一种面向大型航天器薄壁舱体的高精度调姿装备的制作方法



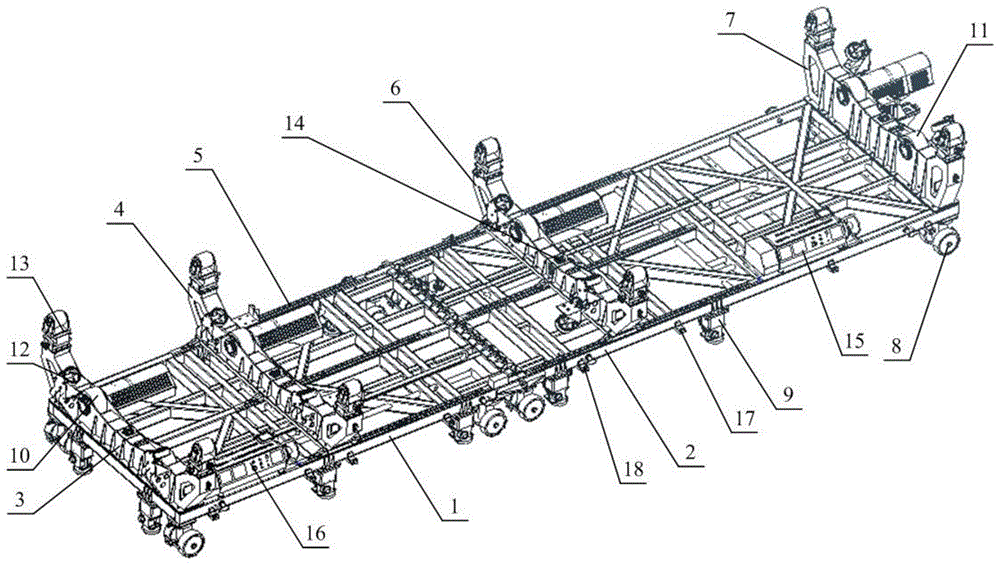
本发明涉及航天器总装的地面机械支持装备领域,对大型航天器薄壁舱体进行高精度姿态调整、长期停放及快速转运,具体涉及一种面向大型航天器薄壁舱体的高精度调姿装备。
背景技术:
在大型航天器的总装和测试过程中,舱体尺寸、重量不断增大,装配复杂程度日益提高,为了将各个分系统的载荷设备可靠地固定到预定位置并采用电缆、导管等将其有效连接,在装配大厅内各分段舱体的姿态需进行高精度调整,并能够在不同的实验区域、指定工位进行长期停放和快速转运。
现有技术中,传统的舱体调姿装备存在如下问题:
第一、舱体的尺寸、重量在总装过程中发生变化,传统的单一设备扩展性不足、通用性不高,无法适应航天器多舱体并行的总装过程工况多变性。
第二、薄壁舱体自身为弱刚性结构,传统的首尾两端支撑、滚转方式存在引发大型舱体扭曲、变形的风险。
第三、舱体内、外载荷设备的种类多、空间占用比重大,在狭小空间、有限区域内的舱体限位采取固定式易引发磕碰,存在损伤载荷设备、影响舱体精度的风险。
技术实现要素:
本发明解决的技术问题是:克服现有技术的不足,本发明提供了一种面向大型航天器薄壁舱体的高精度调姿装备,能够同时满足多个型号大重量、大尺寸薄壁舱体的安全、高效、高精度的总装和测试工作需求,实现不同型号、不同直径、不同高度舱体在装配大厅内的高精度滚转姿态调整,并可进行长期停放、快速转运,提高了航天器总装、测试过程中的操作效率,保证了航天器总装的质量。
本发明的目的在于提供以下技术方案:一种面向大型航天器薄壁舱体的高精度调姿装备,包括第一舱体平台、第二舱体平台、第一固定托架组件、第二移动托架组件、导轨滑块组件、第三移动托架组件、第四固定托架组件、万向脚轮、调节支腿、主动执行机构、随动执行机构、轴向限位机构、辅助支撑装置、位置反馈组件、第一控制系统、第二控制系统、转运结构和吊装结构;其中,第一舱体平台上分别装有用于薄壁舱体第一前端环状单元支撑的第一固定托架组件、用于薄壁舱体第一后端环状单元支撑的第二移动托架组件、用于第二移动托架组件沿舱体轴线方向位置调整的导轨滑块组件、用于舱体在装配大厅内快速转运的万向脚轮、用于舱体高度调整和俯仰调整的调节支腿、用于舱体气浮转运或电动转运的转运结构、用于自身吊装转运的吊装结构和用于舱体姿态调整的第一控制系统;
第二舱体平台上分别装有用于薄壁舱体第二前端环状单元支撑的第三移动托架组件、用于薄壁舱体第二后端环状单元支撑的第四固定托架组件、用于第三移动托架组件沿舱体轴线方向位置调整的导轨滑块组件、用于舱体在装配大厅内快速转运的万向脚轮、用于舱体高度调整和俯仰调整的调节支腿、用于舱体气浮转运或电动转运的转运结构、用于自身吊装转运的吊装结构和第二控制系统;第一固定托架组件、第二移动托架组件、第三移动托架组件、第四固定托架组件上分别装有用于薄壁舱体滚转驱动的主动执行机构一套、用于薄壁舱体滚转随动的随动执行机构一套、用于舱体滚转过程中端面限位的轴向限位机构两套、用于舱体滚转过程中防侧滚的辅助支撑装置两套、用于舱体滚转线速度实时采集的位置反馈组件一套。
