一种蒸汽流量与加热功率协同作用的锅炉系统的制作方法



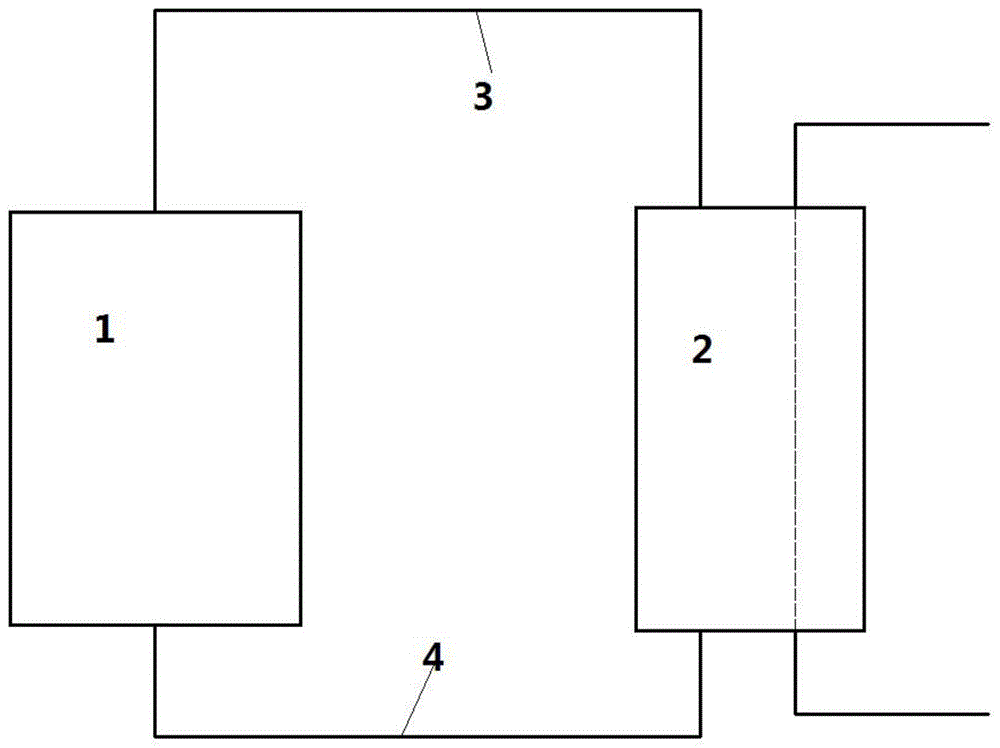
本发明涉及一种蒸发器技术,尤其涉及一种智能启动的锅炉系统。
背景技术:
锅炉是利用燃料或其他能源的热能把水加热成为蒸汽的机械设备。锅炉应用领域广泛,广泛适用于制衣厂,干洗店,饭店,馍店,食堂,餐厅,厂矿,豆制品厂等场所。
目前的锅炉多采用燃气或者燃油加热,而且加热效率低,而对于利用余热的锅炉研究的不是很多。
现有的锅炉产出效率低,智能化程度不高,因此需要设计一种根据进行智能控制的烟气余热的锅炉。
针对上述问题,本发明在前面发明的基础上进行了改进,提供了一种新的结构的锅炉,充分利用热源,降低能耗,实现智能控制。
技术实现要素:
针对上述问题,本发明在前面发明的基础上进行了改进,提供了一种新的智能锅炉系统,以实现热量的充分利用。
为了实现上述目的,本发明的技术方案如下:
一种锅炉系统,包括锅炉和换热器,锅炉产生的蒸汽通过蒸汽管路进入换热器中,与进入换热器中的空气进行热交换,所述锅炉包括电加热部件、汽箱,所述电加热部件设置在汽箱中,所述汽箱包括进水管和蒸汽出口,所述蒸汽出口管路上设置流量传感器,用于测量单位时间产出的蒸汽流量,所述流量传感器与控制器数据连接。所述控制器根据流量传感器测量的单位时间产出的蒸汽流量数据来自动控制电加热器的加热功率的大小;
如果测量的蒸汽流量低于一定的数值,则控制器控制电加热器的加热功率增加;如果流量传感器测量的流量高于一定的数值,则控制器控制控制器控制电加热器的加热功率的降低。
作为优选,所述电加热部件包括第一集管、第二集管和盘管,盘管与第一集管和第二集管相连通,形成加热流体封闭循环,电加热器设置在第一集管内;第一集管内填充相变流体;盘管为一个或者多个,每个盘管包括多根圆弧形的热交换管,多根圆弧形的热交换管的中心线为以第一集管为同心圆的圆弧,相邻热交换管的端部连通,从而使得热交换管的端部形成热交换管自由端;沿着高度方向电加热器设置为多段,每段独立控制,随着时间的变化,在半个周期t/2内,电加热器的沿着高度方向从下端开始依次启动,直到全部段都启动,然后在后面的半个周期t/2内,从上端开始依次关闭,直到周期结束,全部段关闭。
与现有技术相比较,本发明具有如下的优点:
1、本发明设置了根据蒸汽输出量智能控制电加热器功率大小,可以根据蒸汽输出量智能控制加热功率大小,从而根据实际情况实现加热器和锅炉出口蒸汽温度之间的协同换热功能,以满足实际工作需求。
2、本发明设计了一种新式结构的电加热部件在汽箱中的布局图,可以进一步提高加热效率。
3、本发明电加热部件在周期内间歇式的加热,能够实现弹性盘管周期性的频繁性的振动,从而实现很好的除垢以及加热效果。
4、本发明将盘管周期性不断增加加热功率以及降低加热功率,使得加热流体受热后会产生体积不停的处于变化状态中,诱导盘管自由端产生振动,从而强化传热。
5、本发明通过大量的实验和数值模拟,优化了盘管的参数的最佳关系,从而实现最优的加热效率。
附图说明
图1是本发明锅炉系统的结构示意图。
图2是本发明锅炉系统控制结构的示意图。
图3为本发明电加热锅炉的电加热部件的俯视图。
图4为电加热部件的主视图。
图5是电加热部件间隙式加热的坐标示意图。
图6是电加热部件周期性增加以及降低加热功率坐标示意图。
图7是电加热部件周期性增加以及降低加热功率的另一个实施例坐标示意图。
