一种电磁感应蒸汽发生器的制造方法及蒸汽发生器与流程



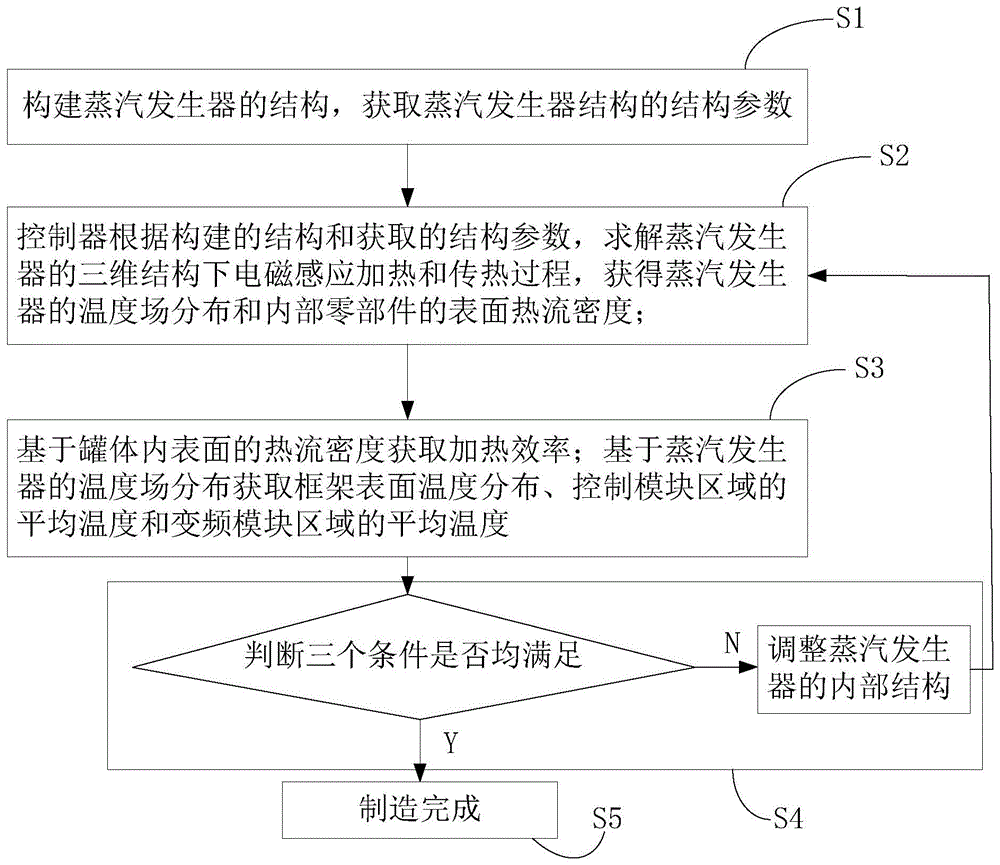
本发明涉及一种蒸汽发生器,特别是涉及一种电磁感应蒸汽发生器的制造方法及蒸汽发生器。
背景技术:
目前,市场上出现的工业用低压蒸汽发生器,多采用燃油加热、燃煤加热或电热管加热等形式,这些传统的加热方式均存在能耗大,运行成本高,污染环境等问题,随着国家积极推广绿色、环保、高效节能新能源的形式以及日益严重的雾霾问题,这些低效率的加热方式正逐步被淘汰。相比于上述传统加热方式,出现了电磁加热式的蒸汽发生器,电磁加热式蒸汽发生器不但解决了传统加热方式的热效率低、耗能高,环境污染严重的问题,而且也解决了电阻丝加热所存在的安全隐患问题,具有良好的市场及经济价值。但是,现有的电磁感应蒸汽发生器也存在着诸如蒸汽发生器壳体散热性不好导致内部存在局部高温、局部金属壳体或内部金属结构因电磁感应而发热、大功率条件下变频模块因焦耳热温度过高、双罐间距设置不合理导致电磁转化效率下降等问题,给蒸汽发生器的运行稳定性和安全性带来了风险,能量损耗较大。随着当前对电磁感应蒸汽发生器的小型化和紧凑化要求越来越高,上述问题将更加突出,亟待解决。
技术实现要素:
本发明旨在至少解决现有技术中存在的技术问题,特别创新地提出了一种电磁感应蒸汽发生器的制造方法及蒸汽发生器。
为了实现本发明的上述目的,根据本发明的第一个方面,本发明提供了一种电磁感应蒸汽发生器的制造方法,包括:步骤s1,构建蒸汽发生器的结构,获取蒸汽发生器结构的结构参数;步骤s2,根据构建的结构和获取的结构参数,求解蒸汽发生器的三维结构下电磁感应加热和传热过程,获得蒸汽发生器的温度场分布和内部零部件的表面热流密度;步骤s3,基于罐体内表面的热流密度获取加热效率;基于蒸汽发生器的温度场分布获取框架表面温度分布、控制模块区域的平均温度和变频模块区域的平均温度;步骤s4,判断是否满足以下三个条件:条件一:加热效率大于等于目标效率;条件二:框架表面不存在达到局部温度阈值的位置点;条件三:控制模块区域的平均温度未达到第一高温阈值,并且变频模块区域的平均温度未达到第二高温阈值;若上述三个条件均满足,进入步骤s5;若上述三个条件中至少有一个条件不满足,则调整蒸汽发生器的内部结构,具体包括调整线圈直径、线圈匝数、罐体绕线密度、增加罐体之间的间距、罐体位置、控制模块与变频模块之间的距离六者中至少一者,返回步骤s2;步骤s5,完成制造。
上述技术方案的有益效果为:该制造方法通过调整内部结构,确保加热效率、框架表面局部高温、以及控制模块区域和变频模块区域的平均温度都符合预设要求,减少了能量损耗,避免框架表面出现用户体验不好的局部高温,使控制模块和变频模块工作在允许的温度范围内,提高了蒸汽发生器的运行稳定性、可靠性和安全性,有利于蒸汽发生器的小型化和紧凑化。
在本发明的一种优选实施方式中,在所述步骤s4中,调整蒸汽发生器的内部结构的过程包括:若条件一不满足,则执行减小线圈直径、增加线圈匝数、增大罐体绕线密度、当罐体为一个以上时增加罐体之间的间距四者中至少一者;若条件二不满足,调整罐体位置以增大框架上所述位置点与罐体的距离;若条件三不满足,增大控制模块与变频模块之间的距离,和/或设置一个冷却回路,用于降低控制模块区域和/或变频模块区域的温度。
