乙炔割炬用粉末冶金割嘴的制作方法



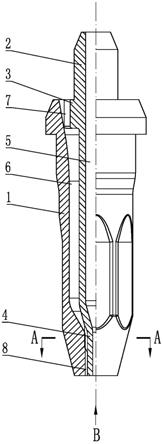
[0001]
本实用新型涉及乙炔割炬技术领域,尤其涉及一种乙炔割炬用粉末冶金割嘴。
背景技术:
[0002]
气体切割通过如下方式来进行:从气割嘴喷射由燃料气体和氧气而混合形成的混合燃气,燃烧形成的预热火焰对钢板等被切割件进行预热,并向被充分预热后的被切割件喷射切割氧而使母材燃烧,并且利用喷射能量来去除熔融母材、氧化生成物。然后,通过在持续进行气体切割的同时使气割嘴向目标方向行驶,由此能够将被切割件切割为目标形状。
[0003]
气体切割的燃料气体包括乙炔气、液化石油气、天然气、乙烯气、氢气等,每种燃料气体具有专用的割嘴,割嘴是割炬的重要部件,对整个割炬的性能影响至关重要。其中乙炔气主要采用环形割嘴,而液化石油气或天然气等主要采用梅花型割嘴。
[0004]
传统的环形割嘴一般由割嘴外套、割嘴芯、割嘴座三部分组成,三个部件之间采用螺纹配合连接,参见图10为现有技术中常用的环形割嘴。该种通过螺纹连接的割嘴当受高温膨胀后,螺纹连接处容易变形、松动,一方面造成漏气以至产生回火现象,另一方面扰乱原有的气流秩序导致切割质量降低;此外,现有技术中的割嘴芯仅是通过螺纹连接在割嘴座上,并且割嘴芯与割嘴外套前端之间具有环形出气道,所以导致割嘴芯的外端由于不具有定位而形成了悬臂结构,长时间高温切割后,割嘴芯会产生一定变形,导致割嘴芯与割嘴外套之间的不再同轴,使得气体从割嘴芯与割嘴外套之间的环形出气道出气不均匀,造成切割质量不好。
技术实现要素:
[0005]
本实用新型所要解决的技术问题是提供一种结构简单、加工方便、不漏气、同轴度较高的乙炔割炬用粉末冶金割嘴。
[0006]
为解决上述技术问题,本实用新型的技术方案是:乙炔割炬用粉末冶金割嘴,包括割嘴外套,所述割嘴外套内安装有割嘴芯杆,所述割嘴芯杆的后端设置有割嘴杆座,所述割嘴杆座的外周设置有外锥面,所述割嘴外套的后端设置有与所述外锥面配合安装的内锥孔,所述割嘴杆座与所述割嘴外套之间还设置有杆座固定结构;所述割嘴芯杆的前端设置有割嘴芯头,所述割嘴芯杆、所述割嘴杆座与所述割嘴芯头一体成型形成割嘴芯套;
[0007]
所述割嘴芯套的中心贯穿设置有氧气通道;所述割嘴芯杆与所述割嘴外套之间设置有混合燃气通道,所述割嘴杆座与所述割嘴外套之间设置有多个与所述混合燃气通道连通的混合燃气进口,所述割嘴芯头的后端同轴固定在所述割嘴外套内,所述割嘴芯头的前端与所述割嘴外套之间设置有与所述混合燃气通道连通的混合燃气环形出气道。
[0008]
作为优选的技术方案,所述杆座固定结构包括所述外锥面和所述内锥孔之间的自锁锥面配合和/或设置在所述割嘴外套与所述割嘴杆座之间的焊接部。
[0009]
作为优选的技术方案,所述割嘴杆座的外周设置有多个混合燃气进气槽,所述混
合燃气进气槽与所述割嘴外套之间围合形成所述混合燃气进口。
[0010]
作为优选的技术方案,所述割嘴杆座两侧的混合燃气进气槽对称设置,同侧的所述混合燃气进气槽的开口朝向同一方向,且两侧的所述混合燃气进气槽的开口方向相反;所述混合燃气进气槽为方便向外脱模的槽。
[0011]
作为优选的技术方案,所述割嘴芯头的后端设置有同轴固定在所述割嘴外套内的芯头定位段,所述割嘴芯头的前端设置有与所述割嘴外套之间间隙配合的芯头出口段,所述混合燃气环形出气道设置在所述芯头出口段与所述割嘴外套之间。
