一种用于蒸气净化的气液分离系统的制作方法



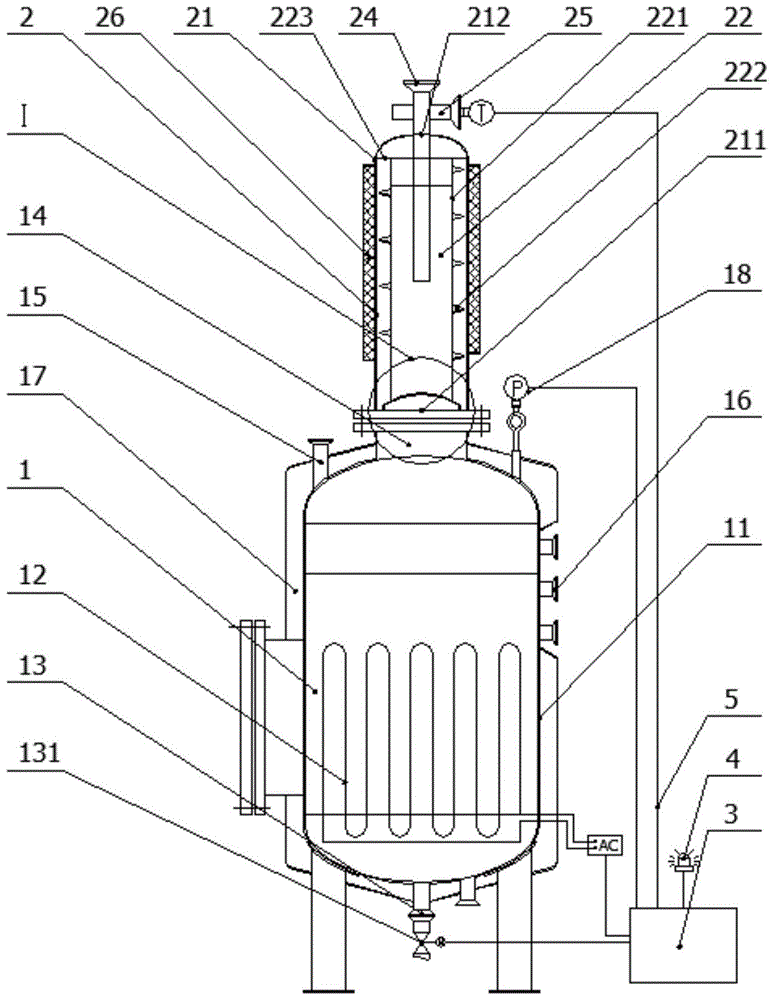
本实用新型涉及一种气液分离系统,具体涉及一种用于蒸气净化的气液分离系统。
背景技术:
气液分离技术即从气流中分离出液滴的技术,该技术广泛应用于环保,医药,化工等领域的工艺过程,用以分离清除气体中的有害物质或高效回收有用物质。气液分离的机理有:重力沉降,离心分离,惯性碰撞及经典吸引等,因此,运用上述机理研制的气液分离系统成为相应技术领域技术人员的关注热点。
具体到水蒸气的气液分离,以医药领域为例,在现有技术中,目前国内大部分制药企业的加热蒸汽采用集中制取、(锅炉间)管线输送方式获得,在厂区大面积使用汽量时,能耗损失较小;当厂区休息过程中,大部分设备停止使用,只有个别的设备要求单体间歇供热,由于加热蒸汽采用集中制取,导致热损耗加大,能源浪费严重。因此,气液分离应用领域,亟需一种结构简单,配套设备少,安装位置灵活的气液分离系统。
技术实现要素:
为了解决上述技术问题,本实用新型提出了一种适用于小范围小功率供热需求的结构相对简单,占用空间小,且无复杂的配套设施的气液分离系统。
为了实现上述目的,本实用新型的技术方案如下:
一种用于蒸气净化的气液分离系统,用以去除蒸发气体中的微小液滴,包括:蒸气生成装置,包括内部具有容纳原料液体空间的中空腔体及加热装置,所述中空腔体分为底部的液体区域和上部的蒸气区域,所述液体区域底部设有用于加入或排出原料液体的出入口,所述蒸气区域顶部设有排出所述液体受热所产生蒸气的第一排气口;螺旋分离装置,内含螺旋结构的长形腔体,以轴线沿竖直方向设置在所述蒸气生成装置顶部,包括筒体,螺旋结构,导向结构及排气管,所述筒体的下端和上端分别设有入气口和通孔,所述入气口与所述蒸气生成装置的第一排气口连通,所述螺旋结构由上下开口的圆筒,缠绕固定在所述圆筒外表面的螺旋板及支撑架组成,所述螺旋结构内置于所述筒体中间段,并由所述支撑架固定于所述筒体内壁,所述导向结构包括设有透气孔的圆形中封板,所述圆形中封板与所述螺旋结构圆筒的下方开口紧密接触,用以防止来自于所述第一排气口的蒸气进入所述螺旋结构圆筒内,所述排气管设置在所述螺旋结构内侧,一端位于所述螺旋结构中部位置,另一端穿过所述筒体上端的通孔伸出筒体外部。
与传统气液分离系统相比,采用上述技术方案的有益效果是:本技术方案在综合运用了重力分离和离心分离的原理下研制的气液螺旋分离系统,一方面,将蒸气生成装置和螺旋分离装置一体化设计,大大节约了设备占地面积,有效提高了厂区房间的利用率,这对于空间本就紧张的用户而言作用尤为重要;另一方面,且在气液分离过程中充分考虑到蒸气分离工艺的流程的长短对于分离的效果具有重要的影响,因此,本技术方案中除在螺旋的过程中延长了分离的工艺过程外,又将螺旋升到顶部的蒸气引至螺旋结构内部,进而进入排气管排出,实现了在有限的空间内更多的创造气液分离的途径,显著增强了气液分离效果。
作为本实用新型的进一步改进,所述蒸气生成装置设有不凝气体排放口,所述不凝气体排放口位于所述中空腔体的顶部。
采用上述技术方案的有益效果是:不凝气体排放口的设置,有效降低了进入螺旋分离装置蒸气中的不凝气体含量,不凝气体非但不能给后续设备或蒸气的利用带来任何有益的效果,还会对设备造成损害。因此,降低甚至除去蒸气中的不凝气体可大大提高蒸气的质量。
作为本实用新型的进一步改进,所述蒸气生成装置的中空腔体侧面设有液位检测装置,所述液位检测装置分别位于所述中空腔体内所述原料液体的最高限位,最低限位及最低警戒位。
采用上述技术方案的有益效果是:通过设置液位检测装置,可以随时掌握蒸气生成装置内的液体余量状态,便于判断何时需要补充原料液体,并及时发现蒸气生成装置内的异常情况。
