一种柔性吸波织物用吸波纤维材料的制备方法与流程



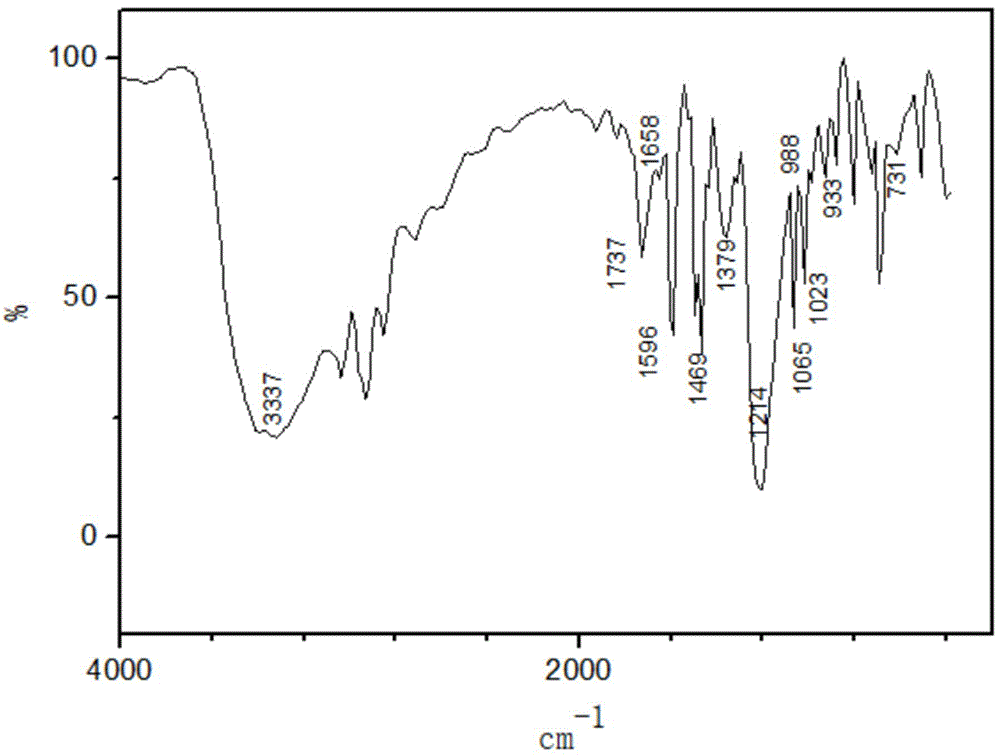
本发明涉及材料制备领域,具体关于一种柔性吸波织物用吸波纤维材料的制备方法。
背景技术:
电磁波吸波材料,即吸波材料是武器装备的重要材料之一。应为其可以大幅降低飞行器的雷达散射截面,从而提高其生存防御能力和总体作战性能,所以受到了越来越多的关注,成为各国专家研制的热点。
cn105925023a一种疏水疏油型吸波材料及其制备方法。一种疏水疏油型吸波材料,包括以下组分:具有疏水疏油性能的吸波材料粘结剂、吸波材料和助剂;按质量百分比计,具有疏水疏油性能的吸波材料粘结剂87%-93%、吸波材料6%-12%和助剂0.5%-1%。制备时,将各组分混合均匀。该发明所述的疏水疏油型吸波材料可以用于厨电产品的涂层。具有疏水性能好、易清洁、耐高温和健康环保等优点。
cn106118144a提供了一种导热型吸波材料及其制备方法。导热型吸波材料,包括以下组分:吸波材料粘结剂、吸波材料和助剂;按质量百分比计,吸波材料粘结剂为99.2%-99.7%,吸波材料为0.2%-0.5%,助剂为0.1%-0.3%;所述吸波材料为石墨烯类材料。制备时,按配比将各种组分混合到一起。该发明所述导热型吸波材料具有导热性能好、温度分布均匀和吸波性能好等优点。
cn106116426a公开了一种亲水型吸波材料及其制备方法。亲水型吸波材料包括吸波材料无机粘结剂、吸波材料和助剂;按质量百分数剂,吸波材料无机粘结剂为90%-98%,吸波材料为1%-9%,助剂为1%-1.5%;所述吸波材料无机粘结剂为亲水型无机材料。制备时,按配比将各组分混合到一起。该发明所述的亲水型吸波材料可应用于厨电产品领域,具有亲水性能好、容易清洁、消除健康隐患、耐温性能好以及涂层厚度薄等优点。
以上专利以及现有技术制备的现有的吸波材料均为硬质材料,其形状适应性、便携性差,应用领域受到明显限制。
技术实现要素:
为了解决上述问题,本发明提供了一种柔性吸波织物用吸波纤维材料的制备方法。
一种柔性吸波织物用吸波纤维材料的制备方法,制备技术方案如下:
按照质量份数,将42-68份的聚合物纤维松解、清除其中的杂质,所述的聚合物纤维包括15-22份的23g/5m的聚合物纤维,12-18份的18g/5m的聚合物纤维,其他为12g/5m的聚合物纤维;将58-76份的碳纤维条表面清理干净,所述的碳纤维包括38-46份的10g/5m碳纤维和20-30份的29g/5m的碳纤维;先将聚合物纤维合并得到混合聚合物纤维条;将混合聚合物纤维条分别与两种碳纤维进行合并,得到芳纶和碳混纺纤维;将所得到的两种芳纶和碳混纺纤维条加捻度,将其卷装成适应细纱机喂入的细度的芳纶和碳混纺纤维粗纱;芳纶和碳混纺纤维粗纱均匀拉长拉细为40-68tex的细纱,并给该细纱加上32.4-48.2捻/10cm的捻度,得到芳纶和碳混纺纤维细纱;将得到的芳纶和碳混纺纤维细纱作为工作电极进行表面电聚合包覆改性,所述的表面电聚合包覆改性在混纱表面改性液中进行,电位设定在1.5-3.6v,沉积时间200-500s,完成表面包覆改性后混砂经过清洗干燥后即可得到所述的一种柔性吸波织物用吸波纤维材料。
