一种含有机硅烷废气废液焚烧系统的制作方法



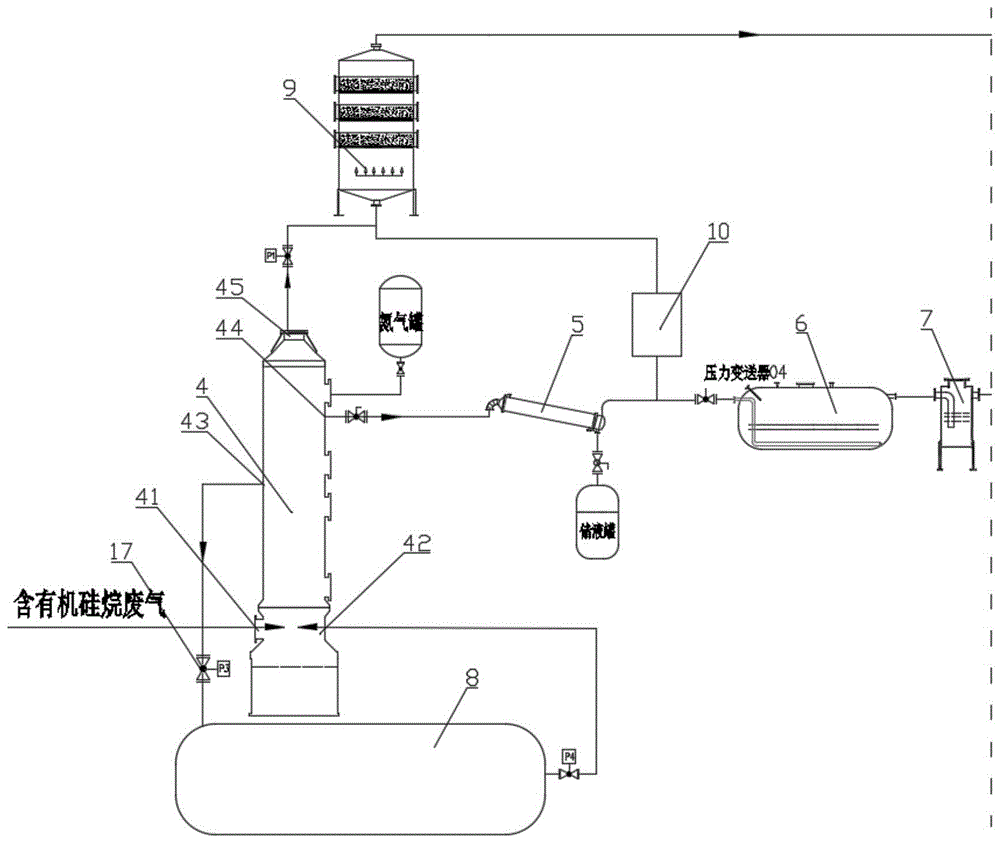
本实用新型涉及废气、废液的焚烧处理技术领域,尤其涉及一种含有机硅烷废气废液焚烧系统。
背景技术:
目前,国内多晶硅相关产业在生产过程中,冷氢化尾气急冷工序与精馏工序、合成尾气精馏工序、还原尾气精馏工序中都会不可避免产生部分氯硅烷残液。多晶硅生产企业在生产多晶硅原料过程中产生大量含氯硅烷、氢气、氯化氢等污染物,上述废气/废液的处理问题已成为限制多晶硅发展的瓶颈之一,国外对多晶硅氯硅烷残液中存在的高附加值组分硅烷的回收的研究相当热门而我国在此方面的研究仍处于空白阶段硅烷作为一种提供硅组分的气体源,可用于制造高纯度多晶硅、单晶硅、微晶硅、非晶硅、氮化硅、氧化硅、异质硅、各种金属硅化物。硅烷广泛应用于微电子、光电子工业,用于制造太阳电池、平板显示器、玻璃和钢铁镀层。硅烷又以它特有的自燃、爆炸性而著称。硅烷有非常宽的自发着火范围和极强的燃烧能量,决定了它是一种高危险性的气体。
目前处理方法主要采用淋洗塔喷淋去除大部分污染物后高空排放。由于处理方法的不完善等原因,导致现场工作环境差、污染严重,这部分残液主要由以高氯化硅为主的氯硅烷、硅粉为主的杂质废气废液、含有高附加值组分高氯硅烷等构成。目前国内大部分企业采用粗放式的水解方式处理此残液,原料浪费严重、水解操作环境恶劣并对设备、成本需求高。部分不良企业甚至直接排放至环境,或者简单对工艺产生的废气废液(废水)进行焚烧后直排,废气废液中含有机硅烷、氯硅烷等成分,焚烧后尾气中会有:二氧化硅、氮氧化物、二噁英、氯化氢等有害气体形成二次污染问题,对环境造成了极大的破坏。因此,迫切针对有机硅烷废气废水合理化处置工艺,对废气中的氯硅烷和氯化氢气体进行有效的去除处理。安全连续化生产及处理尾气排放满足国家环保允许的排放标准,有利于节能减排。
技术实现要素:
为解决上述问题,本实用新型的目的在于提供一种安全环保、可连续化生产的含有机硅烷废气废液焚烧系统。
本实用新型采用的技术方案为:
一种含有机硅烷废气废液焚烧系统,包括依次连接的一次焚烧室、二次焚烧室以及尾气净化装置,含有机硅烷废气经废气预处理装置送入一次焚烧室内,含有机硅烷废液经高压雾化装置送入一次焚烧室内,其特征在于,所述废气预处理装置包括依次连接的喷淋水洗塔、冷凝器、水封罐以及阻火器,所述喷淋水洗塔包括废气进口ⅰ、废气进口ⅱ、废气出口ⅰ、废气出口ⅱ、废气出口ⅲ,废气进口ⅰ通入外部含有机硅烷废气,废气进口ⅱ和废气出口ⅰ连接废气缓存罐,废气出口ⅱ连接冷凝器,废气出口ⅲ连接活性炭吸附罐;所述冷凝器另通过气体检测仪连接活性炭吸附罐。
进一步地,所述尾气净化装置包括依次连接的余热锅炉、高温陶瓷膜除尘器、急冷塔、水洗塔、碱洗塔、湿电除尘器以及烟囱;所述活性炭吸附罐连接烟囱。
进一步地,所述废气进口ⅱ、废气出口ⅰ、废气出口ⅱ、废气出口ⅲ与所对应设备的连接管道上均安装有阀门。
进一步地,所述余热锅炉的炉膛为全膜式壁结构,且其上安装有若干弹簧锤振打装置,防止炉膛积灰结渣、阻塞。
