一种圆柱形低氮节能承压水管锅炉的制作方法



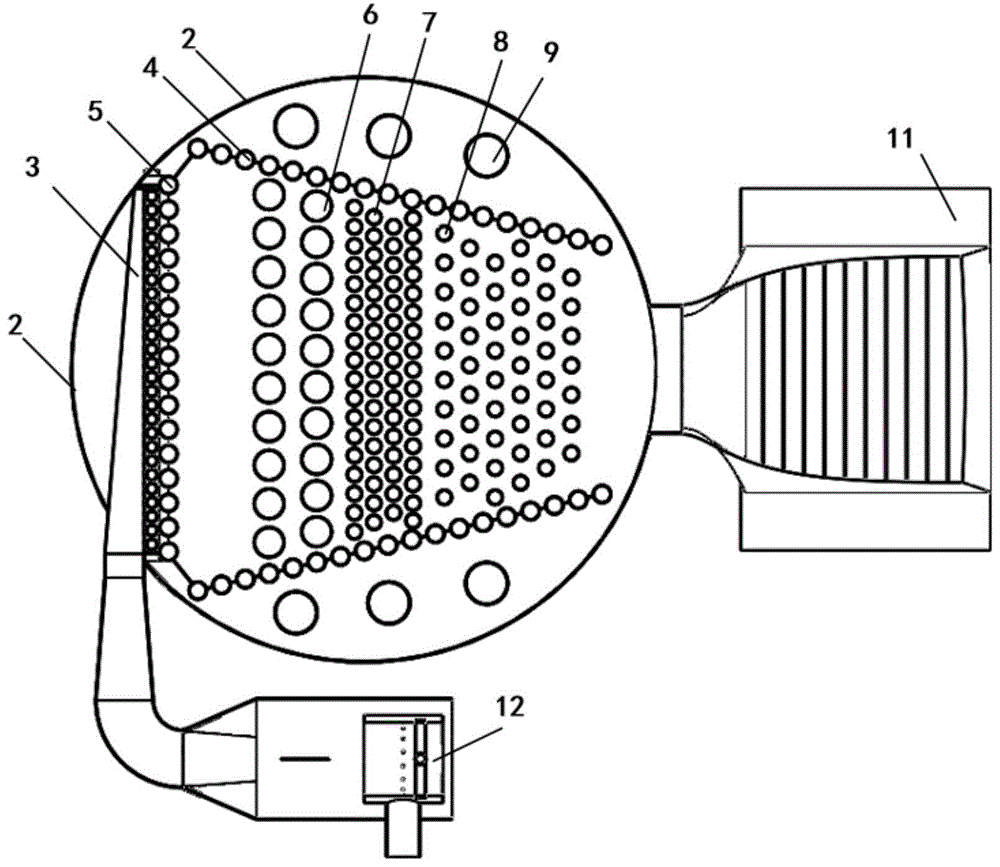
本发明涉及燃气锅炉技术领域,具体涉及一种圆柱形低氮节能承压水管锅炉。
背景技术:
根据我国的能源规划,到2035年天然气占一次能源的比例将提升至15%以上,年使用量可达6400亿立方米以上。2019年我国天然气消费量3067亿立方米,未来15年内,天然气年使用量将高速增长。我国工业燃料用气占天然气总用量的30%左右,工业领域需求的锅炉多为压力低于2.45mpa的低压小容量锅炉,包括低压热水锅炉和低压蒸汽锅炉。目前35蒸吨以下的燃煤锅炉已基本淘汰,低压小容量锅炉这一细分市场已被燃气锅炉所独占。伴随着工业的发展和天然气供应量的不断增加,未来15年内35蒸吨以下的燃气低压锅炉必将以每年5%以上的速度增加,低压燃气锅炉有着光明的前景。
目前市场上的主流承压蒸汽锅炉有水管式和火管式。火管式锅炉包括立式横烟管锅炉、卧式内燃湿背锅炉(wns)等,水管式锅炉包括贯流式锅炉、d型锅炉、角管锅炉等。主流蒸汽锅炉的配套燃烧器多为扩散式燃烧器和圆柱表面燃烧器,都留有巨大的炉膛空间。近年来,平面/曲面燃烧器技术迅速发展,水冷燃烧器、多孔陶瓷板燃烧器、金属纤维/丝网燃烧器,火焰均匀稳定,调节比可达1:5以上,火焰温度低于1100℃,氮氧化物排放低于30mg,符合最新的环保标准,广泛应用于燃气热水锅炉和燃气壁挂炉等小型燃气锅炉,但还未进入承压燃气锅炉市场。平面/曲面燃烧器为表面燃烧器,火焰悬浮在面板上方200mm的空间内,不需要巨大的炉膛空间,只需利用锅炉的一面炉墙即可布置燃烧器,为此需要设计一种全新的炉型来匹配平面/曲面燃烧器。缩小炉膛空间,强化换热,合理布置不同温度下的受热面,同时保证锅炉承压能力和维修保养的便利性,因此需要开发匹配平面/曲面燃烧器的紧凑高效锅炉。
cn201821004317.2公开了一种低氮不锈钢冷凝热水锅炉,炉膛由上向下布置,火焰依次经过一级换热器和二级冷凝换热器,所用燃烧器为矩形平面燃烧器,不同层级之间的水通过前后水室连通转弯。该型锅炉是一种适配平面燃烧器的热水锅炉,炉膛空间小,换热元件紧凑,但没有承压能力,无法生成蒸汽。cn201621007598.8公开了一种低氮燃烧的蒸汽锅炉,由炉膛、上下锅炉腔、燃烧器等组成,炉膛包括水冷壁、用于降低火焰温度的第一水冷管、进行辐射换热的第二水冷管、用于对流换热的第三水冷管。内部采用多排的错列光管,烟气侧一但结垢则难以清洗,用于冷却火焰的水冷管束易积碳堵塞,也需定期清洗,炉体维修不便。
目前市场上缺少适配平面/曲面燃烧器的便于检修的承压燃气锅炉,为此开发新型立式水管锅炉。
技术实现要素:
为了实现平面/曲面燃烧器的机炉一体化,开发便于检修、维护,体积紧凑,实现低氮冷凝的可承压天然气锅炉,本发明的目的在于提供一种圆柱形低氮高效承压水管锅炉,采用上下封头和中间立式水管、圆柱形外壳的锅炉本体结构,配合可拆卸平面/曲面燃烧器、外置冷凝换热器。中间的立式水管包括水冷壁管束、水冷火焰管束、辐射管束、高温对流管束和低温对流管束五个分区;外壳连接上下椭球/球型封头并包覆这水冷壁管束;减少了锅炉本体散热损失;全水管换热,并随烟温变化优化水管的排布,提高平均换热系数。
为了达到上述目的,本专利采用如下技术方案:
一种圆柱形低氮节能承压水管锅炉,包括上封头1、外壳2、燃烧器分配头3、膜式水冷壁管束4、水冷火焰管束5、辐射管束6、高温对流管束7、低温对流管束8、下降管束9、下封头10、外置冷凝器11、预混合器12以及配套的风机、给水泵、燃气阀组、控制器;所述膜式水冷壁管束4、水冷火焰管束5、辐射管束6、高温对流管束7、低温对流管束8、下降管束9均连接于上封头1和下封头10之间;所述膜式水冷壁管束4包围着辐射管束6、高温对流管束7和低温对流管束8,通过扁钢与水冷火焰管束5的左右两端管相连,膜式水冷壁管束4与上封头1和下封头10共同组成了约束烟气流通的壁面;外壳2包覆着除外置冷凝器11和预混合器12外的所有部件形成的锅炉本体,仅露出燃烧器分配头3的入口部分以及锅炉本体与外置冷凝器11的连接部分;膜式水冷壁管束4、水冷火焰管束5、辐射管束6、高温对流管束7、低温对流管束8和下降管束9的上下两端分别与上封头1和下封头10连通;预混合器12出口连通燃烧器分配头3入口,燃烧器分配头3与水冷火焰管束5紧临;外置冷凝器11与锅炉本体的出口烟道相连且外置冷凝器11的管侧出口连接上锅筒1的补水口;预混合器12出口的天然气和空气的混合气体先进入燃烧器分配头3,从燃烧器分配头3均匀分配进入水冷火焰管束5,在水冷火焰管束5的前方表面点火燃烧,生成的高温烟气依次经过辐射管束6、高温对流管束7、低温对流管束8,最后进入外置冷凝器11;锅炉给水先进入外置冷凝器11管侧预热,随后进入上封头1的补水口,通过上封头1分配到各个管束区,进入下封头10;管束中的水受热生成蒸汽,蒸汽向上流动从上封头1离开锅炉;上封头1的上方区域为汽空间,下方区域为水空间,下封头则为水空间。
所述上封头1和下封头10作为承压件,选用球形封头型和椭球形封头型两种;所述球形封头型包括球形封头、圆柱段和管板三部分;所述椭球形封头型包括椭球形封头、圆柱段和管板三部分;所述下封头10与上封头1的主体结构相同;上封头1布置汽水分离器、多个法兰接口,用以进水、排汽、检修,安装压力表、温度表、水位计和安全阀;下封头10布置多个法兰接口,用以检修、排污,测量温度和压力。
所述外壳2和膜式水冷壁管束4之间填充隔热材料,或留出空腔,降低锅炉本体散热损失;外壳2与上封头1和下封头10管板的边缘焊接,起到拉撑作用,作为管板强度计算时的支点线;外壳2上留出预混气体入口、烟气出口、检修孔、观火孔和测点孔。