[0012]
作为优选的技术方案,所述芯头定位段的外周设置有多个呈环形阵列的混合燃气导条,相邻两所述混合燃气导条之间设置有混合燃气导槽,所述混合燃气导槽将所述混合燃气环形出气道与所述混合燃气通道之间连通。
[0013]
作为优选的技术方案,所有混合燃气导条的外周共同构成用于紧固在所述割嘴外套上的芯头定位面。
[0014]
作为优选的技术方案,其中至少三个均匀布置的混合燃气导条的外周共同构成用于紧固在所述割嘴外套上的芯头定位面,其余混合燃气导条均与割嘴外套之间间隙配合。
[0015]
作为优选的技术方案,所述外锥面与所述内锥孔的配合面上还对应设置有定位台肩。
[0016]
作为优选的技术方案,所述割嘴外套为粉末冶金外套,所述割嘴芯套为粉末冶金芯套。
[0017]
由于采用了上述技术方案,乙炔割炬用粉末冶金割嘴,包括割嘴外套,所述割嘴外套内安装有割嘴芯杆,所述割嘴芯杆的后端设置有割嘴杆座,所述割嘴杆座的外周设置有外锥面,所述割嘴外套的后端设置有与所述外锥面配合安装的内锥孔,所述割嘴杆座与所述割嘴外套之间还设置有杆座固定结构;所述割嘴芯杆的前端设置有割嘴芯头,所述割嘴芯杆、所述割嘴杆座与所述割嘴芯头一体成型形成割嘴芯套;
[0018]
所述割嘴芯套的中心贯穿设置有氧气通道;所述割嘴芯杆与所述割嘴外套之间设置有混合燃气通道,所述割嘴杆座与所述割嘴外套之间设置有多个与所述混合燃气通道连通的混合燃气进口,所述割嘴芯头的后端同轴固定在所述割嘴外套内,所述割嘴芯头的前端与所述割嘴外套之间设置有与所述混合燃气通道连通的混合燃气环形出气道;
[0019]
本实用新型的有益效果是:
[0020]
(1)所述割嘴芯套的后端通过所述割嘴杆座采用锥面配合安装在所述割嘴外套的后端,保证了所述割嘴杆座与割嘴外套之间的同轴度,所述割嘴芯套的前端通过将所述割嘴芯头同轴固定在所述割嘴外套的前端,保证了所述割嘴芯头与割嘴外套之间的同轴度;所述割嘴芯套的前端与后端的同轴度均得到了保证,尤其所述割嘴芯头的同轴度得到了保证,当所述割嘴芯头长时间高温切割后,所述割嘴芯头受热即使会发生变形,但是仍然会保持与所述割嘴外套之间的同轴度,混合燃气从所述割嘴芯头与所述割嘴外套之间的环形出气道出气始终保持均匀,出气流畅,有效避免出现传统设计中通过螺纹连接出现配合不同轴而造成出气不均匀等问题;
[0021]
(2)所述割嘴杆座通过所述杆座固定结构安装在所述割嘴外套上,不再如现有技术中一样将嘴杆通过螺纹连接在外套上,配合安装方式较为简单,可以实现快速安装效果,同时可以保证所述割嘴杆座与所述割嘴外套之间连接的稳定性,避免出现连接脱落等影响
使用安全性的问题;
[0022]
(3)所述割嘴芯杆、所述割嘴杆座与所述割嘴芯头一体成型形成割嘴芯套,不再如现有技术中一样将嘴芯通过螺纹连接在芯杆上,本装置的一体成型结构通过模具一次成型,加工方式更加方便,成本较低,可大批量生产;且不需要如现有技术中分别加工后再加工螺纹进行配合,因此本装置割嘴芯套与割嘴外套之间的互换性较高,配合度较好;并且氧气通过所述氧气通道时,不存在由于螺纹配合而产生的连接缝,气流阻力较小,可以有效保证氧气流动的流畅性与稳定性,使得出气快速与稳定,形成的割缝具有一致性,有效提高切割质量;此外由于割嘴芯头与割嘴芯杆之间为一体结构,氧气通过时,不会出现漏气的现象,具有较好的安全性;
