一种用于装功率半导体器件的塑胶包装管的生产线的制作方法



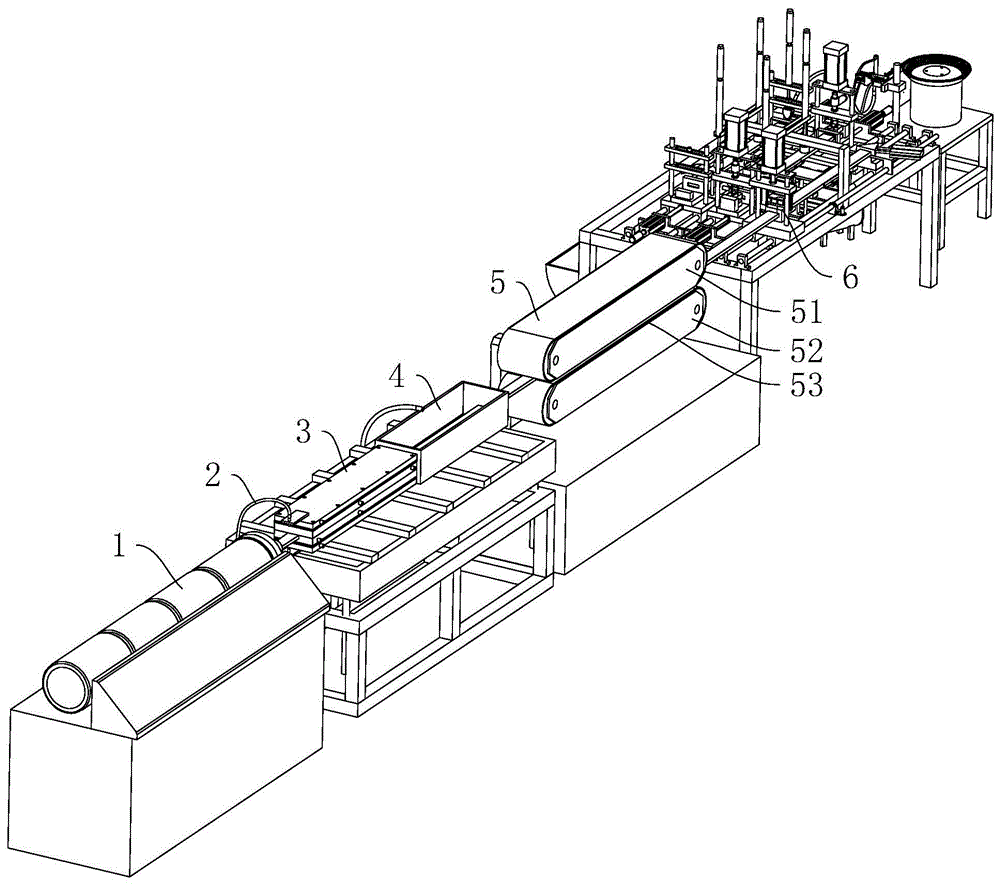
本申请涉及包装管生产的领域,尤其是涉及一种用于装功率半导体器件的塑胶包装管的生产线。
背景技术:
目前,在对电子元器件进行存储时,比如功率半导体器件(即芯片),通常采用塑胶包装管对芯片进行存储。芯片是一种长方形且侧面带有防呆口的板状物体,而塑胶包装管是一种底面带有凹槽的空心管,该凹槽朝向塑胶包装管的内部凹陷且沿塑胶包装管的长度方向开设。在使用时,将芯片上的防呆口与塑胶包装管的凹槽相对应再依次滑入塑胶包装管内,即可实现芯片的逐片排列和储存,以方便后续使用时有序取出。
在相关技术中,生产塑胶部件有两种方法,一种是用于生产不规则形状的塑胶部件的模具加工方法,其通过分别成型出塑胶部件的两部分再热拼接在一起,但是该种方法的生产速度较慢、工序复杂且良品率较低;一种是用于生产规则形状的塑胶部件的挤塑生产方法,其通过挤塑机挤塑出产品形状并牵引,在牵引过程中对产品的外壁冷却并定形即可。如果为了提高生产速度而采用挤塑生产方法来生产塑胶包装管,则在使用模具塑造出塑胶包装管底面上的凹槽时,模具上的凸起将会顶在塑胶包装管上底面上,塑胶包装管内部由于缺少支撑,将会导致凹槽的槽壁和塑胶包装管底面的连接处发生弯曲,无法形成直角。
技术实现要素:
为了提高塑胶包装管的生产速度并提高产品良率,本申请提供一种用于装功率半导体器件的塑胶包装管的生产线。
本申请提供的一种用于装功率半导体器件的塑胶包装管的生产线,采用如下的技术方案:
一种用于装功率半导体器件的塑胶包装管的生产线,包括用于挤出圆形的塑胶包装管的挤出机、用于将塑胶包装管塑由圆形塑形为大致呈方形的成型部、用于冷却塑胶包装管的冷却装置、用于将塑胶包装管从成型部牵引出的动力源、以及用于将动力源传出的塑胶包装管裁切成段的切断装置;
所述成型部内穿设有成型通道,所述成型通道的内壁上设有若干组负压凹槽;
所述冷却装置包括用于盛装冷却水并供塑胶包装管穿过的冷却槽、以及连通于冷却槽出口端的冷却水管,所述成型部设置于冷却槽的入口端内,所述成型通道与穿过的塑胶包装管之间的缝隙构成供冷却水流动的冷却流道,所述冷却流道与负压凹槽相连通;
所述切断装置包括机架、位于塑胶包装管运动路径上的推动组件、连接机架和推动组件的复位件、以及安装于机架上并在塑胶包装管运动路径上与推动组件同步运动的切刀组件,所述推动组件用于抵接塑胶包装管的位置设置有用于与塑胶包装管内腔相连通的通气孔,所述切刀组件在推动组件受塑胶包装管推动的过程中裁切塑胶包装管,所述复位件在切刀组件进行裁切动作后复位推动组件。
通过采用上述技术方案,挤出机的模头包括内模和外模,两者相互配合形成环形的缝隙,塑胶熔融液从该缝隙中流出并在牵引的作用下形成圆形的塑胶包装管。该圆形的塑胶包装管温度较高且可塑性强,在牵引的作用下进入冷却槽入口端内的成型部。成型部内成型通道的截面形状与所设计规格的塑胶包装管的截面形状相适配,因此圆形的塑胶包装管在进入成流通道后受到流道壁的塑形而成为方形。
