一种变厚度叶片金属包边的成形连接一体化装置及方法与流程



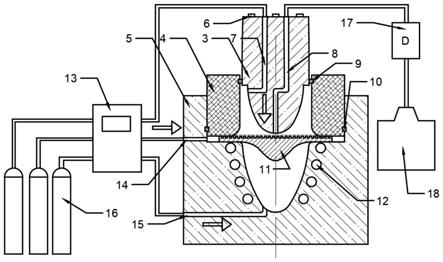
[0001]
本发明涉及材料成形技术领域,特别是涉及一种变厚度叶片金属包边的成形连接一体化装置及方法。
背景技术:
[0002]
目前的叶片包边金属的制备多采用铸造或机加工,但铸造工艺会使得叶片包边的薄壁部分出现浇不满、铸造质量差、尺寸精度低的问题,而机加工的问题在于材料利用率低、金属流线被打破、服役性能差。采用冲压或滚压等塑性成形再使用胶接也是叶片包边的一种常见方法,但是制作步骤复杂,成形效率低,成形后再进行胶接会导致几何精度畸变问题;气压成形相比于冲压滚压来说具有更好的成形效率,但常用的气压成形多为单侧施压,此时板料变形行为无法灵活调控,这一方式可能会存在低压区甚至死区,出现起皱和破裂缺陷,使得成形效果低于预期。此外,在碳纤维布树脂常规固化过程,易出现充填不满、间隙、性能不均等缺陷。因此如何提高叶片金属包边的成形质量和效率成为了本领域亟待解决的技术难题。
技术实现要素:
[0003]
本发明的目的是提供一种变厚度叶片金属包边的成形连接一体化装置及方法,以解决上述现有技术存在的问题,提高叶片金属包边的成形质量和效率。
[0004]
为实现上述目的,本发明提供了如下方案:
[0005]
本发明提供了一种变厚度叶片金属包边的成形连接一体化装置,包括上模、压边圈和下模,所述压边圈位于所述上模和所述下模之间;所述上模和所述下模之间能够形成金属包边的成形腔;所述上模中设置有上模腔气体通道和注胶通道,所述下模中设置有径向气体通道、下模腔气体通道和若干个接触式热电偶,所述上模腔气体通道、所述径向气体通道和所述下模腔气体通道分别通过管路与压力控制器连通,所述压力控制器与高压气瓶连通,所述注胶通道与注胶泵连通,所述注胶泵与储胶罐连通;所述上模上还设置有若干个超声振动探头。
[0006]
优选的,所述压边圈与所述上模之间设置有上模密封环,所述压边圈通过下模密封环与所述下模连接,初始金属板料夹设在所述压边圈与所述下模之间。
[0007]
本发明还提供一种变厚度叶片金属包边的成形连接一体化方法,基于上述的变厚度叶片金属包边的成形连接一体化装置,包括以下步骤:
[0008]
(1)对初始金属板料进行前处理,包括研磨抛光、除油、除锈及阳极氧化,然后将所述初始金属板料放置在压边圈和下模之间;
[0009]
(2)在待包边的变厚度叶片中设置上模腔气体通道和注胶通道,并在待包边的变厚度叶片的顶面设置振动探头,以将待包边的所述变厚度叶片作为气压成形中的上模;
[0010]
(3)在所述下模中设置径向气体通道、下模腔气体通道和接触式热电偶;
[0011]
(4)对所述接触式热电偶通电将所述下模加热,利用所述下模对所述初始金属板
料进行加热处理;
[0012]
(5)通过压力控制器向所述上模腔气体通道、所述径向气体通道和所述下模腔气体通道中通入高压气体,从所述上模腔气体通道、所述径向气体通道和所述下模腔气体通道中出来的高压气体分别挤压所述初始金属板料,同时向下进给所述上模,并开启注胶泵通过所述注胶通道向所述上模和所述初始金属板料之间的空隙内注胶;
[0013]
(6)在步骤(5)中所述初始金属板料发生塑性变形时,还应开启所述超声振动探头,以在所述初始金属板料周围施加超声振动,辅助所述初始金属板料的变形;
[0014]
(7)待所述上模进给到设定位置后,调节所述上模腔气体通道与所述下模腔气体通道压力差和所述径向气体通道中高压气体的压力,使得变形后的金属板料逐渐实现贴模和胶接;
[0015]
(8)对变形后的金属板料进行保温保压处理,保温保压处理结束后开模取出所述上模和变形后的金属板料,对所述上模和变形后的金属板料进行空冷。
[0016]
