等离子体气化熔融炉的制作方法



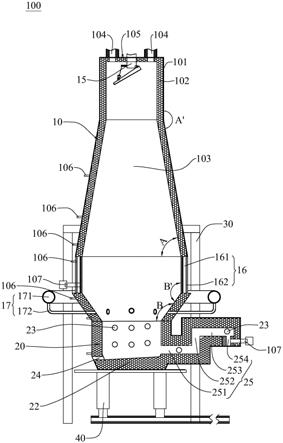
[0001]
本实用新型涉及废弃物处理技术领域,尤其涉及一种等离子体气化熔融炉。
背景技术:
[0002]
目前,对固体废弃物常用的处理技术主要有固化填埋法、焚烧法及高温熔融技术等方法。固化填埋法是最简单和普遍的方法,但该方法存在重大的环境风险和土地资源占用问题,目前已逐步被其他方法所取代。焚烧法是危险废弃物处理领域中较为主流的处理方法,该方法虽然在一定程度上能够起到减量化的作用,但是处理后的残留物如飞灰等依然为危险废弃物,后期仍然需要固化填埋处理,因此无法从根本上解决污染环境及占用土地资源的问题。等离子体高温熔融技术是目前国际上公认的最行之有效且适用于大部分危险废弃物处理的方法,能够做到轻排放和少填埋的效果。但是,现有的等离子体气化炉在焚烧过程中容易产生熔渣挂壁、结瘤等现象,也存在焚烧不完全的现象,而且很难进行清洁、检修。
[0003]
因此,亟需一种能够使减少炉壁内熔渣挂壁、结瘤等现象,又能促进焚烧,而且方便检修的等离子体气化熔融炉。
技术实现要素:
[0004]
本实用新型的目的在于提供一种可以减少炉壁内熔渣挂壁、结瘤等现象,又能促进焚烧且方便检修的等离子体气化熔融炉。
[0005]
为实现上述目的,本实用新型提供了一种等离子体气化熔融炉,包括用于燃烧分解固体废弃物的炉体,炉体上设置有用于鼓风的风管、用于进料的布料装置及用于产生等离子体的等离子发生器;炉体具有中空内腔,炉体包括炉上部和炉下部,炉上部呈拆卸的安装于炉下部并形成中空内腔,中空内腔由上往下依次包括转化段、干燥热解还原段、氧化段、渣段和溶液段,转化段、干燥热解还原段、氧化段、渣段位于炉上部,溶液段位于炉下部,转化段的壁体与干燥热解还原段的壁体之间形成第一夹角,以减少物料下降的阻力;氧化段的壁体与渣段的壁体之间形成第二夹角,以使物料于渣段处充分燃烧。
[0006]
与现有技术相比,本实用新型的等离子体气化熔融炉分为炉上部和炉下部,炉上部和炉下部呈可拆卸的安装在一起,以方便拆卸检修。炉上部包括转化段、干燥热解还原段、氧化段和渣段,转化段的壁体和干燥热解还原段的壁体之间形成第一夹角,设置有第一夹角可以减小危险废弃物下降的摩擦阻力,避免形成料拱,可以减少炉壁内熔渣挂壁、结瘤等现象。氧化段的壁体与渣段的壁体之间形成第二夹角,设置第二夹角可以起到一定的缓冲作用,使物料于渣段处停留并充分燃烧,物料经氧化段反应后变成灰渣,掉入渣段,由于燃烧后体积变小,设置第二夹角可以在渣段呈现锁口,使得灰渣可以在渣段停留更长时间以进行充分燃烧,可以避免物料中心部位焚烧不完全的现象。本实用新型的等离子体气化熔融炉可以减少炉壁内熔渣挂壁、结瘤等现象,又能促进焚烧而且检修方便。
[0007]
较佳地,炉下部包括按预设角度倾斜设置的底壁。底壁倾斜设置以便排出溶液段
内的金属。
[0008]
较佳地,溶液段在靠近底壁低端的一侧开设有用于排出金属的金属出口。金属出口开设在底壁的低端能够更方便的排出燃烧后分解出的金属物质。
[0009]
较佳地,溶液段还开设有溶液通道,溶液通道包括相互连通的流液洞、上升通道、主流道及溶液出口,溶液出口处设置有等离子发生器。溶液通过流液洞、上升通道、主流道,然后从溶液出口流出,在溶液出口处设置有等离子发生器,以便对通道内的溶液进行加热,以防止熔液出口堵塞。
[0010]
较佳地,中空内腔中还设有电极,电极分别布置于溶液段及溶液通道处。在溶液段和溶液通道内设置电极,以将灰渣熔融,灰渣熔融后在溶液段形成熔池。
[0011]
