一种锅炉膨胀监测方法及系统与流程



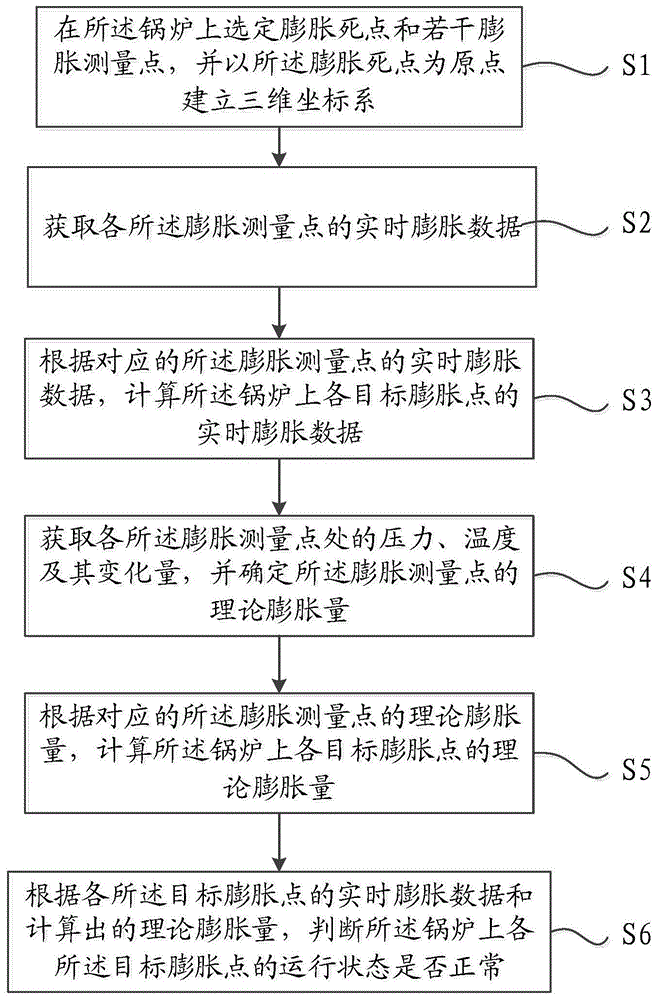
本发明涉及膨胀监测领域,特别是涉及一种锅炉膨胀监测方法及系统。
背景技术:
当前锅炉膨胀监测仍然以记录机械式膨胀装置数据为主,未实现真正意义上的计算机远程监视。究其原因,有几个方面:
一是测量问题未根本解决。当前对锅炉膨胀的多维度测量方案较多,但多数实现起来都存在原理简单,安装实施却不便,成本高,推广存在困难。
二是以往发电厂锅炉负荷较为稳定,因此锅炉膨胀次数及膨胀幅度较小,对锅炉膨胀监测及分析的迫切性不高。但随着电网结构的变化,火力发电厂锅炉负荷从30%至100%频繁变化,甚至需要经常性地进行启动、停止操作,这样锅炉膨胀的频次、幅度就大幅增加。这种情况下,就迫切需要对发电厂锅炉膨胀进行连续监测及分析,掌握锅炉运行状况,分析金属寿命及健康状况,从而为优化锅炉检修频次及重点检查部位提供数据支撑。
三是大型锅炉膨胀测量点数量较多,这就造成数据采集点数量大,所需耗费的电缆及i/o卡件较多,成本无法有效降低。
因此,如何有效提高膨胀监测的精度和效率,是本领域技术人员目前需要解决的技术问题。
技术实现要素:
本发明的目的是提供一种锅炉膨胀监测方法及系统,用于获取并分析各膨胀测量点的膨胀量,为锅炉的运行提供更加精确的指导和寿命分析。
为实现上述目的,本发明提供如下技术方案:
一种锅炉膨胀监测方法,包括以下步骤:
在所述锅炉上选定膨胀死点和若干膨胀测量点,并以所述膨胀死点为原点建立三维坐标系;
获取各所述膨胀测量点的实时膨胀数据;
根据对应的所述膨胀测量点的实时膨胀数据,计算所述锅炉上各目标膨胀点的实时膨胀数据;
获取各所述膨胀测量点处的压力、温度及其变化量,并确定所述膨胀测量点的理论膨胀量;
根据对应的所述膨胀测量点的理论膨胀量,计算所述锅炉上各目标膨胀点的理论膨胀量;
根据各所述目标膨胀点的实时膨胀数据和计算出的理论膨胀量,判断所述锅炉上各所述目标膨胀点的运行状态是否正常。
优选的,所述根据各所述膨胀测量点的实时膨胀数据,计算所述锅炉上各目标膨胀点的实时膨胀数据包括:
确定需要计算的目标膨胀点在膨胀前的坐标;
选取对应的参考膨胀测量点在膨胀前的坐标,以及所述参考膨胀测量点的实时膨胀数据;
根据膨胀前所述目标膨胀点与所述膨胀死点之间的位置关系,膨胀前所述参考膨胀测量点与所述膨胀死点之间的位置关系以及膨胀后所述参考膨胀测量点与所述膨胀死点之间的位置关系,进行等比例计算得到所述目标膨胀点的实时膨胀数据;
所述根据对应的所述膨胀测量点的理论膨胀量,计算所述锅炉上各目标膨胀点的理论膨胀量包括:
确定需要计算的目标膨胀点在膨胀前的坐标;
选取对应的参考膨胀测量点在膨胀前的坐标,以及所述参考膨胀测量点的理论膨胀数据;
根据膨胀前所述目标膨胀点与所述膨胀死点之间的位置关系,膨胀前所述参考膨胀测量点与所述膨胀死点之间的位置关系以及膨胀后所述参考膨胀测量点与所述膨胀死点之间的位置关系,进行等比例计算得到所述目标膨胀点的理论膨胀数据;
所述参考膨胀测量点为所述目标膨胀点相对于所述膨胀死点的膨胀方向的前方最近的膨胀测量点;
所述参考膨胀测量点为所述目标膨胀点相对于所述膨胀死点的膨胀方向的前方最近的膨胀测量点。
优选的,设定所述参考膨胀测量点在膨胀前的坐标为x0,y0,z0;所述目标膨胀点在膨胀前的坐标x01,y01,z01;当所述膨胀测量点监测到的实时膨胀量为δx0、δy0、δz0时,则x01,y01,z01的膨胀量值分别为:
δx01=(x01/x0)*δx0;
δy01=(y01/y0)*δy0;
δz01=(z01/z0)*δz0。
