蓄热式高温氧化炉的制作方法



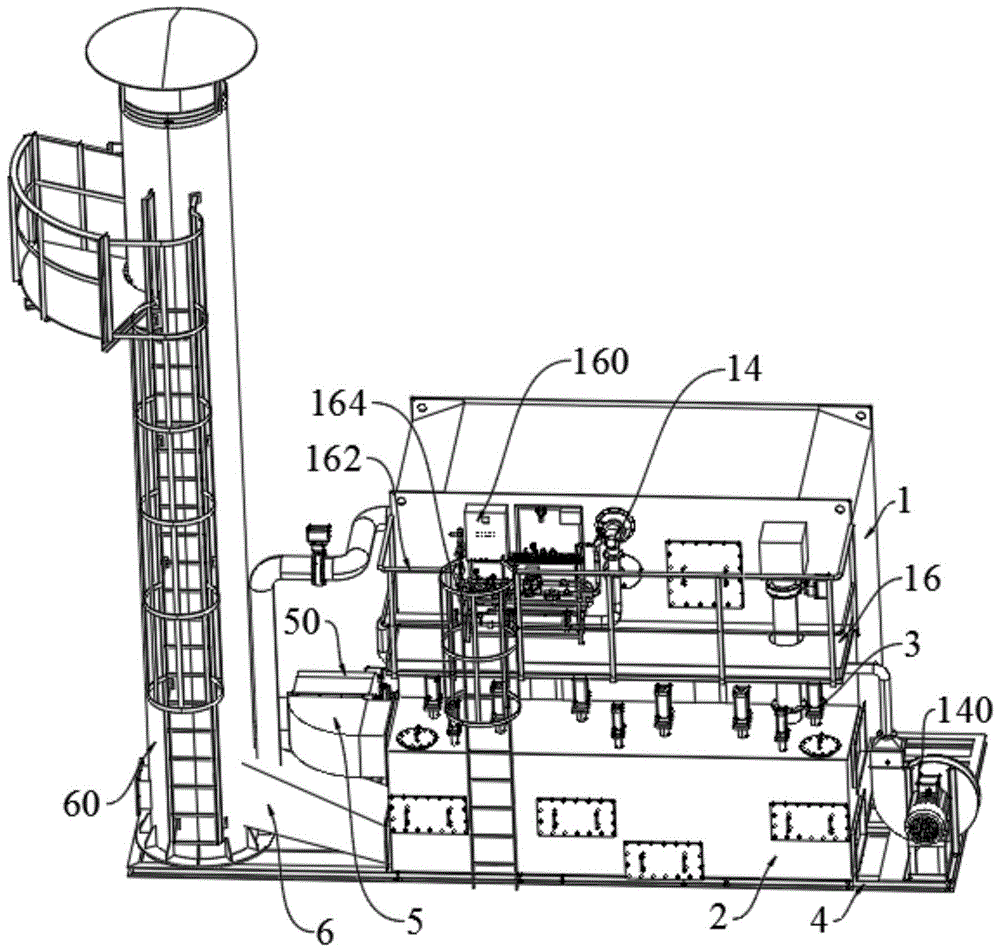
本申请涉及废气处理技术领域,尤其涉及一种蓄热式高温氧化炉。
背景技术:
蓄热式高温氧化设备(regenerativethermaloxidizer,简称rto)是一种高效有机废气治理设备。其原理是在高温下将可燃废气氧化成对应的氧化物和水,从而净化废气,并回收废气分解时所释放出来的热量,废气分解效率达到99%以上,热回收效率达到95%以上。
现有的蓄热式高温氧化设备主要采用工厂制造模块或零部件,并将模块和零部件运输到施工现场进行组装,导致现有的蓄热式高温氧化设备结构复杂,难以实现自动化生产,且制造过程无法有效控制,产品质量差,处理效率无法满足日益提高的气体排放要求。
技术实现要素:
本申请提供了一种蓄热式高温氧化炉,以简化蓄热式高温氧化设备的结构,实现蓄热式高温氧化设备的一体化生产。
本申请提供了一种蓄热式高温氧化炉,其包括炉体,所述炉体内设有燃烧室以及多个相互隔开的蓄热室,各所述蓄热室分别连通所述燃烧室,其特征在于,
所述炉体的一侧设有切换箱,所述切换箱内分隔形成有进气室、排气室和反吹室,
所述进气室设有分别连通各所述蓄热室的第一通气口,所述第一通气口设有进气切换阀门,
所述排气室设有分别连通各所述蓄热室的第二通气口,所述第二通气口设有出气切换阀门,
所述反吹室设有分别连通各所述蓄热室的第三通气口,所述第三通气口设有反吹切换阀门。
可选地,所述切换箱内还分隔形成有多个分配室,所述分配室与所述蓄热室一一对应且相互连通,所述第一通气口设置于所述进气室与所述分配室之间,所述第二通气口设置于所述排气室与所述分配室之间,所述第三通气口设置于所述反吹室与所述分配室之间。
可选地,多个所述蓄热室沿所述炉体的长度方向依次排列,多个所述分配室沿所述炉体的长度方向依次排列。
可选地,所述进气室、所述排气室以及所述反吹室分别沿所述炉体的长度方向延伸。
可选地,沿所述炉体的高度方向,所述切换箱内设置成三层结构,所述分配室位于所述切换箱的中层,所述进气室、所述排气室以及所述反吹室围绕所述分配室,分布于所述分配室的上下两侧。
可选地,所述进气室与所述反吹室位于所述分配室的同一侧,所述排气室位于所述分配室的另一侧。
可选地,所述分配室的横截面设置成折线型,所述分配室的底部靠近所述炉体的一侧向下延伸,形成连通所述蓄热室的通道。
可选地,所述切换箱设置于所述炉体的一侧的下部,且所述切换箱与所述炉体设置成一体。
可选地,所述炉体的一侧还设有操作平台,所述操作平台位于所述切换箱的上方,且与所述切换箱之间设有间隙。
可选地,所述蓄热式高温氧化设备还包括:
底板,设置于所述炉体与所述切换箱的底部;
送气系统,安装于所述底板上,用于将待处理气体送入进气室;
排气系统,安装于所述底板上,用于排放完成处理的气体。
本申请提供的技术方案可以达到以下有益效果:
本申请提供的蓄热式高温氧化设备在炉体的一侧设置切换箱,并将切换箱内分隔形成进气室、排气室和反吹室,采用进气室、排气室和反吹室取代原有的进气管道、排气管道和反吹管道,使整体结构更加简单紧凑,减小了蓄热式高温氧化设备占用空间的大小,从而简化了蓄热式高温氧化设备的结构,便于实现蓄热式高温氧化设备的一体化生产。
