一种双支鼻梁条的制作方法



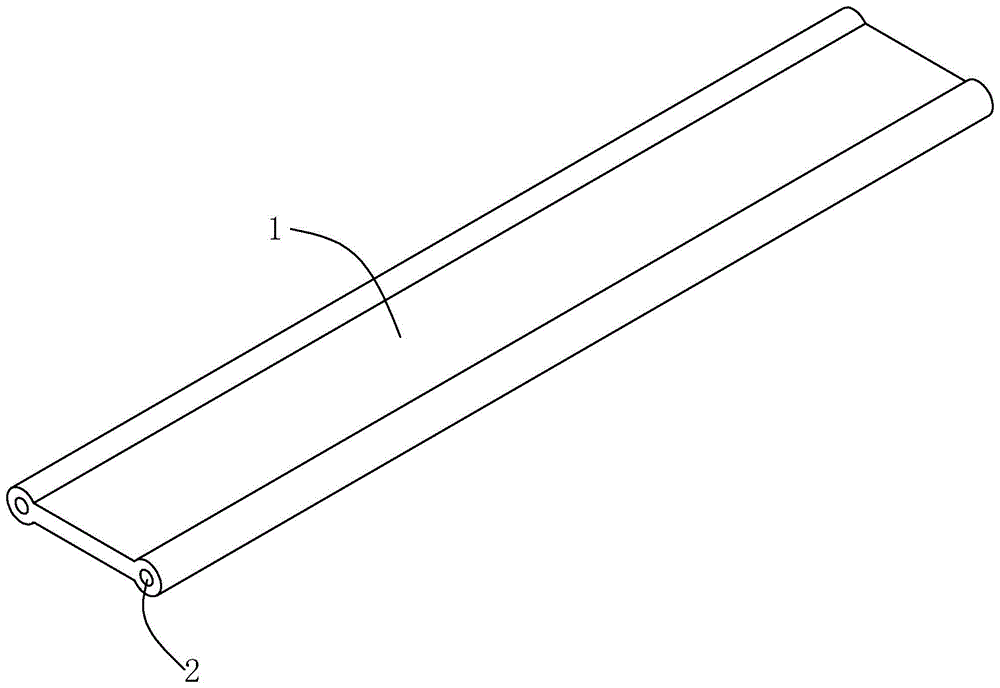
本实用新型涉及口罩生产技术领域,尤其是涉及一种双支鼻梁条。
背景技术:
鼻梁条是口罩里面的一根细胶条,起着将口罩固定在鼻梁上的作用,其能够随外力作用而弯曲变形,失去外力作用不回弹,从而良好的适配于使用者的鼻梁;目前的鼻梁条通常会在细胶条内设置定型条,用于使受力变形后的鼻梁条保持已有形状,主要包括单支鼻梁条与双支鼻梁条等。其中,双支鼻梁条相比单支鼻梁条,具体更好的韧性,能够良好的保持形变后的形状,常用于防尘、医用和n95等口罩中。
参照图1和图2,现有技术中的双支鼻梁条包括鼻梁条本体1和两根定型条2,其中,两根定型条2分别位于鼻梁条本体1宽度方向的两侧,并被鼻梁条本体1完全包覆在内;利用两根定型条2对鼻梁条本体1进行定型固定,使鼻梁条本体1能够保持形变后的形状。
上述中的现有技术方案存在以下缺陷:鼻梁条本体1将定型条2包覆后,在鼻梁条本体1厚度方向的两个表面均会存在包覆定型条2留下的鼓包,而鼻梁条本体1的一个表面朝向于使用者的鼻梁,使用者佩戴口罩时,可能因鼓包的存在而降低口罩与使用者鼻梁的贴合紧密性,影响到口罩的实际防护效果。
技术实现要素:
针对现有技术存在的不足,本实用新型的目的之一是提供一种双支鼻梁条,该双支鼻梁条可提升口罩与使用者鼻梁的贴合紧密性,保持口罩佩戴时的良好防护效果。
本实用新型的上述技术目的是通过以下技术方案得以实现的:一种双支鼻梁条,包括鼻梁条本体和两根定型条,所述鼻梁条本体呈长条状,且所述鼻梁条本体厚度方向的一侧为平面;所述鼻梁条本体宽度方向的两端均沿鼻梁条本体的长度方向设有通孔,两根所述定型条分别设于两个通孔内。
通过采用上述技术方案,鼻梁条本体宽度方向的一侧为平面状,相对于现有技术中鼻梁条本体宽度方向两侧均有鼓包的情况,可提升口罩与使用者鼻梁的贴合紧密性,从而保持口罩佩戴时的良好防护效果。
优选的,所述鼻梁条本体包括下包覆层与上包覆层,所述下包覆层远离上包覆层的表面为平面,所述上包覆层与下包覆层热熔连接,两个所述通孔形成于上包覆层与下包覆层的连接面,所述通孔的内壁与定型条的外壁相粘合。
通过采用上述技术方案,上包覆层与下包覆层热熔连接,连接面处形成的通孔将定型条包覆粘接,使得鼻梁条本体与定型条之间的连接稳定且紧密,同时,利用下包覆层远离上包覆层的表面呈平面,使得上包覆层与下包覆层热熔形成的鼻梁条本体的下表面呈平面。
优选的,所述上包覆层包括第一包膜、第二包膜和连接膜,所述第一包膜与下包覆层形成一个通孔,所述第二包膜与下包覆层形成另一个通孔;所述连接膜的一侧连接于第一包膜,另一侧连接于第二包膜;所述第一包膜与下包覆层相背离两侧的最远间距大于连接膜与下包覆层相背离两侧的最远间距,所述第二包膜与下包覆层相背离两侧的最远间距大于连接膜与下包覆层相背离两侧的最远间距。
