一种长单板条定向刨花板的制备方法与流程



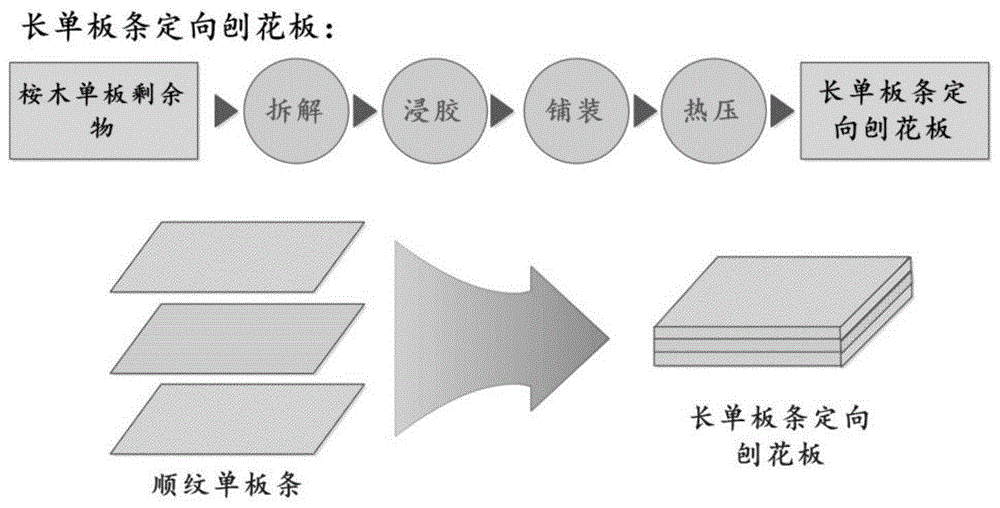
本发明涉及一种定向刨花板的制备方法,特别涉及一种长单板条定向刨花板的制备方法。
背景技术:
定向刨花板(osb)全称orientedstrandboard,是一种以长刨花为基本单元的结构板材。定向刨花板是将原木或木材剩余物沿顺纹方向加工成大片刨花,刨花尺寸通常控制在长40-120mm,宽5-20mm,厚0.3-1.0mm;经过干燥,施以胶黏剂和其他改性剂,各层呈一定角度分别进行定向铺装,在压机的作用下压制而成。我国对于木材的需求日益增加,但森林资源本相对缺乏,导致木材供应日益紧张,所以需要大量人工林来为人造板行业提供原材料。定向刨花板对原料要求低,桉木、杨木等木材即可满足生产要求,但所需原料的来源广泛,这两种木材是我国最主要的速生树种,正好缓解我国木材紧缺的形势。定向刨花板静曲强度高,尺寸稳定性好,是一种性价比较高的新板材,而且与胶合板、细木工板劳动密集型的生产不同,osb生产线的自动化程度高,更加标准化、现代化。桉木力学性能优异,用桉树生产的胶合板和刨花板具有较高的力学强度,化学性质对人造板制备有重要的影响,桉木中影响胶合的物质较少,桉木比松木等对胶黏剂的亲和力更强,使得桉木osb具有良好的胶接强度以及优异的力学性能。将桉木用在osb生产,在加工成长木片的工艺过程中,桉木的生长应力会得到释放,保证应力不影响成板的尺寸稳定;同样刨花加工后可以克服桉木开裂变形的缺陷。桉木物理材性较好,通过定向铺装,可以发挥其高顺纹强度的优势,桉木osb在和其他树种osb的比较中强度更高。制造定向刨花板时,希望胶黏剂在刨花表面胶结,可以充分发挥胶黏剂的性能,桉木渗透性较差,所以胶黏剂会停留在刨花表面,桉木生产的osb胶合强度更高。综合考虑桉木的各方面材性和osb的生产特点,桉木osb具有优良的力学强度和使用性能。
osb几十年的发展中,刨花形态大体变化是:在厚度、宽度基本不变的前提下,刨花长度不断增加。刨花长度增长,代表着同样尺寸的osb内刨花之间的搭接端头更少,端头在人造板内相当于缺陷,所以刨花长度与osb强度成正比,而且更长的刨花尺寸使得长刨花的定向性更好,更接近胶合板的内部结构。而现有技术中缺少通过调节刨花长度从而制造出性能上更优异的定向刨花板的方法,因此,目前亟需一种能用长单板条制备得到一种性能好的定向刨花板的制备方法。
公开于该背景技术部分的信息仅仅旨在增加对本发明的总体背景的理解,而不应当被视为承认或以任何形式暗示该信息构成已为本领域一般技术人员所公知的现有技术。
技术实现要素:
本发明针对上述技术问题,发明一种能够提高桉木单板剩余物利用率,并且能够制备得到一种力学性能好的定向刨花板的制备方法。
为实现上述目的,本发明提供的技术方案如下:
一种长单板条定向刨花板的制备方法,包含以下操作步骤:
(1)拆解:将桉木单板剩余物切成等宽的顺纹单板条,对等宽的顺纹单板条进行筛选,尺寸要求如:长度40cm~120cm,宽度9mm,厚度0.8-2.5mm;
(2)浸胶:取酚醛树脂,以酚醛树脂质量3%-8%的比例添加高筋面粉,搅拌均匀得到胶黏剂,再将步骤(1)中筛选所得顺纹单板条放入胶黏剂中,搅拌,使胶黏剂均匀分布在顺纹单板条上;
(3)干燥:将步骤(2)施胶后的顺纹单板条干燥至含水量为5%~8%,称量干燥后的顺纹单板条质量与最初质量比较,得出浸渍量为9%-25%,即为步骤(2)中的施胶量;
