一种含碳固废燃烧利用与烧结烟气净化处理的耦合系统的制作方法



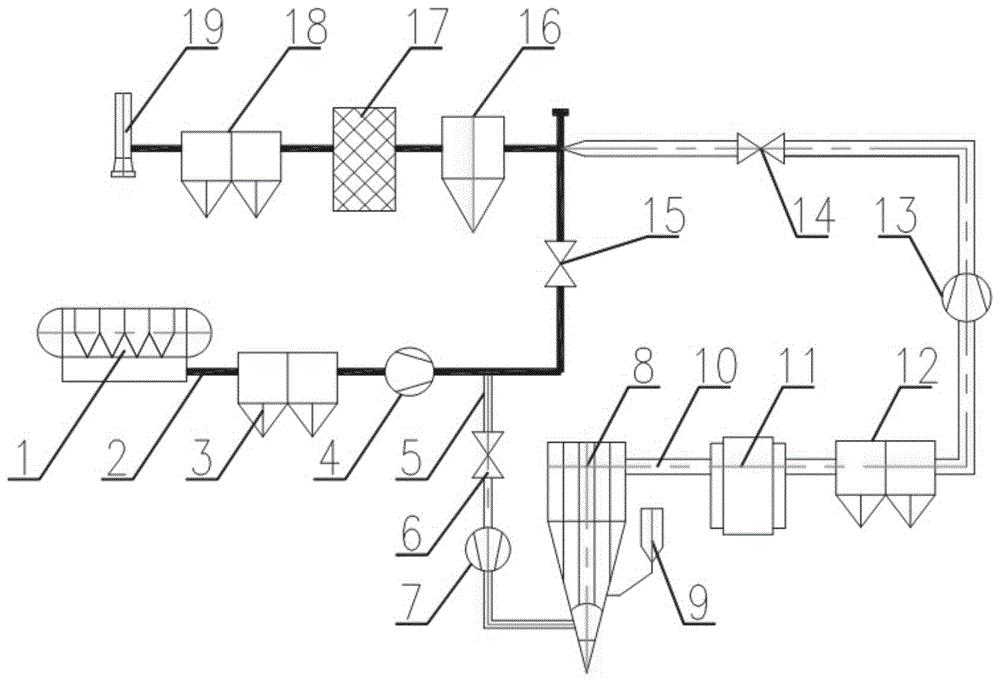
本实用新型属于含碳固废燃烧利用领域,具体涉及一种含碳固废燃烧利用与烧结烟气净化处理的耦合系统,其通过将烧结生产、含碳固废燃烧两个过程耦合,实现了最终烟气的超净排放,同时可有效回收含碳固废和烧结烟气的热能,实现了节能降耗。
背景技术:
:在我国以煤炭为主要能源,目前,每年煤炭消费量约为40亿吨,2020年3月份我国煤产量约3.5亿吨。我国煤的70%是通过燃烧被利用的,典型的应用燃煤电厂、燃煤热力厂等等。煤的燃烧利用过程会产生so2、nox、粉尘等污染物,为了降低燃煤污染物,煤的洗选是优先选择。煤的洗选是洁净煤技术的重要组成部分,通过洗选降低煤的灰分、硫分改善煤质。有资料显示:洗选1亿吨原煤,一般可以减少燃煤排放so2约100~150万吨。为进一步改善大气质量,洗选煤的比例会逐渐增高。煤炭清洁高效利用行动计划(2015-2020年)中提出:到2020年,原煤入选率达到80%以上。而洗选煤会产生煤矸石、煤泥两种含碳固废,为了利用煤矸石、煤泥中的化学能,大部分采用传统的燃烧方式。然而采用传统的燃烧方式,含碳固废含有的污染物只是发生了转移,而没有真正消除,洗选煤的效果会大打折扣。如果燃烧烟气处理不当或变成散烧利用,还会造成污染物排放增加。为了降低煤及含碳固体燃料排放的污染物量,开发研制更高效率的脱硫、脱硝技术成为首选目标。然而上述技术路线成本较高,且能耗较大,在污染物的排放量上存在瓶颈。我国庞大的钢铁产业是有可能同含碳固体燃烧利用相耦合联动的,通过钢铁生产的某个工序同含碳固废燃烧之间的耦合发展,有可能实现含碳固废或煤炭的燃烧利用零排放。因此,有必要细分钢铁生产各个工序的特点,并将含碳固体燃烧镶嵌在其中的某个生产单元中,开发一种含碳固废燃烧利用烟气污染零排放技术,实现洗选煤的真正目的。烧结生产是现代钢铁生产的重要工艺单元之一,密封完好的大型烧结机吨矿产生的烟气量也有~3000m3。未经处理的烧结烟气含有co、co2、n2、o2、so2、nox、h2o、二噁英及各种粉尘等,其中体积占比含量分别为:co~1%、o2~16%、h2o~10%、粉尘~10g/m3、二氧化硫含量一般在800~1500mg/nm3,氮氧化物含量在100~450mg/nm3,二噁英浓度~3ng-teq/nm3。烧结烟气平均温度~150℃,物理热~195kj/nm3,烧结烟气co~1%,烟气化学热~120kj/nm3。国内钢铁公司的烧结厂,其烧结烟气经过脱硫、脱销、除尘,达到国家制定的排放标准后排入大气。烧结烟气在净化处理过程中,烟气中含有的co不能处理掉,随烟气排入大气中。现有的处理设施对消除二噁英作用也不明显,在排放至大气时也会对大气造成污染。另外,从已运行的烧结生产系统分析,烧结烟气中所含的物理热也没有得到有效利用。技术实现要素:鉴于现有技术的不足,本实用新型旨在于提供一种含碳固废燃烧利用与烧结烟气净化处理的耦合系统,其通过将烧结生产、含碳固废燃烧两个过程耦合,实现了最终烟气的超净排放,同时可有效回收含碳固废和烧结烟气的热能,实现了节能降耗。