利用煤气化装置的合成气发生蒸汽的方法和系统与流程



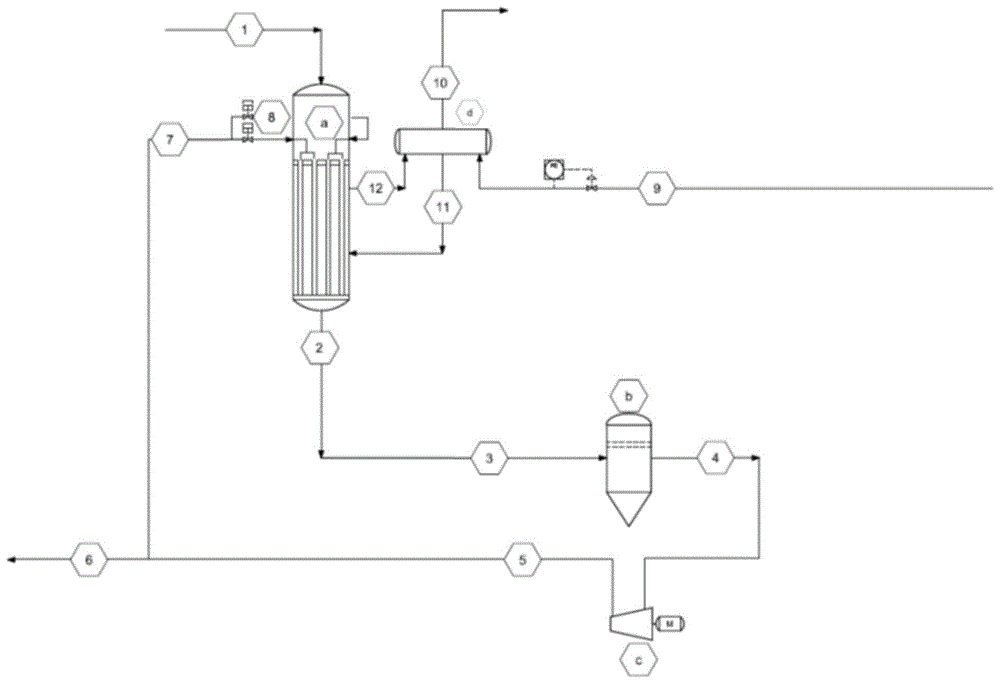
本公开涉及煤气化技术领域,具体地,涉及一种利用煤气化装置的合成气发生蒸汽的方法和系统。
背景技术:
煤气化装置有废锅流程,利用粗合成气来发生超高压蒸汽,由于粗合成气中的飞灰会沉积在锅炉管内,长时间的积灰会导致锅炉压差过高,从而引起气化炉停工。所以大部分废锅流程的煤气化装置都不能长周期运行。由于废锅入口粗合成气温度一般都在800度的高温,所以很少利用机械除灰的方法。因为在高温环境下,转动部件的密封很难,一但密封做不好就会引起高温合成气泄露到大气中引起安全事故。
技术实现要素:
本公开的目的是提供一种利用煤气化装置的合成气发生蒸汽的方法和系统,该装置及方法能够对废锅入口换热管进行吹扫,防止飞灰沉积在废锅管内。
为了实现上述目的,本公开第一方面提供一种利用煤气化装置的合成气发生蒸汽的方法,该方法包括如下步骤:
使粗合成气进入废热锅炉的换热管内作为热介质与所述废热锅炉的壳程介质换热,得到换热后的合成气和换热后的壳程介质;
使所述换热后的合成气经过滤、升压后得到升压合成气;
使至少部分所述升压合成气返回所述废热锅炉的换热管入口,对所述换热管进行吹扫除尘;
使所述换热后的壳程介质进入气液分离装置进行气液分离,得到饱和蒸汽和冷凝液;使所述冷凝液作为所述壳程介质返回所述废热锅炉。
可选地,该方法包括:使补充介质进入所述气液分离装置与所述换热后的壳程介质混合以补充循环水量,所述补充介质为锅炉给水。
可选地,所述废热锅炉内设有气体分布器,所述气体分布器设有气体喷孔,所述气体喷孔朝向所述换热管的入口,且所述气体喷孔的个数和位置与所述换热管相匹配;所述升压合成气经所述气体喷孔喷入所述换热管。
可选地,所述升压合成气与所述换热后的合成气的压力比为(2~2.5):1。
可选地,该方法包括:使所述升压合成气间歇地喷入所述换热管的入口;每次喷射的持续时间为10~20s,相邻两次所述喷射的间隔时间为10~20min。
本公开第二方面提供一种利用煤气化合成气发生蒸汽的系统,该系统包括合成气原料入口、废热锅炉、气液分离装置、过滤器、气体增压装置、蒸汽出口和净化合成气出口;所述废热锅炉包括壳体、合成气入口、合成气出口和设置于所述壳体内的换热管,所述换热管的入口和出口分别与所述合成气入口和所述合成气出口连通,所述合成气出口依次与所述过滤器及所述气体增压装置连通,所述气体增压装置的出口通过气体循环管路与所述换热管的入口连通;
所述废热锅炉的壳程出口与所述气液分离装置的气液混合物入口连通,所述气液分离装置的气体出口与所述蒸汽出口连通,所述气液分离装置的液体出口与所述废热锅炉的壳程入口连通。
可选地,所述气液分离装置为汽包,所述系统还包括与所述汽包连通的补充介质入口。
可选地,所述气体循环管路的出口延伸至所述废热锅炉内,且所述出口处连接有气体分布器;所述气体分布器设有朝向所述换热管的入口的气体喷孔;所述气体喷孔的个数和位置与所述换热管相匹配。
可选地,所述废热锅炉内设有多个所述气体分布器,多个所述气体分布器分别设置于所述换热管的上方;所述气体分布器包括设置于同一平面内的主管和多个支管,多个所述支管分别与所述主管连通,所述主管与所述气体循环管路的出口连通;所述支管的底端设有多个所述气体喷孔。
可选地,所述气体循环管路上设有开关阀,以间隔开启所述气体循环管路。
通过上述技术方案,本公开的方法和系统通过将过滤升压后清洁的升压合成气返回废热锅炉,利用升压合成气与废热锅炉内的高压差形成的高速气流对废锅入口换热管进行反吹冲刷,防止飞灰沉积在废锅管内。本公开的方法和系统可以减少废锅换热管内的飞灰沉积,延长废锅的操作周期,并延长气化炉的运行时间,从而节省煤气化装置的操作和设备费用。
