一种自动异型卷烟成型装置的制作方法



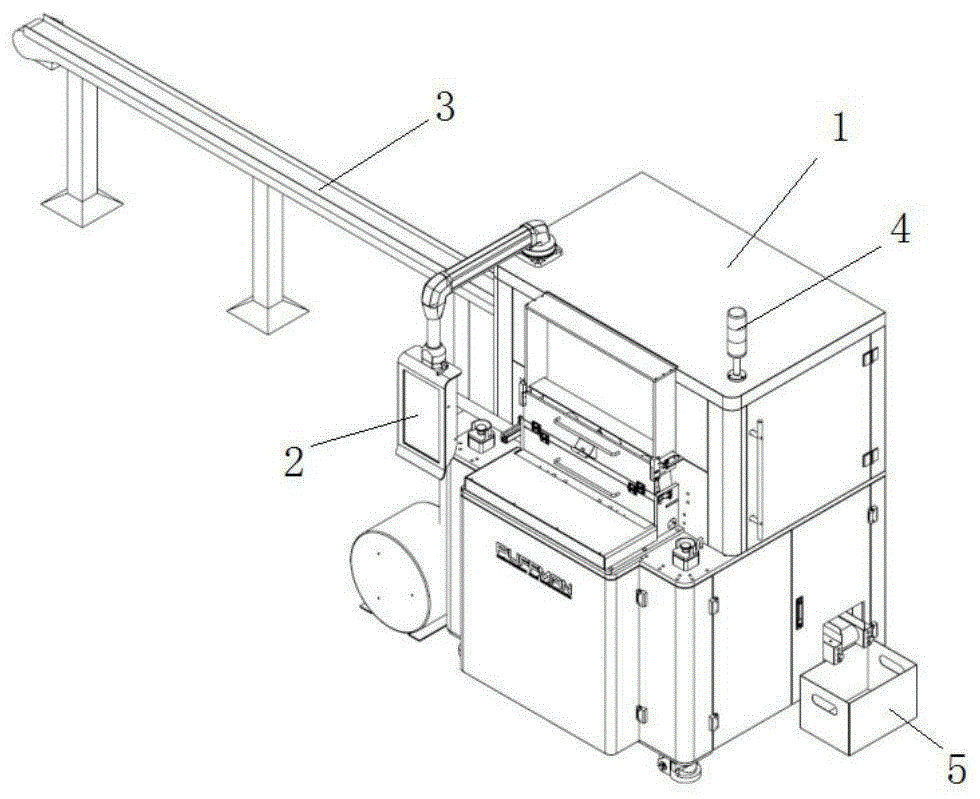
本发明涉及一种卷烟成型装置,尤其是一种自动异型卷烟成型装置。
背景技术:
目前,针对消费者对卷烟的需求不断提高,已经不满足于传统的圆柱形的卷烟,为了提升消费者的感官体验,目前有关于异型卷烟的研究,将烟支生产为方形或者方形与圆柱形组合的“天圆地方”烟支,然而,如何加工这样的卷烟,使其达到生产线的要求,同时保证外观良好,形状不回弹,自动剔除不合格的产品,成了目前急需解决的问题。
技术实现要素:
为了解决上述问题,本发明提供一种自动异型卷烟成型装置,能够按一定生产量自动加工异型卷烟,将合格品和不合格品分开。
本发明的技术方案具体如下:
一种自动异型卷烟成型装置,包括烟支上烟机构、烟库整料机构、翻转落料机构、烟丝回顶机构、合模成型机构、塑形长度调节机构和接料机构,烟支进入烟库整料机构,自动落料被输送进行拨料排序,至烟支上烟机构上烟,塑形长度调节机构调节好位置控制塑形长度,然后翻转落料机构落料,烟支在合模成型的过程中进行烟丝回顶,最后进入接料机构,接料机构将合格品和不合格品分开。
进一步地,烟支上烟机构包括基板以及设置于所述基板上的多个并列设置烟支推杆、直线驱动装置、直线导向机构、推杆固定座;所述多个并列设置烟支推杆的近端固定在所述推杆固定座上,所述推杆固定座与所述基板通过所述直线导向机构连接;所述推杆固定座与所述直线驱动装置连接。
进一步地,烟库整料机构包括料腔,料腔下方设有导料槽,导料槽底部设有带若干拨辊的拨辊排序机构,若干拨辊下方对应设有落烟子通道,导料槽中部设有菱形导向装置,两侧设有圆形导向装置,料腔底部设有抽板,料腔中的烟支靠下落入库,菱形导向装置左右摆动疏导烟支,烟支拍齐机构将烟支拍齐,使得烟支均匀分布和端部对齐,且料仓物料的重量不会都压到拨辊上,拨辊排序组件正反旋转排序,使得烟支连续进入落烟子通道;落烟子通道下方沿烟支运动方向头部布置有吸风槽,吸风槽通过管卡与吸废风管前端连通,吸废风管后端通过管卡与吸废风机连通。
进一步地,拨辊排序机构包括电机,与电机输出轴连接的主轴,主轴上设有拨辊驱动斜齿轮,拨辊驱动斜齿轮带动拨辊正反旋转,主轴通过两端的轴承座固定于料仓背板上,拨辊驱动斜齿轮由塑料斜齿轮和金属斜齿轮组成,所述塑料斜齿轮固定于主轴上,所述金属斜齿轮固定于拨辊的后端,金属斜齿轮设于塑料斜齿轮下方,由塑料斜齿轮带动转动,拨辊通过轴承座固定于料仓背板上,拨辊的前端穿过料仓背板伸到料仓中,电机根据系统指令正反旋转时,主轴正反旋转,拨辊在拨辊驱动斜齿轮传动下正反旋转,拨辊在料仓中靠摩擦力带动烟支左右运动,在运动到落烟通道上方时,烟支在烟支自身重力和上面烟支重力而形成的压力作用下,掉落进落烟通道。
进一步地,菱形导向装置由烟库导向组件摆动气缸、摆臂和四边菱形块组成,所述烟库导向组件摆动气缸固定于料仓背板上,摆动气缸的伸缩轴通过螺纹连接到摆臂上,所述摆臂的输出旋转轴偏心连接到四边菱形块上,烟库导向组件摆动气缸伸缩并通过摆臂驱动四边菱形块左右自由摆动;圆形导向装置由导向圆筒和安装于导向圆筒底部的偏心旋转轴组成,偏心旋转轴通过轴端的外螺纹固定到料库的背板,当料库中存满烟支时,菱形导向装置在摆动气缸伸缩作用下左右小角度摆动,从而带动料仓中的烟支也左右小角度摆动,圆形导向装置在烟支的挤压作用和导向圆筒自重的作用下左右自由摆动。
进一步地,烟支翻转落料机构包括两个翻转支座,以及设置在两个翻转支座之间、且与所述两个翻转支座连接的旋转主轴;所述旋转主轴的一端与旋转驱动装置连接;所述旋转驱动装置固定在所述翻转支座上;所述旋转主轴在沿垂直其轴线方向上并列固定设置有多个烟支管;所述烟支翻转落料机构还包括:直线驱动装置、直线导向机构、导向支座;所述直线导向机构固定于所述翻转支座的下方,所述直线驱动装置固定于所述翻转支座的上方;所述直线导向机构的延伸方向与所述旋转主轴的轴线方向垂直;所述导向支座固定在所述两个翻转支座之间、且与所述旋转主轴平行设置,且所述导向支座上设置有与所述烟支管一一对应的烟支导向槽。
进一步地,烟支自动合模成型机构包括槽体、设置在所述槽体内的前压模板、后压模板、成型模具单元、左压模导向组件、右压模导向组件、前压模导向组件、后压模导向组件;所述前压模板包含上前压模板和下前压模板,所述后压模板包含上后压模板和下后压模板;所述成型模具单元包括:相对设置的第一成型模具组件和第二成型模具组件,以及相对设置的第三成型模具组件和第四成型模具组件;所述前压模板和所述后压模板相对设置,所述前压模板和所述后压模板之间沿长度方向设置有多个成型模具单元;所述第一成型模具组件和所述第二成型模具组件分别固定在所述上前压模板和所述上后压模板上,所述第三成型模具组件和所述第四成型模具组件分别固定在所述下前压模板和所述下后压模板上;所述左压模导向组件与所述上前压模板和所述上后压模板的左端连接,所述右压模导向组件与所述下前压模板和所述下后压模板的右端连接;所述前压模导向组件与所述前压模板的前侧连接,所述后压模导向组件与所述后压模板的后侧连接;所述烟支自动合模成型机构还包括:左驱动装置、右驱动装置、前驱动装置、后驱动装置;所述左驱动装置与所述左压模导向组件通过同步轮和同步带连接,所述右驱动装置与所述右压模导向组件通过同步轮和同步带连接,所述前驱动装置与所述前压模导向组件通过同步轮和同步带连接,所述后驱动装置与所述后压模导向组件通过同步轮和同步带连接。
进一步地,烟丝回顶机构包括升降驱动装置、上固定板、升降板、多个回顶组件、直线光轴、直线轴承、导向轴支座、丝杆组件、限位柱;所述丝杆组件包括丝杆和丝母;所述升降板的两端分别通过所述直线轴承与所述直线光轴连接,所述多个回顶组件固定于所述升降板的下表面;所述上固定板位于所述升降板的正上方,且所述上固定板的两端分别通过所述导向轴支座与所述直线光轴的端部连接;所述升降驱动装置固定于所述上固定板的上表面,且所述升降驱动装置的驱动端通过所述丝杆组件与所述升降板连接;所述丝杆通过联轴器与所述升降驱动装置的驱动端连接;所述丝母通过螺钉与升降板连接;所述限位支柱位于所述升降板的上方,且固定在所述定板的下表面。
进一步地,烟支塑形长度调节机构包括上部为开口结构的支架、竖直驱动装置、丝杆组件、上固定板、下导向固定板、导向承载板、直线光轴、光轴夹紧套、直线导向机构、吹气导向座、水平驱动装置;所述上固定板位于所述支架的开口上方,且所述上固定板与所述支架固定连接;所述下导向固定板位于所述支架的开口内;所述导向承载板位于所述上固定板的上方;所述竖直驱动装置固定在所述支架的底部,且所述竖直驱动装置的驱动端通过同步轮和同步带与所述丝杆端部连接,所述丝杆通过所述丝母与下导向固定板连接;所述下导向固定板的两端分别通过所述光轴夹紧套与所述直线光轴的一端连接,所述直线光轴的另一端与所述导向承载板的下表面连接,且所述直线光轴的中部与所述上固定板之间通过直线轴承连接;所述吹气导向座包括导向板和安装座;所述导向板安装在所述安装座上,所述安装座通过所述直线导向机构安装在所述导向承载板上,所述水平驱动装置的驱动端与所述安装座连接;所述导向板的上表面设置有多个烟支导向槽以及吹气孔,每个所述吹气孔内部装有带密封的活塞顶杆。
