发热体及其制备方法、加热不燃烧气雾形成装置与流程



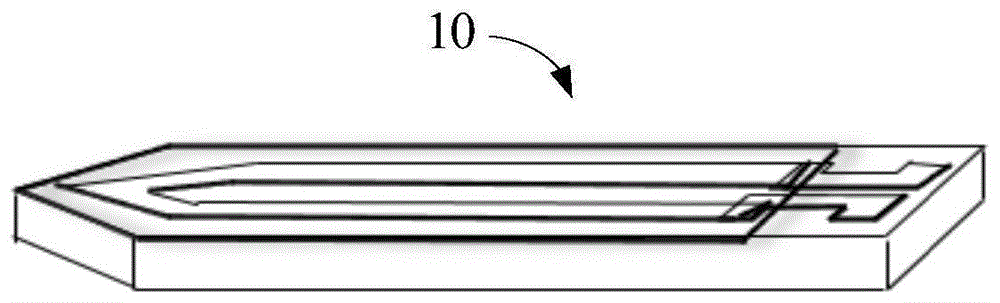
本发明涉及烟具技术领域,特别是涉及一种发热体及其制备方法、加热不燃烧气雾形成装置。
背景技术:
传统烟草通过燃烧的方式产生烟气,在超过800℃的高温炙烤下,大量的有害物质挥发出来。为了满足人们对尼古丁的需求,同时降低烟草燃烧带来的危害,加热不燃烧气雾形成装置(烟具)应运而生。加热不燃烧烟具主要是以200℃~400℃的低温烘烤烟草,使之产生烟气,但又不会有大量裂解带来的有害物质。
目前的加热不燃烧烟具采用的加热方式主要为中心加热或者四周加热。其中,中心加热的热效率高,且不需要进行隔热处理,但中心加热不可避免发热体与烟草接触。所以,以中心加热方式的加热不燃烧烟具在使用过程中,烟草碳化的同时析出无法汽化的液态物质,不可避免地形成了烟垢,而烟垢容易粘附在发热体表面难以清洁,使得以中心加热方式的加热不燃烧烟具在使用一段时间后,抽吸口感容易变差。
技术实现要素:
基于此,有必要提供一种抗烟垢粘附的发热体。
此外,还有必要提供一种抗烟垢粘附的发热体的制备方法和包括该抗烟垢粘附的发热体的加热不燃烧烟具。
一种发热体,包括:
基体,所述基体具有第一表面和与所述第一表面相对的第二表面;
发热层,设于所述第一表面上;
第一复合层,设于所述发热层上;
第二复合层,设于所述第二表面上;
所述第一复合层由用于制备瓷膜的原料与第一组分混合后烧结而成,所述第二复合层由用于制备瓷膜的原料与第二组分混合后烧结而成,所述第一组分和所述第二组分独立选自石墨、氮化硼、二硫化钼、聚酰亚胺和聚四氟乙烯中的一种。
上述发热体包括通过第一复合层和第二复合层,第一复合层和第二复合层均是由石墨、氮化硼、二硫化钼、聚酰亚胺及聚四氟乙烯中的一种和用于制备瓷膜的原料混合后烧结而成。通过用于制备瓷膜的原料与石墨、氮化硼、二硫化钼、聚酰亚胺及聚四氟乙烯中的一种的配合,使得制得的复合层具有良好的抗烟垢粘附性,不易粘附烟垢。
在其中一个实施例中,所述第一复合层中用于制备瓷膜的原料与所述第一组分的质量之比为(99~80):(1~20),所述第二复合层中用于制备瓷膜的原料与第二组分的质量之比为(99~80):(1~20)。
在其中一个实施例中,所述第一复合层中用于制备瓷膜的原料为水性无机陶瓷涂料;及/或,所述第二复合层中用于制备瓷膜的原料为水性无机陶瓷涂料。
在其中一个实施例中,所述第一复合层中用于制备瓷膜的原料选自用于制备有机硅瓷膜的原料、用于制备纳米氧化铝瓷膜的原料和用于制备碳化硅瓷膜的原料中的一种;及/或,所述第二复合层中用于制备瓷膜的原料选自用于制备有机硅瓷膜的原料、用于制备纳米氧化铝瓷膜的原料和用于制备碳化硅瓷膜的原料中的一种。
在其中一个实施例中,以质量百分数计,所述第一复合层中用于制备瓷膜的原料包括50%~70%纳米氧化硅分散液、10%~20%甲基三甲氧基硅烷、5%~10%正硅酸乙酯、1%~5%的有机硅消泡剂和5%~15%的铜铬黑;及/或,所述第二复合层中用于制备瓷膜的原料包括50%~70%纳米氧化硅分散液、10%~20%甲基三甲氧基硅烷、5%~10%正硅酸乙酯、1%~5%的有机硅消泡剂和5%~15%的铜铬黑。
在其中一个实施例中,所述第一复合层的烧结温度为200℃~700℃,所述第二复合层的烧结温度为200℃~700℃。
在其中一个实施例中,所述第一复合层的厚度为1μm~30μm;及/或,所述第二复合层的厚度为1μm~30μm;及/或,所述发热层的厚度为10μm~15μm。
在其中一个实施例中,所述发热层包括发热线路和与所述发热线路电连接的导电线路。
在其中一个实施例中,所述发热体还包括第一过渡层,所述第一过渡层设于所述发热层和所述第一复合层之间;及/或
所述发热体还包括第二过渡层,所述第二过渡层设于所述基体和所述第二复合层之间。
在其中一个实施例中,所述发热体还包括第一介质层,所述第一介质层设于所述发热层与所述基体之间;及/或,所述发热体还包括第二介质层,所述第二介质层设于所述第二复合层与所述基体之间。