所述燃烧器分配头3由预混气体入口3-1、风壳3-2、均流孔板3-4和燃烧面3-5四部分组成;所述燃烧面3-5采用平面或曲面形式,与水冷火焰管束5贴合;预混气体入口3-1与燃烧面3-5平行或垂直或成任意角度,平行时风壳3-2为渐扩段,垂直时风壳3-2为侧面进气的等压风道;均流孔板3-4位于风壳3-2内的预混气体入口3-1到燃烧面3-5之间,为一层或多层,使燃烧面3-5上各个位置的预混气体流量均匀;燃烧面3-5采用金属孔板、多孔陶瓷板、密排布置的矩形管、密排布置的螺旋翅片管、密排布置的圆管五种结构中的一种;金属孔板和多孔陶瓷板上的小孔以及密排布置的矩形管、螺旋翅片管和圆管之间的缝隙都起到防回火、均流气体、稳焰的作用;预混气体在水冷火焰管束5的缝隙之后着火,因此燃烧面3-5未受到火焰的直接冲击,仅有少量辐射热,并持续受到室温预混气体的冷却;密排布置管与大气直接连通,管内气体受热后上升,形成空气自然循环冷却密排布置管;密排布置管利用炉水冷却;密排布置管设置上集箱3-5-1和下集箱3-5-2,外置烟气冷凝器11出口的锅炉给水先进入下集箱3-5-2,沿密排布置管上升流动至上集箱3-5-1,随后进入下封头10。
所述燃烧器分配头3还包括位于风壳3-2内的预混气体入口3-1到燃烧面3-5之间的一层或多层导流板3-3,使燃烧面3-5上各个位置的预混气体流量更加均匀;
所述的燃烧器分配头3为可拆卸式;燃烧器分配头3利用抽屉方式与水冷火焰管束5实现连接和密封,通过外壳2上的开口2-1放入锅炉内,并在锅炉内预设导轨的约束下实现固定;燃烧器分配头3的边框与导轨内的凹槽面实现密封,加入密封条提升密封效果;燃烧器分配头低负荷时可能出现积碳,可拆卸式的燃烧器分配头3方便清洗,更易实现长周期安全运行。
所述膜式水冷壁管束4、水冷火焰管束5、辐射管束6、高温对流管束7、低温对流管束8的整体排布形状包括矩形、梯形、曲边梯形;采用矩形排布时,烟道宽度不变;采用梯形排布时,水冷火焰管束5处的烟道最宽,沿烟气流动方向烟道不断变窄,提高烟气流速;采用曲边梯形排布时,烟道宽度先增大后减小,高温对流管束7处最宽,充分利用圆柱状外壳的空间,降低辐射管束6、高温对流管束7的热负荷,降低管内结垢风险,随后缩小烟道宽度以提高烟气流速,增大换热系数,减少管束使用量。
所述燃烧器分配头3、水冷火焰管束5采用凸形排布,以增大燃烧表面积;锅炉功率增大时,需等比增大燃烧器面积,锅炉高度受运输和锅炉房限高影响,增加幅度有限,封头、锅筒直径受加工能力和筒体强度的制约,锅炉直径增加有限,此时凸形布置在不改变锅炉宽度和高度的情况下,增加燃烧表面积,增大锅炉功率;采用凸形布置时,将燃烧表面布置成深入炉膛空间的梯形、三角形或具有尖锐凸起的曲面,同时改变水冷火焰管束5和辐射管束6的布置,以冷却火焰,屏蔽燃烧面之间的热辐射。