优选的,还包括:
设定测量周期,获取各所述测量周期下各所述膨胀测量点的实时膨胀数据;
根据所述锅炉的原始形状、原始尺寸以及各所述膨胀点的实时膨胀数据,获取所述锅炉膨胀时的动态三维立体图像。
优选的,还包括:
当所述锅炉上各目标膨胀点的实时膨胀数据小于理论膨胀量的预设允许范围时,发出膨胀受阻报警信号。
优选的,还包括:
根据所述锅炉的形状,选定若干目标膨胀点作为同组目标膨胀点;
当所述同组目标膨胀点中的某一目标膨胀点的实时膨胀数据与同组其他任意目标膨胀点的实时膨胀数据相差5%-10%时,则发出膨胀不均报警信号。
优选的,还包括:
根据所述膨胀测量点的温度和压力确定额定膨胀速率;
当所述锅炉上各目标膨胀点的膨胀速率大于额定膨胀速率时,则发出膨胀速率报警信号。
优选的,所述锅炉上各目标膨胀点的膨胀速率包括:
所述锅炉升温时各目标膨胀点向外延展的速率和/或所述锅炉降温时各目标膨胀点收缩的速率。
优选的,还包括:
对锅炉疲劳度进行统计,当某一膨胀测量点所代表区域的锅炉金属疲劳分值(n+1)大于预设疲劳分值时,则需对该区域处的金属管材进行维护;
锅炉金属疲劳分值(n+1)=锅炉金属疲劳分值(n)+锅炉膨胀记数脉冲*系数1+锅炉膨胀速率脉冲*系数2;
其中,锅炉金属疲劳分值(n+1)为最新锅炉金属疲劳分值,锅炉金属疲劳分值(n)为上一次锅炉金属疲劳分值;锅炉膨胀记数脉冲为1或0,当该膨胀测量点的膨胀量每大于额定膨胀量或收缩量每小于预设收缩量时,进行计数,锅炉膨胀计数脉冲发一次脉冲,由0变1,随后恢复;锅炉膨胀速率脉冲为1或0,当该膨胀测量点的膨胀速率每超过一次预设膨胀速率,锅炉膨胀速率脉冲由0变1,然后恢复;系数1和系数2均为经验值。
一种锅炉膨胀监测系统,包括膨胀监测装置、控制器、用于显示各所述膨胀测量点的实时膨胀数据的膨胀监测仪表以及用于执行图像显示或执行报警的服务器,所述控制器用于执行如上所述的锅炉膨胀监测方法。
本发明所提供的锅炉膨胀监测方法,包括以下步骤:在所述锅炉上选定膨胀死点和若干膨胀测量点,并以所述膨胀死点为原点建立三维坐标系;获取各所述膨胀测量点的实时膨胀数据;根据对应的所述膨胀测量点的实时膨胀数据,计算所述锅炉上各目标膨胀点的实时膨胀数据;获取各所述膨胀测量点处的压力、温度及其变化量,并确定所述膨胀测量点的理论膨胀量;根据对应的所述膨胀测量点的理论膨胀量,计算所述锅炉上各目标膨胀点的理论膨胀量;根据各所述目标膨胀点的实时膨胀数据和计算出的理论膨胀量,判断所述锅炉上各所述目标膨胀点的运行状态是否正常。本发明所提供的锅炉膨胀监测方法,通过坐标系的建立,能够在收集所述锅炉各膨胀测量点的实时膨胀数据后,计算出各目标膨胀点的实时膨胀数据,然后通过将各目标膨胀点的实时膨胀数据与理论膨胀值的比较,分析锅炉运行状态是否正常,该方法不仅可以对膨胀测量点的膨胀情况进行检测,还可以对锅炉任意位置的膨胀情况进行分析,从而实现对锅炉系统运行的指导及金属材料寿命的分析,更加全面和精确。
本发明所提供的锅炉膨胀监测系统,包括控制器、用于显示各所述膨胀测量点的实时膨胀数据的膨胀监测仪表以及用于执行图像显示或执行报警的服务器,所述控制器用于执行上述锅炉膨胀监测方法的控制器。由于锅炉膨胀监测方法具有上述技术效果,因此,设有该锅炉膨胀监测系统也应当具有相应的技术效果。
附图说明
为了更清楚地说明本发明实施例或现有技术中的技术方案,下面将对实施例或现有技术描述中所需要使用的附图作简单地介绍,显而易见地,下面描述中的附图仅仅是本发明的一些实施例,对于本领域普通技术人员来讲,在不付出创造性劳动的前提下,还可以根据这些附图获得其他的附图。
