一体化过热器的制作方法



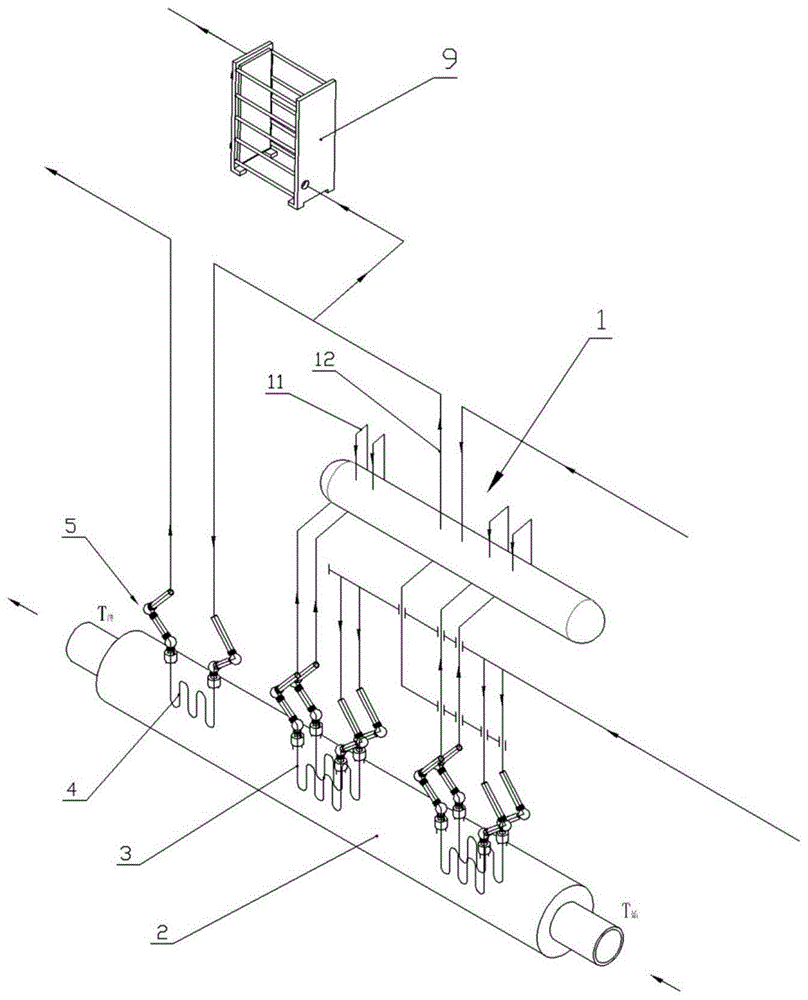
本实用新型属于有色金属冶炼技术领域,特别是涉及一种一体化过热器。
背景技术:
有色金属冶炼技术领域存在着很多的中高温流体,比如:中高温烟气、高温熔渣、中高温金属熔体、高温熔盐等。
目前有色金属冶炼行业对中高温的流体的余热回收研发应用的非常有限,目前广泛应用的是对高温烟气的余热回收,且仅止步于产生饱和蒸汽,送去发电系统产生的电量远远小于过热系统;其他大部分的中高温流体的热量损失于工艺流转过程中,并没有回收措施。
火法冶炼工艺中,除了高温烟气,其他中高温流体的的余热回收仍然是一个空白。高温熔渣的冷却目前采用放水渣和放干渣两种形式,一般排放的熔渣的温度在1000~1300℃,冷却后的温度在25℃左右,并且渣量很大。采用放水渣的方式,冲渣用冷却水用量大且需经过冷却塔冷却,不仅热量没有回收,还增加了辅助设施的投资,增加了运行成本;放干渣的方式,使得熔渣的热量损失于环境中,亦会对环境产生热污染。中高温金属流体的冷却主要存在于三种工艺过程中:1、金属熔体的降温过程。铅锌冶炼过程中,冶金炉的排粗铅温度约900℃,下一步的粗铅除铜工序的操作温度为500℃,目前这部分大约500℃的温降的热量完全损失,没有回收措施;2、真空炉出口的金属蒸汽以及金属熔体的冷却。真空炉出口金属蒸汽温度以及金属熔体的出炉温度一般为:400~1000℃,金属蒸汽采用循环冷却水冷却的方式冷却为液态金属,金属熔体在空气中自然冷却到固态,这两部分的冷却热量均没有任何的回收措施;3、冶炼工艺中金属降温分离过程。比如isp工艺中的铅锌分离,我国在生产企业对这个过程中的化学反应热和冷却放出热均没有进行收集。
高温熔盐体系被广泛应用于制取超导体膜、燃料电池等领域,温度在400℃~800℃范围内,当热载体熔盐出现较多沉淀物时,应更换熔盐,熔盐更换时的降温过程中的余热目前没有进行过回收。
技术实现要素:
本实用新型的目的在于针对现有技术的不足之处,提供一种在冶金过程中既能高效回收过程热能、又能解决环境热污染问题的一体化过热器。
本实用新型提供的这种一体化过热器,它包括集汽器和过热器主体;集汽器上连通有输入管路和输出管路;过热器主体包括外壳、ⅱ级受热片、ι级受热片和旋转升降装置,外壳的两端为开口,ⅱ级受热片和ι级受热片均设置于外壳内通过旋转升降装置与外部连通,ⅱ级受热片的输入端为冷媒入口、输出端与输入管路连通,ι级受热片的输入端与输出管路连通、输出端向外输出。
在一个具体实施方式中,所述旋转升降装置包括球体管、可滑动管和绝缘层;球体管外设有便于相对滑动的涂层,其管壁上设有一对通孔;绝缘层上设一对通孔,绝缘层包覆于球体管外;可滑动管包括依次相连的弹性段和圆弧段,弹性段为波纹管,可滑动管以其圆弧段包覆于球体管外,能够相对球体管转动,弹性段的外端伸至绝缘层外用作输出或输入。
作为替代方案,所述旋转升降装置包括外壳、中心辊轴和波纹管;外壳为金属制球形外壳,其上设有一对开口,其外包覆有绝缘层;中心辊轴设置于外壳的中心,中心辊轴外和外壳内均设有光滑涂层;波纹管伸至中心辊轴与外壳之间,两端分别伸出一对开口外,波纹管能够绕中心辊轴相对转动。