图8是电加热部件加热功率线性变化的坐标示意图。
图9是圆形汽箱中设置电加热部件的布局示意图。
图10是盘管结构示意图。
图11是汽箱结构示意图。
图中:1、锅炉,2、换热器,3、蒸汽管道,4、回水管道,5、风机,6、传感器,7控制器,8、盘管,9、第一集管,10、自由端,11、自由端,12、进水管,13、蒸汽出口,14、自由端,15、第二集管,16、连接点,17、电加热部件,18、汽箱,19热交换管,20电加热器
具体实施方式
下面结合附图对本发明的具体实施方式做详细的说明。
本文中,如果没有特殊说明,涉及公式的,“/”表示除法,“×”、“*”表示乘法。
下面结合附图对本发明的具体实施方式做详细的说明。
一种蒸汽锅炉系统,如图1所示,所述系统包括锅炉1和换热器2,所述锅炉1产生蒸汽。所述蒸汽通过蒸汽管道3进入换热器2中。在换热器中与进入换热器中的空气进行热交换,然后通过回水管路4返回到锅炉中继续加热。所述空气通过风机5进入热交换器2。
通过上述结构,锅炉中产生的蒸汽进入热交换器,加热交换器中的空气,从而形成热空气。
作为一个改进,所述蒸汽管路3设置流动检测器6,用于检测是否具有蒸汽流过,所述流动监测器6、风机5与控制器7数据连接,所述控制器根据流动监测器检测的数据来自动控制风机的启动和关闭。
作为优选,所述控制器根据流动监测器检测的数据来自动控制风机的启动和关闭包括如下步骤:
1)流动检测器检测蒸汽是否流过,并将检测数据传递给控制器;
2)控制器根据检测的数据,判断蒸汽是否流过;
3)控制器根据判断的结果,控制风机是否启动。
作为优选,控制器判断有蒸汽流过时,控制风机启动,从而使得空气进入换热器进行换热,控制器判断没有蒸汽流过时,控制风机关闭。
通过上述的方法,可以根据蒸汽流动智能控制风机启动,从而根据实际情况实现换热器和锅炉之间的协同换热功能,以满足实际工作需求。这样可以充分利用热量,避免过多的热量的浪费。
作为一个改进,所述蒸汽管路3设置流量传感器,用于检测是蒸汽流量大小,所述流量传感器、风机5与控制器7数据连接,所述控制器根据流量监测器检测的数据来自动控制风机的频率。
作为优选,所述控制器根据流量传感器检测的数据来自动控制风机的频率包括如下步骤:
1)流量传感器检测蒸汽的流量,并将检测数据传递给控制器;
2)控制器根据检测的数据,进行判断流量的变化;
3)控制器根据判断的结果,控制风机的频率。
作为优选,控制器判断流量增加时,控制风机频率增加,从而使得更多空气进入换热器进行换热,控制器判断流量减小时,控制风机频率减小,从而使得更少空气进入换热器进行换热。
通过上述的方法,可以根据蒸汽流量智能控制风机频率大小,从而根据实际情况实现换热器和锅炉之间的协同换热功能,以满足实际工作需求。这样可以充分利用热量,避免过多的热量的浪费。
作为另一个改进,可以根据检测的蒸汽的流量以及蒸汽温度、压力自动控制风机的频率。
所述蒸汽管路3设置流量传感器,用于检测是蒸汽流量流量大小,蒸汽管路设置温度传感器和压力传感器,用于检测蒸汽的温度和压力,所述流量传感器、温度传感器、风机5与控制器7数据连接,所述控制器根据流量监测器、温度传感器、压力传感器检测的数据来自动控制风机的频率。
作为优选,所述控制器根据流量传感器、温度传感器、压力传感器检测的数据来自动控制风机的频率包括如下步骤:
1)流量传感器检测蒸汽的流量、蒸汽温度、压力,并将检测数据传递给控制器;
