锅炉安全节能综合利用系统的制作方法



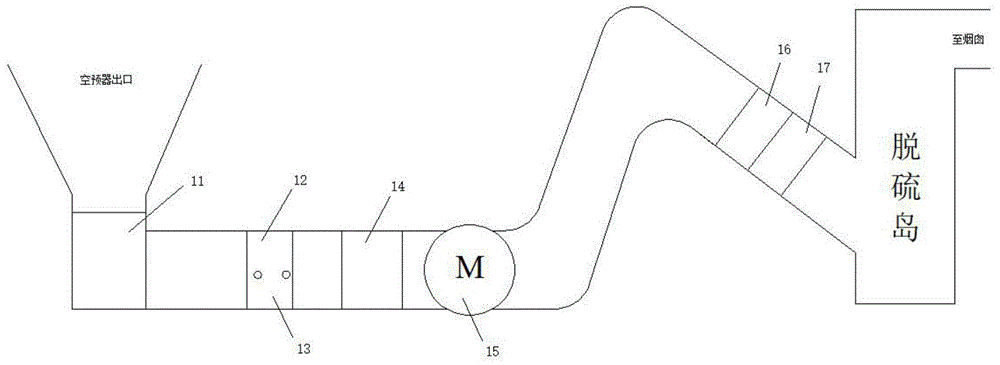
本发明属于火力发电技术领域,尤其涉及一种锅炉安全节能综合利用系统。
背景技术:
实现锅炉的安全和经济是锅炉设计、建设、运行和检修追求的目标,往往安全性和经济性追求极致过程中出现矛盾,锅炉热损失是锅炉的主要方式,减少锅炉热损失的主要手段就是降低排烟温度,而降低排烟温度会导致烟气酸露和硫酸氢铵对回转式空气预热器的堵塞,同时烟气温度降低也会增加飞灰的硬度,加剧受热面的磨损,给烟气的降温带来一系列的困难,轻则烟气余热利用效果降低,中则机组降负荷运行,重则机组停机。为了降低飞灰颗粒对受热面的磨损、消除空预器的硫酸氢铵堵塞和平衡酸露对受热面的危害,需要一种锅炉安全节能综合利用系统。
技术实现要素:
本发明的目的是提供一种锅炉安全节能综合利用系统,以解决上述技术问题。
本发明提供了一种锅炉安全节能综合利用系统,包括烟气放热系统、余热利用循环换热系统及热风加热系统;
所述烟气放热系统包括空预器出口至脱硫岛烟道,所述烟道内沿烟气流动方向依次设有飞灰分离器、换热器、除尘器、引风机、一级换热器、二级换热器;所述二级换热器至脱硫岛段烟道采用防酸蚀烟道;所述一级换热器、二级换热器采用微倾斜布置,以使凝结的酸露安全的流到脱硫岛;
所述余热利用循环换热系统包括补水水箱、暖风器循环泵、引风机出口一级换热器、引风机出口二级换热器、除尘器入口换热器、风机入口一级换热器、风机入口二级换热器、高温风冷却器、汽机除氧器;所述补水水箱通过所述暖风器循环泵依次连接所述引风机出口二级换热器、引风机出口一级换热器、除尘器入口换热器、风机入口一级换热器;所述除尘器入口换热器通过所述高温风冷却器与所述汽机除氧器连接;所述高温风冷却器通过所述风机入口二级换热器与所述风机入口一级换热器连接;所述风机入口一级换热器与所述补水水箱连接;
所述热风加热系统包括送风加热系统及一次风加热系统,所述送风加热系统的送风通道内沿送风方向依次设有送风机、热风换热器、空气预热器、高温风冷却器,所述送风加热系统热风换热器采用一级换热器或沿送风方向依次采用一级换热器及二级换热器;所述送风通道还连接有冬季防冻再循环风道,所述冬季防冻再循环风道一端与所述送风机与风机入口之间的送风通道连通,另一端沿送风方向与所述高温风冷却器后的送风通道连通。
所述一次风加热系统的一次风通道内沿一次风流向依次设有一次风机、热风换热器、空气预热器、高温风冷却器,所述一次风加热系统热风换热器采用一级换热器或沿一次风流向依次采用一级换热器及二级换热器;所述一次风通道还连接有冬季防冻再循环风道,所述冬季防冻再循环风道一端与所述一次风机与风机入口之间的一次风通道连通,另一端与所述送风加热系统的高温风冷却器后的送风通道连通。
进一步地,所述空预器出口至脱硫岛烟道的空预器出口至飞灰分离器进口段为细径段,飞灰分离器出口至脱硫岛段为粗径段。
进一步地,所述空气预热器采用三分仓布置或四分仓布置的空气预热器,用于将空预器入口风温提高到温风或热风,用以在空气预热器旋转到烟气侧前,确保转子温度达到硫酸氢铵不板结条件,保证任何一点排烟温度不低于146℃。
进一步地,所述烟气放热系统中换热器上设有防磨瓦。
进一步地,所述飞灰分离器包括烟气导流板、锁气式机翼型分离格栅、储灰罐,所述烟气导流板设于烟气入口及烟气出口,所述锁气式机翼型分离格栅设于烟气入口烟气导流板下方,所述储灰罐与所述锁气式机翼型分离格栅连接。
进一步地,所述送风加热系统中所述一级换热器与送风机之间设有风机出口电动门。
进一步地,所述送风加热系统中所述冬季防冻再循环风道内设有调节电动门。
