一种全塑鼻梁条的制作方法



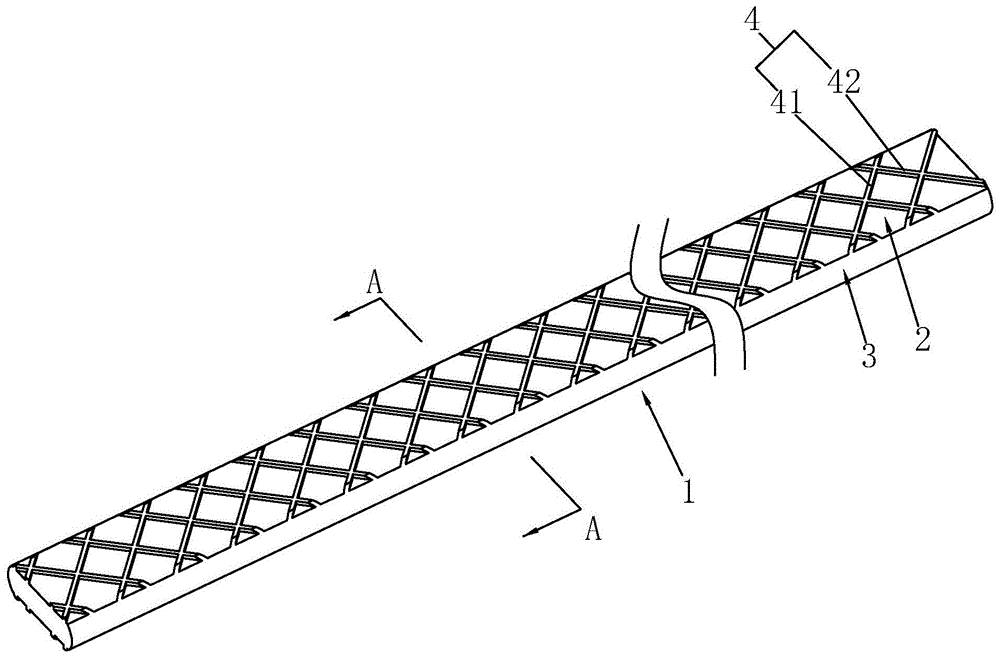
本实用新型涉及鼻梁条技术领域,尤其是涉及一种全塑鼻梁条。
背景技术:
鼻梁条是用于口罩中的一根细胶条,鼻梁条通常呈条形扁带状,鼻梁条起到将口罩固定贴合于鼻梁上的效果。
目前,市场上常用到的一种鼻梁条为塑包镀锌鼻梁条,塑包镀锌鼻梁条是一种在塑料外壳内部包裹有镀锌条的一种鼻梁条,塑包镀锌鼻梁条可像金属丝一样具有随外力作用而弯曲变形,同时当塑包镀锌鼻梁条失去外力后不易回弹,得以保持已有形状不变的优异性能。
然而,塑包镀锌鼻梁条的加工生产工艺步骤较为复杂,而且在存放原材料时需要将镀锌条材料以及塑料材料分开储存,仓储成本较高,同时,由于塑包镀锌鼻梁条由两种材料组成,因此当需要对鼻梁条进行回收时,往往需要对两者进行分离收集,步骤繁琐,不便于鼻梁条的回收利用,并且,塑包镀锌鼻梁条在使用过程中容易造成塑料层破损,从而使得镀锌条的端部戳伤人体,使用不够安全。
技术实现要素:
本实用新型的目的是提供一种全塑鼻梁条,其具有一体成型的特点,起到减少仓储成本、回收困难以及提升使用时的安全性的效果。
为实现上述目的,本实用新型提供以下技术方案:
一种全塑鼻梁条,包括呈长条扁带状的塑料条本体,所述塑料条本体的表面处设置有凹凸纹路。
通过采用上述技术方案,塑料条本体通过一体成型的方式省去了镀锌鼻梁条,减少了原材料的仓储成本;同时在对塑料条本体进行回收时,只需将塑料条本体进行集中收集即可实现回收,省去了分离步骤,方便快捷;并且塑料条本体具有较好的柔软性,不易对人体造成损伤,提高了产品使用时的安全性;塑料条本体通常在安装时包覆于无纺布层以及棉布层之间,塑料条本体上的凹凸纹路增大了塑料条本体的表面粗糙度,从而使得塑料条本体与无纺布以及棉布之间的摩擦力得到增大,进而使得塑料条本体安装于口罩内时不易产生位置的偏移。
本实用新型进一步设置为:所述塑料条本体的宽度a为2.8mm至5.0mm,所述塑料条本体的厚度b为0.7mm至1.3mm。
通过采用上述技术方案,当塑料条本体的宽度a小于2.8mm时或者当塑料条本体的厚度b小于0.7mm时,塑料条本体的强度较弱,容易造成塑料条本体1断裂以及塑形状态不稳的情况出现,当塑料条本体的宽度a大于5.0mm或塑料条本体的厚度b大于1.3mm时,则会浪费较多的制造材料。
本实用新型进一步设置为:所述凹凸纹路位于所述塑料条本体相背的两侧表面上。
通过采用上述技术方案,塑料条本体可通过其相背的两侧表面分别与口罩的无纺布层以及棉布层抵接,如此进一步提升了鼻梁条防偏移效果。
本实用新型进一步设置为:所述凹凸纹路包括若干根第一凸棱以及第二凸棱,若干根所述第一凸棱相互平行,且若干根所述第一凸棱沿着所述塑料条本体的长度方向等间距设置,若干根所述第二凸棱相互平行,且所述第二凸棱沿着所述塑料条本体的长度方向呈等间距设置,所述第一凸棱以及第二凸棱之间相互交叉形成网格状。