2)控制器根据检测的数据,进行判断蒸汽总体热量的变化;
3)控制器根据判断的结果,控制风机的频率。
作为优选,控制器判断蒸汽总体热量增加时,控制风机频率增加,从而使得更多空气进入换热器进行换热,控制器判断总体热量减小时,控制风机频率减小,从而使得更少空气进入换热器进行换热。
所述总体热量通过调取存取在控制器中的数据库来计算水蒸气与空气所要达到的加热温度之间的温差所含的热量。例如热力学中的水蒸气温度压力焓表。
通过上述的方法,可以根据蒸汽流量智能控制风机频率大小,从而根据实际情况实现换热器和锅炉之间的协同换热功能,以满足实际工作需求。这样可以充分利用热量,避免过多的热量的浪费。
作为优选,所述锅炉包括电加热部件17、汽箱18,所述电加热部件17设置在汽箱18中,所述汽箱18包括进水管12和蒸汽出口13。蒸汽出口13设置在汽箱上部。
作为优选,所述汽箱是圆柱形结构。
图3展示了电加热部件17的俯视图,如图3所示,所述电加热部件17包括第一集管9、第二集管15和盘管8,盘管8与第一集管9和第二集管15相连通,流体在第一集管9和第二集管15以及盘管8内进行封闭循环,所述电加热部件17内设置电加热器20,所述电加热器20用于加热电加热部件17的内流体,然后通过加热的流体来加热汽箱内的水。
如图3-4所示,电加热器20设置在第一集管9内;第一集管9内填充相变流体;盘管8为一个或者多个,每个盘管8包括多根圆弧形的热交换管19,多根圆弧形的热交换管19的中心线为以第一集管9为同心圆的圆弧,相邻热交换管19的端部连通,流体在第一集管9和第二集管15之间形成串联流动,从而使得热交换管的端部形成热交换管自由端10、4;所述流体是相变流体,汽液相变液体,所述电加热部件与控制器进行数据连接,所述控制器控制电加热部件的加热功率随着时间的变化而周期性发生变化。
作为优选,所述第一集管9和第二集管15沿着高度方向上设置。
研究以及实践中发现,持续性的功率稳定性的电加热器的加热会导致内部电加热部件的流体形成稳定性,即流体不在流动或者流动性很少,或者流量稳定,导致盘管8振动性能大大减弱,从而影响盘管8的除垢以及加热的效率。因此需要对上述电加热盘管进行如下改进。
作为一个优选,加热功率采取间歇式的加热方式。
如图5所示,在一个周期时间t内,电加热器的加热功率p变化规律如下:
0-t/2的半个周期内,p=n,其中n为常数数值,单位为瓦(w),即加热功率保持恒定;
t/2-t的半个周期内,p=0。即电加热器不加热。
t是50-80分钟,其中4000w<n<5000w。
通过上述的时间变化性的进行加热,可以使得流体在弹性热交换管内频繁的蒸发膨胀以及收缩,从而不断的带动弹性热交换管的振动,从而能够进一步实现加热效率以及除垢操作。
作为一个优选,所述电加热器20设置为多个,每个电加热器独立控制,随着时间的变化,电加热器启动的数量进行周期性变化。
作为一个优选,电加热器为n个,则在一个周期t内,每隔t/2n的时间,启动一个电加热器,直到t/2时间加热器全部启动,然后再每隔t/2n的时间,关闭一个电加热器,直到t时间加热器全部关闭。
作为优选,每个电加热器加热功率都相同。关系图如图4所示。
通过上述的时间变化性的进行加热,可以使得流体在弹性热交换管内频繁的蒸发膨胀以及收缩,从而不断的带动弹性热交换管的振动,从而能够进一步实现加热效率以及除垢操作。
