全自动竹条上料装置的制作方法



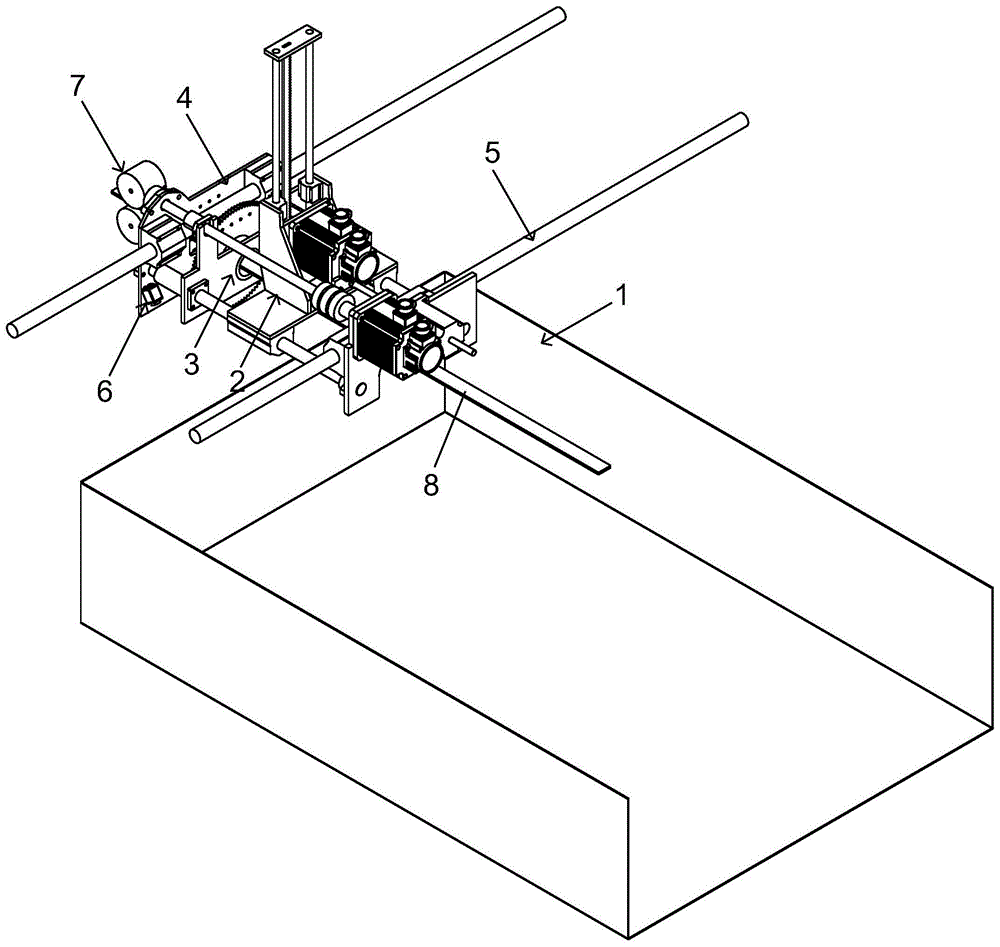
本发明涉及竹子加工设备,特别是一种全自动竹条上料装置。
背景技术:
竹板材是由竹条经胶合压制而成的集成材,具有卓越的物理力学性能,并且具有吸水膨胀系数小、强度高、稳定性和韧性好的优点。
传统竹板材的制作方法是先将竹子经截段、去内外结、开片后制成竹条,而后再将一根根竹条分别铣削成前端与后端等厚的竹胚,最后由若干根竹胚粘贴拼接成竹板材。
竹条的铣削操作是通过刨切机完成。目前刨切机上料仍然采用手工完成,生产过程中工人需要快速且连续不断的将竹条放入剖切机进料侧,并且每次上料需要保证竹条的上下面统一,即在上料的同时还需要调整竹条的正反面,而刨切机的处理速度较快,可要达到0.5秒数量级,采用人工上料不仅劳动强度大,还会限制刨切机的生产效率。此外,采用人工上料也存在一定的安全隐患。
技术实现要素:
本发明的目的在于提供一种高效、智能的全自动竹条上料装置。
本发明的目的通过如下技术方案实现:一种全自动竹条上料装置,它包括进料机构、抓料机构以及抽拉机构;所述进料机构包括用于堆叠竹条的进料框;所述抓料机构包括用于夹持竹条左右侧边的抓取部、驱动抓取部竖向位移的升降组件以及架设在进料框上方且用于固定升降组件的抓料座;
所述抽拉机构包括滑动座、设于滑动座上的夹持部a以及驱动滑动座在抓料机构和刨切机进口侧之间横向移动的抽拉驱动组件;所述滑动座的中部设有容竹条前端穿过的的输送孔,所述夹持部a设于输送孔处。
较之现有技术而言,本发明的优点在于:
1.本发明包括进料机构、抓料机构以及抽拉机构;抓料机构可自动抓取进料机构内竹条,并通过抽拉机构精确送入剖切机,上料过程无需人工参与,自动化程度高。
2.抽拉机构包括滑动座、设于滑动座上的夹持部a以及抽拉驱动组件;夹持部a包括两相对设置的夹持板a,夹持板a采用单向夹持设计,即滑动座向抓料机构移动时,竹条端部撑开两夹持板a;滑动座向刨切机进口侧移动时,两夹持板a夹紧固定在竹条的上下面;在滑动座在抓料机构和刨切机进口侧之间往复运动过程中,可实现竹条的单向抽拉。
3.抽拉机构上设有翻转组件,翻转组件包括转动盘以及用于驱动转动盘180°旋转的翻转驱动组件;翻转组件可根据视觉监测机构反馈数据选择是否执行翻转操作,当需要翻转时,电机控制转动盘旋转180度。
4.抽拉机构和刨切机进口侧之间设有定位机构,当全自动竹条上料装置与刨切机间距较远时,可通过定位机构先固定竹条前段,配合抽拉机构多次往复输送,实现竹条精确的长距离上料。
5.本发明可采用双工位结构,每个工位均包括抓料机构、抽拉机构以及定位机构,在其中一个工位抽拉上料的同时,另一工位在进料框内抓取竹条,两工位交替衔接,可极大提高上料速度。
附图说明
图1是本发明一种全自动竹条上料装置实施例的结构示意图。
图2是全自动竹条上料装置的立体结构示意图。
图3是图2的正视图。
图4是图3中a-a剖视图。
图5是抓料机构和抽拉机构的配合关系示意图。
图6是图5另一视角的结构示意图。