第一舱体平台采用矩形钢管焊接结构,局部焊接筋板进行加强,成为具有封闭结构的整体结构件;第一舱体平台焊后进行整体组合加工,作为接口安装基准面;第一舱体平台的下表面焊接万向脚轮、调节支腿、转运结构的接口,上表面焊接第一固定托架组件、导轨滑块组件的接口,宽度方向上的一端焊接第二舱体平台的对接接口;第一舱体平台在间距5390mm相对于质心对称位置设置吊装结构,用于装备自身的吊装转运。
第二舱体平台采用矩形钢管焊接结构,局部焊接筋板进行加强,成为具有封闭结构的整体结构件;第二舱体平台焊后进行整体组合加工,作为接口安装基准面;第二舱体平台的下表面焊接万向脚轮、调节支腿、转运结构的接口,上表面焊接第四固定托架组件、导轨滑块组件的接口,宽度方向上的一端焊接第一舱体平台的对接接口;第二舱体平台在间距6570mm相对于质心对称位置设置吊装结构,用于装备自身的吊装转运。
所述第一固定托架组件包括第一基座底板、第一前支撑立板、第一后支撑立板、第一顶板和若干第一筋板;第一固定托架组件采用厚度20mm的q235或q345钢板焊接而成,在所有焊接工作完成后采用组合加工的方法保证整体精度;第一前支撑立板设有主动执行机构和随动执行机构的连接孔,第一后支撑立板设有主动执行机构和随动执行机构的连接孔;第一前支撑立板上主动执行机构连接孔与第一后支撑立板上主动执行机构连接孔共轴,共轴轴线平行于第一基座底板;第一前支撑立板上随动执行机构连接孔与第一后支撑立板上随动执行机构连接孔共轴,共轴轴线平行于第一基座底板和第一前支撑立板、第一后支撑立板上的主动执行机构连接孔轴线;第一基座底板为第一固定托架组件与第一舱体平台的固定连接接口;第一顶板上设有轴向限位机构的固定连接接口、辅助支撑装置的固定连接接口;第一固定托架组件的中间设有位置反馈组件的固定连接接口。
所述第二移动托架组件包括第二滑块安装座、第二基座底板、第二前支撑立板、第二后支撑立板、第二顶板和若干第二筋板;第二移动托架组件采用厚度20mm的q235或q345钢板焊接而成,在所有焊接工作完成后采用组合加工的方法保证整体精度;第二前支撑立板设有主动执行机构和随动执行机构的连接孔,第二后支撑立板设有主动执行机构和随动执行机构的连接孔;第二前支撑立板上主动执行机构连接孔与第二后支撑立板上主动执行机构连接孔共轴,且与第一固定托架组件的主动执行机构连接孔共轴,共轴轴线平行于第二基座底板;第二前支撑立板上随动执行机构连接孔与第二后支撑立板上随动执行机构)连接孔共轴,且与第一固定托架组件的随动执行机构连接孔共轴,共轴轴线平行于基座底板和第二前支撑立板、第二后支撑立板上的主动执行机构连接孔的轴线;第二滑块安装座通过导轨滑块组件与第一舱体平台连接,实现第二移动托架组件在第一舱体平台上沿舱体轴线方向的位置调整,通过导轨限位块实现第二移动托架组件在第一舱体平台上沿着舱体轴线方向上的固定,从而适应不同长度的薄壁舱体或者整舱的总装需求;第二顶板上设有轴向限位机构的固定连接接口以及辅助支撑装置的固定连接接口;第二移动托架组件的中间设有位置反馈组件的固定连接接口;第二移动托架组件上设置沿着舱体轴向双方向的轴向限位机构连接接口,分别适用于第一舱体平台单独使用,或者第一舱体平台与第二舱体平台在双平台对接口使用工况。