作为优选,沿着高度方向电加热器设置为多段,每段独立控制,随着时间的变化,在半个周期t/2内,电加热器的沿着高度方向从下端开始依次启动,直到全部段都启动,然后在后面的半个周期t/2内,从上端开始依次关闭,直到周期结束,全部段关闭。
即假设电加热器为n段,则在一个周期t内,每隔t/2n的时间,从下端开始启动一个段,直到t/2时间所有段全部启动,然后再每隔t/2n的时间,从上端开始,关闭一个段,直到t时间全部段关闭。
作为优选,每个段加热功率都相同。关系图如图4所示。
通过电加热器从下部向上逐渐启动,可以使得下部流体充分加热,形成一个很好的自然对流,进一步促进流体的流动,增加弹性振动效果。通过上述的时间变化性的加热功率的变化,可以使得流体在弹性热交换管内频繁的蒸发膨胀以及收缩,从而不断的带动弹性热交换管的振动,从而能够进一步实现加热效率以及除垢操作。
作为优选,所述电加热器20为多个,每个电加热器20功率不同,可以一个或者多个组合形成不同的加热功率,在上半个周期内,按照时间循序,先是单个电加热器启动,单个电加热器按照加热功率依次增加的顺序独立启动,然后再启动两个电加热器,两个电加热器按照加热功率依次增加的顺序独立启动,然后再逐渐增加电加热部件启动的数量,如果数量为n,则n个电加热器按照加热功率依次增加的顺序独立启动;直到最后所有的电加热器启动,保证所述电加热部件的加热功率依次增加。在下半个周期内,先是单个电加热器不启动,单个电加热器按照加热功率依次增加的顺序独立不启动,然后再不启动两个电加热器,两个电加热器按照加热功率依次增加的顺序独立不启动,然后再逐渐增加电加热部件不启动的数量,如果数量为n,则n个电加热器按照加热功率依次增加的顺序独立不启动;直到最后所有的电加热器不启动,保证所述电加热器的加热功率依次降低。
例如所述电加热部件为三个,分别是第一电加热部件d1、第二电加热部件d2和第三电加热部件d3,加热功率分别为p1,p2和p3,其中p1<p2<p3,p1+p2>p3;即其中第一电加热部件、第二电加热部件之和大于第三电加热部件,按照时间顺序依次启动第一,第二,第三,第一加第二,第一加第三,第二加第三,然后是第一第二第三,在下半个周期内不启动的顺序是第一,第二,第三,第一加第二,第一加第三,第二加第三,然后是第一第二第三。
通过电加热器逐渐增加减少加热功率,进一步促进流体的流动,增加弹性振动效果。通过上述的时间变化性的加热功率的变化,可以使得流体在弹性热交换管内频繁的蒸发膨胀以及收缩,从而不断的带动弹性热交换管的振动,从而能够进一步实现加热效率以及除垢操作。
作为优选,在前半个周期内,电加热部件的加热功率是线性增加的,后半个周期内,电加热部件的加热功率是线性减少的,参见附图6。
通过输入电流或电压的变化实现加热功率的线性变化。
通过设置多个电加热器,实现电加热器的逐渐数量增加的启动,实现线性变化。
作为优选,周期是50-300分钟,优选50-80分钟;电加热部件平均加热功率为2000-4000w。
作为优选,所述第一集管9的管径小于第二集管15的管径,第一集管9的管径是第二集管15管径的0.5-0.8倍。通过第一集管和第二集管的管径变化,能够保证流体进行相变在第一箱体内时间短,快速进入盘管,充分进入第二箱体换热。
作为优选,盘管在第一集管的连接位置9低于第二集管与盘管的连接位置。这样保证蒸汽能够快速的向上进入第二集管。