优选的,在步骤(1)中,需要在所述初始金属板料的顶面设置若干个横槽和若干个竖槽后再将所述初始金属板料放置在压边圈和下模之间,所述横槽与所述竖槽交叉。
[0017]
本发明相对于现有技术取得了以下技术效果:
[0018]
本发明的变厚度叶片金属包边的成形连接一体化装置及方法提高了叶片金属包边的成形质量和效率。本发明的变厚度叶片金属包边的成形连接一体化装置及方法将待包边的纤维复合材料叶片作为上模,将预包边的金属板料安置于下模上;通过对预包边的金属板料进行加热、注胶、三面加压和超声振动辅助,同时实现变厚度叶片包边的超声辅助气压成形与连接,得到包边好的叶片。采用本发明变厚度叶片金属包边的成形连接一体化方法,可以将纤维复合材料叶片金属包边的气压成形与连接过程一体化,显著提高加工效率,相比于先成形再连接的分步过程提高了约60%;本发明成形过程中加入超声振动辅助,能够有效的提高金属板料的成形极限,降低金属板料的变形抗力并减小成形力,同时超声振动促进组织晶粒细化提高板料的强度,也能够促进胶液的均匀分布从而提高界面强度与成形质量;采用三面气体压力成形,避免模具刚性接触,同时可调整的自由度高,能够更精确的实现所需的变形效果,也能够有效降低金属板料塑性变形时的过度减薄,包边表面的质量更好,强度更高。
附图说明
[0019]
为了更清楚地说明本发明实施例或现有技术中的技术方案,下面将对实施例中所需要使用的附图作简单地介绍,显而易见地,下面描述中的附图仅仅是本发明的一些实施例,对于本领域普通技术人员来讲,在不付出创造性劳动的前提下,还可以根据这些附图获得其他的附图。
[0020]
图1为包边后的叶片的结构示意图;
[0021]
图2为本发明变厚度叶片金属包边的成形连接一体化装置的结构示意图;
[0022]
图3为本发明变厚度叶片金属包边的成形连接一体化装置在成形过程中的结构示意图;
[0023]
图4为本发明变厚度叶片金属包边的成形连接一体化装置在成形结束后的结构示意图;
[0024]
图5为变厚度叶片金属包边的成形连接一体化装置在气压成形过程中的温度与压力示意图;
[0025]
其中:1、金属包边;2、叶片基体;3、上模;4、压边圈;5、下模;6、超声振动探头;7、上模腔气体通道;8、注胶通道;9、上模密封环;10、下模密封环;11、初始金属板料;12、接触式热电偶;13、压力控制器;14、径向气体通道;15、下模腔气体通道;16、高压气瓶;17、注胶泵;18、储胶罐;19、成形过程中的金属包边;20、成形结束的金属包边。
具体实施方式
[0026]
本发明的目的是提供一种变厚度叶片金属包边的成形连接一体化装置及方法,以解决上述现有技术存在的问题,提高叶片金属包边的成形质量和效率。
[0027]
为使本发明的上述目的、特征和优点能够更加明显易懂,下面结合附图和具体实施方式对本发明作进一步详细的说明。
[0028]
如图1至图5所示:本实施例提供了一种变厚度叶片金属包边的成形连接一体化装置,包括上模3、压边圈4和下模5,压边圈4位于上模3和下模5之间,压边圈4与上模3之间设置有上模密封环9,压边圈4通过下模密封环10与下模5连接,初始金属板料11夹设在压边圈4与下模5之间;初始金属板料11在贴合下模5边缘上表面后,压边圈4挤压住初始金属板料11并通过侧边的下模密封环10与下模5的凸起边缘固定在一起,为后续的径向气压的作用提供一个密闭空间。下模5为根据叶片形状而设计的变轴线形式。变厚度叶片为纤维复合材料基体,直接将其作为气压成形的上模3,并在其中非关键部位设置注胶道和气压通道。
[0029]
