一种燃气锅炉蓄热稳燃装置的制作方法



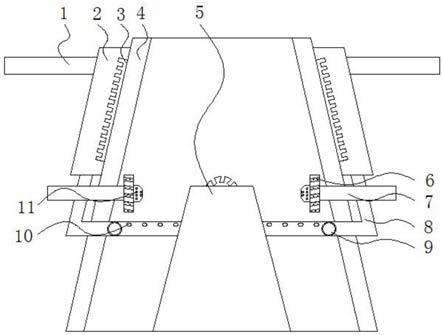
[0001]
本实用新型涉及燃气锅炉蓄热稳燃技术领域,具体为一种燃气锅炉蓄热稳燃装置。
背景技术:
[0002]
燃气锅炉包括燃气开水锅炉、燃气热水锅炉、燃气蒸汽锅炉等,其中燃气热水锅炉也称燃气采暖锅炉和燃气洗浴锅炉,燃气锅炉顾名思义指的是燃料为燃气的锅炉,燃气锅炉和燃油锅炉、电锅炉比较起来最经济,所以大多数人们都选择了燃气锅炉作为蒸汽、采暖、洗浴用的锅炉设备。
[0003]
如申请公布号cn 205782932 u的专利公开了,一种燃气锅炉蓄热稳燃装置,通过在燃烧腔上方的炉体内设有蓄热块,蓄热块与炉体内壁相配合,蓄热块中间嵌设有蓄热网,蓄热网在锅炉燃烧时会蓄热,温度可达1000度,而且这种蓄热网为网状结构,进而极大的增大了燃气和蓄热网的接触面积,从而提高了燃气的燃烧效率,在锅炉燃烧时,锅炉燃烧时,空气和燃气分别沿着氧气供气管和燃气供气管进入氧气加热腔和燃气加热腔,进而被氧气加热腔5和燃气加热腔所在的散热翅片进行加热,这里就能利用炉体外壁的燃烧余热对燃气和氧气进行预热,进而提高了燃气的燃烧效率,本实用新型结构简单、合理,极大的提高了燃气的燃烧效率,降低排气对环境的污染,起到节能的作用,实用性强。
[0004]
现有技术的燃气锅炉蓄热稳燃有以下缺点:1、上述专利中氧气管和燃气管位于炉体两侧,燃烧时燃气与氧气混合不完全,有部分燃气未吸收足够氧气,燃烧不充分,燃烧效果不好;2、燃气管内输送燃气时,燃气内含有固体燃料颗粒,燃烧过程中固体燃料颗粒打到炉体表面造成炉体磨损,炉体使用寿命短,为此,我们提出一种燃气锅炉蓄热稳燃装置。
技术实现要素:
[0005]
本实用新型要解决的技术问题是克服现有的缺陷,提供一种燃气锅炉蓄热稳燃装置,燃气通过稳焰器上通孔分散排入炉体,氧气管环绕在炉体内部经出气口排出,可使氧气与燃气充分混合进行燃烧;炉体内内壳和耐磨涂层a、耐磨涂层b配合提高炉体内表面耐磨能力,避免燃气内固体颗粒对炉体造成损伤,可以有效解决背景技术中的问题。
[0006]
为实现上述目的,本实用新型提供如下技术方案:一种燃气锅炉蓄热稳燃装置,包括炉体,所述炉体内表面堆砌连接有耐火砖,所述耐火砖表面粘接有内壳,所述内壳表面喷涂有耐磨涂层a,所述耐磨涂层a表面涂敷有耐磨涂层b,所述炉体顶端固定连接有加热箱,所述加热箱两侧可拆卸连接有进气管,所述加热箱底端间隙连接有出气管,所述出气管的进气口延伸到氧气管的内部,所述氧气管表面开设有出气口,所述氧气管位于燃气管的下方,所述燃气管贯穿连接有炉体且燃气管有四个,所述燃气管可拆卸连接有稳焰器,所述稳焰器表面开设有通孔且通孔有两组,所述炉体中部安装有蓄热块。
[0007]
作为本实用新型的一种优选技术方案,所述炉体顶端表面粘接有散热片,所述散热片位于加热箱的内部。
[0008]
作为本实用新型的一种优选技术方案,所述氧气管可拆卸连接在炉体的内表面,所述内壳材质为钨钢。
[0009]
与现有技术相比,本实用新型的有益效果是:
[0010]