通过采用上述技术方案,第一包膜、第二包膜均与下包覆层形成包覆定型条的通孔,且鼻梁条本体在第一包膜、第二包膜两处的厚度要大于连接膜处的厚度,使第一包膜、第二包膜能够对定型条形成良好的包覆作用,增加鼻梁条本体在第一包膜、第二包膜两处位置的耐磨性,减少定型条外露的情况。
优选的,所述第一包膜的表面为圆弧面。
通过采用上述技术方案,佩戴装有鼻梁条本体的口罩时,鼻梁条本体为平面的一侧朝向使用者的鼻梁,另一侧供使用者手动捏压,以实现鼻梁条本体与使用者鼻梁的适配;第一包膜位于鼻梁条本体远离使用者鼻梁的一侧,令第一包膜的表面为圆弧面,让使用者手动捏压鼻梁条本体的过程更加舒适,同时,设置为圆弧面也相对能够减少第一包膜处的材料使用量,起到节约材料的效果。
优选的,所述第二包膜的表面为圆弧面。
通过采用上述技术方案,第二包膜位于鼻梁条本体远离使用者鼻梁的一侧,令第二包膜的表面为圆弧面,让使用者手动捏压鼻梁条本体的过程更加舒适,同时,设置为圆弧面也相对能够减少第二包膜处的材料使用量,起到节约材料的效果。
优选的,所述定型条为镀锌铁丝,所述镀锌铁丝的横截面为圆形,且所述镀锌铁丝的线径为0.45-1.2mm。
通过采用上述技术方案,镀锌铁丝具有良好的韧性与弹性,便于使用者施力弯折;同时,将镀锌铁丝线径设置为0.45-1.2mm,线径合适且可稳定保持受力变形后的已有形状。
优选的,所述上包覆层与下包覆层均为聚烯烃树脂层。
通过采用上述技术方案,上包覆层与下包覆层均为聚烯烃树脂层,使上包覆层与下包覆层热熔形成的鼻梁条本体也能具有受力弯曲且不回弹的性能,使得鼻梁条本体保持受力变形后的已有形状的能力更优良。
优选的,所述第一包膜与下包覆层相背离两侧之间最大间距、第二包膜与下包覆层相背离两侧之间最大间距均为定型条线径的1.5-1.7倍。
通过采用上述技术方案,鼻梁条本体在第一包膜与第二包膜处的厚度为定型条线径的1.5-1.7倍,使鼻梁条本体对定型条形成良好的包覆作用,保持鼻梁条本体在第一包膜、第二包膜两处位置良好的耐磨性,减少定型条外露的情况。
综上所述,本实用新型包括以下至少一种有益技术效果:
1、鼻梁条本体朝向使用鼻梁的一侧为平面状,可提升口罩与使用者鼻梁的贴合紧密性,从而保持口罩佩戴时的良好防护效果;
2、第一包膜与第二包膜均位于鼻梁条本体远离使用者鼻梁的一侧,令第一包膜与第二包膜的表面为圆弧面,让使用者手动捏压鼻梁条本体的过程更加舒适;
3、鼻梁条本体在第一包膜与第二包膜处的厚度为定型条线径的1.5-1.7倍,使鼻梁条本体对定型条形成良好的包覆作用,保持鼻梁条本体在第一包膜、第二包膜两处位置良好的耐磨性,减少定型条外露的情况。
附图说明
图1是本实用新型背景技术中所指出的双支鼻梁条的整体结构示意图。
图2是本实用新型背景技术中所指出的双支鼻梁条的纵向截面示意图。
图3是本实用新型实施例的整体结构示意图。
图4是本实用新型实施例的纵向截面示意图。
附图标记:1、鼻梁条本体;1a、通孔;11、上包覆层;11a、第一包膜;11b、第二包膜;11c、连接膜;12、下包覆层;2、定型条;2a、镀锌铁丝。