上模3和下模5之间能够形成金属包边1的成形腔;上模3中设置有上模腔气体通道7和注胶通道8,下模5中设置有径向气体通道14、下模腔气体通道10和若干个接触式热电偶12,上模腔气体通道7、径向气体通道14和下模腔气体通道10分别通过管路与压力控制器13连通,压力控制器13与高压气瓶16连通,注胶通道8与注胶泵17连通,注胶泵17与储胶罐18连通;上模3上还设置有若干个超声振动探头6。
[0030]
本实施例的变厚度叶片金属包边的成形连接一体化装置将待包边的纤维复合材料的叶片基体2作为上模3,将预包边的金属板料安置于下模5上;通过对预包边的金属板料进行加热、注胶、三面加压和超声振动辅助,同时实现变厚度叶片包边的超声辅助气压成形与连接,得到包边好的叶片。
[0031]
本实施例还提供一种变厚度叶片金属包边的成形连接一体化方法,基于上述的变厚度叶片金属包边的成形连接一体化装置,包括以下步骤:
[0032]
(1)对初始金属板料11进行前处理,包括研磨抛光、除油、除锈及阳极氧化,金属板料为变厚度材料,且越靠近中心部位,厚度越大。
[0033]
在初始金属板料11的顶面设置若干个横槽和若干个竖槽,任意一个横槽与任意一个竖槽交叉,在初始金属板料11的顶面形成十字交叉开槽,然后将初始金属板料11放置在压边圈4和下模5之间;
[0034]
在本实施例中,初始金属板料11与叶片连接的部位均进行细小的十字交叉型开槽处理;初始金属板料11较薄处的厚度优选为8mm~12mm,进一步优选为9mm~11mm;最厚处的厚度优选为30mm~45mm,进一步优选为35mm~40mm;初始金属板料11开槽深度为2mm~6mm,进一步优选为3mm~5mm;
[0035]
(2)在待包边的变厚度叶片中设置上模腔气体通道7和注胶通道8,并在待包边的变厚度叶片的顶面设置振动探头,以将待包边的变厚度叶片作为气压成形中的上模3;
[0036]
(3)在下模5中设置径向气体通道14、下模腔气体通道10和接触式热电偶12;
[0037]
(4)对接触式热电偶12通电将下模5加热,利用下模5对初始金属板料11进行加热至70℃~90℃;
[0038]
(5)通过压力控制器13向上模腔气体通道7、径向气体通道14和下模腔气体通道10中通入高压气体,从上模腔气体通道7、径向气体通道14和下模腔气体通道10中出来的高压气体分别挤压初始金属板料11,对初始金属板料11加压过程与升温过程时间是相等的,优选为15min~45min,进一步优选为20min~40min,更优选为25min~35min。
[0039]
同时向下进给上模3,并开启注胶泵17通过注胶通道8向上模3和初始金属板料11之间的空隙内注胶;
[0040]
上下模合模后,在70℃~90℃的基础温度下继续升温,目标温度为120℃~140℃,优选为125℃~135℃,对已经变形的金属板料进行二级三面加压,施加于板料边缘的压力不变,施加于下表面的压力高于上表面,促使金属板料贴合上模3叶片,上下模合模后,对初始板料的升温时间与加压时间相同,优选为10min~20min,进一步优选为10min~15min。在进行二级三面加压的过程中,金属板料边缘出现反胀效果,金属板料逐渐贴合叶片表面并完成连接,直至形成理想的包边形状。同时,金属板料在120℃~140℃下进行热处理,有效提高了叶片包边的力学性能。因此,在二级加压过程中,变厚度叶片包边在气压成形的同时完成了连接与热处理工艺,最终实现了气压成形连接一体化,极大提高了生产效率。
[0041]
施加于初始金属板料11边缘的径向压力为5mpa~15mpa,优选为6mpa~14mpa,进一步优选为7mpa~13mpa;施加于初始金属板料11上表面的压力高于下表面,为15mpa~20mpa,优选为16mpa~19mpa,进一步优选为17mpa~18mpa;施加于初始金属板料11下表面的压力为10mpa~15mpa,优选为11mpa~14mpa,进一步优选为12mpa~13mpa。且三面加压过程是从0开始压力逐渐升高到目标压力的过程。施加于初始金属板料11下表面的压力优选高于施加于初始金属板料11上表面的压力,压力差优选为0mpa~15mpa,进一步优选为2mpa~13mpa,更优选为5mpa~10mpa。将初始金属板料11下表面施加压力控制为高于上表面,有利于金属板料更好的贴合上模3叶片,并促进金属板料与叶片的连接。