进一步地,所述一次风加热系统中所述一级换热器与一次风机之间设有风机出口电动门。
进一步地,所述一次风加热系统中所述冬季防冻再循环风道内设有调节电动门。
借由上述方案,通过锅炉安全节能综合利用系统,具有如下技术效果:
(1)降低了飞灰对余热利用受热面磨损的危害。
(2)解决了脱硝投入过程中回转式空预器硫酸氢铵堵塞问题。
(3)平衡了烟气酸蚀对烟气余热利用受热面的损害。
(4)实现了烟气余热的梯级利用,提高了电厂的经济性。
(5)解决了寒冷地区暖风器冬季频繁冻裂泄漏的问题。
(6)解决了寒冷地区空气预热器冬季漏风增大的问题。
(7)机翼型分离格栅净化了烟气中的飞灰,除降低飞灰对余热利用受热面磨损的危害外也降低了除尘器的负担。
(8)锁气式机翼型分离格栅实现了积灰的自动清理。
(9)余热利用采用独立循环换热系统,能够实现安全可靠、调整灵活的要求。
(10)高温风冷却器高负荷不仅能够实现风温的降温作用,低负荷引入锅炉辅汽也可实现低负荷的冷风加热作用。
(11)风加热器布置在风机出口和热风再循环后,不仅能够保证暖风器前风温度始终大于5℃,也能够利用风机的升压热量,从而保证暖风器的安全。
(12)系统的实用性、科学性、可行性、安全性和创新性达到了工程应用的全部要求。
上述说明仅是本发明技术方案的概述,为了能够更清楚了解本发明的技术手段,并可依照说明书的内容予以实施,以下以本发明的较佳实施例详细说明如后。
附图说明
图1是本发明烟气放热系统的结构示意图;
图2是空预器布置型式示意图;
图3是本发明换热器防磨瓦布置示意图;
图4是本发明飞灰分离器的结构示意图;
图5是本发明机翼型分离格栅的结构示意图;
图6是本发明锁气器阻挡器的结构示意图;
图7是本发明锁气器配重块及支撑轴的结构示意图;
图8是本发明余热利用循环换热系统的结构示意图;
图9是本发明送风加热系统的结构示意图;
图10是本发明一次风加热系统的结构示意图。
图中标号:
11-飞灰分离器;111-烟气导流板;112-机翼型分离格栅;113-储灰罐;114-阻挡器;115-锁气器配重块;116-支撑轴;12-换热器;121-换热器防磨瓦;13-吹灰器;14-除尘器;15-引风机;16-烟气放热系统一级换热器;17-烟气放热系统二级换热器;
21-补水水箱;22-暖风器循环泵;23-引风机出口一级换热器;24-引风机出口二级换热器;25-除尘器入口换热器;26-风机入口一级换热器;27-风机入口二级换热器;28-高温风冷却器;29-汽机除氧器;
31-热风加热系统一级换热器;32-热风加热系统二级换热器;33-冬季防冻再循环风道;34-高温风冷却器;35-空气预热器;36-送风机;37-一次风机;38-风机出口电动门;39-调节电动门。
具体实施方式
下面结合附图和实施例,对本发明的具体实施方式作进一步详细描述。以下实施例用于说明本发明,但不用来限制本发明的范围。
本实施例提供了一种锅炉安全节能综合利用系统,主要包括烟气放热系统、余热利用循环换热系统、热风加热系统。下面对各系统作进一步详细说明。
1、烟气放热系统
参图1所示,烟气放热系统由飞灰分离器11、除尘器前换热器12(包含吹灰器13)、脱硫岛前的烟气防热系统一级换热器16、脱硫岛前的烟气放热系统二级换热器17、烟道、受热面管道、阀门和对应的热工测点组成。烟道从空预器出口开始变细,烟气速度增加,经飞灰分离后,重新扩粗,在除尘器入口换热器12前实现烟气降速。
烟气放热系统包括空预器出口至脱硫岛烟道,烟道内沿烟气流动方向依次设有飞灰分离器11、换热器、除尘器14、引风机15、烟气放热系统一级换热器16、烟气放热系统二级换热器17;烟气放热系统二级换热器17至脱硫岛段烟道采用防酸蚀烟道;烟气放热系统一级换热器16、烟气放热系统二级换热器17采用微倾斜布置,以使凝结的酸露安全的流到脱硫岛。
