内循环低氮燃气燃烧器的制作方法



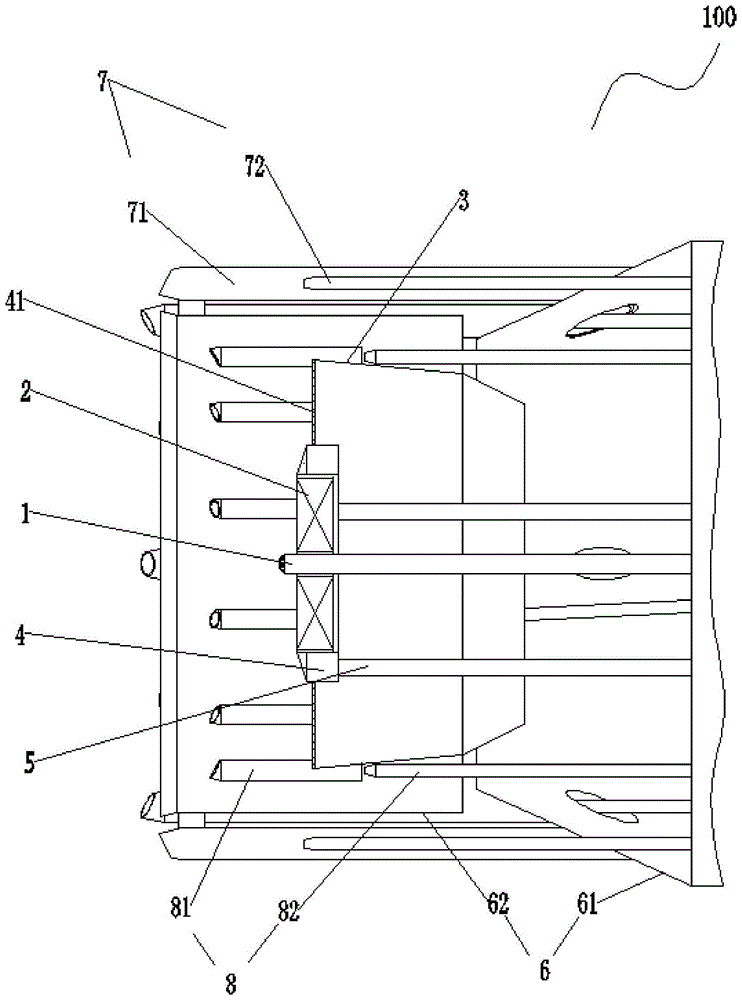
本发明涉及一种燃烧器领域,具体涉及一种内循环低氮燃气燃烧器。
背景技术:
烟气再循环技术是一种低氮技术,被广泛用于锅炉系统中,通过在锅炉尾部抽取一部分烟气直接送入锅炉内,或与一次风或二次风混合后再送入锅炉内。烟气再循环技术通过将烟气的燃烧产物加入到燃烧区域内,降低了燃烧温度,同时加入的烟气降低了氧气的分压,将减弱氧气与氮气生成热力型氮氧化物的过程,从而减少了氮氧化物的生成,研究表明,外部烟气循环将减少70%的氮氧化物生成。
市场上能广泛流通的机型是附加烟气外循环技术的扩散式燃烧器,以此来降低氮氧化物的排放量。此种类型燃烧器相对来说参数稳定由于其工作原理是利用风机将烟气进行循环燃烧,需要加大鼓风机的功率或使用烟循风机,造成投资成本的增加。
另外,多数现场烟气回收管道,烟气温度较高,助燃空气温度较低,在两者交汇处产生冷凝水,造成烟风道内的腐蚀,严重时冷凝水进入燃烧器导致火焰检测器感应及点火元件出现问题,产生安全隐患。
技术实现要素:
本发明是为了解决上述问题而进行的,目的在于提供一种稳定安全、使用成本低的内循环低氮燃气燃烧器。
本发明提供了一种内循环低氮燃气燃烧器,安装在锅炉燃烧室内,用于降低氮氧化物的排放,包括:第一燃气管,用于向燃烧室输送燃气,形成中心火焰;旋流器,套设在第一燃气管的外侧,用于分散第一燃气管输出的燃气;第二燃气管,用于向燃烧室输送燃气;环形燃气头,套设在旋流器的外侧并与第二燃气管连通,用于分散第二燃气管输出的燃气;分流管,套设在环形燃气头的外侧,用于对空气进行分流,形成混烟用空气以及混燃用空气,混燃用空气用于与环形燃气头以及第一燃气管输出的燃气混合形成可燃混合气;隔流件,套设在分流管的外侧,隔流件的内侧面与分流管的外侧面形成烟气通道,该烟气通道用于混合混烟用空气以及燃烧室内的烟气形成烟空混合气;多组内圈燃气组件,位于烟气通道内,多组内圈燃气组件输出的燃气与烟空混合气混合后形成烟空燃混合气;多组外圈燃气组件,安装在隔流件的周侧,多组外圈燃气组件输出的燃气与空气混合形成可燃混合气;其中,隔流件的周侧具有进烟口,燃烧室内的烟气通过进烟口进入烟气通道,并与混烟用空气混合形成烟空混合气后重新进入燃烧室燃烧。
在本发明提供的内循环低氮燃气燃烧器中,还可以具有这样的特征:其中,隔流件包括:渐缩管,用于接收空气;分隔管,一端安装在渐缩管的小端并与渐缩管的小端形成进烟口。
在本发明提供的内循环低氮燃气燃烧器中,还可以具有这样的特征:其中,多组外圈燃气枪组件均包括:导气管,一端与渐缩管连通,另一端伸出分隔管;第三燃气管,位于导气管内,其中,导气管靠近分隔管的端部为缩口,该缩口的方向远离中心火焰。
在本发明提供的内循环低氮燃气燃烧器中,还可以具有这样的特征,其中,多组内圈燃气枪组件均包括:第四燃气管,安装在渐缩管上,第四燃气管具有出气口,该出气口位于烟气通道内;混合管,安装在分流管的外侧面,混合管的一端连通出气口,另一端位于分隔管内;其中,混合管靠近分隔管的端部为缩口,该缩口的方向朝向中心火焰。