较佳地,风管设置于炉上部并连通于渣段。为避免物料的中心部位焚烧不完全,在渣段区域布置风管,由于渣段与炉下部连接,此处可能存在缝隙且渣段下部的直径偏小,在渣段设置风管,空气更容易的吹到炉内中心位置,空气均匀的透过渣段到氧化段,致使氧化段均匀的燃烧,燃烧需要氧气,氧化段产生了自吸原理,使空气更容易均布。
[0012]
较佳地,氧化段包含水冷套及支撑筋板,支撑筋板安装于水冷套的外侧处,等离子发生器分别呈环绕水冷套的周向布置。设置水冷套可以有效防止渣块挂壁,等离子发生器能够加速氧化段的反应。
[0013]
较佳地,炉体上还设置有用于固定炉上部的固定框架及用于固定支撑炉下部的底部支撑架,炉上部与固定框架固定连接,底部支撑架伸入固定框架内,炉下部安装于底部支撑架处。通过设置固定框架和底部支撑架可以固定支撑整个炉体,使炉体的结构更加稳固。
[0014]
较佳地,底部支撑架包含水平布置并伸入固定框架内的轨道及滑设于轨道上的升降驱动器,炉体下部安装于升降驱动器的输出端处。通过设置升降驱动器,以使炉下部靠近或远离炉上部。
[0015]
较佳地,干燥热解还原段、氧化段、渣段和溶液段均设置有温度传感器。设置有温度传感器可以监测并反馈各反应段的温度。
附图说明
[0016]
为了更清楚地说明本实用新型实施例技术方案,下面将对实施例描述中所需要使用的附图作简单地介绍,显而易见地,下面描述中的附图是本实用新型的一些实施例,对于本领域普通技术人员来讲,在不付出创造性劳动的前提下,还可以根据这些附图获得其他的附图。
[0017]
图1是本实用新型一实施例提供的等离子体气化熔融炉的内部结构示意图。
[0018]
图2是图1所示的等离子体气化熔融炉在界定炉体各段的内部结构示意图。
[0019]
附图标记说明:
[0020]
100、等离子体气化熔融炉;101、外壳;102、耐火层;103、中空内腔;104、烟道;105、料位计;106、温度传感器;107、等离子发生器;
[0021]
10、炉上部;11、转化段;12、干燥热解还原段;13、氧化段;14、渣段;15、布料装置;16、水冷装置;161、水冷套;162、支撑筋板;17、风管;171、环形管;172、进气管;
[0022]
20、炉下部;21、溶液段;22、底壁;23、电极;24、金属出口;25、溶液通道;251、流液洞;252、上升通道;253、主流道;254、溶液出口;
[0023]
30、固定框架;
[0024]
40、底部支撑架;41、升降驱动器;42、轨道。
具体实施方式
[0025]
为了详细说明本实用新型的技术内容、构造特征,以下结合实施方式并配合附图作进一步说明。
[0026]
请参阅图1和图2,本实用新型提供了一种等离子体气化熔融炉100,包括用于燃烧分解固体废弃物的炉体,炉体上设置有用于鼓风的风管17、用于进料的布料装置15及用于产生等离子体的等离子发生器107。炉体具有中空内腔103,通过位于炉体顶部的布料装置15布料进中空内腔103中,固体废弃物在中空内腔103中燃烧熔融。具体的,炉体包括炉上部10和炉下部20,炉上部10呈拆卸的安装于炉下部20并形成用于燃烧熔融固体废弃物的上述中空内腔103。中空内腔103由上往下依次包括转化段11、干燥热解还原段12、氧化段13、渣段14和溶液段21,转化段11、干燥热解还原段12、氧化段13、渣段14位于炉上部10,溶液段21位于炉下部20。其中,转化段11的壁体与干燥热解还原段12的壁体之间形成第一夹角a’,以减少物料下降的阻力。氧化段13的壁体与渣段14的壁体之间形成第二夹角b’,以使物料于渣段14处充分燃烧。
[0027]
在本实施例中,干燥热解还原段12呈上小下大的圆台状,干燥热解还原段12的圆台锥度为角a,转化段11的壁体与干燥热解还原段12的壁体之间形成第一夹角越大则圆台锥度越大,第一夹角越小则圆台锥度越小,∠a’=∠a+90
