牵引梁构架、底架前端结构和轨道车辆的制作方法



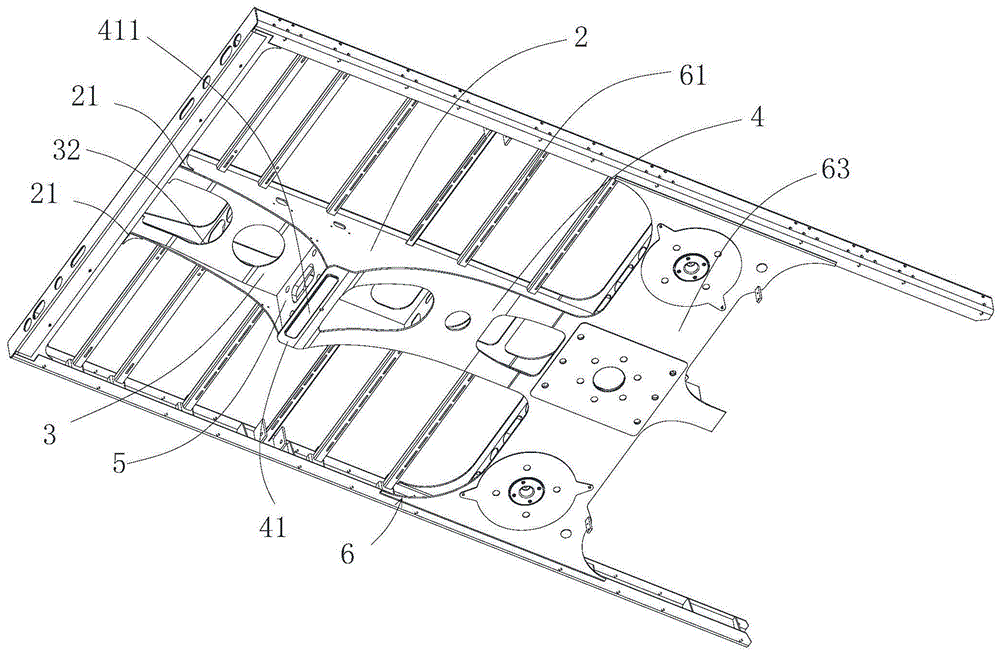
本发明属于轨道车辆牵引梁技术领域,更具体地说,是涉及一种牵引梁构架、设有该牵引梁构架的底架前端结构和设有该底架前端结构的轨道车辆。
背景技术:
目前,国内城轨车辆车体结构常采用轻量化设计。在不锈钢车体的设计上,尤其能体现出强度刚度高、耐腐蚀能力强、维护保养成本低等优点。车体轻量化研究中,一般分别对车体结构的各部件进行轻量化设计,如底架、侧墙、车顶、端墙等部件结构,上述设计方式虽然对车体重量减小有贡献,但是却很容易造成车体结构整体性差的问题。
针对地铁类车体,底架的前端部件一般由枕梁、牵引梁、边梁、端梁、支撑横梁及部分补强附件组成,其中牵引梁为车钩安装的连接部件,也是车体加载校验的重点。常用的牵引梁一般采用对称的外向槽型板材结构,并用铆钉铆接车钩安装座,另外还根据需要增加补强板。整个底架前端部件起到固定框架的作用,能够把车钩安装座受到的压缩及拉伸工况传递至整个车体结构。但是由于车钩安装座本身的体积和重量都比较大,且铆钉的布置需要进行多次调整和优化,所以底架牵引梁构架的轻量化改进难度较大。
技术实现要素:
本发明的目的在于提供一种牵引梁构架,以解决现有技术中存在的牵引梁构架受空间影响较大、难以进行轻量化设计的技术问题。
为实现上述目的,本发明采用的技术方案是:提供一种牵引梁构架,用于设置在底架上,包括上盖板、两个立板、中隔板、下盖板以及安装板,上盖板用于连接在底架上;两个立板的上边缘与上盖板的底面相连,两个立板沿车体的走向平行设置,且沿车体的宽度方向间隔排布;中隔板设置于两个立板之间且位于上盖板的下方,中隔板的一端用于与底架的端梁相连,另一端向上倾斜并与上盖板的底面相连;下盖板设置于两个立板之间且位于上盖板的下方,下盖板的一端用于与底架的枕梁相连,另一端延伸至中隔板的下方;安装板设置于下盖板的延伸端与中隔板的延伸端之间,安装板上还设有车钩安装孔;上盖板、中隔板和下盖板上分别设有减重孔。
作为本申请另一实施例,下盖板自枕梁至端梁向斜下方倾斜设置。
作为本申请另一实施例,下盖板的延伸端设有垂直于安装板的板面设置且与安装板的下端面相连的连接部。
作为本申请另一实施例,中隔板与安装板相连的一端设有向下弯折的凸起,凸起设有用于与安装板相连的平面,中隔板与上盖板相连的一端与上盖板之间设有锐角夹角。
作为本申请另一实施例,中隔板的一端设有上下贯通且开口朝向端梁设置的第一开口,另一端设有上下贯通且开口朝向上盖板设置的第二开口。
作为本申请另一实施例,上盖板与端梁相连的一端还设有第三开口。
作为本申请另一实施例,立板与端梁之间设有两个板面沿水平方向设置的辅助加强板,两个辅助加强板分别位于两个立板的外侧且与中隔板内外对应。
作为本申请另一实施例,上盖板的两侧边沿分别向外凸出于两个立板的外侧面,上盖板的底面用于与底架的横梁相连,立板的外侧面用于与横梁的内端相连。