上述技术方案的有益效果为:条件一不满足时的改善措施,能够有效提高加热效率,避免多罐时罐间距设置不合理导致电磁转化效率下降等问题。条件二不满足时的改善措施,直接有效地改善了框架局部高温的问题。若条件三不满足时,增大控制模块与变频模块之间的距离,能够分散热源,避免热源交叉影响使温度更高;通过冷却回路,能够快速有效地降低控制模块和变频模块的温度,提高其运行可靠性。
在本发明的一种优选实施方式中,所述加热效率rheating为:
上述技术方案的有益效果为:公开了一种快速计算加热效率的方法。
在本发明的一种优选实施方式中,若条件一不满足时,还包括如下步骤:
根据蒸汽管道和汽包表面的加热密度获取散热比,判断所述散热比是否小于预设的目标散热比,若所述散热比不小于目标散热比,在蒸汽管道和汽包的全部或部分外表面裹附一层保温层,若所述散热比小于目标散热比,不增设保温层;所述散热比rra为:
上述技术方案的有益效果为:对蒸汽管道和汽包散热损耗进行有效估计,当其散热比不小于目标散热比时,设置保温层,能够减少散热损耗,从而提高加热效率。
为了实现本发明的上述目的,根据本发明的第一个方面,本发明提供了一种利用本发明所述制造方法制造的电磁感应蒸汽发生器,包括框架,所述框架内划分有加热区和控制区;在所述加热区内设置有至少一个罐体、缠绕在所述罐体上的线圈、与罐体出气口连接的蒸汽管道、串接于所述蒸汽管道上的汽包,所述蒸汽管道延伸出所述框架;在所述控制区内设置有控制模块和为所述线圈供电的变频模块,所述控制模块与变频模块连接通信。
上述技术方案的有益效果为:该蒸汽发生器的加热效率、框架表面局部高温、以及控制模块区域和变频模块区域的平均温度都符合预设要求,减少了能量损耗,避免框架表面出现用户体验不好的局部高温,使控制模块和变频模块工作在允许的温度范围内,运行稳定性、可靠性和安全性,其结构还具有小型化和紧凑化的特点。
在本发明的一种优选实施方式中,还包括裹附于蒸汽管道和/或汽包的全部或部分外表面的保温层。
上述技术方案的有益效果为:能够有效减少蒸汽管道和/或汽包表面的散热损耗,从而提高了加热效率。
在本发明的一种优选实施方式中,还包括设置于控制区的冷却回路;所述冷却回路上依次管路连接有进液口、冷却泵、途经控制模块和/或变频模块的冷却管道、以及出液口;所述控制模块的第一信号输出端与冷却泵的控制端连接。
上述技术方案的有益效果为:冷却回路采用水冷方式对控制模块和/或变频模块进行进行快速降温,环境污染小,使控制模块和/或变频模块工作在适宜的温度环境中,增加了运行可靠性,延长了使用寿命。
在本发明的一种优选实施方式中,所述冷却回路的出液口与至少一个罐体的进水口管路连接;或者所述冷却回路还包括回收支路,所述回收支路一端与出液口附近的冷却回路管道连通,回收支路的另一端与至少一个罐体的的进水口连通,所述回收支路上设置有电控阀,所述罐体内设有液位计,控制模块接收液位计输出的罐体内液位信号控制电控阀开启或关闭。
上述技术方案的有益效果为:将流经控制模块和/或变频模块的冷却水回收到罐体中产生蒸汽,在降低控制模块和/或变频模块温度的同时,对热量进行了回收利用,能够提高蒸汽发生器的加热效率。单设回收支路,便于自动根据罐体内液位情况控制冷却水的回收利用。
