一种组装式锅壳过热蒸汽锅炉的制作方法



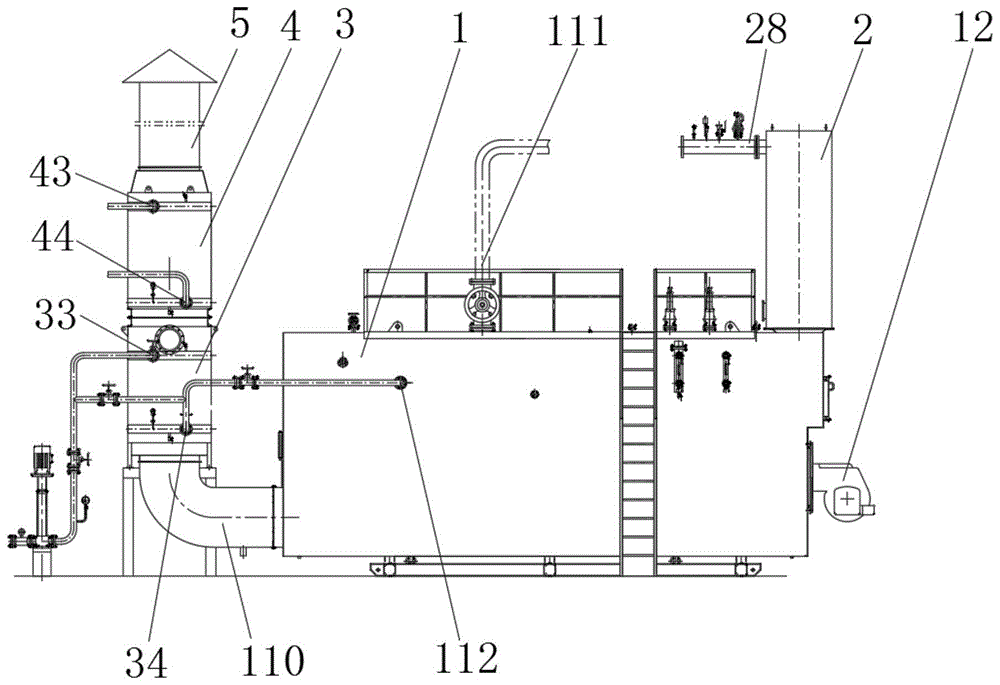
本发明属于锅炉领域,具体涉及一种组装式锅壳过热蒸汽锅炉。
背景技术:
燃油燃气锅炉从结构上可以分为锅壳锅炉和水管锅炉两种。
其中,水管锅炉虽然承压比较好,但结构相对复杂,生产制作耗费工时比较高,且占地面积比较大,对流管束不易检修,因此多用于一些高压力,大容量的锅炉。
而锅壳锅炉的水容量大,对负荷变动适应性好,对水质要求低;其圆筒形状的炉膛有利于油气燃料燃烧,采用微正压燃烧方式可取得较高的热效率,螺纹烟管、扰流条、扰流片等强化传热技术的应用使得锅炉结构更加简单,更加紧凑。因此,锅壳锅炉在一些小容量,低压力的场合得到了广泛应用。
但是,,当蒸汽锅炉距用户较远时,锅炉产生的饱和蒸汽在输送过程中易发生冷凝,一方面影响蒸汽的品质,另一方面冷凝出的水积聚在蒸汽输送管道内影响管道的使用寿命,而现有的锅壳锅炉,多为饱和蒸汽锅炉。
因此,亟需设计一种过热锅壳蒸汽锅炉,通过产生过热蒸汽来防止蒸汽输送过程中的冷凝。
技术实现要素:
本发明的目的是为克服上述现有技术的不足,提供一种组装式锅壳过热蒸汽锅炉。
为实现上述目的,本发明采用如下技术方案:
一种组装式锅壳过热蒸汽锅炉,包括锅炉主机,所述锅炉主机采用锅壳式三回程结构;所述锅炉主机的前烟箱顶端设置过热器;
所述过热器包括箱体,所述箱体的底板中部设置有与锅炉主机中二回程管束相连通的进烟口;所述进烟口两侧的箱体底板上对称设置向上延伸的烟气隔板;所述烟气隔板与箱体相应侧壁之间的箱体底板上设置有与锅炉主机中三回程管束相连通的出烟口;
两块烟气隔板之间沿竖直方向设置有若干排水平式蛇形换热管,所述水平式蛇形换热管的弯曲部穿过相应的烟气隔板且与相应的烟气隔板固定连接;
所述水平式蛇形换热管的蒸汽入口端与沿竖直方向延伸的进口中间联箱相连通,所述进口中间联箱的顶部与入口集箱相连通,所述入口集箱与锅炉主机的蒸汽出口管相连通;
所述水平式蛇形换热管的蒸汽出口端与沿竖直方向延伸的出口中间联箱相连通,所述出口中间联箱的顶部与出口集箱相连通,所述出口集箱与过热蒸汽出口管相连通。
优选的,两块烟气隔板之间的水平式蛇形换热管上螺旋缠绕有钢带。
优选的,所述烟气隔板的下端中部设置有矩形烟气调节口,所述矩形烟气调节口内设置调烟板;
所述调烟板一侧的中部固定设置一根沿烟气隔板宽度方向延伸的调节轴;
所述调节轴的一端穿过箱体的相应侧壁且与箱体的相应侧壁进行转动连接;所述调节轴穿出箱体侧壁的一端垂直固定设置调节把手,所述调节把手的端部垂直向外设置螺柱,所述螺柱上设置蝶形螺母;
所述调节把手对应的箱体侧壁外端设置调节筒,所述调节筒的外端设置封板;所述封板上设置有供螺柱穿过的环形轨道。
优选的,所述箱体的底板与锅炉主机通过螺栓进行可拆卸连接。
优选的,所述锅炉主机的烟气出口管后端依次设置节能器和冷凝器;
所述节能器包括节能箱体,所述节能箱体的底部烟气入口与锅炉主机的烟气出口管相连通;所述节能器内设置有若干排第一垂直式蛇形换热管;所述第一垂直式蛇形换热管的顶部入口端与节能器进水口相连,所述第一垂直式蛇形换热管的底部出口端与节能器出水口相连;