本发明提供的牵引梁构架的有益效果在于:与现有技术相比,本发明提供的牵引梁构架,将用于与车钩相连的安装板固定在中隔板、下盖板以及两个立板形成的空间内,在保证与车钩连接强度的同时,省去了原有的安装座的设置,大大减少了空间占用,实现了轻量化设计,减小了材料的使用量;中隔板与安装板相连的部位的高度可以通过对中隔板的折弯造型进行对应调节,该结构不仅可以保证安装板以及安装孔的位置准确度,还可以减小安装板的整体高度,起到节约材料的作用。
本发明还提供了底架前端结构,底架前端结构设有牵引梁构架。
本发明还提供了轨道车辆,轨道车辆设有底架前端结构。
本发明提供的底架前端结构以及轨道车辆的有益效果在于:与现有技术相比,本发明提供的底架前端结构和轨道车辆,将用于与车钩相连的安装板固定在中隔板、下盖板以及两个立板形成的空间内,保证与车钩连接强度的同时,大大减少了空间占用,实现了牵引梁和底架的轻量化设计,便于轨道车辆运行过程中的节能减排,具有良好的经济效益。
附图说明
为了更清楚地说明本发明实施例中的技术方案,下面将对实施例或现有技术描述中所需要使用的附图作简单地介绍,显而易见地,下面描述中的附图仅仅是本发明的一些实施例,对于本领域普通技术人员来讲,在不付出创造性劳动性的前提下,还可以根据这些附图获得其他的附图。
图1为本发明实施例提供的牵引梁构架一个状态的结构示意图;
图2为本发明实施例提供的牵引梁构架另一个状态的结构示意图;
图3为图2中中隔板的结构示意图;
图4为图2中下盖板的结构示意图;
图5为图1的主视剖视结构示意图;
图6为图5中第一板的结构示意图;
图7为图5中第二板的结构示意图;
图8为原有牵引梁和安装座的主视结构示意图。
其中,图中各附图标记:
1、上盖板;11、第三开口;12、减重孔;2、立板;21、辅助加强板;3、中隔板;31、凸起;32、第一开口;33、第二开口;34、板体;4、下盖板;41、连接部;411、防磨垫层;5、安装板;51、车钩安装孔;6、底架;61、横梁;62、端梁;63、枕梁;71、第一补强板;711、第一孔;712、第二孔;72、第二补强板;721、第三孔;8、安装座。
具体实施方式
为了使本发明所要解决的技术问题、技术方案及有益效果更加清楚明白,以下结合附图及实施例,对本发明进行进一步详细说明。应当理解,此处所描述的具体实施例仅仅用以解释本发明,并不用于限定本发明。
需要说明的是,当元件被称为“设置于”另一个元件,它可以直接在另一个元件上或者间接在该另一个元件上。需要理解的是,术语“长度”、“宽度”、“上”、“下”、“前”、“后”、“顶”、“底”“内”、“外”等指示的方位或位置关系为基于附图所示的方位或位置关系,仅是为了便于描述本发明和简化描述,而不是指示或暗示所指的装置或元件必须具有特定的方位、以特定的方位构造和操作,因此不能理解为对本发明的限制。此外,术语“第一”、“第二”仅用于描述目的,而不能理解为指示或暗示相对重要性或者隐含指明所指示的技术特征的数量。由此,限定有“第一”、“第二”的特征可以明示或者隐含地包括一个或者更若干个该特征。在本发明的描述中,“若干个”的含义是两个或两个以上,除非另有明确具体的限定。