图1为本发明所提供的锅炉膨胀监测方法的流程图;
图2为本发明所提供的锅炉膨胀监测方法中坐标系建立示意图;
图3为本发明所提供的锅炉膨胀监测系统的示意图;
图4为本发明所提供的锅炉膨胀监测系统中膨胀监测装置的结构示意图;
其中:检测组件-100、主体框架-101、探头支架-102、框架固定杆-103、第一连接件-104、第二连接件-105;变动组件-200、位移变动块-201、变动块固定杆-202;服务器-400、控制器-500。
具体实施方式
本发明的核心是提供一种锅炉膨胀监测方法及系统,用于获取并分析各膨胀测量点的膨胀量,为锅炉的运行提供更加精确的指导和寿命分析。
为了使本技术领域的人员更好地理解本发明方案,下面结合附图和具体实施方式对本发明作进一步的详细说明。
请参考图1至图4,图1为本发明所提供的锅炉膨胀监测方法的流程图;图2为本发明所提供的锅炉膨胀监测方法中坐标系建立示意图;图3为本发明所提供的锅炉膨胀监测系统的示意图;图4为本发明所提供的锅炉膨胀监测系统中膨胀监测装置的结构示意图。
在该实施方式中,锅炉膨胀监测方法包括以下步骤:
步骤s1:在锅炉上选定膨胀死点和若干膨胀测量点,并以膨胀死点为原点建立三维坐标系,如图2所示,膨胀死点即为a点;具体的,每个膨胀测量点上均安装有测量装置;
步骤s2:通过测量装置,获取各膨胀测量点的实时膨胀数据;
步骤s3:根据对应的膨胀测量点的实时膨胀数据,计算锅炉上各目标膨胀点的实时膨胀数据;其中,目标膨胀点可以为锅炉上的任意一点;
步骤s4:获取各膨胀测量点处的压力、温度及其变化量,并确定膨胀测量点的理论膨胀量;
步骤s5:根据对应的膨胀测量点的理论膨胀量,计算锅炉上各目标膨胀点的理论膨胀量;对于目标膨胀点的理论膨胀值的计算方法,可以与实时膨胀数据的计算方向相同。
步骤s6:根据各目标膨胀点的实时膨胀数据和计算出的理论膨胀量,判断锅炉上各目标膨胀点的运行状态是否正常;具体的,上述对于膨胀数据的比较,优选包括x、y、z三个坐标轴方向上的向量比较,加上三个向量求和得出的向量比较,当任意一者出现异常时,均应当发出报警信号。
本发明所提供的锅炉膨胀监测方法,通过坐标系的建立,能够在收集锅炉各膨胀测量点的实时膨胀数据后,计算出各目标膨胀点的实时膨胀数据,然后通过将各目标膨胀点的实时膨胀数据与理论膨胀值的比较,分析锅炉运行状态是否正常,该方法不仅可以对膨胀测量点的膨胀情况进行检测,还可以对锅炉任意位置的膨胀情况进行分析,从而实现对锅炉系统运行的指导及金属材料寿命的分析,更加全面和精确。
在上述各实施方式的基础上,根据各膨胀测量点的实时膨胀数据,计算锅炉上各目标膨胀点的实时膨胀数据包括:
确定需要计算的目标膨胀点在膨胀前的坐标;
选取对应的参考膨胀测量点在膨胀前的坐标,以及参考膨胀测量点的实时膨胀数据;
根据膨胀前目标膨胀点与膨胀死点之间的位置关系,膨胀前参考膨胀测量点与膨胀死点之间的位置关系以及膨胀后参考膨胀测量点与膨胀死点之间的位置关系,进行等比例计算得到目标膨胀点的实时膨胀数据;
参考膨胀测量点为目标膨胀点相对于膨胀死点的膨胀方向的前方最近的膨胀测量点。
具体的,设定参考膨胀测量点在膨胀前的坐标为x0,y0,z0;目标膨胀点在膨胀前的坐标x01,y01,z01;当膨胀测量点监测到的实时膨胀量为δx0、δy0、δz0时(δx0、δy0、δz0可以为正数,也可以为负数),则x01,y01,z01的膨胀量值分别为:
δx01=(x01/x0)*δx0;
δy01=(y01/y0)*δy0;
δz01=(z01/z0)*δz0。
同样的,根据对应的膨胀测量点的理论膨胀量,计算锅炉上各目标膨胀点的理论膨胀量包括:
