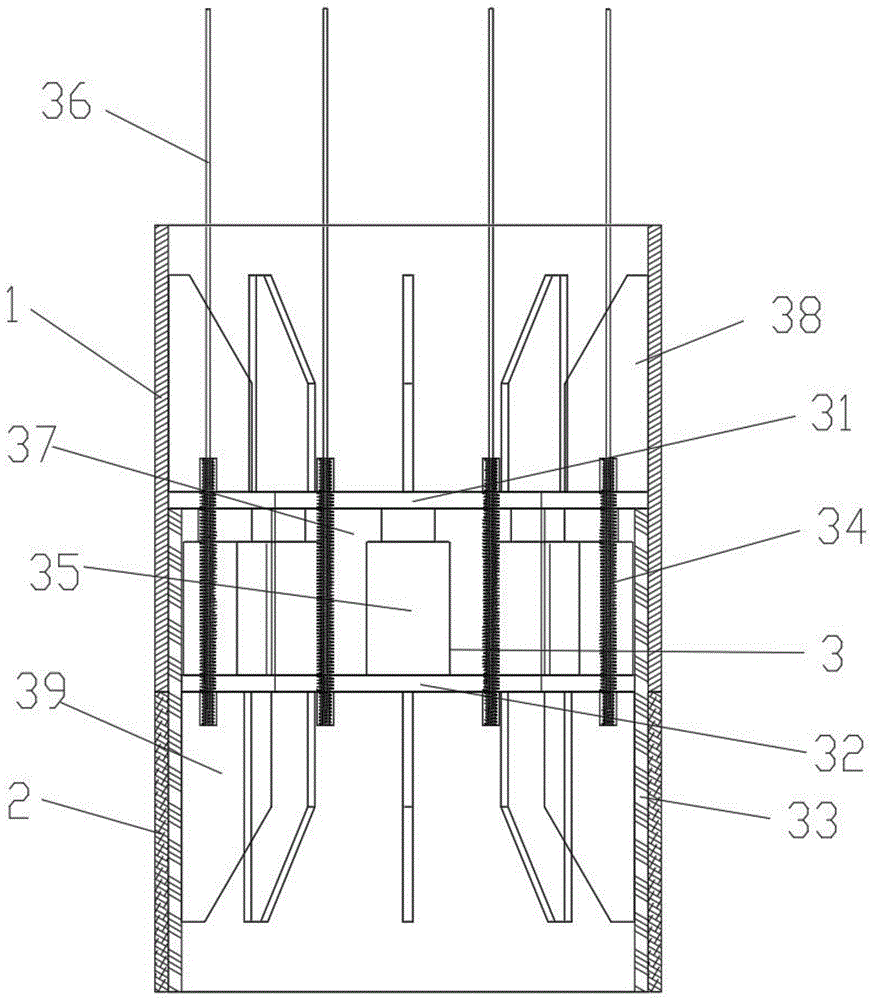
本发明属于检测技术领域,尤其涉及一种钢管桩静轴向承载力检测装置及检测方法。
背景技术:
传统的桩基荷载试验方法大多是采用堆载法或锚桩法,但对较高检测荷载的单桩静载试桩,所需反力较大,传统试桩方法存在施工时间长、操作难度大、试验费用高、安全风险大等缺点。相比传统试桩方法,自平衡试验方法可以应用于超大吨位桩基,以及特殊环境下不具备堆载和锚桩条件的桩基承载力试验,且省时、经济,是一种很有发展前途的桩基测试技术。自平衡试验方法是把一种特制的加载装置荷载箱放置在桩身指定位置,通过地面油泵及连通油泵和荷载箱的高压油管对荷载箱加压,荷载箱顶板和底板分离即迫使荷载箱上、下桩段发生相应位移,同时记录荷载箱荷载、顶板和底板位移、桩顶位移以及桩身应力等获得荷载-位移规律。目前,自平衡试验方法多数用于灌注桩,用于预制桩如钢管桩、phc桩的案例相对较少,钢管桩自平衡试验按荷载箱的安装方法可分为两类:第1类钢管桩自平衡试验荷载箱与上下段钢管桩焊接成整体,然后打入土层中;第2类钢管桩自平衡试验首先在上下段钢管桩之间焊接专用荷载箱安装接头,钢管桩打入土层中后,将钢管桩中的土芯清空至荷载箱安装位置以下一定深度,然后安装荷载箱。
进行第1类试验方法时,荷载箱的埋设方式都是将桩身分成上、下两部分再焊接荷载箱,为保证荷载箱顶板和底板在试验过程中能顺利分离,打桩过程中,顶板和底板之间的连接较弱,这严重影响了桩身抗弯、剪、及拉压性能,打桩过程中,较高的桩身动应力可能导致荷载箱段钢管桩接头错位、折断、拉断,致使无法进行载荷试验,若增强了荷载箱顶板和底板的连接,但又使得在进行自平衡试验时需要很大的推力将连接的顶板和底板顶开才能进行试验,无论是否能顺利顶开荷载箱顶板和底板的连接,对试验的开展和测试数据的准确性均会造成不利影响。同时在试验结束后,埋设在钢管桩内部的位移测杆为一次性消耗品,不能进行回收后重复利用,导致检测费用高。
技术实现要素:
本发明的目的在于一种钢管桩静轴向承载力检测装置及检测方法,可有效地抵抗沉桩时桩身的弯矩、剪切力、压力和拉力,顶板和底板牢固连接并容易分开,可回收并重复利用位移测杆,检测数据准确可靠。
本发明是通过以下技术方案实现的:
一种钢管桩静轴向承载力检测装置,包括上钢管节、下钢管节和可控制变形荷载箱体,上钢管节和下钢管节的规格相同;
可控制变形荷载箱体包括顶板、底板和外护筒,顶板和底板均为环形结构,顶板固定在上钢管节内,底板固定在外护筒内,外护筒的外壁下部固定在下钢管节内;
顶板上设有多个第一螺纹通孔,底板上设有与多个第一螺纹通孔对应的第二螺纹通孔,第一螺纹通孔与对应的第二螺纹通孔之间通过锁紧螺杆连接,使得上钢管节的下端与下钢管节的上端抵接,且外护筒的上端与顶板抵接;
顶板和底板之间设有若干千斤顶,若干千斤顶等间距设置,且若干千斤顶的下端与底板固定连接,上端与顶板抵接;
锁紧螺杆的上端可拆卸连接有位移测杆。
进一步地,可控制变形荷载箱体还包括内护筒,内护筒、顶板和底板三者的内径相同,内护筒设置在顶板和底板之间,且其下端固定在底板上,其上端与顶板抵接。
