一种垃圾热解气化耦合高炉熔渣处理系统的制作方法



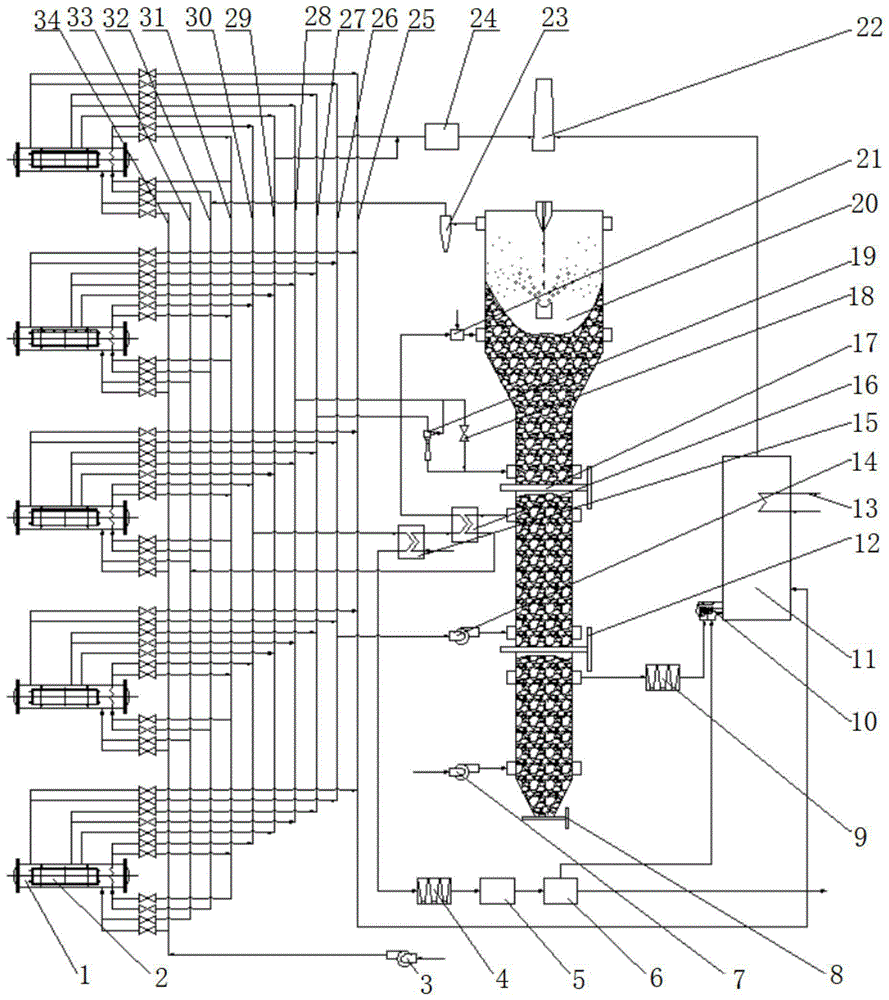
本实用新型涉及城市生活垃圾处理,具体涉及一种垃圾热解气化耦合高炉熔渣处理系统。
背景技术:
生活垃圾处理技术包括填埋、堆肥、热处置三大技术。热处置技术可分为直接焚烧和热解气化两种。热解气化技术可将城市生活垃圾转化为成分较为稳定的气、液、固3类产品加以利用,有效提高其利用效率、利用范围和经济性;从污染物排放角度分析,由于直接焚烧的不充分性所引起的二次污染,特别是二噁英的排放问题,严重制约着该技术的推广及应用,而热解气化过程是在贫氧或缺氧气氛下进行的,从原理上减少了二噁英的生成,同时大部分的重金属会在热解气化过程中溶入灰渣,减少了重金属的排放量。然而,国内现有的生活垃圾热解气化技术主要采用内热式热解气化,由于内热式热解气化过程中会有大量空气进入炉内,和垃圾焚烧一样容易产生二噁英污染。同时,热解产出气中含有的n2和co2占很大一部分比例,明显降低了燃气的热值,增大了其利用局限性。另一方面,垃圾热解气化是强吸热反应,尤其是生活垃圾中含有大量的水分,需要外加热源对垃圾进行加热干燥、热解,如采用煤加热,则易产生二次污染;采用电和煤气加热,则成本较高。
我国钢铁产量长期稳居世界第一,并且遥遥领先于其他国家。同时伴随高炉冶炼生产排出的含丰富热能的高炉渣数量也是巨大的。炉渣的出炉温度一般在1400-1550℃之间。每吨炉渣约含1.74gj的热量,相当于60kg标准煤的热值。回收这部分显热对于节能减排具有重大的意义。目前我国90%的高炉渣都采用水冲渣法处理,传统的水冲渣法存在水耗高、污染大、未回收显热、水渣需要干燥、磨损、堵塞等问题。干式显热回收技术是行业探索的技术路线,主要有风淬法、旋转杯粒化法和甲烷-水蒸气重整法。各类方法虽然取得一定的进展,但实际上存在经济性不足、效率还比较低的问题,目前几乎没有工业应用。
技术实现要素:
针对现有技术的不足,本实用新型的目的在于提供一种垃圾热解气化耦合高炉熔渣处理系统,解决目前热解气化技术处理垃圾利用率不高,成本高,同时炉渣利用率不足的问题,
为实现上述目的,本实用新型拟采取如下技术手段:
本实用新型首先提出一种垃圾热解气化耦合高炉熔渣处理工艺,该工艺将垃圾热解气化和高炉熔渣处理过程耦合:利用高炉熔渣处理过程产生的热量完成垃圾烘干、干燥、热解产气过程;同时随着高炉熔渣的处理完成垃圾热解气、半焦粉、水蒸汽的气化反应;
所述垃圾热解气化依次包括烘干、干燥、热解产气、降压以及冷却五个过程;
烘干过程在常压下进行,热源为高炉熔渣处理过程产生的烘干烟气,其直接与垃圾接触,将垃圾中的游离水分蒸发;
干燥过程反应压力在1-2mpa,热源为高炉熔渣处理过程产生的中温气化气,其通过间接换热的方式,将垃圾中化合态水分离;
热解产气过程压力维持在1-2mpa,热源为高炉熔渣处理过程产生的高温气化气,其通过间接换热的方式,使垃圾热解产生热解气和残余半焦;
降压过程中,排出热解产气过程产生的热解气,通过引射的方式进一步排出残余热解气供高炉熔渣处理过程用,直至变成负压状态;
冷却过程,通过冷空气对残余半焦进行冷却,同时与残余热解气混合后排出。
进一步,烘干烟气温度在200-250℃;干燥过程热源为450-550℃的中温气化气;热解产气过程的热源为800-1000℃高温气化气。