1、燃气通过稳焰器上通孔分散排入炉体,氧气管环绕在炉体内部经出气口排出,可使氧气与燃气充分混合进行燃烧;燃气经多个燃气管排入炉体内,燃气管顶端安装有稳焰器且稳焰器顶端开设有通孔,通孔有多个且环绕在稳焰器顶端,燃气经通孔排出后燃气整体分散,同时加热后的空气经出气管输送进氧气管内,氧气管环绕在炉体内表面且氧气管上开设有多个出气口,出气口向内倾斜,氧气管内喷出的空气倾斜喷射到上方与燃气管喷出的燃气进行混合,燃气和空气分别经通孔和出气口进行分散,分散后的气体相混合进行燃烧,燃烧过程中蓄热块放热对与蓄热块接触的未完全燃烧的混合气进行加热使其充分燃烧,可使燃气与氧气充分混合进行燃烧,燃烧效果好。
[0011]
2、炉体内内壳和耐磨涂层a、耐磨涂层b配合提高炉体内表面耐磨能力,避免燃气内固体颗粒对炉体造成损伤;炉体内表面连接有内壳,内壳材质为钨钢,钨钢具有硬度高、耐磨、耐热一系列优良性能,特别是它的高硬度和耐磨性,即使在500℃的温度下也基本保持不变,在1000℃时仍有很高的硬度,耐磨涂层a和耐磨涂层b均为陶瓷耐磨涂层,陶瓷耐磨涂层喷涂后内壳表面硬度可提高5到10倍,可大幅减少表面磨耗,可显著降低炉体与燃气中携带的燃料固体颗粒间的摩擦力,明显减少燃气燃烧过程中产生的刮痕及磨耗,耐磨涂层为双层,可显著提高炉体的硬度和耐磨性能,钨钢与耐磨涂层相配合可减少燃气固体颗粒与炉体间的磨损。
附图说明
[0012]
图1为本实用新型实施例的一种燃气锅炉蓄热稳燃装置的整体结构示意图;
[0013]
图2为本实用新型实施例的一种燃气锅炉蓄热稳燃装置的炉体的结构示意图;
[0014]
图3为本实用新型实施例的一种燃气锅炉蓄热稳燃装置的燃气管位置安装的结构示意图;
[0015]
图4为本实用新型实施例的一种燃气锅炉蓄热稳燃装置的稳焰器的结构示意图。
[0016]
图中:1、进气管;2、加热箱;3、散热片;4、炉体;5、蓄热块;6、稳焰器;7、燃气管;8、出气管;9、氧气管;10、出气口;11、通孔;12、耐火砖;13、内壳;14、耐磨涂层a;15、耐磨涂层b。
具体实施方式
[0017]
下面将结合本实用新型实施例中的附图,对本实用新型实施例中的技术方案进行清楚、完整地描述,显然,所描述的实施例仅仅是本实用新型一部分实施例,而不是全部的实施例。基于本实用新型中的实施例,本领域普通技术人员在没有做出创造性劳动前提下所获得的所有其他实施例,都属于本实用新型保护的范围。
[0018]
请参阅图1-4,本实用新型提供一种技术方案:一种燃气锅炉蓄热稳燃装置,包括炉体4,所述炉体4内表面堆砌连接有耐火砖12,所述耐火砖12表面粘接有内壳13,所述内壳13表面喷涂有耐磨涂层a14,所述耐磨涂层a14表面涂敷有耐磨涂层b15,所述炉体4顶端固定连接有加热箱2,所述加热箱2两侧可拆卸连接有进气管1,所述加热箱2底端间隙连接有
出气管8,所述出气管8的进气口延伸到氧气管9的内部,所述氧气管9表面开设有出气口10,所述氧气管9位于燃气管7的下方,所述燃气管7贯穿连接有炉体4且燃气管7有四个,所述燃气管7可拆卸连接有稳焰器6,所述稳焰器6表面开设有通孔11且通孔11有两组,所述炉体4中部安装有蓄热块5。
[0019]
示例的,炉体4内包括燃气管7、稳焰器6、氧气管9和蓄热块5,蓄热块5呈圆台形结构,炉内蓄热块5在点火时吸收热量,温度升高后成为一个炽热体,运行温度一般在1000c以上,它的温度高于高炉煤气时,就向高炉煤气传热,使其温度升高,提高燃烧品质,当它的温度低于高炉煤气时,就从其中吸收热量,使自身温度提高,加热箱2环绕在炉体4顶端表面,空气经进气管1进入加热箱2内,加热箱2内散热片3与炉体4内烟气进行热交换,空气与散热片3接触对空气进行加热。