本公开的其他特征和优点将在随后的具体实施方式部分予以详细说明。
附图说明
附图是用来提供对本公开的进一步理解,并且构成说明书的一部分,与下面的具体实施方式一起用于解释本公开,但并不构成对本公开的限制。在附图中:
图1本公开的一种具体实施方式的利用煤气化装置的合成气发生蒸汽的方法的工艺流程图;
图2是本公开的一种具体实施方式的利用煤气化装置的合成气发生蒸汽的系统的换热管板截面示意图;
图3是本公开的一种具体实施方式的利用煤气化装置的合成气发生蒸汽的系统的气体分布器的结构示意图。
附图标记说明
1.粗合成气2.换热后的合成气3.换热后的合成气
4.清洁的合成气5.升压合成气6.外送合成气
7.反吹合成气8.反吹合成气9.补充介质
10.饱和蒸汽11.冷凝液12.换热后的壳程介质
a.废热锅炉b.过滤器c.压缩机
d.汽包
具体实施方式
以下结合附图对本公开的具体实施方式进行详细说明。应当理解的是,此处所描述的具体实施方式仅用于说明和解释本公开,并不用于限制本公开。
在本公开中,在未作相反说明的情况下,使用的方位词如“上、下”通常是指装置在正常使用状态下的上和下,具体可参考图1的图面方向。“内、外”是针对装置本身的轮廓而言的。
如图1所示,本公开第一方面提供一种利用煤气化装置的合成气发生蒸汽的方法,该方法包括如下步骤:使粗合成气1进入废热锅炉的换热管内作为热介质与废热锅炉的壳程介质换热,得到换热后的合成气2和换热后的壳程介质12;使换热后的合成气2经过滤、升压后得到升压合成气5;使至少部分升压合成气返回废热锅炉a的换热管入口,对换热管进行吹扫除尘;使换热后的壳程介质12进入气液分离装置进行气液分离,得到饱和蒸汽10和冷凝液11;使冷凝液11作为壳程介质返回废热锅炉a。
本公开的方法通过将过滤升压后清洁的升压合成气返回废热锅炉,利用升压合成气的高速气流对废锅入口换热管进行反吹,防止飞灰沉积在废锅管内,延长废锅的操作周期和气化炉的运行时间,从而节省煤气化装置的操作费用。
在本公开的方法中,粗合成气具有较高的温度,利用粗合成气发生蒸汽能够充分利用系统热能,起到节能降耗作用,通常粗合成气的温度可以为800~1024℃;利用粗合成气作为热介质换热得到的饱和蒸汽可以送至其他装置利用,饱和蒸汽的温度可以为320~327℃,经过过滤和升压后送出装置的外送合成气的温度可以为180~187℃,压力可以为9~11mpa。
为了补充废热锅炉与气液分离装置之间的循环水量,可以向系统中加入补充介质,补充介质为锅炉给水;将锅炉给水送入系统的方法没有特别要求。在一种具体实施方式中,如图1所示,可以使补充介质9进入气液分离装置与换热后的壳程介质12混合以补充循环水量,在这一实施方式中,气液分离装置中补充介质9与换热后的壳程介质12混合并经气液分离后,得到的冷凝液11可以在重力作用下经管路流入废热锅炉a,而无需外加液体输送装置,节约设备成本和系统能耗。
为了进一步提高升压合成气在废热锅炉内分布的均匀性,以提高对换热管进行反吹除尘的效果,在一种具体实施方式中,如图1所示,废热锅炉内可以设有气体分布器,气体分布器上可以设有气体喷孔,气体喷孔优选朝向换热管的入口,以充分吹扫换热管;进一步地,气体喷孔的个数和位置优选与换热管相匹配,即每个换热管的入口处设有一个气体喷孔,升压合成气经气体分布器上的气体喷孔喷入换热管,以确保每个换热管内的积尘都被充分吹扫去除。
在本公开的方法中,换热后的合成气2经过滤可以除去飞灰,得到清洁的合成气4,该清洁的合成气4经升压后可以得到高速射流的升压合成气5,以进一步提高对换热管的吹尘效果;升压的方法和装置可以为本领域常规的,例如进入压缩机c进行升压,升压合成气的压力可以在较大范围内变化,例如升压合成气与换热后的合成气的压力比可以为(2~2.5):1。
