竹片铣削用智能分列、识别及自动输送方法和设备与流程



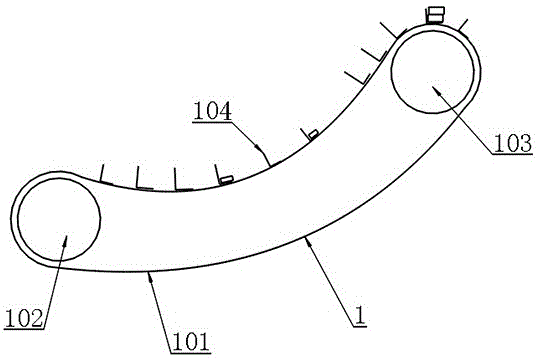
本发明属于竹木加工技术领域,尤其涉及一种竹片铣削用智能分列、识别及自动输送方法和设备。
背景技术:
竹片,指的是圆竹经定长截断、破竹开片后的弧形竹片,一般成堆成垛存放,其在进行后续深加工时,需要逐个分开并有序进入后续加工设备中,这就需要对竹片进行分列输送,以及统一朝向面的工作,例如要求竹片全部竹青面朝上或竹黄面朝上。
另一方面,现有的竹片深加工前端输送进料方式,目前主要靠人工依次一片一片地送入后续加工设备,进料效率较低、劳动强度较大、安全风险较高,而要实现此工序的自动化和智能化,则需要解决竹片有序分列、识别翻面、自助依次输送等问题。
专利公告号为cn208213698u,公告日为2018.12.11的中国实用新型专利公开了一种竹片品质视觉智能分拣机,包括机架,竹片存储仓,皮带提升机,离心盘,输送带,不良踢除站,高速相机,光源,180度翻转带,良品存储仓,控制装置,所述竹片存储装置在机架的尾部,皮带提升机,离心盘,不良品踢除站,高速相机,良品存储装置180度翻转装置在设备中部,控制装置操作面在设备前端。
但是该实用新型专利中的竹片分拣机存在输送分拣效率低的问题。
技术实现要素:
本发明的目的是提供一种竹片铣削用智能分列、识别及自动输送方法和设备,其能通过将倾斜输送带单元、单个竹片分离单元、翻转单元以及推动单元整合为一套竹片输送设备,并按照先上提、再单个分离、接着竹青识别翻面、最后轴向出料四步法操作的方式,达到竹片有序输送出料的效果。本发明具有竹片输送、分离、翻面、出料操作简单高效,设备自身结构稳定性高,操作使用灵活方便,以及最终的竹片能够全部竹黄面朝上逐个稳定出料送出的优点。
本发明解决上述问题采用的技术方案是:竹片铣削用智能分列、识别及自动输送方法,依次包括以下步骤:
s1、将平行排列的成堆竹片进行上提式输送推动;
s2、将单个限位推动结构上输送的两个竹片进行分离操作,保证后续输送过程中竹片单个推动;
s3、对竹青朝上的竹片进行识别、翻面,保证所有的竹片全部竹黄朝上;
s4、将竹片下落至轴向输送带上,输送出料。
进一步优选的技术方案在于:步骤s1、s2、s3以及s4中,所述限位推动结构的竖向截面形状均为l型,限位推动结构的开口朝向与输送前进方向相同。
竹片铣削用智能分列、识别及自动输送设备,沿着竹片前进方向依次包括用于上提竹片的倾斜输送带单元,用于对所述倾斜输送带单元上聚集的两个竹片进行分离的单个竹片分离单元,用于将竹青朝上的竹片翻面的翻转单元,以及用于接收下落的竹片并进行轴向输送出料操作的推动单元。
进一步优选的技术方案在于:所述倾斜输送带单元包括上层带体上安放成堆竹片的下垂式输送带,设置在所述下垂式输送带内的下方带轮,设置在所述下垂式输送带内且靠近所述单个竹片分离单元的上方带轮,以及设置在所述下垂式输送带外表面上的l型第一推动板。
进一步优选的技术方案在于:所述竹片分离单元在沿着竹片前进方向上依次包括用于引导竹片倾斜下落的两侧弯折板,设置两个所述两侧弯折板之间并通过远离所述倾斜输送带单元一侧设有向下斜面的方式以用于先接收再抬起竹片的第一升降板,通过前进方向上宽度小于竹片宽度的方式以用于顶起单独一个竹片,而将可能的第二个竹片推动滑落回到所述第一升降板上的第二升降板,以及用于在所述第二升降板上升最高点接收竹片并引导竹片滑动下落至所述翻转单元上的固定倾斜板。
进一步优选的技术方案在于:所述翻转单元包括用于提升竹片至水平状态且倾斜初始端位于所述固定倾斜板下方的弯折形输送带,设置在所述弯折形输送带外表面上的l型第二推动板,分别设置在所述弯折形输送带两边的两个固定板,设置在所述固定板相对内侧面上的旋转用气缸,设置在所述旋转用气缸上的旋转板,分别设置在所述旋转板相对内侧面上两侧位置处的两个推动气缸,以及设置在所述推动气缸上并用于夹紧竹青面朝上的竹片的夹紧板。
进一步优选的技术方案在于:所述翻转单元还包括设置在所述固定板相对内侧面上并用于向下检测竹片朝上面颜色、竹节凸起和弯曲面的识别摄像头,设置在所述旋转板侧面上并用于限位固定所述夹紧板的滑动向凸出条,以及设置中所述弯折形输送带水平段尾部中间位置处并用于对竹片进行下落导向的弧形板。