作为替代方案,所述旋转升降装置包括中心轴管、滑动伸缩组件、绝缘弹性外壳;中心轴管为圆柱形,其上设有一对开口,其外表面设有光滑涂层;滑动伸缩组件包括依次相连的直线段、伸缩段和包覆段,包覆段有两段分别焊接于伸缩段内端的两侧,直线段连接于伸缩段的外端,滑动伸缩组件以其包覆段包覆于中心轴管外能够绕中心轴管转动;中心轴管外对应两伸缩管之间区域均设有绝缘弹性外壳,绝缘弹性外壳包括两端的绝缘壳和设置于两绝缘段之间的弹性壳。
作为优选,所述ⅱ级受热片为夹套式受热片、呈蛇形布置,包括内管、外管和防护层;外管的端部设有密封腔,内管伸出密封腔外,密封腔内填充有惰性气体,外管外设高热导率的耐火层;内管与外管之间填充有液态金属耦合剂、并在密封腔内设有伸至液态金属耦合剂表面内的液位传感器;ι级受热片与ⅱ级受热片结构相同,并在各受热片外设有与内管连通的安全阀。
作为替代方案,或者在所述内管与所述外管之间填充石墨类物质。
为了提高换热效果,在所述ⅱ级受热片和/或ι级受热片外设有翅片。
作为优选,所述ⅱ级受热片和所述ι级受热片的顶部均伸至相应球体管内,连接处包覆有绝缘非金属层。
在一个具体实施方式中,所述外壳的一端设有流体进口,另一端设有流体出口,外壳的内表面设有高温无机涂层。
作为优选,所述输入管路和所述输出管路为304h不锈钢制成的无缝钢管,其端部内壁设有螺纹。
本实用新型在使用时,将ⅱ级受热片、ι级受热片均通过旋转升降装置装配于外壳内,使得受热片的工作数量和受热面积均可通过旋转升降装置进行调节,生产过程中亦可以完成受热面零部件的检修和更换,便于保证余热回收过程的安全和稳定。使用时水与冶金过程中出现的高温流体在外壳内进行换热,热交换后ⅱ级受热片内的水形成汽水混合物并汇入集汽器内,再自集汽器进入ι级受热片内再次热交换产出过热饱和汽后输出,在冶金过程中既能高效回收过程热能、又能解决环境热污染问题。
附图说明
图1为本实用新型优选实施例一的布置示意图。(安全阀未画出)
图2为优选实施例一中旋转升降装置与受热片的装配放大示意图。
图3为优选实施例一中受热片的剖视放大示意图。
图4为优选实施例一中旋转升降装置的剖视放大示意图。(工作状态)
图5为优选实施例一中旋转升降装置的剖视放大示意图。(检修状态)
图6为优选实施例二中旋转升降装置的剖视放大示意图。
图7为优选实施例三中旋转升降装置的剖视放大示意图。
图示序号:
1—集汽器,11—输入管路,12—输出管路;
2—外壳;
3—ⅱ级受热片,31—内管,32—外管,33—耐火层;
4—ι级受热片;
5—旋转升降装置,51—球体管、52—可滑动管、53—绝缘层、54—涂层,
6—液位传感器;
7—翅片;
8—安全阀;
9—旁路换热器;
a5—旋转升降装置ⅱ,a51—球形外壳,a52—中心辊轴,a53—波纹管,a54—绝缘层,a55—光滑石墨涂层。
b5—旋转升降装置ⅲ,b51—中心轴管,b52—滑动伸缩组件、b521—直线段、b522—伸缩段、b523—包覆段,b53—绝缘弹性外壳、b531—绝缘壳、b532—弹性壳,b54—光滑涂层。
具体实施方式
如图1所示,本实施例公开的这种一体化过热器为一体式,包括集汽器1、外壳2、ⅱ级受热片3、ι级受热片4和旋转升降装置5。