进一步地,顶板的外径与上钢管节的内径相同,其顶面设有若干上支撑肋板,上支撑肋板其中的两条边分别固定在上钢管节和顶板上;底板的外径与外护筒的内径相同,其底面设有若干下支撑肋板,下支撑肋板其中的两条边分别固定在外护筒和底板上。
进一步地,第一螺纹通孔的数量为六,六个第一螺纹通孔两两为一组,同一组的两个第一螺纹通孔对称布设在顶板上。
进一步地,锁紧螺杆的两端均可与位移测杆可拆卸连接。
进一步地,锁紧螺杆与位移测杆之间通过螺纹连接。
进一步地,位移测杆包括多节杆体,多节杆体依次螺纹连接。
进一步地,位移测杆的外侧套设有保护套管。
进一步地,千斤顶为油压千斤顶,顶板上开设有供千斤顶的油管穿过的油管通孔。
一种如上述任一项的钢管桩静轴向承载力检测装置的检测方法,检测方法包括如下步骤:
将组装好的钢管桩静轴向承载力检测装置安装在待检测钢管桩上,并将待检测钢管桩打入预设的深度;
将多个锁紧螺杆划分成三组,分别为第一组锁紧螺杆、第二组锁紧螺杆和第三组锁紧螺杆,将第一组锁紧螺杆向下旋转至与顶板和底板脱离,并下放至待检测钢管桩底部,将第二组锁紧螺杆向上旋转至其下部与底板脱离,将第三组锁紧螺杆向下旋转至其上部与顶板脱离;
在待检测钢管桩满足休止时间后,对待检测钢管桩进行承载力检测,记录各位移测杆的位移数据;
对记录的各位移测杆的位移数据进行分析,确定待检测钢管桩的承载力。
相比于现有技术,本发明的有益效果为:将可控制变形荷载箱体的顶板和底板分别固定在上钢管节和外护筒内,外护筒的外壁下部固定在下钢管节内,形成承插结构,有效地抵抗沉桩时桩身的弯矩、剪切力和压力,可有效避免打桩过程中桩身折断、错位,保护可控制变形荷载箱体;可控制变形荷载箱体的顶板和底板之间通过多根锁紧螺杆连接固定,可根据打桩需要设计抗拉能力,使得顶板和底板连接牢固,有效地抵抗沉桩时桩身的拉力,在需要对顶板和底板分开时,只需要通过位移测杆旋转相应的锁紧螺杆,使得锁紧螺杆脱离顶板或底板即可,顶板和底板分离方便;位移测杆与锁紧螺杆之间为可拆卸连接,在检测结束后,位移测杆均可回收重复利用,降低检测费用。
附图说明
图1为本发明钢管桩静轴向承载力检测装置的结构透视图;
图2为本发明钢管桩静轴向承载力检测装置中可控制变形荷载箱体的内部示意图;
图3为本发明钢管桩静轴向承载力检测装置的俯视图;
图4为本发明钢管桩静轴向承载力检测装置的仰视图。
图中,1-上钢管节,2-下钢管节,3-可控制变形荷载箱体,31-顶板,32-底板,33-外护筒,34-锁紧螺杆,35-千斤顶,36-位移测杆,37-内护筒,38-上支撑肋板,39-下支撑肋板。
具体实施方式
下面结合附图和实施例对本发明作进一步说明。
