一种垃圾焚烧飞灰资源化处理方法及系统与流程



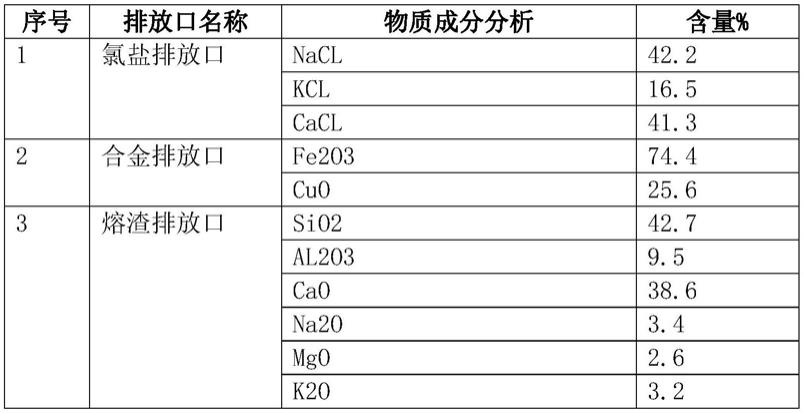
[0001]
本发明属于飞灰资源化技术领域,涉及一种垃圾焚烧飞灰资源化的系统及方法。
背景技术:
[0002]
垃圾焚烧锅炉在运行过程中会产生大量的飞灰,约占焚烧量的3%-5%。由于飞灰中含有大量的重金属及二噁英,对环境造成严重的污染。现有的飞灰处理手段为“固化+填埋”。但是,填埋会占用大量的土地资源,并且渗滤液也可能会污染环境。
[0003]
目前,通过等离子技术将飞灰熔融处理后,可有效分解飞灰中的二噁英,重金属被固化在玻璃体中,进而用做建筑材料等进行资源化处理。但是,由于飞灰中往往富含氯盐,主要以氯化钠、氯化钾、氯化钙形式存在。在资源化前,必须对氯盐进行处理。常规的方式是采取水洗飞灰,此方法的缺点会产生富含重金属的废水,会产生二次危废;再者,等离子处理技术能耗高,无论采用非转移弧还是转移弧等离子技术,采用清洁的电能处理几乎无热值的飞灰,对能源都是巨大的消耗。
技术实现要素:
[0004]
针对现有技术的缺陷或不足,本发明的目的是提供一种垃圾焚烧飞灰资源化的方法及系统。
[0005]
为此,本发明一种垃圾焚烧飞灰资源化方法,所提供的方法包括:
[0006]
将飞灰颗粒从炉体上部区域的进料口送进炉内后,飞灰颗粒降至炉内中下部区域被纯氧燃烧器燃烧熔融,熔融过程中产生的烟气上升至温度为500~700℃炉内上部区域后排出;熔融液体下沉至炉内底部区域过程中形成由上至下的液态氯盐层、熔渣层和液态合金层;
[0007]
之后对所述液态氯盐层、熔渣层和液态合金层进行分层回收。
[0008]
可选的,通过调整飞灰颗粒的物料高度,使炉内上部区域的温度维持在500~700℃。
[0009]
优选的,熔融区温度维持在1500~1600℃。
[0010]
进一步,飞灰颗粒熔融后酸度系数为0.8-1.2。
[0011]
可选的,所述飞灰颗粒的制备配方由淀粉和石灰石,或者淀粉和石英砂配置而成。
[0012]
同时,本发明还提供了一种垃圾焚烧飞灰资源化处理系统。
[0013]
本发明所提供的系统包括熔融炉,所述熔融炉设有耐火保温材料,其特征在于,所述熔融炉内由上至下依次设有气相区、固相区、氯盐熔融区、熔渣区、合金熔融区;所述气相区设有进料口和排烟口;所述固相区与氯盐熔融区之间安装有纯氧燃烧器;所述氯盐熔融区设有液态氯盐排放口;所述熔渣区设有熔渣排放口;所述合金熔融区设有液态合金排放口。
[0014]
优选的,所述气相区设于至少两个进料口,且至少两个进料口沿炉体周向均匀分布;所述固相区与氯盐熔融区之间安装有至少两个纯氧燃烧器,且至少两个纯氧燃烧器沿
炉体周向均匀分布;所述进料口与炉壁的角度在30~50
°
;纯氧燃烧器与炉壁的角度在30~50
°
。
[0015]
可选的,所述气相区的炉体侧壁中安装有热电偶;所述熔渣区的炉体侧壁中安装有热电偶。
[0016]
进一步,系统还包括造粒设备和烟气处理系统,所述造粒设备与所述进料口连接;所述烟气处理系统与所述排烟口连接。
[0017]
进一步,系统还包括制棉设备,该制棉设备与所述熔渣排放口连接。
[0018]
本发明与现有技术相比,本发明的有益效果是:
[0019]
本发明采用纯氧燃烧器,燃烧后三原子气体比例增大,辐射能力增强;烟气排放量小,可降低后续烟气处理系统的设备投资;并且,经本发明处理后,飞灰熔融后形成氯盐、合金、熔渣层,可对各层分进行回收。进一步,其中氯盐可作为融雪剂,合金可作为炼铁的半成品,熔渣用来制作矿渣棉或岩棉进行资源化利用。
[0020]