在本发明提供的内循环低氮燃气燃烧器中,还可以具有这样的特征:其中,分流管的外侧面与渐缩管的内侧面形成导风通道,分流管的外侧面与分隔管的内侧面形成混合通道,导风通道与混合通道的截面均呈楔形,导风通道的小端与混合通道的大端连通,从而形成烟气通道。
在本发明提供的内循环低氮燃气燃烧器中,还可以具有这样的特征:其中,环形燃气头通过节流孔板安装在分流管上;环形燃气头具有多个预混孔以及扩散孔;预混孔位于节流孔板的内侧,且预混孔的出气方向与分流管的轴线垂直;扩散孔位于节流孔板的外侧,且扩散孔的出气方向与分流管的轴线倾斜。
在本发明提供的内循环低氮燃气燃烧器中,还可以具有这样的特征:其中,外圈燃气组件与内圈燃气组件交错分布。
在本发明提供的内循环低氮燃气燃烧器中,还可以具有这样的特征:其中,旋流器包括:内圆架,外圆架,套设在内圆架的外侧;多个叶片,位于内圆架与外圆架之间,并连接内圆架与外圆架;其中,叶片与内圆架轴线之间的夹角7°-70°。
在本发明提供的内循环低氮燃气燃烧器中,还可以具有这样的特征:其中,渐缩管小端的流通面积与分流管入气端截面之比2:1~10:1。
在本发明提供的内循环低氮燃气燃烧器中,还可以具有这样的特征:其中,渐缩管的缩口角度12°-60°。
发明的作用与效果
根据本发明所涉及的内循环低氮燃气燃烧器,在工作时,空气通过分流管进行分流形成混烟用空气以及混燃用空气,隔流件的周侧具有进烟口,混烟用空气在流经隔流件的内侧面与分流管的外侧面形成烟气通道时,在进烟口处产生负压,燃烧室内的烟气通过进烟口进入烟气通道并与混烟用空气混合形成烟空混合气,一部分烟空混合气直接进入燃烧室,另一部分烟空混合气与多组内圈燃气组件输出的燃气混合形成烟空燃混合气后在进入燃烧室。由于采用真空的方式进行烟气再循环,省去了烟气回收管道,因此避免在管道内部形成冷凝水造成烟风道内的腐蚀以及冷凝水进入燃烧器导致火焰检测器感应及点火元件出现问题,从而消除安全隐患。其次,利用真空的方式回收烟气省去了风机,进而降低燃烧器的使用成本。
此外,混燃用空气分别与第一燃气管输出的燃气、环形燃气头输出的燃气以及多组外圈燃气组件输出的燃气相混合形成可燃混合气,实现分层燃烧,降低局部高温,进一步降低氮氧化物的产生。
附图说明
图1是本发明的实施例中内循环低氮燃气燃烧器的主视图;
图2是本发明的实施例中内循环低氮燃气燃烧器的右视图;以及
图3是本发明的实施例中旋流器的主视图;
图4是本发明的实施例中旋流器左视透视图;
图5是本发明的实施例中旋流器俯视透视图;
图6是本发明的实施例中环形燃气头的示意图;
图7是本发明的实施例中隔流件的示意图;以及
图8是本发明的实施例中内循环低氮燃气燃烧器的工作原理图。
具体实施方式
为了使本发明实现的技术手段、创作特征、达成目的与功效易于明白了解,以下结合实施例及附图对本发明作具体阐述。
<实施例>
图1是本发明的实施例中内循环低氮燃气燃烧器的主视图。图2是本发明的实施例中内循环低氮燃气燃烧器的右视图。
如图1、图2所示,本实施例中的内循环低氮燃气燃烧器100包括第一燃气管1、旋流器2、分流管3、环形燃气头4、第二燃气管5、隔流件6、多组外圈燃气枪组件7以及多组内圈燃气枪组件8。
第一燃气管1呈为圆管,第一燃气管1的一端安装有燃气头,该燃气头具有六个燃气孔,六个燃气孔沿第一燃气管1的轴线环形均匀分布且六个燃气孔的朝向与第一燃气管1的轴线倾斜,从而方便分散燃气。