进一步地,为了保证系统内合成气量平衡,并提高对换热管的吹扫除尘效果,在一种具体实施方式中,该方法可以包括:使升压合成气间歇地喷入换热管的入口;其中,使合成气间歇地喷入换热管的入口的方法可以为本领域常规的,在一种优选的具体实施方式中,可以通过开关阀控制升压合成气喷入换热管的入口,开关阀可以为本领域常规种类,例如为电磁阀,开关阀可以由时间继电器控制,优选地,每次喷射的持续时间可以为10~20s,优选为10s;相邻两次喷射的间隔时间可以为10~20min,优选为10min。
如图1所示,本公开第二方面提供一种利用煤气化合成气发生蒸汽的系统,该系统包括合成气原料入口、废热锅炉a、气液分离装置、过滤器b、气体增压装置、蒸汽出口和净化合成气出口;废热锅炉包括壳体、合成气入口、合成气出口和设置于壳体内的换热管,换热管的入口和出口分别与合成气入口和合成气出口连通,合成气出口依次与过滤器及气体增压装置连通,气体增压装置的出口通过气体循环管路与换热管的入口连通;废热锅炉的壳程出口与气液分离装置的气液混合物入口连通,气液分离装置的气体出口与蒸汽出口连通,气液分离装置的液体出口与废热锅炉的壳程入口连通。
本公开的系统通过将过滤升压后清洁的升压合成气返回废热锅炉,利用升压合成气与废热锅炉内的高压差形成的高速气流对废锅入口换热管进行反吹冲刷,防止飞灰沉积在废锅管内,可以减少废锅换热管内的飞灰沉积,延长废锅的操作周期,并延长气化炉的运行时间,从而节省煤气化装置的操作费用。
根据本公开,合成气原料入口可以与废热锅炉a的合成气入口连通,废热锅炉a还可以包括壳程介质入口和壳程介质出口,壳程介质出口可以与气液分离装置连通;粗合成气可以经合成气原料入口进入废热锅炉a,为壳程介质加热,得到换热后的合成气2和换热后的壳程介质12,换热后的合成气2可以从合成气出口离开废热锅炉a,经过滤器b过滤得到清洁的合成气4,再经气体增压装置升压后得到升压合成气5;少部分升压合成气可以作为反吹合成气7返回废热锅炉的换热管入口处对换热管进行吹扫除尘,另一部分升压合成气可以作为外送合成气6经净化合成气出口送出系统;换热后的壳程介质12可以经壳程介质出口离开废热锅炉a进入气液分离装置进行气液分离,得到饱和蒸汽10和冷凝液11;冷凝液11可以作为壳程介质经壳程介质入口返回废热锅炉,饱和蒸汽10可以从系统的蒸汽出口送出。
根据本公开,气液分离装置可以为常规种类,优选地,气液分离装置为汽包;进一步地,为了补充废热锅炉与气液分离装置之间的循环水量,在一种具体实施方式中,系统还可以包括与汽包连通的补充介质入口,以使补充介质9进入气液分离装置与换热后的壳程介质12混合以补充循环水量,在这一实施方式中,气液分离装置中补充介质9与换热后的壳程介质12混合并经气液分离后,得到的冷凝液11可以在重力作用下经管路流入废热锅炉a,而无需外加液体输送装置,节约设备成本和系统能耗。
为了进一步提高升压合成气在废热锅炉内分布的均匀性,以提高对换热管进行反吹除尘的效果,在一种具体实施方式中,如图1所示,气体循环管路的出口可以延伸至废热锅炉内,且出口处可以连接气体分布器;进一步地,为了提高喷气除尘的效果,气体分布器可以设有朝向换热管的入口的气体喷孔,以充分吹扫换热管;进一步地,气体喷孔的个数和位置优选与换热管相匹配,即每个换热管的入口处设有一个气体喷孔,换热管的入口和气体喷孔一一对应,升压合成气经气体分布器上的气体喷孔喷入换热管,以确保每个换热管内的积尘都被充分吹扫去除。