所述膜式水冷壁管束4采用外径25~76mm的光管相切焊接或光管和10~60mm扁钢间隔排列焊接或鳍片管中间焊接构成,采用光管相切则连接上封头1和下封头10的管端应该缩颈以维持最低要求的孔桥尺寸,点火针、检火针、观火孔布置在水冷火焰管束5与膜式水冷壁管束4之间的扁钢处,用以引燃预混气体并检测观察火焰;所述水冷火焰管束5采用外径25~60mm光管,管束间距1mm~20mm,缠绕翅片高度低于10mm的螺旋翅片,管束表面距燃烧器分配头3表面小于20mm,以避免预混气体在燃烧器分配头3和水冷火焰管束5之间的缝隙处着火;预混气体离开水冷火焰管束5的缝隙后点火燃烧,水冷火焰管束5吸收火焰的辐射热并冷却火焰根部,从而在过量空气系数小于1.3的条件下实现折算氮氧化物低于30mg;水冷火焰管束5长期受高温火焰冲刷,停炉时表面易生成冷凝水,需要防高温腐蚀和低温腐蚀,如果采用不锈钢则面临着异种钢焊接问题,因此采用表面喷镀镍铬合金的方式,提高耐腐蚀性能;所述辐射管束6采用外径51~200mm的大直径管,辐射管束区吸收了锅炉40%以上的热量,烟温高于900℃,蒸发强烈,采用大直径管避免蒸汽堵塞造成的流动停滞;所述高温对流管束7区域烟气温度900~600℃,以对流换热为主,采用外径25~76mm的管子,选用光管或翅片管,翅片管的翅片高度小于10mm,以避免翅片超温损毁;所述低温对流管束8和外置冷凝换热器11区域的换热温差小,需要采取强化换热措施,包括密排光管、螺旋翅片管、鳍片管、针翅管方式;所述下降管束9位于水冷壁管束4之外,上封头1和下封头10之间,不受热,多布置于水冷火焰管束5、辐射管束6、高温对流管束7附近,这几个管束区的热流密度大,水蒸发强烈,对应的下封头10区域需要补充大量的水,设置下降管束9避免该管束区出现流动停滞带来的传热恶化问题。
所述外置冷凝器11为水管式换热器,换热管束均为光管11-2,减少烟气侧积垢;蒸汽锅炉的给水量远少于热水锅炉,为确保换热器内水侧流速达到0.3m/s以上,需将数根光管分为一组,采用水室11-3连接各组光管;水室11-3位于光管11-2两侧,内有上下各组水管的分隔板,水在各组管中折返流动,水室11-3采用法兰盲板11-4密封,能够打开清洗水侧污垢;出口11-5位于外置冷凝器11的上部,方便水流及时带走换热器内堆积的气泡;由于水室11-3的承压能力较弱,因此将给水泵位于外置冷凝器11之后,确保外置冷凝器11中不承压或仅承微压;外置冷凝器11采用304以上级别的奥氏体不锈钢或430以上级别的铁素体不锈钢以减少冷凝水的腐蚀。
所述预混合器12为燃烧器分配头3提供预混气体,与燃烧器分配头3的预混气体入口相连;预混合器12由圆柱形外壳12-1、同轴圆柱形套筒12-2、中心气管12-3和整流板12-4四部分组成;同轴圆柱形套筒12-2占预混合器轴向总长的20%~60%,靠近预混合器空气入口一侧,将预混合器分为套筒内和套筒外两部分,两部分的面积相同;中心气管12-3位于同轴圆柱形套筒12-2的前端,整流板12-4位于预混合器12的出口侧;空气沿预混合器12的轴线方向流动,天然气穿过圆柱形外壳12-2进入同轴圆柱形套筒12-2内空间,同轴圆柱形套筒12-2与中心气管12-3连通,同轴圆柱形套筒12-2的内侧和外侧、中心气管12-3的下表面开有轴线与所在表面倾斜的小孔,天然气从倾斜的小孔喷出形成旋转射流,使燃气与空气在旋转搅拌的作用下充分混合,同轴圆柱形套筒12-2的内侧和外侧旋流的方向同向或异向,出口侧的整流板12-4用于消除预混气体的旋转;整流板12-4为十字板型,米字板型或平行板型。