所述第三移动托架组件包括第三滑块安装座、第三基座底板、第三前支撑立板、第三后支撑立板、第三顶板和若干第三筋板;第三移动托架组件采用厚度20mm的q235或q345钢板焊接而成,在所有焊接工作完成后采用组合加工的方法保证整体精度;第三前支撑立板设有主动执行机构和随动执行机构的连接孔,第三后支撑立板设有主动执行机构和随动执行机构的连接孔;第三前支撑立板上主动执行机构连接孔与第三后支撑立板上主动执行机构连接孔共轴,共轴轴线平行于第三基座底板;第三前支撑立板上随动执行机构连接孔与第三后支撑立板上随动执行机构连接孔共轴,共轴轴线平行于第三基座底板和第三前支撑立板、第三后支撑立板上的主动执行机构连接孔的轴线;在第一舱体平台与第二舱体平台通过双平台对接接口进行定位组合后,第三移动托架组件的主动执行机构连接孔与第一固定托架组件的主动执行机构连接孔、第二移动托架组件的主动执行机构连接孔均共轴,共轴轴线平行于第三基座底板;在第一舱体平台与第二舱体平台通过双平台对接接口进行定位组合后,第三移动托架组件的随动执行机构连接孔与第一固定托架组件的随动执行机构连接孔、第二移动托架组件的随动执行机构连接孔均共轴,共轴轴线平行于第三基座底板;第三滑块安装座通过导轨滑块组件与第二舱体平台连接,实现第三移动托架组件在第二舱体平台上沿舱体轴线方向的位置调整,通过导轨限位块实现第三移动托架组件在第二舱体平台上沿着舱体轴线方向上的固定,从而适应不同长度的薄壁舱体或者整舱的总装需求;第三顶板上设有轴向限位机构的固定连接接口以及辅助支撑装置的固定连接接口;第三移动托架组件的中间设有位置反馈组件的固定连接接口。
所述第四固定托架组件包括第四基座底板、第四前支撑立板、第四后支撑立板、第四顶板和若干第四筋板;第四固定托架组件采用厚度20mm的q235或q345钢板焊接而成,在所有焊接工作完成后采用组合加工的方法保证整体精度;第四前支撑立板设有主动执行机构和随动执行机构的连接孔、第四后支撑立板设有主动执行机构和随动执行机构的连接孔;第四前支撑立板上主动执行机构连接孔与第四后支撑立板上主动执行机构连接孔共轴,共轴轴线平行于第四基座底板、第三移动托架组件的主动执行机构连接孔;第四前支撑立板上随动执行机构连接孔与第四后支撑立板上随动执行机构连接孔共轴,共轴轴线平行于基座底板和第四前支撑立板、第四后支撑立板上的主动执行机构)连接孔轴线,且与第三移动托架组件的随动执行机构连接孔平行;第四基座底板为第四固定托架组件与第二舱体平台的固定连接接口;第四顶板上设有轴向限位机构、辅助支撑装置的固定连接接口;第四固定托架组件的中间设有位置反馈组件的固定连接接口。
所述万向脚轮包括脚轮座、立柱、方向锁、面刹、轮轴和包胶轮体;脚轮座为万向脚轮的安装接口,用于与第一舱体平台或第二舱体平台进行螺接;方向锁实现万向脚轮的转向锁定,面刹为双轮同时刹车装置,同时还配有弹簧装置,使得万向脚轮能够防震和自动平衡地面的不平度。
所述调节支腿包括支撑法兰、球铰、丝杠机构、壳体、尾罩支架和驱动组件;调节支腿采用丝杠运动式,工作原理为蜗轮驱动丝杠进行直线运动,运行过程中丝杠不旋转;支撑法兰通过球铰与丝杠连接,且支撑法兰与地面接触的一侧粘贴5mm厚硅橡胶垫和0.1mm特氟隆胶带纸,用于降低厂区地面引发压痕、凹坑的影响;调节支腿的高度进行装备的俯仰调整,实现舱体的姿态调整。
