一种列车自动翻车作业系统和方法与流程



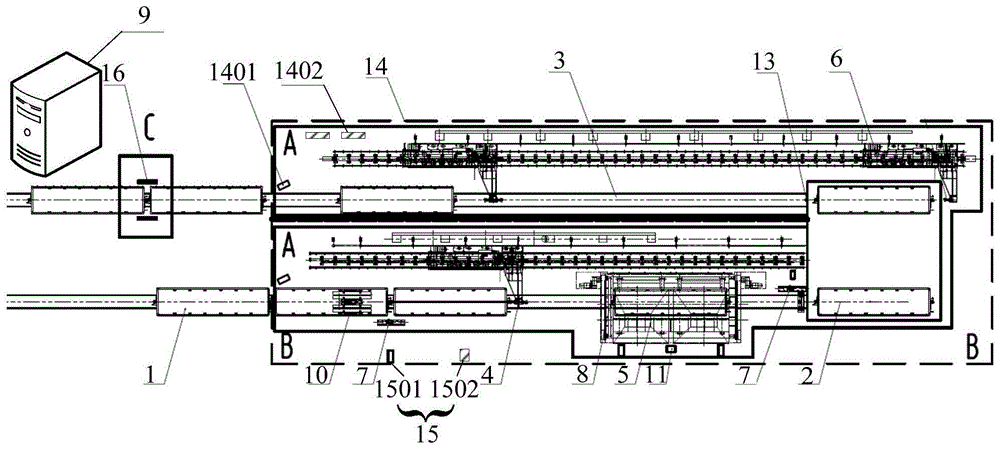
本发明涉及列车运输技术领域,尤其涉及一种列车自动翻车作业系统和方法。
背景技术:
在火力发电、港口运输、金属冶炼和煤炭焦化等生产运输领域,都需要使用列车敞车装卸物料;其中对于物料的翻卸,需要用到专门的翻车作业系统。
通常,翻车作业系统包括摘钩作业的翻车作业系统和不摘钩作业的翻车作业系统。摘钩作业的翻车作业系统的主要设备包括夹轮器、翻车机、重车调车机、迁车台和空车调车机等设备。
该摘钩作业的翻车作业系统,其具体工作流程如下:首先,重车调车机将整列火车牵引至人工摘钩工位,在该人工摘钩工位的夹轮器将火车车轮夹住;此时由人工进行摘钩作业,以将待翻卸的列车车厢与其他车厢分离;然后,重车调车机将待翻卸的列车车厢牵引至翻车机内部并定位;此时将重车调车机的车钩与列车车厢的车钩进行人工提销摘钩;当火车车厢摘钩完成后,翻车机固定住待翻卸的列车车厢并与该列车车厢一同翻转,完成列车车厢的翻卸;再然后,使用重车调车机将上一个循环翻卸完毕的空车厢推至迁车台,再由迁车台将空车厢平移至空车线;最后,由空车调车机将空车厢推出出翻车作业线外,使该空车厢与上一循环中推出的空车厢连接。
在上述翻车作业过程中,在使用翻车机卸料前,翻车作业系统需要人工对火车车厢进行摘钩;并且在翻车机翻转过程中,被翻转火车车厢的车钩由于重力的作用会摆向翻车方向,导致该火车车厢的车钩与翻车机车钩或其他火车车厢的车钩无法对接,需要人工对火车车钩进行正钩;另外,摘钩、正钩和主控室三者之间是通过对讲机呼唤应答方式进行作业的。
这样,从整个作业流程来看,人工工作量极大且工作环境恶劣;目前翻车作业是24小时不间断进行的,长时间的工作会导致作业人员注意力下降、精神疲劳,进而可能造成人身安全事故;这样既浪费了人力,还影响了翻卸作业的流畅性,导致作业效率低下。
技术实现要素:
本发明提供一种列车自动翻车作业系统和方法,旨在解决现有技术中人工摘钩、正钩和监控列车翻车,导致的人工工作量大,浪费人力,作业效率低下,甚至容易造成安全事故的问题。
为实现上述目的,根据本发明的第一方面,本发明提出了一种列车自动翻车作业系统,包括:
依次相连的重车线、迁车台和空车线;
沿重车线设置的重车调车机和翻车机;
以及,沿空车线设置的空车调车机;
列车自动翻车作业系统还包括移动式摘钩机器人、车钩防偏摆装置以及作业控制设备;
其中,作业控制设备分别与重车调车机、移动式摘钩机器人、翻车机、车钩防偏摆装置、迁车台和空车调车机电连接;
重车调车机,用于在作业控制设备的控制下,沿重车线移动列车车厢;
移动式摘钩机器人,用于在作业控制设备的控制下,对列车车厢进行摘钩操作;
翻车机,用于在作业控制设备的控制下,固定并翻卸已摘钩的列车车厢;
车钩防偏摆装置与翻车机相连,用于在翻车机翻卸列车车厢时,固定列车车厢的车钩;
迁车台,用于在作业控制设备的控制下,牵引已翻卸的列车车厢至空车线;
空车调车机,用于在作业控制设备的控制下,沿空车线将列车车厢移出翻车作业区。
优选地,所述列车自动翻车作业系统还包括智能夹轨控制装置,该智能夹轨控制装置包括:
固定于重车线、且与作业控制设备电连接的夹轨器;
平行设置于重车线的轨道外侧、且与作业控制设备电连接的多个检测开关,多个检测开关包括:
沿重车线的起始端至迁车台方向依次设置、且与作业控制设备分别电连接的减速位置检测开关、到位检测开关和计数检测开关;其中,
减速位置检测开关包括:
沿重车线的起始端至迁车台方向依次设置、且与作业控制设备分别电连接的起始减速位置检测开关、中间减速位置检测开关和结尾减速位置检测开关。
优选地,所述移动式摘钩机器人包括:
设置于重车线轨道外侧的机器人移动轨道;
连接于机器人移动轨道的轨道移动式底座;
电连接于轨道移动式底座的伺服驱动机构;
以及,与伺服驱动机构电连接的摘钩机械臂;
移动式摘钩机器人还包括:
固定于轨道移动式底座的机器人视觉模块;
与机器人视觉模块电连接的钩挡图像特征处理器;钩挡图像特征处理器还与摘钩机械臂电连接。
优选地,所述车钩防偏摆装置包括:固定于翻车机的轨道的车钩翻转机构;以及与车钩翻转机构相连的车钩顶升机构。
优选地,所述列车自动翻车作业系统还包括雷达测量装置,该雷达测量装置包括:
固定于翻车机的受料篦子边缘的自动横移机构;
与自动横移机构垂直相连的检测支架;
以及,固定于检测支架、且与作业控制设备电连接的雷达测量仪。
优选地,所述列车自动翻车作业系统还包括固定于翻车机的漏料斗的料位计;该料位计包括:
对称连接于漏料斗两侧的阻旋式料位检测仪,其中,阻旋式料位检测仪包括伸入至漏料斗内部的旋转叶片。
优选地,所述列车自动翻车作业系统,还包括固定于重车线与迁车台连接处、以及固定于空车线与迁车台连接处的迁车台到位检测装置;其中,该迁车台到位检测装置包括:
固定于重车线与迁车台连接处、以及固定于空车线与迁车台连接处的轨道对位检测开关,轨道对位检测开关还与作业控制设备电连接;