作为优选,第一集管和第二集管底部设置回流管,保证第二集管内冷凝的流体能够进入第一管线。
作为优选,第一集管和第二集管沿着高度方向上设置,沿着第一集管的高度方向,所述盘管设置为多个,从上向下方向,盘管的管径不断变小。
作为优选,沿着第一集管的从上向下方向,盘管的管径不断变小的幅度不断的增加。
通过盘管的管径幅度增加,可以保证更多的蒸汽通过上部进入第二箱体,保证所有盘管内蒸汽的分配均匀,进一步强化传热效果,使得整体振动效果均匀,换热效果增加,进一步提高换热效果以及除垢效果。通过实验发现,采取此种结构设计可以取得更好的换热效果以及除垢效果。
作为优选,沿着第一集管的高度方向,所述盘管设置为多个,从上向下方向,相邻盘管的间距不断变大。
作为优选,沿着第一集管的高度方向,盘管之间的间距不断变大的幅度不断的增加。
通过盘管的间距幅度增加,可以保证更多的蒸汽通过上部进入第二箱体,保证所有盘管内蒸汽的分配均匀,进一步强化传热效果,使得整体振动效果均匀,换热效果增加,进一步提高换热效果以及除垢效果。通过实验发现,采取此种结构设计可以取得更好的换热效果以及除垢效果。
作为优选,如图7所示,所述汽箱是横截面为圆形汽箱,汽箱中设置多个电加热部件。
作为优选,如图7所示,所述汽箱内设置的多个电加热部件,其中一个设置在汽箱的中心,成为中心电加热部件,其它的围绕汽箱的中心分布,成为外围电加热部件。通过如此结构设计,可以使得汽箱内流体充分达到振动目的,提高换热效果。
作为优选,单个外围电加热部件的加热功率小于中心电加热部件的加热功率。通过如此设计,使得中心达到更大的震动频率,形成中心振动源,从而影响四周,达到更好的强化传热和除垢效果。
作为优选,同一水平换热截面上,流体要达到均匀的振动,避免换热分布不均匀。因此需要通过合理分配不同的电加热部件中的加热功率的大小。通过实验发现,中心电加热部件与外围热交换管电加热部件的加热功率比例与两个关键因素相关,其中一个就是外围电加热部件与汽箱中心之间的间距(即外围电加热部件的圆心与中心电加热部件的圆心的距离)以及汽箱的直径相关。因此本发明根据大量数值模拟和实验,优化了最佳的脉动流量的比例分配。
作为优选,汽箱内壁半径为r,所述中心电加热部件的圆心设置在汽箱圆形截面圆心,外围电加热部件的圆心距离汽箱圆形截面的圆心的距离为s,相邻外围电加热部件的圆心分别与圆形截面圆心进行连线,两根连线形成的夹角为a,外围电加热部件的加热功率为第二功率,单个中心电加热部件的加热功率为第一功率,则满足如下要求:
第一功率/第二功率=a-b*ln(r/s);ln是对数函数;
a,b是系数,其中1.9819<a<1.9823,0.5258<b<0.5264;
1.25<r/s<2.1;
1.6<第一功率/第二功率<1.9。
其中35°<a<80°。
作为优选,四周分布数量为4-5个。
作为优选,r为1600-2400毫米,优选是2000mm;s为1200-2000毫米,优选为1700mm;换热管的直径为12-20毫米,优选16mm;脉动盘管的最外侧直径为300-560毫米,优选400mm。立管的管径为100-116毫米,优选108毫米,立管的高度为1.8-2.2米,优选为2米,相邻的脉冲管的间距是65-100mm。优选80毫米左右。
总加热功率优选为6000-14000w,进一步优选为7500w。
进一步优选,a=1.9821,b=0.5261。