图3是本发明的实施例中旋流器的主视图。图4是本发明的实施例中旋流器左视图。图5是本发明的实施例中旋流器俯视图。
如图3、图4以及图5所示,本实施例中的旋流器2包括内圆架21、6个叶片22以及外圆架23。内圆架21上嵌设有旋转轴承,内圆架21通过旋转轴承可转动地套设在第一燃气管1的端部且靠近第一燃气管1上的燃气头。6个叶片22以内圆架21的轴线为中心环形均匀地分布在内圆架21的外侧,且与内圆架21的轴线形成30°的夹角。外圆架23套设在6个叶片22上,并与6个叶片22固定连接。
在本实施中,内圆架21的厚度小于外圆架23的厚度,内圆架21的一端面与外圆架23的一端面相重合,另一端面位于外圆架23内。叶片22具有大端以及小端,叶片22的小端连接内圆架21且叶片22小端的两侧与内圆架21的两个端面平齐。叶片22的大端连接外圆架23且叶片22大端的两侧与外圆架23的两个端面平齐。
分流管3包括收风锥管以及扩风锥管,收风锥管的大端焊接在扩风锥管的小端,且收风锥管的轴线与扩风锥管的轴线相重合。分流管3的目的在于对空气进行分流,形成混烟用空气以及混燃用空气。
图6是本发明的实施例中环形燃气头的示意图。
如图1和图6所示,环形燃气头4具有两圈燃气分配腔室以及总燃气腔室,总燃气腔室分别与两圈燃气分配腔室连通。环形燃气头4具有20个预混孔以及20个扩散孔。20个预混孔与其中一圈燃气分配腔室连通,20个预混孔的朝向与空气流动的方向垂直。20个扩散孔与另一圈燃气分配腔室连通,20个预混孔的朝远离环形燃气头4的轴线倾斜。
环形燃气头4套设在旋流器2的外侧,并与旋流器2相分离。环形燃气头4的外周面具有节流孔板41,节流孔板41位于预混孔与扩散孔之间。环形燃气头4通过节流孔板41安装在扩风锥管的大端。
第二燃气管5的一端安装在环形燃气头4上并与总燃气腔室连通,从而向环形燃气头4提供燃气。
混燃用空气经过收风锥管进入扩风锥管,继而分成两路:
其中一路混燃用空气通过旋流器2形成旋转的气流。旋转的气流与第一燃气管1喷出的燃气混合形成可燃混合气,并进一步燃烧形成中心火焰。中心火焰的存在是为了稳住整体火焰,防止形成中心空洞导致燃烧器负荷变化时熄火停路甚至是发生危险。
另一路混燃用空气与20个预混孔喷出的燃气进行预先混合形成可燃混合气,可燃混合气经节流孔板41进入燃烧室燃烧形成第二圈火焰,第二圈火焰的方向与中心火焰的方向相平行。环形燃气头4通过预混孔进行预混燃烧,减少过量空气系数的不均匀性,从而降低氮氧化物生成的几率。
20个扩散孔喷出的燃气一边扩散一边燃烧,从而形成第一圈火焰。第一圈火焰的方向朝远离中心火焰的方向远离。环形燃气头4通过扩散孔进行扩散燃烧,具有容易点火、燃烧稳定以及不会回火的优点。
图7是本发明的实施例中隔流件的示意图。
如图7所示,隔流件6包括渐缩管61以及分隔管62。
渐缩管的锥度为12°。
分隔管62的一端通过四个连接支架焊接在渐缩管的小端,使得分隔管62的轴线与渐缩管的轴线相重合,分隔管62的另一端远离渐缩管。分隔管62靠近渐缩管的一端与渐缩管的小端形成进烟口,分隔管62远离渐缩管的一端为扩口结构。