应当理解的是,以上的一般描述和后文的细节描述仅是示例性的,并不能限制本申请。
附图说明
图1为本申请实施例提供的蓄热式高温氧化设备的结构示意图;
图2为图1所示炉体与切换箱的内部结构示意图;
图3为图1所示炉体的内部结构示意图;
图4为图1所示炉体与切换箱的侧视结构示意图;
图5为图1所示切换箱的结构示意图;
图6为图5所示切换阀门的安装结构示意图;
图7为图6所示切换阀门的立体结构示意图。
附图标记:
1-炉体;
10-燃烧室;
12-蓄热室;
120-第一蓄热室;
122-第二蓄热室;
124-第三蓄热室;
14-燃烧系统;
140-助燃风机;
16-操作平台;
160-控制箱;
162-围栏;
164-爬梯;
2-切换箱;
20-进气室;
200-第一通气口;
202-进气口;
22-排气室;
220-第二通气口;
222-排气口;
24-反吹室;
240-第三通气口;
242-反吹口;
26-分配室;
260-第一分配室;
262-第二分配室;
264-第三分配室;3-切换阀门;
3a-进气切换阀门;
3b-排气切换阀门;
3c-反吹切换阀门;
30-阀座;
300-安装孔;
300a-滑动轴承;
302-通气孔;
304-环形凸台;
30a-内环;
30b-外环;
30c-辐条;
32-阀杆;
34-阀板;
340-密封圈;
342-容纳槽;
36-套管;
38-驱动装置;
4-底板;
5-送气系统;
50-主风机;
6-排气系统;
60-烟囱。
此处的附图被并入说明书中并构成本说明书的一部分,示出了符合本申请的实施例,并与说明书一起用于解释本申请的原理。
具体实施方式
为了使本申请的目的、技术方案及优点更加清楚明白,以下结合附图及实施例,对本申请进行进一步详细说明。应当理解,此处所描述的具体实施例仅仅用以解释本申请,并不用于限定本申请。
在本申请的描述中,除非另有明确的规定和限定,术语“第一”、“第二”仅用于描述的目的,而不能理解为指示或暗示相对重要性;除非另有规定或说明,术语“多个”是指两个或两个以上;术语“连接”、“固定”等均应做广义理解,例如,“连接”可以是固定连接,也可以是可拆卸连接,或一体地连接,或电连接;可以是直接相连,也可以通过中间媒介间接相连。对于本领域的普通技术人员而言,可以根据具体情况理解上述术语在本发明中的具体含义。
本说明书的描述中,需要理解的是,本申请实施例所描述的“上”、“下”等方位词是以附图所示的角度来进行描述的,不应理解为对本申请实施例的限定。此外,在上下文中,还需要理解的是,当提到一个元件连接在另一个元件“上”或者“下”时,其不仅能够直接连接在另一个元件“上”或者“下”,也可以通过中间元件间接连接在另一个元件“上”或者“下”。