进一步,高炉熔渣处理过程分为气化段、干燥段以及冷却段;
气化段实现1300-1500℃熔渣降温至800-1000℃,放出的热量作为热解产气过程的热源,同时热解产气过程产生的热解气、水蒸汽和半焦粉进入气化段;
干燥段实现熔渣从800-1000℃被干燥气冷却到300-500℃,放出的热量作为干燥过程的热源;
冷却段实现熔渣从300-500℃降低到150-250℃,放出的热量用来预热空气实现二次利用。
进一步,干燥气入口温度为100-200℃,出口温度为450-550℃;
在此基础上,本实用新型还提供一种垃圾热解气化耦合高炉熔渣处理系统,包括气化炉和多个干燥热解反应釜,所述干燥热解反应釜用于实现上述垃圾热解气化五个过程;所述气化炉用于进行高炉熔渣的处理以及同时完成垃圾热解气、半焦粉、水蒸汽的气化反应,干燥热解反应釜和气化炉之间由若干个管路接通。
进一步,所述干燥热解反应釜,包括壳体,还包括位于壳体内的反应腔体,在壳体内壁布置有换热管;
在壳体外侧下部和上部的位置分别设置有烘干烟气入口和烟气出口,烘干烟气通过烘干烟气入口进入反应腔体烘干反应腔体内物质后通过烟气出口排出;
在壳体外侧下部和上部的位置分别设置有中温气化气入口、干燥产出蒸汽出口和低温气化气出口,中温气化气入口与换热管相通,干燥产出蒸汽出口和低温气化气出口用于干燥反应腔体内物质后分别排出水蒸气和气化气;
在壳体外侧下部和上部的位置分别设置有高温气化气入口、热解气产出气出口和中温气化气出口,高温气化气入口与换热管相通,热解气产出气出口和中温气化气出口用于反应腔体内物质热解产气后分别排出热解气和残余气化气;
在壳体外侧上部的位置设置有热解气引射气出口,用于进一步排出残余热解气直至反应釜内为负压;
在壳体外侧下部和上部的位置还分别设置有常温空气入口和冷却空气出口出口,用于最后对反应釜内残余半焦进行冷却并排出混合气。
进一步,所述气化炉,包括炉体以及炉体下部的料斗,所述料斗从上至下依次包括气化段、干燥段和冷却段;
气化段的炉体上设置有水蒸汽半焦粉入口、热解气入口、高温气化气出口;
干燥段的炉体上设置有干燥气入口和干燥气出口、中温气化气出口;
冷却段的炉体上设置有常温空气入口、空气出口、烘干烟气出口。
优选的,干燥热解反应釜烘干过程产出的烟气,部分通过除臭装置除臭后通过烟囱排放,另一部分通过鼓风机送入气化炉干燥段,再次加热后通过换热器制蒸汽。
干燥热解反应釜干燥过程产生的水蒸气减压后经除臭装置除臭后通过烟囱排放。
冷却过程中通过鼓风机将冷空气送入干燥热解反应釜,混合残余热解气后一同送入燃气锅炉燃烧,产出的气化气经过除尘、洗涤后成为产品燃料送入储气柜。
与现有技术相比,本实用新型具有如下有益的技术效果:
本实用新型的工艺,采用高炉熔渣余热作为垃圾热解气化反应的热源,分段回收高炉熔渣热量,高品位热用于气化反应吸热,中品味热用于干燥热解反应吸热,低品位热通过冷空气回收用于燃气锅炉燃烧,梯级利用了高炉熔渣的热量。相较于传统用水冲渣法,提高了能源利用效率。
本实用新型的系统,用热解气化的方式处理垃圾,相较于传统填埋或焚烧的方式,环保性更好,且产出气化气既可以作为清洁燃料直接燃烧,也可以作为化工原料用于其他化工生产,还能解决炉渣利用率不足的问题。
附图说明