所述主动执行机构包括第一摩擦轮、主动轮轴、第一角接触球轴承、第一轴承座、第一轴承端盖、膜片联轴器、行星齿轮减速器和伺服电机;每个第一摩擦轮两端使用第一角接触球轴承支撑,第一角接触球轴承承受较大径向载荷;膜片联轴器将主动轮轴与行星齿轮减速器进行同轴安装,伺服电机直接安装在行星齿轮减速器的输入端;第一轴承座固定安装在各托架组件前支撑立板、后支撑立板的主动执行机构连接孔内。
所述随动执行机构包括第二摩擦轮、随动轮轴、第二角接触球轴承、第二轴承座和第二轴承端盖;第二轴承座固定安装在各托架组件的前支撑立板、后支撑立板的随动执行机构连接孔内;第二摩擦轮与主动执行机构的第一摩擦轮一致。
轴向限位机构包括定向轮、斜角安装基座;定向轮垂直于舱体轴线安装,采用抗冲击型固定式可随动平轮,轮子表面包覆聚氨酯,定向轮的轮面宽度和安装高度匹配于舱体的前端、后端环状单元;每个托架组件上设置两套轴向限位机构,在各托架组件宽度方向上的左右两侧对称布置。
辅助支撑装置包括下滑座组件、中滑座组件、上辅助组件和辅助轮;辅助支撑装置位于托架组件的顶板上部左右两侧,对舱体前端环状单元或后端环状单元的环面形成112°的包角,防止薄壁舱体在落放、滚转或转运时出现侧滚;辅助支撑装置为二自由度可调节结构,可沿着舱体轴线方向或水平面内垂直于舱体轴线方向进行辅助轮位置调整;当舱体在装备上落放平稳后,调整辅助支撑装置与舱体前端环状单元或后端环状单元的环面小间隙贴合,从而实现对舱体的辅助支撑与可靠停放。
位置反馈组件包括小摩擦轮、角度传感器、联轴器、支架、弹簧和底座;小摩擦轮采用尼龙材料,通过弹簧保证小摩擦轮与舱体前端环状单元或后端环状单元的外环面贴紧,小摩擦轮实时随着舱体环状单元的转动而运动,实现对舱体滚转线速度的数据采集和比较;角度传感器与小摩擦轮同轴安装,实时测量舱体的旋转速度和滚转状态监控;位置反馈组件在各托架组件的中间位置分别安装一套。
本发明与现有技术相比的有益效果是:
【1】本发明在实现大尺寸、薄壁舱体的高精度姿态调整、长期停放、快速转运基础上,极大地扩展了装备对于不同尺寸、重量的舱体的通用性,能够快速转换并适用于五种舱体、三种组合舱体的工况,提高了装备对大尺寸薄壁舱体的总装过程通用性。
【2】本发明有效改善了薄壁舱体在调姿、停放、转运时的受力状态,降低了舱体扭曲、变形的风险,避免了差速回转造成舱体变形的风险,提高了航天器总装过程中的安全性和可靠性。
【3】本发明整体结构紧凑,高精度的滚转定位功能有助于航天器有效载荷的高效对接安装,能够更好的适应载人航天和深空探测快速发展对地面机械支持设备的需求。
附图说明
图1示出本发明一种面向大型航天器薄壁舱体的高精度调姿装备的结构示意图;
图2示出本发明一种优选实施方式中第一舱体平台的结构示意图;
图3示出本发明一种优选实施方式中第二舱体平台的结构示意图;
图4示出本发明一种优选实施方式中第一固定托架组件的结构示意图;
图5示出本发明一种优选实施方式中第二移动托架组件的结构示意图;
图6示出本发明一种优选实施方式中第四固定托架组件的结构示意图;