[0020]
参考图1所示,所述炉体4顶端表面粘接有散热片3,所述散热片3位于加热箱2的内部。
[0021]
示例的,散热片3与炉体4顶端接触,燃烧后烟气的热量经炉体4传递给散热片3,散热片3在加热箱2内与流经的空气接触对空气进行加热。
[0022]
参考图1所示,所述氧气管9可拆卸连接在炉体4的内表面,所述内壳13材质为钨钢。
[0023]
示例的,氧气管9粘接在炉体4内表面进行固定,内壳13为钨钢,钨钢是指至少含有一种金属碳化物组成的烧结复合材料,具有硬度高、耐磨、强度和韧性较好、耐热等一系列优良性能。
[0024]
在使用时:空气经空气泵作用下经进气管1进入加热箱2,燃气经多个燃气管7排入炉体4内,燃气管7顶端安装有稳焰器6且稳焰器6顶端开设有通孔11,通孔11有多个且环绕在稳焰器6顶端,燃气经通孔11排出后燃气整体分散,加热箱2内散热片3粘接在炉体4顶端,散热片3与炉体4顶端接触,燃烧后烟气的热量经炉体4传递给散热片3,散热片3在加热箱2内与流经的空气接触对空气进行加热,加热后的空气经出气管8输送进氧气管9内,氧气管9环绕在炉体4内表面且氧气管9上开设有多个出气口10,出气口10向内倾斜,氧气管9内喷出的空气倾斜喷射到上方与燃气管7喷出的燃气进行混合,燃气和空气分别经通孔11和出气口10进行分散,分散后的气体相混合进行燃烧,燃烧过程中蓄热块5放热对与蓄热块5接触的未完全燃烧的混合气进行加热使其充分燃烧,可使燃气与氧气充分混合进行燃烧,炉体4内表面连接有内壳13,内壳13材质为钨钢,钨钢具有硬度高、耐磨、耐热一系列优良性能,特别是它的高硬度和耐磨性,即使在500℃的温度下也基本保持不变,在1000℃时仍有很高的硬度,耐磨涂层a14和耐磨涂层b15均为陶瓷耐磨涂层,陶瓷耐磨涂层喷涂后内壳13表面硬度可提高5到10倍,可大幅减少表面磨耗,可显著降低炉体4与燃气中携带的燃料固体颗粒间的摩擦力,明显减少燃气燃烧过程中产生的刮痕及磨耗,耐磨涂层为双层,可显著提高炉体的硬度和耐磨性能,减少燃气固体颗粒与炉体间的磨损。
[0025]
需要说明的是,本实用新型为一种汽车座椅靠背架的预成型模具,包括1、进气管;2、加热箱;3、散热片;4、炉体;5、蓄热块;6、稳焰器;7、燃气管;8、出气管;9、氧气管;10、出气口;11、通孔;12、耐火砖;13、内壳;14、耐磨涂层a;15、耐磨涂层b,部件均为通用标准件或本领域技术人员知晓的部件,其结构和原理都为本技术人员均可通过技术手册得知或通过常规实验方法获知。
[0026]
尽管已经示出和描述了本实用新型的实施例,对于本领域的普通技术人员而言,可以理解在不脱离本实用新型的原理和精神的情况下可以对这些实施例进行多种变化、修改、替换和变型,本实用新型的范围由所附权利要求及其等同物限定。
起点商标作为专业知识产权交易平台,可以帮助大家解决很多问题,如果大家想要了解更多知产交易信息请点击 【在线咨询】或添加微信 【19522093243】与客服一对一沟通,为大家解决相关问题。
此文章来源于网络,如有侵权,请联系删除



tips