(4)铺装:将步骤(3)中干燥后所得的顺纹单板条铺装,按照一定的方向均匀地排列在自制模具中作为下层,再将另一份顺纹单板条铺在下层之上作为中层,中层顺纹单板条与下层顺纹单板条呈90°方向定向均匀排列,最后将再一份的顺纹单板条铺在中层之上作为上层,上层顺纹单板条与中层顺纹单板条呈90°方向定向均匀排列,得到板坯,其中,上层:中层:下层按照质量比为2~4:2~6:2~4;
(5)热压:将步骤(4)所得板坯进行热压,保压时间为10-20min,压力为1.0-2.0mpa,热压温度为120-150℃,得到10mm厚度的板坯,即得长单板条定向刨花板。
优选的是,步骤(1)中所述的顺纹单板条厚度为1.7mm。
优选的是,步骤(2)中所述的高筋面粉的添加量为5%。
优选的是,步骤(3)中所述的施胶量为15%。
优选的是,步骤(3)中所述干燥温度为65℃,干燥时间2小时。
优选的是,步骤(4)中所述的上、中、下三层按照质量比为2:6:2。
优选的是,步骤(5)中所述的保压时间为15min,压力为1.5mpa,热压温度为135℃。
与现有技术相比,本发明具有如下有益效果:
本发明方法直接采用与成板通长一致的顺纹单板条作为基本单元,充分发挥桉木在单一方向上的强度优势,以酚醛树脂作为胶黏剂,通过设计顺纹单板条参数、铺装方式、施胶量以及热压条件制得具有高强度、符合标准的新型定向刨花板。
附图说明
图1是长单板条定向刨花板制备工艺示意图。
图2是不同因素对本发明制备所得定向刨花板静曲强度的影响。
图3是不同因素对本发明制备所得定向刨花板弹性模量的影响。
图4是不同因素对本发明制备所得定向刨花板内结合强度的影响。
图5是不同因素对本发明制备所得定向刨花板吸水膨胀率的影响。
具体实施方式
下面结合附图具体实施方式进行详细描述,但应当理解本发明的保护范围并不受具体实施方式的限制。实施例中采用的原料、实际若无特殊说明,皆为市售所得,实施例中使用的桉木单板剩余物为桉木单板加工过程中剩余的边角料。
实施例1
一种长单板条定向刨花板的制备方法,操作步骤如下:
(1)拆解:利用疏解机将桉木单板剩余物切成等宽的顺纹单板条,选择长度41cm-43cm、宽度9mm、厚度1.7mm的顺纹单板条刨花;
(2)浸胶:取酚醛树脂,以酚醛树脂质量5%的比例添加高筋面粉,用玻璃棒搅拌均匀得到胶黏剂,再将步骤(1)中筛选所得顺纹单板条放入托盘中手动搅拌,使用搅拌均匀所得胶黏剂均匀喷洒分布在顺纹单板条上;
(3)干燥:将步骤(2)施胶后的顺纹单板条保持温度为65℃干燥2小时,干燥至含水量为5%~8%,称量干燥后的顺纹单板条质量与最初质量比较,得出浸渍量为15%,即为步骤(2)中的施胶量;
(4)铺装:将步骤(3)中干燥后所得的顺纹单板条通过手工方式铺装,按照一定的方向均匀地排列在自制模具中作为下层,也称为下表层,再将另一份顺纹单板条铺在下层之上作为中层,也即芯层,中层顺纹单板条与下层顺纹单板条呈90°方向定向均匀排列,最后将再一份的顺纹单板条铺在中层之上作为上层,也即上表层,上层顺纹单板条与中层顺纹单板条呈90°方向定向均匀排列,得到板坯,其中,上层:中层:下层按照质量比为2:6:2,上表层和下表层统称表层;
(5)热压:将步骤(4)所得板坯放入实验用热压机中进行热压,通过计算机热压系统对试验参数进行控制,保压时间为15min,压力为1.5mpa,热压温度为135℃,得到10mm厚度的板坯,即为长单板条定向刨花板。
陈放:热压完成后取出步骤(5)所得板坯陈放2-5天,留待检测。
实施例2
一种长单板条定向刨花板的制备方法,操作步骤如下:
(1)拆解:利用疏解机将桉木单板剩余物切成等宽的顺纹单板条,选择长度41cm-43cm、宽度9mm、厚度1.7mm的顺纹单板条刨花;