本发明创新点、优点和积极效果是:
1、本发明的一种圆柱形低氮高效承压水管锅炉采用机炉一体化的设计理念,将平面/曲面燃烧器与承压锅炉结合到一起,摈弃了传统大炉膛的结构;全膜式壁包覆,减少了锅炉本体散热损失;全水管换热,并随烟温变化优化水管的排布,提高平均换热系数。
2、本发明的一种圆柱形低氮高效承压水管锅炉的平面/曲面燃烧器采用水冷降氮的原理,利用锅炉本体受热面的一部分作为燃烧器的水冷火焰管束,解决了水冷低氮的热量分配难题,在过量空气系数小于1.3的条件下实现了排放氮氧化物不高于30mg的目标。
3、本发明的一种圆柱形低氮高效承压水管锅炉采用抽屉式可拆卸燃烧器分配头,避免了传统水冷低氮燃烧器因无法拆卸导致的长期运行时因积碳堵塞而报废的问题。
4、本发明的一种圆柱形低氮高效承压水管锅炉优化了燃烧平面/曲面和辐射管束的排布,采用凸型布置,最大化利用炉膛空间,增大给定炉膛宽度下的燃烧器功率。
5、本发明的一种圆柱形低氮高效承压水管锅炉采用全光管冷凝器,减少烟气侧结垢并方便清洗,水侧采用水室连接各根光管,且水室可以打开清洗,避免了传统冷凝换热器烟气侧和水侧结垢堵塞难以清洗的问题。
附图说明
图1是本发明一种圆柱形低氮节能承压水管锅炉的剖面示意图。
图2a是上封头为椭球形的示意图;图2b是上封头为球型的示意图。
图3a是燃烧器分配头各部分的示意图;图3b是抽屉式连接方式的示意图;图3c是燃烧器分配头剖面图的示意图。
图4a是膜式水冷壁管束、水冷火焰管束、辐射管束、高温对流管束和低温对流管束梯形排布示意图;图4b是膜式水冷壁管束、水冷火焰管束、辐射管束、高温对流管束和低温对流管束曲边梯形排布示意图。
图5是本发明一种圆柱形低氮节能承压水管锅炉的燃烧器分配头、水冷火焰管束采用凸形排布的示意图。
图6是本发明一种圆柱形低氮节能承压水管锅炉的外置冷凝器的示意图。
图7a是本发明一种圆柱形低氮节能承压水管锅炉的预混合器的横剖面示意图;图7b是本发明一种圆柱形低氮节能承压水管锅炉的预混合器的立体示意图。
具体实施方式
下面结合附图和具体实施方式对专利进行详细说明。
如图1所示,本发明一种圆柱形低氮节能承压水管锅炉,包括上封头1、外壳2、燃烧器分配头3、膜式水冷壁管束4、水冷火焰管束5、辐射管束6、高温对流管束7、低温对流管束8、下降管束9、下封头10、外置冷凝器11、预混合器12以及配套的风机、给水泵、燃气阀组、控制器;所述膜式水冷壁管束4、水冷火焰管束5、辐射管束6、高温对流管束7、低温对流管束8、下降管束9均连接于上封头1和下封头10之间;所述膜式水冷壁管束4包围着辐射管束6、高温对流管束7和低温对流管