一种微正压颗粒成型污泥焚烧沸腾炉的制作方法



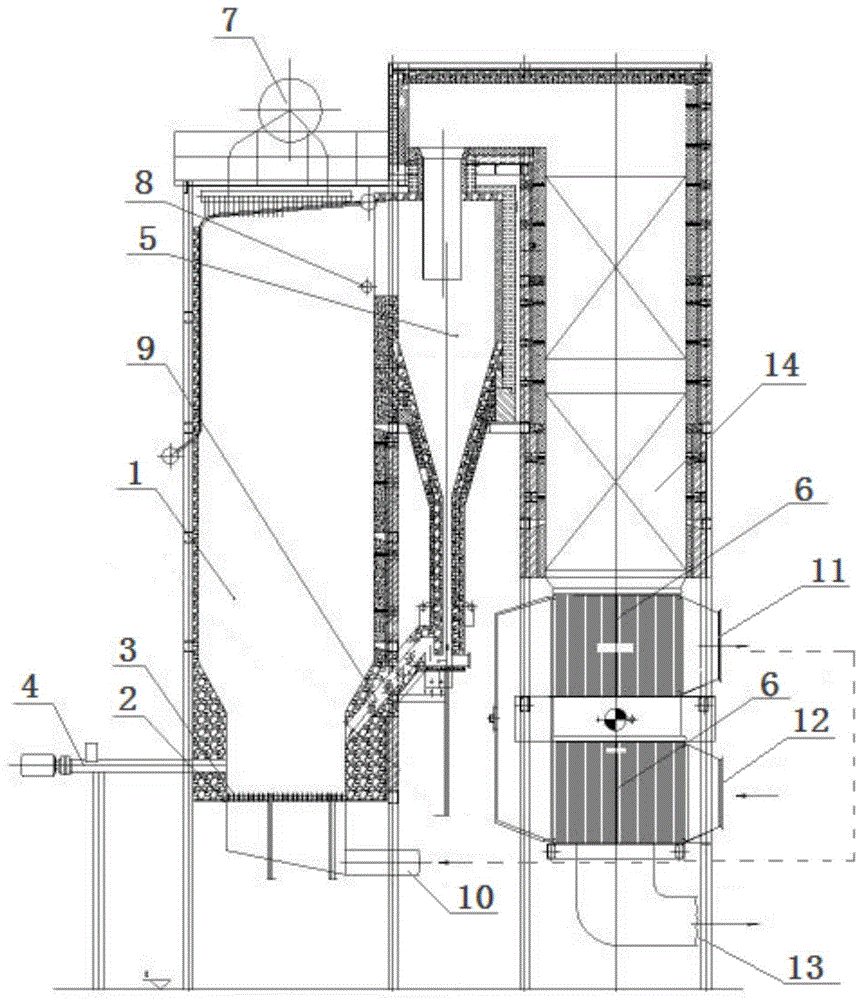
技术领域:
本实用新型属于环境保护技术领域,具体涉及一种微正压颗粒成型污泥焚烧沸腾炉。
背景技术:
:
随着污泥政策收紧及污泥量的日益剧增,污泥填埋已满足不了污泥处理的需求,政府也不再批复新的填埋场地,所以污泥的处理必须得另辟蹊径。
而目前主流的方式是通过焚烧减量化、资源化处理污泥。焚烧有两种方式,一是气化裂解燃烧焚烧,这种方式对污泥的发热量要求比较高,通常要在2000大卡/公斤以上,而常规污泥一般很难达到,所以需要加入大量辅助燃料,而且单炉难以大型化,最大处理一般在150吨/日左右。二是沸腾燃烧焚烧方式,这种方式大大降低了污泥的发热量要求,一般要求发热量1200大卡/公斤左右,单台最大处理可达300吨/日以上,利用高温烟气还可配置余热锅炉,供污泥干化,能量循环利用,变废为宝。
污泥焚烧沸腾炉的现状
尽管沸腾焚烧炉在发热量及资源利用方面比气化裂解炉有较大优势,但还存在许多不足之处,主要有以下几方面:
1、为了提高污泥的发热量,通常需要将污泥进行深度脱水,待脱水到30%左右时,发热量才能达到800大卡/公斤左右,仍然达不到污泥自持燃烧1200大卡/公斤入炉热量要求,所以需要添加一定的辅助燃料。
2、焚烧所产生的炉渣,可作为一般固废,并进行综合利用;而排出的飞灰,则被定性为危废,那么就需要进行二次处理。目前沸腾焚烧炉的灰渣比都在1以上,从而增加了用户的处理难度和处理费用,所以减少飞灰的产生量是技术需要克服的关键。
3、热效率低,通常只有70%左右。
技术实现要素:
:
本实用新型所要解决的技术问题是:解决上述现有技术存在的问题,而提供一种微正压颗粒成型污泥焚烧沸腾炉,降低对焚烧污泥发热量要求,能够焚烧最低发热量750大卡/公斤的污泥,实现灰渣比0.5~0.6。
本实用新型采用的技术方案是:
一种微正压颗粒成型污泥焚烧沸腾炉,包括依次连接连通的炉膛、高温除尘器、省煤器和空气预热器,在炉膛顶部安装有余热锅炉,炉膛底部安装有布风板、风帽和风厢,所述高温除尘器的下端与炉膛下部连接有飞灰返料通道,所述空气预热器的出风口与炉膛底部的风厢入口连接有预热空气通道,在炉膛下部一侧连接有给煤机;本实用新型的实用新型特征是:
a、所述炉膛四周墙壁除炉膛前墙上部及炉膛顶部布置受热面外,其余都采用绝热结构,以减少对炉膛的吸热,降低对入炉污泥发热量的要求;
b、所述炉膛采用全封闭结构,做到炉体承压不漏气,为正压燃烧、加强物料之间的传热创造了条件;
c、加大炉膛截面积2.5倍以上,以降低烟气流速,减少灰渣比;
d、减少风帽节距至60mm,风帽小孔直径控制在4mm以内,以降低流化风速;
e、所述空气预热器布置在炉膛尾部输出烟道内,以加热进入炉膛燃烧的空气。