在其中一个实施例中,所述发热体还包括第一介质层、第二介质层、第一过渡层和第二过渡层,所述第一介质层、所述发热层、所述第一过渡层和所述第一复合层依次层叠在所述基体的第一表面,所述第二介质层、所述第二过渡层和所述第二复合层依次层叠在所述基体的第二表面。
在其中一个实施例中,所述第一过渡层为粗化的玻璃釉层;及/或,所述第二过渡层为粗化的玻璃釉层。
在其中一个实施例中,所述第一介质层为热膨胀系数为9×10-6(1/k)~13×10-6(1/k)的玻璃釉层;及/或,所述第二介质层为热膨胀系数为9×10-6(1/k)~13×10-6(1/k)的玻璃釉层。
在其中一个实施例中,所述基体的材料为不锈钢、氧化锆、氧化铝、氮化硅、碳化硅、氮化铝、氧化硅及镍钴合金中的至少一种。
一种发热体的制备方法,包括以下步骤:
在基体的第一表面制备发热层;
将用于制备瓷膜的原料混合熟化后,与石墨、氮化硼、二硫化钼、聚酰亚胺及聚四氟乙烯中的一种混合,得到复合层的浆料;及
将所述复合层的浆料分别印刷在所述发热层上和所述基体的第二表面后,烧结,在所述发热层上形成第一复合层和在所述基体的第二表面上形成第二复合层。
在其中一个实施例中,制备所述第一复合层时的烧结温度为200℃~700℃,及/或,制备所述第二复合层时的烧结温度为200℃~700℃。
在其中一个实施例中,在制备所述发热层之前,还包括分别在所述基体的第一表面和第二表面印刷介质层的浆料后烧结而得到第一介质层和第二介质层的步骤,所述第一介质层位于所述第一表面上,所述第二介质层位于所述第二表面上;制备所述第一介质层时的烧结温度为700℃~900℃;及/或,制备所述第二介质层时的烧结温度为700℃~900℃。
在其中一个实施例中,在制备第二复合层之前,还包括分别在所述第二介质层上印刷第二过渡层的浆料后烧结而得到第二过渡层的步骤;及/或,在将所述复合层浆料印刷在所述发热层的步骤之前,还包括在所述发热层上印刷第一过渡层的浆料后烧结而得到第一过渡层的步骤,所述第二过渡层和所述第二过渡层的烧结温度均为700℃~900℃。
在其中一个实施例中,在得到所述第一过渡层的步骤之后,还包括对所述第一过渡层进行粗化处理的步骤;及/或,在得到所述第二过渡层的步骤之后,还包括对所述第二过渡层进行粗化处理的步骤。
一种加热不燃烧气雾形成装置,包括上述的发热体或上述的发热体的制备方法制得的发热体。
附图说明
图1为一实施方式的发热体;
图2为图1所示的发热体的截面图;
图3为图1所示的发热体的分解图。
具体实施方式
为了便于理解本发明,下面将参照相关附图对本发明进行更全面的描述。附图中给出了本发明的部分实施例。但是,本发明可以以许多不同的形式来实现,并不限于本文所描述的实施例。相反地,提供这些实施例的目的是使本发明公开内容更加透彻全面。
除非另有定义,本文所使用的所有的技术和科学术语与属于本发明的技术领域的技术人员通常理解的含义相同。本文中在本发明的说明书中所使用的术语只是为了描述具体的实施例的目的,不是旨在于限制本发明。
请参阅图1、图2和图3,本发明一实施方式提供了一种发热体10,该发热体10包括基体110、第一介质层120、第二介质层130、发热层140、第一过渡层150、第二过渡层160、第一复合层170和第二复合层180。
具体地,基体110用于承载其他层,基体110具有第一表面111和与第一表面111相对的第二表面112。基体110的材料选自不锈钢、氧化锆、氧化铝、氮化硅、碳化硅、氮化铝、氧化硅和镍钴合金中的至少一种。在其中一个实施例中,基体110的材料选自不锈钢、氧化锆、氧化铝、氮化硅、碳化硅、氮化铝、氧化硅和镍钴合金中的一种。基体110的材料包括镍钴合金时,高温抗氧化能力更强。
优选地,基材的材料为不锈钢。进一步地,基材的材料为430不锈钢。采用不锈钢作为基材具有良好的抗弯折能力,使得发热体10的抗弯折能力强,不易折断。
在其中一个实施例中,基体110的厚度为300μm~600μm。当然,在其他实施例中,基体110的厚度可以根据实际需求进行调整。
第一介质层120位于基体110的第一表面111,起过渡和/或绝缘作用。在其中一个实施例中,第一介质层120为热膨胀系数为9×10-6(1/k)~13×10-6(1/k)的玻璃釉层。当然,第一介质层120不限于热膨胀系数为9×10-6(1/k)~13×10-6(1/k)的玻璃釉层,在其他一些实施例中,第一介质层120的材料可以根据实际情况进行调整。