确定需要计算的目标膨胀点在膨胀前的坐标;
选取对应的参考膨胀测量点在膨胀前的坐标,以及参考膨胀测量点的理论膨胀数据;
根据膨胀前目标膨胀点与膨胀死点之间的位置关系,膨胀前参考膨胀测量点与膨胀死点之间的位置关系以及膨胀后参考膨胀测量点与膨胀死点之间的位置关系,进行等比例计算得到目标膨胀点的理论膨胀数据;
参考膨胀测量点为目标膨胀点相对于膨胀死点的膨胀方向的前方最近的膨胀测量点;
参考膨胀测量点为目标膨胀点相对于膨胀死点的膨胀方向的前方最近的膨胀测量点。具体的计算方式,可以参考上述实时膨胀数据的计算方法。
在上述各实施方式的基础上,还包括:
设定测量周期,获取各测量周期下各膨胀测量点的实时膨胀数据;
根据锅炉的原始形状、原始尺寸以及各膨胀点的实时膨胀数据,获取锅炉膨胀时的动态三维立体图像。
本实施例所给出的方法中,锅炉画面以三维立体画面显示,通过鼠标或者通过键盘可翻转查看任意锅炉位置膨胀量。其中,锅炉三维立体画面可依据本锅炉的设计图纸,按比例缩小得到。
具体的,由于大型发电机组锅炉的高度达到100米左右,结构十分复杂,在进行锅炉膨胀测点设置时,也只有40个左右,不能覆盖锅炉所有部位。为了能够得到所有位置的膨胀数值,而采用本实施例所给出的方法,具体的:首先,将锅炉设计时的膨胀死点,优选在锅炉顶部;由于大型发电锅炉都是悬吊在空中,膨胀死点就是锅炉发生膨胀时位置不变的点,锅炉其它部位以膨胀死点为中心向外膨胀,因而将锅炉顶部设定为锅炉膨胀计算零点,以此点为中心,将锅炉膨胀划分为三个方向,向下方向设定为z方向,锅炉只能向下膨胀,不能向上膨胀,向前方向,可将锅炉前墙方向设定为x方向正向,反方向为负向,向左方向,可将锅炉左墙方向设定为y方向正向,反方向为负。这些方向选取时,与安装于就地的膨胀测量装置的测量方向保持一致,这样就得到了数值计算的坐标。也就是说,锅炉被分成了四个向量区间,如图2所示。
进一步,各目标膨胀点的膨胀量的计算从最接近锅炉膨胀死点的位置开始向远离锅炉膨胀死点的方向逐个计算。计算时选择的目标膨胀测量点为该点膨胀方向上,也就是说,沿该目标膨胀点膨胀方向向前,离该点最接近的膨胀量测量点的数据。该目标膨胀测量点的x、y、z方向的膨胀量,通过该目标膨胀测量点离膨胀死点x、y、z方向的距离进行等比例计算。由于锅炉膨胀测点是按照锅炉结构分段布置的,且每个膨胀测量点测得的锅炉膨胀量是一个综合了两个膨胀测量点之间所有金属特性后的综合膨胀量,因此采用等比例计算可以基本代表每个点的膨胀量。
更进一步,当锅炉运行时,锅炉各部位发生膨胀,通过上述方式可计算出锅炉各部位的膨胀量,即可以计算出任一目标膨胀点的膨胀量。此时,可通过计算得到各点膨胀量,修正原始锅炉三维立体画面,当鼠标停止在画面某个部位时,该处的膨胀量可自动显示。同时,按照预设周期,根据各膨胀测量点的膨胀数据,对锅炉画面各目标膨胀点的膨胀量参数进行一次计算,并作为历史数据进行存储。这些历史数据不仅可以作为锅炉膨胀过程动态显示的数据源使用,也可作为锅炉膨胀应力计算的数据源,还可以作为故障分析的数据源。
当进行膨胀过程动态显示时,软件调取选定时间段的锅炉膨胀数据,按设定周期逐个调取每个时间点各目标膨胀点的膨胀数据,并修正锅炉各点位置参数进行显示,从而随时间的变化形成动态画面,反映锅炉膨胀过程。
在上述各实施方式的基础上,还包括:
当锅炉上各目标膨胀点的实时膨胀数据小于理论膨胀量的预设允许范围时,发出膨胀受阻报警信号。
具体的,不同温度下锅炉上各点的理论膨胀量计算,可根据公式δl=l*α*δt(l为初始长度,α为线性膨胀系数,δt温度变化量,δl为长度变化量,也就是线性膨胀量),计算得到不同温度下锅炉每个点的理论膨胀量。将δl分解到x、y、z三个方向上,得到:
δlx0=x0*α*δt
δly0=y0*α*δt
δlz0=z0*α*δt
x0,y0,z0为测量点未膨胀前的坐标,δt为锅炉当前温度与膨胀前选定的参考温度之差。当然,根据锅炉结构及不同部位材质,计算锅炉不同位置膨胀量时可以采用不同的线性膨胀系数。具体的,理论膨胀量计算方法可以参考现有技术。
在上述各实施方式的基础上,还包括:
根据锅炉的形状,选定若干目标膨胀点作为同组目标膨胀点,其中,同组目标膨胀点可以为某一个参数特定下的若干点,例如,z坐标相同的各点作为同组目标膨胀点;
当同组目标膨胀点中的某一目标膨胀点的实时膨胀数据与同组其他任意目标膨胀点的实时膨胀数据相差5%-10%时,则发出膨胀不均报警信号。
在上述各实施方式的基础上,还包括:
根据膨胀测量点的温度和压力确定额定膨胀速率;
当锅炉上各目标膨胀点的膨胀速率大于额定膨胀速率时,则发出膨胀速率报警信号。
具体的,锅炉膨胀速率是指锅炉单位时间内的膨胀量。本实施例所提供的方法中,通过以下方式实现对膨胀速率的测量:
假设膨胀测量点在未膨胀前的坐标为x,y,z,在初始时刻,即t0时刻的膨胀量为δx(t0),δy(t0),δz(t0),单位时间后,即t1时刻的膨胀量为δx(t1),δy(t1),δz(t1),则其单位时间的锅炉膨胀速率vl=sqrt{[δx(t1)-δx(t0)]2+[δy(t1)-δy(t0)]2+[δz(t1)-δz(t0)]2}。具体的,额定膨胀速率计算方法可以参考现有技术。
在上述各实施方式的基础上,锅炉上各目标膨胀点的膨胀速率包括:
锅炉升温时各目标膨胀点向外延展的速率和/或锅炉降温时各目标膨胀点收缩的速率。
进一步,锅炉膨胀量报警分为两种情况:
第一种是膨胀受阻报警。具体的,当锅炉内部介质温度变化后,锅炉应根据介质温度进行膨胀。若在锅炉内部介质温度发生变化后,锅炉膨胀测量点监测到锅炉未发生膨胀或膨胀量较理论膨胀量或设计膨胀量,或经验膨胀量偏小,达到预设报警值,优选以理论膨胀量的5%-15%选择偏差报警量,则发出膨胀受阻报警;
第二种是锅炉膨胀不均报警。具体的,当同组目标膨胀点中,监测到某一目标膨胀点的膨胀量出现明显偏差,优选为与同组其他任意目标膨胀点的实时膨胀数据相差5%-10%时,则发出锅炉膨胀不均报警。锅炉膨胀不均反映了锅炉各方向介质温度、介质流速不均衡。锅炉设计时,对称分布的管材膨胀要基本保持对称,其内部流动的流体也基本保持平衡,不然会造成锅炉整体失去平衡。
另外,关于锅炉膨胀速率报警,具体的,根据前述锅炉膨胀速率计算方式,当计算得到锅炉膨胀测量点的膨胀速率达到预设报警值,该预设报警值是与锅炉金属材质、锅炉大小等相关的一个数值,需要具体锅炉具体计算,可以设定为额定膨胀速率的102%-105%时,则发出锅炉膨胀速率报警。膨胀速率分为两种,一种是锅炉升温时向外延展速率,一种是锅炉温度降低时的收缩速率。锅炉膨胀速率反映了锅炉膨胀过程中产生的应力大小。
在上述各实施方式的基础上,还包括:
对锅炉疲劳度进行统计,当某一膨胀测量点所代表区域的锅炉金属疲劳分值(n+1)大于预设疲劳分值时,则需对该区域处的金属管材进行维护;
锅炉金属疲劳分值(n+1)=锅炉金属疲劳分值(n)+锅炉膨胀记数脉冲*系数1+锅炉膨胀速率脉冲*系数2;
其中,锅炉金属疲劳分值(n+1)为最新锅炉金属疲劳分值,锅炉金属疲劳分值(n)为上一次锅炉金属疲劳分值;锅炉膨胀记数脉冲为1或0,当该膨胀测量点的膨胀量每大于额定膨胀量或收缩量每小于预设收缩量时,进行计数,锅炉膨胀计数脉冲发一次脉冲,由0变1,随后恢复;锅炉膨胀速率脉冲为1或0,当该膨胀测量点的膨胀速率每超过一次预设膨胀速率,锅炉膨胀速率脉冲由0变1,然后恢复;系数1和系数2均为经验值。