作为本实用新型的更进一步改进,所述蒸气生成装置的加热装置为电加热,所述电加热元件置于所述中空腔体的液体区域,且所述电加热元件最高点低于所述中空腔体内液体区域的最低警戒位。
采用上述技术方案的有益效果是:电加热方式配置简单,只需在蒸气生成装置内设置加热元件,接通电源并辅以控制开关即可实现加热原料液体的目的,可有效减少气液分离系统的配套设备,这种加热方式尤其适用于本技术方案中的小型化蒸气供应设备。
作为本实用新型的更进一步改进,所述螺旋结构的螺旋板为双螺旋结构板。
采用上述技术方案的有益效果是:双螺旋结构板较单螺旋结构板而言,蒸气螺旋上升途径更多,工艺过程更长,有助于提升蒸气的分离效果。
作为本实用新型的更进一步改进,所述圆形中封板的中间部位为球形面的曲面板,所述曲面板凸起面方向朝上,抵住并封住所述螺旋结构圆筒的下方开口。
采用上述技术方案的有益效果是:圆形中封板的中间部位为向上凸起设计时,便于将螺旋结构圆筒内形成的冷凝液体集聚在底部的周边,排出更为方便。
作为本实用新型的更进一步改进,所述螺旋结构下端靠近开口处的侧面设有放液口,且放液口端部装有单向阀,以保证所述螺旋结构圆筒内部冷凝液体可以经放液口排出,且所述螺旋结构外部蒸汽无法通过所述放液口进入所述螺旋结构圆筒内部。
采用上述技术方案的有益效果是:螺旋结构圆筒内形成的冷凝液体集聚在底部可以通过放液口排出,但是外部的蒸气无法通过放液口进入螺旋结构的圆筒内部并直接排出,从而避免部分未经螺旋通道分离的蒸气走捷径排出,影响气液分离效果。
作为本实用新型的更进一步改进,所述螺旋分离装置还包括温度测量装置,所述温度测量装置设在所述螺旋分离装置排气管出口处,用以测量出口蒸气温度。
采用上述技术方案的有益效果是:螺旋分离装置出口增设温度测量装置,有利于实时掌握净化后的蒸气是否满足使用的需要,并为加热装置功率的调整提供依据。
作为本实用新型的又进一步改进,所述蒸气生成装置及螺旋分离装置外部均设有保温层。
采用上述技术方案的有益效果是:蒸气生成装置及螺旋分离装置外表面设置保温层一方面可降低设备外表面温度,避免产生烫伤等风险,另一方面,减少装置内热量损失,有效提高能量利用率,降低单位蒸气生产能耗,气液分离系统的经济性更佳。
作为本实用新型的又进一步改进,所述蒸气生成装置还包括压力传感器,所述液位检测装置为液位传感器,所述出入口设有电动控制阀,所述螺旋分离装置的温度测量装置为温度传感器,所述气液分离系统还包括:控制单元,实时接收分别来自压力传感器,温度传感器及液位传感器的压力信号,温度信号及液位信号,并根据接收到的信号向所述加热装置下达启停或功率调整指令,向所述电动控制阀下达启闭或开度调整指令;报警器,当所述气液分离装置内的液位或压力超出预定的警戒值时,接收所述控制单元的警报指令并发出相应警报;控制导线,用以连接所述控制单元,压力传感器,温度传感器,加热装置,电动控制阀及报警器,为信号传输提供通道。
采用上述技术方案的有益效果是:控制系统的配置可实现操作程序无人化,减少人工用工成本,减少人工控制的不稳定性,大大提高了系统的自动化和智能化水平。
附图说明
为了更为清楚地说明本实用新型实施例或现有技术中的技术方案,下面将对实施例或现有技术描述中所需要使用的附图作简单地介绍,显而易见地,下面描述中的附图仅仅是本实用新型的一些实施例,对于本领域普通技术人员而言,在不付出创造性劳动的前提下,还可以根据这些附图获得其它附图。
图1为本实用新型的气液分离系统示意图。
图2为本实用新型的导向结构局部放大示意图ⅰ。
图3为本实用新型的螺旋结构示意图。
图中数字及字母所表示的相应的部件名称如下:
蒸气生成装置1;中空腔体11;加热装置12;出入口13;电动控制阀131;第一排气口14;不凝气体排放口15;液位检测装置16;(蒸气生成装置)保温层17;压力传感器18;螺旋分离装置2;筒体21;入气口211;通孔212;螺旋结构22;圆筒221;螺旋板222;双螺旋结构板222a;支撑架223;放液口224;单向阀225;导向结构23;圆形中封板231;排气管24;温度测量装置25;(螺旋分离装置)保温层26;控制单元3;报警器4;控制导线5。
具体实施方式
为了便于理解本实用新型,下文将结合说明书附图和较佳的实施例对本实用新型作更全面、细致地描述,但本实用新型的保护范围并不限于以下具体的实施例。需要说明的是,在不冲突的情况下,本实用新型中的实施例及实施例中的特征可以相互组合。
为了实现本实用新型的目的,本实用新型提供的技术方案为:
如图1所示,一种用于蒸气净化的气液分离系统,用以去除蒸发气体中的微小液滴,包括:蒸气生成装置1,包括内部具有容纳原料液体空间的中空腔体11及加热装置12,中空腔体11分为底部的液体区域和上部的蒸气区域,液体区域底部设有用于加入或排出原料液体的出入口13,蒸气区域顶部设有排出液体受热所产生蒸气的第一排气口14;螺旋分离装置2,内含螺旋结构的长形腔体,以轴线沿竖直方向设置在蒸气生成装置顶部,包括筒体21,螺旋结构22,导向结构23及排气管24,筒体21的下端和上端分别设有入气口211和通孔212,入气口211与蒸气生成装置的第一排气口14连通,螺旋结构22由上下开口的圆筒221,缠绕固定在圆筒外表面的螺旋板222及支撑架223组成,螺旋结构22内置于筒体21中间段,并由支撑架223固定于筒体21内壁,导向结构23包括设有透气孔的圆形中封板231,圆形中封板231与螺旋结构圆筒221的下方开口紧密接触,用以防止来自于第一排气口14的蒸气进入螺旋结构圆筒221内,排气管24设置在螺旋结构22内侧,一端位于螺旋结构22中部位置,另一端穿过筒体上端的通孔212伸出筒体21外部。
与传统气液分离系统相比,采用上述技术方案的有益效果是:本技术方案在综合运用了重力分离和离心分离的原理下研制的气液螺旋分离系统,一方面,将蒸气生成装置和螺旋分离装置一体化设计,大大节约了设备占地面积,有效提高了厂区房间的利用率,这对于空间本就紧张的用户而言作用尤为重要;另一方面,且在气液分离过程中充分考虑到蒸气分离工艺的流程的长短对于分离的效果具有重要的影响,因此,本技术方案中除在螺旋的过程中延长了分离的工艺过程外,又将螺旋升到顶部的蒸气引至螺旋结构内部,进而进入排气管排出,实现了在有限的空间内更多的创造气液分离的途径,显著增强了气液分离效果。
在本实用新型的另一些实施方式中,如图1所示,蒸气生成装置1设有不凝气体排放口15,不凝气体排放口15位于中空腔体11的顶部。
采用上述技术方案的有益效果是:不凝气体排放口的设置,有效降低了进入螺旋分离装置蒸气中的不凝气体含量,不凝气体非但不能给后续设备或蒸气的利用带来任何有益的效果,还会对设备造成损害。因此,降低甚至除去蒸气中的不凝气体可大大提高蒸气的质量。
在本实用新型的另一些实施方式中,如图1所示,蒸气生成装置1的中空腔体11侧面设有液位检测装置16,液位检测装置16分别位于中空腔体11内原料液体的最高限位,最低限位及最低警戒位。
采用上述技术方案的有益效果是:通过设置液位检测装置,可以随时掌握蒸气生成装置内的液体余量状态,便于判断何时需要补充原料液体,并及时发现蒸气生成装置内的异常情况。
在本实用新型的另一些实施方式中,如图1所示,蒸气生成装置1的加热装置12为电加热,电加热元件置于中空腔体11的液体区域,且电加热元件最高点低于中空腔体11内液体区域的最低警戒位。