进一步地,为了提高吹扫除尘的效果,一种实施方式中,废热锅炉内可以设有多个气体分布器,例如2~6个,多个气体分布器可以分别设置于换热管的上方,进一步地,多个气体分布器可以在换热管上方的同一平面内分布,并优选覆盖整个换热管入口区域,以使经气体分布器喷出的升压合成气能够充分吹扫每一根换热管。
在一种实施方式中,如图3所示,气体分布器可以包括设置于同一平面内的主管和多个支管,以覆盖更大的吹扫面积,多个支管可以分别与主管连通,主管可以与气体循环管路的出口连通,进一步地,支管可以与主管垂直排布,多个支管可以间隔排布以形成鱼骨式分布的气体分布器;进一步地,如图2所示,支管的底端可以设有多个气体喷孔,气体喷孔的个数和位置优选与换热管相匹配,即每个换热管的入口处可以设有一个气体喷孔,升压合成气经气体分布器上的气体喷孔喷入换热管,以确保每个换热管内的积尘都被充分吹扫去除。
为了进一步提高升压合成气对换热管的吹扫除尘效果,在一种具体实施方式中,气体循环管路上可以设有开关阀,以间隔开启气体循环管路,从而使升压合成气间歇地喷入换热管的入口;在一种优选的具体实施方式中,气体循环管路上可以设置开关阀,以通过开关阀控制升压合成气喷入换热管的入口,开关阀可以为本领域常规种类,例如为电磁阀;进一步地,开关阀可以与时间继电器连接,以由时间继电器控制开关阀的通断,从而定时间隔开闭气体循环管路。
以下通过实施例进一步说明本公开,但是本公开并不因此而受到任何限制。
实施例1
本实施例用于说明本公开的利用煤气化合成气发生蒸汽的方法和系统。
如图1所示,使高温的粗合成气1经过废热锅炉a的管侧,与壳侧的冷凝液11进行换热,换热后的壳程介质12进入汽包d,饱和蒸汽10送出装置。换热后的合成气2经过过滤器过滤掉飞灰,清洁的合成气4经过压缩机c升压至压力为粗合成气压力的2.5倍得到升压合成气5。升压合成气5的一部分作为外送合成气6送至系统外,另一部分作为反吹合成气7返回废热锅炉a入口。反吹合成气7分为两路,两路管平均布置且末端分别从废热锅炉两边对称插入废热锅炉a内部,开口相对,即废热锅炉内两路反吹合成气管路开口呈180度布置。两路气体循环管上分别装有开关阀,开关阀由时间继电器控制,每10分钟开启一次,每次开启10秒。如图3所示,两路气体循环管路的末端分别伸入废热锅炉内,且每个气体循环管路的末端分别连接两个气体分布器。每个气体分布器包括一根主管和4根支管,呈鱼骨状分布排列,每根支管的底部开有气体喷孔,如图2所示,每根支管上的气体喷孔的数量与所覆盖的换热管数量一致,且位置相对应。反吹合成气7的两路管路上的阀门打开时,升压合成气经过气体分布器的主管、支管并从气体喷孔喷出,进入废热锅炉a的换热管内。每个开孔都喷出升压合成气形成的高速射流的气体,气体将换热管内的飞灰冲刷掉,从而减少飞灰在换热管内的沉积。
与不进行合成气反吹的常规方法相比,本实施例中的废锅的操作周期延长了3-6个月,气化炉的运行时间延长了3-6个月。
以上结合附图详细描述了本公开的优选实施方式,但是,本公开并不限于上述实施方式中的具体细节,在本公开的技术构思范围内,可以对本公开的技术方案进行多种简单变型,这些简单变型均属于本公开的保护范围。
另外需要说明的是,在上述具体实施方式中所描述的各个具体技术特征,在不矛盾的情况下,可以通过任何合适的方式进行组合。为了避免不必要的重复,本公开对各种可能的组合方式不再另行说明。
此外,本公开的各种不同的实施方式之间也可以进行任意组合,只要其不违背本公开的思想,其同样应当视为本公开所公开的内容。
起点商标作为专业知识产权交易平台,可以帮助大家解决很多问题,如果大家想要了解更多知产交易信息请点击 【在线咨询】或添加微信 【19522093243】与客服一对一沟通,为大家解决相关问题。
此文章来源于网络,如有侵权,请联系删除