值得说明的是,渐缩管与分隔管62的重合范围为-20mm~50mm,此区间是回收烟气量多少的调整范围。当锅炉的炉膛室容积过大时(因为技术原因,具体尺寸比例无法给)回收过量的烟气会导致外圈火焰的不稳定,有可能带来脱火(脱火:全称“火焰脱离”,亦称“吹熄”。若火焰传播速度慢于新鲜可燃混合气的流速,就会出现火焰前锋不能驻定而沿来流方向传播的现象)的问题,因此特限定此范围。
此外,渐缩管61小端的流通截面与收风锥管的小端流通截面的比值范围为10:1~2:1,从而适配不同锅炉或不同的炉膛,即燃烧器需要根据不同的工况调节内圈燃气腔组件枪以及中心枪的不同的过量空气系数,使得燃烧器可以组织炉内空气动力场,保证火焰不贴壁、不冲墙、充满度高,壁面热负荷均匀,从而达到稳定燃烧的目的。
分隔管62套设在分流管3的外侧,并通过三个连接板与分流管3固定连接,使得分隔管62的轴线与分流管3的轴线相重合。其中,分隔管62的内侧面与扩风锥管的外侧面形成楔形的混合通道,渐缩管61的内侧面与收风管的外侧面形成楔形的导风通道,导风通道的小端与混合通道的大端连通,从而形成与进烟口连通的烟气通道。
烟气通道用于回收燃烧室内的烟气,具体如下:混烟用空气流经烟气通道的过程中在进烟口处形成负压,使得燃烧室内烟气通过进烟口进入烟气通道并与混烟用空气混合形成烟空混合气。
在本实施例中,外圈燃气枪组件7的数量为12组,每组外圈燃气枪组件7均包括导气管71以及位于导气管71内的第三燃气管72。12根导气管71通过焊接的方式并以渐缩管61的轴线为中心环形均匀地固定在渐缩管61的周侧,且导气管71的轴线与渐缩管61的轴线相平行。导气管71的一端为进气口,进气口与渐缩管61连通。导气管71的另一端为出气口,该出气口伸出分割管。出气口为缩口结构,出气口的方向朝远离中心火焰倾斜。导气管71这样的目的有两个:一是为了将火焰进行分离,防止火焰聚集,解决局部高温,降低氮氧化物的产生;二是为了减少一氧化碳的产生,燃气过度集中除了会有产生局部高温,也会有燃烧不完全产生一氧化碳的可能,一次将燃气分散还有解决一氧化碳的优点。
此外,通过引流渐缩管61的空气对导气管71进行冷却,能够防止导气管71烧红,从而保证外圈燃气枪组件7可靠运行。
其中,第三燃气管72与导气管71之间的距离可根据实际应用进行调整,重合范围尺寸为-20毫米~200毫米。此情况是当遇到微正压锅炉(微正压锅炉,是指正常运行中锅炉的燃烧室与烟道中的烟气压力高于大气压力200-400帕的锅炉)。所以重合范围尺寸能重合比较广的范围,即使重合到200毫米,也依旧可以达到外圈枪烟气混合的状态。如果是遇到负压燃烧锅炉(负压燃烧锅炉是指运行中锅炉的炉膛和烟道中的烟气压力低于大气压力的锅炉)则需要更多导流力,因此需要将重合范围尺寸控制在-20毫米左右才能达到更好的效果(相同工况下,形状一定管道截面积不变,管道越长其阻力越大)。
如果目标项目是负压燃烧锅炉(负压燃烧锅炉是指大气压力高于运行中锅炉的炉膛和烟道中的烟气压力的锅炉)则需要更多导流力,所以根据需要增加第三燃气管72的管径。如果目标项目是正压燃烧锅炉,则对导流力的需求较少,此时根据需要降低第三燃气管72的管径。
外圈燃气枪组件7先充分混合燃气以及空气形成可燃混合气,避免混合不充分导致的燃气残留。需要说明的是,可燃混合气不会在导气管71处直接燃烧,而是喷射到一定距离与与燃烧室内的烟气混合形成烟空燃混合气,烟空燃混合气被中心火焰点燃形成悬浮式外圈火焰。通过这样的设计间接增加外圈火焰与中心火焰之间的距离,防止燃烧室内局部高温,降低氮氧化物的产生。
