一种背开门集装箱的货物自动装卸系统的制作方法



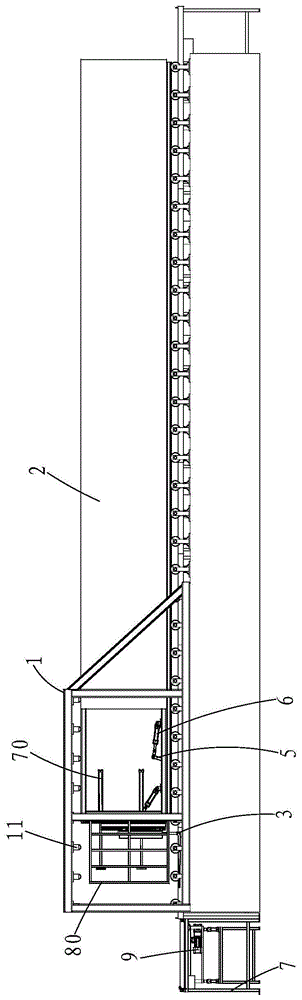
本发明涉及集装箱自动装卸货物技术领域,特别是一种背开门集装箱的货物自动装卸系统。
背景技术:
在背开门集装箱的货物自动装卸领域,传统装卸货物采用的方法是人工或者叉车将货物搬运至集装箱内。采用人工装卸方式效率太低、人力成本高,采用叉车装卸则位置精度低,需要重复调整货物的摆放位置,也导致效率低。
而现有技术中,有采用在悬臂端部设置货叉,进行装卸货物,但是在实际应用中发现,这种装卸货物的系统实用性差。这是因为由于背开式集装箱深度即长度方向的尺寸较大,随着悬臂逐渐伸入到集装箱内,则悬臂逐渐增长,即力臂也逐渐增大,使得悬臂受到的力矩也越大,越容易造成横梁弯曲、甚至横梁断裂。这对货物装卸的安全性造成影响。
技术实现要素:
本发明要解决的技术问题,在于提供一种背开门集装箱的货物自动装卸系统,采用在横梁的前端设置货叉,伸入集装箱内进行装卸货物,并在横梁的底部设置可调节的第二支撑架,对横梁进行支撑,避免横梁成为悬臂,增加横梁的强度。
本发明是这样实现的:一种背开门集装箱的货物自动装卸系统,包括
控制装置;
第一支撑架;
横梁,沿横向活动地连接于所述第一支撑架;
货叉,上下滑动地连接于所述横梁的前端;
水平驱动装置,通信连接于所述控制装置,并驱动所述横梁沿横向移动;
第二支撑架,旋转地连接于所述横梁的底部;
第一旋转驱动装置,通信连接于所述控制装置,且输出端连接于所述第二支撑架;
纵向输送装置,通信连接于所述控制装置,并沿纵向架设在所述横梁的前方,且高度低于所述横梁的底面。
进一步地,还包括横向输送装置,通信连接于所述控制装置,并沿横向架设在所述纵向输送装置的一侧。
进一步地,还包括
第一滑轨,沿竖向铺设在所述横梁的前端;
第一滑块,固定连接于所述货叉,且滑动连接于所述第一滑轨;
第一驱动装置,通信连接于所述控制装置,并固定连接于所述横梁的前端,且输出端连接于所述货叉。
进一步地,还包括
支撑板,顶端绕纵向轴线旋转地连接于所述横梁的前端;
第二驱动装置,通信连接于所述控制装置,并固定连接于所述横梁,且输出端连接于所述支撑板;
其中,所述第一滑轨沿竖向铺设在所述支撑板的前端面。
进一步地,还包括
推板,
第三驱动装置,通信连接于所述控制装置,固定连接于所述支撑板或所述横梁,且输出端连接于所述推板,驱动所述推板沿横向移动。
进一步地,还包括
轨道,至少有两个,沿横向固定连接于所述横梁的底部;
轨道轮,有若干个,旋转地架设在所述轨道的下方,并沿横向布置成至少两排,且每排所述轨道轮一一对应滚动地连接于所述轨道;
其中,所述水平驱动装置驱动所述轨道轮旋转。
进一步地,还包括滚轮,所述滚轮活动连接于所述第二支撑架的底部。
进一步地,所述横梁的底部位于横向中心线上设有纵向旋转轴;所述纵向旋转轴连接于所述第二支撑架。
进一步地,所述第二支撑架的顶端高于所述纵向旋转轴,顶端第一旋转驱动装置的输出端连接于所述第二支撑架的顶端。
进一步地,还包括
整形保护件,有两个,并位于所述货叉的两侧呈对称布置;
第四驱动装置,通信连接于所述控制装置,并连接于所述横梁,且输出端固定连接于所述每所述整形保护件。