(2)浸胶:取酚醛树脂,以酚醛树脂质量3%的比例添加高筋面粉,用玻璃棒搅拌均匀得到胶黏剂,再将步骤(1)中筛选所得顺纹单板条放入托盘中手动搅拌,使胶黏剂均匀分布在顺纹单板条上;
(3)干燥:将步骤(2)施胶后的顺纹单板条保持温度为65℃干燥2小时,干燥至含水量为5%~8%,称量干燥后的顺纹单板条质量与最初质量比较,得出浸渍量为15%,即为步骤(2)中的施胶量;
(4)铺装:将步骤(3)中干燥后所得的顺纹单板条通过手工方式铺装,按照一定的方向均匀地排列在自制模具中作为下层,也称为下表层,再将另一份顺纹单板条铺在下层之上作为中层,也即芯层,中层顺纹单板条与下层顺纹单板条呈90°方向定向均匀排列,最后将再一份的顺纹单板条铺在中层之上作为上层,也即上表层,上层顺纹单板条与中层顺纹单板条呈90°方向定向均匀排列,得到板坯,其中,上层:中层:下层按照质量比为3:4:3,上表层和下表层统称表层;
(5)热压:将步骤(4)所得板坯放入实验用热压机中进行热压,通过计算机热压系统对试验参数进行控制,保压时间为10min,压力为1.5mpa,热压温度为135℃,得到10mm厚度的板坯,即为长单板条定向刨花板。
陈放:热压完成后取出步骤(5)所得板坯陈放2-5天,留待检测。
实施例3
一种长单板条定向刨花板的制备方法,操作步骤如下:
(1)拆解:利用疏解机将桉木单板剩余物切成等宽的顺纹单板条,选择长度41cm-43cm、宽度9mm、厚度2.2的顺纹单板条刨花;
(2)浸胶:取酚醛树脂,以酚醛树脂质量8%的比例添加高筋面粉,用玻璃棒搅拌均匀得到胶黏剂,再将步骤(1)中筛选所得顺纹单板条放入托盘中手动搅拌,使胶黏剂均匀分布在顺纹单板条上;
(3)干燥:将步骤(2)施胶后的顺纹单板条保持温度为65℃干燥2小时,干燥至含水量为5%~8%,称量干燥后的顺纹单板条质量与最初质量比较,得出浸渍量为25%,即为步骤(2)中的施胶量;
(4)铺装:将步骤(3)中干燥后所得的顺纹单板条通过手工方式铺装,按照一定的方向均匀地排列在自制模具中作为下层,也称为下表层,再将另一份顺纹单板条铺在下层之上作为中层,也即芯层,中层顺纹单板条与下层顺纹单板条呈90°方向定向均匀排列,最后将再一份的顺纹单板条铺在中层之上作为上层,也即上表层,上层顺纹单板条与中层顺纹单板条呈90°方向定向均匀排列,得到板坯,其中,上层:中层:下层按照质量比为4:2:4,上表层和下表层统称表层;
(5)热压:将步骤(4)所得板坯放入实验用热压机中进行热压,通过计算机热压系统对试验参数进行控制,保压时间为15min,压力为1.5mpa,热压温度为145℃,得到10mm厚度的板坯,即为长单板条定向刨花板。
陈放:热压完成后取出步骤(5)所得板坯陈放2-5天,留待检测。
检测:
参照实施例1的操作方法,分别改变以下参数:单板条厚度(步骤(1)),热压温度,施胶量,铺层结构(步骤(4)中上层:中层:下层),进行制备长单板条定向刨花板。
表1
表1中铺层结构20/60/20中20表示上层、下层各占制备所得长单板条定向刨花板质量的20%,60表示中层占制备所得长单板条定向刨花板质量的60%,20/60/20表示上层:中层:下层按照质量比为2:6:2,其他铺层结构解释相同。对根据表1参数制备所得各长单板条定向刨花板的静曲强度、弹性模量、内结合强度、煮沸后内结合强度、吸水厚度膨胀率进行检测,结果如表2所示:
表2