图1为本实用新型的工艺系统流程图。
图2为干燥热解反应釜示意图。
图中各标号代表的含义为:
1—干燥热解反应釜,2—小车,3、7—鼓风机,4、9—除尘器,5—气体洗涤,6—储气柜,8、12、17—锁料器,10—燃烧器,11—燃气锅炉,13—外送蒸汽,14—鼓风机,15、16—换热器,18—阀门,19—引射器,20—气化炉,21—半焦粉输送器,22—烟囱,23—旋风除尘器,24—除臭装置,25—冷却气总管,26—低温烟气总管,27—热解气产出气总管,28—热解气引射器总管,29—干燥蒸汽总管,30—低温气化气总管,31—中温气化气总管,32—高温气化气总管,33—烘干烟气总管,34—常温空气总管。
1-1—冷却空气出口,1-2—烘干烟气出口,1-3—热解气产出气出口,1-4—热解气引射气出口,1-5—干燥产出蒸汽出口,1-6—低温气化气出口,1-7—中温气化气出口,1-8—中温气化气入口,1-9—高温气化气入口,1-10—烘干烟气入口,1-11—常温空气入口
以下结合附图以及实施例对本实用新型的方案进一步进行说明。
具体实施方式
本实用新型所述烘干烟气来源于气化炉三段,约为200℃左右的温度,烟气直接与垃圾接触,将垃圾中的游离水分蒸发。
本实用新型所述中温气化气,是干燥过程中的热源,温度约500℃的,来源于气化炉二段,气化气降温到300℃左右排出。
本实用新型所述高温气化气,是热解产气过程,热源温度约900℃左右,来源于气化炉一段,在此将垃圾加热到400℃左右,原生垃圾成为热解气和半焦。
需要说明的是,工艺中各环节温度数值的选取为最佳温度范围,不同物料配比时,具体温度可能发生改变,采用本实用新型工艺路线,选取不同的温度,也属于本申请保护范畴。
本发明所述热解气化是一个反应过程,包括烘干、干燥、热解产气、降压以及冷却五个过程,其中的热解产气发生在第三个过程,指的是垃圾发生热解反应生成热解气,热解气是热解反应产生气体的总称,最后上述产生的热解气、残余半焦以及烘干和干燥过程产生的水蒸气耦合入高炉熔渣处理过程。
实施例1:
按照上述的工艺,本实施例提供一种垃圾热解气化耦合高炉熔渣处理工艺,该工艺将垃圾热解气化和高炉熔渣处理过程耦合:利用高炉熔渣处理过程产生的热量完成垃圾烘干、干燥、热解产气过程;同时随着高炉熔渣的处理完成垃圾热解气、半焦粉、水蒸汽的气化反应;
所述垃圾热解气化依次包括烘干、干燥、热解产气、降压以及冷却五个过程;
烘干过程在常压下进行,热源为高炉熔渣处理过程产生的烘干烟气,其直接与垃圾接触,将垃圾中的游离水分蒸发;
干燥过程反应压力在1-2mpa,热源为高炉熔渣处理过程产生的中温气化气,其通过间接换热的方式,将垃圾中化合态水分离;
热解产气过程压力维持在1-2mpa,热源为高炉熔渣处理过程产生的高温气化气,其通过间接换热的方式,使垃圾热解产生热解气和残余半焦;
降压过程中,排出热解产气过程产生的热解气,通过引射的方式进一步排出残余热解气供高炉熔渣处理过程用,直至变成负压状态;
冷却过程,通过冷空气对残余半焦进行冷却,同时与残余热解气混合后排出。
进一步,烘干烟气温度在200-250℃;干燥过程热源为450-550℃的中温气化气;热解产气过程的热源为800-1000℃高温气化气。
进一步,高炉熔渣处理过程分为气化段、干燥段以及冷却段;