在本实施方式中,第一介质层120的厚度为10μm~30μm。当然,在其他实施例中,第一介质层120的厚度不限于20μm~30μm,可以根据实际需求进行调整。
第二介质层130位于基体110的第二表面112,起过渡和/或绝缘作用。在其中一个实施例中,第二介质层130为热膨胀系数为9×10-6(1/k)~13×10-6(1/k)的玻璃釉层。当然,第二介质层130不限于热膨胀系数为9×10-6(1/k)~13×10-6(1/k)的玻璃釉层,在其他一些实施例中,第二介质层130的材料可以根据实际情况进行调整。
在本实施方式中,第二介质层130的厚度为20μm~30μm。当然,在其他实施例中,第二介质层130的厚度不限于20μm~30μm,可以根据实际需求进行调整。
发热层140设于第二介质层130远离第一表面111的一侧,发热层140用于发热。具体地,发热层140包括发热线路141和与发热电离电连接的导电线路142。发热线路141用于发热,导电线路142用于外部电源与发热线路141的电连接。在本实施方式中,导电线路142的材料为银。发热电路的材料选自银、银钯合金、铂、镍和钨中的一种。当然,在其他一些实施例中,导电线路142的材料和发热电路的材料不限于上述,还可以是本领域常用的其他材料。
在本实施方式中,发热层140的厚度为10μm~15μm。当然,在其他实施例中,发热层140的厚度不限于10μm~15μm,可以根据实际需求进行调整。
第一过渡层150设于发热层140远离第一介质层120的一侧,第一过渡层150起绝缘和/或过渡的作用,用于防止漏电和/或增强发热层140与复合层之间的粘附力。在其中一个实施例中,第一过渡层150起绝缘作用,用于发热层140的绝缘。在另一个实施例中,第一过渡层150起绝缘和过渡作用,不仅用于发热层140的绝缘,还用于增强发热层140与第一复合层170的粘附力,使得发热层140与第一复合层170不易分离。在其中一个实施例中,第一复合层170不具有导电性,第一过渡层150用于增强发热层140与第一复合层170的粘附力。在本实施方式中,第一过渡层150为粗化的玻璃釉层。当然,在其他一些实施例中,第一过渡层150不限于粗化的玻璃釉层,还可以根据实际需求选择本领域常用的其他用于绝缘和/或过渡的材料。
在本实施方式中,第一过渡层150的厚度为10μm~20μm。当然,在其他实施例中,第一过渡层150的厚度不限于10μm~20μm,可以根据实际需求进行调整。
第二过渡层160设于第二介质层130远离基体110第二表面112的一侧,第二过渡层160起绝缘和/或过渡的作用,用于防止漏电和/或增强第二介质层130与第二复合层180的粘附力。在本实施方式中,第二过渡层160为粗化的玻璃釉层。当然,在其他一些实施例中,第二过渡层160不限于粗化的玻璃釉层,还可以根据实际需求选择本领域常用的其他用于绝缘和/或过渡的材料。
在本实施方式中,第二过渡层160的厚度为10μm~20μm。当然,在其他实施例中,第二过渡层160的厚度不限于10μm~20μm,可以根据实际需求进行调整。
第一复合层170设于第一过渡层150上,第二复合层180设于第二过渡层160上,第一复合层170和第二复合层180均具有抗烟垢粘附的作用,均具有疏水疏油性。
具体地,第一复合层170由用于制备瓷膜的原料与第一组分混合后烧结而成;第二复合层180由用于制备瓷膜的原料与第二组分混合后烧结而成,其中,第一组分和第二组分分别独立选自石墨、氮化硼、二硫化钼、聚酰亚胺及聚四氟乙烯中的至少一种。由于瓷膜耐高温不超过300℃,硬度低且脆,所以,瓷膜本身不能直接应用于加热不燃烧烟具的发热体10上。上述发热体10的第一复合层170和第二复合层180均是将石墨、氮化硼、二硫化钼、聚酰亚胺及聚四氟乙烯中的至少一种与用于制备瓷膜的原料混合之后烧结而成,通过引入的石墨、氮化硼、二硫化钼、聚酰亚胺和聚四氟乙烯中的至少一种,以提高第一复合层170和第二复合层180的防粘性能、导热性能、耐高温性能和硬度。
在其中一个实施例中,第一组分和第二组分分别独立选自石墨、氮化硼、二硫化钼、聚酰亚胺及聚四氟乙烯中的一种。