所述冷凝器包括冷凝箱体,所述冷凝箱体的底部烟气入口与节能器的顶部烟气出口相连通;所述冷凝器内设置有若干排第二垂直式蛇形换热管;所述第二垂直式蛇形换热管的顶部入口端与冷凝器进水口相连,所述第二垂直式蛇形换热管的底部出口端与冷凝器出水口相连;
所述冷凝器的顶部烟气出口设置烟囱。
优选的,所述第一垂直式蛇形换热管的直管段、第二垂直式蛇形换热管的直管段上均螺旋缠绕有钢带。
优选的,所述锅炉主机内设置炉胆,所述炉胆的前端设置燃烧器,所述炉胆的后端设置回燃室;
所述锅炉主机的前后两端分别设置前管板和后管板;所述前管板与锅炉主机的前烟箱形成前烟室,所述后管板与锅炉主机的后烟箱形成后烟室;
所述炉胆上方设有层层排列的二回程管束和三回程管束;
所述二回程管束的入口与回燃室相连通,所述二回程管束的出口与前烟室相连通,所述前烟室与过热器箱体的底部进烟口相连通;
所述三回程管束的入口与过热器箱体底部的出烟口相连通,所述三回程管束的出口与后烟室相连通,所述后烟室与锅炉主机的烟气出口管相连通;
所述锅炉主机的锅炉进水口与节能器的节能器出水口相连通。
优选的,所述锅炉主机内蒸汽出口管的前端设置汽水分离器;
所述汽水分离器包括分离一壳、分离二壳;
所述分离一壳呈横向设置的且两端封堵的管状结构,所述分离一壳的侧壁上部设置有用来与锅炉主机内蒸汽出口管底端相连接的通孔;所述通孔两侧的分离一壳侧壁上部设置有若干一壳匀汽通孔;所述分离一壳的侧壁下部沿长度方向设置若干一壳排水孔;
所述分离二壳位于分离一壳的外部;所述分离二壳包括两块沿分离一壳长度方向延伸的且对称设置的缝隙挡板,两块缝隙挡板的底部固定连接;两块缝隙挡板的两端固定设置二壳封板;所述缝隙挡板、二壳封板的顶部与锅炉主机的内壁固定连接;
所述缝隙挡板的下部呈向内弯折的结构;所述缝隙挡板上端竖直段的上部设置若干条形通孔;所述分离二壳的底部设置若干排水管;
所述分离二壳两侧缝隙挡板的外部对称设置分离三壳;
所述分离三壳包括匀汽孔板,所述匀汽孔板的上下两端均呈弯折结构;所述匀汽孔板的两端固定设置三壳封板;所述匀汽孔板的上下两端、三壳封板的端部均与相应缝隙挡板上部竖直端的外端面固定连接;
所述匀汽孔板的中间竖直段上均匀设置若干三壳匀汽通孔;
所述缝隙挡板上端竖直段的下部设置若干疏水孔;
所述缝隙挡板上条形通孔、疏水孔位于相应匀汽孔板的上下两端之间;
所述分离三壳的内侧设置钢丝网分离器。
优选的,所述钢丝网分离器包括若干层压紧的钢丝网。
优选的,所述钢丝网分离器包括4层或5层压紧的钢丝网。
本发明的有益效果是:
(1)本发明通过在锅炉主机上设置过热器,将锅炉主机蒸汽出口管的蒸汽通过二回程管束的来烟在过热器箱体内进行再次加热,从而得到过热蒸汽,来防止蒸汽输送过程中的冷凝。
(2)本发明中过热器内调烟板的设置,当调烟板发生转动时,锅炉主机中二回程管束的来烟有一部分沿调烟板与烟气隔板之间的空隙直接回到锅炉主机中三回程管束中,而不参与与过热器中水平式蛇形换热管内蒸汽的换热过程;即通过调烟板的转动控制进入到过热器与蒸汽进行换热的实际烟量,进而调节过热器出口过热蒸汽的温度;其中,通过调烟板的不同转动角度,实现烟量的调节,进而实现过热器出口不同过热蒸汽温度的调节。
(3)本发明中锅炉主机内汽水分离器包括分离三壳、钢丝网分离器、分离二壳、分离一壳,使锅炉主机内的湿蒸汽实现多级分离,提高了分离效果;多级分离之后的蒸汽干度大大提升,极大地提高了进入过热器的蒸汽品质。