采用纯氧燃烧技术将飞灰高温熔融,降低了能耗;飞灰不需要进行水洗预处理,避免了废水的产生;飞灰在入炉前和添加剂(生石灰、石英砂、粘结剂等)进行混合造粒,满足成纤的成分要求,不需要在熔融炉外设置调质炉;飞灰在处理过程中,在不同的位置分层排放出氯盐、合金、熔渣。氯盐可作为融雪剂,合金可作为炼铁的半成品,熔渣用来制作岩棉进行资源化利用。
附图说明
[0021]
图1为本发明的垃圾焚烧飞灰资源化处理系统结构参考示意图;
[0022]
图2为炉体侧壁热偶的安装示意图。
具体实施方式
[0023]
本文中的“上”、“中”、“下”等方位性词语均指附图中所示结构的相应方位。
[0024]
除非另有说明,本文中的术语均按照本领域常规理解或采用本领域的常规、已有和可实现本发明技术目的的手段实现。
[0025]
本发明所述的飞灰颗粒为由飞灰加相关辅料、助剂等经过造粒工艺制程的颗粒,例如,飞灰、生石灰、石英砂和粘结剂进行混合造粒,本领域已有的飞灰造粒技术和相应造粒设备均适用于本发明,并且从理论上讲,围绕飞灰造粒为技术目的的技术改进同样适用于本发明。本发明的垃圾焚烧飞灰资源化方法中可包括造粒工艺或直接对已经成型的飞灰颗粒进行处理。另外,本发明对飞灰颗粒大小无严格要求,现有公开的飞灰颗粒大小均适用于本发明,如30~50mm。
[0026]
纯氧燃烧技术由于其氧气浓度高,燃烧温度高,在与天然气当量燃烧时,燃烧温度可达2000℃以上。本发明优选的方案中控制熔融区温度维持在1500~1600℃。具体可选择通过调整纯氧燃烧器的天然气量,使熔融区温度维持在1500~1600℃。
[0027]
更进一步的方案中,在制备飞灰颗粒时,通过调整飞灰颗粒成分使得飞灰颗粒熔融后酸度系数mk=1.2满足成纤的成分要求,不需要在熔融炉外设置调质炉。一种可选的飞灰颗粒配方是,在飞灰中加入生石灰和淀粉或者石英砂和淀粉进行混合造粒。
[0028]
本发明所述炉体为化工、煤炭领域的立式熔融炉,此类炉子的内壁或外壁设有耐
火保温材料,根据实际工艺要求,炉内划分为相应功能区或工艺区,炉身上相应的设有功能性部件或部位;与现有技术不同的是,本发明的炉体内由上至下依次设有气相区、固相区、氯盐熔融区、熔渣区和合金熔融区;即炉体内上部区域为气相区,中部区域为固相区,下部区域为氯盐熔融区、熔渣区和合金熔融区,并且根据工艺要求,其中气相区设有进料口和排烟口;固相区与氯盐熔融区之间(即中下部区域)安装有纯氧燃烧器;氯盐熔融区设有液态氯盐排放口;熔渣区设有熔渣排放口;合金熔融区设有液态合金排放口。
[0029]
优选的方案中,在气相区a沿炉壁均匀设置至少两个进料口,保证进料的均匀性。更进一步优选的方案是,进料口与炉壁的角度在30~50
°
。
[0030]
优选的方案中,在固相区b均匀设置至少两个纯氧燃烧器,保证飞灰熔融固相和液相区温度的均匀性。更进一步优选的方案是,纯氧燃烧器与炉壁的角度在30~50
°
。
[0031]
可选的方案是,通过在炉体上部区域的炉壁内或气相区的炉壁内设置热电偶,或/和通过调整飞灰颗粒的物料高度,使炉内气相区a温度维持在500~700℃,防止飞灰中氯盐高温气化,同时,可有效降低排烟热损失,降低能耗。
[0032]
为更好实现炉内温度控制,气相区a和熔渣区c的炉壁内均设置有热电偶。示例:热电偶安装于相应区的炉体耐火材料构筑的盲孔中。
[0033]
本发明所述的烟气处理系统和制棉设备均采用现有相关设备或可实现相关功能的设备。
[0034]
下面结合附图和具体实施方式对本发明进行详细说明。
[0035]
实施例1:
[0036]