上述技术方案中,所述炉膛前墙上部及炉膛顶部布置的受热面是指布置循环水管,但炉膛前墙上部外侧及炉膛顶部外侧仍采用耐火砖或保温砖、红砖砌成;所述炉膛四周墙壁除炉膛前墙上部及炉膛顶部外其余都采用绝热结构是指炉膛墙壁整体耐火砖或保温砖、红砖砌成。
上述技术方案中,所述炉膛采用全密封结构是指炉体的耐火砖或保温砖、红砖外再采用钢板满焊承压不漏气,炉体上的给煤口、测温测压孔精加工密封。工作原理及显著效果:
成型后的污泥经给煤机送入炉膛,空气经空预器加热后通过风厢、布风板、风帽参与污泥燃烧,燃烧所产生的高温烟气经高温除尘器后将一部分返回至炉膛,其余的大部分高温烟气经余热锅炉降温产生蒸汽(或与其他介质换热),再经空气预热器加热空气,返回炉膛辅助燃烧,充分利用并降温后的烟气最后经脱硫、脱硝、除尘等烟气处理系统,达标后通过烟囱排入大气。焚烧所产生的炉渣进行综合利用,尾部的除尘灰进行再处理。
本实用新型的技术方案能将入炉污泥的发热量要求降低至750大卡/小时左右,实现入炉污泥在不需要辅助燃料的情况自持稳燃焚烧,并降低灰渣比至0.6以下,热效率大于80%。是污泥处理焚烧技术的一大突破。
附图说明:
图1为本实用新型结构示意图;
图2为本发明的实验数据表。
附图标注说明:
1—炉膛,2—布风板,3—风帽,4—给煤机,5—高温除尘器,6—空气预热器,7—余热锅炉,8—炉膛上部压力测点,9—飞灰返料通道,10—预热空气通道,11—预热空气出风口,12—进风口,13—排烟口,14—省煤器。
具体实施方式:
参见图1,本实用新型的一种微正压颗粒成型污泥焚烧沸腾炉,包括依次连接连通的炉膛1、高温除尘器5、省煤器14和空气预热器6,在炉膛1顶部安装有余热锅炉7,炉膛1底部安装有布风板2、风帽3和风厢,所述高温除尘器的下端与炉膛下部连接有飞灰返料通道9,所述空气预热器6的出风口11与风厢入口连接有预热空气通道10,在炉膛1下部一侧连接有给煤机4;本实用新型的实用新型特征是:
a、所述炉膛四周墙壁除炉膛前墙上部及炉膛顶部布置受热面外,其余都采用绝热结构,以减少对炉膛的吸热,降低对入炉污泥发热量的要求;
b、所述炉膛采用全封闭结构,做到炉体承压不漏气,为正压燃烧、加强物料之间的传热创造了条件;
c、加大炉膛截面积2.5倍以上,以降低烟气流速,减少灰渣比;
d、减少风帽节距至60mm,风帽小孔直径控制在4mm以内,以降低流化风速;
e、所述空气预热器布置在炉膛尾部输出烟道内,以加热进入炉膛燃烧的空气。
上述炉膛前墙上部及炉膛顶部布置的受热面是指布置循环水管,但炉膛前墙上部外侧及炉膛顶部外侧仍采用耐火砖或保温砖、红砖砌成;所述炉膛四周墙壁除炉膛前墙上部及炉膛顶部外其余都采用绝热结构是指炉膛墙壁整体耐火砖或保温砖、红砖砌成。
