一种复合材料壳体及飞行器的制作方法



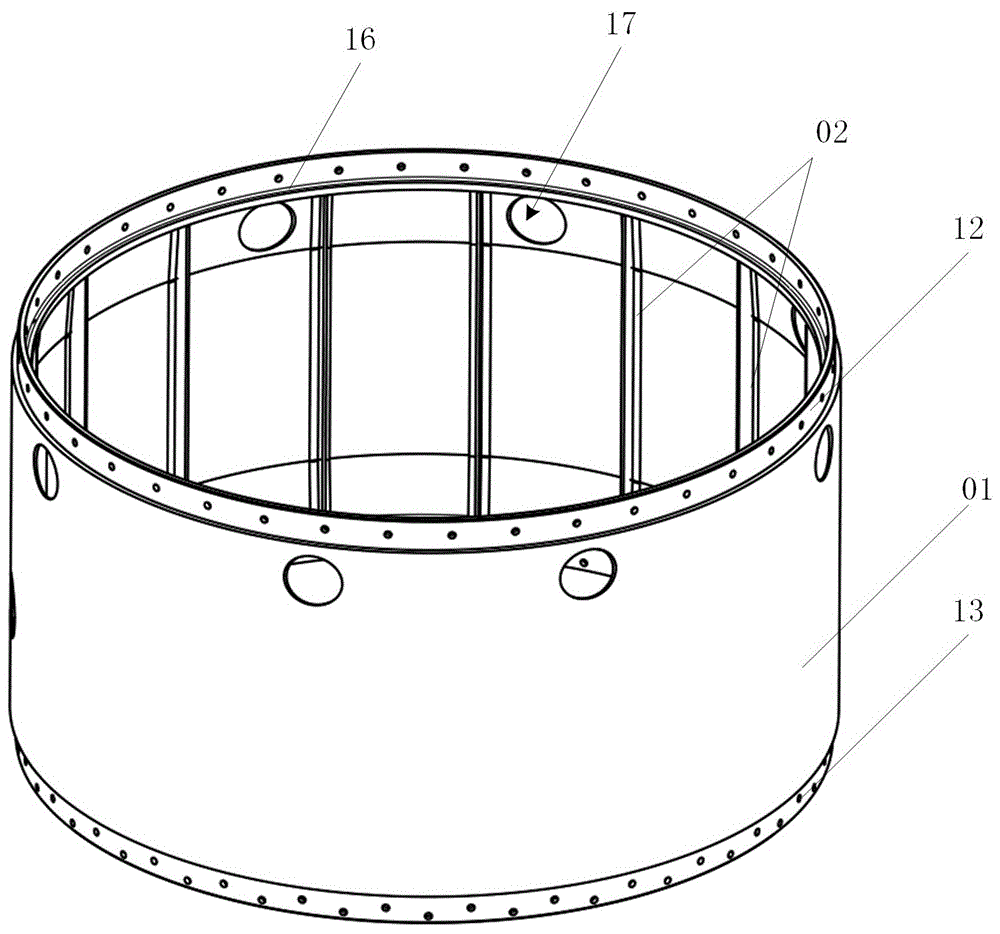
本实用新型涉及高端设备制造技术领域,更具体地说,是涉及一种复合材料壳体及飞行器。
背景技术:
飞行器(例如火箭或导弹等)的舱段壳体结构设计一般有光筒结构、蒙皮桁条结构和网格加筋结构三类。光筒结构工艺最简单,但承载效率最低。蒙皮桁条结构舱段的可设计性强、稳定性好,轴向载荷承载效率最高,适用于按稳定性和应力强度、刚度设计的结构,具有较好的重量优势。作为主要承受轴向载荷的舱段壳体,既要保证应力强度和刚度要求,同时如何进一步减重以提升导弹射程或是火箭的有效载荷。
为此,在复合材料发展已经相当成熟的当下,如何更为经济的提升舱段壳体的载荷效率,是本领域技术人员正致力解决的技术难题。
技术实现要素:
鉴于上述现有技术中的问题,本实用新型的目的在于提供一种复合材料壳体及飞行器。
第一方面,本实用新型提供的复合材料壳体,包括:复合材料光壳和若干条复合材料桁条,所述复合材料光壳包括:蒙皮区域,位于所述蒙皮区域两端的上端框区域和下端框区域、由上端框区域向蒙皮区域过渡延伸的上端框过渡区、由下端框区域向蒙皮区域过渡延伸的下端框过渡区、分别沿所述上端框区域和下端框区域内侧面周向设置的环向加强筋区域,所述蒙皮区域、上端框区域、下端框区域、上端框过渡区、下端框过渡区和环向加强筋区域为环氧树脂基碳纤维单向带一体铺设固化成型结构,所述复合材料桁条沿所述复合材料光壳的轴向共固化成型的连接于所述复合材料光壳的内壁,各所述复合材料桁条相间隔布设。
在一些实施方案中,所述复合材料桁条为t型桁条,所述t型桁条包括缘板和腹板,所述腹板贴合于所述复合材料光壳的内壁,所述缘板垂直于所述腹板。
在一些实施方案中,所述缘板至少包括10层环氧树脂基碳纤维单向带,且所述10层环氧树脂基碳纤维单向带的铺层顺序为[±45/0/90/0]s;所述腹板至少包括16层环氧树脂基碳纤维单向带,且所述16层环氧树脂基碳纤维单向带的铺层顺序为[±45/0/90/0/±45/0]s。
在一些实施方案中,在所述复合材料光壳中,所述蒙皮区域包括第一层和第二层,所述第一层中的所述环氧树脂基碳纤维单向带沿所述复合材料光壳所在外侧连续经过上端框过渡区域至上端框区域位置,所述第二层中的所述环氧树脂基碳纤维单向带沿所述复合材料光壳所在内侧连续经过下端框过渡区,并在绕过所述环向加强筋区域后汇合。
在一些实施方案中,所述蒙皮区域至少包括14层环氧树脂基碳纤维单向带;所述第一层包括7层环氧树脂基碳纤维单向带,所述第二层包括7层环氧树脂基碳纤维单向带,所述第一层和第二层中的所述环氧树脂基碳纤维单向带为对称结构,且所述第一层和第二层的所述环氧树脂基碳纤维单向带的铺层顺序为[±45/0/90/0/90/0]。
在一些实施方案中,所述第二层中的所述环氧树脂基碳纤维单向带沿所述复合材料光壳所在内侧连续经过下端框过渡区并在绕过所述环向加强筋区域后汇合,具体包括:所述第二层中的7层环氧树脂基碳纤维单向带在沿所述复合材料光壳所在内侧连续经过下端框过渡区至所述环向加强筋区域位置分开,其中2层环氧树脂基碳纤维单向带绕过环向加强筋区域后与另外5层环氧树脂基碳纤维单向带在环向加强筋内侧汇合。
