一种绕发装置的制作方法



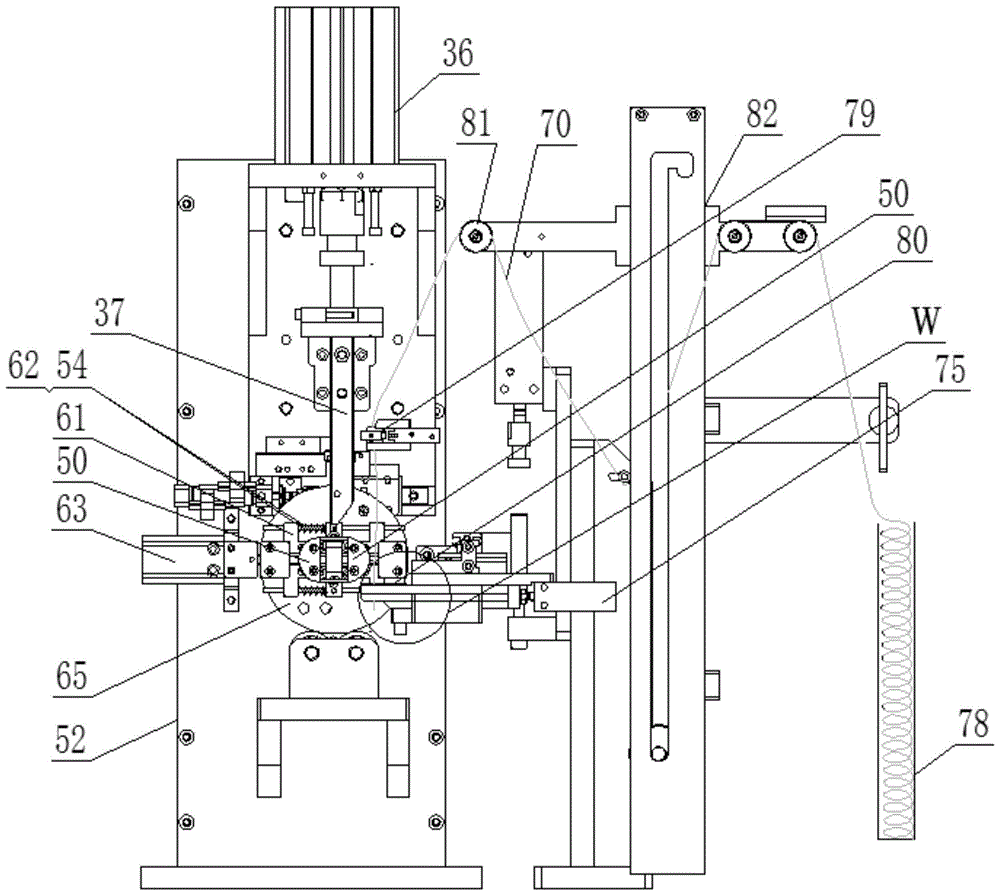
本发明涉及假发生产设备,具体涉及一种假发生产设备绕发装置。
背景技术:
发束(如玩具娃娃的马尾发束)生产过程中,需要采用绕发装置将发丝(一种塑料丝)绕制成发束圈,目前,主要是通过两种方式将发丝盘绕成发束圈,一是通过人工直接将盘绕发丝,二是通过人工先将发丝在绕线盘上盘绕几圈使其固定,然后通过电机驱动绕线盘旋转进行盘丝。然而,这两种操作方式都需要借助于手动配合来固定发丝端头,导致操作繁琐且发束圈的生产效率较低。更为重要地是,对于微型玩具娃娃的发束圈而言,由于单个发束圈所需发丝用量小,往往在绕线盘上盘绕几圈发丝并固定时发丝就已经超出所需用量,导致绕制的发束圈不符合要求以及材料浪费。
另外,采用现有方式将发丝盘绕成发束圈需要不停地通过操作者手臂拉动发丝和剪切发丝(拉发丝和剪切发丝的过程称之为发丝进料),由于发丝较软,剪断后如果不拉紧,线头就会回退,这样每次都需要操作者重新抓丝头并拉至绕线盘处,操作起来比较麻烦,且效率低下。
技术实现要素:
针对背景技术中存在的问题,本发明目的在于提供一种绕发装置。
为了实现上述目的,本发明采用如下技术方案。
一种绕发装置,包括绕发盘,绕发盘连接驱动系统,驱动系统用于驱动绕发盘转动,其特征在于:在绕发盘上设置可横向移动的丝头压紧件,丝头压紧件可随着绕发盘同步转动,当外力驱动丝头压紧件横向背离绕发盘后,丝头压紧件与绕发盘之间的空隙作为放置发丝端头的空间,外力撤销后通过丝头压紧件贴紧绕发盘以实现将发丝端头压紧在绕发盘上;当发丝端头被压紧在绕发盘上后,通过驱动系统驱动绕发盘旋转以实现将发丝在绕发盘上盘绕成发束圈。
]作为优选方案之一,丝头压紧件的活动杆从绕发盘内部横向穿过,在活动杆上套设有弹簧,弹簧一端通过绕发盘进行限位、另一端通过活动杆上的凸沿进行限位,外力撤销后,通过弹簧带动横向背离绕发盘的丝头压紧件复位。
]作为优选方案之二,丝头压紧件的活动杆位于绕发盘端侧,丝头压紧件设置在弹性机构上;弹性机构包括固定块四,固定块四侧方设置有活动块四,活动块四通过拉杆连接在固定块四上,在活动块四与固定块四之间的拉杆上套设有弹簧;丝头压紧件的活动杆连接在活动块四上,当外力驱动活动块四向固定块四靠近后,活动块四带动丝头压紧件横向背离绕发盘;当外力撤销后,弹簧驱动活动块四复位并带动丝头压紧件贴紧绕发盘。
]进一步地,在丝头压紧件的活动杆外侧设置有气缸九,初始状态下,气缸九的伸缩杆前端与丝头压紧件间隔开,当气缸九的伸缩杆伸长时,通过伸缩杆前端推动丝头压紧件横向前移。采用这样的结构巧妙地实现了气缸九与绕发盘的互不干涩,使得绕发过程完全不受气缸九影响,有利于顺利绕发。
]进一步地,在绕发盘环壁横向设置有丝头压槽,当发丝端头被压紧在绕发盘上后,丝头压紧件的压紧部刚好位于丝头压槽内。采用这样的结构有利于将绕发盘做得小型化,同时方便将绕制的发束圈卸出。
]作为优选,沿着绕发盘环壁设置有用于容纳发丝的线槽,丝头压槽与线槽呈相互交叉的结构。