请参阅图1至图4,图1为本发明钢管桩静轴向承载力检测装置的结构透视图,图2为本发明钢管桩静轴向承载力检测装置中可控制变形荷载箱体的内部示意图,图3为本发明钢管桩静轴向承载力检测装置的俯视图,图4为本发明钢管桩静轴向承载力检测装置的仰视图。一种钢管桩静轴向承载力检测装置,包括上钢管节1、下钢管节2和可控制变形荷载箱体3,上钢管节1和下钢管节2的规格相同;可控制变形荷载箱体3包括顶板31、底板32和外护筒33,顶板31和底板32均为环形结构,顶板31固定在上钢管节1内,底板32固定在外护筒33内,外护筒33的外壁下部固定在下钢管节2内;顶板31上设有多个第一螺纹通孔,底板32上设有与多个第一螺纹通孔对应的第二螺纹通孔,第一螺纹通孔与对应的第二螺纹通孔之间通过锁紧螺杆34连接,使得上钢管节1的下端与下钢管节2的上端抵接,且外护筒33的上端与顶板31抵接;顶板31和底板32之间设有若干千斤顶35,若干千斤顶35等间距设置,且若干千斤顶35的下端与底板32固定连接,上端与顶板31抵接;锁紧螺杆34的上端可拆卸连接有位移测杆36。
上钢管节1和下钢管节2的规格相同,即上钢管节1和下钢管节2的具有大小相同的内径和外径。可控制变形荷载箱体3的顶板31固定在上钢管节1内,底板32通过外护筒33固定在下钢管节2上,底板32的底面与下钢管节2的上端平齐,外护筒33的外径与下钢管节2的内径相同。而本发明钢管桩静轴向承载力检测装置进行检测试验时,通过上钢管节1和下钢管节2与待检测钢管桩的桩身对接焊接在桩身的指定位置,指定位置由检测人员经过计算得出。该设置通过上钢管节1和下钢管节2加大了可控制变形荷载箱体3与桩身的接触面积和结合强度,同时可控制变形荷载箱体3通过外护筒33加大了与下钢管节2的接触面积和结合强度,有效地抵抗沉桩时桩身的弯矩、剪切力和压力,可有效避免打桩过程中桩身折断、错位,保护可控制变形荷载箱体3。并且上钢管节1和下钢管节2直接焊接在桩身上,安装简单便捷。在一实施例中,顶板31的外径与上钢管节1的内径相同,其顶面设有若干上支撑肋板38,上支撑肋板38其中的两条边分别固定在上钢管节1和顶板31上;底板32的外径与外护筒33的内径相同,其底面设有若干下支撑肋板39,下支撑肋板39其中的两条边分别固定在外护筒33和底板32上。在顶板31与上钢管节1之间设置若干上支撑肋板38,在底板32和外护筒33之间设置若干下支撑肋板39,进一步的加大顶板31与上钢管节1的结合强度,以及加大底板32与外护筒33的结合强度,从而进一步加大了可控制变形荷载箱体3与桩身的结合强度。优选地,若干上支撑肋板38等间距设置在顶板31的顶面,若干下支撑肋板39等间距设置在底板32的底面。在一实施例中,上支撑肋板38包括第一矩形段和第一直角梯形段,第一矩形段的下端固定在顶板31的顶面上,其上端与第一直角梯形段的下底连接,第一直角梯形的直角腰与上钢管节1焊接。下支撑肋板39包括第二矩形段和第二直角梯形段,第二矩形段的上端固定在底板32的底面上,其下端与第二直角梯形段的下底连接,第二直角梯形段的直角腰与外护筒33焊接。
