一种丁苯胶乳天然胶乳并用生胶湿法混炼方法与流程



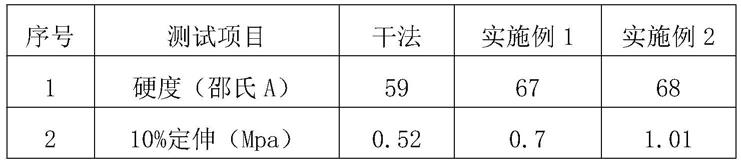
:
[0001]
本发明属于橡胶湿法混炼技术领域,具体涉及一种丁苯胶乳天然胶乳并用生胶湿法混炼方法,能够缩短生产周期,提高不同橡胶种类之间的相容性,提升橡胶性能。
背景技术:
:
[0002]
丁苯橡胶和天然橡胶是橡胶制品行业中主要基础材料之一,丁苯橡胶在耐磨、耐老化以及耐热等性能上优于天然橡胶,但在强度、弹性、耐屈挠龟裂性和加工性能上差于天然橡胶,所以在橡胶制品中将丁苯橡胶与天然橡胶掺用,能够协同提高橡胶制品性能。
[0003]
天然橡胶和丁苯胶乳在制备天然橡胶和丁苯橡胶时先将胶乳凝固或凝聚,再进行清洗和干燥等步骤,而凝固或凝聚工艺是形成制备固体橡胶的重要步骤,通常需要酸和盐类的一些化学试剂,可是,化学试剂的使用在造成环境污染同时也会对橡胶制品本身的性能造成影响。
[0004]
混炼是橡胶制品加工过程中最为关键的工序,其目的是将配方内的橡胶与橡胶之间和橡胶助剂与橡胶之间充分混合,并使各个物料之间尽可能的分散均匀。目前,橡胶工业中的传统混炼方式是沿用密炼机或开炼机多段式捏合型或者剪切型的混炼方法,由于聚合物之间的物性各不相同,存在工艺相容性问题,工艺相容性即指多种聚合物以任意比例共混时形成稳定均相体系的能力。从热力学角度来看,目前已知的聚合物中大多数共混都存在不相容的问题,很难达到分子或者链段水平混合。
[0005]
为了突破传统机械混炼以及聚合物本身物性带来的桎梏,可以利用湿法混炼工艺:将两种不同的物质以液态混合形成混合乳液,促使物质相互分散分布,形成均相,例如:中国专利201811319015.9公开的一种合成橡胶湿法混炼工艺,包括如下步骤:步骤s1、制液:将合成橡胶放入容器中,在600r/min搅拌速度下将白炭黑乳液滴加到合成橡胶中,滴加完毕后,1000r/min搅拌30min,使乳液混合均匀,降低搅拌速度至800r/min,搅拌下向乳液中依次加入氨基磺酸、促进剂ns、硬脂酸、防老剂,加完后,继续搅拌45-48min,得到胶乳混合液;步骤s2、凝聚:胶乳混合液在混合室的内壁凝聚;步骤s3、收集:凝聚后的液体沿混合室内壁流出,收集得到橡胶混合物;步骤s4、搅拌:对所述橡胶混合物在橡胶湿法混合器内进行搅拌,搅拌工艺参数,搅拌速度300-500r/min,搅拌时间3-8min;步骤s5、干燥:对搅拌后的混合物进行絮凝、洗胶和脱溶剂获得湿法混炼合成橡胶;具体步骤为:将凝固之后的胶乳混合体放入洗胶机中进行脱溶剂,同时用自来水对其进行冲洗、将经洗胶机脱溶剂之后的胶片放入75℃的烘箱中干燥7-8h,再将烘箱温度调至150℃将胶片再烘110-115s,取出,将烘干之后的胶片放到开炼机上进行补充混炼,在开炼机辊筒间隙最小状态下,将胶片在开炼机上过辊十次即可下片,得终炼胶、将制得的混炼胶在150℃、10mpa压力下在平板硫化机上硫化15min,制得合成橡胶;中国专利201710839208.6公开的一种湿法混炼制备炭黑母胶的方法,包括以下步骤:选用表面活性剂处理炭黑制备分散均匀的炭黑浆液,在转速300~600m/min下搅拌20~60min制备得到炭黑浆液;将橡胶胶乳加入炭黑浆液在转速100~300m/min搅拌20~50min,将胶乳和炭黑絮出,过滤,干燥;其中,炭黑浆液的质量百分数为2
~8%;表面活性剂为正丁醇、葡萄糖、聚乙二醇、脂肪醇聚氧乙烯醚-9、十二烷基硫酸钠、十二烷基苯磺酸钠中的至少一种;以橡胶胶乳中干胶质量为100份计,炭黑的加入量为30~80份,表面活性剂加入量为1~5份;中国专利201410345431.1公开的一种湿法混炼的方法,选用浸润剂浸润填料来制备分散均匀的填料水溶液,填料水溶液的质量百分数2-20%;以乳胶中干胶质量为100份计,填料水溶液中填料的加入量在3-80份;浸润剂加入量为10-200份;填料为炭黑、有机改性白炭黑、有机改性黏土或以上填料的混合物;浸润剂为乙醇;上述浆料分散后,与质量百分含量为10-40%的乳胶在管道中混合进行预絮凝;然后混入复合絮凝剂中;在搅拌速度为10-250m/min和温度为40-80℃条件下进行絮凝,将絮凝