束8,通过扁钢与水冷火焰管束5的左右两端管相连,膜式水冷壁管束4与上封头1和下封头10共同组成了约束烟气流通的壁面;外壳2包覆着除外置冷凝器11和预混合器12外的所有部件形成的锅炉本体,仅露出燃烧器分配头3的入口部分以及锅炉本体与外置冷凝器11的连接部分;膜式水冷壁管束4、水冷火焰管束5、辐射管束6、高温对流管束7、低温对流管束8和下降管束9的上下两端分别与上封头1和下封头10连通;预混合器12出口连通燃烧器分配头3入口,燃烧器分配头3与水冷火焰管束5紧临;外置冷凝器11与锅炉本体的出口烟道相连且外置冷凝器11的管侧出口连接上锅筒1的补水口;预混合器12出口的天然气和空气的混合气体先进入燃烧器分配头3,从燃烧器分配头3均匀分配进入水冷火焰管束5,在水冷火焰管束5的前方表面点火燃烧,生成的高温烟气依次经过辐射管束6、高温对流管束7、低温对流管束8,最后进入外置冷凝器11;锅炉给水先进入外置冷凝器11管侧预热,随后进入上封头1的补水口,通过上封头1分配到各个管束区,进入下封头10;管束中的水受热生成蒸汽,蒸汽向上流动从上封头1离开锅炉;上封头1的上方区域为汽空间,下方区域为水空间,下封头则为水空间。
作为本发明的优选实施方式,所述上封头1和下封头10作为承压件,选用球形封头型和椭球形封头型两种;如图2b所示,所述球形封头型包括球形封头、圆柱段和管板三部分;如图2a所示,所述椭球形封头型包括椭球形封头、圆柱段和管板三部分;所述下封头10与上封头1的主体结构相同;上封头1布置汽水分离器、多个法兰接口,用以进水、排汽、检修,安装压力表、温度表、水位计和安全阀;下封头10布置多个法兰接口,用以检修、排污,测量温度和压力。
作为本发明的优选实施方式,所述外壳2和膜式水冷壁管束4之间填充隔热材料,或留出空腔,降低锅炉本体散热损失;外壳2与上封头1和下封头10管板的边缘焊接,起到拉撑作用,作为管板强度计算时的支点线;外壳2上留出预混气体入口、烟气出口、检修孔、观火孔和测点孔。
如图3a、图3b、图3c所示,所述燃烧器分配头3由预混气体入口3-1、风壳3-2、均流孔板3-4和燃烧面3-5四部分组成;所述燃烧面3-5采用平面或曲面形式,与水冷火焰管束5贴合;预混气体入口3-1与燃烧面3-5平行或垂直或成任意角度,平行时风壳3-2为渐扩段,垂直时风壳3-2为侧面进气的等压风道;均流孔板3-4位于风壳3-2内的预混气体入口3-1到燃烧面3-5之间,为一层或多层,使燃烧面3-5上各个位置的预混气体流量均匀;燃烧面3-5采用金属孔板、多孔陶瓷板、密排布置的矩形管、密排布置的螺旋翅片管、密排布置的圆管五种结构中的一种;金属孔板和多孔陶瓷板上的小孔以及密排布置的矩形管、螺旋翅片管和圆管之间的缝隙都起到防回火、均流气体、稳焰的作用;预混气体在水冷火焰管束5的缝隙之后着火,因此燃烧面3-5未受到火焰的直接冲击,仅有少量辐射热,并持续受到室温预混气体的冷却;密排布置管与大气直接连通,管内气体受热后上升,形成空气自然循环冷却密排布置管;密排布置管利用炉水冷却;密排布置管设置上集箱3-5-1和下集箱3-5-2,外置烟气冷凝器11出口的锅炉给水先进入下集箱3-5-2,沿密排布置管上升流动至上集箱3-5-1,随后进入下封头10。