进一步地,烟支接料机构包括支撑底板以及设置所述支撑底板上的回字形传输同步带组件、落料导向组件、视觉检测组件、剔除出料组件;所述落料导向组件位于所述回字形传输同步带组件的一个侧边的正上方,以将烟支通过所述落料导向组件导向至所述回字形传输同步带组件中;所述视觉检测组件设置于所述回字形传输同步带组件的输出侧上游,用于检测所述回字形传输同步带组件中的烟支是否合格;所述剔除出料组件设置于所述回字形传输同步带组件的输出侧下游,用于根据所述视觉检测组件的对烟支的检测结果,将不合格烟支剔除,将合格烟支输出。
与现有技术相比,本发明的有益效果具体如下:
1、本发明的异型烟支成型装置,其独立于卷接包设备,可自动完成滤嘴段和烟支段“天圆地方”及全方卷烟的生产。设备生产速度达到:250支/min,且外观良好,形状不回弹,且通过视觉检测功能保证异型烟的产品品质,从根本上解决目前异型烟大规模生产研究的技术障碍。异型烟成型机设计包含了烟支手动上样,烟支自动定量进烟,批量压制成型,烟丝清除,外露烟丝回顶,成品视觉检测剔除和皮带自动输出等功能,可以满足项目的技术要求。
2、烟支上烟机构通过直线驱动装置驱动推杆固定座,进而带动多个烟支推杆做往复直线运动,在多个烟支推杆向前推出时,将位于烟库机构中与多个烟支推杆相对应的烟支上烟滑板u型槽中的烟支推送到烟支翻转落料机构中(也就是上烟);然后烟支推杆缩回,进行下一次上烟过程,如此通过烟支推杆做往复直线运动,实现连续的上烟作业。
3、烟库整料机构一次上料能保证设备可连续生产15分钟以上,烟库导向装置和烟支拍齐机构,可以让烟支均匀分布和端部对齐,且料仓物料的重量不会都压到拨辊上,有利于进料的顺畅,防止烟支搭桥和错位,拨烟滚轮在伺服电机驱动下完成对烟支的搭桥状态的破坏,使烟支能够快速有序的进入落料子通道,拨辊不会对烟支造成损伤。烟库装有多处堵塞传感器,实时监测烟支流动的情况和堵塞情况。拨料滚轮会根据状况实时调整转速,自动对进料料仓口排堵。
4、烟支翻转落料机构通过旋转驱动装置带动旋转主轴旋转,从而将上烟机构送入烟支管中的烟支进行旋转90°至竖直方向;同时通过直线驱动装置驱动翻转支座,并带动旋转主轴以及设置在旋转主轴上的多个烟支管中的烟支沿水平方向移动至自动合模成型机构的入料口,以便进行后续的作业。
5、自动合模成型机构作为异型烟支成型设备中的核心组成部分,其位于设备的内部的烟丝回顶机构和烟支塑形长度调节机构之间,当烟支落入成型模具组件中后,通过烟支塑形长度调节机构来限定落入深度,同时烟丝回顶机构将顶杆从上烟的方向伸到成型模具组件中直至顶杆接触到烟支,此时前压模板和后压模板在左、右、前、后驱动装置驱动左、右、前、后压模导向组件的导向下合模,并通过位移传感器实现合模位置的实时闭环控制,确保烟支成型效果。在完成合模后,前、后驱动装置带动前、后压模导向组件将前成型模具和后模成型模具打开,烟丝回顶机构缩回、塑形长度调节组件的吹气导向座后移,烟支下落至接料机构的导向槽中。
6、烟丝回顶机构通过升降驱动装置驱动丝杆组件旋转带动升降板上下移动,进而带动回顶组件上下移动,从而能够在烟支进行异型塑形预定位完成后,通过升降驱动装置驱动回顶组件的前端与烟支的端部烟丝面接触,在烟支塑形过程中,回顶组件的前端压住烟支的烟丝面,进而避免了烟支在塑形过程中因挤压形变而造成烟丝外溢(也即烟丝冒头)的现象;并在烟支塑形完成后,通过升降驱动装置驱动升降板收回回顶组件,等待下一组烟支的塑形。
7、烟支塑形长度调节机构,在烟支进行异型塑形工序时,在烟支落入塑形机构的塑形模具时,能够根据烟支的塑形长度需求,通过竖直驱动装置调整导向板的高度,也即调整烟支下端的高度,来控制烟支插入塑形模具的长度,以便塑形机构对烟支进行预定长度的塑形;并在烟支塑形完成后,通过水平驱动装置驱动导向板后移,以将烟支从塑形模具的导向槽中释放下落至下一工序。
8、烟支接料机构的落料导向组件位于烟支塑形长度调节机构的下方,在烟支完成塑形后,烟支通过落料导向组件落入回字形传输同步带组件,并通过输出侧上游的视觉检测组件检测烟支是否合格,并在烟支移动至输出侧的剔除出料组件后,根据视觉检测组件的检测结果,将不合格烟支剔除,将合格烟支输出。
附图说明
图1为异型卷烟成型装置的结构示意图;
图2为异型卷烟成型装置的背面的结构示意图;
图3为异型卷烟成型装置的自动异型卷烟成型平台的结构示意图;
图4为烟支上烟机构的结构示意图;
图5为烟库整料机构的结构示意图;
图6为烟库整料机构的正视图;
图7为烟库整料机构的后侧的结构示意图;
图8为烟库整料机构的烟库机构中菱形导向装置、拨辊排序机构和烟支拍齐机构的结构示意图;
图9为烟支上滑板和吸风槽的结构示意图;
图10为烟支翻转落料机构的结构示意图;
图11为烟丝回顶机构的立体示意图;
图12为烟丝回顶机构的主视图;
图13为烟丝回顶机构中的回顶头组件的结构示意图;
图14为烟支自动合模成型机构的立体示意图;
图15为图14的烟支自动合模成型机构的俯视图;
图16a为图14在成型模具单元位置处的局部放大结构示意图;
图16b为成型模具组件的结构示意图;
图16c为图16a在i位置的剖面结构示意图;
图16d为图16a在h位置的剖面结构示意图;
图17为前上压模板的结构示意图;
图18为烟支自动合模成型机构在前压模导向组件位置的剖面示意图;
图19为烟支自动合模成型机构在左压模导向组件位置的剖面示意图;
图20为烟支塑形长度调节机构的结构示意图;
图21为烟支接料机构的俯视图;
图22为烟支接料机构的主视图;
图23为烟支接料机构的仰视图;
图24为烟支接料机构的落料导向组件的结构示意图;
图25为烟支接料机构的落料导向组件的局部剖面示意图;
图26为烟支接料机构的视觉检测组件的结构示意图;
图27为烟支接料机构的剔除出料组件的结构示意图;
图28为烟支接料机构的剔除出料组件的结构示意图;
图29为异型卷烟成型成型工艺流程图。
具体实施方式
下面将结合本申请实施例中的附图,对本发明实施例中的技术方案进行清楚、完整地描述,显然,所描述的实施例仅仅是本发明一部分实施例,而不是全部的实施例。基于本发明中的实施例,本领域普通技术人员在没有做出创造性劳动前提下所获得的所有其他实施例,都属于本发明保护的范围。
除非另外定义,本申请实施例中使用的技术术语或者科学术语应当为本发明所属领域内具有一般技能的人士所理解的通常意义。本发明实施例中使用的“第一”、“第二”以及类似的词语并不表示任何顺序、数量或者重要性,而只是用来区分不同的组成部分。“包括”或者“包含”等类似的词语意指出现该词前面的元件或者物件涵盖出现在该词后面列举的元件或者物件及其等同,而不排除其他元件或者物件。“安装”、“相连”、“连接”应做广义理解,例如,可以是固定连接,也可以是可拆卸连接,或一体地连接;可以是直接相连,也可以通过中间媒介间接相连,可以是两个元件内部的连通。“上”、“下”、“左”、“右”、“横”以及“竖”等仅用于相对于附图中的部件的方位而言的,这些方向性术语是相对的概念,它们用于相对于的描述和澄清,其可以根据附图中的部件所放置的方位的变化而相应地发生变化。
如图1所示,本实施例的异型卷烟成型装置,由2个独立的平台构成,自动异型卷烟成型平台1和异型卷烟输送装盘平台3,自动异型卷烟成型平台1一端设有次品收集盒5,异型卷烟输送装盘平台3输送合格品,自动异型卷烟成型平台1上端设有警报灯4,装置的操作和参数的设定通过操作屏2完成。
如图2所示,本实施例的接料结构1.7能够将合格品和不合格品分离开,如图3所示,自动异型卷烟成型平台1包括烟支上烟机构1.1、烟库整料机构1.2、翻转落料机构1.3、烟丝回顶机构1.4、合模成型机构1.5、塑形长度调节机构1.6和接料机构1.7,接料机构1.7将合格品和不合格品分开,合格品进入异型卷烟输送装盘平台3,不合格品通过不合格品输出皮带1.8落入次品收集盒5。