该实施例的垃圾焚烧飞灰资源化的系统,如图1所示,具体为纯氧燃烧熔融炉1,纯氧燃烧熔融炉1由炉壁2、耐火材料3组成,炉内可分为气相区a、飞灰颗粒固相区b、氯盐熔融区c、熔渣区d、合金熔融区e;
[0037]
在气相区a沿炉壁均匀分布两个进料口4,保证进料的均匀性,进料口与炉壁的角度为40
°
;炉体顶部设有排烟口;
[0038]
在飞灰颗粒固相区b均匀分布两个纯氧燃烧器5,保证飞灰熔融固相和液相区温度的均匀性,纯氧燃烧器与炉壁的角度为40
°
;
[0039]
氯盐熔融区c、熔渣区d、合金熔融区e分别设置有氯盐排放口9,熔渣排放口11,合金排放口10。实现熔融物的分层回收;
[0040]
气相区a和熔渣区c的炉壁内均设置有热电偶6、7,如图2所示,热电偶6、7安装于耐火材料3构筑的盲孔之中。
[0041]
进一步的方案中,排烟口处连接有烟气处理系统。进料口出连接有飞灰造粒设备。
[0042]
更进一步的方案中,熔渣排放口11处连接有制棉设备离心机或喷嘴,以及集棉、固化、切边、包装系统。
[0043]
实施例2:
[0044]
采用实施例1的炉子对飞灰为例,该飞灰的物料成分分析如表1所示:
[0045]
表1
[0046]
组分质量分数%sio220.30al2o312.11
cao41.137fe2o30.898cuo0.256p2o50.349na2o5.11mgo1.84k2o3.70nacl6.70kcl2.25cacl25.35
[0047]
以1t表1中的飞灰为例,在入炉前添加300kg石灰石,80kg淀粉作为粘结剂进行造粒,造粒粒径30~50mm。
[0048]
实施例3:
[0049]
以1t表1中的飞灰为例,在入炉前添加320kg石英砂(纯度98%),100kg淀粉作为粘结剂进行造粒,造粒粒径30~50mm。该造粒配方可保证飞灰熔融后酸度系数mk=1.2,满足矿渣棉的成分要求。
[0050]
将此造粒后的物料从进料口4送入纯氧燃烧熔融炉内,通过控制固体物料的高度,使炉内气相区a温度维持在500~700℃,同时,通过调整纯氧燃烧器的天然气量,使熔融区温度维持在1500~1600℃。
[0051]
该实施例中氯盐排放口排放物、合金排放口排放物质、熔渣排放口排放物质的化学分析结果如表2所示。
[0052]
表2
[0053][0054]
其中:氯盐通过排放口9排出,合金通过排放口10排出。
[0055]
熔渣通过排放口11排出后,进入熔融炉下部布置的离心机,熔渣成纤后进入后续制棉设备,经过集棉、固化、切边、包装工序最终制成矿渣棉。
[0056]
经过除烟系统后,产生的500~700℃的烟气可通过降温、急冷、脱硝、脱酸,保证烟气达标排放。
[0057]
通过此方法,与等离子熔融飞灰相比较,处理1t飞灰,成本可降低30%以上。
[0058]
1t飞灰通过等离子熔融,需要耗电1200kw.h左右,按照一度电0.8元,合计960元/吨飞灰。通过纯氧燃烧,需要消耗天然气150方左右,按照工业用气4元/方,合计600元/吨飞灰。即降低处理成本37.5%/吨飞灰。
[0059]
实施例4:
[0060]
与实施例3不同的是,以1t表1中的飞灰为例,在入炉前添加101kg石英砂(纯度98%),100kg淀粉作为粘结剂进行造粒,造粒粒径30~50mm。该造粒配方可保证飞灰熔融后酸度系数mk=0.8。
起点商标作为专业知识产权交易平台,可以帮助大家解决很多问题,如果大家想要了解更多知产交易信息请点击 【在线咨询】或添加微信 【19522093243】与客服一对一沟通,为大家解决相关问题。
此文章来源于网络,如有侵权,请联系删除
相关标签: 垃圾焚烧



tips