气化段实现1300-1500℃熔渣降温至800-1000℃,放出的热量作为热解产气过程的热源,同时热解产气过程产生的热解气、水蒸汽和半焦粉进入气化段;
干燥段实现熔渣从800-1000℃被干燥气冷却到300-500℃,放出的热量作为干燥过程的热源;
冷却段实现熔渣从300-500℃降低到150-250℃,放出的热量用来预热空气实现二次利用。
进一步,干燥气入口温度为100-200℃,出口温度为450-550℃;
本实用新型的主要工艺路线为:原生垃圾通过小车送入干燥热解反应釜,在反应釜内进行干燥、热解,原生垃圾被转化为热解气和残余半焦,热解气以一氧化碳、二氧化碳、甲烷、焦油为主,半焦主要是以固定碳为主,同时含有原生垃圾中不可燃物。热解气通过管道进入气化炉内,进行水蒸气气化反应;残余半焦经过筛分去除不可燃物,固定碳经过粉碎变成半焦粉,半焦粉经过蒸汽输送进入气化炉内,在气化炉内实现热解气、半焦粉、水蒸气的气化反应,气化反应产出气主要成分为氢气、一氧化碳、水蒸汽、二氧化碳。产出气化气热量被各工艺环节利用后经过洗涤送入储气罐,可以直接作为产品燃料或成为化工原料。
实施例2:
实施例的工艺中主要用到2个关键设备:干燥热解反应釜1和气化炉20。本实施例进一步说明本实用新型的系统。
干燥热解反应釜1结构如图2所示,原生垃圾在反应釜内依次经过烘干、干燥、热解产气、降压、冷却五个过程:烘干过程基本在常压下进行,烟气由烘干烟气入口1-10进入反应釜,200℃左右烟气直接与垃圾接触,将垃圾中的游离水分蒸发,通过烘干烟气出口1-2排出,垃圾加热到100℃时,基本完成游离水的分离,进入干燥过程;干燥过程中,热源为产出的约500℃的中温气化气,气化气通过中温气化气入口1-8进入反应釜,反应釜内壁布置蛇形换热管,气化气通过间接换热的方式,将垃圾加热到200℃左右,过程中垃圾中化合态水被分离,调节反应釜内压力到1-2mpa,产出的水蒸气通过干燥产出蒸汽出口1-5排出,气化气降温到300℃左右通过低温气化气出口1-6排出;热解产气过程中,反应釜内压力维持在1-2mpa,热源为产出的约900℃高温气化气,气化气通过高温气化气入口1-9进入反应釜,反应釜内壁布置蛇形换热管,气化气通过间接换热的方式,将垃圾加热到400℃左右,过程中垃圾热解产生热解气,热解气通过热解气产出气出口1-3排出,残余半焦留在小车内,高温气化气降温到500℃左右通过中温气化气出口1-7排出;降压过程中,反应釜内压力高于气化炉内压力,打开阀门进行泄压,残余热解气通过热解气引射气出口1-4排出,减压后直接进入气化炉,当压力降低接近气化炉压力时,利用其他处于热解产气过程排出的热解气,通过引射的方式进一步排出残余热解气,反应釜内变成负压状态;最后进入冷却过程,冷空气通过常温空气入口1-11进入反应釜,对残余半焦进行冷却,同时与残余热解气混合后通过冷却空气出口1-1排出反应釜。