[0023]
(4)通过混合燃气进气槽的结构设计,使得割嘴杆座的混合燃气进口加工成型方式较为简单,模具可以反复使用,形成的混合燃气进气槽结构具有良好的一致性,并且不需要其他辅助工具或者孔加工方式进行额外加工,加工效率明显得到提升,利于产品的批量生产;
[0024]
(5)本实用新型中通过设置芯头定位段实现所述割嘴芯头的同轴固定安装,可以有效避免出现由于芯头不同轴而出现出气不均匀的现象,同时由于该芯头定位段内还具有使得气流变得更加稳定有序的作用,使得由所述混合燃气环形出气道内排出的环形气流稳定、运动流速快,从而使得形成的火焰较长,提高了预热与切割速度;
[0025]
(6)本实用新型结构简单、设计合理,采用一体成型结构加工方便,并且通过锥面配合使得拆装更加方便;此外所述割嘴芯杆的前端与后端的同轴度均能得到保证,保证出气更加顺畅,提高出气速度,保证切割质量;同时割嘴杆座与割嘴芯头结构等的特殊设计,使得本实用新型加工效率明显得到提升,利于产品的批量生产。
附图说明
[0026]
以下附图仅旨在于对本实用新型做示意性说明和解释,并不限定本实用新型的范围。其中:
[0027]
图1是本实用新型实施例一的结构示意图;
[0028]
图2是本实用新型实施例一的结构原理图;
[0029]
图3是本实用新型实施例一割嘴芯套的结构示意图;
[0030]
图4是本实用新型实施例一割嘴杆座的结构示意图;
[0031]
图5是图3中c处的放大示意图;
[0032]
图6是图2中a-a向的剖面放大图;
[0033]
图7是图2中b向的截面放大图;
[0034]
图8是本实用新型实施例二割嘴芯头与割嘴外套的配合示意图;
[0035]
图9是本实用新型实施例三的结构原理图;
[0036]
图10是背景技术的结构原理图;
[0037]
图中:1-割嘴外套;2-割嘴芯杆;3-割嘴杆座;31-外锥面;32-混合燃气进气槽;33-分模面;34-左半模;35-右半模;4-割嘴芯头;41-混合燃气导槽;42-混合燃气导条;43-芯头定位面;44-芯头定位段;45-芯头出口段;5-氧气通道;6-混合燃气通道;7-混合燃气进口;8-混合燃气环形出气道;9-定位台肩。
具体实施方式
[0038]
下面结合附图和实施例,进一步阐述本实用新型。在下面的详细描述中,只通过说明的方式描述了本实用新型的某些示范性实施例。毋庸置疑,本领域的普通技术人员可以认识到,在不偏离本实用新型的精神和范围的情况下,可以用各种不同的方式对所描述的实施例进行修正。因此,附图和描述在本质上是说明性的,而不是用于限制权利要求的保护范围。
[0039]
实施例一:
[0040]
如图1至图7所示,乙炔割炬用粉末冶金割嘴,主要用于乙炔气;该结构包括割嘴外套1,所述割嘴外套1内安装有割嘴芯杆2,所述割嘴芯杆2的后端设置有割嘴杆座3,所述割嘴杆座3采用锥面配合安装在所述割嘴外套1的后端,所述割嘴芯杆2的前端设置有割嘴芯头4,所述割嘴杆座与所述割嘴外套之间还设置有杆座固定结构;所述割嘴芯杆2、所述割嘴杆座3与所述割嘴芯头4一体成型形成割嘴芯套。
[0041]
