一种具有可分离逃生座舱的新型直升机的制作方法



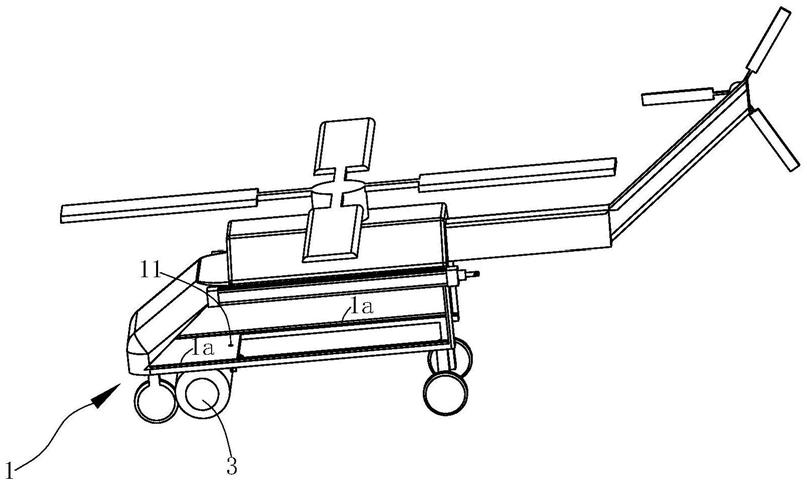
[0001]
本发明涉及一种直升机,具体涉及一种具有可分离逃生座舱的新型直升机。
背景技术:
[0002]
直升机广泛应用于作战、救援、运输等领域,直升机结构复杂,飞行员工作强度大,飞行高度低,飞行环境复杂,导致直升机事故率远高于固定翼飞机,特别是武装直升机,因其飞行高度低,在遭遇敌地面火力袭击时,战损率较高。2013年世界范围内直升机损毁事故517起,损失各类直升机537架,导致420死亡。作为世界上产量最大的直升机型号,黑鹰直升机总产量超过了4500架,截至2020年1月就有高达332架坠毁失事记录。
[0003]
对比直升机广阔的应用领域和较高的事故率,直升机救生技术却相对滞后,制约直升机危急时刻救生的因素有两点,一是直升机高速旋转的主旋翼,使上部逃生难度大;二是直升机飞行高度低,逃生时间短,无法达到安全开伞高度。通常情况下降落伞完全张开的安全高度约为500米,极限跳伞高度约为200米,然而直升机飞行高度一般较低,尤其是武装直升机,其飞行高度多在100米以下,在如此低的高度实现安全逃生十分困难。
[0004]
目前直升机普遍采用被动式吸能结构提高其抗坠撞能力,比如加装液压缓冲起落架;使用可变形双层机体结构;改进飞行员座椅来被动吸收能量等等措施,这些被动吸能措施基本能保证乘员95%的存活率的坠毁高度为10多米,如果直升机在几十米甚至数百米高空因故障坠毁时,存活率将迅速下降。另外,俄罗斯卡-50和卡-52采用了k-37弹射座椅,该系统首先引爆主旋翼上的爆炸螺栓,炸飞旋翼,然后,炸掉直升机顶盖,最后启动弹射座椅将飞行员弹射到安全高度开伞降落。爆炸产生的旋翼碎片在150m范围内形成巨大安全威胁;该系统仅适用于俄罗斯产共轴双旋翼机型,适用范围有限。现有技术通过对逃生装置进行改进避免旋翼碎片威胁,如炸开前门等,但对于普通民用直升机而言,引爆爆炸螺栓需要特殊的装置,设计复杂、价格昂贵,实用性差。
[0005]
如一申请号为cn201210255729.4(公告号为cn103538725a)的中国发明专利《直升机应急逃生系统》披露了由启动模块、舱门定向抛离模块、人-椅固定与分离模块、座椅弹射模块、射伞模块、快速开伞模块、安全防护模块、控制模块组成;所述的启动模块包括启动扳手、自由轮、转轴、钢索,钢索固定于自由轮上,扳起扳手自由轮不动,只有扳起并上拉扳手,钢索才能触发收紧装置,系统进入弹射救生程序;所述的舱门定向抛离模块主要包括微型弹射弹和爆炸螺栓,前门、中门及门柱预设5个爆炸螺栓,门梁预设2个微型弹射弹;所述的人-椅固定与分离模块包括气压式收紧活塞、塔轮、转向滑轮、钢索、拉力传感器、射伞枪底座、剪断钳和钢索,钢索与拉力传感器和背带系统相连,通过拉力传感器确定收紧度控制背带系统运动。该应急逃生系统虽然避免炸飞旋翼,但设计复杂、成本高,对于普通的民用直升机而言实用性差。
[0006]