进一步,系数1为一个经验值,它代表了锅炉膨胀变化引起的锅炉金属疲劳量,大幅的金属材料收缩,必然会引金属疲劳度的增加。此处通过分值来代表,具体分值根据使用者习惯确定,只要在本计分规则中,各参数计分原则保持一致,相同的分值代表的金属疲劳增加量相当即可;系数2是一个与锅炉最大膨胀速率有关的函数,锅炉最大膨胀速率越高,系数2越大,快速的金属膨胀、收缩,必然会引金属疲劳度的增加,且速率越高疲劳度增加越多。此处通过分值来代表,具体分值根据使用者习惯确定,只要在本计分规则中,与其它参数计分原则保持一致,相同的分值代表的金属疲劳增加量相当即可。系数2与膨胀速率之间的函数关系,与锅炉金属材料、锅炉尺寸等特性有关,具体锅炉具体确定。
具体的,在锅炉运行中,该方法对锅炉升温膨胀及降温收缩次数进行统计。统计规则是当锅炉升温过程中膨胀量达到一个预设量值时记录升温膨胀一次,锅炉降温过程中收缩量达到一个预设量值时记录降温收缩一次。该预设量值是与锅炉金属材质、锅炉大小、锅炉运行参数相关的一个量值,根据锅炉特性具体计算。可以设定为锅炉最大膨胀量的10%-30%。在统计锅炉膨胀、收缩次数的同时,该方法对锅炉膨胀速率超过预设速率,可以设定为额定膨胀速率的102%-105%的次数进行统计,并同时记录本次最大膨胀速率。通过锅炉膨胀次数和锅炉膨胀速率超预警值的次数,该方法对锅炉金属疲劳程度进行综合分析,给出以分值大小代表的金属疲劳程度。
进一步,锅炉金属疲劳分值以锅炉不同膨胀测量点监测到的膨胀量分别计算,由于在设计锅炉膨胀测量点时,每一个膨胀测量点代表了一个区域的金属膨胀情况,因此通过该膨胀测量点可以代表该区域金属疲劳的情况。当然局部的信号可以综合起来分析整个锅炉的情况。
除上述锅炉膨胀监测方法外,本发明还提供了一种锅炉膨胀监测系统。
该锅炉膨胀监测系统包括膨胀监测装置、控制器500、用于显示各膨胀测量点的实时膨胀数据的膨胀监测仪表以及用于执行图像显示或执行报警的服务器400,其中,膨胀监测装置的个数应当与选取的膨胀测量点的数量一致,控制器500用于执行如上述的锅炉膨胀监测方法。其中,膨胀监测仪表位于对应的监测装置的附件,可实时显示对应膨胀测量点的膨胀数据。
本实施例所提供的锅炉膨胀监测系统,其膨胀监测仪表安装于锅炉膨胀测量点附近,一块膨胀监测仪表与一组膨胀监测装置为一个单元,膨胀监测仪表用于采集对应单元的膨胀数据,在实现就地显示功能的同时,通过现场总线将信号传输给膨胀监测系统的服务器400,膨胀监测系统服务器400与dcs控制系统或plc控制系统通过现场总线或rs485协议进行通信。
进一步,锅炉膨胀监测系统从外部获取三个方面的实时数据:
1、现场膨胀监测仪表监测到的各膨胀点的膨胀数据;
2、从dcs系统或plc系统采集锅炉主要监测点的温度和压力,包括主、再热蒸汽温度和压力、锅炉壁温、汽包温度和压力、联箱温度和压力等,包括但不限于以上膨胀测量点。当条件允许情况下,锅炉膨胀监测系统也可自行检测以上信号。
3、从dcs系统或plc系统采集锅炉负荷,如主蒸汽流量,各主要管道负荷,如蒸汽或水流量,机组负荷等数据,这些数据主要用来进行对比分析。通过同时调阅这些数据及变化趋势,并结合锅炉膨胀情况,进行锅炉膨胀影响因素的综合分析。当条件允许情况下,锅炉膨胀监测系统也可自行检测以上信号。