固定于迁车台一侧、且与轨道侧检测开关电连接的液压定位机构;
以及,固定于迁车台边沿、且与液压定位机构相连的空车到位检测开关,空车到位检测开关还通过作业控制设备与空车调车机电连接。
优选地,上述翻车作业区包括翻车运行区域和人员作业区域;该列车自动翻车作业系统还包括:
沿翻车运行区域边沿设置的虚拟电子围栏,其中,虚拟电子围栏包括运行监控设备和运行区域越界报警器;
沿人员作业区域边沿设置的人员识别装置,其中,人员识别装置包括人脸识别设备和作业区域越界报警器;
其中,虚拟电子围栏和人员识别装置分别与作业控制设备电连接。
根据本发明的第二方面,本发明还提供了一种列车自动翻车作业方法,列车自动翻车作业方法用于上述任一项技术方案所述的列车自动翻车作业系统,该列车自动翻车作业方法包括:
控制重车调车机沿重车线将列车移动至预定位置;
当检测到列车移动至预定位置时,控制移动式摘钩机器人移动至列车车厢处并对列车车厢进行摘钩操作;
当检测到列车车厢完成摘钩操作时,控制重车调车机将列车车厢移动至翻车机处;
控制翻车机固定并翻卸列车车厢;
当翻车机翻卸列车车厢时,控制车钩防偏摆装置固定列车车厢的车钩;
当检测到重车调车机将已翻卸的列车车厢移动至迁车台时,控制迁车台将列车车厢牵引至空车线;
当检测到列车车厢牵引至空车线时,控制空车调车机将空车线上的列车车厢移出翻车作业区。
优选地,上述列车自动翻车作业方法还包括:
获取减速位置检测开关发送的减速位置信息;
根据减速位置信息向重车调车机发送减速指令,减速指令用于控制重车调车机减速运行至夹轨器位置;
接收到位检测开关发送的列车到位信息;
根据列车到位信息向夹轨器发送夹轮控制指令,夹轮控制指令用于控制夹轨器夹紧列车车轮;
当检测到夹轨器夹紧列车车轮时,向移动式摘钩机器人发送移动摘钩指令,以控制移动式摘钩机器人对列车车厢摘钩;
当检测到列车车厢摘钩完毕时,向重车调车机发送车厢移动指令,车厢移动指令用于控制重车调车机将已摘钩的列车车厢移动至翻车机处。
本申请提出的列车自动翻车作业方案,通过设置移动式摘钩机器人,能够沿着重车线移动并且为需要摘钩的车厢进行自动摘钩,从而便于重车调车机、迁车台等设备与车厢的摘钩操作;设置车钩防偏摆装置,用于当翻车机翻卸列车时固定车钩,从而避免车钩因重力偏摆至翻车方向导致的车钩偏歪无法对接的问题;因此,通过移动式摘钩机器人和车钩防偏摆装置,不需要人工摘钩和扶正车钩,解放了人力;并且设置作业控制设备,分别与重车调车机、移动式摘钩机器人、翻车机、车钩防偏摆装置、迁车台和空车调车机电连接,能够实现列车自重车线驶入至列车车厢驶出空车线过程中,列车翻车的自动作业,从而解决了现有技术中需要专门操作人员检测列车车厢是否已摘钩,车钩是否摆正,以及需要专人控制列车翻车作业,导致的人工工作量大,浪费人力,影响作业效率且容易造成安全事故的问题。
附图说明
为了更清楚地说明本发明实施例或现有技术中的技术方案,下面将对实施例或现有技术描述中所需要使用的附图作简单地介绍,显而易见地,下面描述中的附图仅仅是本发明的一些实施例,对于本领域普通技术人员来讲,在不付出创造性劳动的前提下,还可以根据这些附图示出的结构获得其他的附图。
图1是本发明实施例提供的第一种列车自动翻车作业系统的结构示意图;
图2是图1所示实施例提供的一种智能夹轨控制装置的结构示意图;
图3是图1所示实施例提供的第一种移动式摘钩机器人的结构示意图;
图4是图1所示实施例提供的第二种移动式摘钩机器人的结构示意图;
图5是图1所示实施例提供的一种车距雷达测量装置的结构示意图;
图6是图1所示实施例提供的一种车钩防偏摆装置的结构示意图;
图7是图1所示实施例提供的一种雷达测量装置的俯视图;
图8是图7所示实施例提供的一种雷达测量装置的左视图;
图9是图1所示实施例提供的一种料位计的结构示意图;
图10是本发明实施例提供的一种迁车台的结构示意图;
图11是图10所示实施例提供的一种迁车台到位检测装置的结构示意图;
图12是本发明所示实施例提供的第一种列车自动翻车作业方法的流程示意图;
图13是本发明所示实施例提供的第二种列车自动翻车作业方法的流程示意图;
图14是本发明所示实施例提供的第三种列车自动翻车作业方法的流程示意图。
本发明目的的实现、功能特点及优点将结合实施例,参照附图做进一步说明。
具体实施方式
下面将结合本发明实施例中的附图,对本发明实施例中的技术方案进行清楚、完整地描述,显然,所描述的实施例仅仅是本发明的一部分实施例,而不是全部的实施例。基于本发明中的实施例,本领域普通技术人员在没有作出创造性劳动前提下所获得的所有其他实施例,都属于本发明保护的范围。
需要说明,本发明实施例中所有方向性指示(诸如上、下、左、右、前、后……)仅用于解释在某一特定姿态(如附图所示)下各部件之间的相对位置关系、运动情况等,如果该特定姿态发生改变时,则该方向性指示也相应地随之改变。