为了实现上述目的,本实用新型采用的技术方案如下:本实用新型提供的一种含碳固废燃烧利用与烧结烟气净化处理的耦合系统包括烧结系统和连接所述烧结系统的烧结烟气净化处理系统,其中,作为本实用新型的一种改进,该耦合系统还包括含碳固废燃烧利用系统,所述含碳固废燃烧利用系统的烧结烟气引出端与所述烧结系统的下游端连接,所述含碳固废燃烧利用系统的下游端烟气汇流口与所述烧结烟气净化处理系统连接。优选地,在上述的含碳固废燃烧利用与烧结烟气净化处理的耦合系统中,所述烧结系统包括烧结机,所述烧结机的烧结主烟道沿着烟气流动方向,依次连接有静电除尘器、主抽风机和烧结主烟道阀门,所述烧结烟气净化处理系统连接在所述烧结主烟道阀门的下游端。优选地,在上述的含碳固废燃烧利用与烧结烟气净化处理的耦合系统中,所述含碳固废燃烧利用系统包括连接在所述烧结主烟道上的烧结烟气引出烟道,其烧结烟气引出端设在所述烧结主烟道在位于所述主抽风机和所述烧结主烟道阀门之间的位置处,所述烧结烟气引出烟道沿着烟气流动方向依次连接有反应炉前阀门、前引风机和反应炉,所述反应炉连接有含碳固废仓,所述反应炉内集成有脱硫反应模块和脱硝反应模块,所述反应炉的烟气排出口连接有燃烧后烟道,所述燃烧后烟道上连接有取热器,所述燃烧后烟道的下游端烟气汇流口连接在所述烧结主烟道在位于所述烧结主烟道阀门和所述烧结烟气净化处理系统之间的位置处,所述燃烧后烟道在靠近其下游端烟气汇流口的位置处设有反应炉后阀门。优选地,在上述的含碳固废燃烧利用与烧结烟气净化处理的耦合系统中,沿着所述燃烧后烟道的烟气流动方向,所述燃烧后烟道在位于所述取热器的下游端依次设有反应炉除尘器和后引风机。优选地,在上述的含碳固废燃烧利用与烧结烟气净化处理的耦合系统中,所述烧结烟气净化处理系统包括沿着所述烧结主烟道的烟气流动方向,依次连接在所述烧结主烟道下游端的烧结脱硫塔、烧结脱硝装置、烟气净化除尘器和烟囱。本实用新型有益效果:1、实现了含碳固废燃烧利用烟气污染零排放,烧结生产、含碳固废燃烧两个过程耦合,在反应炉内,使用烧结烟气助燃,在反应炉内实现部分脱硫、脱硝反应。排出反应炉的烟气经过取热、除尘后进入烧结生产已有的烧结烟气净化处理工序进行再次处理,实现了最终烟气的超净排放。在整个工艺生产过程中,没有增加新的烟气排放点,从总排放量看实现了含碳固废的燃烧利用和烟气污染的零排放。2、实现了节能降耗,含碳固废燃烧利用、烧结烟气净化处理两个过程相耦合,烧结烟气中的co~1%化学热~120kj/nm3,可以有效利用。同时可有效回收烧结烟气~150℃的物理余热,降低了有效单位取热量的能耗。3、在反应炉内,含碳固废同烧结烟气发生燃烧反应,反应炉中烟气里的二噁英可被彻底分解,进一步减少了污染物的排放。附图说明图1为本实用新型所述耦合系统的结构示意图。具体实施方式为使本实用新型实施例的目的、技术方案和优点更加清楚,下面结合附图以及具体实施例将对本实用新型的技术方案进行清楚、完整地描述。请参见图1,如图1所示,本实用新型公开的一种含碳固废燃烧利用与烧结烟气净化处理的耦合系统包括烧结系统和连接烧结系统的烧结烟气净化处理系统。该耦合系统还包括含碳固废燃烧利用系统,该含碳固废燃烧利用系统的烧结烟气引出端与烧结系统的下游端连接,该含碳固废燃烧利用系统的下游端烟气汇流口与烧结烟气净化处理系统连接。