又因为成型部是设置在冷却槽的出口端中,冷却水从冷却槽的入口端朝向出口端流动,并进入冷却流道,成型通道内壁的负压凹槽将冷却流道中的水和空气吸入,以使得冷却流道中的冷却水和气体高速流动,对塑胶包装管的进行快速冷却,从而使得塑胶包装管表面硬化。为了使得塑胶包装管的管壁与成型通道的内壁相贴合,从而使得凹槽的槽壁和塑胶包装管底面的连接处形成直角,则需要塑胶包装管的内部压力大于外部压力,从而利用气压差将塑胶包装管的管壁撑在成型通道的内壁上。由于负压凹槽的作用,塑胶包装管位于成型部内部分的外侧气压低于大气压,因此只需要塑胶包装管的内侧气压等于大气压即可。
由于塑胶包装管在不断地被挤出,也就意味着,塑胶包装管在不断被延长,内部的空腔不断增大,如果不对内补充空气,则将会导致内部的气压降低,从而影响成型效果。塑胶包装管在动力源的作用下,推动推动组件同步运动。在塑胶包装管运动过程中,切断装置对塑胶包装管进行裁切,塑胶包装管下落,推动组件失去支撑,复位件驱使推动组件复位。如果推动组件上不设置有通气孔,则塑胶包装管在抵接于推动组件运动时,将会导致塑胶包装管内部与外部的连通被阻断,在延伸过程中内部气压不断降低,从而对塑胶包装管的成型效果造成不良影响。
综上,对比于相关技术,即减低了产品生产的工序,实现了产品的高速生产,同时还保证了产品的良率。
优选的,还包括设置于挤出机和成型部之间的预定型装置,所述预定型装置包括出风口用于朝向塑胶包装管顶面一侧的上出风管、出风口用于朝向塑胶包装管底面一侧的下出风管、以及用于与塑胶包装管底面一侧相抵接的顶起弹丝,所述顶起弹丝用于与塑胶包装管的管壁相抵接以使塑胶包装管的管壁向内凹陷。
通过采用上述技术方案,上出风管和下出风管朝向圆形的塑胶包装管吹气冷却,形成圆形的塑胶包装管进入方形的成型通道的过渡阶段,使得塑胶包装管由圆形变扁,且表面初步硬化,以利于圆形的塑胶包装管朝向方形的塑胶包装管的转变。此外,顶起弹丝顶在塑胶包装管的底部以使得塑胶包装管向内产生凹陷,避免了塑胶包装管直接进入成型通道时被划破。由于顶起弹丝具有一定的弹性,其能够避免对塑胶包装管的压力过大而导致塑胶包装管的管壁被划破。
优选的,所述成型部包括相互连接的上模板和下模板,所述下模板朝向上模板的一侧设置有与塑胶包装管相适配的成型凹槽,所述成型凹槽的槽底沿成型凹槽的开设方向设置有成型凸棱,所述上模板与成型凹槽配合形成所述成型通道。
通过采用上述技术方案,圆形的塑胶包装管在经过上模板和下模板之间的成型通道后,将会被塑形为方形的塑胶包装管,且该塑胶包装管的底部将会有与成型凸棱相适配的凹槽。此外,上模板和下模板的相互配合,相比于一体化的成型部,检修更加方便。
优选的,所述上模板和下模板均包括有依次相连的外侧部、中层夹板和内侧部,所述上模板的内侧部和所述下模板的内侧部相对设置并栓接,所述外侧部朝向中层夹板的一侧设置有供冷凝水流动的冷却夹槽。
通过采用上述技术方案,由于内侧部贴合于塑胶包装管,温度较高,为了快速硬化塑胶包装管,外侧部的冷却夹槽对内侧部进行快速冷却。
优选的,所述冷却夹槽呈U形,所述外侧部上设置有与冷却夹槽两端相连通的进水口和出水口。