附图说明
构成本申请的一部分的说明书附图用来提供对本申请的进一步理解,本申请的示意性实施例及其说明用于解释本申请,并不构成对本申请的不当限定。
图1是本发明组装式锅壳过热蒸汽锅炉的外部结构示意图;
图2是本发明组装式锅壳过热蒸汽锅炉的内部结构示意图;
图3是本发明中锅炉主机与过热器的位置关系示意图;
图4是本发明中过热器的结构示意图;
图5是图4的a向视图;
图6是图5中e的局部放大图;
图7是图4的b向视图;
图8是本发明中节能器的结构示意图;
图9是本发明中冷凝器的结构示意图;
图10是本发明中汽水分离器的结构示意图;
图11是本发明中分离一壳、分离二壳的结构示意图;
图12是本发明中分离一壳的展开示意图;
图13是本发明中缝隙挡板的结构示意图;
图14是图13的c向视图;
图15是本发明中匀汽孔板的结构示意图;
图16是图15的d向视图;
图17是本发明中钢丝网分离器的结构示意图;
其中,
1-锅炉主机,11-炉胆,12-燃烧器,13-回燃室,14-前管板,15-后管板,16-前烟室,17-后烟室,18-二回程管束,19-三回程管束,110-烟气出口管,111-蒸汽出口管,112-锅炉进水口;
2-过热器,21-箱体,22-烟气隔板,221-调烟板,222-调节轴,223-调节把手,224-螺柱,225-蝶形螺母,226-调节筒,227-封板,23-水平式蛇形换热管,24-进口中间联箱,25-入口集箱,26-出口中间联箱,27-出口集箱,28-过热蒸汽出口管,29-钢带;
3-节能器,31-节能箱体,32-第一垂直式蛇形换热管,33-节能器进水口,34-节能器出水口;
4-冷凝器,41-冷凝箱体,42-第二垂直式蛇形换热管,43-冷凝器进水口,44-冷凝器出水口;
5-烟囱;
61-分离一壳,611-通孔,612-一壳匀汽通孔,613-一壳排水孔;62-分离二壳,621-缝隙挡板,622-二壳封板,623-条形通孔,624-疏水孔,625-排水管;63-分离三壳,631-匀汽孔板,632-三壳匀汽通孔;64-钢丝网分离器,641-连接凸块;
→烟气流通方向。
具体实施方式
应该指出,以下详细说明都是例示性的,旨在对本申请提供进一步的说明。除非另有指明,本文使用的所有技术和科学术语具有与本申请所属技术领域的普通技术人员通常理解的相同含义。
本发明中,术语如“相连”、“连接”等应做广义理解,表示可以是固定连接,也可以是一体地连接或可拆卸连接;可以是直接相连,也可以通过中间媒介间接相连。对于本领域的相关科研或技术人员,可以根据具体情况确定上述术语在本发明中的具体含义,不能理解为对本发明的限制。
下面结合附图和实施例对本发明进一步说明。
实施例1:
如图1-3所示,一种组装式锅壳过热蒸汽锅炉,包括锅炉主机1,所述锅炉主机1采用锅壳式三回程结构;所述锅炉主机1的前烟箱顶端设置过热器2;
如图4-7所示,所述过热器2包括箱体21,所述箱体21的底板中部设置有与锅炉主机1中二回程管束18相连通的进烟口;所述进烟口两侧的箱体21底板上对称设置向上延伸的烟气隔板22,具体地,所述烟气隔板22的前后两端与箱体21的前后内侧壁固定连接;所述烟气隔板22与箱体21相应侧壁之间的箱体底板上设置有与锅炉主机1中三回程管束19相连通的出烟口;