[0042]
高压气体优选为氮气,本实施例在板料进行塑性变形时,通过向板料边缘的气体通道通入气体,并向成形模具的上、下表面的气体通道通入气体,使压力达到目标压力,避免了传统方法中成形模具直接与板料表面接触,对成形模具进行加压时导致的金属板料表面质量差,存在划痕的问题,同时还有助于在上模3向下运动时推动凸缘向模具腔室运动,有效消除板料塑性变形时的过度减薄现象,从而提高包边质量。
[0043]
(6)在步骤(5)中初始金属板料11发生塑性变形时,还应开启超声振动探头6,以在初始金属板料11周围施加超声振动,辅助初始金属板料11的变形,如图3中所示的成形过程中的金属包边19;
[0044]
(7)待上模3进给到设定位置后,调节上模腔气体通道7与下模腔气体通道10压力差和径向气体通道14中高压气体的压力,使得变形后的金属板料逐渐实现贴模和胶接,最终变形后的金属板料与上模3连接在一起;
[0045]
(8)如图4所示为成形结束的金属包边20,对变形后的金属板料进行保温保压处
理,保压时间优选为50min~70min,进一步优选为55min~65min,在120℃~140℃条件下,对气压成形模具内部进行降压,直至板料边缘压力与上、下表面均降为0mpa,降压处理时间优选为8min~12min,进一步优选为10min。降压完成后,本实施例继续对叶片包边进行保温处理,保温处理的温度优选为120℃~150℃,进一步优选为120℃~140℃;保温时间优选为60min~120min,进一步优选为80min~100min。本实施例在上述条件下进行保温处理,使金属能够进行时效处理,同时胶液也能更好的实现连接效果,有利于提高包边的质量。保温保压处理结束后,开模取出上模3和变形后的金属板料,对上模3和变形后的金属板料进行空冷,至此实现变厚度叶片的金属包边1的成形与连接。
[0046]
成形连接一体化过程中,叶片金属包边1的压力与温度示意图如图4所示,图4中t1为70℃~90℃,t2为120℃~140℃;气体压力p1为7mpa~13mpa,p2为13mpa~17mpa,p3为12mpa~13mpa,p4为17mpa~18mpa,p5为22mpa~23mpa;时间t1为25min~35min,(t2-t1)为10min~15min,(t3-t2)为55min~65min,(t4-t3)为10min,(t5-t4)为80min~100min。
[0047]
下面将结合本发明实施例中的附图,对本发明实施例中的技术方案进行清楚、完整地描述,显然,所描述的实施例仅仅是本发明一部分实施例,而不是全部的实施例。基于本发明中的实施例,本领域普通技术人员在没有付出创造性劳动的前提下所获得的所有其他实施例,都属于本发明保护的范围。
[0048]
实施例一
[0049]
本实施例中金属板料选用固溶态铝合金,变厚度的复合材料叶片采用热塑性(聚酰亚胺)碳纤维复合材料;对包边的铝板进行常规的研磨抛光、除油、除锈、活化等表面处理,并在板料上表面进行开槽处理,板料薄处的厚度为9mm,厚处的厚度为35mm,开槽深度为3mm;将制备好的板料放置于下模5上表面,并通过压边圈4将板料的纵向自由度约束固定,同时压边圈4与下模5凸缘通过密封环密封,上模3复材叶片也用密封环进行约束,整个成形腔形成一个可通入气体的密封环境;安置好上模3与板料后,利用下模5电阻加热将铝板进行加热至80℃,经由上模3的注胶通道8,对铝板表面进行注胶,同时经由上下模5以及侧边的气体通道,对铝板施加上下表面以及径向的气体压力,当时间至30min时,上模3腔压力上升为18mpa,下模5腔压力上升为13mpa,径向压力上升为10mpa。