通过采用上述技术方案,冷却夹槽呈U形,相比于直线形状的流道,其内部冷却水的流动距离更长,与中层夹板的接触面积更大,冷却效率更高。
优选的,所述负压凹槽设置于内侧部背离外侧部的侧面上,所述内侧部在负压凹槽的两端各设置有一排负压通孔,所述负压通孔分别连通于负压凹槽,所述内侧部和中层夹板之间设置有两个负压流道,两个所述负压流道分别与一排负压通孔相连通,所述内侧部的两侧分别设置有与负压流道相连通的抽气管。
通过采用上述技术方案,抽气管抽取负压流道内的空气和冷却水,从而使得负压通孔和负压凹槽内形成负压。
优选的,各组所述负压凹槽在远离挤出机的方向上间距逐渐增大,各组所述负压凹槽中负压凹槽的数量在远离挤出机的方向上逐渐减少。
通过采用上述技术方案,由于在成型部的入口端处,塑胶包装管的温度较高,硬度较低,且形状初变,需要较大的负压将塑胶包装管吸附在成型通道的内壁上,从而完成更好的定形。同时,该处负压较高,有利于吸引冷却水流,从而提高冷却效果。
优选的,所述动力源包括上层传送带、下层传送带和调压装置,所述上层传送带和下层传送带相配合形成用于夹持塑胶包装管的牵引通道,所述调压装置调节上层传送带朝向下层传送带移动以将夹紧塑胶包装管,所述上层传送带和下层传送带的相对侧面朝向远离挤出机的方向运动。
通过采用上述技术方案,上层传送带和下层传送带压紧在塑胶包装管上并使得塑胶包装管均匀受力,避免塑胶包装管局部受压而发生变形。同时,动力源为塑胶包装管提供大的拉力,以将塑胶包装管从成型部中拉出,并朝向切断装置处运动。
优选的,所述机架上设置有固定轴,塑胶包装管沿所述固定轴的设置方向运动,所述切断装置还包括用于检测推动组件运动距离的传感器、以及与传感器相连的控制器,所述推动组件包括设置于塑胶包装管运动路径上的推块、用于推动或拉动推块以使推块进入或退出塑胶包装管运动路径的推动气缸、与推块相连并在固定轴上滑动的连接件、以及与连接件相连并平行设置于固定轴的推杆,所述推块用于抵接塑胶包装管的一侧设置有用于与塑胶包装管内腔相连通的通气孔;所述传感器包括设置于机架上的金属传感器和设置于推杆上的金属块,所述金属传感器位于金属块运动路径的下方,所述金属传感器与所述金属块相对时输出检测信号,所述控制器与金属传感器相连并基于检测信号控制切刀组件进行裁切。
通过采用上述技术方案,塑胶包装管朝向切断装置进料,由于推块位于塑胶包装管的运动路径上,因此塑胶包装管运动一定距离后,将会推动推块和连接件和切刀组件同步运动,由于连接件与固定轴滑动连接,因此将会在塑胶包装管的运动方向上与塑胶包装管同步运动。塑胶包装管位于推块和切刀组件之间部分的长度即与产品设计的长度规格相适配。在推动组件运动一段距离后,传感器发出检测信号,控制器基于该检测信号控制切刀组件裁切塑胶包装管。由于在裁切过程中切刀组件和塑胶包装管同步运动,因此避免了切刀在裁切时受到塑胶包装管的压迫而发生变形的风险。
此外,推块上设置有通气孔,则在塑胶包装管在抵接于推块运动时,塑胶包装管内部与外部相连通,避免了在塑胶包装管的延伸过程中内部气压发生降低,保证了前序工序中塑胶包装管的成型效果。