本发明具有如下优点:一种背开门集装箱的货物自动装卸系统,包括控制装置;第一支撑架;横梁,沿横向活动地连接于所述第一支撑架;货叉,上下滑动地连接于所述横梁的前端;水平驱动装置,通信连接于所述控制装置,并驱动所述横梁沿横向移动;第二支撑架,旋转地连接于所述横梁的底部;第一旋转驱动装置,通信连接于所述控制装置,且输出端连接于所述第二支撑架;纵向输送装置,通信连接于所述控制装置。通过控制装置控制各个驱动装置实现自动装卸,采用横梁载着货叉,进行装卸货物,通过第二支撑架在横梁的底部进行支撑,避免横梁为悬臂而造成弯曲甚至断裂,提高了横梁的强度,保证装卸货物的安全性。
附图说明
下面参照附图结合实施例对本发明作进一步的说明。
图1为本发明的货物自动装卸系统的主视图。
图2为本发明的货物自动装卸系统的左视图。
图3为本发明的货物自动装卸系统的俯视图。
图4为图3中的A-A剖视图。
图5和图6为本发明的货物自动装卸系统的立体图。
图7为图6中B处的局部放大示意图。
图8为本发明的转移装置的主视图。
图9为本发明的转移装置的左视图。
图10为本发明的转移装置的立体图。
图11为本发明的横向输送装置、转移装置和纵向输送装置的立体图。
图12为图11中C处的局部放大示意图。
图13为本发明的横向输送装置、转移装置和纵向输送装置的立体图。
图14为图13中D处的局部放大示意图。
图15至图17为本发明的货物自动装卸系统的使用状态示意图。
图18是图4中E处的局部放大示意图。
图19是图13中F处的局部放大示意图。
附图标记说明:
第一支撑架1,限位轮11;
横梁2,轨道21,轨道轮22;
货叉3;
水平驱动装置4;
第二支撑架5,滚轮51,纵向旋转轴52;
第一旋转驱动装置6;
纵向输送装置7,第二检测装置71,第三检测装置72,避让凹槽73;
横向输送装置8,第一检测装置81;
转移装置9,固定架91,升降机92,升降平台93,驱动电机94,链条95,链轮96,转轴97;
第一滑轨10;
第一滑块20;
第一驱动装置30;
支撑板40;
第二驱动装置50;
推板60;
第三驱动装置70;
整形保护件80;
第四驱动装置90。
具体实施方式
在对本发明的描述中,需要理解的是,指示方位或位置关系的描述为基于附图所示的方位或位置关系,仅是为了便于描述本发明和简化描述,而不是指示或暗示所指的装置或元件必须具有特定的方位、以特定的方位构造和操作,因此不能理解为对本发明保护范围的限制。
在本发明的描述中,需要说明的是,除非另有明确的规定和限定,术语“设置”、“相连”、“连接”应做广义理解,例如,可以是固定连接,也可以是可拆卸连接,或一体地连接;可以是机械连接,也可以是电连接;可以是直接相连,也可以通过中间媒介间接相连,可以是两个元件内部的连通。对于本领域的普通技术人员而言,可以具体情况理解上述术语在本发明中的具体含义。
本发明的发明构思如下:
通过在横梁2的前端设置货叉3,横梁2进行横向移动,带动货叉3叉着货物进入集装箱内,并通过控制装置控制各个驱动装置进行动作,实现自动化装卸货物。
本发明的重点在于,第二支撑架5可随横梁2移动,通过可旋转的第二支撑架5在集装箱内对所述横梁2进行支撑,避免横梁2为孤立的悬臂,避免横梁2在装卸货物时受力矩太大,而造成弯曲甚至断裂,从而保证货物装卸时的安全性。
同时,所述第二支撑架5可旋转设置,使得第二支撑架5可在进入集装箱后,再旋转下来对所述横梁2进行支撑,避免和外部的设备发生干涉。