目前国外整机降落伞技术比较成熟,已经广泛应用于起飞重量在1至2吨的轻型固定翼飞机、直升机上,但对于起飞重量在3吨以上的中小型直升机,如果用整机降落伞系统(caps),就需要使用质量及面积巨大的降落伞,这将会使直升机的负载显著增高,提高了降
落伞开伞高度及难度,如何提高中小型直升机救生技术,具有重要研究价值。因此,针对现有的直升机逃生机构需要改进。
技术实现要素:
[0007]
本发明所要解决的技术问题是针对上述现有技术现状而提供一种设计简单且容易实现的具有可分离逃生座舱的新型直升机。
[0008]
本发明解决上述技术问题所采用的技术方案为:一种具有可分离逃生座舱的新型直升机,包括机舱、位于机舱内的座舱,所述座舱与机舱能够分离,所述座舱上设置有降落伞装置,其特征在于:还包括
[0009]
锁定装置,实现所述机舱与座舱的锁定及解锁;
[0010]
气缸活塞杆装置,设置在机舱上;以及
[0011]
储气罐,设置在机舱上,所述储气罐为气缸活塞杆装置提供动力;
[0012]
在直升机正常行驶状态下,锁定装置将所述机舱与座舱锁定;在遇到紧急危险情况下,先触发锁定装置将机舱与座舱解锁,再触发储气罐与气缸活塞杆装置连通,在气缸活塞杆装置的驱动下,推动所述座舱从机舱内脱出从而实现与机舱分离,降落伞装置打开实现逃生。
[0013]
机舱与座舱的锁定及解锁方式有多种,作为优选,所述气缸活塞杆装置包括气缸以及位于气缸内的活塞杆,所述锁定装置实现活塞杆与座舱锁定与解锁。
[0014]
为利于机舱与座舱快速分离,作为优选,所述气缸的数量为两个,分别设置在机舱的两侧,所述气缸的内径为5~15cm,所述储气罐内存储的气体压强为1~2.5mpa,所述活塞杆推动座舱的有效行程s为2~6m。直升机的重量一般在1~10吨,相应的直升机内座舱的重量也不同,因此,根据不同重量及尺寸大小的座舱可以调整储气罐的压强、气缸的内径以及活塞杆推动座舱的有效行程,从而实现座舱与机舱的快速分离。
[0015]
实现座舱与机舱锁定的装置有多种,作为优选,所述锁定装置包括设置在活塞杆尾端的第一穿孔,所述座舱上设置有固定板,所述固定板上设置有能够相对固定板左右移动的第一齿条,所述第一齿条与第一齿轮啮合,所述第一齿条上设置有第一锁柱,在电机驱动下所述第一齿轮与第一齿条配合实现第一锁柱穿过和脱离第一穿孔;所述固定板上设置有供活塞杆穿过的第二穿孔;
[0016]
当机舱与座舱处于锁定状态时,所述第一锁柱穿设在第一穿孔内;在遇到紧急危险情况下,触发锁定装置使得第一锁柱脱离第一穿孔实现机舱与座舱解锁;再触发储气罐与气缸活塞杆装置连通,高压气体驱动两个活塞杆同时高速伸出,活塞杆推动固定板实现座舱从机舱内脱出。
[0017]
为利于座舱相对于机舱固定,作为优选,所述锁定装置还包括设置在机舱底部的第三穿孔,所述座舱的底部设置有第四穿孔,所述机舱的底部设置有能够相对机舱上下移动的第二齿条,所述第二齿条与第二齿轮啮合,所述第二齿条上设置有第二锁柱,在电机驱动下所述第二齿轮与第二齿条配合实现第二锁柱穿过和脱离第三穿孔和第四穿孔;
[0018]