进一步优选的技术方案在于:所述推动单元包括设置在所述弯折形输送带水平段尾部下方位置处且移动方向平行竹片长轴向的输送皮带,设置在所述输送皮带上的皮带轮,以及设置在所述输送皮带上方且远离竹片出料一侧并用于推动竹片的推动气缸。
进一步优选的技术方案在于:所述推动单元还包括设置在所述皮带轮长轴向两侧的两个限位板,以及设置在所述推动气缸的气缸轴上的推动板。
进一步优选的技术方案在于:所述倾斜输送带单元、单个竹片分离单元、翻转单元以及推动单元均设置在设备架体上。
本发明通过将倾斜输送带单元、单个竹片分离单元、翻转单元以及推动单元整合为一套竹片输送设备,并按照先上提、再单个分离、接着竹青识别翻面、最后轴向出料四步法操作的方式,达到竹片有序输送出料的效果。本发明具有竹片输送、分离、翻面、出料操作简单高效,设备自身结构稳定性高,操作使用灵活方便,以及最终的竹片能够全部竹黄面朝上逐个稳定出料送出的优点。
附图说明
图1为本发明中倾斜输送带单元的结构示意图。
图2为本发明中单个竹片分离单元的位置结构示意图。
图3为本发明中翻转单元的位置结构示意图。
图4为本发明中夹紧板的使用示意图。
图5为本发明中推动单元的位置结构示意图。
具体实施方式
以下所述仅为本发明的较佳实施例,并非对本发明的范围进行限定。
实施例:如附图1、2、3、4以及附图5所示,竹片铣削用智能分列、识别及自动输送方法,依次包括以下步骤:
s1、将平行排列的成堆竹片进行上提式输送推动;
s2、将单个限位推动结构上输送的两个竹片进行分离操作,保证后续输送过程中竹片单个推动;
s3、对竹青朝上的竹片进行识别、翻面,保证所有的竹片全部竹黄朝上;
s4、将竹片下落至轴向输送带上,输送出料。
在本实施例中,步骤s1用于将成堆竹片分开输送,但是也会发生两个竹片一起输送的情况,依次就需要步骤s2对这两个竹片进行分离,然后是步骤s3中,用于对竹青面、即竹筒外侧面朝上的竹片进行翻面,保证所有的竹片全部竹黄,即竹筒内侧面朝上即可,最后是在步骤s4中,将竹片逐个按长轴向输送出料,保证有序进入竹片加工的下一道工序。
步骤s1、s2、s3以及s4中,所述限位推动结构的竖向截面形状均为l型,限位推动结构的开口朝向与输送前进方向相同。
在本实施例中,所述限位推动结构可以是l型长板,也可以是两侧的两个l型块,保证可以对竹片进行向前推动输送即可。
竹片铣削用智能分列、识别及自动输送设备,沿着竹片前进方向依次包括用于上提竹片的倾斜输送带单元1,用于对所述倾斜输送带单元1上聚集的两个竹片进行分离的单个竹片分离单元2,用于将竹青朝上的竹片翻面的翻转单元3,以及用于接收下落的竹片并进行轴向输送出料操作的推动单元4。
在本实施例中,所述倾斜输送带单元1出料处的竹片大部分逐个分开,少数部分两个堆叠,所述单个竹片分离单元2处用于将一起进入的两个竹片分离,保证所述翻转单元3上通过的竹片是逐个的,接着所述翻转单元3用于将竹青面朝上的竹片翻面,最后在所述推动单元4处沿着竹片的长轴向向外出料即可。
所述倾斜输送带单元1包括上层带体上安放成堆竹片的下垂式输送带101,设置在所述下垂式输送带101内的下方带轮102,设置在所述下垂式输送带101内且靠近所述单个竹片分离单元2的上方带轮103,以及设置在所述下垂式输送带101外表面上的l型第一推动板104。
在本实施例中,平行的成堆竹片放在所述下垂式输送带101的上层带体上,一个或最多两个竹片在单个所述l型第一推动板104上被卡合推动,成堆的竹片变成有效前进的分开竹片,最后在所述上方带轮103处下落。
所述竹片分离单元2在沿着竹片前进方向上依次包括用于引导竹片倾斜下落的两侧弯折板201,设置两个所述两侧弯折板201之间并通过远离所述倾斜输送带单元1一侧设有向下斜面的方式以用于先接收再抬起竹片的第一升降板202,通过前进方向上宽度小于竹片宽度的方式以用于顶起单独一个竹片,而将可能的第二个竹片推动滑落回到所述第一升降板202上的第二升降板203,以及用于在所述第二升降板203上升最高点接收竹片并引导竹片滑动下落至所述翻转单元3上的固定倾斜板204。