同时,可通过调节所述第二支撑架5的旋转角度,来调节第二支撑架5在竖直方向的高度,以适应不同车型的集装箱的高度,增加使用范围。
请参阅图1至图19所示。
本发明的一种背开门集装箱的货物自动装卸系统,包括
控制装置(未图示),可采用PLC,例如型号为:6ES7215-1AG40-0XB0 CPU1215C DC/DC/DC。
第一支撑架1;
横梁2,沿横向活动地连接于所述第一支撑架1;在具体实施中,所述横梁可根据需要设计成各种各样,例如,在附图所示的实施例中,所述横梁2采用长方体框架结构,通过钢管焊接而成,结构简单,制造方便。在具体一实施例中,如图1和图2所示,在所述第一支撑架1的左右两侧和上方分别设有限位轮11,限位轮11分别对应在所述横梁2的左、右、上表面滚动,从而实现所述横梁2和第一支撑架1活动连接,并通过左、右、上三个表面的滚轮对横梁2进行限位,避免横梁2在装卸货物时后端翘起。
货叉3,上下滑动地连接于所述横梁2的前端;所述货叉3可制作为一个,也可以是两个或两个以上,可一次性叉起一托盘的货物,或者一次性叉起两个或两个以上托盘的货物,这可根据需要去布置即可。例如,在具体一实施例中,根据集装箱的内宽,货叉3有两个,可一次性叉起两个托盘的货物。
水平驱动装置4,通信连接于所述控制装置(未图示),受所述控制装置(未图示)控制,且输出端连接于所述横梁2,用于驱动所述横梁2进行横向滑动,从而将货叉3和货物输送至集装箱内,或从集装箱内输送出来;在具体一实施例中,所述水平驱动装置4可采用电机、丝杆螺母副的组合方式进行驱动所述横梁2进行横向移动,也可以采用附图所示的实施例,如图7所示,电机、齿轮链条的方式,或者电机、带轮传动等方式。
第二支撑架5,旋转地连接于所述横梁2的底部;在具体实施中,所述第二支撑架5和第一旋转驱动装置6的数量可以是一个,也可以是一个以上,数量可根据实际需求去设定。
第一旋转驱动装置6,通信连接于所述控制装置(未图示),受所述控制装置(未图示)控制,且输出端连接于所述第二支撑架5,驱动第二支撑架5进行旋转;在具体一实施例中,所述第一旋转驱动装置6可采用气缸或液压缸。
纵向输送装置7,通信连接于所述控制装置(未图示),受所述控制装置(未图示)控制,并沿纵向架设在所述横梁2的前方,且高度低于所述横梁2的底面。所述纵向输送装置7用于将托盘和货物输送至所述货叉3的前方预定的位置,和所述货叉3相对,使得所述横梁2载着所述货叉3横向移动,可将托盘和货物叉起。在具体一实施例中,如图13和图19所示,在纵向输送装置7上设有第三检测装置72,第三检测装置72通信连接于控制装置(未图示),通过第三检测装置72来检测货物是否到达预定的装货位置,并和货叉3相对。在具体实施中,所述纵向输送装置7可采用现有的输送线,也可以采用其它的输送设备。当将货物直接置于纵向输送装置7上进行装卸货物时,可在纵向输送装置7上设置避让凹槽73,便于货叉3伸入避让凹槽73内,在避让凹槽73内向上升起,从而将货物叉起。
在具体实施中,货物可直接置于所述纵向输送装置7上,也可以将所述纵向输送装置7和其它输送线进行组合使用,从而由输送线将货物输送至所述纵向输送装置7上。