通过采用上述技术方案,第一凸棱与第二凸棱之间呈交叉状相交设置使得第一凸棱与第二凸棱之间形成网格状凹凸纹路,如此起到增大塑料条本体的表面粗糙度的作用。
本实用新型进一步设置为:所述塑料条本体上设置有锯齿凸台,所述锯齿凸台沿着所述塑料条本体的长度方向设置。
通过采用上述技术方案,锯齿凸台能通过其锯齿状的结构将塑料条本体钩持于口罩上,使得锯齿状本体安装于口罩中时不易产生偏移。
本实用新型进一步设置为:所述凹凸纹路包括凹陷设置于所述塑料条本体上的容置槽。
通过采用上述技术方案,容置槽除了可以增加塑料条本体表面的摩擦外,通过设置容置槽,塑料条本体可通过容置槽对胶水进行容置,如此使得塑料条本体除了包裹于口罩内,还可以粘贴于无纺布层外,增加了塑料条本体的适用范围,满足了口罩适用需求的多样性。
本实用新型进一步设置为:所述容置槽的开口呈圆形设置,所述容置槽在所述塑料条本体上呈阵列分布。
通过采用上述技术方案,阵列分布于塑料条本体上的圆孔状容纳槽可均匀地对涂抹于塑料条本体上的胶水进行容置。
本实用新型进一步设置为:所述容置槽的开口呈矩形状设置,所述容置槽沿着所述塑料条本体的长度方向呈等间距布置。
通过采用上述技术方案,等间距布置于塑料条本体上的容置槽可沿着塑料条本体的长度方向对胶水进行均匀容置。
综上所述,本实用新型的有益技术效果为:
1、塑料条本体通过一体成型的方式减少了原材料的仓储成本;同时在对塑料条本体进行回收省去了分离步骤,方便快捷地对塑料条本体进行回收;并且塑料条本体具有较好的柔软性,不易对人体造成损伤,提高了产品使用时的安全性;
2、凹凸纹路起到当塑料条本体安装于口罩中时防止产生偏移的效果;
3、塑料条本体通过设置容置槽,可实现将塑料条稳固地粘合固定于口罩外,当需要对塑料条本体进行回收时,将塑料条本体撕开即可实现拆卸,过程方便快捷。
附图说明
图1是本实用新型实施例1中的结构示意图;
图2是图1中a-a方向的剖视图;
图3是本实用新型实施例2中的结构示意图;
图4是本实用新型实施例3中的结构示意图;
图5是本实用新型实施例4中的结构示意图。
图中,1、塑料条本体;2、表面;3、侧边;4、凹凸纹路;41、第一凸棱;42、第二凸棱;5、锯齿凸台;6、容置槽。
具体实施方式
实施例1:参照图1,为本实用新型公开的一种全塑鼻梁条,包括呈长条扁带状的塑料条本体1,塑料条本体1采用聚烯烃树脂一体成型,其中,塑料条本体1包括相互平行且相互背对的两侧表面2,塑料条本体1还包括位于塑料条本体1上两侧表面2之间的呈圆弧过渡状的侧边3,塑料条本体1上相背的两侧表面2处均一体成型有凹凸纹路4,凹凸纹路4包括若干根第一凸棱41以及第二凸棱42,若干根第一凸棱41之间相互平行,且若干根第一凸棱41沿着塑料条本体1的长度方向等间距设置,若干根第二凸棱42之间相互平行,且第二凸棱42沿着塑料条本体1的长度方向呈等间距设置,第一凸棱41以及第二凸棱42之间相互交叉形成网格状,网格状的凹凸纹路4起到增大塑料条本体1的表面2粗糙度的作用,塑料条本体1在安装于口罩上时,塑料本体1包覆于口罩的无纺布层以及棉布层之间,塑料条本体1上的凹凸纹路4增大了塑料条本体1的表面2粗糙度,从而使得塑料条本体1与无纺布以及棉布之间的摩擦力得到增大,进而使得塑料条本体1安装于口罩内时不易产生位置的偏移。