所述的混纱表面改性液为一种苯胺-改性吡咯单体共聚前驱溶液,采用反式-2,4-己二烯酰氯与吡咯钠盐反应得到含羰基的吡咯单体;
其中,制备含羰基的吡咯单体的反应机理示意为:
含羰基的吡咯单体与二异丙基二氢硅烷发生硅氢加成反应,得到硅烷接枝改性吡咯单体,反应机理示意为:
所述的苯胺-改性吡咯单体共聚前驱溶液,其制备方法如下:
按照质量份数,在氮气保护下,将4.3-8.7份的金属钠和10.7-20.2份的吡咯加入到400-800份的无水四氢呋喃中,控温60-80℃,搅拌反应5-10h;反应完全后,降温至室温后将300-600份四氢呋喃,12-22份的反式-2,4-己二烯酰氯,缓慢加入到反应体系中,加完后控温40-60℃下搅拌反应4-10h,然后加入1.2-3.5份的氯铂酸3-7%的异丙醇溶液,3-8份的二异丙基二氢硅烷,70-85℃下反应60-120min,即可得到所述的硅烷接枝改性吡咯单体。
硅烷接枝改性吡咯单体蒸去无水四氢呋喃,加入27.8-36.4份的磺酸基水杨酸和500-1000份的纯水中,搅拌混合均匀后加入17.4-26.3份的苯胺,控温到0-10℃,然后搅拌60-90min,然后加入12.3-18.2份的过硫酸铵,搅拌60-90min,得到苯胺-改性吡咯单体共聚前驱溶液。
所述的聚合物纤维为芳纶纤维或聚丙烯腈纤维或聚丙烯纤维。
所述的碳纤维为聚丙烯腈基碳纤维或沥青基碳纤维或酚醛基碳纤维。
所述的一种柔性吸波织物用吸波纤维材料经过纺织后即可得到柔性吸波织物。
本发明方法公开的一种柔性吸波织物用吸波纤维材料的制备方法,本方法首先用聚合物纤维和碳纤维混纺成混纱,然后用电聚合方法将一种硅烷接枝改性吡咯单体和苯胺共聚到纤维表面制备出一种苯胺-硅烷接枝改性吡咯单体共聚物包裹的纤维吸波材料,该材料来源广泛,成本低廉,而且具有良好的介电性能,所制备的织物的顶破强力为1581.2n,织物的反射率为-3.73db,本发明是一种高效吸波材料,也为工业开发多用途吸波纺织品指明了一个方向。
附图说明
图1为实施例2制备的苯胺-改性吡咯单体共聚前驱溶液的傅里叶红外光谱图:
在1214cm-1附近存在磺酸基的反对称伸缩吸收峰,在1065/1023/933cm-1附近存在磺酸基的对称伸缩吸收峰,在3337cm-1附近存在羟基的伸缩吸收峰,说明磺酸基水杨酸参与了反应;在1596/1469/1379cm-1附近存在苯环的伸缩吸收峰,说明苯胺参与了反应;在988cm-1附近存在碳氮单键的吸收峰,在1658cm-1附近存在碳碳双键的吸收峰,说明吡咯参与了反应;在1737cm-1附近存在羰基的吸收峰,说明反式-2,4-己二烯酰氯参与了反应;在731cm-1附近存在硅碳的吸收峰,说明二异丙基二氢硅烷参与了反应。
具体实施方式
下面通过具体实施例对该发明作进一步说明:
以下实施例中制备的纤维都采用缎纹纺织法纺织成经/纬密为180/120的织物,然后釆用反射传输网络参数法,按照gjb2038-1994使用弓形反射率测试系统对织物的吸波性能进行测试。实验仪器为矢量网络分析仪,是“自动矢量网络参数扫频测量系统”,其工作方式为扫频测量,测得16.5ghz频率处织物的反射率。采用yg06电子式顶破强力仪对织物进行织物的顶破实验测试,测试试样为直径为80mm的圆形织物。