表2得出的相应数据,做极差分析,得出图2-5,图2a表明静曲强度∥随着温度上升先上升后大幅度下降,但静曲强度⊥对温度变化不敏感;图2b表明静曲强度∥随着施胶量的减少而减小,但静曲强度⊥是先减小后增大;图2c表明随着单板条厚度的增大静曲强度先增大后减小;图2d表明表芯层比为4:2:4时静曲强度∥大于另两个表芯层比,而静曲强度⊥小于两个另外表芯层比。这是由于单板条厚度的增加会使得每一根组成板材的单板条的强度得到增长,1.7mm的单板条比1mm单板条的水平强度增加巨大,整体水平方向的静曲强度大幅增长,而单板条厚度继续增加,每张板所用单板条数量较少,在定向的有序性上比较差,成板内部存在空洞和缺失,这些缺陷位置容易被破坏,静曲强度∥会低于内部均匀无缺陷的结构。随着施胶量的减少,定向刨花板会出现缺胶现象,胶液分布不均,影响水平方向的静曲强度。改变铺层比例,当表层比例越高时,静曲强度∥理所当然的越强,但表芯层比例从3:4:3到4:2:4提高不大,原因可能是4:2:4的各层结构均匀性更差,结构稳定性不强。综合分析得出,在热压温度为135℃,施胶量为15%,单板条厚度为1.7mm,表芯层比为3:4:3条件下的定向刨花板静曲强度∥达到68.37mpa左右,静曲强度⊥达到22.36mpa左右,达到标准ly/t1580-2010中10mm~18mm厚度的osb/4的静曲强度∥所要求的30mpa,静曲强度⊥所要求的16mpa。
图3a表明弹性模量∥随着温度上升先上升后下降,但弹性模量⊥对温度变化不敏感;图3b表明弹性模量∥随着施胶量的减少而减小,但弹性模量⊥是先减小后增大;图3c表明随着单板条厚度的增大弹性模量先增大后减小;图3d表明表芯层比为4:2:4时弹性模量∥大于另两个表芯层比,而弹性模量⊥小于另外两个表芯层比。弹性模量与静曲强度相关性很强,对相对应的影响因素的变化,弹性模量的趋势变化与静曲强度相同,分析其原因也与静曲强度趋势分析相同。综合分析得出,在热压温度为135℃,施胶量为15%,单板条厚度为1.7mm,表芯层比为2:6:2条件下的定向刨花板弹性模量∥达到7941.81mpa左右,弹性模量⊥达到3188.51mpa左右,达到标准ly/t1580-2010中10mm~18mm厚度的osb/4的弹性模量∥所要求的4800mpa,弹性模量⊥所要求的1900mpa。
由图4可得,试件的内结合强度均高于煮沸后内结合强度:如图4a所示,在125℃到145℃的热压温度范围内,干内结合强度先是上升后再下降,在135℃时刨花板的内结合强度达到0.4mpa,之后开始下降,而煮沸后内结合强度缓慢增加至0.06mpa,这可能是因为135℃是所施胶的最佳固化温度,125℃的时候胶液固化不完全,而145℃温度过高出现过固化导致内结合强度下降;如图4b所示,在随施胶量的减少,试件的内结合强度持续下降,煮沸后内结合强度总体上也呈下降趋势(从0.059mpa下降到0.031mpa);如图4c所示,在单板条厚度为1.0mm~2.2mm的范围内,内结合强度缓慢上升。煮沸后内结合趋势与内结合强度相一致,分析其原因也一致,可能是由于当单板条的厚度增加时,其抵抗剪切的能力增强,单板条发生木破的难度提高,要将试件破坏,所需的载荷变大。此外,单板条厚度还间接地影响了单位面积的施胶量,单板条越厚,所需的数量越少,总体的表面积越小,使得单位面积上施胶更多,胶结更均匀紧密,所以随着单板条厚度增加,内结合强度增加。如图4d所示,在表芯层比例的各水平中,试件的内结合强度先下降后上升,4:2:4和2:6:2的内结合强度基本相同,为0.39mpa,比例为3:4:3的板材内结合强度较低,为0.31mpa。参照ly/t1580-2010,osb/3型的内结合强度不应低于0.34mpa,单板条厚度1.7mm和2.2mm水平可满足此类板要求,热压温度各水平均满足此类板要求,施胶量15%和12%水平满足此类板要求,表芯层比例4:2:4和2:6:2水平满足此类板要求;osb/4型的内结合强度不应低于0.5mpa,以上各水平均不能达到标准要求,根据表2可以看到实验第8组、第9组内结合强度达到0.5mpa,说明经过优化后该osb的内结合强度有能力达到osb/4型的标准要求。
