一种气动开门的径向挤压模具的制作方法



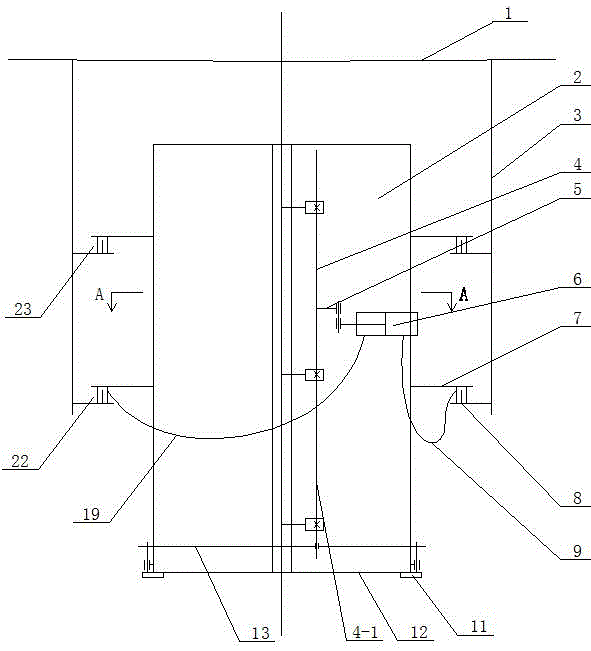
本实用新型涉及混凝土及钢筋混凝土管生产设备。
背景技术:
目前径向挤压工艺制管时的单开口模具由行车通过吊具起吊模具,吊具包括横梁和两根可以根据模具规格调整开档距离的吊杆,底托装入模具筒体后关闭模具,吊杆夹紧模具,将模具移至转台,移开吊具,转台带动模具旋转到生产工位,等钢筋混凝土管成型后转台将模具旋转到初始位置,吊具将模具运送到脱模位置后打开模具。开关模具为人工操作,如专利号为zl201721414011.x,专利名称为“一种径向挤压模具的连锁脱模装置”,这种模具不适用于自动化生产线。
技术实现要素:
本实用新型的目的是为了克服现有技术的不足,提供一种适用于自动化生产线的气动开门的径向挤压模具。
本实用新型的目的是这样实现的:一种气动开门的径向挤压模具,包括吊具和单开口的筒体,吊具包括横梁和两根吊杆,两根吊杆和筒体均竖向布置,两根吊杆分别设置在筒体外的两侧;在所述筒体的内腔底部设置底托,在筒体的底部铰接多个旋转托板,转动所述旋转托板将底托与筒体分离或固定;在所述筒体的外部连接打开筒体的脱模装置,脱模装置包括转轴,转轴的轴向与筒体的轴向一致;在所述筒体的外部连接第一气缸,第一气缸的活塞杆铰接第一连杆,第一连杆与转轴固定连接,在所述第一气缸上连接第一有杆腔气管和第一无杆腔气管;每根吊杆与筒体分别通过一组进气装置可分离式连接,两组进气装置连接气源,其中一组进气装置与第一有杆腔气管相连接,另一组进气装置与第一无杆腔气管相连接。
本实用新型的每组进气装置均包括竖向的通气套管和竖向的通气杆,两个通气套管分别连接在所述筒体的外壁上,在每个通气套管上分别设置第一气口,两个第一气口中其中一个第一气口与第一有杆腔气管连接,另外一个第一气口与第一无杆腔气管连接;所述通气杆连接在吊杆上,每根通气杆插接在对应的通气套管内,在每根通气杆上分别设置第二气口,第二气口的一端连接气源、另一端与通气套管的内腔相连通。
本实用新型是在现有单开口模具的基础上改进而成,使用第一气缸推动脱模装置。吊具将模具放置到转台上需要与模具分离,钢筋混凝土管生产成型模具转出后需要夹紧模具,因此吊具与模具上的气管必须能够自动分离与连接,无需人工干预可以将高压气体输送到模具上的第一气缸。
工作时,吊杆夹紧模具,将模具移至转台,移开吊具。转台带动模具旋转到生产工位,等钢筋混凝土管成型后转台将模具旋转到初始位置。移动吊具,由于两个通气杆的距离与筒体上的两个通气套管的距离相匹配,吊杆向下移动,通气杆对准通气套管,吊杆再向上移动,从而将通气杆插接在通气套管内,吊具上的通气杆连接高压气体,将高压气体输送至通气套管,经气管进入第一气缸的有杆腔或无杆腔,使第一气缸伸缩,从而打开或合上模具,实现自动化生产。
为了保证密封效果,在所述通气套管与通气杆之间设置密封垫,防止通气套管与通气杆之间漏气。
本实用新型在所述筒体的外壁设置两块底板,每块底板上分别设置调节孔,调节孔的长度方向与筒体的轴向一致,底板通过螺栓穿过调节孔与筒体连接;在每块底板上分别焊接套管安装座,每个通气套管分别焊接在相应的套管安装座上;在所述吊杆上焊接通气杆安装座,每个通气杆分别焊接在相应的通气杆安装座上。底板和调节孔的设计,便于保证筒体两侧的通气套管与通气杆的相对位置准确,降低制造难度。