另外,在本发明中如涉及“第一”、“第二”等的描述仅用于描述目的,而不能理解为指示或暗示其相对重要性或者隐含指明所指示的技术特征的数量。由此,限定有“第一”、“第二”的特征可以明示或者隐含地包括至少一个该特征。在本发明的描述中,“多个”的含义是至少两个,例如两个,三个等,除非另有明确具体的限定。
在本发明中,除非另有明确的规定和限定,术语“连接”、“固定”等应做广义理解,例如,“固定”可以是固定连接,也可以是可拆卸连接,或成一体;“连接”可以是机械连接,也可以是电连接;可以是直接相连,也可以通过中间媒介间接相连,可以是两个元件内部的连通或两个元件的相互作用关系,除非另有明确的限定。对于本领域的普通技术人员而言,可以根据具体情况理解上述术语在本发明中的具体含义。
另外,本发明各个实施例之间的技术方案可以相互结合,但是必须是以本领域普通技术人员能够实现为基础,当技术方案的结合出现相互矛盾或无法实现时应当认为这种技术方案的结合不存在,也不在本发明要求的保护范围之内。
本发明实施例的主要技术问题如下:
现有翻车作业系统,通过人工对列车车厢进行摘钩、正钩、控制车厢翻转和移动,导致人工工作量大导致的作业人员注意力下降和精神疲劳,可能造成人身安全事故;既浪费了人力,还影响了翻卸作业的流畅性,导致作业效率低下的问题。
为了解决上述问题,参见图1,图1为本发明实施例提供的一种列车自动翻车作业系统的结构示意图。如图1所示,该列车自动翻车作业系统包括:
依次相连的重车线1、迁车台2和空车线3;载有物料的列车进入重车线1时,会通过重车线1进行翻卸等操作,翻卸后的列车车厢会通过迁车台2牵引至空车线3,并在空车线3上完成列车车厢的车钩连挂。
沿重车线1设置的重车调车机4和翻车机5;重车调车机4能够将载有物料的列车车厢沿重车线1运输至翻车机5进行翻卸,并将翻卸后的空车厢推送至迁车台2,通过迁车台2运输至空车线3。翻车机5用于翻卸列车车厢所运输的物料,当重车调车机4将列车车厢运输至该翻车机5时,翻车机5固定该列车车厢并翻卸物料,重车调车机4与原载有物料的列车车厢摘钩后,能够再次将翻车机5已经翻卸的空载列车车厢推送至迁车台2。
以及,沿空车线3设置的空车调车机6;空车调车机6沿空车线3设置,用于在迁车台2将空载列车车厢运输至空车线3时,沿空车线3移动空载的列车车厢,直至列车车厢移出翻车作业区。
列车自动翻车作业系统还包括移动式摘钩机器人7、车钩防偏摆装置8以及作业控制设备9;本申请实施例设置移动式摘钩机器人7,该移动式摘钩机器人7可沿重车线1移动,并对重车线1上的列车车厢进行摘钩;例如当重车调车机4将列车移动到预定位置,如夹轨器101的位置时,此时可以将移动式摘钩机器人7移动至该预定位置,并使用该摘钩机器人对每节列车车厢进行摘钩。车钩防偏摆装置8与翻车机5相连,用于在翻车机5翻卸物料时固定列车车厢的车钩,这样避免因车钩不正导致碰撞其他设备或者无法与其他设备对接的问题,进而无需人工扶正车钩,减少人工工作量。
其中,作业控制设备9分别与重车调车机4、移动式摘钩机器人7、翻车机5、车钩防偏摆装置8、迁车台2和空车调车机6电连接。作业控制设备9是整个列车自动翻车作业系统的控制中枢,用于根据列车车厢的运行位置和状态,自动控制重车调车机4、移动式摘钩机器人7、翻车机5、车钩防偏摆装置8、迁车台2和空车调车机6执行相关操作,从而实现整个列车自动翻车作业系统的自动化运行。
重车调车机4,用于在作业控制设备9的控制下,沿重车线1移动列车车厢;其中,重车调车机4可在重车线1初始端移动该列车,将列车移动至预定位置,例如夹轨器101位置,通过夹轨器101固定列车、且通过移动式摘钩机器人7摘钩后,再次牵引满载的列车车厢沿重车线1前行;当重车调车机4将列车车厢牵引至翻车机5处时,重车调车机4自动摘钩以使翻车机5固定该列车车厢;当翻车机5翻卸物料后,重车调车机4再将空载的列车车厢沿重车线1移动至迁车台2处,在迁车台2处摘钩,由迁车台2将列车车厢牵引至空车线3,此时重车调车机4沿重车线1原路返回,执行对其他列车车厢的操作。
移动式摘钩机器人7,用于在作业控制设备9的控制下,对列车车厢进行摘钩操作;移动式摘钩机器人7可沿重车线1分别设置于翻车机5的左右两侧,在翻车机5翻卸列车车厢之前,移动式摘钩机器人7首先在夹轨器101处完成对列车车厢的自动摘钩,将列车车厢与其他列车车厢分离;当翻车机5翻卸物料后,移动式摘钩机器人7还能够在重车调车机4将列车车厢移动至迁车台2处时,对重车调车机4和列车车厢进行摘钩。另外,移动式摘钩机器人7还能够设置于空车线3处,完成列车车厢的摘钩。
翻车机5,用于在作业控制设备9的控制下,固定并翻卸已摘钩的列车车厢;翻车机5具体用于固定和翻卸载有物料的列车车厢;当该列车车厢经过移动式摘钩机器人7摘钩后,会在重车调车机4的牵引下运行至该翻车机5处,然后翻车机5将该列车车厢进行定位,列车车厢的后钩头由翻车机5上的固定装置,即车钩防偏摆装置8顶住,同时重车调车机4后车钩自动摘钩并继续将翻车机5卸下的空车厢推送至迁车台2。其中,翻车机5包括翻车机5轨道、受料篦子501和漏料斗502等装置。