集汽器1上连通有输入管路11和输出管路12,输入管路和所述输出管路为304h不锈钢制成的无缝钢管,其端部内壁设有螺纹以便连接。
外壳2为由20号钢焊接而成的圆筒型壳体,两端为开口用于高温流体穿过,内壁喷涂氧化铝质高温无机涂层,涂层厚度大于等于10mm。
如图1、图2所示,ⅱ级受热片3和ι级受热片4结构相同,均为夹套式的蛇形排管;如图3所示,ⅱ级受热片3包括内管31和外管32,外管的端部封闭,内管伸出封闭端外,外管外设耐火层33,外管和内管之间的区域内填充导热性、保热性能良好的液态金属耦合剂,可选用多元易熔合金,并在液面以上留有30-50mm的空间充入惰性气体以封闭,并在外管的封闭端设置液位传感器6,液位传感器穿过惰性气体空间,插入液态金属耦合剂液面以下进行在线渗漏监测及远程报警。ⅱ级受热片和ι级受热片的内管、外管的材质为20号锅炉钢,并在外管外表面喷涂金刚砂耐火材料复合层作为耐火层,以承受冶金中高温流体的机械冲刷和化学腐蚀。另外为了提高换热效果,在ⅱ级受热片和ι级受热片外设有翅片7,为了提高安全性能,在需要时实现对各受热片进行排气,在受热片的输出端上设置于内管连通的安全阀8。
如图2、图4所示,旋转升降装置5包括球体管51、可滑动管52和绝缘层53;球体管外设有便于相对滑动的涂层54,其管壁上设有一对通孔;绝缘层上设一对通孔,绝缘层包覆于球体管外;可滑动管包括依次相连的伸缩段和圆弧段,伸缩段为特种不锈钢制波纹管,可滑动管以其圆弧段包覆于球体管外,能够相对球体管转动,伸缩段的外端伸至绝缘层外用作输出或输入。系统正常运行时,如图4所示,汽水混合物或者过热饱和蒸汽通过可滑动管件进入到球体管件中,当ⅰ级受热片和ⅱ级受热片需要更换或者检修时,如图5所示,转动滑动管件以封闭球体管件通孔,即可将受热片从中高温流体中提升出来,提升过程中汽水混合物或者过热蒸汽通道被完全阻隔,完成受热片的安全提升。
一体化过热器自身装配时,根据工况选择适宜数量的ⅱ级受热片和ι级受热片,然后将ⅱ级受热片设置于外壳内、输入端与给水泵连通,输出端通过旋转升降装置与集汽器的输入管路连通,ι级受热片设置于外壳内、一端通过旋转升降装置与集汽器的输出管路连通、另一端通过旋转升降装置输出,在受热片与旋转升降装置装配时,将受热片的顶部均伸至相应基座内与底管连通,并在连接处包覆有绝缘非金属层,使具有绝缘效果,提高安全性和可靠性。旋转升降装置的设置得以实现系统带负荷生产情况下的检修和零部件更换,可以实现对受热片平移和提升,提高了一体化过热器的安全性以及整个系统的运行效率。
如图1所示,本实施例在使用时,将介质在外壳内进行换热,热交换后ⅱ级受热片内的水形成汽水混合物并汇入集汽器内,再自集汽器进入ι级受热片内再次热交换产出过热饱和汽后输出。同时为了确保一体化过热器能够正常运行,在集汽器的输出管路上设置有与ι级受热片并联的旁路换热器9,在ι级受热片出现事故时,为ⅱ级受热片提供蒸汽临时利用旁路;另外,还在各个换热片外均设置有与之内管连通的安全阀以备用。
本实施例中还可以向受热片的内管和外管之间填充石墨类物质替代液态金属耦合剂,可省去液位传感器。