图7示出本发明一种优选实施方式中主动执行机构的结构示意图;
图8示出本发明一种优选实施方式中辅助支撑装置的结构示意图;
图9示出本发明一种优选实施方式中位置反馈组件的结构示意图。
具体实施方式
下面通过附图和实施例对本发明进一步详细说明。通过这些说明,本发明的特点和优点将变得更为清楚明确。
如图1所示,本发明提供了一种面向大型航天器薄壁舱体的高精度调姿装备,该装备包括第一舱体平台1、第二舱体平台2、第一固定托架组件3、第二移动托架组件4、导轨滑块组件5、第三移动托架组件6、第四固定托架组件7、万向脚轮8、调节支腿9、主动执行机构10、随动执行机构11、轴向限位机构12、辅助支撑装置13、位置反馈组件14、第一控制系统15、第二控制系统16、转运结构17、吊装结构18;其中,
第一舱体平台1上分别装有用于薄壁舱体第一前端环状单元支撑的第一固定托架组件3、用于薄壁舱体第一后端环状单元支撑的第二移动托架组件4、用于第二移动托架组件4沿舱体轴线方向位置调整的导轨滑块组件5、用于舱体在装配大厅内快速转运的万向脚轮8、用于舱体高度调整和俯仰调整的调节支腿9、用于舱体气浮转运或电动转运的转运结构17、用于自身吊装转运的吊装结构18和用于舱体姿态调整的第一控制系统15;
第二舱体平台2上分别装有用于薄壁舱体第二前端环状单元支撑的第三移动托架组件6、用于薄壁舱体第二后端环状单元支撑的第四固定托架组件7、用于第三移动托架组件6沿舱体轴线方向位置调整的导轨滑块组件5、用于舱体在装配大厅内快速转运的万向脚轮8、用于舱体高度调整和俯仰调整的调节支腿9、用于舱体气浮转运或电动转运的转运结构17、用于自身吊装转运的吊装结构18和第二控制系统16;第一固定托架组件3、第二移动托架组件4、第三移动托架组件6、第四固定托架组件7上分别装有用于薄壁舱体滚转驱动的主动执行机构10一套、用于薄壁舱体滚转随动的随动执行机构11一套、用于舱体滚转过程中端面限位的轴向限位机构12两套、用于舱体滚转过程中防侧滚的辅助支撑装置13两套、用于舱体滚转线速度实时采集的位置反馈组件14一套。
如图2所示,第一舱体平台1采用矩形钢管焊接结构,局部焊接筋板进行加强,成为具有封闭结构的整体结构件;第一舱体平台1焊后进行整体组合加工,作为接口安装基准面;第一舱体平台1的下表面焊接万向脚轮8、调节支腿9、转运结构17的接口,上表面焊接第一固定托架组件3、导轨滑块组件5的接口,宽度方向上的一端焊接第二舱体平台2的对接接口;第一舱体平台1在间距5390mm相对于质心对称位置最好量化设置吊装结构18,用于装备自身的吊装转运。
如图3所示,第二舱体平台2采用矩形钢管焊接结构,局部焊接筋板进行加强,成为具有封闭结构的整体结构件;第二舱体平台2焊后进行整体组合加工,作为接口安装基准面;第二舱体平台2的下表面焊接万向脚轮8、调节支腿9、转运结构17的接口,上表面焊接第四固定托架组件7、导轨滑块组件5的接口,宽度方向上的一端焊接第一舱体平台1的对接接口;第二舱体平台2在间距6570相对于质心对称位置设置吊装结构18,用于装备自身的吊装转运。