当机舱与座舱处于锁定状态时,所述第二锁柱穿设在第三穿孔和第四穿孔内;在遇到紧急危险情况下,触发锁定装置使得第二锁柱脱离第三穿孔和第四穿孔实现机舱与座舱解锁。
[0019]
当飞机遇到紧急情况即将面临坠毁时,首先触发三个锁定装置,三个锁定装置同时解锁,然后再触发储气罐与气缸活塞杆装置连通,高压气体驱动两个活塞杆同时高速伸出运动,活塞杆推动固定板,因固定板与座舱连接一体,所以座舱被活塞杆高速推出,实现分离逃生。
[0020]
为降低座舱与机舱之间的摩擦,所述机舱内设置有滑槽,所述座舱上设置有与滑槽配合便于座舱从机舱内脱离的滚轮。为了减轻座舱的重量,亦可以把滚轮设置在机舱上。
[0021]
为降低座舱在坠地时与地面的撞击,作为优选,所述座舱的底部设置有吸能缓冲的抗坠装置。
[0022]
与现有技术相比,本发明的优点在于:座舱位于机舱内,通过锁定装置实现座舱与机舱能够分离,以高压气体作为动力源驱动气缸活塞杆装置实现座舱与机舱快速分离,该设计简单且容易实现,该设计非常适合用于不同吨位的通用航空领域民用直升机、中小型固定翼飞机甚至军用飞机上。
附图说明
[0023]
图1为本发明实施例中机舱的结构示意图;
[0024]
图2为本发明实施例中机舱的结构示意图;
[0025]
图3为图2中i1部的放大示意图;
[0026]
图4为图2中i2部的放大示意图;
[0027]
图5为本发明实施例中座舱的结构示意图;
[0028]
图6为本发明实施例中座舱与活塞杆通过锁定装置实现锁定的结构示意图;
[0029]
图7为本发明实施例中座舱的结构示意图。
具体实施方式
[0030]
以下结合附图实施例对本发明作进一步详细描述。
[0031]
如图1至图7所示,本发明实施例中具有可分离逃生座舱的新型直升机包括机舱1、位于机舱1内的座舱2、锁定装置、气缸活塞杆装置、储气罐3。
[0032]
储气罐3设置在机舱1上,储气罐3为气缸活塞杆装置提供动力。
[0033]
气缸活塞杆装置设置在机舱1上,气缸活塞杆装置包括气缸41以及位于气缸41内的活塞杆42,锁定装置实现活塞杆42与座舱2锁定与解锁。本实施例中气缸41的数量为两个,分别设置在机舱1的两侧,气缸41的内径为10cm,储气罐3内存储的气体压强为2mpa,活塞杆42推动座舱2的有效行程s为3m。
[0034]
锁定装置包括设置在活塞杆42尾端的第一穿孔5,座舱2上设置有固定板6,固定板6上设置有能够相对固定板6左右移动的第一齿条61,第一齿条61与第一齿轮63啮合,第一齿条61上设置有第一锁柱62,固定板6上设置有供活塞杆42穿过的第二穿孔64;机舱1底部设置有第三穿孔11,座舱2的底部设置有第四穿孔21,机舱1的底部设置有能够相对机舱1上下移动的第二齿条12,第二齿条12与第二齿轮13啮合,第二齿条12上设置有第二锁柱14;在电机驱动下,第一齿轮63与第一齿条61配合实现第一锁柱62穿过和脱离第一穿孔5,第二齿轮13与第二齿条12配合实现第二锁柱14穿过和脱离第三穿孔11和第四穿孔21。
[0035]
机舱1内设置有滑槽1a。