所述割嘴芯套的中心贯穿设置有氧气通道5,所述氧气通道5内用于通入氧气实现切割作用;所述割嘴芯杆2与所述割嘴外套1之间设置有混合燃气通道6,所述割嘴杆座3与所述割嘴外套1之间设置有多个与所述混合燃气通道6连通的混合燃气进口7,所述割嘴外套1的前端设置有用于安装所述割嘴芯头4的柱形孔,所述割嘴芯头4的后端同轴固定在所述割嘴外套1内,所述割嘴芯头4的前端与所述割嘴外套1之间设置有与所述混合燃气通道6连通的混合燃气环形出气道8,混合燃气从所述混合燃气进口7进入至所述混合燃气通道6内,然后再由所述混合燃气环形出气道8排出,在此混合燃气指乙炔气与氧气的混合气体。
[0042]
所述割嘴芯套的后端通过所述割嘴杆座3采用锥面配合安装在所述割嘴外套1的后端,保证了所述割嘴杆座3与割嘴外套1之间的同轴度,所述割嘴芯套的前端通过将所述割嘴芯头4同轴固定在所述割嘴外套1的前端,保证了所述割嘴芯头4与割嘴外套1之间的同轴度;所述割嘴芯套的前端与后端的同轴度均得到了保证,尤其所述割嘴芯头4的同轴度得到了保证,当所述割嘴芯头4长时间高温切割后,所述割嘴芯头4受热即使会发生变形,但是仍然会保持与所述割嘴外套1之间的同轴度,混合燃气从所述割嘴芯头4与所述割嘴外套1之间的缝隙出气始终保持均匀,出气流畅,有效避免出现传统设计中通过螺纹连接出现配合不同轴而造成出气不均匀等问题。
[0043]
所述割嘴杆座3通过所述杆座固定结构安装在所述割嘴外套1上,不再如现有技术中一样将嘴杆通过螺纹连接在外套上,配合安装方式较为简单,可以实现快速安装效果;同时可以保证所述割嘴杆座3与所述割嘴外套1之间连接的稳定性,避免出现连接脱落等影响使用安全性的问题。
[0044]
所述割嘴芯杆2、所述割嘴杆座3与所述割嘴芯头4一体成型形成割嘴芯套,不再如现有技术中一样将嘴芯通过螺纹连接在芯杆上,本装置的一体成型结构通过模具一次成型,加工方式更加方便,成本较低,可大批量生产;且不需要如现有技术中分别加工后再加工螺纹进行配合,因此本装置割嘴芯套与割嘴外套1之间的互换性较高,配合度较好;并且氧气通过所述氧气通道5时,不存在由于螺纹配合而产生的连接缝,气流阻力较小,可以有效保证氧气流动的流畅性与稳定性,使得出气快速与稳定,形成的割缝具有一致性,有效提高切割质量;此外由于割嘴芯头4与割嘴芯杆2之间为一体结构,氧气通过时,不会出现漏气的现象,具有较好的安全性。
[0045]
本实用新型结构简单、设计合理,采用一体成型结构加工方便,并且通过锥面配合使得拆装更加方便;此外所述割嘴芯杆的前端与后端的同轴度均能得到保证,保证出气更加顺畅,提高出气速度,保证切割质量;同时割嘴杆座与割嘴芯头结构等特殊设计,使得本实用新型加工效率明显得到提升,利于产品的批量生产。
[0046]
所述割嘴芯头4的前端与所述割嘴外套1的前端齐平,与现有技术中用于乙炔的环形割嘴结构相同。
[0047]
所述氧气通道5从后往前由大直径圆柱通道通过锥面过渡形成小直径圆柱通道,当氧气由大直径圆柱通道通过进入至小直径圆柱通道时,由于直径突然变小,使得氧气流速突然增大,可以实现快速出气效果;所述混合燃气通道6从后往前由大直径圆环通道通过锥面过渡形成小直径圆环通道,混合燃气由大直径圆环通道进入至小直径圆环通道时,由于直径突然变小,使得混合燃气流速突然增大,可以实现快速出气效果。
[0048]
参见图3,所述割嘴杆座3的外周设置有外锥面31,所述割嘴外套1的后端设置有与所述外锥面31配合安装的内锥孔,在圆锥配合中,外锥面31与内锥孔在轴向力的作用下能自动对中,以保证内、外锥的轴线具有较高的同轴度,并能快速安装。
[0049]