还包括横向输送装置8,通信连接于所述控制装置(未图示),并沿横向架设在所述纵向输送装置7的一侧。在具体实施中,所述横向输送装置8也可采用现有的输送线,或其它的输送设备。设置所述横向输送装置8的目的是为了应对不同场地的布置需求,增加本发明的使用范围,因为有的场地可能纵向的长度不足,无法做到只用所述纵向输送装置7直接对接至其它输送线进行输送托盘或货物时,因此,通过所述横向输送装置8进行变向,将纵向的长度缩短,使用时,先通过所述横向输送装置8和其它输送线进行对接,将货物或托盘输送至纵向输送装置,再由纵向输送装置7输送至预定的装货位置。
在具体实施中,货物可直接置于所述横向输送装置8上,也可以将所述横向输送装置8和其它输送线进行组合使用,从而由输送线将货物输送至所述横向输送装置8上。
在具体一实施例中,位于所述横向输送装置8的后方,且位于所述纵向输送装置7的下方还设有一转移装置9,所述转移装置9将托盘或货物从所述横向输送装置8转移至纵向输送装置7的预定位置,避免在托盘或货物的末端搭在所述纵向输送装置7的边缘部位,而影响纵向输送装置7输送托盘或货物。当然,这可根据所述纵向输送装置7的结构去选取是否使用所述转移装置,因此,所述纵向输送装置7采用输送线,输送线的型号不同,结构也不同,有的输送线的边框比辊筒高,这样就需要所述转移装置9将托盘或货物进行位置调整,使得托盘或货物完全位于辊筒上,而有的输送线,则是辊筒比边框高,此时,则无需使用所述转移装置也可以。当然有所述转移装置9使用效果会更好,可将托盘或货物的位置调节至更佳。
其中所述转移装置9包括升降机92,升降机92则安装在一固定架91上,升降机92通信连接于控制装置(未图示),升降机92的输出端固定连接有升降平台93,升降平台93上设有驱动电机94和若干链轮96和链条95组件,其中,若干链轮96固定套设在转轴97上,转轴97旋转地架设在所述升降平台93上,链条95和链轮96啮合,且链条95和所述纵向输送装置7的辊筒平行布置,且每所述链条95位于相邻辊筒之间的间隙内,从而使得链条95和链轮96可在间隙内升降;在具体一实施例中,在驱动电机94的输出轴上固定套设主动齿轮(未图示),在转轴97上固定套设从动齿轮(未图示),主动齿轮(未图示)和从动齿轮(未图示)通过主动力链条(未图示)连接,从而由驱动电机94驱动主动齿轮(未图示)旋转,通过齿轮链条带动从动齿轮(未图示)旋转,进而带动和从动齿轮(未图示)固定的转轴97旋转,最后带动链轮96旋转,从而驱动链条转动。
在横向输送装置8上设有第一检测装置81,第一检测装置81通信连接于所述控制装置(未图示),在具体实施中,所述第一检测装置81可采用位置传感器、CCD视觉检测仪、工业相机等检测设备。使用时,当第一检测装置81检测到托盘或货物时,控制装置(未图示)控制升降机92的活塞杆向上伸出,将升降平台93抬升至预定的位置,各个链条95从辊筒之间的间隙升起,此时链条的顶面和纵向输送装置7的辊筒的顶面平齐,通过各个链条和辊筒将托盘或货物支撑,升起到位后,同时链条95转动又可以带动货物移动;控制装置(未图示)控制驱动电机94工作,驱动链轮96旋转,带动链条95旋转,货物或托盘由横向输送装置8和链条95逐渐向纵向输送装置7上输送,从而将托盘或货物沿横向继续移动至预定的位置,在具体实施中,可在纵向输送装置7上设置第二检测装置71,第二检测装置71通信连接于控制装置(未图示),第二检测装置可采用位置传感器,第二检测装置用于检测托盘或货物是否被链条95输送到纵向输送装置7上预定的位置,到位后,被第二检测装置71检测到,第二检测装置71反馈信号给控制装置(未图示),控制装置(未图示)控制驱动电机94停止工作,并控制装置(未图示)控制升降机92的活塞杆下降复位,使得链条95位于辊筒下方,此时,货物或托盘由所述纵向输送装置7的辊筒支撑,升降机92复位后,控制装置(未图示)控制所述纵向输送装置7工作,将托盘或货物输送至预定的停放放置进行装货。