在其中一个实施例中,第一复合层170中用于制备瓷膜的原料与第一组分的质量之比为(99~80):(1~20)。优选地,第一复合层170中用于制备瓷膜的原料与第一组分的质量之比为(95~90):(5~10)。第一复合层170中用于制备瓷膜的原料与第一组分按照上述比例设置,能够提高第一复合层170的耐温性能和硬度。
在其中一个实施例中,第二复合层180中用于制备瓷膜的原料与第二组分的质量之比为(99~80):(1~20)。优选地,第二复合层180中用于制备瓷膜的原料与第二组分的质量之比为(95~90):(5~10)。第二复合层180中用于制备瓷膜的原料与第一组分按照上述比例设置,能够提高第二复合层180的耐温性能和硬度。
在其中一个实施例中,第一复合层170中用于制备瓷膜的原料为水性无机陶瓷涂料。
在其中一个实施例中,第二复合层180中用于制备瓷膜的原料为水性无机陶瓷涂料。
在其中一个实施例中,第一复合层170中用于制备瓷膜的原料为水性无机陶瓷涂料,第二复合层180中用于制备瓷膜的原料为水性无机陶瓷涂料。
在其中一个实施例中,第一复合层170中用于制备瓷膜的原料为用于制备有机硅瓷膜的原料、用于制备纳米氧化铝瓷膜的原料和用于制备碳化硅瓷膜的原料中的一种。
在其中一个实施例中,第二复合层180中用于制备瓷膜的原料为用于制备有机硅瓷膜的原料、用于制备纳米氧化铝瓷膜的原料和用于制备碳化硅瓷膜的原料中的一种。
在其中一个实施例中,第一复合层170的瓷膜为用于制备有机硅瓷膜、用于制备纳米氧化铝瓷膜和用于制备碳化硅瓷膜中的一种,第二复合层180的瓷膜为用于制备有机硅瓷膜、用于制备纳米氧化铝瓷膜和用于制备碳化硅瓷膜中的一种。
在其中一个实施例中,以质量百分数计,第一复合层170中用于制备瓷膜的原料包括50%~70%纳米氧化硅分散液、10%~20%甲基三甲氧基硅烷、5%~10%正硅酸乙酯、1%~5%的有机硅消泡剂和5%~15%的铜铬黑。采用纳米氧化硅分散液作为瓷膜的原料能够提高发热体10的稳定性和耐温性。优选地,第一复合层170中用于制备瓷膜的原料包括55%~65%纳米氧化硅分散液、15%~20%甲基三甲氧基硅烷、6%~9%正硅酸乙酯、1%~3%的有机硅消泡剂和10%~15%的铜铬黑。更优选地,第一复合层170中用于制备瓷膜的原料包括60%纳米氧化硅分散液、18%甲基三甲氧基硅烷、7%正硅酸乙酯、2%的有机硅消泡剂和13%的铜铬黑。
在其中一个实施例中,以质量百分数计,第二复合层180中用于制备瓷膜的原料包括50%~70%纳米氧化硅分散液、10%~20%甲基三甲氧基硅烷、5%~10%正硅酸乙酯、1%~5%的有机硅消泡剂和5%~15%的铜铬黑。优选地,第二复合层180中用于制备瓷膜的原料包括55%~65%纳米氧化硅分散液、15%~20%甲基三甲氧基硅烷、6%~9%正硅酸乙酯、1%~3%的有机硅消泡剂和10%~15%的铜铬黑。更优选地,第二复合层180中用于制备瓷膜的原料包括60%纳米氧化硅分散液、18%甲基三甲氧基硅烷、7%正硅酸乙酯、2%的有机硅消泡剂和13%的铜铬黑。
在其中一个实施例中,第一组分为石墨粉。进一步地,第一组分为200目~5000目的石墨粉。石墨能够提高第一复合层170和第二复合层180的耐温性和硬度,并且石墨具有良好的自润滑效果,能够提高第一复合层170和第二复合层180的防粘性能。此外,石墨导热性能好,还可以使得发热体10的温度场更均匀,一定程度上降低烟垢的产生。
在其中一个实施例中,第二组分为石墨粉。进一步地,第二组分为200目~5000目的石墨粉。石墨能够提高第一复合层170和第二复合层180的耐温性和硬度,并且石墨具有良好的自润滑效果,能够提高第一复合层170和第二复合层180的防粘性能。此外,石墨导热性能好,可以使得发热体10的温度场更均匀,一定程度上降低烟垢的产生。
在其中一个实施例中,第一组分为石墨粉,第二组分也为石墨粉。进一步地,第一组分为200目~5000目的石墨粉,第二组分为200目~5000目的石墨粉。