如图1-图7所示,本申请实施例提供了一种蓄热式高温氧化设备,其包括炉体1和切换箱2。炉体1内设有燃烧室10以及多个相互隔开的蓄热室12,燃烧室10位于蓄热室12的顶部,各蓄热室12分别连通燃烧室10,炉体1的外部可以设置燃烧系统14,通过燃烧系统14加热和点燃燃烧室10内的气体,燃烧系统14可以设置助燃风机140,以便使燃烧室10内的气体能够充分燃烧,提高废气的处理效率;切换箱2设置于炉体1的一侧,切换箱2内分隔形成有进气室20、排气室22和反吹室24。其中,进气室20设有分别连通各蓄热室12的第一通气口200,第一通气口200设有进气切换阀门3a,通过进气切换阀门3a打开或关闭第一通气口200;排气室22设有分别连通各蓄热室12的第二通气口220,第二通气口220设有排气切换阀门3b,通过排气切换阀门3b打开或关闭第二通气口220;反吹室24设有分别连通各蓄热室12的第三通气口240,第三通气口240设有反吹切换阀门3c,通过反吹切换阀门3c打开或关闭第三通气口240。本申请采用进气室20、排气室22和反吹室24取代原有的进气管道、排气管道和反吹管道,使整体结构更加简单紧凑,减小了蓄热式高温氧化设备占用空间的大小,从而简化了蓄热式高温氧化设备的结构,便于实现蓄热式高温氧化设备的一体化生产。
具体地,本申请实施例提供的蓄热式高温氧化设备还包括送气系统5和排气系统6;进气室20设有连通切换箱2的外部的进气口202,送气系统5设有主风机50,送气系统5连通进气口202并将待处理气体送入进气室20内;排气室22设有连通切换箱2的外部的排气口222,排气系统6设有烟囱60,排气系统6连通排气口222,并将排气口222排出的气体排放到设备外部;反吹室24设有连通切换箱2的外部的反吹口242,反吹口242用于清除设备中残存的有害气体,反吹口242可以接入送气系统5,以便对反吹口242排出的气体进行再次处理,防止有害气体排放到设备的外部。
其中,进气口202、排气口222和反吹口242可以设置连接法兰,以使连接更加方便。进气口202的数量可以为两个,两个进气口202分别位于(或靠近)进气室20的两端,使用时,其中一个进气口202用于连接送气系统5,另一个进气口202通过盖板进行封闭,以使设备能够更好地适应施工现场的空间安装要求。相应地,排气口222和反吹口242的数量可以分别为两个,两个排气口222分别位于(或靠近)排气室22的两端,两个反吹口242分别位于(或靠近)反吹室24的两端。
进一步地,本申请实施例提供的蓄热式高温氧化设备还可以包括底板4,炉体1、切换箱2、送气系统5和排气系统6均整合安装固定在底板4上,使设备各部分的制造和组装能够在制造车间内完成,提高了设备制造的自动化水平,且能够有效保证产品质量可靠,且使设备能够整体制造和运输,避免了施工现场组装所造成的安全隐患。
优选地,切换箱2设置于炉体1的一侧的下部,以减小切换箱2与蓄热室12之间的距离,使切换箱2能够连通蓄热室12的底部,使气体能够充分穿过蓄热室12,并通过蓄热室12吸收和储存气体的热量;切换箱2与炉体1设置成一体,使炉体1与切换箱2之间的结构更加紧凑,从而减小整体的尺寸。