车钩防偏摆装置8与翻车机5相连,用于在翻车机5翻卸列车车厢时固定列车车厢的车钩。通常,翻车机5在翻卸列车车厢时,列车车厢的车钩是由操作人员进行扶正的,这样将导致人力的浪费。为了解决该问题,本申请设置与翻车机5相连的车钩防偏摆装置8,在翻车机5翻卸列车车厢时,该车钩防偏摆装置8固定列车车厢的车钩,从而避免车钩歪斜,碰撞翻车机5或其他设备。
迁车台2,用于在作业控制设备9的控制下,牵引已翻卸的列车车厢至空车线3。迁车台2连接于重车线1和空车线3之间,这样载有物料的列车车厢在重车线1上的翻车机5翻卸货物后,运输至该迁车台2,由迁车台2将该列车车厢横向牵引至空车线3,并通过空车线3移出翻车作业区。
空车调车机6,用于在作业控制设备9的控制下,沿空车线3将列车车厢移出翻车作业区。空车调车机6设置于空车线3上,当检测到迁车台2将空载的列车车厢推送至空车线3的预定位置时,空车调车机6将沿空车线3将列车车厢移出翻车作业区,期间该辆列车车厢将与其它列车车厢的车钩连挂,同时通过测量光幕16自动检测连挂状态,然后空车调车机6内置的自动摘钩装置对该列车车厢自动摘钩并返回进行下一次列车车厢的运输。
本申请提出的列车自动翻车作业系统,通过设置移动式摘钩机器人7,能够沿着重车线1移动并且为需要摘钩的车厢进行自动摘钩,从而便于重车调车机4、迁车台2等设备与车厢的摘钩操作;设置车钩防偏摆装置8,用于当翻车机5翻卸列车时固定车钩,从而避免车钩因重力偏摆至翻车方向导致的车钩偏歪无法对接的问题;因此,通过移动式摘钩机器人7和车钩防偏摆装置8,不需要人工摘钩和扶正车钩,解放了人力;并且设置作业控制设备9,分别与重车调车机4、移动式摘钩机器人7、翻车机5、车钩防偏摆装置8、迁车台2和空车调车机6电连接,能够实现列车自重车线1驶入,至列车车厢驶出空车线3过程中,列车翻车的自动作业,从而解决了现有技术中需要专门操作人员检测列车车厢是否已摘钩以及车钩是否摆正,以及需要专人控制列车翻车作业,导致的人工工作量大且浪费人力,影响作业效率且容易造成安全事故的问题。
另外,在图1所示实施例中,在空车线3上的空车连挂区域安装测量光幕16,通过自动检测两列车车厢之间的距离,判断两列车车厢的车钩是否正常连挂。当测量光幕16判定列车车厢的车钩连挂异常时,进行报警提醒并暂停作业,经过人工处理再恢复作业。
另外如图1所示,该翻车作业区包括翻车运行区域和人员作业区域;本申请实施例提供的列车自动翻车作业系统中,根据现场工作区域的安全等级不同,将翻车作业区划分为翻车运行区域a、人员作业区域b和翻车厂房外区域c。其中,翻车运行区域a包括移动式摘钩机器人7、重车调车机4、翻车机5、迁车台2、轻车调车机等设备的运行区域;在翻车线作业厂房内除了a区域以外的安全通道、操作间等区域为人员作业区域b。另外,在翻车作业厂房外,重车及轻车进出翻车厂房的区域为翻车厂房外区域c,该翻车厂房外区域c主要包括火车重车线1、空车线3、空车自动连挂检测区域和余料清理等区域;本申请实施例中,对于该翻车厂房外区域c能够记录和回放工作人员的活动轨迹。
为了对翻车作业过程中工作人员进行安全保护,如图1所示,本申请实施例中,该列车自动翻车作业系统还包括:
沿翻车运行区域边沿设置的虚拟电子围栏14,其中,虚拟电子围栏14包括运行监控设备1401和运行区域越界报警器1402。
沿人员作业区域边沿设置的人员识别装置15,其中,人员识别装置15包括人脸识别设备1501和作业区域越界报警器1502。
其中,虚拟电子围栏14和人员识别装置15分别与作业控制设备9电连接。
具体如图1所示,翻车运行区域a是整个翻车线作业流程中危险度最高的区域,在翻车作业时禁止人员进入,通过虚拟电子围栏14实现异常告警及视频监视;例如若有闯入行为,则立即声光报警,提示闯入人员立即离开,同时停止翻车作业。人员作业区域b只允许翻车线作业人员及检修人员通过,对进入人员作业区域b的人员会自动分辨、显示性质(例如识别外来人员、内部人员),对外来人员进行语音警告“翻车作业区域禁止入内,请尽快离开”;对内部人员进入区域进行语音提醒“进入翻车作业区域,请在安全导向区域行走及作业,注意安全”。
本申请实施例提供的技术方案中,在整个翻车机5作业现场,沿着翻车运行区域安装虚拟电子围栏14,能够通过运行监控设备1401自动识别进入人员是内部人员还是外部人员,并通过运行区域越界报警器1402进行报警提醒,在重点区域如摘钩区域、翻车机区域、空车线出口等位置安装视频监控系统,在工作时重点区域属于禁入区域,为现场安全作业提供保障。在人员作业区域中,设置人员识别装置15,包括人脸识别装置和作业区域越界报警器1502,对非作业人员进行越界报警。
另外,如图1所示,该列车自动翻车作业系统还包括智能夹轨控制装置10,该智能夹轨控制装置10的具体结构参见图2,如图2所示,该智能夹轨控制装置10包括:
固定于重车线1、且与作业控制设备9电连接的夹轨器101;夹轨器101用于夹持列车的车轮,从而固定列车。具体地,当重车调车机4将列车运行至该夹轨器101位置时,夹轨器101固定该趟列车的车轮,然后方便移动式摘钩机器人7对列车车厢进行摘钩,进而方便重车调车机4运输该列车车厢。