锁紧螺杆34的数量与第一螺纹通孔的数量相同且一一对应,第二螺纹通孔与第一螺纹通孔的数量相同且一一对应,在需要连接顶板31和底板32时,将顶板31放置在外护筒33上,并使得第一螺纹通孔位于对应的第二螺纹通孔的正上方,上钢管节1的下端放置在下钢管节2的上端,通过锁紧螺杆34依次旋入相应的第一螺纹通孔和相应的第二螺纹通孔,使得顶板31和底板32牢固连接在一起,此时上钢管节1的下端与下钢管节2的上端抵接,外护筒33的上端与顶板31抵接。通过多根锁紧螺杆34连接顶板31和底板32,可根据打桩需要设计抗拉能力,有效地抵抗沉桩时桩身的拉力,避免打桩过程中因桩身拉应力较大而破坏可控制变形荷载箱体3。而在需要将顶板31和底板32分开进行自平衡试验时,只需要将各锁紧螺杆34旋出顶板31或底板32即可,顶板31和底板32分离方便快捷。在一实施例中,可控制变形荷载箱体3还包括内护筒37,内护筒37、顶板31和底板32三者的内径相同,内护筒37设置在顶板31和底板32之间,且其下端固定在底板32上,其上端与顶板31抵接。内护筒37的内径边缘与顶板31的内径边缘和底板32的内径边缘平齐,从而在可控制表型荷载箱体的中间形成一个贯通孔,并且顶板31、底板32、外护筒33和内护筒37之间形成一个容纳腔,若干千斤顶35设置在容纳腔内。避免在打桩过程中,泥土对千斤顶35造成影响,导致千斤顶35损坏不能进行自平衡试验。在一实施例中,千斤顶35为油压千斤顶35,顶板31上开设有供千斤顶35的油管穿过的油管通孔。千斤顶35的油管穿过油管通孔后与高压油泵连接。
锁紧螺杆34的上端可拆卸连接有位移测杆36,通过与锁紧螺杆34连接的位移测杆36,试验人员可通过旋转位移测杆36,带动锁紧螺杆34旋转。在一实施例中,锁紧螺杆34的两端均可与位移测杆36可拆卸连接。优选地,锁紧螺杆34与位移测杆36之间通过螺纹连接。例如,位移测杆36与锁紧螺杆34连接的一端设置有内螺纹,锁紧螺杆34与位移测杆36连接的一端设置有外螺纹,锁紧螺杆34螺接地套设在位移测杆36;当然,也可以是位移测杆36的一端设置有外螺纹,锁紧螺杆34的一端设置有内螺纹,位移测杆36螺接地套设在锁紧螺杆34。通过该种方式将锁紧螺杆34和位移测杆36充分紧固,以便工作人员通过旋转位移测杆36来带动锁紧螺杆34旋转,从而将锁紧螺杆34旋出顶板31或底板32,或将锁紧螺杆34旋出顶板31和底板32。并且根据旋转方向的不同,设置不同走向的螺纹即可。在一实施例中,位移测杆36与锁紧螺杆34连接的一端设置有外螺纹,锁紧螺杆34上端和下端均设有与位移测杆36的外螺纹螺纹配合的内螺纹,锁紧螺杆34上端的内螺纹走向与其下端的内螺纹走向相同。如锁紧螺杆34上端的内螺纹与其下端的内螺纹均为左旋螺纹,或锁紧螺杆34上端的内螺纹与其下端的内螺纹均为右旋螺纹,根据锁紧螺杆34旋转方向的不同,选择不同的端部与位移测杆36螺纹连接即可。从而锁紧螺杆34的结构均相同,可以统一生产,减少成本。