优选的,所述切刀组件包括设置于固定轴上并与固定轴滑动连接的滑动架、设置于滑动架上以供塑胶包装管穿过的定位框、设置于滑动架上的竖直推动气缸、以及连接于竖直推动气缸活塞杆的切刀,所述切刀上设置有切刀通孔,所述切刀通孔在切刀裁切塑胶包装管时与塑胶包装管的内部相连通;所述滑动架与推杆固定相连,所述竖直推动气缸基于控制信号推动切刀朝向定位框运动或拉动切刀远离定位框。
通过采用上述技术方案,推杆在运动时推动或拉动滑动架在固定轴上同步运动。定位框供塑胶包装管穿过,对塑胶包装管起到导向和定位作用,使得切刀落下时塑胶包装管不会在切刀所在平面内发生运动。竖直推动气缸推动切刀向下运动以切断塑胶包装管。切刀上设置有切刀通孔,在切刀在与塑胶包装管的接触过程中,塑胶包装管内部与外部相连通,避免了在塑胶包装管的延伸过程中内部气压发生降低,保证了前序工序中塑胶包装管的成型效果。
附图说明
图1是本申请实施例中一种用于装功率半导体器件的塑胶包装管的生产线的整体示意图;
图2是本申请实施例中预定型装置、成型部和冷却装置的整体示意图;
图3是图2在A处的放大图;
图4是本申请实施例中成型部的整体示意图;
图5是本申请实施例中成型部的爆炸图;
图6是本申请实施例中切断装置的整体示意图;
图7是图6中B处的放大图;
图8是图6中C处的放大图。
附图标记说明:
1、挤出机;
2、预定型装置;21、上出风管;22、下出风管;23、顶起弹丝;
3、成型部;31、上模板;32、下模板;33、成型凹槽;34、成型凸棱;35、成型通道;301、外侧部;302、中层夹板;303、内侧部;304、负压凹槽;305、负压通孔;306、负压流道;307、散热流道;308、冷却夹槽;309、橡胶层;
4、冷却装置;41、冷却槽;42、冷却水管;
5、动力源;51、上层传送带;52、下层传送带;53、牵引通道;
6、切断装置;
61、机架;611、安装架;612、固定轴;
62、推动组件;621、推块;6211、通气孔;622、连接件;623、推杆;624、推动气缸;
63、传感器;631、金属传感器;632、金属块;
64、复位件;641、复位弹簧;
65、切刀组件;651、滑动架;652、定位框;653、竖直推动气缸;654、切刀;655、裁切缝隙;656、切刀通孔。
具体实施方式
以下结合附图1-8,对本申请作进一步详细说明。
本申请实施例公开一种用于装功率半导体器件的塑胶包装管的生产线。参照图1,该生产线包括沿塑胶包装管的运动方向依次设置的用于挤出圆形的塑胶包装管的挤出机1、用于预冷却和预塑形塑胶包装管的预定型装置2、用于将塑胶包装管塑由圆形塑形为大致呈方形的成型部3、用于冷却塑胶包装管的冷却装置4、用于将塑胶包装管从成型部3牵引出的动力源5、以及用于将动力源5传出的塑胶包装管裁切成段的切断装置6。
参照图2和图3,挤出机1的模头包括内模和外模,两者相互配合形成环形的缝隙,塑胶熔融液从该缝隙中流出并在牵引的作用下形成圆形的塑胶包装管,该圆形的塑胶包装管温度较高且可塑性强。