所述蒸汽出口设置在汽箱上壁的中间位置。
作为优选,所述箱体是圆形截面,设置多个电加热部件,其中一个设置在圆形截面圆心的中心电加热部件和其它的形成围绕圆形截面圆心分布的电加热部件。
盘管8为一组或者多组,每组盘管8包括多根圆弧形的热交换管19,多根圆弧形的热交换管19的中心线为同心圆的圆弧,相邻热交换管19的端部连通,从而使得盘管8的端部形成热交换管自由端10、11,例如图2中的自由端10、11。
作为优选,所述的加热流体为汽液相变的流体。
作为以优选,所述第一集管9、第二集管15以及盘管8都是圆管结构。
作为优选,盘管8的热交换管是弹性热交换管。
通过将盘管8的热交换管设置弹性热交换管,可以进一步提高换热系数。
作为优选,所述同心圆是以第一集管9的中心为圆心的圆。即盘管8的热交换管19围绕着第一集管9的中心线布置。
如图6所示,热交换管19不是一个完整的圆,而是留出一个口部,从而形成热交换管的自由端。所述口部的圆弧所在的角度为65-85度,即图8夹角b和c之和是65-85度。
作为优选,热交换管在同一侧的端部对齐,在同一个平面上,端部的延长线(或者端部所在的平面)经过第一集管9的中线。
进一步优选,所述电加热器20是电加热棒。
作为优选,盘管8的内侧热交换管的第一端与第一集管9连接,第二端与相邻的外侧热交换管一端连接,盘管8的最外侧热交换管的一端与第二集管15连接,相邻的热交换管的端部连通,从而形成一个串联的结构。
第一端所在的平面与第一集管9和第二集管15中心线所在的平面形成的夹角c为40-50度。
第二端所在的平面与第一集管9和第二集管15中心线所在的平面形成的夹角b为25-35度。
通过上述优选的夹角的设计,使得自由端的振动达到最佳,从而使得加热效率达到最优。
如图10所示,盘管8的热交换管为4个,热交换管a、b、c、d联通。当然,不局限于四个,可以根据需要设置多个,具体连接结构与图8相同。
所述盘管8为多个,多个盘管8分别独立连接第一集管9和第二集管15,即多个盘管8为并联结构。
作为优选,锅炉1内采取控制方式如下:
(一)出口蒸汽温度控制
所述锅炉蒸汽出口位置设置温度传感器,用于测量蒸汽出口的温度;所述温度传感器与中央控制7数据连接,所述控制器7根据温度传感器测量的温度来自动控制电加热器加热功率的大小。
如果温度传感器测量的温度低于第一温度,则控制器控制电加热器加热功率的增加;如果温度传感器测量的温度高于第二温度,控制器控制电加热器加热功率的减小。此种情况下表明在第一温度下,产生的蒸汽无法满足实际需要的最低温度要求,此时需要提高加热功率。第二温度下,产生的蒸汽温度过高,超出了实际需要的温度,此时锅炉需要降低加热功率。
作为优选,所述温度传感器为多个,所述控制器依据的温度数据是多个温度传感器测量的温度,来控制锅炉的运行。
(二)热水温度控制
作为优选,所述汽箱中设置温度传感器,用于测量汽箱中水的温度。所述温度传感器与控制器7数据连接,所述控制器7根据温度传感器测量的温度来自动控制电加热器的加热功率。
如果温度传感器测量的温度低于某一温度,则控制器控制电加热器加热功率的增加;如果第六温度传感器测量的温度高于一定温度,控制器控制电加热器加热功率的减小。此种情况下表明在某一温度下,因为热水的温度低,从而导致产生的蒸汽无法满足实际需要的最低温度要求,此时需要提高加热功率。高于一定温度下,因为热水的温度高,从而导致产生的蒸汽温度过高,超出了实际需要的温度,此时降低电加热器加热功率,将热量进行存储,避免热量的损失。