以上监测、计算及从dcs系统采集到的温度、压力、流量等数据都作为历史数据存储到历史数据库保存,可与其它数据一起被调阅。通过从锅炉运行监控系统或dcs系统采集锅炉各部位运行温度,结合锅炉设计单位的设计资料,并根据锅炉系统结构计算系统各关键部位的热应力和金属疲劳,从而实现对锅炉系统运行的指导及金属材料寿命的分析。
进一步,如图4所示,本实施例速所提供的膨胀检测系统中的膨胀监测装置,包括检测组件100和变动组件200。其中,变动组件200安装在被检测物上,被检测物上设置若干膨胀测量点,每个膨胀测量点上均安装变动组件200,当被检测物的膨胀测量点发生膨胀时,变动组件200的位置会随之发生变化,检测组件100则通过获取变动组件200的位移量,来获取被检测物的膨胀情况。
具体的,检测组件100包括主体框架101、探头支架102和位移传感器。其中,主体框架101用于安装探头支架102,探头支架102用于安装位移传感器,主体框架101的位移应当固定,例如,主体框架101可以直接焊接到锅炉钢架上,也可作为现有机械式锅炉膨胀监视器固定部分的延伸构件,并与之连接;位移传感器的个数为至少三个,分别获取变动组件200在x、y、z方向上的位移量,使得该检测组件100成为多维度位移检测组件,提高检测精度。进一步,变动组件200可以直接焊接到锅炉膨胀构件上,也可作为原机械式锅炉膨胀监视器活动指针部分的延伸构件,并与之连接。
具体的,被检测物可以为锅炉,或者与锅炉相关的蒸汽管道、给水管道及相关联箱等附属设备。
进一步,主体框架101至少包括两两垂直的三块板体,每个板体上至少铰接有一个探头支架102,探头支架102的一端位置可调的设置在板体上,位移传感器安装在探头支架102的另一端,探头支架102在调整至最佳位置后,应当与主体框架101进行固定。
在上述各实施方式的基础上,板体上开设有弧形槽,探头支架102上设有条形槽,条形槽的长度大于弧形槽的半径;探头支架102可沿弧形槽摆动,且弧形槽与条形槽的相交处可沿条形槽的延伸方向移动。如此设置,可以实现探头支架102的角度调整以及与主体框架101相对位移的调整,进而实现位移传感器位置的调整,使得位移传感器处于最佳检测位置。进一步,板体上位于弧形槽的圆心处设有圆心孔,圆心孔与探头支架102的条形槽的相交处可转动连接,方便探头支架102的摆动,以实现角度调整。优选的,条形槽与圆心孔之间通过第一连接件104固定,条形槽与弧形槽的相交处通过第二连接件105固定。优选的,第一连接件104和第二连接件105均为螺钉和螺母的配合件。
在上述各实施方式的基础上,板体为直角三角形板体,各直角三角形板的直角边依次连接;主体框架101的板体交汇处设有三角形平面,三角形平面上设有框架固定杆103。或者,框架固定杆103安装在两个直角三角形板的连接处,框架固定杆103的延伸方向与连接边平行。当然,框架固定杆103也可以安装在其他位置,在该实施方式中,主体框架101的板体交汇处则无需设置三角形平面。
具体的,主体框架101作为多维度位移传感器固定支架,包括三块相互垂直的直角金属板组成主体框架101,三块金属板刚性焊接,即将三个直角三角形焊接在一起。每块金属板上设计一道弧形槽,在弧形槽的圆心位置开一个圆心孔,分别安装一块探头支架102。探头支架102用于将位移传感器安装于其上,具体的,位移传感器可以通过螺丝固定于其上,也可以以其它方式固定于其上,根据位移传感器的结构确定,但位移传感器应是垂直于位移变动块201相应的表面。在探头支架102的固定端设计有矩形槽,主体框架101的三块金属板的交汇处设计为如图2-3所示的三角形平面,并在其上焊接金属杆,即框架固定杆103,用于将主体框架101固定在目标构件上。探头支架102除可以以中心孔为中心旋转外,还可调整前后位置。当探头支架102的位置确定好后,可以通过第一连接件104和第一连接件104将探头支架102与主体框架101固定;具体方法是:将一个螺丝穿入主体框架101的圆心孔与探头支架102的矩形槽交叉处,将另一个螺丝穿入探头支架102的矩形槽与主体框架101弧形槽交叉点处,并分别使用连个螺母上紧两个螺丝。在需要调整探头支架102的位置时,松开两个螺母即可。