在本发明的一种优选实施方式中,所述变频模块安装在第一散热板上,所述控制模块安装在第二散热板上;所述冷却管道包括分别开设于所述第一散热板中和所述第二散热板中的第一冷却流道和第二冷却流道,所述第一冷却流道和第二冷却流道串接于冷却回路中。
上述技术方案的有益效果为:利用散热板良好的导热性,能够快速均匀地对控制模块和/或变频模块进行散热。
在本发明的一种优选实施方式中,所述罐体包括并行放置的第一罐体和第二罐体,所述第一罐体外缠绕有第一线圈,所述第二罐体外缠绕有第二线圈;
所述蒸汽管道包括贯穿汽包的第一蒸汽管道和第二蒸汽管道,第一蒸汽管道的第一端与第一罐体的出气口连接,第二蒸汽管道的第一端与第二罐体的出气口连接,第一蒸汽管道的第二端与第二蒸汽管道的第二端汇合后向外输出蒸汽。
上述技术方案的有益效果为:公开了双罐体时蒸汽管道和汽包结构,该结构紧凑、整体体积小。
附图说明
图1是本发明一具体实施方式中电磁感应蒸汽发生器的制造方法的流程示意图;
图2是本发明一具体实施方式中求解蒸汽发生器的三维结构下电磁感应加热和传热过程示意图;
图3是本发明一具体实施方式中蒸汽发生器的内部结构示意图;
图4是本发明另一具体实施方式中蒸汽发生器的内部结构示意图。
附图标记:
1框架;2罐体;3线圈;4蒸汽管道;5汽包;6控制模块;7变频模块;8冷却回路;81进液口;82冷却泵;83出液口;84第一冷却流道;85第二冷却流道;9第一散热板;10第二散热板;11水箱。
具体实施方式
下面详细描述本发明的实施例,所述实施例的示例在附图中示出,其中自始至终相同或类似的标号表示相同或类似的元件或具有相同或类似功能的元件。下面通过参考附图描述的实施例是示例性的,仅用于解释本发明,而不能理解为对本发明的限制。
在本发明的描述中,需要理解的是,术语“纵向”、“横向”、“上”、“下”、“前”、“后”、“左”、“右”、“竖直”、“水平”、“顶”、“底”“内”、“外”等指示的方位或位置关系为基于附图所示的方位或位置关系,仅是为了便于描述本发明和简化描述,而不是指示或暗示所指的装置或元件必须具有特定的方位、以特定的方位构造和操作,因此不能理解为对本发明的限制。
在本发明的描述中,除非另有规定和限定,需要说明的是,术语“安装”、“相连”、“连接”应做广义理解,例如,可以是机械连接或电连接,也可以是两个元件内部的连通,可以是直接相连,也可以通过中间媒介间接相连,对于本领域的普通技术人员而言,可以根据具体情况理解上述术语的具体含义。
本发明公开了一种电磁感应蒸汽发生器的制造方法,在一种优选实施方式中,该方法的流程示意图如图1所示,具体包括:
步骤s1,构建蒸汽发生器的结构,获取蒸汽发生器结构的结构参数;
步骤s2,根据构建的结构和获取的结构参数,求解蒸汽发生器的三维结构下电磁感应加热和传热过程,获得蒸汽发生器的温度场分布和内部零部件的表面热流密度;
步骤s3,基于罐体2内表面的热流密度获取加热效率;基于蒸汽发生器的温度场分布获取框架1表面温度分布、控制模块6区域的平均温度和变频模块7区域的平均温度;
步骤s4,判断是否满足以下三个条件:
条件一:加热效率大于等于目标效率;
条件二:框架1表面不存在达到局部温度阈值的位置点;