参照图2,在本实施例中,塑料条本体1的宽度a为2.8mm至5.0mm,塑料条本体1的厚度b为0.7mm至1.3mm,当塑料条本体1的宽度a小于2.8mm时或者当塑料条本体1的厚度b小于0.7mm时,塑料条本体1的强度较弱,容易造成塑料条本体1断裂以及塑形状态不稳的情况出现,当塑料条本体1的宽度a大于5.0mm或塑料条本体1的厚度b大于1.3mm时,则会浪费较多的制造材料。比如,塑料条本体1的宽度a可以是2.8mm、3.0mm、3.2mm、3.5mm、3.8mm、4.0mm及5.0mm,塑料条本体1的厚度可以是0.7mm、0.8mm、0.9mm、1.0mm、1.1mm、1.2mm及1.3mm,在本实施例中,塑料条本体1的宽度a优选为4.0mm,塑料条本体1的厚度b优选为0.9mm。
实施例2:参照图3,本实施例与实施例1的区别点在于,塑料条本体1上一体有锯齿凸台5,锯齿凸台5位于塑料条本体1的两侧侧边3处,且锯齿凸台5沿着塑料条本体1的长度方向设置,锯齿凸台5能通过其锯齿状的结构将塑料条本体1钩持于口罩上,使得塑料条本体1安装于口罩中时不易产生偏移。
实施例3:参照图4,为本实用新型公开的一种全塑鼻梁条,包括呈长条扁带状的塑料条本体1,塑料条本体1采用聚烯烃树脂一体成型,其中,塑料条本体1包括相互平行且相互背对的两侧表面2,塑料条本体1上相背的两侧表面2处均一体成型有凹凸纹路4,凹凸纹路4包括于塑料条本体1的表面2上由外向内凹陷设置的若干个容置槽6,容置槽6的开口呈圆形设置,容置槽6在塑料条本体1上呈阵列分布,且容置槽6排满于塑料条本体1的表面2上,本实施例中的塑料条本体1可包裹安装于口罩内,同时也可通过胶水粘贴于无纺布层外,当塑料条本体1通过胶水粘贴于无纺布层外时,通过设置容置槽6,使得胶水在涂抹于塑料条本体1上时可留存容纳于塑料条本体1的容置槽6内,如此使得塑料条本体1在贴合时能容置更多的胶水,如此使得塑料条本体1的粘合效果更好,同时,当需要对塑料条本体1进行回收时,由于塑料条本体1粘贴在口罩外部,如此便于将塑料条本体1直接从口罩中撕取下来,从而便于塑料条本体1的回收利用。
实施例4:参照图5,本实施例与实施例3的区别在于容置槽6的开口呈矩形状设置,容置槽6沿着塑料条本体1的长度方向呈等间距布置,容置槽6将塑料条本体1上的表面2处排满。
上述实施例仅仅是对本实用新型的解释,其并不是对本实用新型的限制,本领域技术人员在阅读完本说明书后可以根据需要对本实施例做出没有创造性贡献的修改,但只要在本实用新型的权利要求范围内都受到专利法的保护。
起点商标作为专业知识产权交易平台,可以帮助大家解决很多问题,如果大家想要了解更多知产交易信息请点击 【在线咨询】或添加微信 【19522093243】与客服一对一沟通,为大家解决相关问题。
此文章来源于网络,如有侵权,请联系删除