°
。∠a对烟气流的合理分布和物料顺行影响较大。∠a小,有利于炉料的下降,但容易发展边缘烟气流,∠a过小时会导致边缘烟气流过分发展,使焦比升高。∠a大,有利于抑制边缘烟气流,但不利于炉料下降,对炉体顺行不利。因此,较佳地,∠a设计取值一般在81
°
~85
°
之间。
[0028]
另,渣段14呈上大下小的圆台状,渣段14的圆台锥度为∠b,氧化段13的壁体与渣段14的壁体之间形成的夹角∠b’越大则渣段14的圆台锥度越小,夹角∠b’越小则渣段14的圆台锥度越大,∠b’=180
°-
∠b+90
°
。固体废弃物经氧化段13后变成灰渣,掉入渣段14h4,由于燃烧后体积变小。渣段14呈上大下小的圆台状可以呈现锁口,较佳地,∠b在135
°
~165
°
之间取值。由于渣段14呈上大下小的圆台状,直径渐小,空气更容易吹到炉内中心位置,空气均匀的透过渣段14到氧化段13,致使氧化段13均匀的燃烧,燃烧需要氧气,氧化段13产生了自吸原理,使空气更容易均布。
[0029]
与现有技术相比,本实用新型的等离子体气化熔融炉100分为炉上部10和炉下部20,炉上部10和炉下部20呈可拆卸的安装在一起,以方便拆卸检修。炉上部10包括转化段11、干燥热解还原段12、氧化段13和渣段14,转化段11的壁体和干燥热解还原段12的壁体之间形成第一夹角,设置有第一夹角可以减小危险废弃物下降的摩擦阻力,避免形成料拱,可以减少炉壁内熔渣挂壁、结瘤等现象。氧化段13的壁体与渣段14的壁体之间形成第二夹角,设置第二夹角可以起到一定的缓冲作用,使物料于渣段14处停留并充分燃烧,物料经氧化段13反应后变成灰渣,掉入渣段14,由于燃烧后体积变小,设置第二夹角可以在渣段14呈现锁口,使得灰渣可以在渣段14停留更长时间以进行充分燃烧,可以避免物料中心部位焚烧不完全的现象。本实用新型的等离子体气化熔融炉100可以减少炉壁内熔渣挂壁、结瘤等现象,又能促进焚烧而且检修方便。
[0030]
请参阅图1和图2,在一些可选的实施例中,炉下部20包括按预设角度倾斜设置的底壁22,即底壁22的厚度不一,呈一边高一边低的状态。具体的,溶液段21即炉下部20在靠近底壁22低端的一侧开设有用于排出金属的金属出口24。固体废弃物中存在很多金属物质,而溶液段21内设置有电极23,熔池中若是金属含量过高达到石墨电极23的位置,会造成电极23的短路。因此需要定期排出溶液段21内的金属,打开金属出口24,由于底壁22倾斜设置,而金属出口24开设在底壁22的低端能够更方便的排出燃烧后分解出的金属物质。可以理解的,预设角度可以为0
°
~45
°
之间。较佳地,预设角度为5
°
~15
°
,只要能更方便的排出金属又不影响整体结构即可。
[0031]
请参阅图1和图2,在一些可选的实施例中,溶液段21还开设有溶液通道25,溶液通道25包括相互连通的流液洞251、上升通道252、主流道253及溶液出口254。溶液段21及溶液通道25处布置有电极23,溶液出口254处还设置有等离子发生器107。溶液通过流液洞251、上升通道252、主流道253,然后从溶液出口254流出。在溶液段21和溶液通道25内设置电极23,以将灰渣熔融,灰渣熔融后在溶液段21形成熔池。在溶液出口254处设置有等离子发生器107,以便对通道内的溶液进行加热,以防止熔液出口堵塞。
[0032]