空预器入口风温提高到温风或热风,依据空预器旋转方向,在空预器旋转到烟气侧前,确保转子温度达到硫酸氢铵不板结条件,保证任何一点排烟温度不低于146℃,彻底解决硫酸氢铵的板结,解决空预器的硫酸氢铵堵塞问题。常用的布置型式如图2所所示,其中,图a、b为四分仓布置;c、d为三分仓布置。本实施例进入烟气侧前采用热风方式。
提高一次送风温度后,排烟温度能够达到146℃以上,为了除尘器14安全,且保证除尘效果,在除尘前增加换热器12,进一步降低排烟温度。吹灰管路可以直接利用空预器吹灰管路,融入空预器吹灰系统中。除尘器14前换热器12上携带换热器防磨瓦121。
参图3所示,换热器防磨瓦121采用罩在首根受热面管设计,目的是防止受热面受到气流的直接冲刷,降低受热面磨损,同时进行烟气均流,进一步降低气流偏差对受热面的损坏。
引风机15出口设置烟气放热系统一级换热器16、烟气放热系统二级换热器17,进行换热器分级的原因是烟气的酸露点。烟气放热系统一级换热器16布置在烟气酸露点之前,烟气放热系统二级换热器17布置在烟气酸露点之后,所以二级及二级后的烟道需要采用防酸蚀设计,同时两级换热器布置采用微倾斜布置,实现凝结的酸露能够安全的流到脱硫岛。增加的烟气放热系统二级换热器17布置虽能提高烟气余热利用的经济性,但也会增加相应的投资,用户可以根据自己的需求选用一级布置或两级布置。一级布置后的排烟温度应不低于90℃。当一烟气放热系统级换热器16后的排烟温度低于90℃时,为了保护烟气放热系统一级换热器16和烟道,烟气放热系统一级换热器16不投入。
参图4至图7所示,飞灰分离器11由烟气导流板111、锁气式机翼型分离格栅112、储灰罐113及相应的除灰压缩空气、管道、阀门和热工测点组成。烟气导流板111设于烟气入口及烟气出口,机翼型分离格栅112设于烟气入口烟气导流板111下方,储灰罐113与机翼型分离格栅112连接。烟气导流板111实现烟气的均流和烟气流向的调整。靠近烟气入口的导流板使烟气能够正对机翼型分离格栅112,确保烟气中的飞灰更有效的分离,靠近烟气出口的导流板实现烟气均匀流动,降低烟气不均对受热面的磨损。飞灰分离器还能够降低除尘器14的负担,保证环保指标的正常。
机翼型分离格栅112能够利用飞灰的惯性高效实现飞灰的分离,且能够避免飞灰的反流,同时还不增加较多系统的阻力。
机翼型分离格栅112的锁气器由阻挡器114、锁气器配重块115和支撑轴116等组成,也可以采用其它方式的锁气器,目的是当机翼型分离格栅上积灰较多时自然卸灰,使灰进入储灰罐113(除灰系统)。除灰系统采用传统的除灰方式。由于主要输送粗灰,可以直接输灰到除渣系统。
2、余热利用循环换热系统
参图8所示,为了提高系统的安全性,降低对主机系统的干扰,热量的传递采用独立的循环换热系统。循环换热系统用水来自化学除盐水,系统主要由化学来水、补水水箱21、暖风器循环水泵22、引风机出口一级换热器23、引风机出口二级换热器24、除尘器入口换热器25、风机入口一级换热器26、风机入口二级换热器27、锅炉辅汽、高温风冷却器28、汽机除氧器29以及相应的管道、阀门、疏水、旁路和热工测点组成。
补水水箱21通过暖风器循环泵22依次连接引风机出口二级换热器24、引风机出口一级换热器23、除尘器入口换热器25、风机入口一级换热器26;除尘器入口换热器25通过高温风冷却器28与汽机除氧器29连接;高温风冷却器28通过风机入口二级换热器27与风机入口一级换热器26连接;风机入口一级换热器26与补水水箱21连接。
