一种煤粉部分气化协同脱硝系统的制作方法



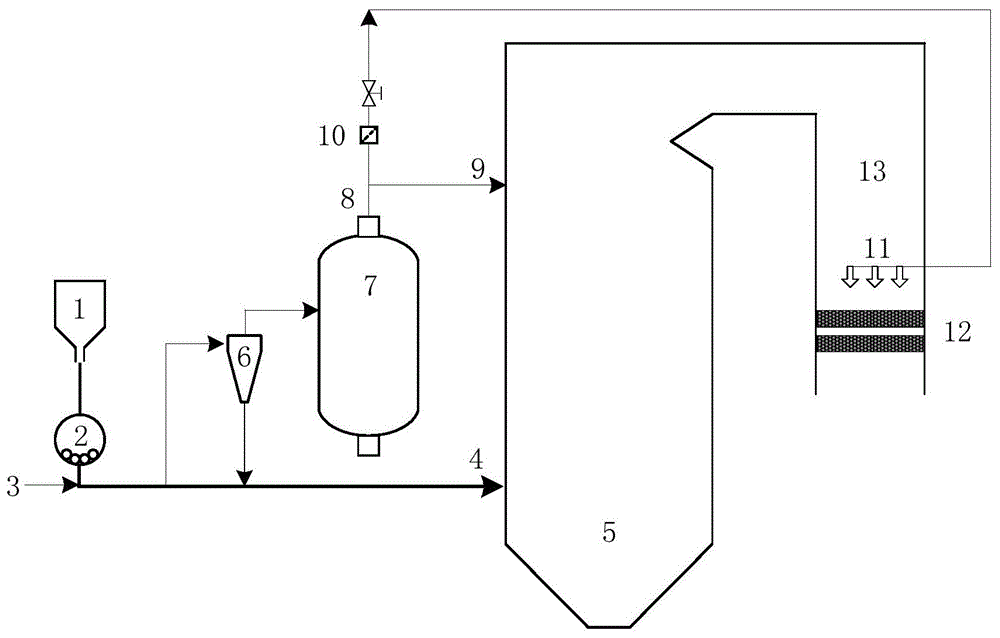
本实用新型涉及火电厂烟气脱硝技术,具体为一种煤粉部分气化协同脱硝系统。
背景技术:
燃煤电厂氮氧化物排放是造成酸雨、光化学污染等环境问题的主要成因之一。近年来,氮氧化物排放标准越来越严格,部分要求氮氧化物排放浓度不能超过30mg/m3。
燃煤电厂常用的氮氧化物减排技术包括低氮燃烧技术、非选择性催化还原技术(sncr)及选择性催化还原技术(scr)。sncr及scr技术均采用氨作为脱硝还原剂,为保证较高的脱硝效率,实际运行时均采用较高的氨氮摩尔比。但是,过量喷氨对脱硝技术经济性造成了很大影响,一台600mw机组每年仅氨耗量费用就达到了数百万元。另外,对于燃用高硫煤的火电机组,过量喷氨引起的空预器堵塞已严重影响了机组安全性。
为减少脱硝系统氨耗量,需要进一步挖掘低氮燃烧技术的脱硝潜力。空气分级、深度空气分级等低氮燃烧技术被广泛采用,但进一步降低主燃区过量空气系数会引起锅炉燃烧效率下降、co高温腐蚀等问题。近年来,相关技术开始采用燃料分级来降低燃烧过程nox排放,如专利cn201610745593公开的一种双炉膛煤粉气化低氮燃烧工业锅炉,利用煤粉气化燃烧技术降低nox排放,利用副炉膛将未燃尽的co和煤粉再次燃烧,采用双炉膛结构使煤粉燃烧有充分的气化空间和燃尽空间。又如专利cn200910201223公开的一种利用煤粉热解气再燃的低nox燃烧方法及装置,以煤粉热解气作为气体再燃燃料,送入煤粉锅炉再燃区高效还原nox,煤粉热解产生的半焦则在一次风携带下进入煤粉锅炉主燃区完成燃烧。但是,煤粉全部热解或气化需要很大的热解或气化设备,初投资大,不适用于现有燃煤机组改造;并且都是将co在主燃区进行燃烧和气化,其在主燃区生成co易形成高温腐蚀,降低设备的使用寿命。
技术实现要素:
针对现有技术中存在的问题,本实用新型提供一种煤粉部分气化协同脱硝系统,结构简单,设计合理,改造方便,能够在不喷氨的条件下实现电站锅炉氮氧化物超低排放,技术经济性高。
本实用新型是通过以下技术方案来实现:
一种煤粉部分气化协同脱硝系统,包括煤仓、磨煤机、锅炉、旋风分离器、气化炉和过滤器;
煤仓的出煤口连接磨煤机入口,磨煤机的煤粉出口分别连接旋风分离器入口和锅炉主燃区设置的燃烧器喷口,磨煤机的煤粉出口接入一次风管;
旋风分离器的细煤粉出口连接燃烧器喷口,粗煤粉出口连接气化炉进口;
气化炉的煤气出口分为两路,一路经再燃喷口接入锅炉的折焰角区域,另一路经过滤器后接入尾部烟道,尾部烟道经喷枪将煤气接入空预器尾部的尾部烟道;尾部烟道内的喷枪下游设置有催化剂层。
优选的,旋风分离器的入口连接管路上设置有一次风调门。
优选的,气化炉上设置有水冷壁,水冷壁的输出端连接锅炉的给水口。
优选的,再燃喷口设置在锅炉中sofa风的下部。
优选的,过滤器采用陶瓷过滤器。
优选的,催化剂层采用cu-mn/al2o3催化剂。
与现有技术相比,本实用新型具有以下有益的技术效果:
本实用新型利用煤粉气化产生的co和h2来还原锅炉烟气中的氮氧化物,在不喷氨的条件下实现电站锅炉氮氧化物超低排放,解决了喷氨脱硝中氨耗量大和氨逃逸高的问题。一级高温还原的还原剂co来自煤粉,无额外物料消耗,在一级还原后能够在低温条件下采用非贵金属催化剂进行二级还原,技术经济性高。通过煤粉部分气化、co高温还原、co低温催化还原三者协同作用,逐级降低氮氧化物浓度,其中高温还原段nox浓度控制在150mg/m3以内,低温还原段nox浓度控制在50mg/m3以内。气化炉可以与已有燃煤锅炉联用,从而完成对现有火电机组的低氮燃烧改造。
煤粉在旋风分离器中进行粗细分离,粗煤粉进入气化炉,可以提高煤气中co收率;细煤粉进入锅炉燃烧,可以提高着火稳定性。气化生成的煤气主要送入锅炉再燃区燃烧,在保证co燃尽的同时产生协同脱硝的效果。