进一步地,所述余热锅炉的炉膛下部为锥形结构,利于烟气中形成的二氧化硅灰渣的自然沉降。
上述的含有机硅烷废气废液焚烧系统的处理工艺,包括如下步骤:
s1、将含有机硅烷废气送入喷淋水洗塔内进行氯硅烷气体和氯化氢气体的吸收,经喷淋水洗塔喷淋处理后的废气通过冷凝器进行冷凝,冷凝所得的高氯硅烷等液体回收,冷凝后的废气经过水封罐和阻火器的防输送回火爆炸处理后,再送入一次焚烧炉内燃烧;与此同时含有机硅烷废液经雾化同步喷入一次焚烧炉内燃烧;其中一次焚烧炉内燃烧温度为750-850℃,烟气滞留时间为1.5-2秒;
s2、将s1产生的烟气送入二次焚烧室内燃烧;其中二次焚烧室内燃烧温度为950-1100℃,烟气滞留时间2秒;
s3、将s2产生的烟气送入余热锅炉进行余热回收,使烟气温度降低到550℃,烟气中的二氧化硅在余热锅炉内冷却形成灰渣回收,烟气最后经净化处理后排放。
其中,s1中的喷淋水洗塔内压力控制在1~5kpa;当喷淋水洗塔内压力达到上限时,将废气抽存到废气缓存罐内暂存,继续超压时,则将废气通入活性炭吸附罐经过吸附处理后泄压排放;当喷淋水洗塔内压力处于负压状态时,废气从废气缓存罐中返至喷淋水洗塔,继续负压时,向喷淋水洗塔内通入氮气升压。
其中,s1中经冷凝器冷凝处理后的废气进行氧含量、有机废气浓度实时检测,当氧含量低于5%或有机废气浓度低于10%时,废气正常进行后续燃烧处理;氧含量超过5%或有机废气浓度超过25%时,废气紧急自动切换通入活性炭吸附罐经过吸附处理后再排放。
其中,s3中的净化处理包括:除尘、碱洗处理。
本实用新型的有益效果为:采用废气预处理装置,确保含有机硅烷废气在输送处置过程中爆炸事故等安全问题彻底消除,生产系统的稳定性得到改善、有害物质在废气废液焚烧炉内充分燃烧,同时以副产物的形式回收烟气中的氯硅烷、氯化氢和二氧化硅等,剩余烟气经尾气处置设备后达标排放,有利于节能减排。
附图说明
图1为本申请的废气预处理部分的结构示意图。
图2为本申请的焚烧处理部分的结构示意图。
图3为本申请的尾气净化处理部分的结构示意图。
图4为本申请的工艺流程图。
图中:一次焚烧室1、二次焚烧室2、高压雾化装置3、喷淋水洗塔4、废气进口ⅰ41、废气进口ⅱ42、废气出口ⅰ43、废气出口ⅱ44、废气出口ⅲ45、冷凝器5、水封罐6、阻火器7、废气缓存罐8、活性炭吸附罐9、气体检测仪10、高温陶瓷膜除尘器11、急冷塔12、水洗塔13、碱洗塔14、湿电除尘器15、烟囱16、阀门17、弹簧锤振打装置18、余热锅炉19。
具体实施方式
下面将结合附图对本实用新型实施例中的技术方案进行清楚、完整地描述。
实施例1
如图1-4所示,一种含有机硅烷废气废液焚烧系统,包括依次连接的一次焚烧室1、二次焚烧室2以及尾气净化装置,尾气净化装置包括依次连接的余热锅炉19、高温陶瓷膜除尘器11、急冷塔12、水洗塔13、碱洗塔14、湿电除尘器15以及烟囱16,其中,余热锅炉19的炉膛为全膜式壁结构,且其上安装有若干弹簧锤振打装置18,防止炉膛积灰结渣、阻塞,余热锅炉19的炉膛下部为锥形结构,利于烟气中形成的二氧化硅灰渣的自然沉降;