在具体实施中,升降机92可采用液压缸。
还包括
第一滑轨10,沿竖向铺设在所述横梁2的前端;
第一滑块20,固定连接于所述货叉3,且滑动连接于所述第一滑轨10;
第一驱动装置30,通信连接于所述控制装置(未图示),并固定连接于所述横梁2的前端,且输出端连接于所述货叉3。
通过第一驱动装置30驱动所述货叉3进行上下滑动,从而将托盘和货物叉起或放下。其中所述第一滑轨10对所述货叉3的滑动方向进行导向,保证运动精度。在具体实施中,所述第一驱动装置30可采用气缸或液压缸等执行元件。
还包括
支撑板40,顶端绕纵向轴线旋转地连接于所述横梁2的前端;在具体一实施例中,支撑板40的顶端和横梁2铰接在一起,实现旋转。
第二驱动装置50,通信连接于所述控制装置(未图示),并固定连接于所述横梁2,且输出端连接于所述支撑板40;在具体实施中,所述第二驱动装置50可采用气缸或液压缸等执行元件。
其中,所述第一滑轨10沿竖向铺设在所述支撑板40的前端面。
从而可在装卸货物时,由所述第二驱动装置50驱动所述支撑板40进行旋转,使得所述货叉3的前端向上翘起移动的角度,翘起角度可预先设定,只需略微翘起即可,使得货物向所述支撑板40方向靠,避免在移动过程货物向前倾斜而发生掉落的风险。如图16所示,当所述货叉3伸入托盘内,并叉起托盘和货物后,所述第二驱动装置50的活塞杆伸出,推动所述支撑板40逆时针旋转,进而带动所述货叉3的向上翘起一定角度。
还包括
推板60,
第三驱动装置70,通信连接于所述控制装置(未图示),固定连接于所述支撑板40或所述横梁2,且输出端连接于所述推板60,驱动所述推板60沿横向移动,从而将货物从所述货叉3上推下来。该实施方式适用于货物去掉托盘,直接放在所述纵向输送装置7上。如果货物是放在托盘上,托盘放置纵向输送装置上,则可无需使用所述推板60和第三驱动装置70,直接控制货叉3从托盘上退出即可。这可根据实际货物运输时是否携带托盘去布置即可。当然采用该实施方式,用于携带托盘装货时,推板60和第三驱动装置70无需开启工作即可。在具体一实施例中,所述推板60的数量和面积可根据货物的大小去布置,确保推板能够将货物平稳地从货叉3推到集装箱内即可,例如,附图所示的实施例中,所述推板60和第三驱动装置70分别有4个,呈矩形布置,在货叉3和支撑板40上开设避让开口,用于避让推板60和第三驱动装置70的活塞杆。
还包括
轨道21,至少有两个,沿横向固定连接于所述横梁2的底部;