不合格品输出皮带1.8为厂家整体定制的产品,负责将不合格品输出。皮带采用绿色pu平皮带,变频调速电机驱动,铝型材框架。
异型卷烟输送装盘平台3为厂家整体定制的产品,负责将合格品输出,传送带两旁可坐人手工装盒。皮带采用pvc链板式输送链传动,每隔一定间隔安装烟支挡板,防止爬坡时烟支回滚。采用变频调速电机驱动,铝型材框架。
如图4所示,本申请实施例提供一种烟支上烟机构,如图1所示,该烟支上烟机构1.1包括基板1.11以及设置于基板1.11上的多个烟支推杆1.13、直线驱动装置1.12、直线导向机构1.14、推杆固定座1.15。
多个烟支推杆1.13并列设置,且多个烟支推杆1.13的近端固定在推杆固定座1.15上,推杆固定座1.15与基板1.11通过直线导向机构1.14连接;直线驱动装置1.12与推杆固定座1.15连接,从而在直线驱动装置1.12驱动推杆固定座1.15沿直线导向机构1.14做往复直线运动,在推杆固定座1.15的带动下,多个烟支推杆1.13做往复直线运动,从而完成烟支从烟库整料机构1.2向烟支翻转落料机构的上烟,其中,烟支翻转落料机构位于烟支推杆1.13的远端,图4中未示出。
采用本申请实施例提供的烟支上烟机构,通过直线驱动装置驱动推杆固定座,进而带动多个烟支推杆做往复直线运动,在多个烟支推杆向前推出时,将位于烟库机构1.2中与多个烟支推杆相对应的烟支上烟滑板u型槽中的烟支推送到烟支翻转落料机构中(也就是上烟);然后烟支推杆缩回,进行下一次上烟过程,如此通过烟支推杆做往复直线运动,实现连续的上烟作业。
在一些可能实现的方式中,上述直线驱动装置1.12可以为气缸、油缸、电动缸中的一种;例如直线驱动装置1.12可以为磁耦合气缸,磁耦合气缸在缸筒外表面有一个外部滑块在磁性耦合力的作用下往复移动,驱动推杆固定座1.15沿直线导向机构1.14做往复直线运动。
在一些可能实现的方式中,上述多个并列设置的烟支推杆1.13为20~40个烟支推杆1.13。示意的,在一些实施例中可以设置为30个烟支推杆1.13。
具体的,通过设置多烟支推杆1.13的个数大于或等于20个,能够通过保证上烟的效率,保证一次上烟过程完成足够数量烟支的上烟;通过设置多烟支推杆1.13的个数小于或等于40个,能够保证整个上烟机构的体积适中,同时也便于对整个机构的控制。
在一些可能实现的方式中,为了保证推杆固定座1.15移动的平稳性,如图4所示,推杆固定座1.15与基板1.11可以通过并列、间隔设置的两组直线导向机构1.14连接。
示意的,在一些实施例中,直线导向机构1.14可以包括:位于基板1.11上的直线导轨,以及位于推杆固定座1.15朝向基板1.11一侧的滑块,滑块位于直线导轨中,通过滑块与直线导轨的配合,从而在直线驱动装置1.12的作用下,完成对推杆固定座1.15(烟支推杆1.13)的直线往复驱动。
如图5所示,本实施例的异型卷烟成型机的烟库整料机构1.2,设于烟支上烟机构1.1上方。
如图6所示,异型卷烟成型机的烟库整料机构1包括料腔1.21,料腔1.21下方设有钣金导料槽1.23,导料槽底部设有拨辊排序机构1.24,拨辊排序机构1.24包括29个排序拨辊1.247,对应相应的落烟子通道1.25。导向装置1.22包括菱形导向装置1.222和圆形导向装置1.221,导料槽1.23中部设有菱形导向装置1.222,两侧设有圆形导向装置1.221。
料腔1.21底部设有原料盘抽板1.29,料腔1.21中的烟支靠下落入库,导向装置1.22疏导烟支,协同烟支拍齐机构1.26,使得烟支均匀分布和端部对齐,且料仓物料的重量不会都压到排序拨辊1.247上,拨辊1.247左右摆动排序,使得烟支进入落烟子通道1.25。
落烟子通道1.25下方沿烟支运动方向头部布置有吸风槽,吸风槽通过管卡与吸废风管1.27前端连通,吸废风管1.27后端通过管卡与吸废风机1.28连通。
导料槽1.23中还设有多个堵塞传感器1.210,通过实时监测和传输烟支流动的情况和堵塞情况,控制器根据堵塞传感器传输的情况,控制拨辊排序机构1.24对进料料仓口排堵。
本实施例中,料腔1.21中还可以设有高低料位开关,用于检测料仓中烟支容量,当料仓中装满烟支时,高位开关和低位开关会同时检测到烟支信号,随着烟支不断生产消耗,料仓中的烟支料位会逐渐降低,当高位开关检测到不到烟支信号时,系统会自动报警并提示操作员手动上料,若当烟支料位继续降到低位开关检测到不到烟支信号时,系统会自动报警停机并提示操作员手动上料。
烟库机构通过手动上原料盘后,人工抽掉插板,烟支通过自重自动落到料库,一次上料能保证设备可连续生产15分钟以上。
人工手动将原料盘上到料库正上方,抽掉抽板,卷烟通过自重开始进料,烟库机构里的烟库导向装置1.22和烟支拍齐机构1.26,可以让烟支均匀分布和端部对齐,且料仓物料的重量不会都压到拨辊上,有利于进料的顺畅,防止烟支搭桥和错位。
如图5-7所示,烟库导向装置1.22包括两侧圆形导向装置1.221和中间四边菱形导向装置1.222,四边菱形导向装置1.222由烟库导向组件摆动气缸1.224、烟库导向组件摆臂1.223和四边菱形块组成,烟库导向组件摆动气缸1.224通过螺钉固定于料仓背板上,如图7所示,导向组件摆动气缸1.224的伸缩轴通过螺纹连接到烟库导向组件摆臂1.223上,所述摆臂1.223的输出旋转轴偏心连接到四边菱形块上,从而,烟库导向组件摆动气缸1.224伸缩并通过摆臂驱动四边菱形块左右自由摆动。如图8所示,烟库导向组件摆臂1.223与菱形导向组件转轴1.225连接,菱形导向组件转轴1.225偏心连接到四边菱形块上,菱形导向组件转轴1.225通过轴承1.226和轴承座1.227设于料仓背板上。
圆形导向装置1.221可以由导向圆筒和安装于导向圆筒底部的偏心旋转轴组成,偏心旋转轴通过轴端的外螺纹固定到料库的背板上,当料库中存满烟支时,四边菱形导向装置在摆动气缸1.224伸缩作用下左右小角度摆动,从而带动料仓中的烟支也左右小角度摆动,安装于料库左右两边的圆形导向装置在烟支的挤压作用和导向圆筒自重的作用下实现左右自由摆动。圆形导向装置是从动,中间菱形导向装置是主动左右自由摆动,让烟支左右摆动,便于烟支掉落,为了不让烟支产生形变,圆形导向装置顺从烟支的摆动方向被动地左右摆动。
如图7-8所示,拨辊排序机构包括拨辊伺服电机1.243,与电机1.243输出轴连接的主轴1.241,主轴1.241上设有拨辊驱动斜齿轮1.242,拨辊驱动斜齿轮1.242带动拨辊1.247正反旋转,主轴1.241通过两端的轴承座1.246固定于料仓背板上,拨辊伺服电机1.243通过电机座固定于料仓背板上,拨辊驱动斜齿轮1.242由塑料斜齿轮1.2422和金属斜齿轮1.2421组成,塑料斜齿轮1.2422通过紧定螺钉固定于主轴1.241上,金属斜齿轮通过紧定螺钉固定于拨辊的后端,塑料斜齿轮1.2422和金属斜齿轮1.2421之间为齿轮啮合,齿轮轴方向90度变化。
