一种涤纶面料的雕印印花工艺的制作方法



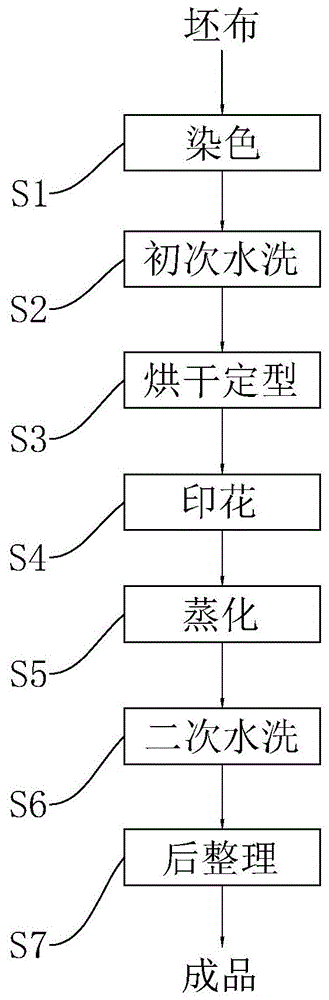
本申请涉及面料印花的领域,尤其是涉及一种涤纶面料的雕印印花工艺。
背景技术:
:涤纶面料是日常生活中用的非常多的一种化纤服装面料。其最大的优点是抗皱性和保形性很好,因此,适合做外套服装、各类箱包和帐篷等户外用品。旗帜的材质通常采用涤纶面料中的春亚纺布料,该布料具有涤纶面料的特点,面料轻薄,遇风可飘,用于旗帜的制作材料最合适不过。春亚纺布料制作的国旗颜色鲜艳,具有防水、防晒、不变形、耐高温、遇水即干的特性。特别是当旗帜悬挂在旗杆上的时候,突然遭受雨水天气,旗帜被淋湿后遇到风会自然晾干。商家根据客户实际情况的需求,会在旗帜上印有一些花型、标志、图形等。现有的印花方式则是采用直印的,但是采用直接印花,难有满意的渗透性,在被印织物的反面往往留有白色和不均匀的色彩,而且正面拉开后也会显露出白色。为了解决这一问题,涤纶织物采用雕印印花可以完全解决上述缺点。但是,旗帜通常使用在室外,亟需提供一种色牢度高的涤纶面料的雕印印花工艺。技术实现要素:为了解决涤纶面料上雕印色牢度低问题,本申请提供一种涤纶面料的雕印印花工艺。本申请提供的一种涤纶面料的雕印印花工艺,采用如下的技术方案:一种涤纶面料的雕印印花工艺,将涤纶坯布经过如下步骤进行:s1:染色;将坯布进行染色;s2:初次水洗;将经过s1处理后的坯布进行水洗;s3:烘干定型;将经过s2处理后的坯布进行烘干定型;s4:印花;将经过s3处理后的坯布进行印花,印花时所用的浆料的各化学组成以重量份计包括:氯化亚锡20-40份、助溶剂4-8份、淀粉糊100-140份、还原染料20-50份以及磺基琥珀酸二乙基己酯钠13-18份;s5:蒸化;s6:二次水洗;s7:后整理;经过s7后得到印花完成的涤纶面料。通过采用上述技术方案,进行雕印时,选择作为氯化亚锡作为雕印的还原剂,氯化亚锡属于酸性还原剂。涤纶的学名为聚酯纤维,在碱性环境易分解。因此本申请中选用酸性的还原剂,能够降低对于涤纶纤维损伤。淀粉糊的抱水性好,渗透性优良,同时能够保证涤纶面料获得清晰的轮廓。通过选择还原染料,同时由于在浆料中添加了磺基琥珀酸二乙基己酯钠,从而增大还原染料与涤纶面料之间的附着力,从而增强了印在涤纶布料上花型的色牢度。同时,由于还原染料与淀粉糊组合,能够使得浆料较为稳定。作为本申请的进一步改进,所述步骤s4印花步骤中的助溶剂为尿素。通过采用上述技术方案,通过将助溶剂选择为尿素,一方面能够起到吸湿的效果,另一方面,能够使得浆料中各个物质之间的相容性更好,起到助溶剂的作用。同时,尿素能够加速蒸化时纤维对染料的吸附和扩散作用,从而进一步的提高坯布上雕印花型的色牢度。作为本申请的进一步改进,s4中印花时所用的浆料中还包括乙醇酸钠2-5份。通过采用上述技术方案,乙醇酸钠作为释酸剂,为浆料提供弱酸性环境,防止不耐碱的染料被破坏,同时对染料具有助溶性,能加速还原染料向纤维内部扩散。作为本申请的进一步改进,s4中印花时所用的浆料中还包括海藻酸钠30-53份。通过采用上述技术方案,海藻酸钠印花时给色量高,渗透性良好,印制精细花纹轮廓清晰,块面得色均匀,并且雕印后海藻酸钠易于洗涤,印花织物手感柔软。作为本申请的进一步改进,s4中印花时所用的浆料中还包括氯酸钠7-15份。通过采用上述技术方案,通过添加氯化钠,能够防止含有硝基或偶氮基的还原染料在蒸化时被还原而变色。作为本申请的进一步改进,s4中印花时所用的浆料中还包括乙醇酸钠2-5份、海藻酸钠30-53份以及氯酸钠7-15份。