由于燃烧阶段产生的氮氧化物已显著降低,催化剂体积可以减小,则催化剂和喷枪可以布置在尾部烟道内,而无需外置烟道,进一步降低了系统复杂性,可以用于现有燃煤锅炉烟气脱硝改造。
附图说明
图1为本实用新型所述的煤粉部分气化协同脱硝系统的结构示意图。
图中:1.煤仓、2.磨煤机、3.一次风管、4.燃烧器喷口、5.锅炉、6.旋风分离器、7.气化炉、8.煤气出口、9.再燃喷口、10.过滤器、11.喷枪、12.催化剂层、13.尾部烟道。
具体实施方式
下面结合具体的实施例对本实用新型做进一步的详细说明,所述是对本实用新型的解释而不是限定。
本实用新型一种煤粉部分气化协同脱硝系统,利用煤粉气化产生的co来经济高效的还原锅炉烟气中的氮氧化物,完全不同于目前火电厂烟气脱硝普遍采用的氨作为还原剂,避免了过量喷氨引起的氨耗量大和氨逃逸高的问题。
其中,脱硝系统如图1所示,包括煤仓1、磨煤机2、锅炉5、旋风分离器6、气化炉7和过滤器10;煤仓1的出煤口连接磨煤机2入口,磨煤机2的煤粉出口分别连接旋风分离器6入口和锅炉5主燃区设置的燃烧器喷口4,磨煤机2的煤粉出口接入一次风管3,用于通过接入的一次风进行煤粉的输送;旋风分离器6用于对煤粉进行粗细分离,细煤粉出口连接燃烧器喷口4将细煤粉送入锅炉5中燃烧,粗煤粉出口连接气化炉7进口,将粗煤粉在气化炉7中气化生成煤气;气化炉7的煤气出口8分为两路,一路经再燃喷口9接入锅炉5的折焰角区域,另一路经过滤器10过滤掉灰分后接入尾部烟道13,尾部烟道13经喷枪将煤气接入尾部烟道13,尾部烟道13内位于喷枪下游设置催化剂层12。
本优选实例中,过滤器10采用陶瓷过滤器;空预器尾部的尾部烟道13温度为120-140℃;催化剂层12采用cu-mn/al2o3催化剂。
本实用新型协同脱硝系统使用时。
1)煤仓1中的原煤经过磨煤机2研磨后成为煤粉,由一次风管3通入的一次风携带送入锅炉5和气化炉7,本实例中以进入气化炉7中的煤粉占10-20%,进入锅炉5中的煤粉占80-90%为例。煤粉挥发分高(如褐煤和烟煤),则减小进入气化炉中的煤粉比例;煤粉挥发分低(如无烟煤),则增加进入气化炉中的煤粉比例。进入气化炉中的煤粉量通过一次风调门控制。
2)煤粉在旋风分离器6中进行粗细分离,细煤粉通过燃烧器喷口4送入锅炉5中燃烧,粗煤粉进入气化炉7中气化生成煤气。煤气主要成分为co、h2、co2和n2。气化炉7采用气流床方式,气化剂为空气,煤粉气化需要的热量来自焦炭燃烧,不需要从锅炉引入热量。气化炉中设有水冷壁,吸收煤粉气化燃烧放出的热量,并加热锅炉给水,从而提高锅炉热效率。
3)煤气通过再燃喷口9送入锅炉5中燃烧,再燃喷口9位于锅炉5中sofa风的下部。co燃尽生成co2并放出热量,同时煤气中的co和h2会在锅炉壁面和烟气飞灰中金属氧化物的催化作用下还原烟气中的氮氧化物,生成n2和h2o。
4)煤气在过滤器10中过滤掉灰分后,通过喷枪11送入尾部烟道13中,在催化剂层12的作用下,与烟气中的氮氧化物反应生成n2和h2o,从而降低锅炉nox排放。喷枪11中co流量根据氮氧化物检测值进行调节,一般为ppm量级。
步骤3)中未反应完的co能够在尾部烟道催化剂层中参与脱硝反应,从而减少co逃逸。喷枪11和催化剂层12均布置在尾部烟道13中。催化剂层12采用cu-mn/al2o3催化剂,在120-140℃温度范围内,能够达到70%的脱硝效率。与现有技术不同的是,催化剂层12布置在空预器尾部,烟气温度范围120-140℃。
起点商标作为专业知识产权交易平台,可以帮助大家解决很多问题,如果大家想要了解更多知产交易信息请点击 【在线咨询】或添加微信 【19522093243】与客服一对一沟通,为大家解决相关问题。
此文章来源于网络,如有侵权,请联系删除