标号说明:1进料机构、2抓料机构、21抓取部、22升降组件、23抓料座、3抽拉机构、31滑动座、311输送孔、32夹持部a、321夹持板a、33抽拉驱动组件、34转动盘、341中心通孔、35翻转驱动组件、36轴承、4定位机构、41定位座、411入料孔、42夹持部b、421夹持板b、5移载机构、51x轴移载部、52y轴移载部、6视觉监测机构、7刨切机进口侧、8竹条。
具体实施方式
下面结合说明书附图和实施例对本发明内容进行详细说明:
如图1-6所示为本发明提供的一种全自动竹条上料装置的实施例示意图。
一种全自动竹条上料装置,它包括进料机构1、抓料机构2以及抽拉机构3;
所述进料机构1包括用于堆叠竹条的进料框;竹条水平置于进料框内,且其前端顶在进料框的前挡板上。
所述进料框的前侧向下倾斜,其上设有震动部。
所述抓料机构2包括用于夹持竹条左右侧边的抓取部21、驱动抓取部21竖向位移的升降组件22以及架设在进料框上方且用于固定升降组件22的抓料座23;
抓取部21为气动夹爪,气动夹爪的夹持宽度略小于竹条的宽度。
升降组件22包括竖向设置的导轨、滑动连接在导轨上的齿条、与齿条啮合的齿轮以及驱动齿轮转动的电机,抓取部21固定在齿条的下侧。
所述抓取部21的抓取位置在竹条的前段,且抓取位置与竹条前端部应预留一定长度,用于后续抽拉机构3的夹持固定。
所述抽拉机构3包括滑动座31、设于滑动座31上的夹持部a32以及驱动滑动座31在抓料机构2和刨切机进口侧之间横向移动的抽拉驱动组件33;所述滑动座31的中部设有容竹条前端穿过的的输送孔311,所述夹持部a32设于输送孔311处。
所述夹持部a32包括两相对设置的夹持板a321;各夹持板a321的外侧边铰接在滑动座31上,其铰接轴上设有弹性件,夹持板a321的内侧边通过弹性件驱动向内翻折;
滑动座31向抓料机构2移动时,竹条端部撑开两夹持板a321;滑动座31向刨切机进口侧移动时,两夹持板a321夹紧固定在竹条的上下面。
所述夹持板a321设于滑动座31的前侧面,并以输送孔311为中心呈上下对称分布。
所述抽拉机构3和刨切机进口侧之间设有定位机构4;
抽拉机构3可直接向刨切机送料,当全自动竹条上料装置与刨切机间距较远时,可通过定位机构4先固定竹条前段,配合抽拉机构3多次往复输送,实现竹条精确的长距离上料。
所述定位机构4包括定位座41以及夹持部b42,所述定位座41上设有与输送孔311对应的入料孔411,所述夹持部b42设于入料孔411处。
所述夹持部b42包括两相对设置的夹持板b421;各夹持板b421的外侧边铰接在定位座41上,其铰接轴上设有弹性件,夹持板b421的内侧边通过弹性件驱动向内翻折;
滑动座31向定位机构4移动时,竹条端部撑开两夹持板b421;滑动座31向抓料机构2移动时,两夹持板b421夹紧固定在竹条的上下面。
现有的人工上料过程,操作人员不仅需要将竹条精确插入刨切机进口侧,还要判断竹条正反面,并手动翻转。在上述实施例中,要解决上料翻面问题,需要在进料框内统一竹条的正反面朝向,本发明在另一实施例中设置了翻转组件,有效解决了翻面问题。
所述抽拉机构3还包括设于滑动座31上的翻转组件;