作为本申请的进一步改进,所述s5蒸化,将所述s4印花后的坯布输送至所述蒸化机内进行蒸化,所述蒸化机的温度调节为170-200℃,车速调节为8-12m/min,蒸化时间为6-10min。通过采用上述技术方案,涤纶纤维在170-200℃的环境下,分子链段运动加剧,有利于还原染料在纤维内扩散,从而使得还原染料与涤纶纤维之间的分子间的作用力增强,最终使得雕印在涤纶面料上的花型固定在纤维上。作为本申请的进一步改进,所述s1染色中染料的各化学组成以重量份计包括分散染料15-25份、分散剂13-26份、匀染剂50-70份、苯酚磺酸铝3-8份、氨基乙醇硫酸酯1-5份、醋酸10-15份以及水250-300份。通过采用上述技术方案,分散染料分子结构简单,相对分子质量小,所以容易扩散进入至涤纶纤维分子之间。通过添加苯酚磺酸铝和氨基乙醇硫酸酯,能够与后续印花的浆料中的磺基琥珀酸二乙基己酯钠互相结合,从而使得雕印在染色完毕后花型与涤纶布料之间的附着力增强,最终增强了花型的色牢度。作为本申请的进一步改进,所述s1染色,先按重量份计无先后顺序的将分散染料、分散剂、匀染剂、苯酚磺酸铝、氨基乙醇硫酸酯、醋酸以及水添加至染液桶内搅拌20min以配置成染液,浴比1:20,持续搅拌50min,然后将染液输送至染色机内,接着将染色机内染液的温度升温至50℃,保温浸泡10min;然后再将染色液温度升至90℃,保温浸泡5min;然后再将染液温度升至115℃,保温浸泡30min;最后将染色机内染液的温度降至70℃,降温时间为15min,染色结束。通过采用上述技术方案,现将染液的温度升高至50℃,然后再升高至90℃,最后将温度升高至115℃。一方面能够使得分散染料上染至涤纶坯布上,使得涤纶坯布具有合格的上染率。另一方面,能够防止分散染料与涤纶纤维完全结合,方便后续进行雕印工作。综上所述,本申请包括以下至少一种有益技术效果:1、由于在浆料中添加了磺基琥珀酸二乙基己酯钠,从而增大还原染料与涤纶面料之间的附着力,从而增强了印在涤纶布料上花型的色牢度;2、通过将助溶剂选择为尿素,一方面能够起到吸湿的效果,另一方面,能够使得浆料中各个物质之间的相容性更好,起到助溶剂的作用。同时,尿素能够加速蒸化时纤维对染料的吸附和扩散作用,从而进一步的提高坯布上雕印花型的色牢度;3、乙醇酸钠作为释酸剂,为浆料提供弱酸性环境,防止不耐碱的染料被破坏,同时对染料具有助溶性,能加速还原染料向纤维内部扩散。附图说明图1为本申请一种涤纶面料的雕印印花工艺的工艺流程图。具体实施方式以下结合附图以及实施例,对本申请作进一步详细描述。实施例1:参照图1,本实施例公开了一种涤纶面料的雕印印花工艺,将涤纶坯布经过如下步骤进行:s1:染色。先将坯布输送至平幅水洗机内进行水洗,水洗持续10min。然后按重量份计无先后顺序的将分散染料20份、分散剂20份、匀染剂60份、苯酚磺酸铝5份、氨基乙醇硫酸酯3份、醋酸12份以及水275份添加至染液桶内搅拌20min,浴比1:20,持续搅拌50min。然后将染液输送至染色机内,接着将染色机内染液的温度升温至50℃,保温浸泡10min。然后再将染色液温度升至90℃,保温浸泡5min。然后再将染色液温度升至115℃,保温浸泡30min。最后将染色机内染液的温度降至70℃,降温时间为15min,染色结束。s2:初次水洗。将经过s1处理后的坯布输送至绳状水洗机内进行水洗15min。s3:烘干定型。将经过s2处理后的坯布输送至定型机内,进行烘干定型。s4:印花。先将经过s3处理后的坯布放入已经制网完成的平网印花机内,再将平网印花机的车速调节为50m/min,烘干温度调节为135℃,然后将配置好的浆料放置浆料添加处,启动平网印花机开始印花。