进一步地,炉体1的一侧(朝向切换箱2的一侧)还设有操作平台16,操作平台16位于切换箱2的上方,以充分利用有效空间,减小设备的整体尺寸,炉体1的相应位置设有控制箱160,通过控制箱160控制设备的正常运行(例如,燃烧系统14、切换阀门3、送气系统5和排气系统6等),操作者可以登上操作平台16操作控制箱160,操作平台16的边缘可以设置围栏162,以确保操作者的安全,操作平台16的一侧可以设置扶梯164,以方便操作者上下操作平台16;操作平台16与切换箱2之间设有间隙,形成各切换阀门3的安装空间,使各切换阀门3均不超出炉体1与切换箱2的边缘,进一步提高空间的有效利用率,减小设备的整体尺寸。
进一步地,切换箱2内还分隔形成有多个分配室26,分配室26与蓄热室12一一对应且相互连通,第一通气口200设置于进气室20与分配室26之间,第二通气口220设置于排气室22与分配室26之间,第三通气口240设置于反吹室24与分配室26之间,也就是说,进气室20、排气室22与反吹室24均连通分配室26,并通过分配室26连通蓄热室12,避免了复杂的管路连接,进一步简化了切换箱2的内部结构。
进一步地,多个蓄热室12沿炉体1的长度方向依次排列,切换箱2位于炉体1的厚度方向的一侧,多个分配室26沿炉体1的长度方向依次排列,提高设备整体布局的紧凑性,简化切换箱2与炉体1之间的连接结构。
在一种优选实施例下,蓄热室12的数量为三个,三个蓄热室12分别为第一蓄热室120、第二蓄热室122和第三蓄热室124;分配室26的数量为三个,三个分配室26分别为第一分配室260、第二分配室262和第三分配室264。三个蓄热室12可以分别通过相应的分配室260,连通进气室20、排气室22和反吹室24,也就是说,三个蓄热室12分别负责进气、排气和反吹,并依次交替循环,充分提高设备的利用效率和气体的处理效率。
具体工作过程参考如下:
在第一个工作循环中,第一蓄热室120通过第一分配室260,连通进气室20,待处理气体通过送气系统5依次经过进气室20、第一分配室260和第一蓄热室120进入燃烧室10进行处理,在此过程中,第一分配室260中会有残留的待处理气体,需要在下一工作循环中进行反吹,使第一分配室260保持清洁;第二蓄热室122通过第二分配室26,连通排气室22,燃烧室10内完成处理的一部分气体依次经过第二蓄热室122、第二分配室262和排气室22进入排气系统6进行排放;第三蓄热室124通过第三分配室26,连通反吹室24,燃烧室10内完成处理的一部分气体依次经过第三蓄热室124、第三分配室264和反吹室24重新进入送气系统5进行再处理,在此过程中,第三分配室264内残留的待处理气体被清理干净,在下一工作循环中可以进行排气。
在第二个工作循环中,第一蓄热室120通过第一分配室260,连通反吹室24;第二蓄热室122通过第二分配室262,连通进气室20;第三蓄热室124通过第三分配室264,连通排气室22。
在第三个工作循环中,第一蓄热室120通过第一分配室260,连通排气室22;第二蓄热室122通过第二分配室262,连通反吹室24;第三蓄热室124通过第三分配室264,连通进气室20。
如此,三个工作循环依次交替进行,实现气体的连续高效处理。
进一步地,进气室20、排气室22以及反吹室24分别沿炉体1的长度方向延伸,以方便进气室20、排气室22以及反吹室24均能够延伸覆盖多个分配室26,从而方便分配室26与其他各室之间的连通。