在一些实施方案中,所述上端框区域和下端框区域各包括52层环氧树脂基碳纤维单向带,所述52层环氧树脂基碳纤维单向带包括所述蒙皮区域所在第一层和第二层的14层环氧树脂基碳纤维单向带,其中,剩余38层环氧树脂基碳纤维单向带在所述上端框区域和下端框区域至所述蒙皮区域各进行丢层铺设,对应形成所述上端框过渡区域和下端框过渡区域,且所述52层环氧树脂基碳纤维单向带的铺层顺序为[±45/0/90/0/90/0/(±45/0/90/0)3/(±45/0/90)]s。
在一些实施方案中,所述环向加强筋区域采用环氧树脂基碳纤维单向带缠绕填充,且每层环氧树脂基碳纤维单向带缠绕填充的铺设顺序为[0]。
在一些实施方案中,在沿所述复合材料光壳周向上贯通开设多个风管出口。
第二方面,本实用新型提供的飞行器,包括第一方面中任一实施方案中的所述复合材料壳体。
本实用新型的有益效果在于:提供的复合材料壳体主结构整体成型,可以实现产品减重30%以上;同时,利用复合材料桁条预成型与壳体共固化装配,保证了壳体的强度和刚性。与此同时,这种一体成型结构有效减少了桁条装配所需紧固件和装配,使得加工的时间周期得以缩短,从而降低加工成本。
关于本实用新型在其他实施方案中的有益效果,将在以下具体实施例中予以详细说明。
附图说明
为了更清楚地说明本实用新型实施例中的技术方案,下面将对实施例或现有技术描述中所需要使用的附图作简单地介绍,显而易见地,下面描述中的附图仅仅是本实用新型的一些实施例,对于本领域普通技术人员来讲,在不付出创造性劳动的前提下,还可以根据这些附图获得其他的附图。
图1为本实用新型在一实施例中提供的复合材料壳体的立体结构图;
图2为本实用新型在图1所示复合材料壳体的剖面示意图;
图3为本实用新型在图1所示复合材料壳体中上端框区域至蒙皮区域的剖面示意图;
图4为本实用新型在图1所示复合材料壳体中复合材料桁条的立体结构图;
图5为本实用新型在图1所示复合材料壳体中复合材料桁条的截面示意图。
其中,图中各附图标记如下:
01-复合材料光壳;
11-蒙皮区域;
111-第一层;
112-第二层;
12-上端框区域;
13-下端框区域;
14-上端框过渡区域;
15-下端框过渡区域;
16-环向加强筋区域;
17-风管出口;
02-复合材料桁条;
21-缘板;
22-腹板。
具体实施方式
为了使本实用新型所要解决的技术问题、技术方案及有益效果更加清楚明白,以下结合附图及实施例,对本实用新型进行进一步详细说明。应当理解,此处所描述的具体实施例仅用以解释本实用新型,并不用于限定本实用新型。
需要说明的是,当部件被称为“固定于”或“设置于”另一个部件,它可以直接或者间接位于该另一个部件上。当一个部件被称为“连接于”另一个部件,它可以是直接或者间接连接至该另一个部件上。术语“上”、“下”、“左”、“右”、“前”、“后”、“竖直”、“水平”、“顶”、“底”、“内”、“外”等指示的方位或位置为基于附图所示的方位或位置,仅是为了便于描述,不能理解为对本技术方案的限制。术语“第一”、“第二”仅用于便于描述目的,而不能理解为指示或暗示相对重要性或者隐含指明技术特征的数量。“多个”的含义是两个或两个以上,除非另有明确具体的限定。
请参考图1-5,为本实用新型实施例提供的一种复合材料壳体,相比于现有飞行器的舱段结构上的壳体,所述复合材料壳体全部采用复合材料制成,在保证结构具有较好的整体性同时,可以有效降低结构重量。
如图1所示,所述复合材料壳体包括复合材料光壳01和若干条复合材料桁条02。即本实用新型实施例提供的所述复合材料壳体为蒙皮桁条结构。