拨辊1.247通过轴承座1.248固定于料仓背板上,拨辊1.247的前端穿过料仓背板伸到料仓中,同步带轮1.245为一对,一个固定于主轴1.241上,一个固定于拨辊伺服电机1.243上,一对同步带轮1.245之间通过同步带相连接并同步旋转。当伺服电机1.243根据系统指令正反旋转时,主轴1.241在同步带和同步带轮1.245传动下也正反旋转,拨辊1.247在拨辊驱动斜齿轮传动下也正反旋转,正反旋转的拨辊排序机构的上端在料仓中靠摩擦力带动烟支左右运动,在运动到落烟通道上方时,因烟支自身重力和上面烟支重力而形成的压力作用下,掉落进落烟通道,无论某个时刻,所有拨辊的运动方向都是相同的,或统一做顺时针运动,或统一做逆时针运动,方向取决于当时拨辊伺服电机的旋转方向。
如图8所示,烟支拍齐机构1.26主要由亚克力门板1.264、拍门拉手1.261、拍门连杆1.262、连杆固定座1.265和拍门气缸1.263组成,上侧和下侧的亚克力门板1.264通过铰链固定于料仓前板1.213上,连杆固定座1.265通过螺钉固定于上侧亚克力门板1.264上,连杆固定座1.265通过拍门拉手1.261与拍门连杆1.262连接,拍门连杆1.262通过螺纹与拍门气缸1.263的伸缩轴连接,拍门气缸1.263穿过四边菱形导向装置1.222的中间固定于料库的背板上。当拍门气缸1.263的伸缩轴前后伸缩时,伸缩轴通过拍门连杆1.262带动安装有连杆固定座1.265的亚克力门板1.264小角度前后摆动,从而自动实现料仓中烟支端部对齐。本实施例中,拍门气缸1.263的气缸活塞可与现有的卡扣组件(例如可以包括卡扣、卡扣轴和钮簧)活动连接,通过卡扣组件上的卡扣轴、扭簧实现。卡扣组件与连杆固定座1.265连接,进而带动亚克力门板以铰链为支点运动。
本实施例中,菱形导向装置是中空设计,拍齐气缸1.263从菱形中间空白穿过,两者分别由两个气缸独立控制,另外,菱形装置的左右运动幅度和拍齐气缸的摆动幅度都很有限,不会互相干涉。
如图5、6、9所示,烟支上烟滑板1.211通过螺钉安装于30个落料子通道的正下方,烟支上烟滑板1.211上开有30个u型烟支定位槽,且与30个落料子通道一一对应,用于烟支的定位和导向,确保烟支上烟时的稳定可靠。
滑道吸风槽1.2111用于将烟库中掉落的烟丝通过吸废风机实时吸走,保持上烟通道通畅。吸风风力在20kpa左右,提供吸风的吸废风机配有手动调速器,吸风管路上设有手动可调开度的旁通阀,操作员可根据烟支落料情况手动调节调速器和旁通阀,实现吸风风力和风量调节,从而不会影响烟支的整理和掉落。
本实施例中,烟支自动拨料排序机构1.24采用伺服电机驱动,机构上装有多组拨烟滚轮,拨烟滚轮在伺服电机驱动下完成对烟支的搭桥状态的破坏,使烟支能够快速有序的进入30个落料子通道,拨辊不会对烟支造成损伤。
本实施例的烟库装有多处堵塞传感器,实时监测烟支流动的情况和堵塞情况。拨料滚轮会根据状况实时调整转速,自动对落料子通道口排堵。30个落料子通道全部经过了精密的滑落轨迹模拟,通道内做镜面抛光处理,保证了烟支能够在通道内畅行无阻。当人工需要干预排堵时,打开烟库机构的亚克力门板即可操作。特别的,烟支上烟的滑板上开有沿烟支运动方向布置的吸风槽,可将烟库中掉落的烟丝通过吸废风机实时吸走,保持上烟通道通畅。
使用时,人工将整箱香烟放入原料盘中,抽掉插板,烟支靠自重下落入库,导向装置左右摆动疏导烟支,拨辊排序组件左右摆动排序烟支进入落烟通道,停留在烟支上烟滑板的凹槽中,等待上烟机构上烟。
烟库整料机构1.2里的卷烟在烟库导向装置,烟支拍齐机构和多组落烟子通道导向下,通过拨辊拨动和自重的作用下落入多组推杆的上烟机构前方,完成烟支落料。
如图10所示,本实施例的烟支翻转落料机构1.3,包括相对设置的两个翻转支座1.33,以及设置在两个翻转支座1.33之间、且与两个翻转支座连接的旋转主轴1.32。
旋转主轴1.32的一端与旋转驱动装置1.35连接;旋转驱动装置1.35固定在翻转支座1.33上;旋转主轴1.32在沿垂直其轴线方向上并列固定设置有多个烟支管1.31(例如可以为不锈钢管);从而通过旋转驱动装置1.35带动旋转主轴1.32旋转,进而带动烟支管1.31进行旋转。
该烟支翻转落料机构还包括:直线驱动装置1.34、直线导向机构1.36、导向支座1.37。
直线导向机构1.36固定于翻转支座1.33的下方,直线驱动装置1.36固定于翻转支座1.33的上方;直线导向机构1.36的延伸方向与旋转主轴1.31的轴线方向垂直;从而通过直线驱动装置1.36驱动翻转支座1.33沿直线导向机构1.36移动,进而带动旋转主轴1.32以及设置在旋转主轴1.32上的多个烟支管1.31沿垂直旋转主轴1.31的轴线方向做往复直线运动。
导向支座1.37固定在两个翻转支座1.33之间、且与旋转主轴1.32平行设置,且导向支座1.37上设置有与烟支管1.31一一对应的烟支导向槽。这样一来,在通过旋转主轴1.32带动烟支管1.31从水平方向旋转90°至竖直方向时,烟支管1.31中的烟支的端部与导向支座1.37接触,并通过导向支座1.37上的烟支导向槽实现对烟支导向。
采用本申请的烟支翻转落料机构,通过旋转驱动装置带动旋转主轴旋转,从而将上烟机构送入烟支管中的烟支进行旋转90°至竖直方向;同时通过直线驱动装置驱动翻转支座,并带动旋转主轴以及设置在旋转主轴上的多个烟支管中的烟支沿水平方向移动至自动合模成型机构的入料口,以便进行后续的作业。
在一些可能实现的方式中,为了检测每个烟支管1.31中是否具有烟支,以便进行修正,如图10所示,该烟支翻转落料机构还可以包括:固定在导向支座1.37侧面的光纤固定座1.38;光纤固定座1.38上设置与烟支导向槽(或者说烟支管1.31)一一对应的光纤传感器1.39,从而在通过旋转驱动装置带动旋转主轴旋转,从而将上烟机构送入烟支管中的烟支进行旋转90°至竖直方向后,通过光纤传感器1.39来检测烟支管1.31中是否具有烟支。
示意的,在一些可能实现的方式中,上述旋转驱动装置可以包括旋转气缸,旋转气缸的驱动端与旋转主轴连接。
示意的,在一些可能实现的方式中,上述直线驱动装置1.34可以包括水平推拉气缸,水平推拉气缸的驱动端与翻转支座1.33连接。
示意的,在一些可能实现的方式中,上述直线导向机构1.36可以包括:设置于翻转支座1.33下方的滑块,以及固定设置于机架上的直线导轨,从而在直线驱动装置1.34的驱动下,使得翻转支座1.33带动旋转主轴1.32以及设置在旋转主轴1.32上的多个烟支管1.31,沿直线导轨移动。
如图11所示,本实施例的烟丝回顶机构。参考图12(图11的侧面示意图),该烟丝回顶机构包括升降驱动装置1.401、上固定板1.44、升降板1.45、多个回顶组件1.402、直线光轴1.48、直线轴承1.47、导向轴支座1.46、丝杠组件1.49、限位柱1.41。其中,丝杆组件1.49包括丝杆和丝母。
示意的,上述多个回顶组件1.402可以为20~40个回顶组件1.402;例如可以为30个回顶组件1.402。
如图12所示,升降板1.45的两端分别通过直线轴承1.47与直线光轴1.48连接,并且多个回顶组件1.402固定于升降板1.45的下表面;也就是说在通过上下移动升降板1.45时,能够同时带动回顶组件1.402上下移动。
上固定板1.44位于升降板1.45的正上方(也即上固定板1.44位于升降板1.45远离设置回顶组件1.402的一侧),上固定板1.44的两端分别通过导向轴支座1.46与直线光轴1.48的端部连接。
升降驱动装置1.401固定于上固定板1.44的上表面(也即升降驱动装置1.401固定于上固定板1.44远离升降板1.45一侧的表面),并且升降驱动装置1.401的驱动端通过丝杆组件1.49与升降板1.45连接;这样一来,通过升降驱动装置1.401驱动丝杆组件旋转从而带动升降板1.45上下运动,进而带动回顶组件1.402上下运动。