实施例1
一种柔性吸波织物用吸波纤维材料的制备方法,制备技术方案如下:
将42kg聚合物纤维松解、清除其中的杂质,所述的聚合物纤维包括15kg的23g/5m的聚合物纤维,12kg的18g/5m的聚合物纤维,其他为12g/5m的聚合物纤维;将58kg碳纤维条表面清理干净,所述的碳纤维包括38kg10g/5m碳纤维和20kg的29g/5m的碳纤维;先将聚合物纤维合并得到混合聚合物纤维条;将混合聚合物纤维条分别与两种碳纤维进行合并,得到芳纶和碳混纺纤维;将所得到的两种芳纶和碳混纺纤维条加捻度,将其卷装成适应细纱机喂入的细度的芳纶和碳混纺纤维粗纱;芳纶和碳混纺纤维粗纱均匀拉长拉细为40tex的细纱,并给该细纱加上32.4捻/10cm的捻度,得到芳纶和碳混纺纤维细纱;将得到的芳纶和碳混纺纤维细纱作为工作电极进行表面电聚合包覆改性,所述的表面电聚合包覆改性在混纱表面改性液中进行,电位设定在1.5v,沉积时间200s,完成表面包覆改性后混砂经过清洗干燥后即可得到所述的一种柔性吸波织物用吸波纤维材料。
所述的混纱表面改性液为一种苯胺-改性吡咯单体共聚前驱溶液,
所述的苯胺-改性吡咯单体共聚前驱溶液,其制备方法如下:
在氮气保护下,将4.3kg的金属钠和10.7kg的吡咯加入到400kg的无水四氢呋喃中,控温60℃,搅拌反应5h;反应完全后,降温至室温后将300kg四氢呋喃,12kg的反式-2,4-己二烯酰氯,缓慢加入到反应体系中,加完后控温40℃下搅拌反应4h,然后加入1.2kg的氯铂酸3%的异丙醇溶液,3kg的二异丙基二氢硅烷,70℃下反应60min,即可得到所述的硅烷接枝改性吡咯单体。
硅烷接枝改性吡咯单体蒸去无水四氢呋喃,加入27.8kg的磺酸基水杨酸和500kg的纯水中,搅拌混合均匀后加入17.4kg的苯胺,控温到0℃,然后搅拌60min,然后加入12.3kg的过硫酸铵,搅拌60min,得到苯胺-改性吡咯单体共聚前驱溶液。
所述的聚合物纤维为芳纶纤维。
所述的碳纤维为聚丙烯腈基碳纤维。
所制备的织物的顶破强力为1524.3n,织物的反射率为-3.54db。
实施例2
一种柔性吸波织物用吸波纤维材料的制备方法,制备技术方案如下:
将54kg聚合物纤维松解、清除其中的杂质,所述的聚合物纤维包括18kg的23g/5m的聚合物纤维,15kg的18g/5m的聚合物纤维,其他为12g/5m的聚合物纤维;将64kg碳纤维条表面清理干净,所述的碳纤维包括42kg的10g/5m碳纤维和25kg29g/5m的碳纤维;先将聚合物纤维合并得到混合聚合物纤维条;将混合聚合物纤维条分别与两种碳纤维进行合并,得到芳纶和碳混纺纤维;将所得到的两种芳纶和碳混纺纤维条加捻度,将其卷装成适应细纱机喂入的细度的芳纶和碳混纺纤维粗纱;芳纶和碳混纺纤维粗纱均匀拉长拉细为54tex的细纱,并给该细纱加上42.6捻/10cm的捻度,得到芳纶和碳混纺纤维细纱;将得到的芳纶和碳混纺纤维细纱作为工作电极进行表面电聚合包覆改性,所述的表面电聚合包覆改性在混纱表面改性液中进行,电位设定在2.3v,沉积时间300s,完成表面包覆改性后混砂经过清洗干燥后即可得到所述的一种柔性吸波织物用吸波纤维材料。