条件三:控制模块6区域的平均温度未达到第一高温阈值,并且变频模块7区域的平均温度未达到第二高温阈值;
若上述三个条件均满足,进入步骤s5;
若上述三个条件中至少有一个条件不满足,则调整蒸汽发生器的内部结构,具体包括调整线圈3直径、线圈3匝数、罐体2绕线密度、增加罐体2之间的间距、罐体2位置、控制模块6与变频模块7之间的距离六者中至少一者,返回步骤s2;
步骤s5,完成制造。
在本实施方式中,优选的,控制模块6区域为控制模块6所占区域,变频模块7区域为变频模块6所占区域。
在本实施方式中,建构蒸汽发生器的结构主要包括将框架1内的空间划分为加热区和控制区,在加热区内布设至少一个罐体2、缠绕在罐体2上的线圈3、与罐体2出气口连接的蒸汽管道4、串接于蒸汽管道4上的汽包5,在控制区内布设变频模块7和控制模块6。优选的,如图3和图4所示,加热区占据左侧,控制区占据右侧,加热区的空间大于控制区的空间。优选的,在加热区和控制区之间设置一个隔热板,加热区的热量串入控制区影响控制模块6和变频模块7工作稳定性。
在本实施方式中,结构参数优选但不限于包括线圈3的直径、匝数,罐体2绕线密度,罐体2位置(在框架1内的摆放位置),当罐体2为一个以上时的罐体2间距,以及变频模,7与控制模块6之间的距离。
在本实施方式中,在步骤s2中,首先,需要根据构建的结构和获取的结构参数获取蒸汽发生器的三维结构(即几何模型)。在三维结构中,优选的,可以对各零部件的结构进行简化,以便快速获得三维结构,如罐体2可简化为圆柱体、框架1或框架1的梁可简化为长方体、控制模块6和变频模块7均可简化为长方体。
在本实施方式中,在步骤s2中,其次,需要建立电磁感应加热和传热过程的数学模型,数学模型包括电磁感应的麦克斯韦方程与三维传热导微分方程模型。
在本实施方式中,基于法拉第电磁感应,法拉第电磁感应定律确定:e=-ndφ/dt,上式中e为感应电动势,n为感应线圈3的匝数,φ为磁通量,t为时间,感应电动势的方向与磁通量变化率的方向相反。对于φ=φmsinωt,角频率为ω=2πf,则感应电动势的有效值为:e=4.44fnφm,f为电流频率。将罐体2视为只有一匝的闭合回路,当感应电动势产生时,该回路中产生交变的自成环路的环流涡流i2。感应加热中就是利用涡流产生的热能来加热金属罐体2。
在本实施方式中,焦耳效应可用下式表述:q=i22rt(j),反映了涡流在罐体2金属坯料中所产生热的速率与坯料的电阻(即rt(j))和涡流(即i2)的平方成正比这样一种现象。其电磁感应加热功率为:
在本实施方式中,三维导热微分方程为:
在本实施方式中,包含电场与磁场分布→涡电流分布→热流分布和温度场分布的过程,主要涉及电磁感应发热过程、固-固导热过程、流-固耦合传热过程以及对流传热过程。
在本实施方式中,总输入电功率与有效加热功率及其它热损失之间的关系为:
q总=q有效+q散热+q局感+q芯片;其中,q有效=c蒸汽m蒸汽(t蒸汽-t0)+γ蒸汽;c蒸汽为蒸汽比热,单位kj/kgk;m蒸汽为单位时间内的蒸汽产量,单位kg/h;t蒸汽为出口蒸汽温度,单位k;t0为水箱水温;γ蒸汽表示t蒸汽条件下的蒸汽潜热。