更进一步地,沿炉体1的高度方向,切换箱2内设置成三层结构,分配室26位于切换箱2的中层,进气室20、排气室22和反吹室24围绕分配室26,分布于分配室26的上下两侧,使切换箱2的高度和宽度均控制在适当的范围内,且形成矩形的整体外观,简化切换箱2的结构,减小切换箱2的尺寸,此外,使其他各室(包括进气室20、排气室22和反吹室24)与分配室26的连通部位位于同一方位(即位于水平面上),从而使各切换阀门3能整体布置在同一空间内,且使各切换阀门3的往复运动方向也处于同一方位(即沿竖直方向),从而使设备的结构更加紧凑,减小设备的整体体积。
进一步地,分配室26的横截面设置成折线型,分配室26的底部靠近炉体1的一侧向下延伸,形成连通蓄热室12的通道,使切换箱2的底部与炉体1的底部相平,进一步充分利用有限空间,形成结构紧凑的连通方式。
进一步地,由于进气室20与反吹室24均连通送气系统5,因此,优选进气室20与反吹室24位于分配室26的同一侧,排气室22位于分配室26的另一侧。其中,反吹室24应具有最小的横截面,避免过多的气体重新进入送气系统5进行再处理,导致气体处理效率降低。
优选地,当分配室26的横截面设置成折线型时,进气室20与反吹室24位于分配室26的上侧,排气室22位于分配室26的下侧,防止排气室22的横截面相比进气室20的横截面过大,降低排气室22的有效利用率。
如图6和图7所示,本申请实施例提供的切换阀门3,安装于相邻两个箱体之间,用于控制相邻两个箱体之间的连通和阻断,其包括阀座30、阀杆32和阀板34。阀座30密封连接(例如焊接等方式)于相邻两个箱体之间设置的连通孔处,通过阀座30对切换阀门提供支撑和固定作用,阀座30的中央设有安装孔300,围绕安装孔300设有通气孔302,通气孔302沿阀座30的厚度方向贯穿阀座30;阀杆32滑动连接于安装孔内,阀杆32能够沿阀座30的轴线方向往复移动;阀板34设置于阀座30的一侧,并与阀座30之间形成密封配合副,阀板34连接于阀杆32上,并通过阀杆32带动阀板34沿阀座30的轴线方向移动,以打开或关闭通气孔302。本申请通过切换阀门自身的阀座30与阀板34之间形成密封配合副,使切换阀门能够独立于箱体之外,从而易于控制切换阀门的制造精度,确保切换阀门的密封性能,延长切换阀门的使用寿命。
具体地,本申请实施例提供的相邻两个箱体可以包括沿厚度方向依次间隔分布的第一箱板、中间箱板和第二箱板,其中第一箱板和中间箱板之间为第一箱体,中间箱板和第二箱板之间为第二箱体,阀座30密封连接于中间箱板,阀板34位于阀座30朝向第二箱板的一侧。
其中,阀座30和阀板34分别为通过浇铸成型的铸造件,使阀座30和阀板34具有较高的结构强度和刚度,避免使用过程中阀座30或阀板34出现变形或损坏,从而能够有效控制阀座30和阀板34之间的配合精度,且便于实现切换阀门的批量化生产。