在其中一个实施例中,第一复合层170中用于制备瓷膜的原料包括50%~70%纳米氧化硅分散液、10%~20%甲基三甲氧基硅烷、5%~10%正硅酸乙酯、1%~5%的有机硅消泡剂和5%~15%的铜铬黑,第一组分为石墨粉;及/或,第二复合层180中用于制备瓷膜的原料包括50%~70%纳米氧化硅分散液、10%~20%甲基三甲氧基硅烷、5%~10%正硅酸乙酯、1%~5%的有机硅消泡剂和5%~15%的铜铬黑,第二组分为石墨粉。
需要说明的是,第一复合层170的材料与第二复合层180的材料可以相同,也可以不同。第一复合层170的材料和第二复合层180的材料可以因选择的不同而不同。例如,第一复合层170由瓷膜的原料和石墨混合后烧结而成,第二复合层180由瓷膜的原料和氮化硼混合后烧结而成。又例如,第一复合层170由瓷膜的原料和石墨混合后烧结而成,第二复合层180由瓷膜的原料和石墨混合后烧结而成,但第一复合层170中用于制备瓷膜的原料与第二复合层180中用于制备瓷膜的原料在组成和/或含量上存在差异。
在其中一个实施例中,第一复合层170的厚度为1μm~30μm。进一步地,第一复合层170的厚度为10μm~20μm。更进一步地,第一复合层170的厚度为10μm、12μm、16μm18μm或20μm。
在其中一个实施例中,第二复合层180的厚度为1μm~30μm。进一步地,第二复合层180的厚度为10μm~20μm。更进一步地,第二复合层180的厚度为10μm、12μm、16μm18μm或20μm。
在图示的实施方式中,发热体10为片式结构。当然,发热体10的形状不限于片式,还可以是针式、管式、三叉戟或者其他异形结构。
可以理解的是,在一些实施方式中,基体110、第二介质层130、下绝缘过滤层和第二复合层180中的至少一个具有绝缘性或对发热层已进行绝缘处理,能够确保发热体10的安全性,发热层140与基体110之间的粘附较牢,此时,第一介质层120可以省略,发热层140层叠于基体110的第一表面111。在一些实施方式中,基体110、第二过渡层160和第二复合层180中的至少一个具有绝缘性或对发热层已进行绝缘处理,能确保发热体10安全,基体110与第二过渡层160之间的粘附较牢。此时,第二介质层130也可以省略,第二过渡层160设于基体110的第二表面112。当然,在一些实施方式中,第一介质层120和第二介质层130均可以省略,此时,发热层140设于基体110的第一表面111,第二过渡层160设于基体110的第二表面112。
可以理解的是,在一些实施方式中,第二复合层180与第二介质层130的之间的粘附力较强,基体110、第二介质层130和第二复合层180中的至少一个具有绝缘性,此时,第二过渡层160可以省略,第二复合层180设于第二介质层130远离第二表面112的一侧。当然,在一些实施例中,第二复合层180与基体110之间的粘附力较强,基体110和第二复合层180中的至少一个具有绝缘性,此时,第二介质层130和第二过渡层160均可以省略,第二复合层180设于基体110的第二表面112。
上述发热体10通过第一复合层170和第二复合层180的设置,使得发热体10不但具有良好的防粘性,使得上述发热体10应用于加热不燃烧烟具时,不易在发热体10的表面沉积烟垢,提高了吸食体验。在第一复合层170及/或第二复合层180中含有石墨、氮化硼和二硫化钼中的至少一种时,发热体10还具有良好的导热性、耐高温和硬度,不易形成烟垢,进一步提高了其吸食体验。在第一复合层170及/或第二复合层180中含有聚酰亚胺和聚四氟乙烯中的至少一种时,发热体10具有良好的耐温性能。此外,通过第一介质层120、第二介质层130、第一过渡层150及第二过渡层160的设置,提高了发热体10的各层之间的粘附力,为发热体10的安全提供保障。
本发明一实施方式还提供上述发热体10的制备方法,该方法包括步骤:
步骤s110、在基体110上制备第一介质层120和第二介质层130。
具体地,基体110的材料选自不锈钢、氧化锆、氧化铝、氮化硅、碳化硅、氮化铝、氧化硅和镍钴合金中的至少一种。需要说明的是,镍钴合金是指能在600℃以上的高温及一定应力作用下长期工作的合金。优选地,基材的材料为不锈钢。在本实施方式中,基材的材料为430不锈钢。