]进一步地,所述绕发装置还包括捆发机构,捆发机构包括震动上料器,震动上料器上设置有输料轨道;在输料轨道末端斜上方设置有具有吸附功能的压料座,在压料座上方设置有气缸四,气缸四连接压料座并用于驱动压料座沿竖直方向往复运行;在压料座正下方设置有绕发盘,绕发盘上设置有弧形槽,弧形槽正对压料座;初始状态下,气缸四处于缩回状态,随着震动上料器的连续上料,金属捆钉逐渐移动至输料轨道末端后被吸附在压料座底端面;随后,气缸四伸长驱动压料座下移且当压料座底端面接触绕发盘后,在压料座的压力作用下和弧形槽壁面的导向作用下,金属捆钉发生弯折以实现将发束困住。
]进一步地,在输料轨道末端正对侧设置有临时载料件,在临时载料件左侧设置有气缸五,气缸五连接临时载料件并用于控制临时载料件沿水平方向往复运行;当金属捆钉逐渐移动至输料轨道末端后先转移至临时载料件上,气缸四伸长驱动压料座适当下移以将金属捆钉吸附在压料座底端面;在压料座上设置有气道,气道一端通向压料座底端面,气道另一端通过管路连接抽真空系统。
]进一步地,所述绕发装置还包括发丝进料机构,包括依序布置的:用于对发丝进行导向的导向装置,用于将发丝夹住并固定的夹固装置,以及用于将发丝固定并切断的夹切装置,夹切装置位于绕线机构的绕发盘侧方;其中,
夹固装置包括固定块一,固定块一上设置有气缸六,气缸六的伸缩杆前端设置有滑动块一,气缸六驱动滑动块一伸至极限位置后,滑动块一与固定块一之间的空间作为发丝的过路通道,气缸六驱动滑动块一回缩至极限位置后,滑动块一与固定块一相贴靠以实现将发丝夹紧;
夹切装置包括呈l形的固定块二,固定块二上设置有固定块三,固定块三底部设置有切割部,固定块二内角侧壁设置有滑动块,滑动块和切割部同时连接气缸七;气缸七伸至极限位置时,滑动块前端抵紧固定块二,并将发丝夹持在滑动块与固定块二之间,切割部的刃将发丝切断;气缸七回退后,滑动块与固定块二之间的缺口用于容纳发丝;
夹切装置整体设置在三维移动机构上,用于驱动夹切装置整体沿着三个相互垂直的方向移动,其目的是将发丝送至丝头压紧件与绕发盘之间的空隙处。
]作为优选,丝头压紧件的活动杆与压紧部相互垂直。
]本发明提供的绕发装置具有如下优点:
(1)进料阶段,一方面通过夹固装置将发丝夹住并固定,另一方面通过夹切装置将发丝固定并切断,无需操作者用手抓紧发丝并剪断,且在每次剪断发丝后能够防止发丝回拉,同时还能够防止丝头回退,如需下一次盘绕发丝,将夹切装置与夹固装置之间的发丝送至绕线盘上固定,省去了操作者反复抓丝头和拉动发丝的麻烦,使得发丝进料操作更为简单、高效;
(2)盘绕阶段,先通过外力(如气缸九)驱动丝头压紧件横向背离绕发盘,然后将发丝端头送至丝头压紧件与绕发盘之间的空隙处,随后立即撤销外力使得丝头压紧件在弹力的作用下复位,通过丝头压紧件贴紧绕发盘以实现将发丝端头压紧在绕发盘上;当发丝端头被压紧在绕发盘上后,通过驱动系统驱动绕发盘旋转以实现将发丝在绕发盘上盘绕成发束圈;由此种方式固定发丝端头并绕发,适用于制备大、中、小三种规格的发束圈,不仅解决了“在绕线盘上盘绕几圈发丝并固定时发丝就已经超出所需用量,导致绕制的发束圈不符合要求以及材料浪费”的技术问题,而且大幅提高了生产效率,可实现5~7秒/个发束圈的制备效率;