分别与多根锁紧螺杆34可拆卸连接的多根位移测杆36用于测量待检测钢管桩的桩端位移、可控制变形箱体的顶板31位移和底板32位移,即将多根锁紧螺杆34和多根位移测杆36划分为三部分。在一实施例中,第一螺纹通孔的数量为六,六个第一螺纹通孔两两为一组,同一组的两个第一螺纹通孔对称布设在顶板31上。第一螺纹通孔的数量为六,则锁紧螺杆34和第二螺纹通孔的数量也是六,六根锁紧螺杆34和第二螺纹通孔根据六个第一螺纹通孔的分组方式,同样两两为一组,同一组的两根锁紧螺杆34对称布设在顶板31和底板32上,同一组的两个第二螺纹通孔对称布设在底板32上。六根锁紧螺杆34分为三组,分别为第一组锁紧螺杆34、第二组锁紧螺杆34和第三组锁紧螺杆34,分别与第一组锁紧螺杆34的两根锁紧螺杆34连接的位移测杆36用于测量桩端位移,分别与第二组锁紧螺杆34的两根锁紧螺杆34连接的位移测杆36用于测量顶板31位移,分别与第三组锁紧螺杆34的两根锁紧螺杆34连接的位移测杆36用于测量底板32位移,在进行自平衡试验时,需要将第一组锁紧螺杆34的两根锁紧螺杆34依次旋出顶板31和底板32,并将第一组锁紧螺杆34的两根锁紧螺杆34下放至待检测钢管桩底部;将第二组锁紧螺杆34的两根锁紧螺杆34旋出底板32,同时仍然通过螺纹与顶板31连接;将第三组锁紧螺杆34的两根锁紧螺杆34旋出顶板31,同时仍然通过螺纹与底板32连接。将六根锁紧螺杆34按照上述方式操作后,此时顶板31和底板32处于分离状态,可进行自平衡试验。
在一实施例中,位移测杆36包括多节杆体,多节杆体依次螺纹连接。每一节杆体的一端设置有内螺纹,另一端设置有外螺纹,设置外螺纹一端的杆体半径小于设置内螺纹一端的杆体半径。在连接时,所述一杆体的设置内螺纹的一端螺接地套设在另一杆体设置外螺纹的一端。通过该种方案可以使位移测杆36中多节杆体均为同样的样式,降低制作工艺的难度,使任一杆体均可以螺接地套设在与其不同的另一杆体上,同时可以根据用户在进行检测试验时,根据对位移测杆36的长度需求自行设置位移测杆36的长度。在一实施例中,位移测杆36的外侧套设有保护套管。保护套管用于保护位移测杆36。
一种如上述任一项的钢管桩静轴向承载力检测装置的检测方法,检测方法包括如下步骤:
s1、将组装好的钢管桩静轴向承载力检测装置安装在待检测钢管桩上,并将待检测钢管桩打入预设的深度;
s2、将多个锁紧螺杆34划分成三组,分别为第一组锁紧螺杆34、第二组锁紧螺杆34和第三组锁紧螺杆34,将第一组锁紧螺杆34旋转至与顶板31和底板32脱离,并下放至待检测钢管桩底部,将第二组锁紧螺杆34旋转至与底板32脱离,将第三组锁紧螺杆34旋转至与顶板31脱离;
s3、在待检测钢管桩满足休止时间后,对待检测钢管桩进行承载力检测,记录各位移测杆36的位移数据;
s4、对记录的各位移测杆36的位移数据进行分析,确定待检测钢管桩的承载力。
在上述步骤s1中,先组装好钢管桩静轴向承载力检测装置,根据待检测钢管桩特性,计算出钢管桩静轴向承载力检测装置的指定安装位置,将上钢管节1和下钢管节2对接焊接在指定安装位置上,然后将所有位移测杆36接长至靠近待检测钢管桩顶部位置。采用整体吊装并通关打桩锤将待检测钢管桩打如预设的深度,将所有位移测杆36接长至高于待检测钢管桩顶部1米左右,同时将千斤顶35的油管与高压油泵连接。