含有机硅烷废气经废气预处理装置送入一次焚烧室1内,含有机硅烷废液经高压雾化装置3送入一次焚烧室1内,废气预处理装置包括依次连接的喷淋水洗塔4、冷凝器5、水封罐6以及阻火器7,所述喷淋水洗塔4包括废气进口ⅰ41、废气进口ⅱ42、废气出口ⅰ43、废气出口ⅱ44、废气出口ⅲ45,废气进口ⅰ41通入外部含有机硅烷废气,废气进口ⅱ42和废气出口ⅰ43连接废气缓存罐8,废气出口ⅱ44连接冷凝器5,废气出口ⅲ45连接活性炭吸附罐9,废气进口ⅱ42、废气出口ⅰ43、废气出口ⅱ44、废气出口ⅲ45与所对应设备的连接管道上均安装有阀门17;冷凝器5另通过气体检测仪10连接活性炭吸附罐9,活性炭吸附罐9连接烟囱16。
上述含有机硅烷废气废液焚烧系统的处理工艺,具体包括如下步骤:
s1、将含有机硅烷废气送入喷淋水洗塔4内进行氯硅烷气体和氯化氢气体的吸收,经喷淋水洗塔4喷淋处理后的废气通过冷凝器5进行冷凝,冷凝所得的高氯硅烷等液体回收,冷凝后的废气经过水封罐6和阻火器7的防输送回火爆炸处理后,再送入一次焚烧炉内燃烧;与此同时含有机硅烷废液经雾化同步喷入一次焚烧炉内燃烧;其中一次焚烧炉内燃烧温度为750-850℃,烟气滞留时间为1.5-2秒;
s2、将s1产生的烟气送入二次焚烧室2内燃烧;其中二次焚烧室2内燃烧温度为950-1100℃,烟气滞留时间2秒;
s3、将s2产生的烟气送入余热锅炉19进行余热回收,使烟气温度降低到550℃,烟气中的二氧化硅在余热锅炉19内冷却形成灰渣回收,烟气最后经净化处理后排放。
其中,s1中的喷淋水洗塔4内压力控制在1~5kpa;当喷淋水洗塔4内压力达到上限时,将废气抽存到废气缓存罐8内暂存,继续超压时,则将废气通入活性炭吸附罐9经过吸附处理后泄压排放;当喷淋水洗塔4内压力处于负压状态时,废气从废气缓存罐8中返至喷淋水洗塔4,继续负压时,向喷淋水洗塔4内通入氮气升压。
其中,s1中经冷凝器5冷凝处理后的废气进行氧含量、有机废气浓度实时检测,当氧含量低于5%或有机废气浓度低于10%时,废气正常进行后续燃烧处理;氧含量超过5%或有机废气浓度超过25%时,废气紧急自动切换通入活性炭吸附罐9经过吸附处理后再排放。
其中,s3中的净化处理包括:除尘、碱洗处理。
含有机硅烷废气进入废气预处理装置控制说明:
1、生产过程中不同时段产生废气量存在较大波动,废气汇集至喷淋水洗塔4,当废气量超出输入焚烧量时候,为避免车间密闭管路频繁泄压报警,本工艺设计废气缓存罐8,废气缓存罐8为真空型储罐,起到库容缓存作用。
2、控制目标:生产密闭管路(喷淋水洗塔4)控制压力范围1-5kpa。
3、控制模式及控制原理:分为手动优先模式与自动模式,自动模式分为:a.停产待机模式;b.生产焚烧运行模式,控制如下:
a.停产待机模式:
停产待机模式:启动后废气缓存罐8如未在排空时间保持现有状态,此前生产焚烧模式结束前程序设计将废气缓存罐8抽空至上限0.06mpa(可调设置),当压力达到上限5kpa时自动开启阀门p3将废气抽存到废气缓存罐8使系统压力降至3kpa并关闭p3。随废气缓存罐8内废气含量增加,真空度下降从而使抽气速度下降,以至存储能力下降不能及时抽存废气,则程序设计在开启阀门p3后,n秒内(预设)压力仍处于上升状态,补开阀门p1使废气通入活性炭吸附罐9泄压至3kpa,p1开启时黄字提示,控制屏幕显示“喷淋塔泄压”