化学来水经暖风器循环泵22升压后进入引风机出口二级换热器24(可不选)、引风机出口一级换热器23、除尘器入口换热器25。在低负荷除尘器入口换热器25换热后的热水直接进入风机入口一级换热器26,进行热风加热;锅炉辅汽进入高温风冷却器28,被冷却的水进入风机入口二级换热器27继续加热热风,风机入口二级换热器27出口水进入风机入口一级换热器26,实现能量的梯级利用;风机入口一级换热器26后的热水回到补水水箱21,实现循环利用。在高负荷时,除尘器入口换热器25换热后的热水直接进入高温风冷却器28,进行热风冷却,换热后的热水依据热风需求,分别流入风机入口二级换热器27和汽机除氧器29,其中汽机除氧器29作为能量利用的辅助功能。风机入口二级换热器27后的疏水进入风机入口一级换热器26,最终回到补水水箱21,实现能源的梯级利用和循环利用。
3、热风加热系统
参图9、图10所示,热风加热系统包括送风加热系统及一次风加热系统,送风加热系统及一次风加热系统均包括热风一级换热器、热风二级换热器、冬季防冻热风再循环风道、高温风冷却器以及相应的测点和挡板等。热风加热系统依据风温的要求,布置一级换热器或一级换热器+二级换热器。同时,增加热风再循环系统应对寒冷地区冬季暖风器冻裂泄漏和寒冷导致的空预器漏风增大问题。由于一次风高温风属于高压头风,为了综合利用风机的效率,一次风机入口再循环风应采用高温风冷却器后送风再循环,如果存在布置困难问题,也可以采用高温风冷却器后一次风。同时烟风道系统上增加温度和压力测点以便于控制调节。
送风加热系统的送风通道内沿送风方向依次设有送风机36、热风换热器、空气预热器35、高温风冷却器34,送风加热系统热风换热器采用热风加热系统一级换热器31或沿送风方向依次采用热风加热系统一级换热器31及热风加热系统二级换热器32;送风通道还连接有冬季防冻再循环风道33,冬季防冻再循环风道33一端与送风机36与风机入口之间的送风通道连通,另一端沿送风方向与高温风冷却器34后的送风通道连通。
一次风加热系统的一次风通道内沿一次风流向依次设有一次风机37、热风换热器、空气预热器35、高温风冷却器34,一次风加热系统热风换热器采用热风加热系统一级换热器31或沿一次风流向依次采用热风加热系统一级换热器31及热风加热系统二级换热器32;一次风通道还连接有冬季防冻再循环风道33,冬季防冻再循环风道33一端与一次风机37与风机入口之间的一次风通道连通,另一端与送风加热系统的高温风冷却器34后的送风通道连通。
空气预热器入口风温提高到80~90℃之间,至少保证换热片返回烟气侧前的风温度不低于80℃。
由于热风的提高,高负荷时,空气预热器出口高温风温度得到提高,为了燃烧器安全、受热面安全和降低排烟温度,需要降低高温风温度,增加高温风冷却器,同时可实现能源的综合利用。高温风冷却器既是高负荷降温换热器,借助锅炉辅汽和一、二级换热器(或再循环风),也是低负荷提高锅炉高温风温度,保护风机出口一、二级换热器安全的加热器。
当环境温度低于5℃时,开启冬季防冻再循环风,以实现对风机入口换热器的保护。同时解决寒冷地区冬季导致的空预器漏风增大问题。利用高温风冷却系统、锅炉辅汽和再循环风道协同工作,实现启动过程中的送风启动加热功能,从而满足从启动到满负荷的全时段暖风器保护,提高机组低负荷稳燃能力。
以上所述仅是本发明的优选实施方式,并不用于限制本发明,应当指出,对于本技术领域的普通技术人员来说,在不脱离本发明技术原理的前提下,还可以做出若干改进和变型,这些改进和变型也应视为本发明的保护范围。
起点商标作为专业知识产权交易平台,可以帮助大家解决很多问题,如果大家想要了解更多知产交易信息请点击 【在线咨询】或添加微信 【19522093243】与客服一对一沟通,为大家解决相关问题。
此文章来源于网络,如有侵权,请联系删除