外圈燃气枪组件7的作用在于,烟气参与预热使燃烧更加平稳,提高烟气的利用率,部分烟气回流可以避免烟气集中。此方法不仅可以让天然气充分燃烧不浪费,又能让燃气燃烧不激烈,从而提高燃烧机效率。在低温富燃料条件和燃料停留时间较短的火焰中氮气才会形成瞬发氮氧化物,烟气预热空气可以提高空气的温度,气体混合之后降低了天然气的浓度,所以利用燃气与空气和烟气三种气体混合后再燃烧进一步降低瞬发型氮氧化物的含量。
在本实施例中,内圈燃气枪组件8的数量为12组,每组内圈燃气枪组件8均包括混合管81以及第四燃气管82。12根混合管81通过焊接的方式并以分流管3的轴线为中心环形均匀地固定在分流管3的周侧,且混合管81的轴线与分流管3的轴线相平行。混合管81的一端为接气口,另一端为出气口,接气口位于烟气通道内,出气口为缩口结构,该缩口的方向朝向中心火焰。第四燃气管82具有出气口。第四燃气管82穿设渐缩管内,使得出气口位于烟气通道内并靠近混合管81的接气口。
第四燃气管82向混合管81输送燃气时在混合管81的接气口处形成负压,使得一部分烟空混合进入混合管81并与混合管81内的燃气混合形成烟空燃混合气。由于混合管81的出气口朝向中心火焰,烟空燃混合气喷向中心火焰后降低中心火焰的温度,进一步降低局部高温。
其中,内圈燃气枪组件8提供的烟空燃混合气的过量空气系数较高,其目的在于,稀释天然气单位体积内的热值,降低氮氧化物的排放。此外,烟空燃混合气流速较快,能防止内圈燃气枪组件8产生的烟空燃混合气因流速慢在进烟口燃烧。
第三燃气管72的流通截面与导气管71的流通截面之比的范围为1:1.5~1:8。其目的在于在中心火焰稳定的前提下导气管71少量供风,由于导气管71开孔较大,利用较大流量的燃气喷射,使得射流长度增加。内圈燃气孔开孔比外圈小,所以内圈枪通过的燃气流量偏小,射流的长度不同使得火焰内外圈分层。
在本实施例中,相邻内圈燃气枪组件8之间具有外圈燃气枪组件7,即:内圈燃气枪组件8与外圈燃气枪组件7交错分布,且内圈燃气枪组件8所在的分度圆的直径与外圈燃气枪组件7所在的分度圆的直径范围差在170~300mm,使燃气枪与枪的间隙变大,轴流风也会增加,这样的结构可以有效地将高温尾焰喷射到锅炉水冷壁周围,从而缓解积碳以及燃烧缺氧的问题。另外这样的结构还可以增加锅炉热效率、降低氮氧化物产生。
图8是本发明的实施例中内循环低氮燃气燃烧器的工作原理图。
如图8所示,本发明提供的内循环低氮燃气燃烧器100的工作原理如下:
空气通过过滤网孔板进行过滤、整流,随后进入渐缩管61。
大部分空气通过渐缩管61进行压缩,然后通过分流管3形成混烟用空气以及混燃用空气。一小部分通过直接进入外圈燃气枪组件7内的导气管71,随后与第三燃气管72喷出的燃气混合形成可燃混合气,可燃混合气脱离导气管71后与燃烧室内的烟气混合形成烟空燃混合气,最后燃烧形成外圈火焰。