作为优选,所述温度传感器为多个,所述控制器依据的温度数据是多个温度传感器测量的温度,来控制锅炉的运行。
(三)水位控制
作为优选,所述的汽箱内设置水位传感器,汽箱补水管上设置水泵,所述水位传感器、水泵与控制器7数据连接,所述控制器7根据测量的汽箱内的水位自动控制水泵的功率。
作为优选,如果水位下降,控制器7则通过控制提高水泵的功率来增加进入汽箱的水的流量,如果水位过高,则通过降低水泵的功率或者关闭水泵来减少进入汽箱内水流量或者停止向汽箱内供水。
通过上述的设置,一方面避免了水位过低造成的蒸汽产出率过低以及汽箱干烧,造成汽箱的损坏以及产生安全事故,另一方面,避免了因为水位过高而造成的水量过大,实现水位的智能控制。
(四)根据水位对加热功率的控制
作为优选,所述的汽箱内设置水位传感器,所述水位传感器与控制器3数据连接,所述控制器3根据测量的汽箱内的水位自动控制电加热器的加热功率。
作为优选,如果水位过低,控制器7则制电加热器减少加热功率,从而避免因为锅炉中的功率过高造成的蒸汽产出过大,造成水位的进一步降低,如果水位过高,控制器7则控制电加热器增加加热功率,提高蒸汽产出,从而降低水位。
通过上述的设置,一方面避免了水位过低造成汽箱的干烧,造成汽箱的损坏以及产生安全事故,另一方面,避免了因为水位过高而造成的箱体内的水量过大。
(五)根据压力对加热功率的控制
作为优选,所述汽箱设置压力传感器,用于测量汽箱中压力。所述压力传感器与控制器7数据连接,所述控制器7根据压力传感器测量的压力来自动控制电加热器的加热功率的大小。
作为优选,如果压力传感器测量的压力低于一定的压力,则控制器控制电加热器加热功率增加。如果压力传感器测量的压力高于一定压力,则控制器控制电加热器加热功率降低。如果压力传感器测量的压力高于上限压力,则为了避免压力过大产生危险,控制器控制电加热器关闭。
通过如此设置,可以根据汽箱内的压力来调节加热功率,从而保证在最大化蒸汽产出的情况下,保证锅炉的安全。
所述压力传感器设置在汽箱的上部位置。
作为优选,所述压力传感器为多个,所述控制器依据的压力数据是多个压力传感器测量的温度,来控制锅炉的运行。
(六)蒸汽流量控制
作为优选,所述蒸汽出口管路上设置流量传感器,用于测量单位时间产出的蒸汽流量,所述流量传感器与控制器7数据连接。所述控制器7根据流量传感器测量的单位时间产出的蒸汽流量数据来自动控制电加热器的加热功率的大小。
作为优选,如果测量的蒸汽流量低于一定的数值,则控制器7控制电加热器的加热功率增加。如果压力传感器测量的流量高于一定的数值,则控制器3控制控制器7控制电加热器的加热功率的降低。
通过如此设置,可以根据锅炉产生的蒸汽数量来调节进入锅炉的加热功率,保证蒸汽产出数量的恒定,避免数量过大或者过小,造成蒸汽数量不足或者浪费,同时可以节约余热能源。
虽然本发明已以较佳实施例披露如上,但本发明并非限定于此。任何本领域技术人员,在不脱离本发明的精神和范围内,均可作各种更动与修改,因此本发明的保护范围应当以权利要求所限定的范围为准。
起点商标作为专业知识产权交易平台,可以帮助大家解决很多问题,如果大家想要了解更多知产交易信息请点击 【在线咨询】或添加微信 【19522093243】与客服一对一沟通,为大家解决相关问题。
此文章来源于网络,如有侵权,请联系删除