由图5中可以看出吸水厚度膨胀率随着热压温度的升高而增加,说明单板条厚度增加会使得定向刨花板吸水膨胀增大,但增长到1.7mm厚度时24h吸水厚度膨胀率增加不大,之后增长加快,分析是酚醛树脂对桉木单板条渗透有限,单板条越厚,渗透部分越少,浸水后,胶层和胶液渗透部分吸水膨胀小,而纯木质部分膨胀大,所以单板条越厚膨胀越大。施胶量的趋势与单板条厚度增长的趋势相仿,随施胶减少,吸水膨胀增大,增长趋势先缓后急,15%和12%的施胶量区别不大,再次证明了12%时施胶接近饱和。而热压温度和表芯层比例趋势平缓,说明其对24h吸水厚度膨胀率影响不大。
利用综合分析法对以上指标进行分析,表芯层比例对定向刨花板的各项性能影响很大,特别是对板的静曲强度和弹性模量,表芯层的不同比例实际上就对应单板条在水平和垂直方向的数量比例,单板条数量更多直接导致强度更高。当表芯层比例为3:4:3和4:2:4时,水平方向上的单板条占比高,水平方向上的静曲强度和弹性模量更高,但垂直方向上静曲强度和弹性模量无法达到osb/4型的要求,所以放弃水平方向上的部分强度,在表芯层比例上选择2:6:2的水平。施胶量方面,15%的水平时各项性能指标基本都在最好的水平,因此选取15%作为优化实验的施胶量水平。对于单板条厚度,厚度增加会使得单根单板条的强度增长,使得整体强度增加,而厚度继续增加,每张板所用单板条数量减少,排列上均匀性差,内部空隙增多增大,导致强度小幅下降,所以选择1.7mm的单板条。热压温度对osb的许多性能影响不显著,所以选择考虑多数指标都达到最佳性能的水平,选择135℃。
综合考虑,制备所得长单板条定向刨花板性能最佳时选用的参数如下:单板条厚度1.7mm,热压温度135℃,施胶量15%,表芯层比例2:6:2(即实施例1),实验数据见下表3;
表3
结果如表3所示,内结合强度、静曲强度、弹性模量这几项力学性能的指标符合ly/t1580-2010中osb/4型的要求。24h吸水厚度膨胀率为12.6%,比表1-2中各组数据都低,可以达到osb/3型的要求,相比正交实验的板材提升了一个等级。煮沸实验后内结合强度为0.11mpa,标准中osb/4型的要求为0.15mpa,验证组仍没有达到标准要求,但已有一定提高,实际检测时,试件的断裂位置发生在热熔胶与试件的界面或是仅有一根单板条被拉开,木破率低,出现这种现象的原因是经沸水煮后,试件已出现变形,表面凹凸不平,热熔胶的胶连界面很小,破坏出现在界面上,破坏应力低于其实际的内结合强度。防水性能而言,优化组有了显著提高,优化实验组的各项性能基本符合预期。
前述对本发明的具体示例性实施方案的描述是为了说明和例证的目的。这些描述并非想将本发明限定为所公开的精确形式,并且很显然,根据上述教导,可以进行很多改变和变化。对示例性实施例进行选择和描述的目的在于解释本发明的特定原理及其实际应用,从而使得本领域的技术人员能够实现并利用本发明的各种不同的示例性实施方案以及各种不同的选择和改变。本发明的范围意在由权利要求书及其等同形式所限定。
起点商标作为专业知识产权交易平台,可以帮助大家解决很多问题,如果大家想要了解更多知产交易信息请点击 【在线咨询】或添加微信 【19522093243】与客服一对一沟通,为大家解决相关问题。
此文章来源于网络,如有侵权,请联系删除