轨道轮22,有若干个,旋转地架设在所述轨道21的下方,并沿横向布置成至少两排,且每排所述轨道轮22一一对应滚动地连接于所述轨道21;在具体实施中,所述水平驱动装置4可采用电机,可每个轨道轮22对应布置一个所述水平驱动装置4进行驱动,也可以不需要每个轨道轮22都用所述水平驱动装置4进行驱动,可将部分轨道轮22作为从动轮使用,所述水平驱动装置4的数量可根据载重量去布置即可;所述轨道轮22的转轴和水平驱动装置4的输出轴可通过联轴器直接连接,水平驱动装置4架设在地面上;当然在另一实施例中,如图7所示,轨道轮22架设在两竖直支撑板上,水平驱动装置4固定在地面或支撑物体上,水平驱动装置4的输出轴套上齿轮或带轮,轨道轮22的转轴上也固定套设从动齿轮或带轮,和水平驱动装置4上的齿轮或带轮通过链条或皮带连接,从而水平驱动装置4的输出轴旋转通过齿轮链条或带轮传动带动轨道轮22旋转,进而带动轨道21横向移动,进而带动所述横梁2横向移动。
其中,所述水平驱动装置4驱动所述轨道轮旋转,从而将所述轨道21和横梁2进行横向移动。采用滚动的方式,使得摩擦阻力为滚动摩擦,降低摩擦阻力。
当然在其它实施例中,还可以采用滑轨和滑块来实现所述横梁2的横向移动,例如,还包括第二滑轨(未图示),沿横向铺设于所述第一支撑架1上;第二滑块(未图示),滑动连接于所述第二滑轨(未图示),并固定连接于所述横梁2。从而实现所述横梁2滑动连接于所述第一支撑架1上,通过第一支撑架1对所述横梁2起支撑和限位作用,避免所述横梁2在伸入集装箱内时,后端发生翘起现象,同时通过第二滑轨(未图示)对所述横梁2的滑动方向进行导向,提高运动精度。此时,可以和所述轨道21和轨道轮22结合起来使用,当然也可单独使用,第二滑轨(未图示)和第二滑块(未图示)单独使用时,所述水平驱动装置4可采用电机,其通过滚珠丝杆螺母副连接于横梁2,从而驱动横梁2进行横向移动。
如图5所示,还包括滚轮51,所述滚轮51活动连接于所述第二支撑架5的底部,在具体实施中,可采用螺栓进行,从而使得所述第二支撑架5还可以通过滚轮51在集装箱内进行滚动,降低摩擦力。在具体一实施例中,所述滚轮51的转轴可沿纵向布置,当然在其它实施例中,因为横向移动方向已经由所述轨道21进行导向限位了,所以所述滚轮51也可以采用万向滚轮。或在其它实施例中,也可以采用其它的布置方式。
所述横梁2的底部位于横向中心线上设有纵向旋转轴52;所述纵向旋转轴52连接于所述第二支撑架5。在具体一实施例中,可在纵向旋转轴52上套上轴承,轴承再嵌接在第二支撑架5内,这样使得第二支撑架5旋转更顺畅。当然在其它实施例中,还可采用其它的结构来实现第二支撑架5旋转,例如,可将纵向旋转轴52直接穿设在第二支撑架5内,采用间隙配合,当然,这种实施方式第二支撑架5旋转没有上种实施方式来的顺畅。
所述第二支撑架5的顶端高于所述纵向旋转轴52,第一旋转驱动装置6的输出端连接于所述第二支撑架5的顶端。在具体一实施例中,所述第一旋转驱动装置6可采用液压缸或气缸,活塞杆铰接于所述第二支撑架5的顶端。在具体实施中,所述第一旋转驱动装置还可采用电机、液压缸等设备,可对旋转的角度进行调节,从而适应不同车型、内腔底面高度不同的集装箱的使用需求,增加使用范围。在具体实施中,当所述第二支撑架5旋转至预定的位置后,滚轮51和集装箱内腔的底面接触,并在其上滚动,对横梁2起支撑作用,避免横梁2处于悬臂状态。在具体一实施例中,所述第二支撑架5布置在横梁2的前端底部,可更好的对横梁2的前端进行支撑。
还包括
整形保护件80,有两个,并位于所述货叉3的两侧呈对称布置;
