一种用于单壳体燃料舱的总组支撑方法与流程



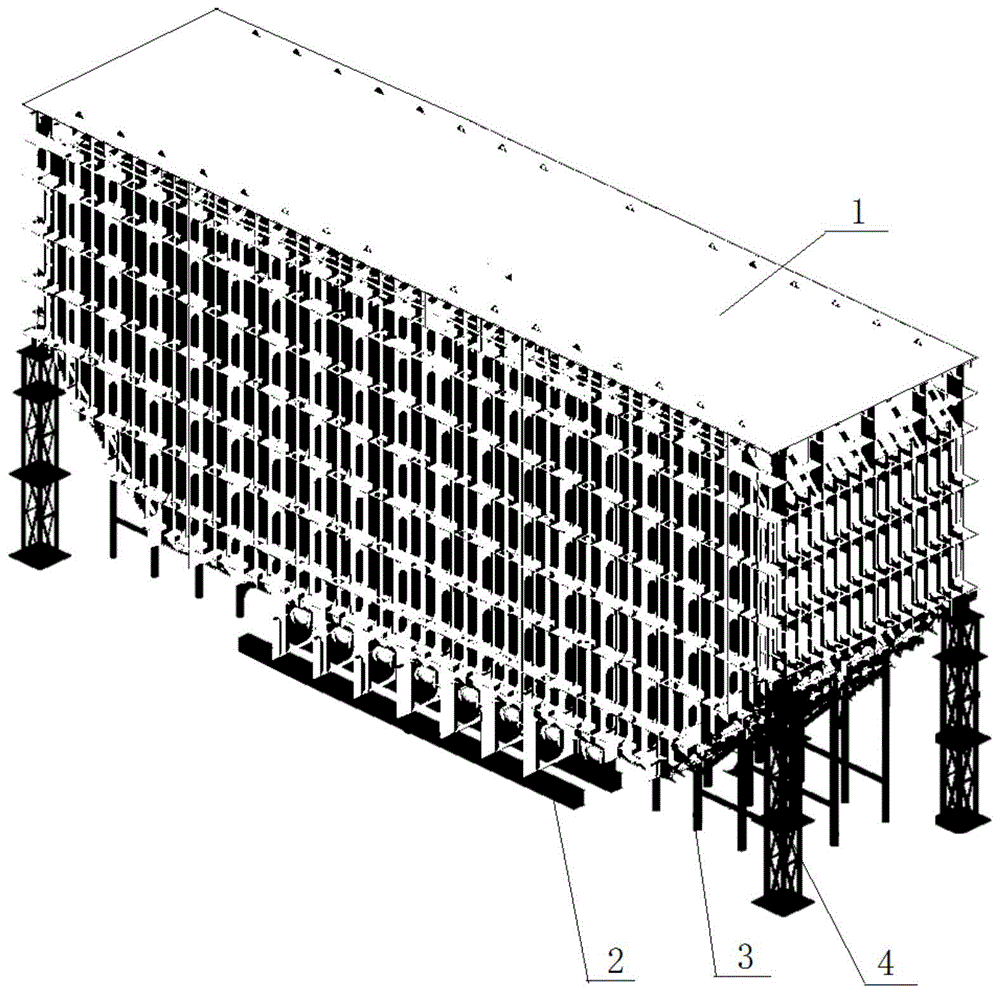
本发明属于船舶建造技术领域,具体涉及一种用于单壳体燃料舱的总组支撑方法。
背景技术:
采用常规燃料的船舶对环境的破坏非常大,随着国际上对环境保护越来越重视,一些船龄较大的船舶逐步面临被淘汰的风险,为了彻底解决气体排放的问题,一些船东选择对燃料系统进行改进,采用lng作为动力,需要将某一舱室改造成燃料舱,因此,需要单独搭载单壳体燃料舱,然后,安装到原船的舱室内。
目前,仅有新船建造时的燃料舱建造记录,而新造船燃料舱是双壳体结构,尚无单壳体燃料舱的建造记录,单壳体燃料舱在总组的过程中容易发生变形,影响燃料舱的建造精度。
技术实现要素:
针对现有技术中存在的问题,本发明提供一种用于单壳体燃料舱的总组支撑方法,本发明能够解决单壳体燃料舱总组时容易发生变形的问题,提高了燃料舱的建造精度。
为实现上述目的,本发明采用以下技术方案:
本发明提供一种用于单壳体燃料舱的总组支撑方法,包括以下步骤:
步骤一、在总组平台上划出的船体中心线、肋检线、钢梁的安装定位线、管子支撑的安装定位线、高墩的安装定位线;
步骤二、按照钢梁的安装定位线在总组平台上将钢梁安装到位,在钢梁上划出垫木的安装定位线;
步骤三、按照垫木的安装定位线在钢梁上将垫木安装到位;
步骤四、将燃料舱底部分段定位安装到钢梁上的垫木上;
步骤五、按照管子支撑的安装定位线在总组平台上将管子支撑安装到位;
步骤六、将管子支撑通过加强槽钢连接;
步骤七、按照高墩的安装定位线将高墩安装到位;
步骤八、将斜旁板分段定位安装到管子支撑的顶部;
步骤九、在高墩的顶部安装支撑座,支撑座的斜面与斜旁板分段的舱壁面板焊接,支撑座的顶面与隔舱顶板之间采用活络楞木调节;
步骤十、将燃料舱剩余分段吊装到位。
作为优选的技术方案,所述步骤二中,钢梁的长度大于等于17米,燃料舱底部分段每档船体肋板处均设置有钢梁,所述钢梁沿所述船体肋板的长度方向设置。
作为优选的技术方案,所述钢梁的水平度在±3毫米之内。
作为优选的技术方案,所述钢梁的中线与船体中心线位于同一条直线上。
作为优选的技术方案,所步骤三中,垫木设置于燃料舱底部分段的纵桁与船体肋板相交的位置。
作为优选的技术方案,所述步骤五中,管子支撑与总组平台的预埋铁连接。
作为优选的技术方案,所述步骤七中,高墩设置为4个,分别设置于前舱壁、后舱壁的两侧。
作为优选的技术方案,所述步骤九中,支撑座包括支撑主板、加强肘板及支撑顶板,支撑主板的一侧设置为与斜旁板分段相配合的倾斜状,支撑主板与加强肘板垂直,支撑主板、加强肘板焊接于高墩的顶部,支撑顶板焊接于支撑主板、加强肘板的顶部,支撑顶板与高墩的顶部平行。
与现有技术相比,本发明的有益效果为:
(1)本发明采用管子支撑与高墩的组合支撑形式,不仅能解决支撑过多而导致支撑底座干涉的问题,也能解决总组时舱壁受风导致燃料舱移位和变形的风险。
(2)本发明采用钢梁作为底部支撑,有利于增加胎架面与船体结构的接触面,减少底部分段结构的变形量。
(3)本发明能够减燃料舱总组过程中及总组后的变形,提高燃料舱总段的建造精度。
附图说明
为了更清楚地说明本发明实施例或现有技术中的技术方案,下面将对实施例或现有技术描述中所需要使用的附图作简单地介绍,显而易见地,下面描述中的附图仅仅是本发明的一些实施例,对于本领域普通技术人员来讲,在不付出创造性劳动的前提下,还可以根据这些附图获得其他的附图。