(3)捆发阶段,发束顺着弧形槽盘绕在绕发盘上,通过震动上料器将金属捆钉转移至输料轨道,随着震动上料器的连续上料,金属捆钉会在输料轨道上逐个紧挨排列并逐步前移,当金属捆钉逐渐移动至输料轨道末端后会进一步转移至临时载料件上,随后通过抽真空系统将金属捆钉吸附在压料座底端面,随后临时载料件在气缸五的作用下左移,为压料座下移让出通道,当气缸四伸长以驱动压料座下移且压料座底端面接触绕发盘后,在压料座的压力作用下和弧形槽壁面的导向作用下,金属捆钉被压弯(发生弯折),从而将发束困住;这不仅能够快速地进行捆发,而且捆发过程中几乎不需要人工手动操作,非常方便、高效,通常情况下可实现3-5秒/个的捆发效率;
(4)整个过程绝大多数工序可有机器自行完成,对人工操作的依赖程度小,可大幅减少企业人力成本。
附图说明
图1为实施例1中绕发装置主向示意图;
图2为实施例1中绕发装置左向示意图;
图3为实施例1中绕发装置的绕发盘所在部位主向示意图;
图4为实施例1中绕发装置的丝头压紧件示意图;
图5为实施例1中绕发装置的绕发盘所在部位俯向示意图;
图6为实施例1中发丝进料机构的夹固装置示意图一(非夹固状态);
图7为实施例1中发丝进料机构的夹固装置示意图二(夹固状态);
图8为实施例1中发丝进料机构的夹切装置示意图一(俯向,非夹切状态);
图9为实施例1中发丝进料机构的夹切装置示意图二(俯向,夹切状态);
图10为实施例1中发丝进料机构的夹切装置示意图三(仰视方向);
图11为图1中w部位的放大图。
图12为实施例1中金属捆钉弯折前后状态示意图,弯折后的状态也是捆发后的状态;
图13为实施例1中发束生产设备的捆发机构示意图一;
图14为实施例1中发束生产设备的捆发机构示意图二;
图15为实施例1中发束生产设备的捆发机构示意图三;
图16为实施例1中绕发盘的中心部件示意图;
图17为实施例2中绕发装置的绕发盘所在部位示意图一(盘绕发丝之前);
图18为实施例2中绕发装置的绕发盘所在部位示意图二(盘绕发丝之后)。
具体实施方式
下面结合附图和具体实施例对本发明作进一步说明,但以下实施例的说明只是用于帮助理解本发明的原理及其核心思想,并非对本发明保护范围的限定。应当指出,对于本技术领域的普通技术人员来说,在不脱离本发明原理的前提下,针对本发明进行的改进也落入本发明权利要求的保护范围内。
实施例1
请参见图1至图16。
一种绕发装置,包括绕发盘50,绕发盘50连接驱动系统,驱动系统用于驱动绕发盘50转动,具体是将绕发盘50设置在基盘65上,基盘65后侧设置有电机51作为驱动系统,电机51的输出轴连接基盘65,绕发盘50采用分体式结构,包括两个半圆形分瓣体,两个半圆形分瓣体之间设置有中间体,分瓣体和中间体固定在基盘65上;在绕发盘50上设置可横向移动的丝头压紧件53,丝头压紧件53的活动杆58与压紧部57相互垂直,丝头压紧件53可随着绕发盘50同步转动,当外力驱动丝头压紧件53横向背离绕发盘50后,丝头压紧件53与绕发盘50之间的空隙作为放置发丝70端头的空间,外力撤销后通过丝头压紧件53贴紧绕发盘50以实现将发丝70端头压紧在绕发盘50上;当发丝70端头被压紧在绕发盘50上后,通过驱动系统驱动绕发盘50旋转以实现将发丝70在绕发盘50上盘绕成发束圈22。