参照图3,预定型装置2包括上出风管21、下出风管22和顶起弹丝23,上出风管21和下出风管22均与冷气泵相连,用于向外输出高速的冷气流。上出风管21的出风口用于朝向塑胶包装管的顶面一侧,下出风管22的出风口用于朝向塑胶包装管的底面一侧。在本实施例中,上出风管21和下出风管22分别固定于成型部3的入口的上方和下方。上出风管21和下出风管22分别朝向圆形的塑胶包装管的相对两侧吹气冷却,形成圆形的塑胶包装管进入方形的成型通道35的过渡区域。在该过渡区域中,塑胶包装管由圆形变扁,且表面初步硬化,以利于圆形的塑胶包装管朝向方形的塑胶包装管的转变。
顶起弹丝23在本实施例中为铁丝,其用于与塑胶包装管的底面相抵接,以使塑胶包装管的管壁向内凹陷,避免了塑胶包装管直接进入成型通道35时被划破。由于顶起弹丝23具有一定的弹性,其能够避免对塑胶包装管的压力过大而导致塑胶包装管的管壁被划破。
参照图4和图5,成型部3包括相互连接的上模板31和下模板32,上模板31和下模板32整体均呈方块状。下模板32朝向上模板31的一侧或上模板31朝向下模板32的一侧设置有与塑胶包装管相适配的成型凹槽33,在本实施例中,成型凹槽33位于下模板32朝向上模板31的一侧。成型凹槽33的槽底沿成型凹槽33的开设方向设置有与顶起弹丝23相对应的成型凸棱34,上模板31与成型凹槽33配合形成成型通道35,相应的,成型通道35的截面形状与塑胶包装管的设计截面形状相适配。
上模板31和下模板32均包括有依次相连的外侧部301、中层夹板302和内侧部303,外侧部301、中层夹板302和内侧部303形成三明治结构。其中,上模板31的内侧部303和下模板32的内侧部303相对设置并栓接,从而实现固定。在需要维护或更换时,只需要卸下螺栓即可解除连接,十分方便。
内侧部303背离外侧部301的侧面上设置有若干组负压凹槽304,每一组负压凹槽304均包括有若干道等距平行的负压凹槽304,且各负压凹槽304沿成型通道35的长度方向排列设置。在本实施例中,上模板31朝向下模板32的侧面为平面,负压凹槽304设置于该平面上。下模板32朝向上模板31的侧面设置有所述的成型凹槽35,负压凹槽304沿下模板32朝向上模板31的侧面、负压凹槽304的槽壁和负压凹槽304的槽底设置。可选的,负压凹槽304的数量为5-20道,在本实施例中,负压凹槽304一共12道,分为4组,各组内负压凹槽304的数量分别为1、2、3、6。各组负压凹槽304在远离挤出机1的方向上间距逐渐增大,且各组负压凹槽304中负压凹槽304的数量在远离挤出机1的方向上逐渐减少。此外,内侧部303在负压凹槽304的两端各设置有一排负压通孔305,两排负压通孔305平行设置。每一道负压凹槽304的两端分别与负压通孔305连通,这两端的负压通孔305分别隶属于不同的两排负压通孔305。由于在成型部3的入口端处,塑胶包装管的温度较高,硬度较低,且形状初变,需要较大的负压将塑胶包装管吸附在成型通道35的内壁上,从而完成更好的定形。同时,该处负压较高,有利于吸引冷却水流,从而提高冷却效果。
内侧部303和中层夹板302之间设置有两个相互平行的负压流道306、以及位于两个负压流道306中间的散热流道307,两个负压流道306各与一排负压通孔305相连通,内侧部303的两侧分别设置有抽气管,抽气管的两端分别连通于负压流道306和抽气泵。抽气管抽取负压流道306内的空气和冷却水,从而使得负压通孔305和负压凹槽304内形成负压。内侧部303上设置有与散热流道307两端相连通的进水管和出水管,冷凝水从散热流道307中流过,以吸收塑胶包装管传递到内侧部303的热量。