浆料的配置过程为:先将还原染料用冷水调匀,然后加入淀粉糊搅拌均匀,再加入助溶剂和磺基琥珀酸二乙基己酯钠搅拌均匀,最后再加氯化亚锡搅拌均匀即可,助溶剂选用尿素。浆料各物质的组成配比以重量份计为:还原染料35份、助溶剂6份、淀粉糊120份、氯化亚锡30份以及磺基琥珀酸二乙基己酯钠15份。使用的平网印花机为日本东伸生产、型号为rsx-1。s5:蒸化。先将蒸化机调试正常,然后将经过s4处理后的坯布输送至蒸化机内,然后将蒸化机内的温度调节至185℃,车速调节为10m/min,持续蒸化时间为8min。使用的蒸化机为武汉中大生产、型号为yxlm1818。s6:二次水洗。将经过s5处理后的坯布输送至冲洗池内,再使用含有固色剂的固色液持续浸泡20min,然后使用清水持续冲洗10min。固色剂为三乙烯四胺,用量为1.5g/l。s7:后整理。将经过s6处理后的坯布输送只定型机内进行定型工作。定型工作时,定型机内的温度调节至190℃,定型8min;定型结束后,将坯布冷却至室温。经过s7后得到印花完成的涤纶面料。实施例2:一种涤纶面料的雕印印花工艺,将涤纶坯布经过如下步骤进行:s1:染色。先将坯布输送至平幅水洗机内进行水洗,水洗持续10min。然后按重量份计无先后顺序的将分散染料20份、分散剂20份、匀染剂60份、苯酚磺酸铝5份、氨基乙醇硫酸酯3份、醋酸12份以及水275份添加至染液桶内搅拌20min,浴比1:20,持续搅拌50min。然后将染液输送至染色机内,接着将染色机内染液的温度升温至50℃,保温浸泡10min。然后再将染色液温度升至90℃,保温浸泡5min。然后再将染色液温度升至115℃,保温浸泡30min。最后将染色机内染液的温度降至70℃,降温时间为15min,染色结束。分散剂为分散剂mf;匀染剂为烷基苯酚聚氧乙烯醚。s2:初次水洗。将经过s1处理后的坯布输送至绳状水洗机内进行水洗15min。s3:烘干定型。将经过s2处理后的坯布输送至定型机内,进行烘干定型。s4:印花。先将经过s3处理后的坯布放入已经制网完成的平网印花机内,再将平网印花机的车速调节为50m/min,烘干温度调节为135℃,然后将配置好的浆料放置浆料添加处,启动平网印花机开始印花。浆料的配置过程为:先将还原染料用冷水调匀,然后加入淀粉糊和乙醇酸钠搅拌均匀,再加入助溶剂和磺基琥珀酸二乙基己酯钠搅拌均匀,最后再加氯化亚锡搅拌均匀即可,助溶剂选用尿素。浆料各物质的组成配比以重量份计为:还原染料35份、助溶剂6份、淀粉糊120份、乙醇酸钠3份、氯化亚锡30份以及磺基琥珀酸二乙基己酯钠15份。使用的平网印花机为日本东伸生产、型号为rsx-1。s5:蒸化。先将蒸化机调试正常,然后将经过s4处理后的坯布输送至蒸化机内,然后将蒸化机内的温度调节至185℃,车速调节为10m/min,持续蒸化时间为8min。使用的蒸化机为武汉中大生产、型号为yxlm1818。s6:二次水洗。将经过s5处理后的坯布输送至冲洗池内,再使用含有固色剂的固色液持续浸泡20min,然后使用清水持续冲洗10min。固色剂为三乙烯四胺,用量为1.5g/l。s7:后整理。将经过s6处理后的坯布输送只定型机内进行定型工作。定型工作时,定型机内的温度调节至190℃,定型8min;定型结束后,将坯布冷却至室温。经过s7后得到印花完成的涤纶面料。实施例3:与实施例1的区别在于,s4:印花。先将经过s3处理后的坯布放入已经制网完成的平网印花机内,再将平网印花机的车速调节为50m/min,烘干温度调节为135℃,然后将配置好的浆料放置浆料添加处,启动平网印花机开始印花。