限位柱1.41位于升降板1.45的上方,且固定在上固定板1.44的下表面,通过限位柱1.41来限制升降板1.45向上的移动距离。
丝杠组件1.49设置在上固定板1.44的下方,丝杆通过联轴器与升降驱动装置1.401的驱动端连接,丝母通过螺钉与升降板1.45连接,通过升降驱动装置1.401与丝杠组件1.49的配合,可以精确控制升降板1.45向下移动的距离。
烟丝回顶机构通过升降驱动装置通过丝杠组件驱动升降板上下移动,进而带动回顶组件上下移动,从而能够在烟支进行异型塑形预定位完成后,通过升降驱动装置驱动回顶组件的前端与烟支的上端部烟丝面接触,在烟支塑形过程中,回顶组件的前端压住烟支的烟丝面,进而避免了烟支在塑形过程中因挤压形变而造成烟丝外溢(也即烟丝冒头)的现象;并在烟支塑形完成后,通过升降驱动装置驱动升降板收回回顶组件,等待下一组烟支的塑形。
在一些可能实现的方式中,如图12所示,可以在上述限位柱1.41内部设置接近传感器,以精确的控制升降板1.45向上移动距离,避免升降板1.45与限位支柱1.41之间产生碰撞。
在一些可能实现的方式中,如图12所示,上述升降驱动装置1.401可以包括:伺服电机1.42。在此情况下,伺服电机1.42的驱动端与联轴器1.43连接,联轴器1.43的输出端通过丝杆组件1.49与升降板1.45连接。
在一些可能实现的方式中,如图12所示,回顶组件1.402可以包括:回顶连杆1.412、联轴器1.411、回顶头组件1.410。其中,回顶连杆1.412的一端与升降板1.45连接,另一端通过联轴器1.411与回顶头组件1.410连接。
在一些可能实现的方式中,如图13所示,上述回顶头组件1.410可以包括回顶头1.4101、回顶头固定件1.4102;其中,回顶头1.4101通过回顶头固定件1.4102与联轴器1.411连接。
在一些可能实现的方式中,上述联轴器1.411可以采用柔性联轴器,回顶头可以采用柔性塑料材质制成,从而可以加大顶杆的挠度,避免机构因相对位置误差造成回顶连杆1.412变形。另一方面,烟丝回顶机构因相对位置误差,装配加工等造成多组(例如30组)回顶头组件1.402的相对位置会有偏差,当烟支自动合模成型机构打开时,多组回顶头组件1.402自动插入合模腔中,烟支自动合模成型机构关闭,多组回顶头组件1.410因挠度大,从而能够在合模中自动根据各自合模腔的位置进行浮动微调,确保了回顶的可靠性,同时也避免了顶头组件因位置误差被压坏,确保了回顶头组件的使用寿命。
如图14所示,本实施例的烟支自动合模成型机构。参考图15(图14的俯视图)所示,该烟支自动合模成型机构包括槽体1.51、设置在槽体1.51内的前压模板1.52、后压模板1.53、成型模具单元1.54、左压模导向组件1.55、右压模导向组件1.56、前压模导向组件1.57、后压模导向组件1.58。
如图16a所示,成型模具单元1.54包括:相对设置的第一成型模具组件1.541和第二成型模具组件1.542,以及相对设置的第三成型模具组件1.543和第四成型模具组件1.544。示意的,第一成型模具组件1.541、第二成型模具组件1.542、第三成型模具组件1.543、第四成型模具组件1.544的结构可以相同;例如可以均采用图16b的结构,一个棒状的成型部,以及位于棒状成型部一端的固定部。
如图16c(图16a在i位置的剖面示意图)和图16d(图16a在h位置的剖面示意图),前压模板1.52和后压模板1.53相对设置,前压模板1.52包含上前压模板1.521和下前压模板1.522,后压模板1.53包含上后压模板1.531和下后压模板1.532。
如图15所示,前压模板1.52和后压模板1.53之间沿长度方向设置有多个成型模具单元1.54。
结合图15、图16a和图16c所示,第一成型模具组件1.541和第二成型模具组件1.542分别固定在上前压模板1.521和上后压模板1.531上;示意的,在一些可能实现的方式中,上前压模板1.521和上后压模板1.531上的顶端设置有第一导向槽和第二导向槽;第一成型模具组件1.541固定在第一导向槽中,第二成型模具组件1.542固定在第二导向槽中。
结合图15、图16a和图16d所示,第三成型模具组件1.543和第四成型模具组件1.544分别固定在下前压模板1.522和下后压模板1.532上。示意的,在一些可能实现的方式中,下前压模板1.522和下后压模板1.532上的底部分别设置有第三导向槽和第四导向槽;第三成型模具组件1.543固定在第三导向槽中,第四成型模具组件1.544固定在第四导向槽中。也即成型模具单元1.54中的四个成型模具组件分别通过导向槽实现精确的导向定位,并且也便于进行不同规格成型模具组件的更换。
本实施例对于上述第一导向槽、第二导向槽、第三导向槽、第四导向槽的具体设置形式不做具体限制。示意的,在一些可能实现的方式中,如图17所示,位于上前压模板1.521顶部的第一导向槽w可以采用燕尾槽结构。同样,第二导向槽,第三导向槽和第四导向槽也可以采用燕尾槽结构。
另外,参考图15,左压模导向组件1.55与前压模板1.52中上前压模板1.521和后压模板1.53中上后压模板1.531的左端连接,右压模导向组件1.56与前压模板1.52中下前压模板1.522和后压模板1.53中下后压模板1.532的右端连接;前压模导向组件1.57与前压模板1.52(包括1.521、1.522)的前侧连接,后压模导向组件1.58与后压模板1.53(包括1.531和1.532)的后侧连接。
另外,如图15所示,该烟支自动合模成型机构还包括:与左压模导向组件1.55连接左驱动装置1.59,与右压模导向组件1.56连接的右驱动装置1.510,与前压模导向组件1.57连接的前驱动装置1.511,与后压模导向组件1.58连接的后驱动装置1.512。
需要说明的是,本实施例对上述左、右、前、后驱动装置(1.59、1.510、1.511、1.512)的设置形式不做具体限制,对左、右、前、后驱动装置(1.59、1.510、1.511、1.512)与左、右、前、后压模导向组件(1.55、1.56、1.57、1.58)之间的连接方式不做具体限制;但可以理解的是,左、右、前、后驱动装置(1.59、1.510、1.511、1.512)与左、右、前、后压模导向组件(1.55、1.56、1.57、1.58)之间必然采用传动连接。
示意的,以左驱动装置1.59与左压模导向组件1.55的连接为例,在一些可能实现的方式中,左驱动装置1.59可以采用伺服电机,并且伺服电机的输出端通过同步带和同步轮与左压模导向组件1.55的输入端(例如丝杆)实现传动连接。同理如右、前、后驱动装置(1.510、1.511、1.512)与右、前、后压模导向组件(1.56、1.57、1.58)之间连接,此处不再赘述。
烟支自动合模成型机构作为异型烟支成型设备中的核心组成部分,其位于设备的内部的烟丝回顶机构和烟支塑形长度调节机构之间,当烟支落入成型模具组件中后,通过烟支塑形长度调节机构来限定落入深度,同时烟丝回顶机构将顶杆从上烟的方向伸到成型模具组件中直至顶杆接触到烟支,此时前压模板和后压模板在左、右、前、后驱动装置驱动左、右、前、后压模导向组件的导向下合模,并通过位移传感器实现合模位置的实时闭环控制,确保烟支成型效果。在完成合模后,左、右、前、后驱动装置带动左、右、前、后压模导向组件将第一、二、三、四成型模具组件打开,烟丝回顶机构缩回、塑形长度调节组件的吹气导向座后移,烟支下落至接料机构的导向槽中。