中层夹板302为钢板,其两侧分别设置有橡胶层309,当上模板31和下模板32栓接在中层夹板302上时,分别与橡胶层309相抵接产生密封效果,从而避免负压流道306发生漏气或者漏水。
外侧部301朝向中层夹板302的一侧和中层夹板302配合形成冷却夹槽308,冷却夹槽308的形状可以为直线形、S形或其它形状,在本实施例中,冷却夹槽308呈U形,且外侧部301上设置有与冷却夹槽308两端相连通的进水口和出水口。在使用时,冷却水从进水口通入冷却夹槽308中,冷却水吸收中层夹板302的热量。
继续参照图2,冷却装置4包括用于盛装冷却水并供塑胶包装管穿过的冷却槽41、以及连通于冷却槽41出口端的冷却水管42,成型部3安装在冷却槽41的入口端,且在使用时,成型部3内的成型通道35需要浸没在冷却槽41的水面以下。成型通道35与穿过的塑胶包装管之间的缝隙构成供冷却水流动的冷却流道,冷却流道与负压凹槽304相连通。在使用时,冷却水从冷却槽41的入口端朝向出口端流动,并进入冷却流道。成型通道35内壁的负压凹槽304和负压通孔305将冷却流道中的水和空气吸入,以使得冷却流道中的冷却水和气体高速流动并形成负压,塑胶包装管发生快速冷却,产生表面硬化。
由于塑胶包装管的内部与大气相连通且无气流产生或几乎无气流产生,因此内部压强接近于大气压。而塑胶包装管外部的压强较低,因此管壁内外两侧产生压强差,塑胶包装管的管壁被内部空气压力撑在成型通道35的内壁上,从而与成型通道35的形状相契合,因此塑胶包装管上凹槽的槽壁和塑胶包装管底面的连接处形成直角。
参照图1,动力源5包括上层传送带51、下层传送带52和调压装置,上层传送带51和下层传送带52相配合形成用于夹持塑胶包装管的牵引通道53,调压装置调节上层传送带朝向下层传送带移动以将夹紧塑胶包装管,上层传送带51和下层传送带52的相对侧面朝向远离挤出机1的方向运动。上层传送带51和下层传送带52压紧在塑胶包装管上并使得塑胶包装管均匀受力,避免塑胶包装管局部受压而发生变形。调压装置调节上层传送带51对塑胶包装管的压力,以改变对塑胶包装管的牵引力。同时,动力源5为塑胶包装管提供大的牵引力,以将塑胶包装管从成型部3中拉出,并朝向切断装置6处运动。
参照图6,切断装置6包括机架61、位于塑胶包装管运动路径上的推动组件62、用于检测推动组件62运动距离的传感器63、连接机架61和推动组件62的复位件64、与传感器63相连的控制器、以及安装于机架61上并在塑胶包装管运动路径上与推动组件62同步运动的切刀组件65。
参照图6和图7,机架61上设置有两个相对设置的安装架611、以及安装于安装架611支架之间的固定轴612,固定轴612呈水平设置,塑胶包装管沿固定轴612的轴向运动。