进一步地,为防止阀杆32与安装孔300之间产生较大的磨损,导致阀座30损坏,安装孔300内可以安装有滑动轴承300a,阀杆32与滑动轴承300a滑动配合。也就是说,滑动轴承300a固定于安装孔300内,例如滑动轴承300a的两端可以分别通过轴肩和卡簧进行固定,阀杆32与滑动轴承300a的内孔间隙配合,减小阀杆32在安装孔300内的配合间隙,防止阀杆32发生晃动。
其中,阀杆32可以向远离阀板34的方向延伸至穿透阀座30,以减小阀座30的厚度,从而减小切换阀门的整体重量;阀杆32远离阀板34的一端可以连接驱动装置38,通过驱动装置38带动阀杆32沿阀座30的轴线方向往复移动,驱动装置38可以采用气缸或液压缸等任意能够实现往复直线运动的装置。优选阀杆32远离阀板34的一端延伸至穿过第一箱板,使驱动装置38能够位于箱体的外部,以避免箱体内的有害气体对驱动装置38产生损坏,且便于控制驱动装置38;当然,阀杆32远离阀板34的一端可以不穿过第一箱板,使驱动装置38位于箱体内。
优选地,阀座30背离阀板34的一侧可以设置套管36,阀杆32穿过安装孔300后,容纳于套管36内。也就是说,套管36设置成中空结构,套管36正对安装孔300,连接(例如焊接等方式)于阀座30背离阀板34的一侧且向远离阀板34的方向延伸,套管36可以密封连接(例如焊接等方式)于第一箱板,通过套管36进一步对切换阀门进行支撑和固定,增加切换阀门整体安装固定的可靠性,防止使用过程中连接松动,导致有害气体泄漏;此外,当阀杆32穿过安装孔300后,插入套管36内,通过套管36对阀杆32形成导向和保护,通过套管36与第一箱板之间的静态密封,取代阀杆32与第一箱板之间的动态密封,达到更好的密封性能。
进一步地,当阀座30设有套管36时,驱动装置38可以设置于套管36远离阀板34的一端,阀杆32远离阀板34的一端连接于驱动装置38,并通过驱动装置38带动阀杆32移动,通过套管36对驱动装置38提供支撑作用,使切换阀门的各部分具有较高的集成性能,使切换阀门整体更加紧凑,方便切换阀门的批量化生产。
进一步地,本申请实施例提供的阀座30设置成法兰状结构,阀座30包括内环30a、外环30b以及连接内环30a与外环30b的多个辐条30c;一方面,使阀座30具有较小的厚度和较高的结构强度,增加切换阀门安装固定的可靠性;另一方向,能够尽可能增大通气孔302的有效面积,使气体流通更加顺畅。其中,内环30a位于中央位置,安装孔300设置于内环30a的中央,相邻辐条30c之间的间隙构成通气孔302,阀板34与外环30b形成密封配合副,使各通气孔302均处于密封配合副的密封区域以内,通过一个密封配合副同时实现多个通气孔302的开启与关闭,简化切换阀门的整体结构,并提高密封配合的可靠性。可以理解地,阀板34也可以与各通气孔302分别形成密封副,此时,会导致切换阀门的整体结构复杂,且难以保证各通气孔302的密封性能的一致性。
进一步地,阀座30朝向阀板34的一侧可以设有环形凸台304,阀板34与环形凸台304的端面之间形成密封配合副,减小阀座30与阀板34之间的接触面积,形成有针对性的密封配合区域,该环形凸台304的端面可以经过精密加工,提高密封配合的可靠性。