根据需要,烟支落入成型模具组件的深度可以进行调节,进而得到自动完成滤嘴段和烟支段“天圆地方”(一端为圆形一端为方形)及全方卷烟的生产。
在一些实施例中,采用本申请的自动合模成型机构的异型烟支成型设备的生产能力达到:250支/min。
以下对前压模导向组件1.57和后压模导向组件1.58的具体设置情况做进一步的说明。如图15所示,前压模导向组件1.57和后压模导向组件1.58的结构相同,两者前后对称设置,以下前压模导向组件1.57为例进行说明。
如图18所示,前压模导向组件1.57包括丝杆1.571、轴承1.572、丝母1.574、直线导轨1.575、导向安装块1.576和限位撞块1.577。
丝杆1.571的第一端与前述的前驱动装置1.511通过同步轮、同步带传动连接,丝杆1.571的中部通过轴承1.572固定在槽体1.51上,丝杆1.571的第二端与丝母1.574连接。
导向安装块1.576左侧与丝母1.574的上侧连接,导向安装块1.576下侧通过直线导轨1.575与槽体1.51底部连接;导向安装块1.576的右侧通过前压模板1.52的直线导轨与上前压模板1.521和下前压模板1.522连接。
在一些可能实现的方式中,为了对导向安装块1.576在远离前压模板1.52一侧的方向上移动距离进行限制,如图18所示,该前压模导向组件1.57还包括限位撞块1.577;该限位撞块1.577设置在导向安装块1.576的左侧。
另外,以下对左压模导向组件1.55和右压模导向组件1.56的具体设置情况做进一步的说明。如图15所示,左压模导向组件1.55和右压模导向组件1.56的结构相同,以下左压模导向组件1.55为例进行说明。
如图19所示,左压模导向组件1.55包括:丝杆1.551、轴承1.552、丝母1.553、导向安装块1.554、前压模连接座1.555、后压模连接座1.556。
丝杆1.551的第一端与左驱动装置1.59通过同步轮、同步带传动连接,丝杆1.551的中部通过轴承1.552固定在槽体1.51上;在丝杆1.551的第二端通过丝母1.553安装在导向安装块1.554上。
导向安装块1.554右侧的前端通过直线导轨1.558与前压模连接座1.555连接,且前压模连接座1.555与上前压模板1.521的左端连接;导向安装块1.554右侧的后端通过直线导轨1.559与后压模连接座1.556连接,且后压模连接座1.556与上后压模板1.531的左端连接。
此处需要说明的是,左压模导向组件1.55和右压模导向组件1.56的结构设置基本一致,此处不再赘述,对于右压模导向组件1.56的具体结构可以参考前述左压模导向组件1.55的相关设置。
右压模导向组件1.56与左压模导向组件1.55的不同之处在于:
在右压模导向组件1.56中,导向安装块左侧的前端通过直线导轨与前压模连接座1.555连接,前压模连接座1.555与下前压模板1.522的右端连接;导向安装块左侧的后端通过直线导轨与后压模连接座1.556连接,后压模连接座1.556与下后压模板1.532的右端连接。
在一些可能实现的方式中,为了保证左压模导向组件1.55中导向安装块1.554的稳定性,如图19所示,可以设置导向安装块1.554左侧的前端和后端分别通过直线轴承安装在槽体1.51上。同理,可以设置右压模导向组件1.56中的导向安装块1.554右侧的前端和后端分别通过直线轴承安装在槽体1.51上。
如图20所示,本实施例的烟支塑形长度调节机构1.6,包括:上部为开口结构的支架1.61、竖直驱动装置1.62、丝杆组件1.63、上固定板1.64、下导向固定板1.65、导向承载板1.66、直线光轴1.67、直线导向机构1.68、吹气导向座1.69、水平驱动装置1.610。其中,丝杆组件1.63包括丝杆和丝母。
上固定板1.64位于支架1.61的开口上方,上固定板1.64与支架1.61固定连接;示意的,上固定板1.64可以通过螺钉与支架1.61固定连接。下导向固定板1.65位于支架1.61的开口内;导向承载板1.66位于上固定板1.64的上方。
竖直驱动装置1.62固定在支架1.61的底部,且竖直驱动装置1.62的驱动端通过同步轮和同步带与丝杆端部连接,丝杆通过丝母与下导向固定板1.65连接。示意的,竖直驱动装置1.62可以为伺服电机,在此情况下,伺服电机的输出端通过同步轮和同步带与丝杆的输入端连接,从而驱动丝杆旋转。
下导向固定板1.65的两端分别通过光轴夹紧套1.612与直线光轴1.67的一端(也即下端)连接,并且直线光轴1.67的另一端(也即上端)与导向承载板1.66的下表面连接,且直线光轴1.67的中部与上固定板1.64之间通过直线轴承1.611连接。
也就是说,通过竖直驱动装置1.62通过对丝杆组件1.63的驱动,能够带动下导向固定板1.65上下移动,进而带动导向承载板1.66上下移动。
另外,吹气导向座1.69包括导向板1.691和安装座1.692。
导向板1.691的上表面设置有多个烟支导向槽(例如可以是30个)以及吹气孔,每个吹气孔内部装有带密封的活塞顶杆,导向板1.691安装在安装座1.692上,安装座1.692通过直线导向机构1.68安装在导向承载板1.66上,水平驱动装置1.610的驱动端与安装座1.692连接;从而在水平驱动装置1.610的驱动下,通过驱动安装座1.692即可带动导向板1.691沿直线导向机构1.68做直线往复运动。
在一些可能实现的方式中,上述水平驱动装置1.610可以包括平移气缸。
在一些可能实现的方式中,如图20所示,上述安装座1.692包括第一连接部s1,以及与两个第一延伸部s1两侧面连接、且沿向上延伸的第二连接部s2;导向板1.691固定在第二连接部s2的外侧;两个第一连接部s1的下表面分别通过直线导向机构1.68安装在导向承载板1.66上。
需要说明的是,对于上述导向板1.691而言,其上表面设置有多个烟支导向槽以及吹气孔,每个吹气孔内部装有带密封的活塞顶杆。具体的,当烟支准备从翻转落料机构中落入塑形机构模具中时,水平驱动装置1.610会提前伸出驱动导向板1.691,吹气孔通气,活塞顶杆在烟支滤嘴端面撞击到导向板1.691上表面之后伸出(在滤嘴段也要塑形时),并通过竖直驱动装置1.62调整导向板1.691的高度,通过活塞顶杆调整烟支处于塑形机构模具中的长度,进而达到调整烟支的塑形长度的目的,然后塑形机构模具合模,开始塑形。当烟支正在塑形机构模具塑形时,水平驱动装置1.610会自动缩回驱动导向板1.691缩回,吹气孔关闭气体,每个吹气孔的活塞顶杆缩回,并通过竖直驱动装置1.62调整导向板1.691的高度,此时烟支在塑形机构模具中完成塑形,塑形机构模具打开,烟支在自重作用下通过烟支导向槽落入接料机构中,完成烟支塑形,然后进行下一循环过程。
另外,对于导向板1.691上的吹气孔而言,可以理解的是,该吹气导向座1.69中设置有与吹气孔连通的气流提供装置,每个吹气孔内部装有带密封的活塞顶杆,在气流作用下活塞顶杆可自由伸缩。
此处需要说明的是,在以下特殊情形下,活塞顶杆才开始动作:除了烟支段塑形以外,烟支滤棒端也要塑形,包括滤嘴端部分塑形或滤嘴端全部塑形时,活塞顶杆会往上伸出,将烟支滤嘴端的部分或全部顶进塑形模具内。