请参阅图1和图2,在一些可选的实施例中,风管17设置于炉上部10并连通于渣段14。风管17包括环形管171和进气管172,进气管172连通于中空内腔103和环形管171,在渣段14的壁体上开设有若干个供进气管172穿置的通孔,进气管172的一端向炉内供气,进气管172的另一端连接于环形管171内。环形管171上至少开设一个用于进气的进气口,设置有环形管171道可以避免炉内的温度直接从进气管172散发,有效减少了炉体内的热量损耗。另,设置环形管171道,在炉内含氧量需要提高时,只需对环形管171道的进气口进行鼓风即可,操作更方便。在本实施例中,为避免物料的中心部位焚烧不完全,在渣段14区域布置风管17,由于渣段14与炉下部20连接,此处可能存在缝隙。而渣段14呈上大下小的圆台状,渣段14下部的直径偏小,在渣段14设置风管17,空气更容易的吹到炉内中心位置,空气均匀的透过渣段14到氧化段13,致使氧化段13均匀的燃烧,燃烧需要氧气,氧化段13产生了自吸原理,使空气更容易均布。
[0033]
请参阅图1和图2,在一些可选的实施例中,氧化段13还设置有水冷装置16,水冷装置16包含水冷套161及支撑筋板162,支撑筋板162安装于水冷套161的外侧处,用于对水冷套161进行支撑固定。等离子发生器107分别呈环绕水冷套161的周向布置。设置水冷套161可以有效防止渣块挂壁,等离子发生器107能够加速氧化段13的反应。较优的是,等离子发生器107的数量为三台,均匀地环绕水冷套161,以使得氧化段13在等离子发生器107的作用下产生高温等离子体,使危险废料中的无机物彻底地分解,同时对炉渣提供了大量的热量。当然,等离子发生器107的数量也可以为其他,例如两台、四台、五台等。水冷套161及支撑筋板162的作用下,防止渣块挂壁现象。具体地,水冷套161上安装有氧化段13的温度传感器106,以便观察反应温度的情况。
[0034]
请参阅图1和图2,在一些可选的实施例中,炉体上还设置有用于固定炉上部10的固定框架30及用于固定支撑炉下部20的底部支撑架40,炉上部10与固定框架30固定连接,底部支撑架40伸入固定框架30内,炉下部20安装于底部支撑架40处。具体的,底部支撑架40包含水平布置并伸入固定框架30内的轨道42及滑设于轨道42上的升降驱动器41,炉体下部安装于升降驱动器41的输出端处。通过设置固定框架30和底部支撑架40可以固定支撑整个
炉体,使炉体的结构更加稳固。通过设置升降驱动器41,以使炉下部20靠近或远离炉上部10,更便于快速检修。可以理解的,炉上部10与固定框架30固定连接,由固定框架30对炉上部10进行支撑固定。而底部支撑架40伸入固定框架30内,炉下部20安装于底部支撑架40处。在本实施例中,底部支撑架40包含水平布置并伸入固定框架30内的轨道42及滑设于轨道42上的升降驱动器41,炉下部20安装于升降驱动器41的输出端处,由升降驱动器41驱使炉下部20做与炉上部10接合或分离的运动。示例性的,升降驱动器41为液压缸,当然,根据实际需要,升降驱动器41还可以为直线电机或气缸,故不以此为限。
[0035]
结合附图1和附图2,对本实用新型的等离子体气体熔融一体炉的工作原理进行说明:
[0036]
炉体中炉上部10和炉下部20均包括钢制的外壳101和耐火层102,耐火层102由外到内依次是纳米绝热板、含锆陶瓷半硬、莫来石保温砖、密封填料和锆铬刚玉砖。炉上部10分为转化段11、干燥热解还原段12、氧化段13和渣段14,而溶液段21位于炉下部20。其中,干燥热解还原段12、氧化段13、渣段14和溶液段21均设置有温度传感器106。设置有温度传感器106可以监测并反馈各反应段的温度。图2中,左边的尺寸标号h1所指的是转化段11的范围,尺寸标号h2所指的是干燥热解还原段12的范围,尺寸标号h3所指的是氧化段13的范围,尺寸标号h4所指的是渣段14的范围,尺寸标号h5所指的是溶液段21的范围。
[0037]