平行设置于重车线1的轨道外侧、且与作业控制设备9电连接的多个检测开关102,检测开关的检测方式可以为红外检测等非接触式检测方式,也能够为接触式检测方式。其中,如图2所示,该多个检测开关102包括:
沿重车线1的起始端至迁车台2方向依次设置、且与作业控制设备9分别电连接的减速位置检测开关1021、到位检测开关1022和计数检测开关1023;减速位置检测开关1021用于根据列车的车厢数量触发列车的减速信号,即根据列车的车厢数量控制列车在该减速位置检测开关1021处减速;到位检测开关1022通常设置于夹轨器101周边,然后当重车调车机4将列车推送至该到位检测开关1022处时,上述作业控制设备9控制重车调车机4停止移动列车,从而将列车停止在该到位检测开关1022处,然后通过上述移动式摘钩机器人7对列车车厢进行摘钩;计数检测开关1023能够统计已摘钩的列车车厢数量,从而作业控制设备9根据已摘钩的列车的车厢数量控制重车调车机4移动列车位置。
本申请实施例中,减速位置检测开关1021用于根据列车的车厢数量向作业控制设备9发送位置信号,因为列车具有惯性;载重越大,车厢数量越多的列车,其惯性越大,因此本申请实施例中设置多个减速位置开关,以根据列车的车厢数量控制列车开始减速的位置,本申请实施例中,减速位置检测开关1021包括:沿重车线1的起始端至迁车台2方向依次设置、且与作业控制设备9分别电连接的起始减速位置检测开关10211、中间减速位置检测开关10212和结尾减速位置检测开关10213。
通过沿着重车线1的起始端至迁车台2方向依次设置多个减速位置开关,这样列车可以在不同的减速位置开关处开始减速。具体地,当重车调车机4移动列车时,检测列车车厢数量,然后根据列车车厢数量选择不同的减速位置检测开关1021进行触发减速;例如,当检测到列车车厢数较多,此时选择起始减速位置检测开关10211,当重车调车机4牵引列车经过该起始减速位置检测开关10211时,起始减速位置检测开关10211触发减速位置信号,然后作业控制设备9向重车调车机4发送减速控制信号,重车调车机4开始减速,直至停止在夹轨器101处。当检测到列车车厢数量适中时,此时选择中间减速位置检测开关10212触发减速,当重车调车机4牵引列车经过该中间减速位置检测开关10212时,中间减速位置检测开关10212向作业控制设备9触发减速位置信号,然后作业控制设备9向重车调车机4发送减速控制信号,重车调车机4开始减速直至停止在夹轨器101处。当检测到列车车厢数量较少时,此时选择结尾减速位置检测开关10213触发减速,当重车调车机4牵引列车经过该结尾减速位置检测开关10213时,结尾减速位置检测开关10213向作业控制设备9触发减速位置信号,然后作业控制设备9向重车调车机4发送减速控制信号,重车调车机4开始减速直至停止在夹轨器101处。
其中,本申请实施例设置的减速位置检测开关1021不仅能够根据列车的车厢数量进行减速,也能够根据后续流程中翻车机5处翻卸列车车厢的阶段进行减速位置的选择和减速信号的触发。
另外,传统翻车作业方案中,都是通过人工对列车车厢进行摘钩的,这样存在人工操作量大,工作环境恶劣的问题,并且翻车作业是24小时不间断进行的,工作人员长时间工作会导致作业人员注意力下降,精神疲劳等问题,甚至可能导致事故,造成作业效率低下。
为了解决上述问题,图1所示实施例提供的列车自动翻车作业系统中设置移动式摘钩机器人7对列车车厢自动摘钩,该移动式摘钩机器人7如图3和图4所示,包括:设置于重车线1轨道外侧的机器人移动轨道701。重车线1轨道包括两根,机器人移动轨道701设置于重车线1轨道外侧,这样移动式摘钩机器人就能够沿着该机器人移动轨道701对重车线1轨道上的列车车厢进行摘钩。
连接于机器人移动轨道701的轨道移动式底座702。轨道移动式底座702连接于机器人移动轨道701,这样通过轨道移动式底座702沿着机器人移动轨道701的前后运行和转动,就能够控制该移动式摘钩机器人的摘钩范围。
电连接于轨道移动式底座702的伺服驱动机构703;以及与伺服驱动机构703电连接的摘钩机械臂704。伺服驱动电机用于驱动摘钩机械臂704运动,这样在伺服驱动电机的驱动下,摘钩机械臂704就能够对列车车厢进行自动摘钩。其中,该摘钩机械臂704能够设置为图3所示的多关节装置式或图4所示的工业机器人式。
另外,本申请实施例提供的移动式摘钩机器人7还包括:固定于轨道移动式底座702的机器人视觉模块705。
与机器人视觉模块705电连接的钩挡图像特征处理器706;钩挡图像特征处理器706还与摘钩机械臂704电连接。
本申请实施例提供的移动式摘钩机器人7,通过设置机器人视觉模块705,能够基于机器视觉原理识别列车车厢的钩挡,拍摄该列车车厢的钩挡图像,然后,钩挡图像特征处理器706对该钩挡图像进行处理,提取钩杆纹理特征;根据像素分布、钩挡宽度和颜色等信息,将图像信息转换为数字信号。钩挡图像特征处理器706对这些信号进行各种运算,然后抽取提钩杆的特征,进而通过该特征确定提钩杆的坐标,进而通过该坐标信息,移动式摘钩机器人7通过与钩挡图像特征处理器706连接的摘钩机械臂704完成自动摘钩作业。
