铜杆生产过程中有机废气处理装置的制作方法



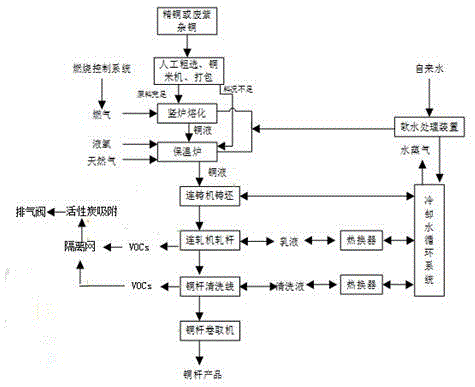
本实用新型涉及铜杆生产辅助设备领域,尤其涉及一种铜杆生产过程中有机废气处理装置。
背景技术:
铜杆是电线电缆生产中的主要原材料之一。
铜杆的常见生产工艺流程,参见图1,包括以下步骤:
a)分选、除杂和打包
企业主要购买精铜及在金属回收公司购买废紫杂铜作为原料,运送至厂区预处理车间进行预处理,主要进行人工分粗选,符合要求的原料过磅并进一步除杂(如精铜要除去油污、铜绿,废紫杂铜要去除油污、塑料、表面非铜金属等),不合格原料返回厂家。特别说明,企业购买的废紫杂铜原料分为两种,一种纯度较高废紫杂铜,另外一种含有塑料包裹的铜线,纯度较高废紫杂铜在原料预处理车间内采用“液压打包机”进行压实打包,将其压实打包成75cm×45cm×40cm的长方体铜包,铜包每块约重700kg,含有塑料包裹的铜线通过铜米机除杂处理成铜米,铜米机处理原料温度约为40℃左右,废塑料不会分解产生其他污染物,分离的塑料外销给塑料制品厂做为原料利用,企业严格限制含有塑料包装物及油污的原料进入下一步工序;
b)投料
①料况充足,使用竖炉生产时,铜包和铜米通过装载机运至铜杆车间进行暂时储存,铜包和铜米主要通过卷扬机料斗输送到竖炉上部加料口投料,进入燃气竖炉进行熔融和除杂,每次连续投料约1.5t;
②料况不足,使用保温炉生产时,铜包和铜米通过装载机运至铜杆车间进行暂时储存,铜包和铜米主要通过加料车投入保温炉进行熔融和除杂,每炉投料约120t,投料时间约8小时;
c)熔融
企业根据原料料况多少灵活安排工艺(原料直接投入坚炉或原料直接投入保温炉),铜熔融过程是将原料经高温熔融得到铜液。预处理后的原料投料进入燃气竖炉中或保温炉中,天然气燃烧(空气助燃或液氧助燃)提供热量将原料铜熔融成铜液,无论是精铜及废紫杂铜,其不是100%的纯铜,均含有一定量的低熔点、低密度及高氧亲和力杂质(如铁、锌等,其总量小于0.1%)与表面灰尘,这些低密度杂质及灰尘在高温熔化下,极易被氧化,其氧化物因密度低于铜,会上浮于铜液表面,为了保证铜精密加工的需要,须对这些铜液表面氧化物及灰尘扒出(简称扒渣),在扒渣过程中,为避免带出更多的铜水,需向铜水中投入相关辅料(玻璃渣、河沙、石灰、木炭)改善铜液的酸碱度、改善铜液的流动性,让这些杂质尽可能与铜水分离,减少带出铜水;
在此过程中,铜液会被部分氧化生成氧化亚铜(4cu+o2==2cu2o),这里需要控制氧含量在2000~7000ppm之间;扒渣后的铜水,属于高氧化特性金属,极易被氧化,要保证增加铜加工的进行,需要对铜水夺氧(简称还原),企业原环评中约定用树木还原,因树木还原烟气量大、灰尘大,且消耗绿色森林资源,企业现已改为用天燃气进行还原(还原原理为:4cu2o+ch4=8cu+2h2o+co2),还原后的铜水(氧含量一般控制在200ppm左右),可用于后续连铸连轧工序加工,为保证连铸连轧工序能够稳定可持续进行,需防止铜水进氧,采用木炭覆盖铜水(炉内铜水及流槽、浇包中的铜水均需覆盖防止进氧)的方式来控制进氧,原理为木炭中的c元素能够与氧较快亲和接触去除铜水的的氧,具有保护及还原功能;