优选实施例二,本实施例与优选实施例一的区别在于,将旋转升降装置采用其它方案,如图6所示,本实施例中的旋转升降装置ⅱa5包括球形外壳a51、中心辊轴a52和波纹管a53;球形外壳为金属制,其上设有一对开口,其外包覆有绝缘层a54;中心辊轴设置于外壳的中心,中心辊轴外和外壳内均设有光滑涂层a55;波纹管伸至中心辊轴与外壳之间,两端分别伸出一对开口外,波纹管能够绕中心辊轴相对转动。
优选实施例三,本实施例与优选实施例一的区别在于,将旋转升降装置采用其它方案,如图7所示,旋转升降装置ⅲb5包括中心轴管b51、滑动伸缩组件b52、绝缘弹性外壳b53;中心轴管为圆柱形,其上设有一对开口,其外表面设有石墨质地的光滑涂层b54;滑动伸缩组件b52包括依次相连的直线段b521、伸缩段b522和包覆段b523,包覆段有两段分别焊接于伸缩段内端的两侧,直线段连接于伸缩段的外端,滑动伸缩组件以其包覆段包覆于中心轴管外能够绕中心轴管转动;中心轴管外对应两伸缩管之间区域均设有绝缘弹性外壳,绝缘弹性外壳包括两端的绝缘壳b531和设置于两绝缘段之间的弹性壳b532。滑动伸缩组件以其包覆段包覆中心轴管开口,使流道与伸缩段连通,而弹性壳为低合金钢材质,在滑动伸缩组件绕中心轴管相对转动的过程中可自由延展和收缩。使用时拉动伸缩管,此时弹性段弹性变形,一对伸缩管相对运动,得以通过绝缘段打开或封闭中心轴管上的开口。
为了验证效果,实用新型人进行了三组测试。
一、将外壳内容积设计为1.25m3,并在其空腔内充满950±50℃的高铅渣,每小时通过高铅渣量为1.31t,通过本系统将高铅液温度降低到500℃。将管型保温外壳内高铅液分为五段,第一段为1050℃到900℃,第二段为900℃到750℃,第三段为750℃到650℃,第四段为650℃到570℃,第五段为570℃到500℃。第一段和第二段分别设置3组夹套式过热片,第三温度和第四温度段分别设置5组夹套式蒸发片,第五温度段设置5组夹套式蒸发片,系统压力为0.70mpa。系统产生过热饱和汽量为28.2t/h,余热回收率为93.6%。
二、将外壳内容积设计为1.25m3,充满700±50℃的高铅渣,每小时通过高铅渣量为1.31t,通过余热回收系统将高铅液温度降低到400℃。将管型保温外壳内高铅液分为四段,第一段为900℃到740℃,第二段为740℃到610℃,第三段为610℃到500℃,第四段为500℃到400℃。第一段设置3组夹套式过热片,第二温度和第三温度段分别设置5组夹套式蒸发片,第四温度段设置5组夹套式蒸发片,系统压力为0.72mpa。系统产生过热饱和汽量为21.9kg/h,余热回收率为93.8%。
三、将外壳内容积设计为1.25m3,充满550±50℃的高铅渣,每小时通过高铅渣量为1.3t,通过余热回收系统将高铅液温度降低到400℃。将管型保温外壳内高铅液分为四段,第一段为600℃到550℃,第二段为550℃到470℃,第三段为470℃到400℃。第一段设置1组夹套式过热片,第二温度和第三温度段分别设置3组夹套式蒸发片,系统压力为0.75mpa。系统产生过热饱和汽量为15.4t/h,余热回收率为92.2%。
起点商标作为专业知识产权交易平台,可以帮助大家解决很多问题,如果大家想要了解更多知产交易信息请点击 【在线咨询】或添加微信 【19522093243】与客服一对一沟通,为大家解决相关问题。
此文章来源于网络,如有侵权,请联系删除