本实施例中,丝头压紧件53的活动杆58位于绕发盘50端侧,丝头压紧件53设置在弹性机构上;弹性机构包括固定块四60,固定块四60侧方设置有活动块四61,活动块四61通过拉杆62连接在固定块四60上,在活动块四61与固定块四60之间的拉杆62上套设有弹簧54;丝头压紧件53的活动杆58连接在活动块四61上,当外力驱动活动块四61向固定块四60靠近后,活动块四61带动丝头压紧件53横向背离绕发盘50;当外力撤销后,弹簧54驱动活动块四61复位并带动丝头压紧件53贴紧绕发盘50。在丝头压紧件53的活动杆58外侧设置有气缸九63,初始状态下,气缸九63的伸缩杆前端与丝头压紧件53间隔开,当气缸九63的伸缩杆伸长时,通过伸缩杆前端推动丝头压紧件53横向前移。
本实施例中,在绕发盘50环壁横向设置有丝头压槽56,当发丝70端头被压紧在绕发盘50上后,丝头压紧件53的压紧部57刚好位于丝头压槽56内。沿着绕发盘50环壁设置有用于容纳发丝70的线槽55,丝头压槽56与线槽55呈相互交叉的结构。
本实施例中,所述绕发装置还包括发丝进料机构,参见图1、图6至图11,它包括依序布置的:用于对发丝70进行导向的导向装置,用于将发丝70夹住并固定的夹固装置,以及用于将发丝70固定并切断的夹切装置64,夹固装置位于夹切装置64上方,夹切装置64位于绕线机构的绕线盘50侧方;夹固装置包括固定块一71,固定块一71上设置有气缸六72,气缸六72的伸缩杆前端设置有滑动块一73,气缸六72驱动滑动块一73伸至极限位置后,滑动块一73与固定块一71之间的空间作为发丝70的过路通道,气缸六72驱动滑动块一73回缩至极限位置后,滑动块一73与固定块一71相贴靠以实现将发丝70夹紧;夹切装置64包括呈l形的固定块二74,固定块二74上设置有固定块三84,固定块三84底部设置有切割部83,固定块二74内角侧壁设置有滑动块76,滑动块76和切割部83同时连接气缸七75;气缸七75伸至极限位置时,滑动块76前端抵紧固定块二74,并将发丝70夹持在滑动块76与固定块二74之间,切割部83的刃71将发丝70切断;气缸七75回退后,滑动块76与固定块二74之间的缺口用于容纳发丝70。夹切装置64的核心点在于:在夹紧发丝的同时将发丝切断,夹紧发丝是通过滑动块76与固定块二74相互抵紧将其夹持住,切断发丝则是通过固定块三84下方的切割部83将其切断。夹切装置64整体设置在三维移动机构上,用于驱动夹切装置64整体沿着三个相互垂直的方向移动,夹切装置64整体可以采用三组相互垂直的气缸驱动,也可以采用市售成品三维移动机构驱动,无论采用何种结构,其只要能够实现将夹切装置64整体驱动至预设位置即可。其中,导向装置采用滚轮导向结构,如图1所示,滚轮导向结构包括支架82,支架82上设置有三组滚轮81,最左侧的一组滚轮81位于夹固装置斜上方。固定块三84呈l形,并在固定块三84的内侧设置内凹部85;滑动块一73呈l形,固定块一71位于滑动块一73内侧。