所述翻转组件包括转动盘34以及用于驱动转动盘180°旋转的翻转驱动组件35;
所述转动盘34通过轴承连接在滑动座31上,且转动盘34上设有与输送孔311对应的中心通孔341,所述夹持部a32设于转动盘34的中心通孔341处。
所述转动盘34为齿轮盘,所述翻转驱动组件35为与齿轮盘啮合的主动齿轮以及驱动主动齿轮转动的电机。
全自动竹条上料装置还包括驱动抓料机构2在进料框上方空间水平移动的移载机构5;
所述移载机构5包括驱动抓料机构2左右移动的x轴移载部51以及驱动抓料机构2前后移动的y轴移载部52。
本发明可采用双工位结构,每个工位均包括抓料机构2、抽拉机构3以及定位机构4,在其中一个工位抽拉上料的同时,另一工位在进料框内抓取竹条,并等待。
全自动竹条上料装置还包括视觉监测机构6,所述视觉监测机构6用于获取进料框内竹条的前段影像,通过计算识别定位竹条的精确位置,并判断竹条的正反面。
视觉监测机构6先定位竹条前端沿,然后以竹条前端沿为起始点,识别竹条前段的轮廓,判断竹条位置,最后将信息发送至主控端,驱动移载机构5和抓料机构2运行;同时视觉监测机构6可识别竹条前段的颜色判断竹条的正反面,并将信息发送至主控端,驱动翻转组件运行。
为了提高视觉监测机构6的识别精度,可在竹筒剖切前对竹筒前后端部进行喷漆处理(黑色),剖切后的竹条端部会留有黑色漆面,便于视觉监测机构6的快速精确定位。
全自动竹条上料装置的工作过程如下:
1.将竹条堆叠在进料框内,各竹条水平放置,其前端顶在进料框的前挡板上。
2.视觉监测机构6先定位竹条的前端沿,以竹条前端沿为起始点,识别竹条的前段轮廓,进而精确定位竹条所在位置,并将信息发送至主控端。
3.移载机构5根据视觉监测机构6的信息驱动抓料机构2移动至定位的竹条正上方。
4.升降组件22驱动抓取部21下降,当抓取部21压到竹条时,其抓臂夹持竹条的左右侧边,升降组件22驱动抓取部21上升至抽拉机构3的水平高度。
5.抽拉驱动组件33驱动滑动座31向抓料机构2移动,抓取部21上的竹条前端部依次穿过滑动座31的输送孔311以及转动盘34的中心通孔341到达夹持部a32,撑开两夹持板a321后继续移动一段距离,滑动座31停止后,两夹持板a321夹紧固定在竹条的上下面,抓取部21复位松开。
6.翻转组件根据视觉监测机构6识别的数据选择是否执行翻转操作,当需要翻转时,电机控制转动盘34旋转180度。
7.抽拉驱动组件33驱动滑动座31向定位机构4移动,滑动座31上的两夹持板a321夹紧固定在竹条的上下面,带动竹条向定位机构4移动。
8.接近定位机构4时,竹条前端部先穿过定位座41上的入料孔411,撑开两夹持板b421后滑动座31继续移动一段距离,滑动座31停止后,两夹持板b421夹紧固定在竹条的上下面。
9.滑动座31接着在抓料机构2和定位机构4之间往复位移,直至竹条逐渐伸长进入刨切机进口侧7。
起点商标作为专业知识产权交易平台,可以帮助大家解决很多问题,如果大家想要了解更多知产交易信息请点击 【在线咨询】或添加微信 【19522093243】与客服一对一沟通,为大家解决相关问题。
此文章来源于网络,如有侵权,请联系删除