需要说明的是,蒙皮、桁条、上端框和下端框等特征,均为本领域对于传统工艺制备的舱段结构的壳体的技术特征命名,在本实施例中,由于这些技术特征全部采用的是复合材料来一体成型得到,为了便于本领域技术人员能够更为清楚了解本实用新型的技术方案,所以所述复合材料壳体同样按照传统技术特征所在位置结构进行划分区域,以便于技术方案的描述与理解。
具体的,结合图1-3所示,所述复合材料光壳01包括:蒙皮区域11,位于所述蒙皮区域11两端的上端框区域12和下端框区域13、由上端框区域12向蒙皮区域11过渡延伸的上端框过渡区14、由下端框区域13向蒙皮区域11过渡延伸的下端框过渡区15、分别沿所述上端框区域12和下端框区域13内侧面周向设置的环向加强筋区域16,所述蒙皮区域11、上端框区域12、下端框区域13、上端框过渡区14、下端框过渡区15和环向加强筋区域16为环氧树脂基碳纤维单向带一体铺设固化成型结构。
其中,所述复合材料壳体中的环氧树脂基碳纤维单向带(也可以简称单向带)可以具体选用0.15mm厚t700s/603b环氧树脂基碳纤维单向带。
此外,在图3中,由于在蒙皮11两侧的上端框区域12、上端框过渡区域14和下端框区域13、下端框过渡区域15是相对于蒙皮的对称的相同结构,故仅示出了对称结构中的其中一半。所以,以下将以图3所示的蒙皮区域11、上端框过渡区域14、上端框区域12和加强筋区域来说明复合材料壳体中单向带的铺设位置关系和层级构造。
具体的,在所述复合材料光壳01中,结合图3所示,所述蒙皮区域11包括第一层111和第二层112,所述第一层111中的所述环氧树脂基碳纤维单向带沿所述复合材料光壳01所在外侧连续经过上端框过渡区域14至上端框区域12位置,所述第二层112中的所述环氧树脂基碳纤维单向带沿所述复合材料光壳01所在内侧连续经过上端框过渡区14,并在绕过所述环向加强筋区域16后汇合。
同理,对于下端框过渡区域15、下端框区域13及其上的加强筋区域的构造具有相同的上述结构。即所述蒙皮区域11包括第一层111和第二层112,所述第一层111中的所述环氧树脂基碳纤维单向带沿所述复合材料光壳01所在外侧连续经过下端框过渡区域15至下端框区域13位置,所述第二层112中的所述环氧树脂基碳纤维单向带沿所述复合材料光壳01所在内侧连续经过下端框过渡区15,并在绕过所述环向加强筋区域16后汇合。
更为详细的,在所述蒙皮区域11中,所述蒙皮区域11至少包括14层环氧树脂基碳纤维单向带,其中,所述第一层111包括7层环氧树脂基碳纤维单向带,所述第二层112包括7层环氧树脂基碳纤维单向带,所述第一层111和第二层112中所述环氧树脂基碳纤维单向带的铺设顺序相对称,且所述第一层111和第二层112中所述环氧树脂基碳纤维单向带的铺层顺序可以为[±45/0/90/0/90/0]s。
需要说明的是,在单向带铺设顺序[±45/0/90/0/90/0]s中,依次表示共有+45°、-45°、0°、90°、0°、90°、0°,7层相对于同一个绝对坐标系的不同铺设角度的单向带,其中,“s”表示按照“[]”中的铺设顺序相对称铺设。其中,如何材料壳体中所有复合材料铺设角度都是基于同一绝对坐标系来铺设的。由于上述单向带铺设顺序的表示方式为现有技术,故这里不再赘述。
再具体的,结合图3所示,蒙皮区域11的第一层111和第二层112在进入上端框过渡区域14或下端框过渡区域15后,分别成型于复合材料壳体的外侧面和内侧面。其中,为了增强加强筋区域的强度,所述第二层112中的所述环氧树脂基碳纤维单向带沿所述复合材料光壳01所在内侧连续经过下端框过渡区并在绕过所述环向加强筋区域16后汇合,具体结构可以包括:
所述第二层112中的7层环氧树脂基碳纤维单向带在沿所述复合材料光壳01所在内侧连续经过上端框过渡区和下端框过渡区至所述环向加强筋区域16位置分开铺设,其中表面2层环氧树脂基碳纤维单向带绕过环向加强筋区域16后与另外5层环氧树脂基碳纤维单向带在环向加强筋内侧汇合,即第二侧的底部5层环氧树脂基碳纤维单向带铺设于所述环向加强筋区域16之下,另外2层环氧树脂基碳纤维单向带绕过环向加强筋区域16后与所述底部5层环氧树脂基碳纤维单向带汇合铺设成型。
此外,所述上端框区域12和下端框区域13各包括52层环氧树脂基碳纤维单向带,其中,所述52层环氧树脂基碳纤维单向带包括所述蒙皮区域11所在第一层111和第二层112的14层环氧树脂基碳纤维单向带,剩余的38层环氧树脂基碳纤维单向带在所述上端框区域12和下端框区域13至所述蒙皮区域11各进行丢层铺设,对应形成所述上端框过渡区域14和下端框过渡区域15,其中,所述52层单向带的铺层顺序为[±45/0/90/0/90/0/(±45/0/90/0)3/(±45/0/90)]s。其中,所述“3”表示对括号中的铺层结构重叠3次。
其中,所述环向加强筋区域16采用环氧树脂基碳纤维单向带缠绕填充,且每层环氧树脂基碳纤维单向带缠绕填充的铺设顺序为[0]。
示例性的,在具体实施中,所述蒙皮区域11的厚度可以为2.1mm,所述上端框区域12和下端框区域13的厚度可以为7.8mm。
具体的,结合图4-5所示,在所述复合材料壳体中,所述复合材料桁条02沿所述复合材料光壳01的轴向共固化成型的连接于所述复合材料光壳01的内壁,各所述复合材料桁条02相间隔布设。
其中,所述复合材料桁条02为t型桁条,所述t型桁条包括缘板21和腹板22,所述腹板22贴合于所述复合材料光壳01的内壁,所述缘板21垂直于所述腹板22。本实施例选用t型桁条可以借用环向加强筋区域16的结构来让t型桁条的两端分别共固化连接在所述环向加强筋区域16上,以此来提高复合材料壳体的强度。
再具体的,结合图5所示,在所述t型桁条中:所述缘板21至少包括10层环氧树脂基碳纤维单向带,且所述10层环氧树脂基碳纤维单向带的铺层顺序为[±45/0/90/0]s。此外,所述腹板22至少包括16层环氧树脂基碳纤维单向带,且所述16层环氧树脂基碳纤维单向带的铺层顺序为[±45/0/90/0/±45/0]s。
示例性的,在具体实施中,所述缘板21厚度可以为1.5mm,所述腹板22厚度可以为2.4mm。
另外,再结合图1-2所示,在沿所述复合材料光壳01周向上贯通开设多个风管出口17。该风管出口17的作用在于所述复合材料壳体在装配使用时,作为轨道修正喷火的出口。
综上所述,本实用新型相比于现有技术,其突出贡献在于:复合材料壳体主结构整体成型,可以实现产品减重30%以上;同时,利用复合材料桁条02预成型与壳体共固化装配,保证了壳体的强度和刚性。与此同时,这种一体成型结构有效减少了桁条装配所需紧固件和装配,使得加工的时间周期得以缩短,从而降低加工成本。
以上所述仅为本实用新型的较佳实施例而已,并不用以限制本实用新型,凡在本实用新型的精神和原则之内所作的任何修改、等同替换和改进等,均应包含在本实用新型的保护范围之内。
起点商标作为专业知识产权交易平台,可以帮助大家解决很多问题,如果大家想要了解更多知产交易信息请点击 【在线咨询】或添加微信 【19522093243】与客服一对一沟通,为大家解决相关问题。
此文章来源于网络,如有侵权,请联系删除