第四驱动装置90,通信连接于所述控制装置(未图示),并连接于所述横梁2,即在具体实施中,所述第四驱动装置90可直接固定连接于所述横梁2,也可以通过中间连接件固定连接于所述横梁2,例如,所述第四驱动装置90固定连接于所述支撑板40,而支撑板40是旋转地连接于所述横梁2的,从而实现第四驱动装置90连接于所述横梁2,且输出端固定连接于所述每所述整形保护件80。由所述第四驱动装置90驱动所述整形保护件80沿纵向进行开合运动,将货物的两侧面推正,起整形的作用,避免货物侧面不整齐在装货时和集装箱的内侧壁发生摩擦,而损坏货物。另一方面,所述整形保护件80将货物的两侧面挡住,从而保护货物,避免货车停放位置出现误差时,使得装卸时位置发生偏差,即使和集装箱的内侧壁发生摩擦,也是所述整形保护件80和集装箱内侧壁发生摩擦,而不会造成货物和集装箱内侧壁直接发生摩擦,从而保护货物。在具体一实施例中,所述第四驱动装置90有四个,呈矩形布置在所述支撑板40的前端面,所述第四驱动装置90采用液压缸或气缸,其活塞杆沿纵向布置,并和所述整形保护件80固定连接。从而由第四驱动装置90的活塞杆伸缩,带动整形保护件80进行开合运动。
具体一使用方式:
在具体实施中,可将货物置于托盘上,然后托盘置于所述横向输送装置8上进行输送,也可以直接将货物置于所述横向输送装置8上进行输送,这个可根据实际使用需求去布置即可。
横向输送装置8和纵向输送装置7都采用现有的由电机驱动的输送线。
以货物直接放在所述横向输送装置8和纵向输送装置7上输送为例:
初始时,控制装置(未图示)控制第一驱动装置30驱动所述货叉3移动至预定的第一低位,此时横梁2横向移动,货叉可直接进入避让凹槽73,伸入货物的下方;
货物放置在横向输送装置8上;
装货时,控制装置(未图示)控制横向输送装置8工作,将货物往纵向输送装置7上输送,货物从横向输送装置8的末端输送至纵向输送装置7上;当货物到达预定的位置被第一检测装置81检测到后,第一检测装置81反馈信号给控制装置(未图示);
控制装置(未图示)控制升降机92的活塞杆向上伸出,驱动升降平台93上升从而带动链条95抬升至和纵向输送装置7的辊筒的顶面平齐,当升降机92的活塞杆至预定的位置,后其自带的行程开关反馈信号给控制装置(未图示),控制装置(未图示)控制驱动电机94工作,带动链条95转动,从而将货物沿横向继续移动,调整货物的位置,至预定的位置被第二检测装置71检测到,第二检测装置71反馈信号给控制装置(未图示);
控制装置(未图示)控制驱动电机94停止工作,然后控制升降机92的活塞杆复位缩回,链条95下降至纵向输送装置7的辊筒下方,由纵向输送装置7的辊筒支撑货物;升降机92的活塞杆复位后,反馈信号给控制装置(未图示);
控制装置(未图示)控制纵向输送装置7的电机工作,驱动辊筒旋转,将货物输送至所述货叉3的前方预定的装货位置,到位后被第三检测装置72检测到,并反馈信号给控制装置(未图示);控制装置(未图示)控制纵向输送装置7的电机停止工作;
后控制装置(未图示)控制所述水平驱动装置4驱动所述轨道轮22旋转,从而带动所述轨道21和横梁2进行横向移动至预定的位置,货叉3伸入避让凹槽73内,位于货物的下方;在具体实施中,可在纵向输送装置7设置第四检测装置(未图示),第四检测装置(未图示)通信连接于控制装置(未图示),用于检测货叉3是否移动到避让凹槽73内预定的位置,当然,也可以通过预设所述水平驱动装置4的行程开关来确定货叉3是否到达避让凹槽73内预定的位置,当然还可以通过预设水平驱动装置4的旋转圈数来设定到达避让凹槽73内预定的位置;