其中,q散热=h壁a罐(tf-t罐壁)+h壁a管路(tf-t管壁)+h壁a汽包(tf–t汽包壁),为罐体2、蒸汽管道4和汽包5的散热计算,tf表示蒸汽发生器内部环境空气温度。a罐、a管路和a汽包分别表示罐体表面有效换热面积、蒸汽管道表面有效换热面积和汽包表面有效换热面积,h壁表示第一换热系数,单位w/m2·℃。t罐壁、t管壁和t汽包壁分别表示罐体表面温度、蒸汽管道表面温度和汽包表面温度。
q局感=h局a局(tf-t局),为线圈3与金属框架1的局部电磁感应发热。t局表示框架1表面的局部高温点的温度,a局表示框架1表面的局部高温点占有面积,h局表示第二换热系数。
q芯片=p芯片,根据电磁加热模块设计计算,确定变频模块7和控制模块6的散热功率,可根据芯片的额定功率确定。
在本实施方式中,求解蒸汽发生器的三维结构下电磁感应加热和传热过程如图2所示,具体地,由电场与磁场分布→涡电流分布→热流分布和温度场分布。可利用有限元方法进行耦合数值求解,为现有技术。也可以借助仿真软件ansys进行电磁耦合仿真与cfd流体传热仿真,获得热流分布和温度场场分布。
在本实施方式中,目标加热效率为预设值,其取值范围可为90%到99.9%,如可为96%;局部温度阈值可预设,其可根据体感设置,如体感认为60℃较高,大于65℃时会存在烫伤风险,因此,局部温度阈值可设置为65℃。第一高温阈值和第二高温阈值均可预设,第一高温阈值可根据控制模块6的允许工作温度范围确定,如控制模块6为单片机、plc、arm等,其允许的最高工作温度为65℃,那么第一高温阈值可为65℃;同样的,第二高温阈值可根据变频模块7(即igbt模块)允许的最高工作温度设置,如可为70℃。
在本实施方式中,优选的,加热效率rheating为:
在本实施方式中,条件一、条件二和条件三是否满足的判断,可全部判断完三个条件后再调整蒸汽发生器结构参数,再返回步骤s2,也可三个条件不用全部判断完,只要判断到一个条件不满足,就可进行蒸汽发生器结构参数调整,调整后就可返回步骤s2。
在一种优选实施方式中,在步骤s4中,调整蒸汽发生器的内部结构的过程包括:
若条件一不满足,则执行减小线圈3直径、增加线圈3匝数、增大罐体2绕线密度、当罐体2为一个以上时增加罐体2之间的间距四者中至少一者;
若条件二不满足,调整罐体2位置以增大框架1上上述位置点与罐体2的距离;即调整罐体2位置后使得框架1表面温度值达到局部温度阈值的位置点与罐体2的距离增大,以减小该位置点的局部感应电动势,进而减少该位置点的温度。
若条件三不满足,增大控制模块6与变频模块7之间的距离,和/或设置一个冷却回路8,用于降低控制模块6区域和/或变频模块7区域的温度。即当条件三不满足时,可以增大控制模块6与变频模块7之间的距离,或者设置一个冷却回路8,或者既增大控制模块6与变频模块7之间的距离又设置一个冷却回路8。
在本实施方式的一种应用场景中,按照如下流程判断三个条件以及调整蒸汽发生器的内部结构,步骤s4具体包括:
步骤s41,判断加热效率是否小于预设的目标效率,若加热效率小于目标效率,则减小线圈直径、增加线圈匝数及罐体绕线密度,当罐体为一个以上时增加罐体之间的间距,进入步骤s42;若加热效率大于等于目标效率,进入步骤s42;