具体实施方式
以下结合附图对本发明作进一步详细说明。
参照图3和图4,为本实用新型公开的一种双支鼻梁条,包括鼻梁条本体1和两根定型条2,其中,鼻梁条本体1呈长条状,具体的,鼻梁条本体1包括下包覆层12与上包覆层11,上包覆层11与下包覆层12均为聚烯烃树脂层,且上包覆层11与下包覆层12热熔粘接,形成一体式的鼻梁条本体1。
参照图4,下包覆层12远离上包覆层11的一侧为平面状,以使鼻梁条本体1厚度方向的一侧为平面。上包覆层11包括连接膜11c、第一包膜11a和第二包膜11b,其中,连接膜11c远离下包覆层12的一侧为平面,第一包膜11a与第二包膜11b分别位于连接膜11c宽度方向的两侧,且第一包膜11a、第二包膜11b与连接膜11c为一体热熔成型。
参照图4,第一包膜11a与第二包膜11b的形状与大小均相同,且第一包膜11a与第二包膜11b的表面均为圆弧面;同时,第一包膜11a、第二包膜11b均与下包覆层12的结合面形成有一个通孔1a,两个通孔1a沿鼻梁条本体1的长度方向设置。
参照图4,两根定型条2均为镀锌铁丝2a,两根镀锌铁丝2a分别位于两个通孔1a内,且在上包覆层11与下包覆层12热熔粘接的过程中,镀锌铁丝2a的外壁与通孔1a的内壁相粘接;具体的,镀锌铁丝2a的截面呈圆形,且镀锌铁丝2a的线径a为0.45-1.2mm,本实施例中,取镀锌铁丝2a的线径a为0.6mm,线径合适且可稳定保持受力变形后的已有形状。此外,第一包膜11a与下包覆层12相背离两侧的最远间距b、第二包膜11b与下包覆层12相背离两侧的最远间距c均大于连接膜11c与下包覆层12相背离两侧的最远间距d;并且,间距b、间距c均为定型条2线径a的1.5-1.7倍,具体的,可取倍数值为4/3,而本实施例中第一包膜11a与第二包膜11b形状与大小均相同,即使得b=c=0.8mm。能够使第一包膜11a、第二包膜11b对定型条2形成良好的包覆作用,减少定型条2外露的情况。
本实施例的实施原理为:上包覆层11与下包覆层12热熔粘接形成鼻梁条本体1,利用下包覆层12远离上包覆层11一侧为平面,使得鼻梁条本体1厚度方向的一侧为平面,便于形成与使用者鼻梁处相贴合的形状;上包覆层11中的第一包膜11a、第二包膜11b均与下包覆层12形成将镀锌铁丝2a包覆粘接的通孔1a,使鼻梁条本体1与定型条2之间的连接稳定且紧密。同时,利用镀锌铁丝2a作为鼻梁条本体1宽度方向两侧的定型条2,使鼻梁条本体1能够稳定维持形变后的形状。
本具体实施方式的实施例均为本实用新型的较佳实施例,并非依此限制本实用新型的保护范围,故:凡依本实用新型的结构、形状、原理所做的等效变化,均应涵盖于本实用新型的保护范围之内。
起点商标作为专业知识产权交易平台,可以帮助大家解决很多问题,如果大家想要了解更多知产交易信息请点击 【在线咨询】或添加微信 【19522093243】与客服一对一沟通,为大家解决相关问题。
此文章来源于网络,如有侵权,请联系删除