物颗粒清洗、脱水、烘干制得橡胶纳米复合母胶;复合絮凝剂中,氯化钙溶液与氯化钠溶液的体积比为1:2-2:1,其中氯化钙质量分数为0.5-3%,氯化钠质量分数为1-3%;中国专利201110064299.3公开的一种湿法混炼天然橡胶料的制备方法,a、配制浆料浆料由白炭黑干料、去离子水、偶联剂和表面活性剂构成,配制程序是:1)将15-40%白炭黑干料浸泡在60-85%的去离子水中,浸泡时间为3-6小时;2)、加入白炭黑干料含量的1-10%偶联剂、0.2-5%表面活性剂,机械搅拌使白炭黑干料、偶联剂和表面活性剂混合均匀,制成白炭黑浆料;b、研磨用研磨机将上述浆料研磨至沉降量小于80mg/h的白炭黑水分散体;c、制取胶乳混合液1)、取干胶含量为15-60%的天然橡胶的田间胶乳或经离心浓缩的天然胶乳;2)、将制备好的白炭黑水分散体加入到胶乳中,在常温下搅拌20-50分钟;3)、胶乳和白炭黑的水分散体均匀混合成胶乳混合液;d、絮凝、洗胶和脱水1)、在经混合均匀后的混合液中加入混合液总量的0.3-1%的醋酸,使其ph值为3-5,胶乳均匀絮凝并与白炭黑共沉;2)、凝固后的胶料用清水将多余的醋酸洗除,经洗胶机进行洗胶和脱水;3)、脱水后的胶料送至橡胶造粒机造粒,然后将胶料粒送入箱式干燥柜中进行干燥,温度为90-120℃,干燥时间为4-6小时;e、干燥完全后即为天然橡胶的混炼胶料。
技术实现要素:
:
[0006]
本发明的目的在于克服现有技术存在的缺点,研发设计一种丁苯胶乳天然胶乳并用生胶湿法混炼方法,解决聚合物的工艺相容性问题,简化混炼程序,减轻污染,提升橡胶制品性能。
[0007]
为了实现上述目的,本发明涉及的一种丁苯胶乳天然胶乳并用生胶湿法混炼方法的具体工艺过程包括制备丁苯/天然胶混合乳液、制备丁苯/天然胶复合材料、混炼和加硫共四个步骤:
[0008]
(一)制备丁苯/天然胶混合乳液:将丁苯胶乳和天然胶乳按照2.319-7.288:1的质量比混合后,搅拌均匀,得到丁苯/天然胶混合乳液;
[0009]
(二)制备丁苯/天然胶复合材料:将步骤(一)制备丁苯/天然胶混合乳液通过喷射雾化的形式絮凝干燥,得到丁苯/天然胶复合材料;
[0010]
(三)混炼:将丁苯/天然胶复合材料和sio2(二氧化硅)、n234(炭黑)、v700(环保芳烃油)、微晶蜡(b-wax)、sad(硬脂酸)、si69(硅烷偶联剂)、4020(防老剂)、zno(氧化锌)、rd(促进剂tmq)投入密炼机混炼,混炼温度为100℃、转速为90r/min,排胶温度条件为145℃保持一分钟,得到混炼胶;
[0011]
(四)加硫:将231.725g混炼胶与1.8质量份s(硫)和1.3质量份cz(n-环已基-2-苯
并噻唑次磺酰胺)置于开炼机中薄通6次,得到终炼胶料。
[0012]
本发明步骤(一)涉及的天然胶乳质量百分比浓度为60%;搅拌频率为40hz;搅拌时间为10min。
[0013]
本发明步骤(二)涉及的喷射雾化的喷射压力为1.2mpa,干燥温度为135℃。
[0014]
本发明步骤(三)涉及的丁苯/天然胶复合材料、sio2、n234、v700、微晶蜡、sad、si69、4020、zno和rd的质量分数分别为:124.38、35、50、8、1.5、4.55、2.3、2和2。
[0015]
本发明涉及的丁苯胶乳天然胶乳并用母胶混炼方法的原理是:物料溶液与压缩空气之间的速度差使得物料溶液在压缩空气的扰动下发生分裂、破碎,达到雾化效果,进而使胶乳粒子-丁苯胶乳粒子之间充分混合形成混合液滴;然后,混合液滴与高温物体的表面碰撞,飞溅爆破,实现胶乳粒子-丁苯胶乳粒子之间的二次分散结合;混合液滴爆破时,其中的水分在高温下被迅速蒸干,避免了单一橡胶烃的聚集,使各组分之间保持高分散状态。
[0016]
本发明与现有技术相比,将丁苯胶乳与天然胶乳混合、絮凝干燥,利用湿法混炼工艺制备成质量均一和加工性能高的丁苯/天然胶复合材料进行混炼,混炼胶的物理性能和动态力学性能相比于传统混炼工艺制备的混炼胶都有显著提高,而且生产周期也得到了缩短,解决了聚合物工艺相容性的问题,简化了混炼程序;其方法操作步骤简单,制备效率高,加工方式连续化,没有使用酸,减少了污染,避免了酸性残留对橡胶性能的影响,具有绿色环保和耗能低的优势。