如图3c所示,所述燃烧器分配头3还包括位于风壳3-2内的预混气体入口3-1到燃烧面3-5之间的一层或多层导流板3-3,使燃烧面3-5上各个位置的预混气体流量更加均匀。
如图3b所示,所述的燃烧器分配头3为可拆卸式;燃烧器分配头3利用抽屉方式与水冷火焰管束5实现连接和密封,通过外壳2上的开口2-1放入锅炉内,并在锅炉内预设导轨的约束下实现固定;燃烧器分配头3的边框与导轨内的凹槽面实现密封,加入密封条提升密封效果;燃烧器分配头低负荷时可能出现积碳,可拆卸式的燃烧器分配头3方便清洗,更易实现长周期安全运行。
所述膜式水冷壁管束4、水冷火焰管束5、辐射管束6、高温对流管束7、低温对流管束8的整体排布形状包括矩形、梯形、曲边梯形;采用矩形排布时,烟道宽度不变;如图4a所示,采用梯形排布时,水冷火焰管束5处的烟道最宽,沿烟气流动方向烟道不断变窄,提高烟气流速;如图4b所示,采用曲边梯形排布时,烟道宽度先增大后减小,高温对流管束7处最宽,充分利用圆柱状外壳的空间,降低辐射管束6、高温对流管束7的热负荷,降低管内结垢风险,随后缩小烟道宽度以提高烟气流速,增大换热系数,减少管束使用量。
如图5所示,所述燃烧器分配头3、水冷火焰管束5采用凸形排布,以增大燃烧表面积;锅炉功率增大时,需等比增大燃烧器面积,锅炉高度受运输和锅炉房限高影响,增加幅度有限,封头、锅筒直径受加工能力和筒体强度的制约,锅炉直径增加有限,此时凸形布置在不改变锅炉宽度和高度的情况下,增加燃烧表面积,增大锅炉功率;采用凸形布置时,将燃烧表面布置成深入炉膛空间的梯形、三角形或具有尖锐凸起的曲面,同时改变水冷火焰管束5和辐射管束6的布置,以冷却火焰,屏蔽燃烧面之间的热辐射。
作为本发明的优选实施方式,所述膜式水冷壁管束4采用外径25~76mm的光管相切焊接或光管和10~60mm扁钢间隔排列焊接或鳍片管中间焊接构成,采用光管相切则连接上封头1和下封头10的管端应该缩颈以维持最低要求的孔桥尺寸,点火针、检火针、观火孔布置在水冷火焰管束5与膜式水冷壁管束4之间的扁钢处,用以引燃预混气体并检测观察火焰;所述水冷火焰管束5采用外径25~60mm光管,管束间距1mm~20mm,缠绕翅片高度低于10mm的螺旋翅片,管束表面距燃烧器分配头3表面小于20mm,以避免预混气体在燃烧器分配头3和水冷火焰管束5之间的缝隙处着火;预混气体离开水冷火焰管束5的缝隙后点火燃烧,水冷火焰管束5吸收火焰的辐射热并冷却火焰根部,从而在过量空气系数小于1.3的条件下实现折算氮氧化物低于30mg;水冷火焰管束5长期受高温火焰冲刷,停炉时表面易生成冷凝水,需要防高温腐蚀和低温腐蚀,如果采用不锈钢则面临着异种钢焊接问题,因此采