更进一步地,环形凸台304的端面上可以设置至少一个环形凹槽,通过设置环形凹槽,将环形凸台304的端面分隔形成多个间隔分布的多个环形密封面,从而进一步减小阀座30与阀板34之间的接触面积,此外,多个环形密封面形成相互独立的多道密封,可以进一步确保密封配合的可靠性。
优选地,当环形凸台304的端面上设置有环形凹槽时,环形凸台304的端面的横截面可以设置呈波浪形,也就是说,环形密封面的横截面为弧形,使环形密封面与阀板34之间能够形成线性密封,且能够避免阀座30与阀板34之间产生磨损或划伤,增加密封性能。可选地,环形凸台304的端面的横截面也可以设置成齿形,也就是说,环形密封面的横截面为矩形(或近似矩形,例如梯形等)或三角形。
进一步地,本申请实施例提供的阀板34可以通过胀紧套连接于阀杆32,可以保证阀板34与阀杆32的完整性,避免对阀板34和阀杆32的结构破坏,例如采用键槽、销等连接方式时需要在阀板34或阀杆32上开孔。此外,由于胀紧套安装时不需要固定的安装位置,因此可以方便阀板34在阀杆32上进行调整,从而将阀板34安装到适当的位置,确保阀板34与阀杆32的密封配合,也就是说,在使用过程中,阀板34与阀座30之间的密封配合副发生磨损产生间隙时,可以通过将阀板34向靠近阀座30的方向适当移动一定距离,即可再次实现阀板34与阀座30的密封配合。此外,由于胀紧套安装和拆卸方便,也可以便于阀板34的后期维修和更换。
具体地,胀紧套可以包括内套和外套,内套与外套之间通过螺栓进行连接。其中内套与外套之间的配合面为锥面,随着螺栓的紧固,外套向外膨胀并抱紧阀板34的内孔,内套向内压缩并抱紧阀杆32的外壁,从而将阀板34固定于阀杆32上。为进一步增加阀板34与阀杆32连接的可靠性,可以在阀板34的内孔中增加轴套,轴套焊接于阀板34的内孔中。
进一步地,阀板34上设有密封圈340,并通过密封圈340与阀座30形成密封配合副,密封圈340可以采用硅胶等耐高温的弹性材料制成,通过密封圈340产生弹性变形,使阀板34与阀座30之间形成可靠的密封配合。
进一步地,阀板34上可以设有容纳槽342,密封圈340嵌装入容纳槽342内,密封圈340可以与容纳槽342过盈配合,增加密封圈340安装定位的可靠性,防止密封圈340发生移位或脱落。当然,密封圈340也可以通过粘接等方式固定于阀板34上。
优选地,容纳槽342设置成燕尾槽,密封圈340的横截面设置成与燕尾槽相配合的梯形结构,通过燕尾槽的收口结构,将密封圈340卡固于容纳槽342内,防止密封圈340从容纳槽342内脱出。可以理解地,容纳槽342也可以设置成其他具有收口趋势的槽状结构,只要容纳槽342内沿槽底向槽口的方向其中有一段槽宽逐渐减小,即可达到卡固的效果。
以上所述仅为本申请的优选实施例而已,并不用于限制本申请,对于本领域的技术人员来说,本申请可以有各种更改和变化。凡在本申请的精神和原则之内,所作的任何修改、等同替换、改进等,均应包含在本申请的保护范围之内。
起点商标作为专业知识产权交易平台,可以帮助大家解决很多问题,如果大家想要了解更多知产交易信息请点击 【在线咨询】或添加微信 【19522093243】与客服一对一沟通,为大家解决相关问题。
此文章来源于网络,如有侵权,请联系删除