在其中一个实施例中,在基体110上制备第一介质层120和第二介质层130的步骤包括:根据需要制备的第一介质层120和第二介质层130的性能,配制第一介质层120和第二介质层130所用的浆料;接着采用双面印刷,在基体110的第一表面111和第二表面112印刷一定厚度的浆料后烧结,得到第一介质层120和第二介质层130。第一介质层120位于第一表面111上,第二介质层130位于第二表面112上。
在本实施方式中,在基体110的第一表面111和第二表面112印刷的浆料的厚度为10μm~30μm。制备第一介质层120时的烧结温度为700℃~900℃。制备第二介质层130时的烧结温度为700℃~900℃。进一步地,在基体110的第一表面111和第二表面112印刷的浆料的厚度为20μm~30μm。制备第一介质层120时的烧结温度为800℃~900℃。制备第二介质层130时的烧结温度为800℃~900℃。
步骤s120、在第一介质层120上制备发热层140。
具体地,在第一介质层120印刷一定厚度的发热线路141的浆料和导电线路142的浆料之后烧结,得到具有发热线路141和导电线路142的发热层140。发热线路141的浆料根据所需制备的发热线路141选择,导电线路142的浆料根据所需制备的导电线路142进行选择。发热线路141和导电线路142的材料如上发热体10处的描述,此处不再赘述。进一步地,制备发热线路141和导电线路142时的烧结温度为700℃~900℃。更进一步地,制备发热线路141和导电线路142时的烧结温度为800℃~900℃。
在本实施方式中,在第一介质层120上印刷厚度为10μm~15μm的银钯浆,在800℃~850℃下烧结40min形成发热线路141。
当然,在一些实施例中,制备第一介质层120和/或制备第二介质层130的步骤可以省略,此时,其他步骤对应更改即可。例如,省略第一介质层120时,直接在基体110的第一表面111上制备发热层140。省略第二介质层130时,在基体110的第二表面112直接制备第二过渡层160或第二复合层180。
步骤s130、在发热层140和第二介质层130上制备第一过渡层150和第二过渡层160。
具体地,在发热层140印刷第一过渡层150的浆料和在第二介质层130上印刷第二过渡层160的浆料后,烧结,得到第一过渡层150和第二过渡层160。第一过渡层150位于发热层140远离第一表面111的一侧,第二过渡层160位于第二介质层130远离第二表面112的一侧。第一过渡层150的浆料和第二过渡层160的浆料根据需要制备的第一过渡层150和第二过渡层160进行对应配置。第一过渡层150和第二过渡层160的材质如上发热体10处的描述,此处不再赘述。进一步地,进一步地,制备第一过渡层150和第二过渡层160时的烧结温度为700℃~900℃。更进一步地,制备第一过渡层150和第二过渡层160时的烧结温度为800℃~900℃。
在本实施方式中,在发热层140印刷第一过渡层150的浆料的厚度为10μm~20μm;在第二介质层130上印刷第二过渡层160的浆料的厚度为10μm~20μm。第一过渡层150的浆料和第二过渡层160的浆料均为玻璃浆料。制备第一过渡层150和第二过渡层160时的烧结温度为800℃~800℃,烧结时间为30min。
在一些实施例中,制备第一过渡层150和/或制备第二过渡层160的步骤可以省略,此时,相应的步骤s130删除。
步骤s140、在第一过渡层150和第二过渡层160上制备第一复合层170和第二复合层180,得到发热体10。
具体地,第一复合层170的材料和第二复合层180的材料如上述,此处不再赘述。
在本实施方式中,第一复合层170和第二复合层180所用的浆料相同。因此,将用于制备瓷膜的原料熟化后,与石墨、氮化硼、二硫化钼、聚酰亚胺及聚四氟乙烯中的一种混合,制得复合层的浆料;接着将复合层的浆料印刷在第一过渡层150上和第二过渡层160上后烧结,得到第一复合层170和第二复合层180。第一复合层170位于第一过渡层150远离发热层140的一侧,第二复合层180位于第二过渡层160远离第二介质层130的一侧。