其中,为了检测移动式摘钩机器人是否完成摘钩,如图5所示,本申请实施例中设置专门的车距雷达测量装置17,在移动式摘钩机器人7摘钩时检测前后车厢之间间距的变化,从而判断对列车车厢的车钩18是否完成摘钩操作。
另外,翻车机5在对列车车厢进行翻卸的过程中,列车车厢的车钩由于重力作用会摆向翻车方向,进而导致该车钩容易碰撞到翻车机5,并且与重车调车机4车钩或者与其他火车车厢的车钩难以对接。现有技术中通常是通过人工扶正列车车厢的车钩,避免该车钩偏摆。然而这种人工扶钩的方式会导致人工工作量大,作业危险等问题。
为解决上述问题,如图6所示,该车钩防偏摆装置8包括:固定于翻车机5的轨道的车钩翻转机构801;以及与车钩翻转机构801相连的车钩顶升机构802。
本申请实施例提供的技术方案中,在翻车机5的轨道中心平台上安装车钩防偏摆装置8,该车钩防偏置装置能够固定车钩18。车钩防偏摆装置8主要包括车钩翻转机构801和车钩顶升机构802,当载有物料的列车车厢在翻车机5内定位后,车钩翻转机构801升起,然后与该车钩翻转机构801相连的车钩顶升机构802再将车钩顶住。当车钩顶升机构802将车钩顶住后,翻车机5再对列车车厢进行翻卸作业,防止在翻转过程中车钩钩头偏向一侧碰撞翻车机5,或者车钩钩头偏歪影响后续空车之间的连挂。
另外,如图7所示,翻车机5在翻车作业过程中,翻车机5的受料篦子501用于刷选和导流物料,列车车厢翻卸的物料会经过该受料篦子501进入到漏料斗中。由于受料篦子501的形状和结构原因,受料篦子501容易出现漏料不畅或堆积严重等问题,甚至影响翻车或造成事故。
为了解决上述问题,如图7和图8所示,该列车自动翻车作业系统还包括雷达测量装置11,该雷达测量装置11包括:
固定于翻车机5的受料篦子501边缘的自动横移机构1101。自动横移机构1101固定于翻车机5的受料篦子501边沿,具体可设置于受料篦子501外侧的防护栏上,这样就能够在该自动横移机构1101上安装雷达测量仪1103,对受料篦子501上的物料体积进行检测。
与自动横移机构1101垂直相连的检测支架1102;检测支架1102用于承载雷达测量仪1103,并且将雷达测量仪1103与受料篦子501隔开预定距离,此时通过检测支架1102沿着自动横移机构1101滑动运行,就能够改变雷达测量仪1103的位置和距离,从而更精准地测量受料篦子501上的物料体积。
以及,固定于检测支架1102、且与作业控制设备9电连接的雷达测量仪1103。雷达测量仪1103用于检测受料篦子501的物料体积,通过检测支架1102沿着自动横移机构1101横向移动,这样雷达测量仪1103能够自动扫描受料篦子501上的实时料位高度,当受料篦子501上物料堆积时,雷达测量仪1103能够向作业控制设备9发送报警信号,这样系统就能够通过清篦机等装置对受料篦子501进行清理,进而避免出现受料篦子501漏料不畅或堆积严重,影响翻车或造成事故的问题。
另外,如图9所示,在图1中翻车机5的漏料斗502上,图1所示实施例提供的列车自动翻车作业系统还设置有料位计12;该料位计12包括:对称连接于漏料斗502两侧的阻旋式料位检测仪1201;其中,
阻旋式料位检测仪1201包括伸入至漏料斗502内部的旋转叶片1202。
本申请实施例提供的技术方案中,通过对称在漏料斗502两侧连接阻旋式料位检测仪1201,然后通过该阻旋式料位检测仪1201内部的旋转叶片1202能够检测漏料斗502中的料位高度,当漏料斗502漏料不畅或堵塞时,漏料斗502内的料位会升高导致料位计12阻断,旋转叶片1202不再旋转,此时系统会进行报警并停止作业,需要人工干预后恢复正常工作。
另外,在列车自动翻车作业过程中,翻车机5翻卸列车车厢后,重车调车机4会将空载的列车车厢移动至迁车台2处,通过迁车台2横向牵车,将列车车厢从重车线1移动至空车线3处。
为了保证列车在迁车台2的顺畅运行,如图10所示,该列车自动翻车作业系统还包括固定于重车线1与迁车台2连接处、以及固定于空车线3与迁车台2连接处的迁车台到位检测装置13。固定于重车线1与迁车台2连接处的迁车台到位检测装置13用于检测翻车机5从重车线1上调运的列车车厢是否在迁车台2处到位;固定于空车线3与迁车台2连接处的迁车台到位检测装置13,用于检测迁车台2是否牵引列车车厢至空车线3。
其中,如图11所示,该迁车台到位检测装置13包括:
固定于重车线1与迁车台2连接处、以及固定于空车线3与迁车台2连接处的轨道对位检测开关1301,该轨道对位检测开关1301还与作业控制设备9电连接。