气化炉20实现利用高炉熔渣热量完成垃圾热解气、半焦粉、水蒸汽的气化反应。高炉熔渣通过顶部漏斗自由下落,落在底部转杯上,旋转的转杯通过撞击,将高炉熔渣破碎成小液滴并抛向空中,高温熔渣液滴在空中被气化气冷却固化后落入气化炉料斗。气化炉由三段组成,一段为气化室,1400℃左右熔渣降温至约900℃,放出的热量作为气化反应的热源,热解气通过旁路18阀门和引射器19减压后进入气化室,水蒸汽和半焦粉通过半焦粉输送器21送入气化室;二段干燥段,熔渣颗粒从约900℃被干燥气冷却到400℃,放出的热量加热干燥气,干燥气入口温度约150℃,被加热到500℃左右;三段为冷却段,熔渣颗粒从约400℃降低到200℃后排出气化炉,放出的热量用来预热空气,加热后的空气进入燃气锅炉。三段气化炉间以及气化炉出口设置有锁料器,间断式排出高炉熔渣颗粒,确保气化炉三段空间相互之间气体泄漏量有限。
干燥热解反应釜1所配各进出管口均满足工艺中烘干、干燥、热解产气、降压、冷却五个过程需要,为配合干燥热解反应釜1的需要,在干燥热解反应釜1和气化炉20之间设计有冷却气总管25,低温烟气总管26,热解气产出气总管27,热解气引射器总管28,干燥蒸汽总管29,低温气化气总管30,中温气化气总管31,高温气化气总管32,烘干烟气总管33,常温空气总管34。需要说明的是,对反应釜进出管线数量增减而进行的改变,也属于本申请保护范畴。
所述的反应釜1各管路出口母管采用分气缸,配气原理上与本申请相同,也属于本申请保护范畴。
所述燃气锅炉11产生蒸汽用于驱动蒸汽轮机发电,或直接采用燃气轮机发电均属于对产品气利用方式的改变,蒸汽不足时采用外送蒸汽13,也属于本申请保护范畴。
所述半焦粉输送器21采用水蒸汽作为输送气体输送半焦粉,采用其他种类气体输送半焦粉,再单独将水蒸气送入气化炉用于气化反应,也属于本申请保护范畴。
锁料器8、12、17通过间断式排出熔渣颗粒,实现排除物料和气空间的隔离作用,采用其他类似功能的设备实现此功能,也属于本申请保护范畴。
该系统的运作流程为:原生垃圾装载入小车2中,通过轨道送入干燥热解反应釜1中,在反应釜1中依次完成上述烘干、干燥、热解产气、降压、冷却五个过程。烘干过程产出的烟气含有大量水蒸汽,部分通过除臭装置24除臭后通过烟囱22环保排放,部分通过鼓风机14送入气化炉二段,再次加热后通过换热器16制蒸汽,烟气温度降低到200℃左右再用于垃圾烘干;干燥过程产生的水蒸气减压后通过除臭装置24除臭后通过烟囱22环保排放;冷却过程中鼓风机3将冷空气送入反应釜1,混合残余热解气后一同送入燃气锅炉燃烧,减少可燃物耗散损失。产出的气化气经过除尘器4、气体洗涤器5后成为产品燃料送入储气柜6,部分直接燃烧发电,同时消纳冷却过程中残余的热解气。
效果论证:
按照本实用新型方案利用aspn对典型工艺参数进行模拟。
典型垃圾成分选择工业分析为含水率14.09%,固定炭1.61%,挥发分56.23%,灰分28.07%,元素分析为碳28.86%,氢3.04%,氮0.28%,硫0.12%,氧39.63%,热值为13.63mj/kg。
反应条件为:一阶段烘干物料常压下升温到100℃,二阶段干燥物料在1mpa下升温到200℃,热解过程在2mpa下升温到450℃,气化过程在常压下升温到950℃。
气化产出气主要成分为水蒸汽20.3%,氢气37%,一氧化碳30.8%,二氧化碳11.6%,经过冷却净化后可燃产品气低位热值可达10mj/nm3以上。
起点商标作为专业知识产权交易平台,可以帮助大家解决很多问题,如果大家想要了解更多知产交易信息请点击 【在线咨询】或添加微信 【19522093243】与客服一对一沟通,为大家解决相关问题。
此文章来源于网络,如有侵权,请联系删除