两块烟气隔板22之间沿竖直方向设置有若干排水平式蛇形换热管23,所述水平式蛇形换热管23的弯曲部穿过相应的烟气隔板22且与相应的烟气隔板22固定连接;所述水平式蛇形换热管23的蒸汽入口端与沿竖直方向延伸的进口中间联箱24相连通,所述进口中间联箱24的顶部与入口集箱25相连通,所述入口集箱25与锅炉主机1的蒸汽出口管111相连通;所述水平式蛇形换热管23的蒸汽出口端与沿竖直方向延伸的出口中间联箱26相连通,所述出口中间联箱26的顶部与出口集箱27相连通,所述出口集箱27与过热蒸汽出口管28相连通,过热蒸汽出口管28上设置过热器仪表集箱。
具体地,锅炉主机1产生的蒸汽通过入口集箱25、进口中间联箱24进入各个水平式蛇形换热管23内,与由锅炉主机1二回程管束18进入到箱体21内的烟气进行换热,从而将蒸汽加热到过热蒸汽,最后经由各个水平式蛇形换热管23的出口端、出口中间联箱26、出口集箱27、过热蒸汽出口管28输送至用户使用,其中本申请锅炉可为用户提供260℃的过热蒸汽;而由底部进烟口进入到箱体21的烟气向上冲刷水平式蛇形换热管23,向上越过烟气隔板22后再向下冲刷水平式蛇形换热管23,最后经出烟口回到锅炉主机1的三回程管束19内。
优选的,两块烟气隔板22之间的水平式蛇形换热管23上螺旋缠绕有钢带29,以增加受热面,提升传热效率。
优选的,如图5-6所示,所述烟气隔板22的下端中部设置有矩形烟气调节口,所述矩形烟气调节口内设置调烟板221,其中调烟板221的大小与矩形烟气调节口的大小相适应;
所述调烟板221一侧的中部固定设置一根沿烟气隔板22宽度方向延伸的调节轴222;
所述调节轴222的一端穿过箱体21的相应侧壁且与箱体21的相应侧壁进行转动连接;所述调节轴222穿出箱体21侧壁的一端垂直固定设置调节把手223,所述调节把手223的端部垂直向外设置螺柱224,所述螺柱224上设置蝶形螺母225;
所述调节把手223对应的箱体21侧壁外端设置调节筒226,所述调节筒226的外端设置封板227;所述封板227上设置有供螺柱224穿过的环形轨道。
沿环形轨道转动螺柱224,使调烟板221发生转动,从而使锅炉主机1中二回程管束18的来烟有一部分沿调烟板221与烟气隔板22之间的空隙直接回到锅炉主机1中三回程管束19中,而不参与与过热器2中水平式蛇形换热管23内蒸汽的换热过程;即通过调烟板221的转动控制进入到过热器2与蒸汽进行换热的实际烟量,进而调节过热器2出口过热蒸汽的温度;其中,通过调烟板221的不同转动角度,实现烟量的调节,进而实现过热器2出口不同过热蒸汽温度的调节。
其中,当转动螺柱224调整好调烟板221的转动角度后,通过拧紧蝶形螺母225,使蝶形螺母225压紧在封板227的外端面上,实现调烟板221的定位。
同时,两块烟气隔板22上的调烟板221可实现单独控制。
优选的,所述箱体21的底板与锅炉主机1通过螺栓进行可拆卸连接,从而实现过热器2与锅炉主机1的单独运输。
实施例2:
在实施例1的基础上,所述锅炉主机1的烟气出口管110后端依次设置节能器3和冷凝器4;