烟支塑形长度调节机构在烟支进行异型塑形工序时,在烟支落入塑形机构的塑形模具时,能够根据烟支的塑形长度需求,通过竖直驱动装置调整导向板的高度,也即调整烟支下端的高度,来控制烟支插入塑形模具的长度,以便塑形机构对烟支进行预定长度的塑形;并在烟支塑形完成后,通过水平驱动装置驱动导向板后移,以将烟支从导向板的导向槽中释放下落至下一工序。
在一些可能实现的方式,如图20所示,上述直线导向机构1.68包括滑块和直线导轨。直线导轨设置于导向承载板1.66的上表面,滑块设置在第一连接部s1的下表面。
如图21所示,本实施例的烟支接料机构,该烟支接料机构包括支撑底板b以及设置在支撑底板b上的回字形传输同步带组件1.71、落料导向组件1.72、视觉检测组件1.73、剔除出料组件1.74。
落料导向组件1.72位于回字形传输同步带组件1.71的一个侧边的正上方,以将烟支通过落料导向组件1.72导向至回字形传输同步带组件1.71中。
视觉检测组件1.73设置于回字形传输同步带组件1.71的输出侧上游,用于检测回字形传输同步带组件1.71中的烟支是否合格。
剔除出料组件1.74设置于回字形传输同步带组件1.71的输出侧下游,用于根据视觉检测组件1.73的对烟支的检测结果,将不合格烟支剔除,将合格烟支输出。
实施例提供的烟支接料机构,落料导向组件位于烟支塑形长度调节机构的下方,在烟支完成塑形后,烟支通过落料导向组件落入回字形传输同步带组件,并通过输出侧上游的视觉检测组件检测烟支是否合格,并在烟支移动至输出侧的剔除出料组件后,根据视觉检测组件的检测结果,将不合格烟支剔除,将合格烟支输出。
以下对本申请实施例提供的回字形传输同步带组件1.71作进一步的说明。
如图22所示,回字形传输同步带组件1.71包括:位于支撑底板b上方的回字形搬运块托板1.711、落烟搬运块1.712、两个主动同步带轮1.713、两个第一张紧同步惰轮1.714、环形同步带1.715、多个第二张紧同步惰轮1.716。
如图22所示,回字形搬运块托板1.711下方通过多个支柱悬空设置在支撑底板b上,多个落烟搬运块1.712均匀分散设置于回字形搬运块托板1.711上。回字形搬运块托板1.711内侧的一组对角分别设置一个第一张紧同步惰轮1.714,另一组对角分别设置一个主动同步带轮1.713。
环形同步带1.715紧套在两个主动同步带轮1.713和两个第一张紧同步惰轮1.714的外侧,且环形同步带1.715的外侧与回字形搬运块托板1.711的内侧不接触。多个第二张紧同步惰轮1.716(并不限制与图2中的4个)设置于环形同步带1.715的内侧、对应剔除出料组件1.74的位置。
另外,如图23所示,该回字形传输同步带组件1.71还包括位于支撑底板b下方的传动带1.717、两个传动轮1.718、两个张紧轮1.719、驱动装置1.7110。
两个传动轮1.718分别与位于支撑底板b上方的两个主动同步带轮1.713的转动轴连接,也就是说,位于支撑底板b下方的传动轮1.718与位于支撑底板b上方的主动同步带轮1.713同步转动。
另外,传动带1.717紧套在两个传动轮1.718和驱动装置1.7110(例如可以为伺服电机)的输出轴的外侧;两个张紧轮1.719位于与驱动装置1.7110的输出轴接触的传动带1.717的两侧,将传动带1.717张紧。
回字形传输同步带组件通过驱动装置驱动传动轮转动,通过传动轮带动位于支撑底板上方的主动同步带轮,通过主动同步带轮带动环形同步带转动,落烟搬运块安装在环形同步带的外表面上,在回字形搬运块托板上滑动,从而使得位于落烟搬运块中的烟支向下游的视觉检测组件、剔除出料组件移动。
需要说明的是,本申请实施例提供的回字形传输同步带组件的工作过程:分3个节拍:第1节拍停在落料导向组件1.72处等待落料完毕,第2节拍匀速搬运烟支途径视觉检测组件1.73完成检测,第3节拍停在出料剔除组件1.74处等待出料剔除完毕,然后回到第1节拍周而复始。
以下对本申请实施例提供的落料导向组件1.72作进一步的说明。
如图24和图25(图24沿aa’位置的剖面示意图)所示,落料导向组件1.72包括:落料导向座1.721、缓冲托架1.722、托架伸缩气缸1.723、直线导轨1.724、导向座开合气缸1.725、落烟搬运块定位板1.726、落料导向座固定块1.727、导向支撑板1.728、光纤传感器1.729、限位块1.7210。
如图24和图25所示,落料导向座1.721包括对合的第一落料导向板(也可以说前落料导向板)1.7211和第二落料导向板1.7212(也可以说后落料导向板),其中,第一落料导向板1.7211在朝向第二落料导向板1.7212的一侧设置有第一半导向槽,第二落料导向板1.7212在朝向第一落料导向板1.7211的一侧设置有第二半导向槽;第一半导向槽和第二半导向槽对合形成烟支导向孔。
在一些可能实现的方式中,可以设置落料导向座1.721的烟支导向孔为锥面,将从上一工序落入的烟支导入到回字形传输同步带组件1.71的落烟搬运块1.712中。
缓冲托架1.722从落料导向座1.721与回字形传输同步带组件1.71之间的位置延伸至落料导向座1.721的内侧。落料导向座1.721的内侧面固定设置有气缸安装板m,托架伸缩气缸1.723设置在气缸安装板m上,且缓冲托架1.722的端部与托架伸缩气缸1.723连接。
缓冲托架1.722可以为钣金件,表面贴附有软质缓冲垫,用于吸收烟支落下的动能,防止烟支缩头。托架伸缩气缸1.723可将缓冲托架1.722进行前后伸缩,释放烟支落下。
如图24所示,光纤传感器1.729设置在落料导向座1.721底部、对应落烟搬运块1.712的位置,以判断落料导向座1.721的烟支导向孔中有无烟支。
如25所示,落烟搬运块定位板1.726位于缓冲托架1.722的下方,落烟搬运块定位板1.726包括前定位板1.7261和后定位板1.7262,以通过前定位板1.7261和后定位板1.7262对落烟搬运块1.712进行定位。
落烟搬运块定位板1.726可将回字形传输同步带组件1.71中的落烟搬运块1.712精确定位,保证烟支顺利下落。
如图24和图25所示,导向支撑板1.728位于落烟搬运块定位板1.726的下方,导向支撑板1.728包括前支撑板1.7281和后支撑板1.7282;前支撑板1.7281和后支撑板1.7282通过直线导轨1.724与支撑底板b连接。
另外,如图25所示,第一落料导向板1.7211、第二落料导向板1.7212分别通过第一支柱t1、第二支柱t2和落料导向座固定块1.727固定在前支撑板1.7281、后支撑板上1.7282上。
导向座开合气缸1.725的缸体1.7251与后支撑板1.7282固定连接,导向座开合气缸1.725的拉头1.7252与前支撑板1.7281固定连接;从而通过导向座开合气缸1.725对前支撑板1.7281、后支撑板上1.7282的反向驱动,进而带动第一落料导向板1.7211和第二落料导向板1.7212的开合。
该导向座开合气缸1.725在所有烟支都落入回字形传输同步带组件1.71中的落烟搬运块1.712后,将第一落料导向板1.7211和第二落料导向板1.7212打开,使烟支可以输出。
另外,如图25所示,在位于导向座开合气缸1.725的前侧、后侧和中部设置有固定在支撑底板b上的限位块,以对导向座开合气缸1.725的拉头1.7252带动前支撑板1.7281的移动位移进行限制,保证气缸打开和关闭的两种状态都在所需位置。