在上述步骤s2中,与第一组锁紧螺杆34连接的位移测杆36为第一组位移测杆36,与第二组锁紧螺杆34连接的位移测杆36为第二组位移测杆36,与第三组锁紧螺杆34连接的位移测杆36为的第三组位移测杆36,利用工具分别旋转第一组位移测杆36,带动第一组锁紧螺杆34旋转,将第一组锁紧螺杆34旋转至与顶板31和底板32脱离,并下放至待检测钢管桩底部,即下放的距离大于预先设定的第一距离,在下放的过程中同步接长第一组位移测杆36,确保第一组位移测杆36仍然高于待检测钢管桩顶部1米左右,第一组位移测杆36用于测量待检测钢管桩桩端的位移;同样利用工具分别旋转与第二组位移测杆36,带动第二组锁紧螺杆34旋转,将第二组锁紧螺杆34旋转至与底板32脱离,即第二组位移测杆36的上升距离大于预先设定的第二距离即可,第二组位移测杆36用于测量可控制变形荷载箱体3的顶板31的位移;利用工具分别旋转与第三组位移测杆36,带动第三组锁紧螺杆34旋转,将第三组锁紧螺杆34旋转至与顶板31脱离,即第三组位移测杆36的下降距离大于预先设定的第三距离即可,第三组位移测杆36用于测量可控制变形荷载箱体3的底板32的位移。
在上述步骤s3中,在待检测钢管桩满足休止时间后,对待检测钢管桩进行承载力检测,通过千斤顶35对顶板31和底板32施加荷载,测量各位移测杆36的位移数据并记录。待检测钢管桩桩端的位移、可控制变形荷载箱体3的顶板31的位移和可控制变形荷载箱体3的底板32的位移均有两根位移测杆36进行测量,试验数据准确可靠,试验简便、安全、经济。
在上述步骤s4中,绘制荷载-位移q-s曲线,位移-时间对数s-lgt曲线以及其他需要辅助分析曲线,从而通过计算确定待检测钢管桩的承载力,根据位移数据计算待检测钢管的承载力的方法为现有的计算方法,在此不再赘述。试验结束后,用工具将位移测杆36旋转,并进行回收,可降低检测费用。
相比于现有技术,本发明的有益效果为:将可控制变形荷载箱体3的顶板31和底板32分别固定在上钢管节1和外护筒33内,外护筒33的外壁下部固定在下钢管节2内,形成承插结构,有效地抵抗沉桩时桩身的弯矩、剪切力和压力,可有效避免打桩过程中桩身折断、错位,保护可控制变形荷载箱体3;可控制变形荷载箱体3的顶板31和底板32之间通过多根锁紧螺杆34连接固定,可根据打桩需要设计抗拉能力,使得顶板31和底板32连接牢固,有效地抵抗沉桩时桩身的拉力,在需要对顶板31和底板32分开时,只需要通过位移测杆36旋转相应的锁紧螺杆34,使得锁紧螺杆34脱离顶板31或底板32即可,顶板31和底板32分离方便;位移测杆36与锁紧螺杆34之间为可拆卸连接,在检测结束后,位移测杆36均可回收重复利用,降低检测费用。
本发明并不局限于上述实施方式,如果对本发明的各种改动或变形不脱离本发明的精神和范围,倘若这些改动和变形属于本发明的权利要求和等同技术范围之内,则本发明也意图包含这些改动和变形。
起点商标作为专业知识产权交易平台,可以帮助大家解决很多问题,如果大家想要了解更多知产交易信息请点击 【在线咨询】或添加微信 【19522093243】与客服一对一沟通,为大家解决相关问题。
此文章来源于网络,如有侵权,请联系删除