步骤s42,判断框架表面温度分布中是否存在温度值大于等于预设的局部温度阈值的位置点,若存在温度值大于等于预设的局部温度阈值的位置点,调整罐体位置以增大框架上上述位置点与罐体的距离,进入步骤s43;若不存在温度值大于等于预设的局部温度阈值的位置点,进入步骤s43;
步骤s43,判断控制模块区域的平均温度是否大于等于第一高温阈值,变频模块区域的平均温度是否大于等于第二高温阈值,若控制模块区域的平均温度大于等于第一高温阈值,和/或变频模块区域的平均温度大于等于第二高温阈值,增大控制模块与变频模块之间的距离,返回执行步骤s2;若控制模块区域的平均温度小于第一高温阈值,并且变频模块区域的平均温度小于第二高温阈值,进入步骤s5。
在一种优选实施方式中,若条件一不满足时,还包括如下步骤:
根据蒸汽管道4和汽包5表面的加热密度获取散热比,判断该散热比是否小于预设的目标散热比,若该散热比不小于目标散热比,在蒸汽管道4和汽包5的全部或部分外表面裹附一层保温层,若散热比小于目标散热比,不增设保温层;散热比rra为:
在本实施方式中,目标散热比可预设,其取值范围为0到5%。
本发明还公开了一种利用上述制造方法制造的电磁感应蒸汽发生器,在一种优选实施方式中,其内部结构示意图如图3和图4所示,包括框架1,框架1内划分有加热区和控制区;在加热区内设置有至少一个罐体2、缠绕在罐体2上的线圈3、与罐体2出气口连接的蒸汽管道4、串接于蒸汽管道4上的汽包5,蒸汽管道4延伸出框架1;在控制区内设置有控制模块6和为线圈3供电的变频模块7,控制模块6与变频模块7连接通信。
在本实施方式中,罐体2为金属材质,能够进行电磁感应加热。框架1的结构可为镂空的框结构,也可为封闭的壳体结构。框架1上优选的设置有汽包5上设置有进口和出口,蒸汽管道4为分段结构,通过蒸汽管道4将罐体2的出气口与汽包5的进口连接,通过蒸汽管道4从汽包5的出口引导出高温蒸汽。
在本实施方式中,控制模块6可控制变频模块7的输出的交变信号频率和幅度。
在一种优选实施方式中,还包括裹附于蒸汽管道4和/或汽包5的全部或部分外表面的保温层。
在本实施方式中,可在蒸汽管道4的全部或部分外表面上的裹附保温层;也可以在汽包5的全部或部分外表面上的裹附保温层;也可以既在蒸汽管道4的全部或部分外表面上的裹附保温层,又在汽包5的全部或部分外表面上的裹附保温层。
在本实施方式中,保温层可选择泡棉、棉布等材料制成。
在一种优选实施方式中,还包括设置于控制区的冷却回路8;冷却回路8上依次管路连接有进液口81、冷却泵82、途经控制模块6和/或变频模块7的冷却管道、以及出液口83;控制模块6的第一信号输出端与冷却泵82的控制端连接。
在本实施方式中,冷却回路8中的冷却液优选但不限于为水、液化co2等。优选的,该蒸汽发生器配备有冷却液源,如图2所示的设于框架1外的水箱11。进液口81与自来水管或水箱11出口通过管道连接。出液口81可以回收池通过管道连接。
在本实施方式中,控制模块6控制冷却泵82开启或关闭。冷却管道途经控制模块6背面、或者途经变频模块7背面、或者依次或并行途经控制模块6背面和变频模块7背面。冷却管道为冷却回路中用于换热的部分管道,其可为一条,依次途经控制模块6背面和变频模块7背面,结构简单,也可为两条并行的子管道,两个子管道分别途经控制模块6背面和变频模块7背面后再汇合入冷却回路8主管道中,这样能够加快换热速度。