具体实施方式:
[0017]
下面通过实施例做进一步说明。
[0018]
实施例1:
[0019]
本实施例涉及的一种丁苯胶乳天然胶乳并用生胶湿法混炼方法的具体工艺过程包括制备羧基-丁苯/天然胶混合乳液、制备羧基-丁苯/天然胶复合材料、混炼和加硫共四个步骤:
[0020]
(一)制备羧基-丁苯/天然胶混合乳液:将135.42g质量百分比浓度为66%的羧基-丁苯胶乳和58.4g质量百分比浓度为60%的天然胶乳混合后,在频率为40hz的条件下搅拌10min,得到羧基-丁苯/天然胶混合乳液;
[0021]
(二)制备羧基-丁苯/天然胶复合材料:将193.82g步骤(一)制备羧基-丁苯/天然胶混合乳液在喷射压力为1.2mpa,干燥温度为135℃的条件下通过喷射雾化的形式絮凝干燥,得到羧基-丁苯/天然胶复合材料;
[0022]
(三)混炼:将124.38g步骤(三)制备的羧基-丁苯/天然胶复合材料和35质量份sio2(二氧化硅),50质量份n234(炭黑)、8质量份v700(环保芳烃油)、1.5质量份微晶蜡(b-wax)、2质量份sad(硬脂酸)、4.55质量份si69(硅烷偶联剂)、2.3质量份4020(防老剂)、2质量份zno(氧化锌)、2质量份rd(促进剂tmq)投入密炼机混炼,混炼温度为100℃、转速为90r/min,排胶温度条件为145℃保持一分钟,得到混炼胶;
[0023]
(四)加硫:将231.725g步骤(四)制备的混炼胶与1.8质量份s(硫)和1.3质量份cz(n-环已基-2-苯并噻唑次磺酰胺)置于开炼机中薄通6次,得到终炼胶料。
[0024]
实施例2:
[0025]
本实施例涉及的一种丁苯胶乳天然胶乳并用生胶湿法混炼方法的具体工艺过程
包括制备乳化-丁苯/天然胶混合乳液、制备乳化-丁苯/天然胶复合材料、混炼和加硫共四个步骤:
[0026]
(一)制备乳化-丁苯/天然胶混合乳液:将425.6g质量百分比浓度为21%的乳化-丁苯胶乳和58.4g质量百分比浓度为60%的天然胶乳混合后,在频率为40hz的条件下搅拌10min,得到乳化-丁苯/天然胶混合乳液;
[0027]
(二)制备乳化-丁苯/天然胶复合材料:将193.82g步骤(一)制备乳化-丁苯/天然胶混合乳液在喷射压力为1.2mpa,干燥温度为135℃的条件下通过喷射雾化的形式絮凝干燥,得到乳化-丁苯/天然胶复合材料;
[0028]
(三)混炼:将124.38g步骤(三)制备的乳化-丁苯/天然胶复合材料和35质量份sio2(二氧化硅),50质量份n234(炭黑)、8质量份v700(环保芳烃油)、1.5质量份微晶蜡(b-wax)、2质量份sad(硬脂酸)、4.55质量份si69(硅烷偶联剂)、2.3质量份4020(防老剂)、2质量份zno(氧化锌)、2质量份rd(促进剂tmq)投入密炼机混炼,混炼温度为100℃、转速为90r/min,排胶温度条件为145℃保持一分钟,得到混炼胶;
[0029]
(四)加硫:将231.725g步骤(四)制备的混炼胶与1.8质量份s(硫)和1.3质量份cz(n-环已基-2-苯并噻唑次磺酰胺)置于开炼机中薄通6次,得到终炼胶料。
[0030]
实施例3:
[0031]
本实施例涉及终炼胶料的综合性能测试,将干法列为对比实验,终炼胶料综合性能的测试结果如下表:
[0032][0033][0034]
表明,实施例1和实施例2的终炼胶料的物理性能优于干法混炼的终炼胶料的物理性能,其中,拉伸强度分别提高了16.7%和23.2%,300%定伸应力分别提高了108.8%和71.6%;这是由于在实施例1和实施例2在制备复合材料的过程中,丁苯橡胶和天然橡胶先以胶乳粒子的形式混合,实现分子或者链段水平的混合,丁苯橡胶和天然橡胶再通过喷射雾化和絮凝干燥工艺进一步接触并混合,提高了工艺相容性,协同程度更高,从而提高了橡胶制品的性能。
起点商标作为专业知识产权交易平台,可以帮助大家解决很多问题,如果大家想要了解更多知产交易信息请点击 【在线咨询】或添加微信 【19522093243】与客服一对一沟通,为大家解决相关问题。
此文章来源于网络,如有侵权,请联系删除



tips