上述炉膛采用全密封结构是指炉体的耐火砖或保温砖、红砖外再采用钢板满焊承压不漏气,炉体上的给煤口、测温测压孔精加工密封。
一种微正压颗粒成型污泥焚烧沸腾炉的焚烧工艺,包括:
一、炉膛墙壁80%以上采用绝热结构,这样结构的目的是减少对炉膛的吸热,从而降低对入炉污泥发热量的要求;
二、炉膛出口正压大于500pa;通常焚烧沸腾炉出口为负压,将负压改为正压燃烧,让整个炉膛都处于正压焚烧状态,从而加强了物料之间的传热、传质性能,强化了燃烧;这样不仅可以降低对入炉污泥发热量的要求,还可提高热效率;
三、加大炉膛截面积至通常炉膛截面积2.5倍以上,炉膛烟气流速控制在0.8m/s以内,烟气流速从通常的2m/s以上减少至0.8m/s以下,大大减少了飞灰的扬析,延长了烟气在炉内的停留时间,不仅可提高热效率,还可减少灰渣比;
四、将污泥成型入炉,将入炉粒径控制在粒径小于6mm的理想状态,而且粒径小于6mm的理想颗粒重量占整个入炉污泥重量的70%以上,入炉污泥的颗粒度均匀,可以很清晰地配置风量,选择合理的流化速度,加强了炉内燃烧,很好地解决了热效率低及飞灰大一系列问题;
五、将布风板面积扩大至0.40平方米/80万大卡时以上,这样不仅增加了密相区的储热能力,降低了流化速度,也降低入炉污泥的发热量要求,并减少了灰渣比;焚烧炉的功率等于污泥的发热量乘以小时的污泥入炉量,通常单位是万大卡/小时,目前大部份沸腾炉布风板面积为0.3平方米/80万大卡时;
六、减少风帽的节距与风帽小孔的直径,将风帽的节距减少至60mm,风帽小孔直径控制在4mm以内,现有风帽小孔直径通常在5mm以上,因而风帽小孔直径减小可降低流化风速提高流化质量,提高热效率,减少灰渣比;
七、高温除尘器除尘下来的飞灰只返其中20-25%到炉膛内,减少循环倍率;加上炉膛采用绝热结构,增加烟气停留时间,在不影响热效率的前提下,大大减少了灰渣比;
八、炉膛输出尾部烟道布有空气预热器,将进入炉膛燃烧的空气加热助燃,进一步降低对入炉燃料的发热量要求。
所述炉膛墙壁80%以上采用绝热结构是指炉膛四周墙壁除炉膛前墙上部及炉膛顶部布置受热面外,其余都采用绝热结构;所述受热面为循环水管,循环水管外侧仍采用耐火砖或保温砖、红砖砌成;所述绝热结构是指炉膛墙壁整体采用耐火砖或保温砖,红砖砌成。
所述的炉膛出口正压大于500pa采取的做法是:向炉膛鼓风的鼓风机的压力选择1300pa,而且整个炉膛全密封,并且在炉膛墙壁的耐火砖或保温砖、红砖外再采用4mm钢板满焊,使炉体做到承压不漏气,红煤口,测温测压孔精加工,严格密封。
起点商标作为专业知识产权交易平台,可以帮助大家解决很多问题,如果大家想要了解更多知产交易信息请点击 【在线咨询】或添加微信 【19522093243】与客服一对一沟通,为大家解决相关问题。
此文章来源于网络,如有侵权,请联系删除