用表面喷镀镍铬合金的方式,提高耐腐蚀性能;所述辐射管束6采用外径51~200mm的大直径管,辐射管束区吸收了锅炉40%以上的热量,烟温高于900℃,蒸发强烈,采用大直径管避免蒸汽堵塞造成的流动停滞;所述高温对流管束7区域烟气温度900~600℃,以对流换热为主,采用外径25~76mm的管子,选用光管或翅片管,翅片管的翅片高度小于10mm,以避免翅片超温损毁;所述低温对流管束8和外置冷凝换热器11区域的换热温差小,需要采取强化换热措施,包括密排光管、螺旋翅片管、鳍片管、针翅管方式;所述下降管束9位于水冷壁管束4之外,上封头1和下封头10之间,不受热,多布置于水冷火焰管束5、辐射管束6、高温对流管束7附近,这几个管束区的热流密度大,水蒸发强烈,对应的下封头10区域需要补充大量的水,设置下降管束9避免该管束区出现流动停滞带来的传热恶化问题。
如图6所示,所述外置冷凝器11为水管式换热器,换热管束均为光管11-2,减少烟气侧积垢;蒸汽锅炉的给水量远少于热水锅炉,为确保换热器内水侧流速达到0.3m/s以上,需将数根光管分为一组,采用水室11-3连接各组光管;水室11-3位于光管11-2两侧,内有上下各组水管的分隔板,水在各组管中折返流动,水室11-3采用法兰盲板11-4密封,能够打开清洗水侧污垢;出口11-5位于外置冷凝器11的上部,方便水流及时带走换热器内堆积的气泡;由于水室11-3的承压能力较弱,因此将给水泵位于外置冷凝器11之后,确保外置冷凝器11中不承压或仅承微压;外置冷凝器11采用304以上级别的奥氏体不锈钢或430以上级别的铁素体不锈钢以减少冷凝水的腐蚀。
如图7所示,所述预混合器12为燃烧器分配头3提供预混气体,与燃烧器分配头3的预混气体入口相连;预混合器12由圆柱形外壳12-1、同轴圆柱形套筒12-2、中心气管12-3和整流板12-4四部分组成;同轴圆柱形套筒12-2占预混合器轴向总长的20%~60%,靠近预混合器空气入口一侧,将预混合器分为套筒内和套筒外两部分,两部分的面积相同;中心气管12-3位于同轴圆柱形套筒12-2的前端,整流板12-4位于预混合器12的出口侧;空气沿预混合器12的轴线方向流动,天然气穿过圆柱形外壳12-2进入同轴圆柱形套筒12-2内空间,同轴圆柱形套筒12-2与中心气管12-3连通,同轴圆柱形套筒12-2的内侧和外侧、中心气管12-3的下表面开有轴线与所在表面倾斜的小孔,天然气从倾斜的小孔喷出形成旋转射流,使燃气与空气在旋转搅拌的作用下充分混合,同轴圆柱形套筒12-2的内侧和外侧旋流的方向同向或异向,出口侧的整流板12-4用于消除预混气体的旋转;整流板12-4为十字板型,米字板型或平行板型。
起点商标作为专业知识产权交易平台,可以帮助大家解决很多问题,如果大家想要了解更多知产交易信息请点击 【在线咨询】或添加微信 【19522093243】与客服一对一沟通,为大家解决相关问题。
此文章来源于网络,如有侵权,请联系删除