浆料的配置过程为:先将还原染料用冷水调匀,然后加入淀粉糊和海藻酸钠搅拌均匀,再加入助溶剂和磺基琥珀酸二乙基己酯钠搅拌均匀,最后再加氯化亚锡搅拌均匀即可,助溶剂选用尿素。浆料各物质的组成配比以重量份计为:还原染料35份、助溶剂6份、淀粉糊120份、海藻酸钠42份、氯化亚锡30份以及磺基琥珀酸二乙基己酯钠15份。使用的平网印花机为日本东伸生产、型号为rsx-1。实施例4:与实施例1的区别在于,s4:印花。先将经过s3处理后的坯布放入已经制网完成的平网印花机内,再将平网印花机的车速调节为50m/min,烘干温度调节为135℃,然后将配置好的浆料放置浆料添加处,启动平网印花机开始印花。浆料的配置过程为:先将还原染料用冷水调匀,然后加入淀粉糊和氯酸钠搅拌均匀,再加入助溶剂和磺基琥珀酸二乙基己酯钠搅拌均匀,最后再加氯化亚锡搅拌均匀即可,助溶剂选用尿素。浆料各物质的组成配比以重量份计为:还原染料35份、助溶剂6份、淀粉糊120份、氯酸钠11份、氯化亚锡30份以及磺基琥珀酸二乙基己酯钠15份。使用的平网印花机为日本东伸生产、型号为rsx-1。实施例5:与实施例1的区别在于,s4:印花。先将经过s3处理后的坯布放入已经制网完成的平网印花机内,再将平网印花机的车速调节为50m/min,烘干温度调节为135℃,然后将配置好的浆料放置浆料添加处,启动平网印花机开始印花。浆料的配置过程为:先将还原染料用冷水调匀,然后加入乙醇酸钠、海藻酸钠、淀粉糊和氯酸钠搅拌均匀,再加入助溶剂和磺基琥珀酸二乙基己酯钠搅拌均匀,最后再加氯化亚锡搅拌均匀即可,助溶剂选用尿素。浆料各物质的组成配比以重量份计为:还原染料35份、助溶剂6份、淀粉糊120份、乙醇酸钠3份、海藻酸钠42份、氯酸钠11份、氯化亚锡30份以及磺基琥珀酸二乙基己酯钠15份。使用的平网印花机为日本东伸生产、型号为rsx-1。实施例6-9与实施例5的区别在于,s1染色中染料的各化学组成以重量份计如表1所示:单位:份;s4印花中浆料各物质的组成配比以重量份计如表1所示:单位:份表1实施例6-9与实施例5的区别在于,s5蒸化中蒸化的温度调节至如表2所示,单位:℃;车速调节至如表2所示:单位:m/min;蒸化时间如表2所示,单位:min表2实施例实施例6实施例7实施例8实施例9温度170200530580车速812911时间61079对比例1:与实施例1的区别在于,s4印花中的浆料中无磺基琥珀酸二乙基己酯钠。对比例2:与实施例1的区别在于,s4印花中的浆料中将还原染料替换为分散染料。性能检测:采用实施例1-9中得到的涤纶面料作为试验样品1-9,采用对比例1-2中获得的涤纶面料作为对照样品1-2。检测方法:采用下述的标准测试标准检测试验样品1-9和对照样品1-2的摩擦牢度和耐洗牢度,并且将检测数据记录至表3中。色牢度测试的方法为:耐洗牢度gb/t3921.1-1997;耐摩擦牢度(干摩、湿摩)gb3920-83;耐汗渍牢度gb/t3922-1995。表3试验样品1-9和对比样品1-2的检测结果得知,采用实施例1-9记载的技术方案得到的涤纶布料的耐洗牢度、耐摩擦牢度、耐汗渍牢度以及上染率逐级递增,因此,采用采用实施例5-9记载的技术方案能够得到雕印色牢度高的涤纶面料。以上均为本申请的较佳实施例,并非依此限制本申请的保护范围,故:凡依本申请的结构、形状、原理所做的等效变化,均应涵盖于本申请的保护范围之内。当前第1页1 2 3 
起点商标作为专业知识产权交易平台,可以帮助大家解决很多问题,如果大家想要了解更多知产交易信息请点击 【在线咨询】或添加微信 【19522093243】与客服一对一沟通,为大家解决相关问题。
此文章来源于网络,如有侵权,请联系删除



tips