所述杆座固定结构包括所述外锥面31和所述内锥孔之间的自锁锥面配合和/或设置在所述割嘴外套1与所述割嘴杆座3之间的焊接部。所述焊接部可以为点焊或者缝焊,在本实施例中采用缝焊,不仅可以实现稳定安装,同时可以进一步保证配合面处的密封效果。
[0050]
所述割嘴杆座3通过所述杆座固定结构固定安装在所述割嘴外套1内,所述杆座固定结构包括三种结构,分别为:一、所述杆座固定结构包括所述外锥面31和所述内锥孔之间的自锁锥面配合,此时所述外锥面31与所述内锥孔的配合面可以形成自锁锥面,安装时将所述外锥面31配合安装在所述内锥孔内,利用自锁锥面配合实现两者之间的固定安装,此时所述内锥孔与外锥面31之间为过盈配合,通过挤压将所述割嘴杆座3安装在所述内锥孔内然后利用自锁原理实现稳定安装,而不是采用现有技术中的套装配合方式,该套装配合方式虽然能保证一定的同轴度,但是效果较本实用新型差,此外该套装配合方式的无法精准保证两者之间连接的稳定性与密封性;二、所述杆座固定结构包括设置在所述割嘴外套1与所述割嘴杆座3之间的焊接部,此时所述外锥面31配合安装在所述内锥孔内后,在所述割嘴杆座3与所述割嘴外套1的配合面外端进行焊接固定,实现两者之间的固定安装;三、所述杆座固定结构包括所述外锥面31和所述内锥孔之间的自锁锥面配合,同时也包括设置在所述割嘴外套1与所述割嘴杆座3之间的焊接部,在此所述割嘴杆座3与所述割嘴外套1之间通过两种方式进行组合固定。为了保证割嘴的使用效果,因此出厂时就将所述割嘴芯套与割嘴外套1安装好,避免用户自己安装时无法保证安装精度而影响割嘴的切割效果,因此出厂前,将所述割嘴杆座3利用自锁锥面配合安装在所述割嘴外套1上,安装完成后所述割嘴杆座3的后端面与割嘴外套1的后端面齐平;但是为了避免运输过程中,由于颠簸或碰撞而造成割嘴芯套从割嘴外套1中脱离的现象,同时也为了避免一旦脱离后割嘴芯头4被磕碰而造成损坏,因此在所述割嘴杆座3与所述割嘴外套1的配合面处进行焊接固定,即在自锁固定安装基础上进一步增设一层安装保障。
[0051]
现有技术中对于所述混合燃气进口7的传统设计是在杆座内的非外周侧开设贯穿孔,因此对混合气孔需要进行额外加工,操作更加复杂,此种贯穿孔的其中一种加工方式主要是在模具成型时,通过增设利于形成贯穿孔的杆用于形成贯穿孔,此种利用杆形成贯穿
孔的方式,增加了模具制造的复杂难度,且杆的定位也较为复杂;另一种加工方式主要是在制品模具成型或者机加工后,再采用其他孔加工方式进行机加工,此种加工方式操作复杂,导致工作效率较低,且易形成瑕疵。而本实用新型所述割嘴杆座3的外周设置有多个混合燃气进气槽32,所述混合燃气进气槽32与所述割嘴外套1之间围合形成所述混合燃气进口7。采用此种混合燃气进气槽32的加工方式更加简单,所述混合燃气进气槽32设置在所述割嘴杆座3的外周侧,虽然将所述混合燃气进气槽32孤立的看,不能实现混合气导入的作用,但是将其与所述割嘴外套1共同围合实现,两者之间形成与现有技术中的混合燃气进口7一样的孔结构。
[0052]
参见图4,所述割嘴杆座3两侧的混合燃气进气槽32对称设置,同侧的所述混合燃气进气槽32的开口朝向同一方向,且两侧的所述混合燃气进气槽32的开口方向相反;所述混合燃气进气槽32为方便向外脱模的槽,所述混合燃气进气槽32可以为曲面槽、矩形槽、梯形槽、三角形槽或组合槽等方便脱模的槽;且所述混合燃气进气槽32沿着所述割嘴杆座3的轴线方向是直上直下的槽,方便加工与利于脱模,参见图3。