如图4所示,第一固定托架组件3第一基座底板31、第一前支撑立板32、第一后支撑立板33、第一顶板34和若干第一筋板35;第一固定托架组件3采用厚度20mm的q235或q345钢板焊接而成,在所有焊接工作完成后采用组合加工的方法保证整体精度;第一前支撑立板32上设有主动执行机构10和随动执行机构11的连接孔,第一后支撑立板33上设有主动执行机构10和随动执行机构11的连接孔;第一前支撑立板32上主动执行机构10连接孔与第一后支撑立板33上主动执行机构10连接孔共轴,共轴轴线平行于第一基座底板31;第一前支撑立板32上随动执行机构11连接孔与第一后支撑立板33上随动执行机构11连接孔共轴,共轴轴线平行于第一基座底板31和第一前支撑立板32、第一后支撑立板33上的主动执行机构10连接孔轴线;第一基座底板31为第一固定托架组件3与第一舱体平台1的固定连接接口;第一顶板34上设有轴向限位机构12的固定连接接口、辅助支撑装置13的固定连接接口;第一固定托架组件3的中间设有位置反馈组件14的固定连接接口。
如图5所示,第二移动托架组件4包括第二滑块安装座41、第二基座底板42、第二前支撑立板43、第二后支撑立板44、第二顶板45和若干第二筋板46;第二移动托架组件4采用厚度20mm的q235或q345钢板焊接而成,在所有焊接工作完成后采用组合加工的方法保证整体精度;第二前支撑立板43上设有主动执行机构10和随动执行机构11的连接孔,第二后支撑立板44上设有主动执行机构10和随动执行机构11的连接孔;第二前支撑立板43上主动执行机构10连接孔与第二后支撑立板44上主动执行机构10连接孔共轴,且与第一固定托架组件3的主动执行机构10连接孔共轴,共轴轴线平行于第二基座底板42;第二前支撑立板43上随动执行机构11连接孔与第二后支撑立板44上随动执行机构11连接孔共轴,且与第一固定托架组件3的随动执行机构11连接孔共轴,共轴轴线平行于基座底板42和第二前支撑立板43、第二后支撑立板44上的主动执行机构10连接孔的轴线;第二滑块安装座41通过导轨滑块组件5与第一舱体平台1连接,实现第二移动托架组件4在第一舱体平台1上沿舱体轴线方向的位置调整,通过导轨限位块实现第二移动托架组件4在第一舱体平台1上沿着舱体轴线方向上的固定,从而适应不同长度的薄壁舱体或者整舱的总装需求;第二顶板45上设有轴向限位机构12的固定连接接口以及辅助支撑装置13的固定连接接口;第二移动托架组件4的中间设有位置反馈组件14的固定连接接口;第二移动托架组件4上设置沿着舱体轴向双方向的轴向限位机构12连接接口,分别适用于第一舱体平台1单独使用,或者第一舱体平台1与第二舱体平台2在双平台对接口使用工况。
第三移动托架组件6包括第三滑块安装座61、第三基座底板62、第三前支撑立板63、第三后支撑立板64、第三顶板65和若干第三筋板66;第三移动托架组件6采用厚度20mm的q235或q345钢板焊接而成,在所有焊接工作完成后采用组合加工的方法保证整体精度;第三前支撑立板63设有主动执行机构10和随动执行机构11的连接孔,第三后支撑立板64设有主动执行机构10和随动执行机构11的连接孔;第三前支撑立板63上主动执行机构10连接孔与第三后支撑立板64上主动执行机构10连接孔共轴,共轴轴线平行于第三基座底板62;第三前支撑立板63上随动执行机构11