该落料导向组件的工作过程大致为:落料导向座闭合,烟支从塑形长度调节组件的吹气导向座的导向孔中下落至落料导向组件的落料导向座的导向孔中,缓冲托架伸出吸收烟支下落动能,缓冲托架收回,烟支下落至回字形传输同步带组件的落烟搬运块中,落料导向座打开,烟支输出。
以下对本申请实施例提供的视觉检测组件1.73作进一步的说明。
如图26所示,该视觉检测组件1.73包括:固定在支撑底板b上的一台顶端面检测相机1.731、四台侧面检测相机1.732、光源1.733。
顶端面检测相机1.731设置于所述落料导向组件1.72的内侧,且所述顶端面检测相机1.731的高度高于落料导向组件1.72的高度。
四台侧面检测相机1.732中,两个位于回字形传输同步带组件1.71的内侧,两个位于回字形传输同步带组件1.71的外侧;并且四台侧面检测相机1.732的拍照侧从正对的四个方向朝向落烟搬运块1.712;光源1.733设置于四台侧面检测相机1.732的中间区域。
该视觉检测组件1.73在烟支被回字形传输同步带组件1.71搬运途径时,通过一台顶端面检测相机1.731和四台侧面检测相机1.732,对每一只香烟的四个侧面和顶部端面进行高速连拍,以对烟支的成型质量进行检测,并且将不合格品的位置信息传输给剔除出料组件1.74。
以下对本申请实施例提供的剔除出料组件1.74作进一步的说明。
该剔除出料组件包括合格品输出组件和不合格品剔除组件。
如图27所示,合格品输出组件包括:旋转气缸1.741、翻板主轴1.742、翻板1.743、落烟导向块靠板1.744、l型出料导槽板1.745、出料抽板1.746、气缸1.747、直线轴承1.748、直线光轴1.749、轴承座1.7410;
翻板主轴1.742位于回字形传输同步带组件1.71输出侧的落烟搬运块1.712的外侧,且翻板主轴1.742的两端通过轴承安装座1.7410固定在支撑底板b上。旋转气缸1.741设置在翻板主轴1.742的末端。
如图28所示,翻板1.743固定在翻板主轴1.742的上侧,且翻板1.743延伸至落烟搬运块1.712的底部;翻板1.743的下方并列设置有多个l型出料导槽板1.745,且相邻两个l型出料导槽板1.745的竖向延伸部在对应每一落烟搬运块位置处形成出料导槽,出料抽板1.746设置于l型出料导槽板1.745的横向延伸部的下方。
四根直线光轴1.749分别与最左边和最右边的l型出料导槽板1.745的横向延伸部连接,并且直线光轴1.749的两端分别安装有直线轴承1.748,所述气缸1.747连接于同侧的两个直线轴承1.748之间,且两个气缸1.747与外侧的l型出料导槽板1.745的外端面连接。
如图28所示,不合格品剔除组件包括:剔除电磁阀岛1.7411、l型剔除翻板1.7412、转轴1.7413、气缸支座1.7414、剔除气缸1.7415、气缸安装板1.7416。
参考图27和图28,l型剔除翻板1.7412的竖向延伸部位于出料导槽中,l型剔除翻板1.7412的竖向延伸部与l型出料导槽板1.745的竖向延伸部平行;l型剔除翻板1.7412的横向延伸部与l型出料导槽板1.745的横向延伸部的延伸方向相反。
转轴在l型剔除翻板1.7412和l型出料导槽板1.745的转角处贯穿所有的l型剔除翻板1.7412和l型出料导槽板1.745;l型剔除翻板1.7412的竖向延伸部的外侧设置有气缸支座1.7414,剔除气缸1.7415位于气缸支座1.7414的正下方,且剔除气缸1.7415的伸缩轴通过螺纹与气缸支座1.7414连接,剔除气缸1.7415的缸体通过铰链旋转轴安装在气缸安装板1.7416上。
剔除电磁阀岛1.7411固定于支撑底板b的下方,例如剔除电磁阀岛1.7411可以通过螺钉固定在支撑底板b的下方,但并不限制于此;剔除阀岛1.7411包含与每一剔除气缸1.7415一一对应的多组电磁阀(例如可以是30组),且每组电磁阀的2个气管接头通过气管与相对应的剔除气缸1.7415的2个气管接头连接。
具体的,当烟支在回字形传输同步带组件1.71输送作用下,经过视觉检测组件1.73的检测,到达剔除出料组件1.74时,控制系统plc会根据视觉检测组件1.73的检测结果将不合格烟支通道所对应的电磁阀打开,从而控制相对应的剔除气缸1.7415,带动l型剔除翻转逆时针翻转,同时控制系统plc也会根据视觉检测组件的检测结果将合格烟支通道所对应的电磁阀断电关闭,从而控制相对应的剔除气缸缩1.7415缩回或保持缩回状态(前一工序剔除气缸可能处于伸出或者缩回状态),带动l型剔除翻板1.7412顺时针翻转或保持现有状态。
需要说明的是,在完成烟支出料前,剔除电磁阀岛1.7411和l型剔除翻板1.7412进入准备工作状态,此时,合格品输出组件中的旋转气缸1.741旋转,带动翻转主轴1.742上的翻板1.743由水平翻转成竖直,烟支在重力作用下和在l型出料导槽板1.745导向下经过不合格剔除组件,从而自动完成不合格品的剔除,并输送到不合格品输出皮带上,合格品的输出,并输送到卷烟输送装盘平台上。
作为一种实施方式,本实施例的所有关键的物料工序均配有现有的检测传感器,控制器通过采集各传感器的信息来判断各工序所需要的工艺参数,进而控制相应的执行元件来协调所有工序的衔接,使工序之间的物料无缝对接。
本实施例中,视觉检测部分,异型卷烟合格与否的判定标准是:①异型烟矩形端面的最长边与最短边之差小于1mm;②矩形的任意一个角的偏差值在±10°以内。同时满足以上两个条件的产品,会被视觉检测系统判定为合格产品。
视觉检测系统为现有技术,根据需要设定相关参数即可。
根据用户需求和操作要求按现有技术定制开发软件功能,使得系统能实时显示故障报警和运行状态,可进行单动操作和自动运行控制,并自动记录存储生产信息和故障报警信息,方便查询,系统可设置参数为:成型长度,塑型压力,塑型时间,塑型压缩量,生产速度等,同时操作人员也可以依照自己的生产习惯自定义部分工序的工艺参数(成型长度,成型时间,成型压力等参数),其余参数系统会自动适应并作出相应调整。成型机的前部为自动异型卷烟成型平台,可自动完成“天圆地方”及“全方卷烟”等特殊形状卷烟的塑形生产,并自动将不合格的产品剔除排出和合格品输出到异型卷烟输送装盘平台上。成型机的后部为异型卷烟输送装盘平台,该平台对异型卷烟成型平台输送过来的异型卷烟进行运输和汇集,最后由人工进行装盘或装盒。
如图29所示,本实施例的异型卷烟成型方法,按以下进行:烟库人工上料进入烟库整料机构1.2后,烟支自动落料被输送进行拨料排序,然后至烟支上烟机构1.1上烟,塑形长度调节机构1.6调节好位置控制塑形长度,然后翻转落料机构1.3落料,烟支在合模成型的过程中进行烟丝回顶,最后进入接料机构1.7,接料机构1.7通过现有的视觉系统设定好合格标准,判断异型卷烟是否合格,将合格品和不合格品分开,合格品进入异型卷烟输送装盘平台3通过皮带输出,不合格品被剔除,通过不合格品输出皮带1.8落入次品收集盒5,人工定时清理,控制器更新生产数据后,继续进行生产。
本实施例的其中一种技术参数如下表所示:
表1
以上所述仅为本发明的较佳实施例而已,并不用以限制本发明,凡在本发明的精神和原则之内,所作的任何修改、等同替换、改进等,均应包含在本发明的保护范围之内。
起点商标作为专业知识产权交易平台,可以帮助大家解决很多问题,如果大家想要了解更多知产交易信息请点击 【在线咨询】或添加微信 【19522093243】与客服一对一沟通,为大家解决相关问题。
此文章来源于网络,如有侵权,请联系删除