本实施例中,所述绕发装置还包括捆发机构,参见图13至图16,它包括震动上料器33,震动上料器33上设置有输料轨道34;在输料轨道34末端斜上方设置有具有吸附功能的压料座37,在压料座37上方设置有气缸四36,气缸四36连接压料座37并用于驱动压料座37沿竖直方向往复运行;在压料座37正下方设置有绕发盘50,绕发盘50上设置有弧形槽40(如图16所示),弧形槽40正对压料座37;初始状态下,气缸四36处于缩回状态,随着震动上料器33的连续上料,金属捆钉35逐渐移动至输料轨道34末端后被吸附在压料座37底端面;随后,气缸四36伸长驱动压料座37下移且当压料座37底端面接触绕发盘50后,在压料座37的压力作用下和弧形槽40壁面的导向作用下,金属捆钉35发生弯折以实现将发束困住。其中,输料轨道34末端正对侧设置有临时载料件41,在临时载料件41左侧设置有气缸五39,气缸五39连接临时载料件41并用于控制临时载料件41沿水平方向往复运行;当金属捆钉35逐渐移动至输料轨道34末端后先转移至临时载料件41上,气缸四36伸长驱动压料座37适当下移以将金属捆钉35吸附在压料座37底端面。在压料座37上设置有气道,气道一端通向压料座37底端面,气道另一端通过管路38连接抽真空系统。在一个可选方案中,如果预先将气缸四36设置在合适高度使压料座37底端面在下移之前与临时载料件41上端面间隔较小的距离,可以直接将金属捆钉35吸附在压料座37底端面。临时载料件41上端面与输料轨道34上端面齐平,或者临时载料件41上端面略低于输料轨道34上端面。临时载料件41与输料轨道34均采用立式布置的板体结构,板体厚度略小于金属捆钉35两侧壁之间的宽度,运行过程中,金属捆钉35卡在板体的棱上。
实施例2
一种绕发装置,其结构参照实施例1、图17和图18,其与实施例1的主要区别在于:丝头压紧件53的活动杆58从绕发盘50内部的孔中横向穿过,在活动杆58上套设有弹簧54,弹簧54一端通过绕发盘50内部的限位台66进行限位、另一端通过活动杆58上的凸沿58进行限位;如图17所示,盘绕发丝70之前,先通过外力驱动丝头压紧件53向左移动,然后通过夹切装置64将发丝70端头送至丝头压紧件53的压紧部57左侧,然后撤销外力,通过弹簧54带动横向背离绕发盘50的丝头压紧件53复位,这样就借助于弹力的作用通过压紧部57将发丝70端头固定在丝头压槽56处了(如图18所示状态),接着就可以驱动绕发盘50转动进行盘绕发丝,一个发束圈22盘绕完成后,再通过夹切装置64将发丝夹断。
进料阶段:将装有发丝70的丝袋78放置于支架82外侧(图1中的右侧),然后将有发丝70拉出并绕过三组滚轮81,然后将夹固装置调至图6所示状态,并将发丝70从滑动块一73与固定块一71之间的空间穿过,然后将夹切装置64调整至图8和图10所示状态,并将发丝70从滑动块76与固定块二74之间的缺口处穿过,接着将发丝70的丝头固定在绕线机构的绕线盘50上;绕线机构启动后,通过绕线盘50转动将发丝70盘绕成发束圈,当一个发束圈盘绕完毕后,绕线盘50停止转动,气缸六72驱动滑动块一73回退至极限位置,滑动块一73与固定块一71相贴靠以实现将发丝70夹紧,如图7所示状态;同时,气缸七75伸至极限位置使滑动块76前端抵紧固定块二74,并将发丝70夹持在滑动块76与固定块二74之间,切割部83的刃71则将发丝70切断,如图9所示状态。