所述的混纱表面改性液为一种苯胺-改性吡咯单体共聚前驱溶液,其制备方法如下:
在氮气保护下,将4.9kg的金属钠和15kg的吡咯加入到600kg的无水四氢呋喃中,控温68℃,搅拌反应7h;反应完全后,降温至室温后将500kg四氢呋喃,18kg的反式-2,4-己二烯酰氯,缓慢加入到反应体系中,加完后控温50℃下搅拌反应7h,然后加入1.8kg的氯铂酸5%的异丙醇溶液,6kg的二异丙基二氢硅烷,77℃下反应90min,即可得到所述的硅烷接枝改性吡咯单体;蒸去无水四氢呋喃,加入32kg的磺酸基水杨酸和700kg的纯水中,搅拌混合均匀后加入22kg的苯胺,控温到5℃,然后搅拌70min,然后加入19kg的过硫酸铵,搅拌70min,得到苯胺-改性吡咯单体共聚前驱溶液。
所述的聚合物纤维为聚丙烯腈纤维。
所述的碳纤维为沥青基碳纤维。
所制备的织物的顶破强力为1541.6n,织物的反射率为-3.67db。
实施例3
一种柔性吸波织物用吸波纤维材料的制备方法,制备技术方案如下:
将68kg聚合物纤维松解、清除其中的杂质,所述的聚合物纤维包括22kg的23g/5m的聚合物纤维,18kg18g/5m的聚合物纤维,其他为12g/5m的聚合物纤维;将76kg碳纤维条表面清理干净,所述的碳纤维包括46kg的10g/5m碳纤维和30kg的29g/5m的碳纤维;先将聚合物纤维合并得到混合聚合物纤维条;将混合聚合物纤维条分别与两种碳纤维进行合并,得到芳纶和碳混纺纤维;将所得到的两种芳纶和碳混纺纤维条加捻度,将其卷装成适应细纱机喂入的细度的芳纶和碳混纺纤维粗纱;芳纶和碳混纺纤维粗纱均匀拉长拉细为68tex的细纱,并给该细纱加上48.2捻/10cm的捻度,得到芳纶和碳混纺纤维细纱;将得到的芳纶和碳混纺纤维细纱作为工作电极进行表面电聚合包覆改性,所述的表面电聚合包覆改性在混纱表面改性液中进行,电位设定在3.6v,沉积时间500s,完成表面包覆改性后混砂经过清洗干燥后即可得到所述的一种柔性吸波织物用吸波纤维材料。
所述的混纱表面改性液为一种苯胺-改性吡咯单体共聚前驱溶液,其制备方法如下:
在氮气保护下,将8.7kg的金属钠和20.2kg的吡咯加入到800kg的无水四氢呋喃中,控温80℃,搅拌反应10h;反应完全后,降温至室温后将600kg四氢呋喃,22kg的反式-2,4-己二烯酰氯,缓慢加入到反应体系中,加完后控温60℃下搅拌反应10h,然后加入3.5kg的氯铂酸7%的异丙醇溶液,8kg的二异丙基二氢硅烷,85℃下反应120min,即可得到所述的硅烷接枝改性吡咯单体;蒸去无水四氢呋喃,加入36.4kg的磺酸基水杨酸和1000kg的纯水中,搅拌混合均匀后加入26.3kg的苯胺,控温到10℃,然后搅拌90min,然后加入18.2kg的过硫酸铵,搅拌90min,得到苯胺-改性吡咯单体共聚前驱溶液。
所述的聚合物纤维为聚丙烯纤维。
所述的碳纤维为酚醛基碳纤维。
所制备的织物的顶破强力为1581.2n,织物的反射率为-3.73db。
实施例4
一种柔性吸波织物用吸波纤维材料的制备方法,制备技术方案如下:
将42kg聚合物纤维松解、清除其中的杂质,所述的聚合物纤维包括15kg的23g/5m的聚合物纤维,12kg的18g/5m的聚合物纤维,其他为12g/5m的聚合物纤维;将58kg碳纤维条表面清理干净,所述的碳纤维包括38kg10g/5m碳纤维和20kg的29g/5m的碳纤维;先将聚合物纤维合并得到混合聚合物纤维条;将混合聚合物纤维条分别与两种碳纤维进行合并,得到芳纶和碳混纺纤维;将所得到的两种芳纶和碳混纺纤维条加捻度,将其卷装成适应细纱机喂入的细度的芳纶和碳混纺纤维粗纱;芳纶和碳混纺纤维粗纱均匀拉长拉细为40tex的细纱,并给该细纱加上32.4捻/10cm的捻度,得到芳纶和碳混纺纤维细纱;将得到的芳纶和碳混纺纤维细纱作为工作电极进行表面电聚合包覆改性,所述的表面电聚合包覆改性在混纱表面改性液中进行,电位设定在1.5v,沉积时间200s,完成表面包覆改性后混砂经过清洗干燥后即可得到所述的一种柔性吸波织物用吸波纤维材料。
所述的混纱表面改性液为一种苯胺-改性吡咯单体共聚前驱溶液按,其制备方法如下:
在氮气保护下,将4.3kg的金属钠和10.7kg的吡咯加入到800kg的无水四氢呋喃中,控温60℃,搅拌反应10h;反应完全后,降温至室温后将600kg四氢呋喃,22kg的反式-2,4-己二烯酰氯,缓慢加入到反应体系中,加完后控温60℃下搅拌反应4h,然后加入1.2kg的氯铂酸3%的异丙醇溶液,3kg的二异丙基二氢硅烷,70℃下反应60min,即可得到所述的硅烷接枝改性吡咯单体;蒸去无水四氢呋喃,加入27.8kg的磺酸基水杨酸和500kg的纯水中,搅拌混合均匀后加入17.4kg的苯胺,控温到10℃,然后搅拌60min,然后加入12.3kg的过硫酸铵,搅拌60min,得到苯胺-改性吡咯单体共聚前驱溶液。
所述的聚合物纤维为聚丙烯纤维。
所述的碳纤维为酚醛基碳纤维。
所制备的织物的顶破强力为1531.5n,织物的反射率为-3.58db。
对比例1
一种柔性吸波织物用吸波纤维材料的制备方法,制备技术方案如下:
将42kg聚合物纤维松解、清除其中的杂质,所述的聚合物纤维包括15kg的23g/5m的聚合物纤维,12kg的18g/5m的聚合物纤维,其他为12g/5m的聚合物纤维;将58kg碳纤维条表面清理干净,所述的碳纤维包括38kg的10g/5m碳纤维和20kg29g/5m的碳纤维;先将聚合物纤维合并得到混合聚合物纤维条;将混合聚合物纤维条分别与两种碳纤维进行合并,得到芳纶和碳混纺纤维;将所得到的两种芳纶和碳混纺纤维条加捻度,将其卷装成适应细纱机喂入的细度的芳纶和碳混纺纤维粗纱;芳纶和碳混纺纤维粗纱均匀拉长拉细为40tex的细纱,并给该细纱加上32.4捻/10cm的捻度,得到芳纶和碳混纺纤维细纱;将得到的芳纶和碳混纺纤维细纱作为工作电极进行表面电聚合包覆改性,所述的表面电聚合包覆改性在混纱表面改性液中进行,电位设定在1.5v,沉积时间200s,完成表面包覆改性后混砂经过清洗干燥后即可得到所述的一种柔性吸波织物用吸波纤维材料。
所述的混纱表面改性液为一种苯胺-改性吡咯单体共聚前驱溶液按,其制备方法如下:
在氮气保护下,将4.3kg的金属钠和10.7kg的吡咯加入到800kg的无水四氢呋喃中,控温60℃,搅拌反应10h;反应完全后,降温至室温后将600kg的含有22kg的反式-2,4-己二烯酰氯的四氢呋喃溶液,缓慢加入到反应体系中,加完后控温60℃下搅拌反应4h;蒸去无水四氢呋喃,加入27.8kg的磺酸基水杨酸和500kg的纯水中,搅拌混合均匀后加入17.4kg的苯胺,控温到10℃,然后搅拌60min,然后加入12.3kg的过硫酸铵,搅拌60min,得到苯胺-改性吡咯单体共聚前驱溶液。
所述的聚合物纤维为聚丙烯纤维。
所述的碳纤维为酚醛基碳纤维。
所制备的织物的顶破强力为1520.8n,织物的反射率为-1.87db。
对比例2
所述的混纱表面改性液为一种苯胺-改性吡咯单体共聚前驱溶液按,其制备方法如下:
在氮气保护下,将4.3kg的金属钠和10.7kg的吡咯加入到800kg的无水四氢呋喃中,控温60℃,搅拌反应10h;反应完全后,然后加入1.2kg的氯铂酸3%的异丙醇溶液,3kg的二异丙基二氢硅烷,70℃下反应60min,即可得到所述的硅烷接枝改性吡咯单体;蒸去无水四氢呋喃,加入27.8kg的磺酸基水杨酸和500kg的纯水中,搅拌混合均匀后加入17.4kg的苯胺,控温到10℃,然后搅拌60min,然后加入12.3kg的过硫酸铵,搅拌60min,得到苯胺-改性吡咯单体共聚前驱溶液。
所制备的织物的顶破强力为1523.1n,织物的反射率为-2.92db。
对比例3
一种柔性吸波织物用吸波纤维材料的制备方法,制备技术方案如下:
将42kg聚合物纤维松解、清除其中的杂质,所述的聚合物纤维包括15kg的23g/5m的聚合物纤维,12kg的18g/5m的聚合物纤维,其他为12g/5m的聚合物纤维;将58kg碳纤维条表面清理干净,所述的碳纤维包括38kg的10g/5m碳纤维和20kg的29g/5m的碳纤维;先将聚合物纤维合并得到混合聚合物纤维条;将混合聚合物纤维条分别与两种碳纤维进行合并,得到芳纶和碳混纺纤维;将所得到的两种芳纶和碳混纺纤维条加捻度,将其卷装成适应细纱机喂入的细度的芳纶和碳混纺纤维粗纱;芳纶和碳混纺纤维粗纱均匀拉长拉细为40tex的细纱,并给该细纱加上32.4捻/10cm的捻度,得到芳纶和碳混纺纤维细纱;将得到的芳纶和碳混纺纤维细纱作为工作电极进行表面电聚合包覆改性,所述的表面电聚合包覆改性在混纱表面改性液中进行,电位设定在1.5v,沉积时间200s,完成表面包覆改性后混砂经过清洗干燥后即可得到所述的一种柔性吸波织物用吸波纤维材料。
所述的混纱表面改性液为一种苯胺-改性吡咯单体共聚前驱溶液按,其制备方法如下:
在氮气保护下,将4.3kg金属钠和10.7kg吡咯,17.4kg苯胺,控温到0℃,然后搅拌60min,然后加入12.3kg过硫酸铵,然后加纯化水稀释至0.5%,搅拌混合均匀后即可得到所述的纱表面改性液。
所述的聚合物纤维为芳纶纤维。
所述的碳纤维为聚丙烯腈基碳纤维。
所制备的织物的顶破强力为1522.8n,织物的反射率为-2.18db。
起点商标作为专业知识产权交易平台,可以帮助大家解决很多问题,如果大家想要了解更多知产交易信息请点击 【在线咨询】或添加微信 【19522093243】与客服一对一沟通,为大家解决相关问题。
此文章来源于网络,如有侵权,请联系删除