[0053]
以图4所示方向为例进行描述,左右两侧的混合燃气进气槽32对称,即在所述割嘴杆座3上形成有一个将左右两侧混合燃气进气槽32对称的对称面,该对称面为左半模34、右半模35的分模面33;所述混合燃气进气槽32是在割嘴芯杆2模具成型时即形成,此时不需要在模具中加入利于成孔的杆,而是在模具的表面增加利于形成混合燃气进气槽32的弧形凸起即可,参见图4,所述割嘴杆座3成型时,以分模面33为界限在左右两侧分别采用左半模34与右半模35,因此脱模时,只要将左半模34向左侧开模,参见图4中ⅰ方向,右半模35向右侧开模,参见图4中ⅱ方向,采用此种成型与脱模方式,混合燃气进口7加工成型方式较为简单,模具可以反复使用,形成的混合燃气进气槽32结构具有良好的一致性,并且不需要其他辅助工具或者孔加工方式进行额外加工,加工效率明显得到提升,利于产品的批量生产。设计模具时,避免将所述混合燃气进气槽32设置在分模面33上。
[0054]
在本实施例中,每个混合燃气进气槽32均为曲面槽,具体地,每个混合燃气进气槽32均包括一个开口朝向外侧的弧形槽孔,所述弧形槽孔的两开口端部设置有利于脱模的脱模面,同一侧混合燃气进气槽32的弧形槽孔的开口均向外朝向该侧,同一侧混合燃气进气槽32的脱模面均相同且与该侧方向平行;左侧的所有混合燃气进气槽32的脱模面均与分模面33垂直,同样右侧的所有混合燃气进气槽32的脱模面均与分模面33垂直,且混合燃气进气槽32的弧形槽孔均与脱模面相切,即左侧的混合燃气进气槽32的开口以及边缘均朝向左侧,右侧所述混合燃气进气槽32的开口以及边缘均朝向右侧,没有出现回勾的曲面。参见图4,左右两侧分别设置在三个混合燃气进气槽32,位于中间的混合燃气进气槽32上下对称,位于上、下的混合燃气进气槽32上下对称,方便模具的加工。
[0055]
现有技术中的割嘴主要采用紫铜材质,并且利用数控机床进行机加工,由于铜材质较软,因此导致割嘴硬度不够,耐磨性较差,而现有技术中为解决这一问题会在割嘴外套1表面镀铬来提高硬度,成本较高,操作复杂;因此本实用新型所述割嘴外套1为粉末冶金外套,所述割嘴芯套为粉末冶金芯套。采用粉末冶金工艺对割嘴外套1和割嘴芯套进行加工制造,加工的具体步骤包括:
[0056]
(1)选择符合要求的金属粉末,根据金属粉末类型选择粘结剂,将金属粉末与粘结剂进行混料、造粒,制成适合注射成型用的原料,在本实施例中,金属粉末选用不锈钢粉末;
[0057]
(2)根据所述割嘴外套1和割嘴芯套的尺寸和结构制作注射成型所用的模具,将原料利用注射成型机注入模具内成型;
[0058]
(3)将模具成型后的制品经过化学办法或者加热分解的办法脱除制品中的粘结剂;
[0059]
(4)将脱除粘结剂后的制品进行高温烧结致密化后得到烧结制品;
[0060]
(5)将烧结制品根据需要进行后处理后得到最终成品。
[0061]
其中,由于所述割嘴芯套的结构复杂,包括所述割嘴芯杆2、割嘴杆座3与割嘴芯头4三部分,为了保证脱模时更加方便与顺利,因此在加工割嘴芯套时采用组合模具,分别为左半模34、右半模35和下半模,下半模用于成型割嘴芯头4,左半模34与右半模35配合用于成型割嘴芯杆2与割嘴杆座3;成型脱模时,左半模34向左侧开模,参见图3中ⅰ方向,右半模35向右侧开模,参见图3中ⅱ方向,下半模向前端开模,参见图3中ⅲ方向,通过此种方式形成的成品,不再需要额外加工孔或者燃气导槽等,加工方式更加简单,生产效率高,生产的割嘴一致性较好,在割嘴装配过程中,各个割嘴芯套与割嘴外套1可以相互替换;此外,本实用新型形成的割嘴为不锈钢割嘴,其结构的硬度以及耐磨性等均较好,不易变形,使用寿命长。