连接孔与第三后支撑立板64上随动执行机构11连接孔共轴,共轴轴线平行于第三基座底板62和第三前支撑立板63、第三后支撑立板64上的主动执行机构10连接孔的轴线;在第一舱体平台1与第二舱体平台2通过双平台对接接口进行定位组合后,第三移动托架组件6的主动执行机构10连接孔与第一固定托架组件3的主动执行机构10连接孔、第二移动托架组件4的主动执行机构10连接孔均共轴,共轴轴线平行于第三基座底板62;在第一舱体平台1与第二舱体平台2通过双平台对接接口进行定位组合后,第三移动托架组件6的随动执行机构11连接孔与第一固定托架组件3的随动执行机构11连接孔、第二移动托架组件4的随动执行机构11连接孔均共轴,共轴轴线平行于第三基座底板62;第三滑块安装座61通过导轨滑块组件5与第二舱体平台2连接,实现第三移动托架组件6在第二舱体平台2上沿舱体轴线方向的位置调整,通过导轨限位块实现第三移动托架组件6在第二舱体平台2上沿着舱体轴线方向上的固定,从而适应不同长度的薄壁舱体或者整舱的总装需求;第三顶板65上设有轴向限位机构12的固定连接接口以及辅助支撑装置13的固定连接接口;第三移动托架组件6的中间设有位置反馈组件14的固定连接接口。
如图6所示,第四固定托架组件7包括第四基座底板71、第四前支撑立板72、第四后支撑立板73、第四顶板74和若干第四筋板75;第四固定托架组件7采用厚度20mm的q235或q345钢板焊接而成,在所有焊接工作完成后采用组合加工的方法保证整体精度;第四前支撑立板72设有主动执行机构10和随动执行机构11的连接孔、第四后支撑立板73设有主动执行机构10和随动执行机构11的连接孔;第四前支撑立板72上主动执行机构10连接孔与第四后支撑立板73上主动执行机构10连接孔共轴,共轴轴线平行于第四基座底板71、第三移动托架组件6的主动执行机构10连接孔;第四前支撑立板72上随动执行机构11连接孔与第四后支撑立板73上随动执行机构11连接孔共轴,共轴轴线平行于基座底板71和第四前支撑立板72、第四后支撑立板73上的主动执行机构10连接孔轴线,且与第三移动托架组件6的随动执行机构11连接孔平行;第四基座底板71为第四固定托架组件7与第二舱体平台2的固定连接接口;第四顶板74上设有轴向限位机构12、辅助支撑装置13的固定连接接口;第四固定托架组件7的中间设有位置反馈组件14的固定连接接口。
万向脚轮8包括脚轮座81、立柱82、方向锁83、面刹84、轮轴85和包胶轮体86;脚轮座81为万向脚轮8的安装接口,可方便的与第一舱体平台1或第二舱体平台2进行螺接。方向锁83可快捷的实现万向脚轮8的转向锁定,面刹84为双轮同时刹车装置,同时还配有弹簧装置,使得万向脚轮8能够防震和自动平衡地面的不平度。
调节支腿9包括支撑法兰91、球铰92、丝杠机构93、壳体94、尾罩支架95和驱动组件96;调节支腿9采用丝杠运动式,其工作原理为蜗轮驱动丝杠进行直线运动,运行过程中丝杠不旋转。支撑法兰91通过球铰92与丝杠连接,且支撑法兰91与地面接触的一侧粘贴5mm厚硅橡胶垫和0.1mm特氟隆胶带纸,有效降低厂区地面引发压痕、凹坑的影响。调节支腿9的高度进行装备的俯仰调整,从而实现舱体的姿态调整。