到位后控制装置(未图示)控制第一驱动装置30工作,驱动货叉3向上抬升至预定的位置;
后控制装置控制(未图示)第四驱动装置90的活塞杆缩回,驱动整形保护件80闭合,将货物推正;第四驱动装置90的活塞杆缩回到位后,控制装置(未图示)再控制第四驱动装置90的活塞杆伸出复位,将两所述整形保护件80复位打开;
后控制装置(未图示)控制第二驱动装置50工作,驱动支撑板40旋转,向上翘起若干角度,例如3°~5°,将货物向上翘起,避免前倾掉落;
后控制装置(未图示)控制第一旋转驱动装置6的活塞杆伸出,驱动第二支撑架5向下旋转至预定的位置,例如第二支撑架5呈竖直或倾斜朝下;其中,所述第二支撑架5旋转至预定的位置,可在货物进入集装箱内后旋转下来,和集装箱内腔的底面接触,这可根据滚轮51和纵向输送装置7的高度,如果两者不会发生干涉,可在进入集装箱前即将第二支撑架5旋转在预定的位置。这可以根据实际使用需求去设定工作程序即可。可通过第一驱动装置30的行程开关、旋转圈数、或者设置检测装置等方式去预设即可。
控制装置(未图示)控制水平驱动装置4工作,驱动横梁2向集装箱内移动至预定的位置,此过程中,随着第二支撑架5进入集装箱内,所述滚轮51在集装箱的内腔底面滚动,从而由第二支撑架5将横梁2支撑,避免横梁2成为独立的悬臂,缩小力臂的长度,降低横梁2所受力矩;
到达集装箱内预定的位置后,控制装置(未图示)控制第一驱动装置30工作,降低至预定的第二低位,将货叉3下放至集装箱底面上;然后控制装置(未图示)控制第二驱动装置50的活塞杆复位缩回,将货叉3旋转至水平;
后控制装置(未图示)控制第三驱动装置70的活塞杆伸出至预定的位置,驱动推板60推动货物,使得货物从货叉3上移动至集装箱内;
然后控制装置(未图示)控制第三驱动装置70的活塞杆复位缩回,并控制第一驱动装置30工作,驱动货叉3抬升至预定的位置;
最后控制装置(未图示)控制水平驱动装置4的输出轴反转,驱动横梁2复位,退出集装箱内;该过程,若滚轮51的底面高于纵向输送装置7的顶面,则第二支撑架5无需复位,若低于,则控制装置(未图示)还需先控制第一旋转驱动装置6的活塞杆复位缩回,将第二支撑架5和滚轮51向上旋转复位,最后再控制水平驱动装置4驱动横梁2复位;
横梁2复位后,控制装置(未图示)最后控制第一驱动装置30驱动货叉3复位至第一低点。
同理,卸货时,货叉3先将集装箱内的货物叉起,此时货物放置在托盘上,货叉3将托盘叉起,从而将货物叉起,后放置在纵向输送装置7上,由纵向输送装置输7送走即可,货物可从纵向输送装置7上直接叉下来,或对接至横向输送装置8,或其它输送设备输送走。卸货时的运动轨迹可根据需求去预设即可。
虽然以上描述了本发明的具体实施方式,但是熟悉本技术领域的技术人员应当理解,我们所描述的具体的实施例只是说明性的,而不是用于对本发明的范围的限定,熟悉本领域的技术人员在依照本发明的精神所作的等效的修饰以及变化,都应当涵盖在本发明的权利要求所保护的范围内。
起点商标作为专业知识产权交易平台,可以帮助大家解决很多问题,如果大家想要了解更多知产交易信息请点击 【在线咨询】或添加微信 【19522093243】与客服一对一沟通,为大家解决相关问题。
此文章来源于网络,如有侵权,请联系删除