[0036]
座舱2上设置有与滑槽1a配合便于座舱2从机舱1内脱离的滚轮2a。座舱2的底部设置有吸能缓冲的抗坠装置。
[0037]
工作原理:在直升机正常行驶状态下,机舱1与座舱2处于锁定状态,第一锁柱62穿设在第一穿孔5内,第二锁柱14穿设在第三穿孔11和第四穿孔21内;在遇到紧急危险情况下,先触发锁定装置使得第一锁柱62脱离第一穿孔5、第二锁柱14脱离第三穿孔11和第四穿孔21实现机舱1与座舱2解锁;再触发储气罐3与气缸活塞杆装置连通,高压气体驱动两个活塞杆42同时高速伸出,活塞杆42推动固定板6实现座舱2从机舱1内脱出从而实现座舱2与机舱1分离,然后降落伞装置打开实现逃生。
[0038]
以气缸无杆腔的内径d=10cm,储气罐存储的气体压力p=2mpa为例,即单个气缸驱动力:f
单
=p
×
a=2
×
106×
π/4
×
d2×
10-4
=15700n;上式中,a为气缸无杆腔的面积;双缸合力f
合
=2
×
f
单
=31400n,座舱底座安装有滚轮,所以预估滑动摩擦系数μ=0.06,如果座舱重量为3吨,则座舱滑动时所受摩擦阻力f
f
=μ
×
mg=1800n,(若飞机坠毁前机舱与座舱处于失重状态做自由落体坠落时,因机舱与座舱之间相互作用力为零,所以上式的摩擦力可忽略)。从而,座舱总的驱动力:f
总
=f
合-f
f
=31400-1800=29600n,座舱加速度a=f
总
/m=29600/3000=9.87m/s2,设气缸活塞杆推动座舱的有效行程为s=3m,根据:v
2t-v
20
=2a
×
s;式中,座舱相对机舱的末速度为v
t
,座舱相对机舱的初速度v0=0;解得:v
t
=7.69m/s,根据:v
t
=v0+a
×
t,解得,t=0.78s,即:座舱相对机舱从静止到飞离直升机,需0.78秒,相对直升机的飞离速度为v
t
=7.69m/s。
[0039]
综上验算,对于座舱质量为3000千克的直升机,设计气缸驱动行程为3米,只需0.78秒就可使座舱从直升机弹出,相对飞离速度为v
t
=7.69m/s,座舱加速度a=9.87m/s2在人体完全能够承受的范围内。所需的气缸无杆腔的内径d=10cm,储气罐存储的气体压力p=2mpa。主要的硬件设备完全可以实现并满足本技术方案的所需的要求。
[0040]
所以本技术方案对于座舱质量为3000千克的直升机,技术上是完全可行的,座舱为3吨重的直升机对应的直升机起飞重量可达6吨,属于中小型直升机。此外,通过增大气缸内径,增加气缸数量,增大气缸驱动行程位移,对于座舱质量为3000至6000千克的中型直升机,本技术方案同样可适用,所以本技术方案可用作起飞重量在1至10吨的轻型、小型、中小型直升机,也可用在相应重量级别的固定翼飞机上。
起点商标作为专业知识产权交易平台,可以帮助大家解决很多问题,如果大家想要了解更多知产交易信息请点击 【在线咨询】或添加微信 【19522093243】与客服一对一沟通,为大家解决相关问题。
此文章来源于网络,如有侵权,请联系删除



tips