轨道对位检测开关1301固定于重车线1与迁车台2连接处,或者固定于空车线3与迁车台2连接处。因为迁车台2也是具有轨道的,因此在牵车之前需要通过轨道对位检测开关1301检测迁车台2与重车线1或者迁车台2与空车线3之间的轨道是否对位。当轨道对位检测开关1301判断迁车台2轨道与重车线1或空车线3轨道不对位时,轨道对位检测开关1301向作业控制设备9发送报警信号,以使监控端及时调节该轨道。
固定于迁车台2一侧的液压定位机构1302。可以先在迁车台2一侧安装检测板,然后在该检测板上安装液压定位机构1302。以及,固定于迁车台2边沿、且与液压定位机构1302相连的空车到位检测开关1303,空车到位检测开关1303还通过作业控制设备9与空车调车机6电连接。
具体如图11所示,迁车台2是横向移动列车车厢的,这样当迁车台2牵引列车车厢至轻车线时,横向移动的迁车台2到位后,到位检测开关1303将信号反馈给作业控制设备9,同时作业控制设备9控制液压定位机构1302动作,液压定位销会被推出,完成迁车台的定位从而发送信号至空车到位检测开关1303。空车到位检测开关1303固定于迁车台2边沿,且与液压定位机构1302相连,当液压定位机构1302的液压定位销推出时,空车到位检测开关1303将发送信号至作业控制设备9,通过作业控制设备9调用空车调车机6将列车车厢移动至空车线3上。
另外,基于上述系统实施例的同一构思,本发明实施例还提供了列车自动翻车作业方法,用于解决现有技术中,翻车作业需要人工摘钩和人工正钩,和监测翻车作业导致的效率低下且安全性差等问题。
具体参见图12,图12为本申请实施例提供的一种列车自动翻车作业方法的流程示意图。,该列车自动翻车作业方法用于上述任一项实施例所述的列车自动翻车作业系统,如图12所示,该列车自动翻车作业方法包括以下步骤:
s110:控制重车调车机沿重车线将列车移动至预定位置;列车首先在重车调车机的牵引下移动至重车线待翻车区域轨道上,此时控制重车调车机将列车移动至预定位置,方便对列车载有物料的列车车厢进行摘钩操作。具体地,可将列车移动至夹轨器所在位置。
s120:当检测到列车移动至预定位置时,控制移动式摘钩机器人移动至列车车厢处并对列车车厢进行摘钩操作。移动式摘钩机器人移动至列车车厢处并在该位置对列车车厢自动摘钩,能够避免人工摘钩导致的工作量大效率低下的问题。其中,本申请实施例中通过设置多个检测开关,控制和检测列车移动至上述预定位置。
s130:当检测到列车车厢完成摘钩操作时,控制重车调车机将列车车厢移动至翻车机处。重车调车机将已经摘钩的列车车厢移动至翻车机处,从而能够通过翻车机对该列车车厢进行翻卸。其中,本申请实施例中设置专门的车距雷达测量装置,在移动式摘钩机器人摘钩时检测前后车厢之间间距的变化,从而判断列车车厢是否完成摘钩操作。
s140:控制翻车机固定并翻卸列车车厢。载有物料的列车车厢经过翻车机翻卸后,将变为空载的列车车厢,然后翻车机将该空载的列车车厢运输至迁车台牵引至空车线。
s150:当翻车机翻卸列车车厢时,控制车钩防偏摆装置固定列车车厢的车钩;在翻车机翻卸列车车厢的过程中,车钩容易出现偏摆,进而碰撞翻车机或者在翻卸后无法与重车调车机或其它列车车厢对接。本申请实施例中设置车钩防偏摆装置固定列车车厢的车钩,从而在翻车机翻卸列车车厢时,固定和摆正车钩,避免车钩偏摆,解决了现有技术中需要人工正钩导致的工作效率低下且容易导致安全事故的问题。
当翻车机翻卸物料后,已翻卸的列车车厢变为空载,然后重车调车机将该空载的列车车厢移动至迁车台,通过迁车台将列车车厢牵引至空车线。
s160:当检测到重车调车机将已翻卸的列车车厢移动至迁车台时,控制迁车台将列车车厢牵引至空车线。重车调车机能够将已翻卸的列车车厢移动至迁车台,通过迁车台将列车车厢运输至空车线上。本申请实施例中,通过在迁车台设置专门的迁车台到位检测装置,具体为空车到位检测开关检测重车调车机是否已将翻卸的列车车厢移动至迁车台。
s170:当检测到列车车厢牵引至空车线时,控制空车调车机将空车线上的列车车厢移出翻车作业区。本申请实施例中通过在空车线与迁车台轨道之间设置空车到位检测开关检测迁车台是否将列车车厢牵引至空车线上。并且,本申请实施例中,空车调车机需要将列车车厢与其它空载的列车车厢连挂,然后空车调车机需要与列车车厢摘钩,本申请实施例中空车调车机通过自身的摘钩装置与列车车厢摘钩,或者通过设置在空车线上的摘钩机器人进行摘钩作业,另外,空车线上的摘钩机器人还同时完成自动打开钩舌的作业。
本申请提出的列车自动翻车作业方法,通过设置移动式摘钩机器人,能够沿着重车线移动并且为需要摘钩的车厢进行自动摘钩,从而便于重车调车机、迁车台等设备与车厢的摘钩操作;设置车钩防偏摆装置,用于当翻车机翻卸列车时固定车钩,从而避免车钩因重力偏摆至翻车方向导致的车钩偏歪无法对接的问题;因此,通过移动式摘钩机器人和车钩防偏摆装置,不需要人工摘钩和扶正车钩,解放了人力;并且设置作业控制设备,分别与重车调车机、移动式摘钩机器人、翻车机、车钩防偏摆装置、迁车台和空车调车机电连接,能够实现列车自重车线驶入至列车车厢驶出空车线过程中,列车翻车的自动作业,从而解决了现有技术中需要专门操作人员检测列车车厢是否已摘钩,车钩是否摆正,以及需要专人控制列车翻车作业,导致的人工工作量大,浪费人力,影响作业效率且容易造成安全事故的问题。