采用上述技术方案的有益效果是:电加热方式配置简单,只需在蒸气生成装置内设置加热元件,接通电源并辅以控制开关即可实现加热原料液体的目的,可有效减少气液分离系统的配套设备,这种加热方式尤其适用于本技术方案中的小型化蒸气供应设备。
在本实用新型的另一些实施方式中,如图3所示,螺旋结构22的螺旋板222为双螺旋结构板222a。
采用上述技术方案的有益效果是:双螺旋结构板较单螺旋结构板而言,蒸气螺旋上升途径更多,工艺过程更长,有助于提升蒸气的分离效果。
在本实用新型的另一些实施方式中,如图1所示,圆形中封板231的中间部位为球形面的曲面板,曲面板凸起面方向朝上,抵住并封住螺旋结构圆筒221的下方开口。
采用上述技术方案的有益效果是:圆形中封板的中间部位为向上凸起设计时,便于将螺旋结构圆筒内形成的冷凝液体集聚在底部的周边,排出更为方便。
在本实用新型的另一些实施方式中,如图2所示,螺旋结构22下端靠近开口处的侧面设有放液口224,且放液口224端部装有单向阀225,以保证螺旋结构圆筒221内部冷凝液体可以经放液口224排出,且螺旋结构22外部蒸汽无法通过放液口224进入螺旋结构圆筒221内部。
采用上述技术方案的有益效果是:螺旋结构圆筒内形成的冷凝液体集聚在底部可以通过放液口排出,但是外部的蒸气无法通过放液口进入螺旋结构的圆筒内部并直接排出,从而避免部分未经螺旋通道分离的蒸气走捷径排出,影响气液分离效果。
在本实用新型的另一些实施方式中,如图1所示,螺旋分离装置2还包括温度测量装置25,温度测量装置25设在螺旋分离装置排气管24出口处,用以测量出口蒸气温度。
采用上述技术方案的有益效果是:螺旋分离装置出口增设温度测量装置,有利于实时掌握净化后的蒸气是否满足使用的需要,并为加热装置功率的调整提供依据。
在本实用新型的另一些实施方式中,如图1所示,蒸气生成装置及螺旋分离装置外部分别设有保温层17及保温层26。
采用上述技术方案的有益效果是:蒸气生成装置及螺旋分离装置外表面设置保温层一方面可降低设备外表面温度,避免产生烫伤等风险,另一方面,减少装置内热量损失,有效提高能量利用率,降低单位蒸气生产能耗,气液分离系统的经济性更佳。
在本实用新型的另一些实施方式中,如图1所示,蒸气生成装置还包括压力传感器18,液位检测装置16为液位传感器,出入口13设有电动控制阀131,螺旋分离装置2的温度测量装置25为温度传感器,气液分离系统还包括:控制单元3,实时接收分别来自压力传感器,温度传感器及液位传感器的压力信号,温度信号及液位信号,并根据接收到的信号向加热装置12下达启停或功率调整指令,向电动控制阀131下达启闭或开度调整指令;报警器4,当气液分离装置内的液位或压力超出预定的警戒值时,接收控制单元3的警报指令并发出相应警报;控制导线5,用以连接控制单元3,压力传感器,温度传感器,加热装置12,电动控制阀131及报警器4,为信号传输提供通道。
采用上述技术方案的有益效果是:控制系统的配置可实现操作程序无人化,减少人工用工成本,减少人工控制的不稳定性,大大提高了系统的自动化和智能化水平。
上述实施例只为说明本实用新型的技术构思及特点,其目的在于让本领域普通技术人员能够了解本实用新型的内容并加以实施,并不能以此限制本实用新型的保护范围,凡根据本实用新型精神实质所作的等效变化或修饰,都应涵盖在本实用新型的保护范围内。
起点商标作为专业知识产权交易平台,可以帮助大家解决很多问题,如果大家想要了解更多知产交易信息请点击 【在线咨询】或添加微信 【19522093243】与客服一对一沟通,为大家解决相关问题。
此文章来源于网络,如有侵权,请联系删除