进一步地,制备第一复合层170和第二复合层180时的烧结温度均为200℃~700℃。复合层的浆料在第一过渡层150上的印刷厚度为1μm~30μm,复合层的浆料在第二过渡层160上的印刷厚度为1μm~30μm。更进一步地,制备第一复合层170和第二复合层180时的烧结温度均为400℃~600℃。复合层的浆料在第一过渡层150上的印刷厚度为10μm~20μm,复合层的浆料在第二过渡层160上的印刷厚度为10μm~20μm。
在其中一个实施例中,第一组分和第二组分均为2000目石墨粉,用于制备瓷膜的原料与石墨粉的比例为40:1,印刷方式为丝网印刷,制备第一复合层170和第二复合层180时的烧结温度均为500℃,烧结时间为1h。复合层的浆料在第一过渡层150上的印刷厚度为15μm,复合层的浆料在第二过渡层160上的印刷厚度为15μm。
当然,在其他一些实施例中,印刷的方式不限于丝网印刷,还可以是其他的方式。可以理解的是,当需要制备的第一复合层170的组成与需要制备的第二复合层180的组成不同时,对应更改制备复合层的浆料即可。当然,制备第一复合层170和第二复合层180的烧结温度可以相同,也可以不同,具体可根据实际情况进行选择,只要烧结温度为200℃~700℃即可。
在其中一个实施例中,在第一过渡层150和第二过渡层160上制备第一复合层170和第二复合层180之前,还包括对第一过渡层150和第二过渡层160进行粗化处理的步骤。粗化处理用于提高第一过渡层150与第一复合层170之间的粘附力和提高第二过渡层160与第二复合层180之间的粘附力。
进一步地,粗化处理的方式为喷砂、打磨或共烧高熔点微纳米颗粒。当然,粗化处理的方式不限于上述,还可以是本领域常用的其他粗化方式。在本实施方式中,采用喷砂的方式进行粗化处理,具体地,喷砂采用5000目的石英砂。
上述发热体10的制备方法通过低温烧结的方式制备第一复合层170和第二复合层180,该方法简捷,适用于工业化生产。
此外,本发明一实施方式还提供一种加热不燃烧气雾形成装置,该加热不燃烧气雾形成装置包括上述发热体10或上述发热体10的制备方法制备得到的发热体10。
由于上述加热不燃烧气雾形成装置包括抗烟垢粘附的上述发热体10,所以上述加热不燃烧气雾形成装置不易形成烟垢,使用寿命长,能改善用户体验。
具体实施例
以下结合具体实施例进行详细说明。以下实施例如未特殊说明,则不包括除不可避免的杂质外的其他组分。实施例中采用药物和仪器如非特别说明,均为本领域常规选择。实施例中未注明具体条件的实验方法,按照常规条件,例如文献、书本中所述的条件或者生产厂家推荐的方法实现。
实施例1
实施例1的发热体的结构如图3所示,实施例1的发热体由基体、第一介质层、第二介质层、发热层、第一过渡层、第二过渡层、第一复合层和第二复合层组成。其中,基体为430不锈钢,基体的厚度为300μm;第一介质层和第二介质层均为热膨胀系数为9.3×10-6(1/k)的玻璃釉层,第一介质层的厚度为15μm,第二介质层的厚度为15μm;发热层由发热线路和导电线路组成,发热线路的材料为银钯合金,导电线路的材料为银,发热线路的厚度为10μm,导电线路的厚度为10μm;第一过渡层和第二过渡层的材料相同,均为粗化的玻璃釉层,第一过渡层的厚度为5μm,第二过渡层的厚度为5μm;第一复合层和第二复合层的材料相同,均由用于制备瓷膜的原料和石墨粉烧结而成,其中,以质量份数计,第一复合层和第二复合层中用于制备瓷膜的原料均是由60份纳米氧化硅分散液、18份甲基三甲氧基硅烷、7份正硅酸乙酯、2份的有机硅消泡剂和13份的铜铬黑组成;第一复合层和第二复合层的石墨粉均是2000目的石墨粉,第一复合层中用于制备瓷膜的原料与石墨粉的质量之比和第二复合层中用于制备瓷膜的原料与石墨粉的质量之比均为95:5,第一复合层的厚度为15μm,第二复合层的厚度为15μm。
实施例1的发热体的制备步骤如下:
(1)将60份纳米氧化硅分散液、18份甲基三甲氧基硅烷、7份正硅酸乙酯、2份的有机硅消泡剂和13份的铜铬黑混合,在24℃条件下搅拌2h进行熟化,得到熟化后的用于制备瓷膜的原料;接着按照熟化后的用于制备瓷膜的原料与石墨粉的质量之比为95:5的比例将熟化后的用于制备瓷膜的原料与石墨粉混合后,搅拌2h,得到用于制备第一复合层和第二复合层的浆料,即复合层浆料。