在上述各实施方式的基础上,变动组件200包括位移变动块201和变动块固定杆202,变动块固定杆202安装在被检测物上;位移变动块201呈长方体型,或者由三块长方形板两两垂直焊接而成,检测组件100位于位移变动块201的边角处,位移变动块201的边角处的三个表面对应有至少一个位移传感器。优选的,多维度的位移变动块201为长方体或正方体空心金属块,当然,也可以其他形式能够形成三个相互垂直的表面的结构;位移变动块201的一个平面中心处焊接金属杆,用于将位移变动块201固定在目标构件上,当位移变动块201由三块长方形板两两垂直焊接而成时,可以在其中的一个连接处焊接金属杆。上述设置,通过长方体型的位移变动块201的设置,仅需将检测组件100设置在位移变动块201的边角处,便可以准确高效的获取位移变动块201在x、y、z方向上的位移量,便于安装检测组件100。
在上述各实施方式的基础上,位移传感器为激光位移传感器或超声波位移传感器等非接触式传感器,当然,位移传感器也可以为回弹式直线位移传感器,回弹式直线位移传感器的端部设有滚柱滚珠,滚柱滚珠抵接于变动组件200上。
具体的,位移传感器安装于主体框架101的探头支架102上,位移传感器可以为回弹式lvdt。本实施例所提供的回弹式lvdt,其固定端固定探头支架102上,位置固定不变,回弹式拉杆紧靠位移变动块201的一面,且保持垂直,由于在锅炉膨胀过程中,膨胀变动块一般安装于锅炉四角,该处的膨胀不存在旋转位移,因此其始终与位移测量装置的探头支架102保持垂直。当锅炉膨胀不均时,膨胀块会发生旋转位移量,但该位移量非常小,探头支架102预期仍然可近似为垂直状态,因此对测量结果影响很小,可忽略。为了保证拉杆与位移变动块201的接触面不产生硬性破坏性摩擦,在拉杆头部增加一个滚珠,满足位移变动块201存在横向移动的要求,将探杆头部设计为滚珠形式,避免强烈地横向摩擦造成拉杆变形。此时位移变动块201虽然发生了横向位移,但拉杆始终与其平面相垂直,从而消除水平位置变化时硬性摩擦产生的设备磨损及拉杆变形;上述设置,不仅安装简便,结构简单,且能始终保持lvdt与位移变动块201的表面垂直,确保测量精度。
本实施例所提供的多维度膨胀监测装置,安装简便,可以简便地进行信号调试,同时信号传输实现了多样性,便于进行大量膨胀测点监视信号的集成;并且,利用就地多维度膨胀监测仪表及现场总线技术,大幅降低了电缆数量,并同时减少了施工成本,从而使锅炉膨胀监测系统的建设成本得到大幅降低,为该项技术的实际应用创造了条件。
以上对本发明所提供的锅炉膨胀监测方法及系统进行了详细介绍。本文中应用了具体个例对本发明的原理及实施方式进行了阐述,以上实施例的说明只是用于帮助理解本发明的方法及其核心思想。应当指出,对于本技术领域的普通技术人员来说,在不脱离本发明原理的前提下,还可以对本发明进行若干改进和修饰,这些改进和修饰也落入本发明权利要求的保护范围内。
起点商标作为专业知识产权交易平台,可以帮助大家解决很多问题,如果大家想要了解更多知产交易信息请点击 【在线咨询】或添加微信 【19522093243】与客服一对一沟通,为大家解决相关问题。
此文章来源于网络,如有侵权,请联系删除