参照图6和图7,推动组件62包括位于塑胶包装管运动路径上的推块621、用于推动或拉动推块621以使推块621进入或退出塑胶包装管运动路径的推动气缸624、与推块621相连并在固定轴612上滑动的连接件622、以及与连接件622相连并平行设置于固定轴612的推杆623,塑胶包装管朝向推块621运动,在抵接于推块621后推动推块621继续运动。推块621用于抵接塑胶包装管的一侧设置有用于与塑胶包装管内腔相连通的通气孔6211,则在塑胶包装管在抵接于推块621运动时,塑胶包装管内部与外部相连通,避免了在塑胶包装管的延伸过程中内部气压发生降低,保证了前序工序中塑胶包装管的成型效果。此外,当切刀组件65切断塑胶包装管后,推动气缸624拉动推块621,使得推块621退出塑胶包装管的运动路径,从而松开塑胶包装管。
参照图6,传感器63包括设置于机架61上的金属传感器631和设置于推杆623上的金属块632,金属传感器631位于金属块632运动路径的下方,当金属块632运动一定距离后,机架61上的金属传感器631检测到金属块632并输出检测信号,控制器与传感器63相连并基于检测信号控制切刀组件65进行裁切。
参照图6和图7,连接件622通过复位件64与机架61相连,在本实施例中,复位件64为复位弹簧641,复位弹簧641套设与固定轴612上,且一端连于连接件622,另一端连于固定轴612远离切刀组件65的一端。当塑胶包装管推动推块621运动时,与推块621相连的连接件622将会压缩复位弹簧641,直至塑胶包装管被切断,复位弹簧641的形变恢复以推动连接件622和推块621复位。
参照图8,切刀组件65包括设置于固定轴612上并与固定轴612滑动连接的滑动架651、设置于滑动架651上以供塑胶包装管穿过的定位框652、设置于滑动架651上的竖直推动气缸653、以及连接于竖直推动气缸653活塞杆的切刀654,定位框652为方框,定位框652的开口朝向水平方向且开口形状与塑胶包装管的截面形状相适配。定位框652上开设有用于供切刀654伸入的裁切缝隙655,裁切缝隙655与定位框652内部相连通且裁切缝隙655与切刀654位于同一平面上。
参照图6和图8,滑动架651与推杆623固定相连,推杆623在运动时推动或拉动滑动架651在固定轴612上同步运动。竖直推动气缸653基于控制信号推动切刀654朝向定位框652运动或拉动切刀654远离定位框652。在本实施例中,切刀654上设置有切刀通孔656,切刀通孔656在切刀654裁切塑胶包装管时与塑胶包装管的内部相连通,在切刀654在与塑胶包装管的接触过程中,塑胶包装管通过切刀通孔656使得内部与外部相连通,避免了在塑胶包装管的延伸过程中内部气压发生降低,保证了成型通道35中的塑胶包装管能够在气压差的作用下贴合于成型通道35内壁上。
以上均为本申请的较佳实施例,并非依此限制本申请的保护范围,故:凡依本申请的结构、形状、原理所做的等效变化,均应涵盖于本申请的保护范围之内。
起点商标作为专业知识产权交易平台,可以帮助大家解决很多问题,如果大家想要了解更多知产交易信息请点击 【在线咨询】或添加微信 【19522093243】与客服一对一沟通,为大家解决相关问题。
此文章来源于网络,如有侵权,请联系删除