此时板料逐渐发生塑性变形,上模3逐渐向下进给;在板料塑性变形的同时,利用超声探头在其四周施加超声振动;当上模3进给到目标位置后,继续对板料进行升温,同时提高径向压力,并保持上模3腔压力不变,提高下模5腔压力,当总时间为40min时,温度提高至130℃,径向压力和下模5腔压力分别增至14mpa和23mpa,此时铝板开始逐渐贴附与叶片上模3上,得到最终所需的包边形状。继续对铝板进行保温保压处理,这期间,铝板进行热处理,胶液也在超声的作用下流动,均匀填充于铝板与叶片之间;当总时间来到100min时,保持模具温度不变,关闭气泵逐步泄压,卸压时间10min,直至三面的压力均降至0,在130℃,压力为0下,对成形的铝板进行保温处理,保温时间为90min,处理结束后,关闭加热装置,开模取件得到最终的叶片包边件。
[0050]
本实施例变厚度叶片金属包边的成形连接一体化方法实现了热塑性纤维复合材料叶片铝合金包边的气压成形与连接过程的一体化,显著提高了加工效率,相比于先成形再连接的分步过程提高了50%;本实施例变厚度叶片铝合金包边的成形过程中加入超声振动辅助,能够有效的提高铝板的成形极限,降低铝板的变形抗力并减小成形力,同时超声振动促进组织晶粒细化提高板料的强度,也能够促进胶液的均匀分布从而提高界面强度与成
形质量;采用三面气体压力成形,避免模具刚性接触,同时可调整的自由度高,能够更精确的实现所需的变形效果,也能够有效降低铝板塑性变形时的过度减薄,包边表面的质量更好,强度更高。
[0051]
实施例二
[0052]
本实施例中金属板料选用固溶态铝合金,变厚度的复合材料叶片采用热固性(环氧树脂)碳纤维复合材料;对包边的铝板进行常规的研磨抛光、除油、除锈、活化等表面处理,并在板料上表面进行开槽处理,板料薄处的厚度为10mm,厚处的厚度为36mm,开槽深度为4mm;将制备好的板料放置于下模5上表面,并通过压边圈4将板料的纵向自由度约束固定,同时压边圈4与下模5凸缘通过密封环密封,上模3复材叶片也用密封环进行约束,整个成形腔形成一个可通入气体的密封环境;安置好上模3与板料后,利用下模5电阻加热将铝板进行加热至75℃,经由上模3的注胶通道8,对铝板表面进行注胶,同时经由上下模5以及侧边的气体通道,对铝板施加上下表面以及径向的气体压力,当时间至35min时,上模3腔压力上升为17mpa,下模5腔压力上升为12mpa,径向压力上升为7mpa。此时板料逐渐发生塑性变形,上模3逐渐向下进给;在板料塑性变形的同时,利用超声探头在其四周施加超声振动;当上模3进给到目标位置后,继续对板料进行升温,同时提高径向压力,并保持上模3腔压力不变,提高下模5腔压力,当总时间为45min时,温度提高至125℃,径向压力和下模5腔压力分别增至13mpa和22mpa,此时铝板开始逐渐贴附与叶片上模3上,得到最终所需的包边形状。继续对铝板进行保温保压处理,这期间,铝板进行热处理,胶液也在超声的作用下流动,均匀填充于铝板与叶片之间;当总时间来到100min时,保持模具温度不变,关闭气泵逐步泄压,卸压时间10min,直至三面的压力均降至0,在125℃,压力为0下,对成形的铝板进行保温处理,保温时间为80min,处理结束后,关闭加热装置,开模取件得到最终的叶片包边件。
[0053]