企业竖炉采用空气与天燃气混合燃烧、保温炉采用全氧与天燃气混合燃烧,其烟气量及烟气温度全面下降,约为200度,烟气不再经过余热处理系统,直接进入烟气处理系统除尘、除黑;熔融过程产生的炉渣和经烟气处理设施收集的灰尘均做为一般固废外售;
d)铸造与轧制
保温炉中的合格铜液自出铜口流出,经流槽进入热顶水平连续铸造工序,通过铜杆连铸连轧生产线的连铸机、牵引机、滚剪、校直、铣角机、打毛机、连轧机、收杆机后,得到ф6mm—ф12mm规格的光亮低氧铜杆,再经过一道清洗工序进入铜杆卷取机,使其每捆卷成4t左右,入库待售;
在连轧机轧制铸坯过程中要使用乳化液,乳化液循环量是10m3/h,乳化液浓度为6%-8%,其他为软水;在连轧机轧杆过程中要使用清洗液,清洗液浓度为为3~5%,其他为软水,循环量是30m3/h,乳化液和清洗液通过热交换器不断与冷却水循环系统进行热交换,达到冷却的目的。乳化液和清洗液需保存在密闭的箱体内循环使用不外排,浓度低时定期补充。连铸连轧生产过程中使用的冷却水循环抽回水池,经冷却塔降温后循环使用。乳化液6%-8%浓度的主要成份为皂化液,其主要作用为高速运转的轧机部件(轧辊、轴承、轴)提供润滑、降温,还能部份保护铜坯不被氧化。清洗液3%-5%浓度的主要成份为乙醇,其主要作用是对快速轧制出的铜杆(温度约为600度)进行降温,降至常温满足包装需要,高温铜会被氧化,夺氧保证铜杆不会被氧化变色。
在上述的连铸机铸坯过程中,用作清洗和降温的乳化液和清洗剂遇到高温后会产生挥发性有机物vocs,即“有机废气”。
目前,对于该过程中产生的有机废气,常见的处理方式包括:1)加入催化剂进行催化反应去除,该方法需要额外加入催化剂,成本较高,且处理效率较低,能耗高;2)在连铸连轧工序中设有集气罩,集气罩收集vocs(温度约30-40℃)通过负压抽风后进入隔离网进行油雾液化、吸附后通过活性炭吸附后汇入主排气管道后由15m排气筒排放,如图1所示的,该方法会产生废弃活性炭,属于危险固废,对后续处理也带来麻烦,成本高、效率低。
技术实现要素:
本实用新型的目的就在于提供一种铜杆生产过程中有机废气处理装置,以解决上述问题。
为了实现上述目的,本实用新型采用的技术方案是这样的:一种铜杆生产过程中有机废气处理装置,包括燃烧室,所述燃烧室的顶部和底部分别设置有进气口,所述进气口分别连接顶部进气管道和底部进气管道,所述顶部进气管道的另一端连接连铸连轧工序中的集气罩,所述底部进气管道的另一端连接连铸连轧工序前端的保温炉;在所述燃烧室内部设置温度探头,在所述燃烧室的顶部和底部进气口分别设置气体流量控制阀。
参见图1,连铸连轧工序前端的保温炉会产生温度约为800℃的废气,简称“燃烧废气”,目前对于该“燃烧废气”的处理方式为直接排放,一方面造成热源浪费,另一方面也会造成大气污染;本实用新型将该燃烧废气通过设置单独的管道,将其引入燃烧室,从燃烧室底部进入,该管道具备保温功能,保证进入燃烧室的温度不低于500℃,从而可以直接将有机废气进行燃烧处理。
作为优选的技术方案:所述底部进气管道从外至内分别为钢板层、保温层、耐火砖和镁砖。