[0062]
参见图3、图5、图6和图7,所述割嘴芯头4的后端设置有同轴固定在所述割嘴外套1内的芯头定位段44,所述割嘴芯头4的前端设置有与所述割嘴外套1之间间隙配合的芯头出口段45,所述混合燃气环形出气道8设置在所述芯头出口段45与所述割嘴外套1之间。所述芯头定位段44的外周设置有多个呈环形阵列的混合燃气导条42,相邻两所述混合燃气导条42之间设置有混合燃气导槽41,混合燃气导槽41沿轴线方向延伸,所述混合燃气导槽41将所述混合燃气环形出气道8与所述混合燃气通道6之间连通。参见图2,所述混合燃气导槽41的后端位于所述混合燃气导条42与割嘴外套1之间配合处的后方,即所述混合燃气导槽41的后端不与所述割嘴外套1配合而是与所述混合燃气通道6连通用于实现气流导通,所述混合燃气导槽41的前端向前延伸至混合燃气环形出气道8,因此,所述混合燃气通道6内的混合燃气首先通过所述混合燃气导槽41的后端进入至所述混合燃气导槽41内,然后沿着所述混合燃气导槽41向前运动,由所述混合燃气环形出气道8的前端排出。
[0063]
所述混合燃气通道6内的混合燃气进入至所述混合燃气导槽41内时,由于混合燃气的运动路径发生改变,因此导致气流的运动方向是无序且混乱的,如果不采取措施,气流继续以此种混乱方式继续运动,会使得排出后的气流发生出气不稳定、不流畅等现象,影响到预热效果;为解决此问题,本实用新型所有混合燃气导条42的外周共同构成用于紧固在所述割嘴外套1上的芯头定位面43,所有所述混合燃气导条42与割嘴外套1之间为过盈配合,即所有所述混合燃气导条42共同构成一个用于紧固在所述割嘴外套1内的定位结构,用于保证所述割嘴芯头4与割嘴外套1之间的安装同轴度;此段由于所有混合燃气导条42与所述割嘴外套1之间均无间隙,因此此段内任意相邻两所述混合燃气导槽41均被位于中间的混合燃气导条42分隔,所以经过所述芯头定位段44内各所述混合燃气导槽41内的混合燃气是相互独立的,在芯头定位段44中每个混合燃气导槽41内形成单独的燃气束,由所述混合燃气通道运动至芯头定位段44的混合燃气被强制分离成分散的气流,将整体无序且混乱的气流分成若干小份的气流,然后让气流沿着各个混合燃气导槽41内运动,运动过程中,由于各个所述混合燃气导槽41内气流之间相互不干扰,且各个气流还单独运动了一段行程,因
此在各个混合燃气导槽41内的气流能快速变得有序且稳定,此时进入至混合燃气环形出气道8内的气流已经趋于稳定,排出至割嘴外的气流稳定性与现有技术相比明显较好;由于芯头出口段45的所述混合燃气环形出气道8为环形结构,因此此段不具有定位作用;此外,进入至芯头出口段45内的混合燃气不再被强制分离,而是形成连续的环形气流,并沿着所述混合燃气环形出气道8呈环形状排出,有利于切割件的预热;本实用新型中通过设置芯头定位段44实现所述割嘴芯头4的同轴固定安装,可以有效避免出现由于芯头不同轴而出现出气不均匀的现象,同时由于该芯头定位段44内还具有使得气流变得更加稳定有序的作用,使得由所述混合燃气环形出气道8内排出的环形气流稳定、运动流速快,从而使得形成的火焰较长,提高了预热与切割速度。