在本实施方式中,优选的,冷却管道在控制模块6背面或变频模块7背面蛇形或回形经过,以进行充分换热。
在一种优选实施方式中,冷却回路5的出液口83与至少一个罐体2的进水口管路连接。
在一种优选实施方式中,冷却回路8还包括回收支路,回收支路一端与出液口83附近的冷却回路8管道连通,回收支路的另一端与至少一个罐体2的的进水口连通,回收支路上设置有电控阀,罐体2内设有液位传感器,控制模块6接收液位传感器输出的罐体2内液位信号控制电控阀开启或关闭。
在本实施方式中,控制模块6检测到液位传感器输出的罐体2内部的水位达到预设的目标水位时,控制电控阀关闭,停止回收冷却水,避免罐体中水溢出,冷却水全部从冷却回路8的出液口83排出;控制模块6检测到液位传感器输出的罐体2内部的水位未达到预设的目标水位时,控制电控阀开启,回收冷却水,使得罐体2中具有充足的水量,部分冷却水从冷却回路8的出液口83排出。
在本实施方式中,优选的,在出液口83还设置有一个由控制模块6控制开启或关闭的电磁阀,当罐体2内的水位没有达到目标水位时,电磁阀关闭,全部冷却水流入罐体2,能够快速补足水量。
在本实施方式中,目标水位可为罐体2总长度的70%到98%。在一种优选实施方式中,变频模块7安装在第一散热板9上,控制模块6安装在第二散热板10上;冷却管道包括分别开设于第一散热板9中和第二散热板10中的第一冷却流道84和第二冷却流道85,第一冷却流道84和第二冷却流道85串接于冷却回路8中。
在本实施方式中,第一散热板9和第二散热板10优选为散热性好的铝制型材。分别在其内部开设有第一冷却流道84和第二冷却流道85。第一冷却流道84和第二冷却流道85可串联后串接于冷却回路8中,或者第一冷却流道84和第二冷却流道85可并联后串接于冷却回路8中。如图1所示,第一冷却流道84和第二冷却流道85可为蛇形或回形。
在一种优选实施方式中,如图4所示,罐体2包括并行放置的第一罐体和第二罐体,第一罐体外缠绕有第一线圈,第二罐体外缠绕有第二线圈;蒸汽管道4包括贯穿汽包5的第一蒸汽管道和第二蒸汽管道,第一蒸汽管道的第一端与第一罐体的出气口连接,第二蒸汽管道的第一端与第二罐体的出气口连接,第一蒸汽管道的第二端与第二蒸汽管道的第二端汇合后向外输出蒸汽。在本实施方式中,第一蒸汽管道和第二蒸汽管道分别与汽包5相贯连接。
在本说明书的描述中,参考术语“一个实施例”、“一些实施例”、“示例”、“具体示例”、或“一些示例”等的描述意指结合该实施例或示例描述的具体特征、结构、材料或者特点包含于本发明的至少一个实施例或示例中。在本说明书中,对上述术语的示意性表述不一定指的是相同的实施例或示例。而且,描述的具体特征、结构、材料或者特点可以在任何的一个或多个实施例或示例中以合适的方式结合。
尽管已经示出和描述了本发明的实施例,本领域的普通技术人员可以理解:在不脱离本发明的原理和宗旨的情况下可以对这些实施例进行多种变化、修改、替换和变型,本发明的范围由权利要求及其等同物限定。
起点商标作为专业知识产权交易平台,可以帮助大家解决很多问题,如果大家想要了解更多知产交易信息请点击 【在线咨询】或添加微信 【19522093243】与客服一对一沟通,为大家解决相关问题。
此文章来源于网络,如有侵权,请联系删除