当压力低于1kpa或到达设定废气缓存罐8排空时间时,控制指令阀门p3关闭,p4阀门开启,真空泵启动将废气抽到喷淋水洗塔4,当主传感器感知超压后开启阀门p1废气紧急排放至活性炭吸附罐9,废气缓存罐8内排空至0.06mpa后(可设置),自动关闭阀门p4,喷淋塔复压3kpa后p1阀门关闭。
b.生产焚烧运行模式,控制如下:
焚烧程序启动运行,一次焚烧室1、二次焚烧室2完成点火准备,点火正常升温,停产待机模式自动转换焚烧运行模式。此时,废气缓存罐8排空时间由定时转换为实时监控,喷淋水洗塔4内压力仍保持在1-5kpa之间,持续向冷凝器5、水封罐6、阻火器7直至一次焚烧室1内增压输送废气。
4、冷凝器运行控制
停产待机模式期间,冷凝器5与喷淋水洗塔4处于断路状态,生产焚烧运行模式期间,冷凝器5启动运行,一是为降低废气温度,避免输送过程中发生燃烧现象,二是通过冷凝将废气冷凝可得到高氯硅烷等液体进行回收处理。
5、气体检测仪运行控制
为避免输送废气中氧含量和有机废气浓度达到爆炸浓度,在管路设置采样式气体检测仪10,微量样气经检测排入活性炭吸附罐9,时刻监控废气输送管路中的氧含量和有机废气浓度。氧含量低于5%或有机废气浓度低于10%时(废气中物质爆炸极限下限),废气进入水封罐6、阻火器7准备进入一次焚烧室1处置;当氧含量超过5%或有机废气浓度超过25%时(废气中物质爆炸极限上限),废气进入活性炭吸附罐9应急排放,系统指令发出报警,当含氧量和有机废气浓度恢复到位于爆炸极限下限以下后,解除报警,继续正常焚烧处理。
6、水封罐运行控制
设计水封罐6目的:在水封罐6设计压力变送器o4或压力开关,当废气输送过量或焚烧异常时因切断废气进入后续设备,至水封罐6增压大于设定上限压力(可调设置)时,则紧急泄压外排并发出声光报警,保障运行安全;当检测水封罐6内压力降至上限以下时,停止外排泄压,报警解除;当水封罐6内压力低于设定下限值时,切断废气进入后续设备并发出报警,此状况通过持续增加废气量解除报警。
7、阻火器前运行控制
当废气废液焚烧炉火焰检测到炉内熄火状态、炉内不在控制压力、炉内超温等异常情况时,切断废气进入后续设备并进行废气泄压,避免管路系统中残留可燃气体进入焚烧炉,避免再起炉时候产生瓦斯气体爆炸。
可以理解的是,以上实施方式仅仅是为了说明本实用新型的原理而采用的示例性实施方式,然而本实用新型并不局限于此。对于本领域内的普通技术人员而言,在不脱离本实用新型的原理和实质的情况下,可以做出各种变型和改进,这些变型和改进也视为本实用新型的保护范围。
起点商标作为专业知识产权交易平台,可以帮助大家解决很多问题,如果大家想要了解更多知产交易信息请点击 【在线咨询】或添加微信 【19522093243】与客服一对一沟通,为大家解决相关问题。
此文章来源于网络,如有侵权,请联系删除