(2)在430不锈钢基片双面印刷一层厚度25μm的介质层浆料,在850℃下烧结40min形成第一介质层和第二介质层,其中,介质层浆料由sio2、al2o3、b2o3、cao、zno、tio2和水组成。
(3)在烧结后的第一介质层上印刷厚度为10μm的银钯浆,在850℃下烧结40min形成发热线路,得到发热片。
(4)在(3)制得的发热片上双面印刷一层厚度20μm的玻璃浆料,在800℃下烧结30min形成第一过渡层和第二过渡层,其中,玻璃浆料的组分为sio2、al2o3、b2o3、cao、bao、zno和水。
(5)对第一过渡层远离发热层的表面和第二过渡层远离第二介质层的表面分别进行喷砂处理形成粗糙表面,其中,喷砂采用粒径为5000目的石英砂。
(5)将(1)制得的复合层的浆料通过丝印的方式在喷砂处理后的第一过渡层和第二过渡层上各印刷一层厚度为15μm的复合层的浆料,然后在220℃下烧结1h,得到具有第一复合层和第二复合层的发热体。
实施例2
实施例2的发热体的结构与实施例1相同,实施例2的发热体与实施例1的发热体的不同仅在于,制备实施例2的第一复合层和第二复合层时的烧结温度与实施例1不同,实施例2的第一复合层和第二复合层的烧结温度均为280℃。
实施例3
实施例3的发热体的结构与实施例1相同,实施例3的发热体与实施例1的发热体的不同仅在于,制备实施例3的第一复合层和第二复合层时的烧结温度与实施例1不同,实施例3的第一复合层和第二复合层的烧结温度均为350℃。
实施例4
实施例4的发热体的结构与实施例1相同,实施例4的发热体与实施例1的发热体的不同仅在于,制备实施例4的第一复合层和第二复合层时的烧结温度与实施例1不同,实施例4的第一复合层和第二复合层的烧结温度均为500℃。
实施例5
实施例5的发热体的结构与实施例1相同,实施例5的发热体与实施例1的发热体的不同仅在于,制备实施例5的第一复合层和第二复合层时的烧结温度与实施例1不同,实施例5的第一复合层和第二复合层的烧结温度均为600℃。
实施例6
实施例6的发热体的结构与实施例1相同,实施例6的发热体与实施例1的发热体的不同仅在于,制备实施例6的第一复合层和第二复合层的浆料与实施例1不同,实施例6的复合层的浆料中,用于制备瓷膜的原料与2000目的石墨粉的质量之比为90:10。
实施例7
实施例7的发热体的结构与实施例6相同,实施例7的发热体与实施例6的发热体的不同仅在于,制备实施例7的第一复合层和第二复合层时的烧结温度与实施例6不同,实施例7的第一复合层和第二复合层的烧结温度为280℃。
实施例8
实施例8的发热体的结构与实施例3相同,实施例8的发热体与实施例3的发热体的不同仅在于,制备实施例8的第一复合层和第二复合层的浆料与实施例3不同,实施例8的复合层的浆料中,用于制备瓷膜的原料与2000目的石墨粉的质量之比为99:1。
实施例9
实施例9的发热体的结构与实施例3相同,实施例9的发热体与实施例3的发热体的不同仅在于,制备实施例9的第一复合层和第二复合层的浆料与实施例3不同,实施例9的复合层的浆料中,用于制备瓷膜的原料与2000目的石墨粉的质量之比为80:20。
测试:
测试各实施例的发热体的水接触角和二碘甲烷接触角,并计算各实施例的发热体的表面能,测试各实施例的耐温性能。结果如表1所示。
表1
由上表可知,实施例1~9的发热体具有良好的疏水疏油性能,而且耐高温能力强。
以上所述实施例的各技术特征可以进行任意的组合,为使描述简洁,未对上述实施例中的各个技术特征所有可能的组合都进行描述,然而,只要这些技术特征的组合不存在矛盾,都应当认为是本说明书记载的范围。
以上所述实施例仅表达了本发明的几种实施方式,其描述较为具体和详细,但并不能因此而理解为对发明专利范围的限制。应当指出的是,对于本领域的普通技术人员来说,在不脱离本发明构思的前提下,还可以做出若干变形和改进,这些都属于本发明的保护范围。因此,本发明专利的保护范围应以所附权利要求为准。
起点商标作为专业知识产权交易平台,可以帮助大家解决很多问题,如果大家想要了解更多知产交易信息请点击 【在线咨询】或添加微信 【19522093243】与客服一对一沟通,为大家解决相关问题。
此文章来源于网络,如有侵权,请联系删除