进一步地,如图1所示,烧结系统包括烧结机1,该烧结机1的烧结主烟道2沿着烟气流动方向,依次连接有静电除尘器3、主抽风机4和烧结主烟道阀门15,烧结烟气净化处理系统连接在烧结主烟道阀门15的下游端。具体地,请继续参见图1所示,该含碳固废燃烧利用系统包括连接在烧结主烟道2上的烧结烟气引出烟道5,该烧结烟气引出烟道5的烧结烟气引出端设在烧结主烟道2在位于主抽风机4和烧结主烟道阀门15之间的位置处。烧结烟气引出烟道5沿着烟气流动方向依次连接有反应炉前阀门6、前引风机7和反应炉8,反应炉8连接有含碳固废仓9。反应炉8内集成有脱硫反应模块和脱硝反应模块,反应炉8的烟气排出口连接有燃烧后烟道10,燃烧后烟道10上连接有取热器11。燃烧后烟道10的下游端烟气汇流口连接在烧结主烟道2在位于烧结主烟道阀门15和烧结烟气净化处理系统之间的位置处。为防止烧结主烟道2中的烧结烟气从燃烧后烟道10在靠近该燃烧后烟道10下游端烟气汇流口返流到该燃烧后烟道10,该燃烧后烟道10在靠近其下游端烟气汇流口的位置处设有反应炉后阀门14。进一步地,在本实用新型的优选实施例中,如图1所示,沿着燃烧后烟道10的烟气流动方向,该燃烧后烟道10在位于取热器11的下游端依次设有反应炉除尘器12和后引风机13。前引风机7和后引风机13作为烟气流动的动力源,前引风机7可将烧结主烟道2中的部分或全部烧结烟气作为助燃空气从烧结主烟道2与烧结烟气引出烟道5的连接位置引出至烧结烟气引出烟道5,再经烧结烟气引出烟道5引入反应炉8。通过反应炉前阀门6和烧结主烟道阀门15可控制烧结主烟道2中的烧结烟气的引出量。进一步地,在本实用新型的优选实施例中,如图1所示,烧结烟气净化处理系统包括沿着烧结主烟道2的烟气流动方向,依次连接在烧结主烟道2下游端的烧结脱硫塔16、烧结脱硝装置17、烟气净化除尘器18和烟囱19。本实用新型的工作流程为:烧结机1产生的烧结烟气进入烧结主烟道2中,经过静电除尘器3、主抽风机4后,部分或全部的烧结烟气被引出到烧结烟气引出烟道5中,引出的烧结烟气经过反应炉前阀门6、前引风机7进入到反应炉8中。储存在含碳固废仓9里的含碳固废,也进入到反应炉8内。在反应炉8内,被引入的烧结烟气同反应炉8中的含碳固废发生燃烧反应,并且在反应炉8内完成炉内烟气的部分脱硫、脱硝反应。然后从反应炉8排出的烟气进入到燃烧后烟道10,并通过取热器11完成热量交换,将高温烟气中的热量进行吸收,使高温烟气变为低温烟气。经过取热器11排出的低温烟气接着进入反应炉除尘器12进行除尘。然后再经过后引风机13、反应炉后阀门14,重新回到原来烧结机1配套的烧结烟气净化处理系统内,此时汇流至烧结烟气净化处理系统的烟气是经过反应炉1内燃烧反应后的烟气,该烟气中的一氧化碳含量和二噁英含量都得到了大幅降低,且烟气经过烧结烟气净化处理系统的烧结脱硫塔16、烧结脱硝装置17、烟气净化除尘器18依次完成脱硫、脱硝、除尘,最后由烟囱19排出。当烧结烟气全部进入反应炉8时,烧结主烟道阀门15完全关闭,反应炉前阀门6、反应炉后阀门14完全打开。当需要部分烧结烟气进入反应炉8时,通过调节烧结主烟道阀门15、反应炉前阀门6、反应炉后阀门14的开度实现流量调节。