[0064]
在本实施例中,所有混合燃气导条42的结构完全相同,同时所述芯头定位段44形成的芯头定位面43为圆柱面,加工方便,当然芯头定位面43也可是设置为朝向前端内缩的锥形的定位面,这样可以更加方便与割嘴外套1的柱形孔进行定位;芯头出口段45也设置为圆柱结构,这样与割嘴外套1形成的柱形孔之间形成的间隙时是不变的,可以保证气流的运动是稳定的;当然所述芯头出口段45也可以为锥形结构,此时芯头出口段45外壁与割嘴外套1之间的间隙会逐渐增大。
[0065]
所述混合燃气导条42的数量至少为3个,用于具有同轴固定安装作用,当然混合燃气导条42的数量越多,固定安装效果越好,且将气流分隔的越分散,气流经过后越趋于稳定;混合燃气导条42的数量根据实际使用需要进行设置,但不可过多,因为数量过多,会影响气流的快速通过,导致气流运动阻力过大。在本实施例中,设置有八个均匀布置的混合燃气导条42。
[0066]
实施例二:
[0067]
实施例二与实施例一、实施例三的结构基本相同,区别主要在于所述割嘴芯头4的结构不同:参见图8,所述芯头定位段44内其中至少三个均匀布置的混合燃气导条42的外周共同构成用于紧固在所述割嘴外套1上的芯头定位面43,其余混合燃气导条42均与割嘴外套1之间间隙配合。混合燃气导条42的总数量至少为六个,其中至少三个用于同轴固定;参见图8,在本实施例中,共设置有八个混合燃气导条42,四个均匀设置的混合燃气导条42的外周形成芯头定位面43,共同构成用于紧固在所述割嘴外套1内的定位结构,用于保证所述割嘴芯头4与割嘴外套1之间连接的同轴度;同时该混合燃气导条42不仅具有定位作用,同时由于其将连续的气流分隔,具有与实施例一中混合燃气导条42相同的作用,将气流分散,用于提高气流的有序与稳定性;而为了避免如实施例一由于混合燃气导条42数量较多,使得阻力过大,导致燃气流速降低,预热效果差,因此在本实施例中,其余混合燃气导条42与割嘴外套1之间有间隙,不具有定位作用,仅具有导流作用,由于此处两混合燃气导槽41之间没有完全隔开,降低气流与预热导气槽之间的运动阻力,燃气流速相对较快,形成的火焰长,从而提高预热与切割速度。
[0068]
实施例三:
[0069]
实施例三与实施例一、实施例二的结构基本相同,其中实施例三是在其他实施例的基础上增设另一竖向定位结构,如图10所示,所述割嘴杆座3的外周设置有外锥面31,所述割嘴外套1的后端设置有与所述外锥面31配合安装的内锥孔;所述外锥面31与所述内锥孔的配合面上还对应设置有定位台肩9,通过定位台肩9可以保证安装时,所述割嘴杆座3可
以准确的安装在所述割嘴外套1内,方便安装人员操作。
[0070]
以上显示和描述了本实用新型的基本原理、主要特征及本实用新型的优点。本行业的技术人员应该了解,本实用新型不受上述实施例的限制,上述实施例和说明书中描述的只是说明本实用新型的原理,在不脱离本实用新型精神和范围的前提下,本实用新型还会有各种变化和改进,这些变化和改进都落入要求保护的本实用新型范围内。本实用新型要求保护范围由所附的权利要求书及其等效物界定。
起点商标作为专业知识产权交易平台,可以帮助大家解决很多问题,如果大家想要了解更多知产交易信息请点击 【在线咨询】或添加微信 【19522093243】与客服一对一沟通,为大家解决相关问题。
此文章来源于网络,如有侵权,请联系删除



tips