为了进一步增强吊杆与模具连接的稳定性,每根吊杆与筒体分别通过插接装置可分离式连接,每组插接装置均包括竖向的外套管和竖向的内导杆,两个外套管分别连接在所述筒体的外壁上;所述内导杆连接在吊杆上,每根内导杆插接在对应的外套管内。
本实用新型的多个旋转托板通过第二连杆相串联,所述转轴的下端连接曲柄,曲柄与第二连杆相连接。当第一气缸带动转轴转动,同时带动曲柄转动,通过第二连杆同时将多个旋转托板旋转,旋转托板同步离开底托。
本实用新型在所述筒体的外壁还连接第二气缸,第二气缸连接第二有杆腔气管和第二无杆腔气管,第二有杆腔气管的另一端与第一有杆腔气管相连接,第二无杆腔气管的另一端与第一无杆腔气管相连接;多个旋转托板通过第三连杆相串联,第二气缸的活塞杆与其中一个旋转托板相铰接。第一气缸带动转轴转动,只打开筒体。旋转托板由第二气缸、第三连杆实现同步离开托板。
本实用新型在所述筒体的外壁还连接多个第三气缸,第三气缸的数量与旋转托板的数量相等,每个第三气缸的活塞杆与相应的旋转托板相铰接;每个第三气缸上均连接第三有杆腔气管和第三无杆腔气管,多根第三有杆腔气管的另一端均与第一有杆腔气管相连接,多根第三无杆腔气管的另一端均与第一无杆腔气管相连接。第一气缸带动转轴转动,只打开筒体。旋转托板由各自的第三气缸实现离开托板。
附图说明
图1为本实用新型的第一种结构示意图。
图2为图1中未画通气套管和通气杆的a-a向视图。
图3为图1中进气装置的结构示意图。
图4为图1中插接装置的结构示意图。
图5为本实用新型的第二种结构示意图。
图6为图5中未画通气套管和通气杆的b-b向视图。
图7为本实用新型的第三种结构示意图。
图8为图7中未画通气套管和通气杆的c-c向视图。
具体实施方式
实施例1
如图1-4所示,为第一种气动开门的径向挤压模具,包括吊具和单开口的筒体2,吊具包括横梁1和两根吊杆3,两根吊杆3可以根据模具规格调整开档距离,两根吊杆3和筒体2均竖向布置,两根吊杆3分别设置在筒体2外的两侧,筒体2由两个半圆形部分相铰接而成。
在筒体2的外部连接打开筒体2的脱模装置4,脱模装置4包括转轴4-1,转轴4-1的轴向与筒体2的轴向一致,脱模装置4和转轴4-1的结构采用专利号为zl201721414011.x中企口板启闭装置和转轴的结构。脱模装置4由第一气缸6驱动,第一气缸6的缸筒连接在筒体2的外部,第一气缸6的活塞杆铰接第一连杆5,第一连杆5与转轴4-1固定连接。
在筒体2的内腔底部设置底托12,在筒体2的底部铰接四个旋转托板11,四个旋转托板11通过第二连杆13串联,在转轴4-1的下端连接曲柄4-2,曲柄4-2与第二连杆13相连接,实现同步转动,同时转动四个旋转托板11将底托12与筒体2分离或固定。