作为优选的技术方案:所述燃烧室外壁为碳钢层,内侧分别为耐火砖和镁砖。通过设置镁砖,防止高温损坏管道,通过设置保温层,比如保温棉,防止燃烧废气温度降低过快,确保燃烧废气到达燃烧室的温度不低于500℃。
作为优选的技术方案:所述气体流量控制阀为电动阀,且设置有用于控制调节所述气体流量控制阀的控制系统。可以实现自动控制,更方便更安全。
与现有技术相比,本实用新型的优点在于:本实用新型通过单独设置燃烧废气进气管道和燃烧室,从而可以充分利用铜杆生产过程中保温炉中产生的高热燃烧废气作为热源对有机废气进行燃烧处理,解决了传统的采用活性炭吸附造成的废弃活性炭危险固废的产生的问题,也不需要额外添加催化剂,也不需要单独通入天然气等能源,减少燃烧废气产生的同时节约了能源;也使有机废气的处理效率提高,采用本实用新型的装置处理效率可达90%以上,而传统方法仅50%左右,具有良好的经济效益和社会环保效应。
附图说明
图1为本实用新型背景技术中铜杆生产流程图;
图2为本实用新型的结构示意图;
图3为图2的a-a剖视图。
图中:1、燃烧室;2、顶部进气管道;3、底部进气管道;31、钢板层;32、保温层;33、耐火砖;34、镁砖;4、气体流量控制阀;5、集气罩;6、保温炉;7、温度探头。
具体实施方式
下面将结合附图对本实用新型作进一步说明。
实施例1:
参见图2和图3,一种铜杆生产过程中有机废气处理装置,包括燃烧室1,所述燃烧室1的顶部和底部分别设置有进气口,所述进气口分别连接顶部进气管道2和底部进气管道3,所述顶部进气管道2的另一端连接连铸连轧工序中的集气罩5,所述底部进气管道3的另一端连接连铸连轧工序前端的保温炉6,本实施例中,底部进气管道3使用钢板焊接成方形,设计引风量约2000m3/h;本实施例中,燃烧室尺寸为2m*3m*6m;在所述燃烧室1内部设置温度探头7,燃烧室7设置温度探7头,随时测量燃烧室内温度;有机废气从燃烧室顶部进气,燃烧废气从燃烧室底部进气;在所述燃烧室1的顶部和底部进气口分别设置气体流量控制阀4;所述底部进气管道3从外至内分别为钢板层31、保温层32、耐火砖33和镁砖34;所述燃烧室1外壁为碳钢层,内侧分别为耐火砖和镁砖,本实施例的气体流量控制阀4为手动阀,通过手动控制底部进气管道3进入的燃烧废气进气量,以及顶部进气管道2进入的有机废气进气量,确保有机废气与燃烧废气的体积比例达到1:1,从而保证有机废气燃烧完全。
实施例2:
本实施例中,所述气体流量控制阀4为电动阀,且设置有用于控制调节所述气体流量控制阀4的控制系统,其余与实施例1相同。通过控制系统自动控制底部进气管道3进入的燃烧废气进气量,以及顶部进气管道2进入的有机废气进气量,使得有机废气与燃烧废气的体积比例达到1:1。
以上所述仅为本实用新型的较佳实施例而已,并不用以限制本实用新型,凡在本实用新型的精神和原则之内所作的任何修改、等同替换和改进等,均应包含在本实用新型的保护范围之内。
起点商标作为专业知识产权交易平台,可以帮助大家解决很多问题,如果大家想要了解更多知产交易信息请点击 【在线咨询】或添加微信 【19522093243】与客服一对一沟通,为大家解决相关问题。
此文章来源于网络,如有侵权,请联系删除