混烟用空气通过导风通道进入混合通道。其中,导风通道的外形呈楔形,使得混烟用空气在流动的过程中流通面积不断缩小。根据伯努利原理,在总流量不变的情况下,截面积越小、流速越快,相应的压力也就越小。因此在进烟口处形成局部负压。燃烧室内的烟气在负压的作用下从进烟口进入混合通道,并与混合通道内的烟气混合形成烟空混合气。烟空混合气分两路,一路由烟气通道直接进入燃烧室,另一路则进入内圈燃气枪组件8的混合管81,并与混合管81内的燃气混合形成烟空燃混合气,烟空燃混合气燃烧形成内圈火焰。
混燃用空气用于混合第一燃气管1以及环形燃气头4喷出的燃气。即:一部分混燃用空气经旋流器2转动由直流风转换成旋转的气流,旋转的气流与第一燃气管1喷出的燃气混合形成可燃混合气,并进一步燃烧形成中心火焰。20个扩散孔喷出的燃气一边扩散一边燃烧形成第一圈火焰。另一部分混燃用空气与20个预混孔喷出的燃气进行混合形成可燃混合气,可燃混合气经节流孔板41进入燃烧室燃烧形成第二圈火焰。
内循环低氮燃气燃烧器产生的整体火焰由内而外依次是中心火焰、第一圈火焰、第二圈火焰、内圈火焰以及外圈火焰,且中心火焰、第一圈火焰、第二圈火焰、内圈火焰以及外圈火焰形成位置不同,实现分层、分段燃烧,防止在燃烧室产生局部高温,从而降低氮氧化物的产生。
而外部烟气再循环是需要将部分烟气回流与冷空气混合,混合后的温度将大幅下降,从而产生冷凝水。即使在回流烟气与冷空气混风器处及时排出冷凝水,在进入燃烧器前的管道中也可能会再次发生冷凝,这是由于混合后的助燃风湿度依然是饱和的原因造成的。这样一来可能造成燃烧器和风机内部潮湿、积水,甚至造成电器腐蚀、短路等严重后果,影响燃烧器和风机的正常工作,缩短燃烧器的使用寿命,甚至会损坏燃烧器。而在本实施例中,烟气直接在锅炉燃烧室内强制循环,避免了烟气回流与冷空气的混合,这样做解决了烟气冷凝的问题。
实施例的作用与效果
根据本实施例所涉及的内循环低氮燃气燃烧器,在工作时,空气通过分流管进行分流形成混烟用空气以及混燃用空气,隔流件的周侧具有进烟口,混烟用空气在流经隔流件的内侧面与分流管的外侧面形成烟气通道时,在进烟口处产生负压,燃烧室内的烟气通过进烟口进入烟气通道并与混烟用空气混合形成烟空混合气,一部分烟空混合气直接进入燃烧室,另一部分烟空混合气与多组内圈燃气组件输出的燃气混合形成烟空燃混合气后在进入燃烧室。由于采用真空的方式进行烟气再循环,省去了烟气回收管道,因此避免在管道内部形成冷凝水造成烟风道内的腐蚀以及冷凝水进入燃烧器导致火焰检测器感应及点火元件出现问题,从而消除安全隐患。其次,利用真空的方式回收烟气省去了风机,进而降低燃烧器的使用成本。
此外,混燃用空气分别与第一燃气管输出的燃气、环形燃气头输出的燃气以及多组外圈燃气组件输出的燃气相混合形成可燃混合气,实现分层燃烧,降低局部高温,进一步降低氮氧化物的产生。
根据本发明所涉及的内循环低氮燃气燃烧器,因为燃烧器采用分层、分段的方式进行燃烧,不但能够充分与空气混合降低一氧化碳的产生,而且能够降低局部高温,防止氮氧化物的产生。
根据本发明所涉及的内循环低氮燃气燃烧器,燃烧器采用独立的供风,因此能够防止燃烧器内外气流不发生干扰,保证火焰稳定燃烧。
上述实施方式为本发明的优选案例,并不用来限制本发明的保护范围。
起点商标作为专业知识产权交易平台,可以帮助大家解决很多问题,如果大家想要了解更多知产交易信息请点击 【在线咨询】或添加微信 【19522093243】与客服一对一沟通,为大家解决相关问题。
此文章来源于网络,如有侵权,请联系删除