当物料(例如但不限于此的危险废弃物)从布料装置15均匀地布置到中空内腔103中位于转化段11内,通过料位计105来观测炉内料位的情况。危险废弃物经过转化段11掉落在干燥热解还原段12内,由于干燥热解还原段12为正圆台状,其形状适应危险废弃物受热后体积的膨胀和烟气流冷却后体积的收缩,有利于减小危险废弃物下降的摩擦阻力,避免形成料拱。同时,干燥热解还原段12安装有用于干燥层的温度传感器106、用于热解层的温度传感器106及用于还原层的温度传感器106,以分别检测干燥热解还原段12各段层的温度。
[0038]
而进入干燥热解还原段12内的危险废弃物被干燥热解还原段12进行处理有如下步骤:当危险废弃物进入干燥热解还原段12内后,在热量的作用下,析出水分。在100~250度时为干燥阶段,当温度升高到300度以上时开始进行热解反应。在300~800度时,危险废弃物中的有机组分就可以释放出70%左右的挥发组分,同时,等离子体发生器的高能量密度输入也加快和促进了有机组分的分解。热解反应析出挥发份主要包括碳氢化合物、氢气、水蒸气、一氧化碳、二氧化碳、甲烷、焦油等。
[0039]
热解反应方程式为:cxhyoz
→
c(s)+h2+h2o+co+co2+ch4+tar
[0040]
还原过程为缺氧环境,其下部的氧化段13中的燃烧产物及水蒸气与还原层中的碳发生反应,生成h2和co等。
[0041]
主要反应如下:co+c
→
co;h2o+c
→
h2+co
[0042]
危险废弃物经过以上三个干燥热解还原阶段后,剩余的固定碳与风管17引入的空气发生化学反应,释放大量的热以支持危险废弃物的干燥、热解和后续的还原反应。主要反应如下:c+o2
→
co2
[0043]
而被干燥热解还原段12处理后的废物进入氧化段13,由于氧化段13的反应温度在900~1200℃,温度过高,部分废物达到灰熔点,等离子发生器107在氧化段13上均匀地布置三台,但不局限于三台。在等离子发生器107的作用下产生高温等离子体,使危险废料中的
无机物彻底地分解,同时对炉渣提供了大量的热量,同时,氧化段13包含水冷套161和支撑筋板162结构,可以防止渣块挂壁现象。
[0044]
经氧化段13后废物将变成灰渣,掉入渣段14,由位于渣段14的温度传感器106检测渣段14的温度。
[0045]
经过渣段14后的物料最后掉入溶液段21,溶液段21设置有温度传感器106,用于观察溶液段21的温度情况。而炉体上部和炉体下部之间的接合处采用玻璃水加高温土结合的方式把上下两个部分连接起来密封,其中,高温土耐温度可达1800摄氏度以上。而内部的高温熔融液体在向外流动的时遇冷凝结成块状,也起到了密封作用。
[0046]
另,由于溶液段21装有电极23,掉入溶液段21内的灰渣提供熔融的温度,熔融后形成溶液,溶液进过流液洞251,在经过上升通道252到主流道253,然后由溶液出口254流出,在溶液出口254处设置有等离子发生器107,以便对通道内的溶液进行加热,以防止熔液出口堵塞。由于炉体下部由底部支撑架40所支撑,而底部支撑架40包含轨道42及升降驱动器41,方便炉体下部的维修。
[0047]
而炉内保持微负压,保证有害气体不外排,烟气经过干燥热解氧化段13后进入转化段11,然后经过顶部左右两侧的烟道104,烟道104的数量可以根据实际需要进行增多或减少,多个烟道104再汇集到一个主烟道然后到达二燃室。
[0048]
以上所揭露的仅为本实用新型的较佳实例而已,不能以此来限定本实用新型之权利范围,因此依本实用新型权利要求所作的等同变化,均属于本实用新型所涵盖的范围。
起点商标作为专业知识产权交易平台,可以帮助大家解决很多问题,如果大家想要了解更多知产交易信息请点击 【在线咨询】或添加微信 【19522093243】与客服一对一沟通,为大家解决相关问题。
此文章来源于网络,如有侵权,请联系删除
相关标签: 等离子



tips