图1为本发明单壳体燃料舱的总组支撑结构示意图。
图2为本发明单壳体燃料舱的总组支撑的底部平面图。
图3为图2非隔舱面的横向剖面图。
图4为图2隔舱面的横向剖面图。
图5为图4的局部放大图。
图6为支撑座的俯视图。
其中,附图标记具体说明如下:燃料舱1、钢梁2、管子支撑3、高墩4、加强槽钢5、垫木6、支撑座7、底部分段8、斜旁板分段9、活络楞木10、支撑主板11、加强肘板12、支撑顶板13。
具体实施方式
下面将结合本发明实施例中的附图,对本发明实施例中的技术方案进行清楚、完整地描述,显然,所描述的实施例仅仅是本发明一部分实施例,而不是全部的实施例。基于本发明中的实施例,本领域普通技术人员在没有付出创造性劳动前提下所获得的所有其他实施例,都属于本发明保护的范围。
本实施例提供一种单壳体燃料舱的总组支撑方法,包括以下步骤:
步骤一、在总组平台上划出的船体中心线、肋检线、钢梁2的安装定位线、管子支撑3的安装定位线、高墩4的安装定位线。
步骤二、按照钢梁2的安装定位线在总组平台上将钢梁2安装到位,在钢梁2上划出垫木6的安装定位线。由于底部分段8的结构非常脆弱,燃料舱1的底部分段8每档船体肋板处均设置有钢梁2,钢梁2沿船体肋板的长度方向设置,钢梁2的长度大于等于17米。钢梁2的水平度在±3毫米之内,钢梁2的中线与船体中心线位于同一条直线上。
步骤三、按照垫木6的安装定位线在钢梁2上将垫木6安装到位;垫木6设置于燃料舱1底部分段8的纵桁与船体肋板相交的位置。
步骤四、将燃料舱1底部分段8定位安装到钢梁2上的垫木6上,垫木6能够有效减少钢梁2与底部分段8的摩擦。
步骤五、按照管子支撑3的安装定位线在总组平台上将管子支撑3安装到位,管子支撑3在不同位置高度不一样,同时为了防止管子支撑3失稳,管子支撑3与总组平台的预埋铁连接。
步骤六、将管子支撑3通过加强槽钢5连接。
步骤七、为了防止前后舱壁受风产生位移,应设置支撑,由于该支撑比较高,为防止支撑失稳,因此该支撑采用了高墩4,按照高墩4的安装定位线将高墩4安装到位。
步骤八、将斜旁板分段9定位安装到管子支撑3的顶部;
步骤九、由于高墩4的高度无法直接顶在结构上,而且支撑面为斜面,因此增加支撑座7和活络楞木10进行调节,在高墩4的顶部安装支撑座7,支撑座7的斜面与斜旁板分段9的舱壁面板焊接,支撑座7的顶面与隔舱顶板之间采用活络楞木10调节;高墩4设置为4个,分别设置于前舱壁、后舱壁的两侧。支撑座7包括支撑主板11、加强肘板12及支撑顶板13,支撑主板11的一侧设置为与斜旁板分段9相配合的倾斜状,支撑主板11与加强肘板12垂直,支撑主板11、加强肘板12焊接于高墩4的顶部,支撑顶板13焊接于支撑主板11、加强肘板12的顶部,支撑顶板13与高墩4的顶部平行。
步骤十、将燃料舱1剩余分段吊装到位。
尽管上述实施例已对本发明作出具体描述,但是对于本领域的普通技术人员来说,应该理解为可以在不脱离本发明的精神以及范围之内基于本发明公开的内容进行修改或改进,这些修改和改进都在本发明的精神以及范围之内。
起点商标作为专业知识产权交易平台,可以帮助大家解决很多问题,如果大家想要了解更多知产交易信息请点击 【在线咨询】或添加微信 【19522093243】与客服一对一沟通,为大家解决相关问题。
此文章来源于网络,如有侵权,请联系删除