当烧结烟气全部需要由原来的气体净化系统处理时,烧结主烟道阀门15完全打开,反应炉前阀门6、反应炉后阀门14完全关闭,其耦合过程和耦合度可灵活调节控制,操作使用方便,设备成本低,烧结生产和含碳固废的燃烧利用的工艺和设备之间耦合施工成本小。为进一步描述本实用新型的超净排放过程,下面对该工作原理进行详细说明:现有的煤矸石、洗煤煤泥等含碳固废的燃烧利用,一般是进入锅炉燃烧产生蒸汽,烟气经过脱硫、脱硝、除尘等净化处理达到超净排放标准后排放。目前执行电厂锅炉烟气超净排放标准,电厂锅炉烟气超净排放指标如下表1所示:表1序号参数单位数值1粉尘浓度mg/nm3102so2浓度mg/nm3353nox浓度mg/nm350按照上述排放标准排放,含碳固废在燃烧利用后的烟气中仍有大量污染物排入大气。而现有的钢铁生产烧结工艺产生的烧结烟气经过除尘、脱硫、脱硝处理后,可实现超净排放。目前钢铁生产烧结工艺中的超净排放的标准同样电厂锅炉烟气超净排放标准相同。在目前的实际应用中,上述两种生产方式是同时平行进行的。其中,含碳固废燃烧后烟气排向大气的污染物为:含碳固废燃烧后烟气量×污染物排放浓度%。烧结烟气排向大气的污染物为:烧结烟气量×污染物排放浓度%。两种生产方式排向大气的污染物总量是:含碳固废燃烧后烟气量×污染物排放浓度%+烧结烟气量×污染物排放浓度%。而本实用新型的含碳固废燃烧利用与烧结烟气净化处理耦合过程,就是将全部或部分烧结烟气做为助燃风使用,在反应炉内与煤泥、煤矸石等含碳固废发生燃烧反应,将含碳固废含有的化学能转移到高温烟气中,使用取热器回收烟气热量,实现含碳固废资源化利用。同时,在内部集成有有脱硫反应模块和脱硝反应模块的反应炉1内,其在燃烧反应时,还伴随脱硫、脱硝反应。出反应炉1的烟气经过取热器11进行热交换,经过反应炉除尘器12进行除尘,然后回到烧结主烟道2,进入烧结系统原来已有的烧结烟气净化处理系统中进行再次的脱硫、脱硝、除尘处理。由于反应炉内集成的脱硫、脱硝功能,以及出反应炉的烟气经过了反应炉除尘器12进行了高效除尘,因此,重新汇流进入烧结主烟道2的这部分烟气的硫、硝、尘的含量均低于原烧结烟气中的含量。故,经过原烧结机配备的脱硫、脱硝、除尘装置后,经过烟囱19排放的烟气中的硫、硝、尘量较原来更低。进一步地可表述为:含碳固废燃烧利用与烧结烟气净化处理耦合联动,烧结烟气在反应炉1先完成含碳固废燃烧利用,然后再汇流进入烧结系统原来已有的烧结烟气净化处理系统中进行净化处理。上述两个过程耦合后向大气的污染物为:烧结烟气量×污染物排放浓度%。由于经过反应炉1后重新进入烧结主烟道烟气的硫、硝、尘的含量均低于原来烧结烟气中的含量,所以总的排放量没有增加,相当于含碳固废燃烧利用过程烟气污染零排放,且烟气中的一氧化碳含量和二噁英含量都得到了大幅降低。对于本领域的技术人员来说,可根据以上描述的技术方案以及构思,做出其它各种相应的改变以及变形,而所有的这些改变以及变形都应该属于本实用新型权利要求的保护范围之内。当前第1页1 2 3 
起点商标作为专业知识产权交易平台,可以帮助大家解决很多问题,如果大家想要了解更多知产交易信息请点击 【在线咨询】或添加微信 【19522093243】与客服一对一沟通,为大家解决相关问题。
此文章来源于网络,如有侵权,请联系删除



tips