如图8所示,所述节能器3包括节能箱体31,所述节能箱体31的底部烟气入口与锅炉主机1的烟气出口管110相连通;所述节能器3内设置有若干排第一垂直式蛇形换热管32;所述第一垂直式蛇形换热管32的顶部入口端与节能器进水口33相连,所述第一垂直式蛇形换热管32的底部出口端与节能器出水口34相连;
如图9所示,所述冷凝器4包括冷凝箱体41,所述冷凝箱体41的底部烟气入口与节能器3的顶部烟气出口相连通;所述冷凝器4内设置有若干排第二垂直式蛇形换热管42;所述第二垂直式蛇形换热管42的顶部入口端与冷凝器进水口43相连,所述第二垂直式蛇形换热管42的底部出口端与冷凝器出水口44相连;
所述冷凝器4的顶部烟气出口设置烟囱5。
本申请中节能器3、冷凝器4形成两级节能装置,经过将烟气与水进行换热,最终排烟温度可降至60℃以下,热效率高。
优选的,所述第一垂直式蛇形换热管32的直管段、第二垂直式蛇形换热管42的直管段上均螺旋缠绕有钢带29,以增加受热面,提升传热效率。
其中,所述第一垂直式蛇形换热管32、第二垂直式蛇形换热管42均采用nd钢材质,可以有效防止硫腐蚀,提高节能器3和冷凝器4的使用寿命。
实施例3:
在实施例2的基础上,如图2所示,所述锅炉主机1内设置炉胆11,所述炉胆11的前端设置燃烧器12,所述炉胆11的后端设置回燃室13;
所述锅炉主机1的前后两端分别设置前管板14和后管板15;所述前管板14与锅炉主机1的前烟箱形成前烟室16,所述后管板15与锅炉主机1的后烟箱形成后烟室17;
所述炉胆11上方设有层层排列的二回程管束18和三回程管束19;
所述二回程管束18的入口与回燃室13相连通,所述二回程管束18的出口与前烟室16相连通,所述前烟室16与过热器箱体21的底部进烟口相连通;
所述三回程管束19的入口与过热器箱体21底部的出烟口相连通,所述三回程管束19的出口与后烟室17相连通,所述后烟室17与锅炉主机1的烟气出口管110相连通;
所述锅炉主机1的锅炉进水口112与节能器3的节能器出水口34相连通;即节能器3利用锅炉主机1烟气的余热对水进行加热,将加热后的水输送至锅炉主机1内,充分利用了烟气的余热,提高了热效率。
其中,锅炉主机1的蒸汽出口管111与过热器2的入口集箱25相连通。
实施例4:
在实施例1或实施例2或实施例3的基础上,所述锅炉主机1内蒸汽出口管111的前端设置汽水分离器;
如图10所示,所述汽水分离器包括分离一壳61、分离二壳62;
如图11-12所示,所述分离一壳61呈横向设置的且两端封堵的管状结构,所述分离一壳61的侧壁上部设置有用来与锅炉主机1内蒸汽出口管111底端相连接的通孔611;所述通孔611两侧的分离一壳61侧壁上部设置有若干一壳匀汽通孔612;所述分离一壳61的侧壁下部沿长度方向设置若干一壳排水孔613;
所述分离二壳62位于分离一壳61的外部;所述分离二壳62包括两块沿分离一壳61长度方向延伸的且对称设置的缝隙挡板621,两块缝隙挡板621的底部固定连接;两块缝隙挡板621的两端固定设置二壳封板622;所述缝隙挡板621、二壳封板622的顶部与锅炉主机1的内壁固定连接;
如图13-14所示,所述缝隙挡板621的下部呈向内弯折的结构,便于分离出的水滑落至排水管625;所述缝隙挡板621上端竖直段的上部设置若干条形通孔623;所述分离二壳62的底部设置若干排水管625;