每根吊杆3与筒体2分别通过一组进气装置22可分离式连接。每组进气装置22均包括竖向的通气套管7和竖向的通气杆8。在筒体2的外壁设置两块底板24,每块底板24上分别设置调节孔26,调节孔26的长度方向与筒体2的轴向一致,底板24通过螺栓25穿过调节孔26与筒体2连接。在每块底板24上分别焊接套管安装座14,在每个套管安装座14上分别焊接竖向的通气套管7,每个通气套管7上分别设置第一气口15,其中一个第一气口15通过第一有杆腔气管19连接第一气缸6的有杆腔,另一个第一气口15通过第一无杆腔气管9连接第一气缸6的无杆腔。在每根吊杆3上分别焊接通气杆安装座16,每个通气杆安装座16分别焊接竖向的通气杆8,两个通气杆8与两个通气套管7一一对应布置,每个通气杆8分别插置在相应的通气套管7内,在通气套管7与通气杆8之间设置密封垫18,在通气杆8上设置第二气口17,第二气口17的一端连接气源、另一端与通气套管7的内腔相连通。
每根吊杆3与筒体2分别通过插接装置23可分离式连接,每组插接装置23均包括竖向的外套管27和竖向的内导杆28,两个外套管27分别连接在筒体2的外壁上。内导杆28连接在3吊杆上,每根内导杆28分别插接在对应的外套管27内。
工作时,吊杆夹紧模具,将模具移至转台,移开吊具。转台带动模具旋转到生产工位,等钢筋混凝土管成型后转台将模具旋转到初始位置。移动吊具,由于两个通气杆的距离与筒体上的两个通气套管的距离相匹配,吊杆向下移动,通气杆对准通气套管,吊杆再向上移动,从而将通气杆插接在通气套管内,吊具上的通气杆连接高压气体,进气由可编程控制器控制,将高压气体输送至通气套管,经气管进入第一气缸的无杆腔,使第一气缸伸出,从而打开模具。转轴转动的同时带动曲柄转动,曲柄带动第二连杆同时转动四个旋转托板,将底托与筒体分离,进行脱模,实现自动化生产。模具打开时,筒体张开,带动通气套管、通气杆、外套管和内导杆小范围移动,移动范围由吊杆轻微变形来实现。
实施例2
如图5、6所示,为第二种气动开门的径向挤压模具,在筒体2的外壁还连接第二气缸10,第二气缸10连接第二有杆腔气管20和第二无杆腔气管21,第二有杆腔气管20的另一端与第一有杆腔气管19相连接,第二无杆腔气管21的另一端与第一无杆腔气管9相连接。四个旋转托板11通过第三连杆32相串联,第二气缸10的活塞杆与其中一个旋转托板11相铰接。无实施例1中的曲柄,其余结构同实施例1。
第一气缸6伸出,打开筒体2。第二气缸10伸出,由第三连杆32同时带动四个旋转托板11转动,将底托12与筒体2分离。
实施例3
如图7、8所示,为第三种气动开门的径向挤压模具,在筒体2的外壁还连接四个第三气缸29,每个第三气缸29的活塞杆与相应的旋转托板11相铰接。每个第三气缸29上均连接第三有杆腔气管30和第三无杆腔气管31,四根第三有杆腔气管30的另一端均与第一有杆腔气管19相连接,四根第三无杆腔气管31的另一端均与第一无杆腔气管9相连接。无实施例1中的曲柄和第二连杆,其余结构同实施例1。
第一气缸6伸出,打开筒体2。每个旋转托板11由各自的第三气缸29控制,将底托12与筒体2分离。
起点商标作为专业知识产权交易平台,可以帮助大家解决很多问题,如果大家想要了解更多知产交易信息请点击 【在线咨询】或添加微信 【19522093243】与客服一对一沟通,为大家解决相关问题。
此文章来源于网络,如有侵权,请联系删除