本实施例变厚度叶片金属包边的成形连接一体化方法实现了热固性纤维复合材料叶片铝合金包边的气压成形与连接过程的一体化,显著提高了加工效率,相比于先成形再连接的分步过程提高了58%,本实施例变厚度叶片铝合金包边的成形过程中加入超声振动辅助,能够有效的提高铝板的成形极限,降低铝板的变形抗力并减小成形力,同时超声振动促进组织晶粒细化提高板料的强度,也能够促进胶液的均匀分布从而提高界面强度与成形质量;采用三面气体压力成形,避免模具刚性接触,同时可调整的自由度高,能够更精确的实现所需的变形效果,也能够有效降低铝板塑性变形时的过度减薄,包边表面的质量更好,强度更高。
[0054]
实施例三
[0055]
本实施例中金属板料选用固溶态钛合金,变厚度的复合材料叶片采用热塑性(聚酰亚胺)碳纤维复合材料;对包边的钛板进行常规的研磨抛光、除油、除锈、活化等表面处理,并在板料上表面进行开槽处理,板料薄处的厚度为10mm,厚处的厚度为38mm,开槽深度为4mm;将制备好的板料放置于下模5上表面,并通过压边圈4将板料的纵向自由度约束固定,同时压边圈4与下模5凸缘通过密封环密封,上模3复材叶片也用密封环进行约束,整个成形腔形成一个可通入气体的密封环境;安置好上模3与板料后,利用下模5电阻加热将钛板进行加热至85℃,经由上模3的注胶通道8,对钛板表面进行注胶,同时经由上下模5以及侧边的气体通道,对钛板施加上下表面以及径向的气体压力,当时间至25min时,上模3腔压力上升为18mpa,下模5腔压力上升为13mpa,径向压力上升为12mpa。此时板料逐渐发生塑性
变形,上模3逐渐向下进给;在板料塑性变形的同时,利用超声探头在其四周施加超声振动;当上模3进给到目标位置后,继续对板料进行升温,同时提高径向压力,并保持上模3腔压力不变,提高下模5腔压力,当总时间为35min时,温度提高至135℃,径向压力和下模5腔压力分别增至17mpa和23mpa,此时钛板开始逐渐贴附与叶片上模3上,得到最终所需的包边形状。继续对钛板进行保温保压处理,这期间,钛板进行热处理,胶液也在超声的作用下流动,均匀填充于钛板与叶片之间;当总时间来到90min时,保持模具温度不变,关闭气泵逐步泄压,卸压时间10min,直至三面的压力均降至0,在135℃,压力为0下,对成形的钛板进行保温处理,保温时间为80min,处理结束后,关闭加热装置,开模取件得到最终的叶片包边件。
[0056]
本实施例变厚度叶片金属包边的成形连接一体化方法实现了热塑性纤维复合材料叶片钛合金包边的气压成形与连接过程的一体化,显著提高了加工效率,相比于先成形再连接的分步过程提高了60%,本实施例变厚度叶片钛合金包边的成形过程中加入超声振动辅助,能够有效的提高钛板的成形极限,降低钛板的变形抗力并减小成形力,同时超声振动促进组织晶粒细化提高板料的强度,也能够促进胶液的均匀分布从而提高界面强度与成形质量;采用三面气体压力成形,避免模具刚性接触,同时可调整的自由度高,能够更精确的实现所需的变形效果,也能够有效降低钛板塑性变形时的过度减薄,包边表面的质量更好,强度更高。
[0057]
在本发明的描述中,需要说明的是,术语“顶”、“底”等指示的方位或位置关系为基于附图所示的方位或位置关系,仅是为了便于描述本发明和简化描述,而不是指示或暗示所指的装置或元件必须具有特定的方位、以特定的方位构造和操作,因此不能理解为对本发明的限制。
[0058]
本说明书中应用了具体个例对本发明的原理及实施方式进行了阐述,以上实施例的说明只是用于帮助理解本发明的方法及其核心思想;同时,对于本领域的一般技术人员,依据本发明的思想,在具体实施方式及应用范围上均会有改变之处。综上所述,本说明书内容不应理解为对本发明的限制。
起点商标作为专业知识产权交易平台,可以帮助大家解决很多问题,如果大家想要了解更多知产交易信息请点击 【在线咨询】或添加微信 【19522093243】与客服一对一沟通,为大家解决相关问题。
此文章来源于网络,如有侵权,请联系删除
相关标签: 铝板



tips