下一次盘绕发丝70时,先先通过气缸六72驱动滑动块一73伸至极限位置(如图6所示状态),然后通过三维移动机构驱动夹切装置64整体移动,从而将夹切装置64与夹固装置之间的这段发丝拉至或送至绕线盘50上固定(绕线盘50固定发丝有很多方法,即固定丝头,通常采用夹紧的方式固定),再将气缸七75回退至如图8所示状态,最后启动绕线机构盘绕发丝。使用过程中,一方面通过夹固装置将发丝70夹住并固定,另一方面通过夹切装置64将发丝70固定并切断,无需操作者用手抓紧发丝并剪断,且在每次剪断发丝后能够防止发丝回拉,同时还能够防止丝头回退,使用时省去了操作者反复抓丝头和拉动发丝的麻烦,使得发丝进料操作更为简单、高效。
盘绕阶段:先通过外力(如气缸九)驱动丝头压紧件横向背离绕发盘,然后将发丝端头送至丝头压紧件与绕发盘之间的空隙处,随后立即撤销外力使得丝头压紧件在弹力的作用下复位,通过丝头压紧件贴紧绕发盘以实现将发丝端头压紧在绕发盘上;当发丝端头被压紧在绕发盘上后,通过驱动系统驱动绕发盘旋转以实现将发丝在绕发盘上盘绕成发束圈;由此种方式固定发丝端头并绕发,适用于制备大、中、小三种规格的发束圈,不仅解决了“在绕线盘上盘绕几圈发丝并固定时发丝就已经超出所需用量,导致绕制的发束圈不符合要求以及材料浪费”的技术问题,而且大幅提高了生产效率,可实现5~7秒/个发束圈的制备效率;
捆发阶段,将发束顺着弧形槽40盘绕在绕发盘50上,通过震动上料器33将金属捆钉35转移至输料轨道34,随着震动上料器33的连续上料(震动上料器的上料原理为现有技术,再次不做赘述),金属捆钉35会在输料轨道34上逐个紧挨排列并逐步前移,当金属捆钉35逐渐移动至输料轨道34末端后会进一步转移至临时载料件41上(如图13所示),随后通过抽真空系统将金属捆钉35吸附在压料座37底端面,随后临时载料件41在气缸五35的作用下左移,为压料座37下移让出通道(如图14所示),当气缸四36伸长以驱动压料座37下移且压料座37底端面接触绕发盘50后(如图15所示),在压料座37的压力作用下和弧形槽40壁面的导向作用下,金属捆钉35被压弯(发生弯折,图12所示状态),从而将发束困住。使用过程中,先通过气缸五39驱动临时载料件41向右移动,直到临时载料件41靠近输料轨道34末端时,最前的一个金属捆钉35就会在后续金属捆钉35的推力下转移到临时载料件41上(此推力属于震动上料原理的一部分),然后通过抽真空系统将金属捆钉35吸附在压料座37底端面,然后气缸五39驱动临时载料件41向左回退为压料座37下移让出通道,然后气缸四36驱动压料座37下移直到金属捆钉35将发束捆发,捆发结束后气缸四36驱动压料座37复位,至此完成一次捆发。这不仅能够快速地进行捆发,而且捆发过程中几乎不需要人工手动操作,非常方便、高效,通常情况下可实现3-5秒/个的捆发效率。
整个过程绝大多数工序可有机器自行完成,对人工操作的依赖程度小,可大幅减少企业人力成本。
起点商标作为专业知识产权交易平台,可以帮助大家解决很多问题,如果大家想要了解更多知产交易信息请点击 【在线咨询】或添加微信 【19522093243】与客服一对一沟通,为大家解决相关问题。
此文章来源于网络,如有侵权,请联系删除