如图7所示,主动执行机构10包括第一摩擦轮101、主动轮轴102、第一角接触球轴承103、第一轴承座104、第一轴承端盖105、膜片联轴器106、行星齿轮减速器107和伺服电机108;每个第一摩擦轮101两端使用第一角接触球轴承103支撑,第一角接触球轴承103承受较大径向载荷;膜片联轴器106将主动轮轴102与行星齿轮减速器107进行同轴安装,伺服电机108直接安装在行星齿轮减速器107的输入端;第一轴承座104固定安装在各托架组件前支撑立板、后支撑立板的主动执行机构10连接孔内。
随动执行机构11包括第二摩擦轮111、随动轮轴112、第二角接触球轴承113、第二轴承座114和第二轴承端盖115;第二轴承座114固定安装在各托架组件的前支撑立板、后支撑立板的随动执行机构11连接孔内;第二摩擦轮111与主动执行机构10的第一摩擦轮101基本一致。
轴向限位机构12包括定向轮121、斜角安装基座122。定向轮121垂直于舱体轴线安装,采用抗冲击型固定式可随动平轮,轮子表面包覆聚氨酯,定向轮121的轮面宽度和安装高度匹配于舱体的前端、后端环状单元。每个托架组件上设置两套轴向限位机构12,在各托架组件宽度方向上的左右两侧对称布置。
如图8所示,辅助支撑装置13包括下滑座组件131、中滑座组件132、上辅助组件133和辅助轮134;辅助支撑装置13位于托架组件的顶板34/45/65/74上部左右两侧,对舱体前端环状单元或后端环状单元的环面形成112°的包角,防止薄壁舱体在落放、滚转或转运时出现侧滚。辅助支撑装置13为二自由度可调节结构,可沿着舱体轴线方向或水平面内垂直于舱体轴线方向进行辅助轮134位置调整。当舱体在装备上落放平稳后,可以调整辅助支撑装置13与舱体前端环状单元或后端环状单元的环面小间隙贴合,从而实现对舱体的辅助支撑与可靠停放。
如图9所示,位置反馈组件14包括小摩擦轮141、角度传感器142、联轴器143、支架144、弹簧145和底座146。小摩擦轮141采用尼龙材料,通过弹簧145保证小摩擦轮141与舱体前端环状单元或后端环状单元的外环面贴紧,小摩擦轮141实时随着舱体环状单元的转动而运动,实现对舱体滚转线速度的数据采集和比较。角度传感器142与小摩擦轮141同轴安装,实时测量舱体的旋转速度和滚转状态监控。位置反馈组件14在各托架组件3/4/6/7的中间位置分别安装一套。
本发明用于大型航天器薄壁舱体的精确调姿、长期停放的多舱体并行自适应方法,也可扩展应用于航空航天领域中的舱体或星体、武器装备领域的导弹或火箭等部组件上架、调姿、对接等装配过程中,通过装备使用状态调整和控制系统指令改变,可适应部组件的变形,降低装配、对接过程中的内应力隐患。
以上结合了优选的实施方式对本发明进行了详细的描述和说明,但应该指明的是,这些实施方式仅是范例性的,仅起到说明性的作用。在此基础上,可以对本发明进行多种替换和改进,这些均落入本发明的保护范围内。
起点商标作为专业知识产权交易平台,可以帮助大家解决很多问题,如果大家想要了解更多知产交易信息请点击 【在线咨询】或添加微信 【19522093243】与客服一对一沟通,为大家解决相关问题。
此文章来源于网络,如有侵权,请联系删除