另外,在使用移动式摘钩机器人对列车摘钩前,需要控制列车减速并移动至预定位置,然后在该预定位置进行列车车厢的摘钩。具体如图13所示,该列车自动翻车作业方法还包括以下步骤:
s210:获取减速位置检测开关发送的减速位置信息。
s220:根据减速位置信息向重车调车机发送减速指令,减速指令用于控制重车调车机减速运行至夹轨器位置。
s230:接收到位检测开关发送的列车到位信息。
s240:根据列车到位信息向夹轨器发送夹轮控制指令,夹轮控制指令用于控制夹轨器夹紧列车车轮。
s250:当检测到夹轨器夹紧列车车轮时,向移动式摘钩机器人发送移动摘钩指令,以控制移动式摘钩机器人对列车车厢摘钩。
s260:当检测到列车车厢摘钩完毕时,向重车调车机发送车厢移动指令,车厢移动指令用于控制重车调车机将已摘钩的列车车厢移动至翻车机处。
结合图2所示的结构,本申请实施例提供的技术方案中,首先作业控制设备根据列车的车厢数选择需要减速的减速位置检测开关,如起始减速位置检测开关、中间减速位置检测开关或结尾减速位置检测开关,然后当重车调车机移动列车碰触相应的减速位置检测开关时,该减速位置检测开关向作业控制设备发送减速位置信息;然后作业控制设备根据减速位置信息向重车调车机发送减速指令,控制重车调车机减速运行至夹轨器位置。在夹轨器位置处设置到位检测开关,当列车触发到该到位检测开关时,到位检测开关会发送列车到位信息;根据该列车到位信息,作业控制设备能够控制重车调车机停止移动列车,即将列车停靠在夹轨器附近,然后作业控制设备根据列车到位信息向夹轨器发送夹轮控制指令,控制夹轨器夹紧列车车轮。夹轨器夹紧列车车轮时,作业控制设备会向移动式摘钩机器人发送移动摘钩指令,从而控制移动式摘钩机器人对列车车厢进行摘钩。最后,再控制重车调车机移动已摘钩的列车车厢至翻车机处。从而完成摘钩过程的自动化控制。
另外,参见图14,图14是本申请实施例提供的第三种列车自动翻车作业方法的流程示意图。如图14所示,该列车自动翻车作业方法在翻车线作业开始后,包括以下步骤:
s301:重车调车机运行牵引重车,该重车即载有物料的列车。
s302:重车调车机提前减速,平稳停止。
s303:重车调车机进行位置检测,判断是否停在预定位置;若是,则执行步骤s305。
s304:对列车进行车型判断,该车型判断主要判断该列车所搭载的列车车厢数量;在判定该车型的类型符合预设类型后,执行步骤s306。
s305:夹轮器动作夹紧车轮,该夹轮器即上述提到的夹轨器的一种。
s306:移动式摘钩机器人移动到位。
s307:使用移动式摘钩机器人进行图像识别,判断当前图像是否为需要摘卸的车钩;若是,则执行步骤s309;若否,则执行步骤s308
s308:判定车钩异常,进行报警,并暂停作业进行人工处理。
s309:开始摘钩,若摘钩过程出现异常,则执行步骤s310。
s310:判定摘钩异常,报警并暂停作业,进行人工处理。
s311:判定摘钩完成,发送已摘钩信号至作业控制设备。
s312:重车调车机牵重车至翻车机。
s313:重车在翻车机定位夹紧,车钩顶紧。
s314:对受料篦子堆积监控,判断受料篦子是否无堆积;若是,则执行步骤s318;若否,则执行步骤s317。
s315:落料斗料位检测,判断落料斗料位是否正常;若是,则执行步骤s318;若否,则执行步骤s316。
s316:判定料位异常,报警,暂停作业并人工处理。
s317:堆积异常,报警,暂停作业并人工处理。
s318:翻车机运行翻转卸料。
s319:重车调车机将翻车机卸下的空车厢推出。
s320:重车调车机推送空车至迁车台定位。
s321:空车摘钩并打开钩舌;此时判断摘钩是否正常,若是,则执行步骤s322。
s322:判定摘钩异常,报警,暂停作业并人工处理。
s323:迁车台运行。
s324:迁车台运行至空车线并自动定位。
s325:空车调车机运行,将空车推出。该空车和上述空车厢相同,均为空载的列车车厢。
s326:将空车连挂。
s327:空车连挂检测,判断空车是否连挂正常;若是,则执行步骤s328;若否,则执行步骤s329。
s329:自动摘钩,空车调车机返回。
这样,整个翻车作业完成,等待下一循环即可。
尽管已描述了本发明的优选实施例,但本领域内的技术人员一旦得知了基本创造性概念,则可对这些实施例作出另外的变更和修改。所以,所附权利要求意欲解释为包括优选实施例以及落入本发明范围的所有变更和修改。
显然,本领域的技术人员可以对本发明进行各种改动和变型而不脱离本发明的精神和范围。这样,倘若本发明的这些修改和变型属于本发明权利要求及其等同技术的范围之内,则本发明也意图包含这些改动和变型在内。
起点商标作为专业知识产权交易平台,可以帮助大家解决很多问题,如果大家想要了解更多知产交易信息请点击 【在线咨询】或添加微信 【19522093243】与客服一对一沟通,为大家解决相关问题。
此文章来源于网络,如有侵权,请联系删除