所述分离二壳62两侧缝隙挡板621的外部对称设置分离三壳63;
所述分离三壳63包括匀汽孔板631,所述匀汽孔板631的上下两端均呈弯折结构,具体地,匀汽孔板631的上下两端均呈钝角弯折结构;所述匀汽孔板631的两端固定设置三壳封板;所述匀汽孔板631的上下两端、三壳封板的端部均与相应缝隙挡板621上部竖直端的外端面固定连接;
如图15-16所示,所述匀汽孔板631的中间竖直段上均匀设置若干三壳匀汽通孔632;
所述缝隙挡板621上端竖直段的下部设置若干疏水孔624;
所述缝隙挡板621上条形通孔623、疏水孔624位于相应匀汽孔板631的上下两端之间;
本申请中匀汽孔板631的设置,一方面起到一定的分离作用,另一方面还起到使蒸汽均匀的进入钢丝网分离器64的作用,避免蒸汽进入不均匀导致分离效果不好。
所述分离三壳63的内侧设置钢丝网分离器64。
优选的,所述钢丝网分离器64包括若干层压紧的钢丝网,具体地,若干层钢丝网通过螺栓、螺母压紧。
优选的,所述钢丝网分离器64包括4层或5层压紧的钢丝网。
优选的,所述缝隙挡板621的上端竖直段、钢丝网、匀汽孔板631的中间竖直段平行设置。
优选的,如图17所示,所述钢丝网分离器64的上、下两端对称设置若干连接凸块641;所述连接凸块641的外端与匀汽孔板631的相应弯折段内侧固定连接。
钢丝网分离器64安装之后,相邻连接凸块641之间与匀汽孔板631弯折段内侧形成空隙,匀汽孔板631分离出的水沿内壁滑落通过该空隙之后再通过疏水孔624进入到分离二壳62内部。
实施例4中,分离三壳63、钢丝网分离器64、分离二壳62和分离一壳61形成四级分离装置;
锅炉主机1内的湿饱和蒸汽沿两侧匀汽孔板631上三壳匀汽通孔632进入分离三壳63内实现一级分离;
一级分离后的蒸汽穿过钢丝网分离器64实现二级分离;
二级分离后的蒸汽通过两侧缝隙挡板621上条形通孔623进入分离二壳62内实现三级分离;
三级分离后的蒸汽通过分离一壳61上一壳匀汽通孔612进入分离一壳61内实现四级分离,四级分离后的蒸汽通过锅炉主机1的蒸汽出口管111排出;
一级分离出的水沿分离三壳63的内壁面滑落,通过相邻连接凸块641之间与匀汽孔板631弯折段内侧形成的空隙之后,再通过疏水孔624进入到分离二壳62内部,最后通过排水管625排出;
二级分离出的水沿分离三壳63的内壁面滑落,通过疏水孔624进入到分离二壳62内,最后通过排水管625排出;
三级分离出的水沿缝隙挡板621的内壁滑落至排水管625排出;
四级分离出的水通过分离一壳61上的一壳排水孔613下落至分离二壳62底部,再通过排水管625排出。
本申请中汽水分离器6的四级分离设置,可以将饱和蒸汽的湿度控制在1%以内,大大提高了进入过热器的蒸汽品质。
上述虽然结合附图对本发明的具体实施方式进行了描述,但并非对本发明的限制,所属领域技术人员应该明白,在本发明的技术方案的基础上,本领域技术人员不需要付出创造性劳动即可做出的各种修改或变形仍在本发明的保护范围以内。
起点商标作为专业知识产权交易平台,可以帮助大家解决很多问题,如果大家想要了解更多知产交易信息请点击 【在线咨询】或添加微信 【19522093243】与客服一对一沟通,为大家解决相关问题。
此文章来源于网络,如有侵权,请联系删除