在本实施例中,竹片在所述上方带轮103处的所述l型第一推动板104上下落,沿着所述两侧弯折板201最终滑落至所述第一升降板202上,即所述第一升降板202上端侧面与所述第二升降板203侧向平面之间组成的锐角旋转槽口内,然后所述第一升降板202的气缸受控抬起,竹片上升,直至滑落到所述第二升降板203的倾斜顶面上,此时情况一分为二,若是单个竹片滑动所述第二升降板203上,则所述第二升降板203的气缸受控抬起,竹片滑到所述固定倾斜板204,最终滑落至所述翻转单元3,即可保证原本就有的单个竹片输送效果。
另一方面,而当两个竹片一起滑到所述第二升降板203上时,所述第二升降板203上自身宽度较小,只要抬起一个竹片,另一个就回落至所述第一升降板202上,然后被所述第二升降板203抬起的竹片下落至所述翻转单元3、被回落的竹片再进行一次上述的正常顶起滑落操作即可,保证可以将原本堆叠的竹片一分为二。
此外,堆叠的两个竹片中回落的竹片在回落到所述第一升降板202上之前,所述第一升降板202顶点的高度都不能低于所述两侧弯折板201最低点的高度,避免回落的竹片处再进料,造成三个竹片堆叠的情况。
所述翻转单元3包括用于提升竹片至水平状态且倾斜初始端位于所述固定倾斜板204下方的弯折形输送带301,设置在所述弯折形输送带301外表面上的l型第二推动板302,分别设置在所述弯折形输送带301两边的两个固定板303,设置在所述固定板303相对内侧面上的旋转用气缸304,设置在所述旋转用气缸304上的旋转板305,分别设置在所述旋转板305相对内侧面上两侧位置处的两个推动气缸306,以及设置在所述推动气缸306上并用于夹紧竹青面朝上的竹片的夹紧板307。所述翻转单元3还包括设置在所述固定板303相对内侧面上并用于向下检测竹片朝上面颜色、竹节凸起和弯曲面的识别摄像头308,设置在所述旋转板305侧面上并用于限位固定所述夹紧板307的滑动向凸出条309,以及设置中所述弯折形输送带301水平段尾部中间位置处并用于对竹片进行下落导向的弧形板310。
在本实施例中,所述识别摄像头308通过现有方式判断竹片朝上面的颜色是绿色还是黄色、判断竹节朝上即为竹青面、判断弧形面朝下即为竹青面,所述推动气缸306先夹紧竹青面朝上的待翻面竹片,所述旋转用气缸304再旋转180°,所述推动气缸306再放开翻面完成的竹片,最后是所述旋转用气缸304再旋转复位即可,所述弧形板310用于过渡连接竹片的下滑通道,保证原本竹黄朝上的竹片不至于翻面。
所述推动单元4包括设置在所述弯折形输送带301水平段尾部下方位置处且移动方向平行竹片长轴向的输送皮带401,设置在所述输送皮带401上的皮带轮402,以及设置在所述输送皮带401上方且远离竹片出料一侧并用于推动竹片的推动气缸403。所述推动单元4还包括设置在所述皮带轮402长轴向两侧的两个限位板404,以及设置在所述推动气缸403气缸轴上的推动板405。
在本实施例中,所述推动板405在所述推动气缸403的作用下,沿竹片的长轴向推动竹片,以进行出料操作,该推动方式为所述输送皮带401输送动作的补充,避免所述输送皮带401与竹片之间摩擦力不够而不能带动输送的问题,比较竹黄面朝上、竹青面朝下是与所述输送皮带401之间的接触面面积相对较小。
所述倾斜输送带单元1、单个竹片分离单元2、翻转单元3以及推动单元4均设置在设备架体上。
在本实施例中,所述倾斜输送带单元1、单个竹片分离单元2、翻转单元3以及推动单元4的控制系统按照使用需要进行开发调试,按照现有技术中的方式完成,所述倾斜输送带单元1、单个竹片分离单元2、翻转单元3以及推动单元4的结构均按照现有连接方式进行安装设置,保证上述使用方法可以顺利进行即可。
上面结合附图对本发明的实施方式作了详细说明,但是本发明不限于上述实施方式,在所述技术领域普通技术人员所具备的知识范围内,还可以在不脱离本发明宗旨的前提下做出各种修改。这些都是不具有创造性的修改,只要在本发明的权利要求范围内都受到专利法的保护。
起点商标作为专业知识产权交易平台,可以帮助大家解决很多问题,如果大家想要了解更多知产交易信息请点击 【在线咨询】或添加微信 【19522093243】与客服一对一沟通,为大家解决相关问题。
此文章来源于网络,如有侵权,请联系删除