请一并参阅图1至图8,现对本发明提供的牵引梁构架、底架前端结构和轨道车辆进行说明。牵引梁构架用于连接在底架6上,包括上盖板1、两个立板2、中隔板3、下盖板4以及安装板5,上盖板1用于连接在底架6上;两个立板2的上边缘与上盖板1的底面相连,两个立板2连沿车体的走向平行设置,且沿车体的宽度方向间隔排布;中隔板3设置于两个立板2之间且位于上盖板1的下方,中隔板3的一端用于与底架6的端梁62相连,另一端向上倾斜并与上盖板1的底面相连;下盖板4设置于两个立板2之间且位于上盖板1的下方,下盖板4的一端用于与底架6的枕梁63相连,另一端延伸至中隔板3的下方;安装板5设置于下盖板4的延伸端与中隔板3的延伸端之间,安装板5上还设有车钩安装孔51;上盖板1、中隔板3和下盖板4上分别设有减重孔12。
本实施例中,取消了现有的牵引梁结构中的安装座8,有效缩减了牵引梁构架的整体重量,利用上盖板1、立板2、中隔板3和下盖板4围合成用于放置安装板5的空间,各部件之间采用焊接连接。当安装板5受到车钩的拉力时,上盖板1、立板2、中隔板3和下盖板4形成的整体结构可以将力均匀的分散至上方的底架6上,均化了安装板5的受力,保证了牵引梁构架整体结构稳定性。
底架6为设置在车辆底部的现有构件,牵引梁沿车体的走向安装在底架6的中部。底架6的两端分别为垂直于车体的走向设置的端梁62和枕梁63,在端梁62和枕梁63之间还分布有多个横梁61,横梁61分别位于牵引梁构架的两侧,用于实现底架6与牵引梁构架之间的可靠连接。
本发明提供的一种牵引梁构架,与现有技术相比,本发明提供的牵引梁构架,将用于与车钩相连的安装板5固定在中隔板3、下盖板4以及两个立板2形成的空间内,在保证与车钩连接强度的同时,省去了原有的安装座8的设置,大大减少了空间占用,实现了轻量化设计,减小了材料的使用量;中隔板3与安装板5相连的部位的高度可以通过对中隔板3的折弯造型进行对应调节,该结构不仅可以保证安装板5以及安装孔的位置准确度,还可以减小安装板5的整体高度,起到节约材料的作用。
请参阅图8,原有的牵引梁是通过多个板状构件焊接完成,然后安装座8通过多个铆钉的铆接连接到牵引梁的下方,连接过程相对复杂,且连接精度要求较高,不利于进行快速安装。另外,为了保证与车钩的连接可靠性,安装座8设置为具有较大强度的整体构件,这就极大增加了车体的重量。另外,由于多个铆接节点的存在,所以牵引梁需要具有较大的厚度来保证其刚性,不利于实现轻量化设计。
本实施例中,为了保证安装板5与车钩之间的连接强度,安装板5的厚度大于立板2、中隔板3以及下盖板4的厚度。安装板5的厚度为25-40毫米,其他构件的厚度为8-12毫米,安装板5的厚度加大便于增加与车钩的连接强度,保证连接的可靠性。
本实施例中,下盖板4、安装板5和中隔板3上分别设有减重孔12。减重孔12的设置位置应避开与安装板5相连的位置,且减重孔12的形状根据实际空间大小进行设定,可以为圆孔也可以为长孔,均可以实现减轻结构重量的作用,便于实现车体的轻量化。
进一步的,根据车钩系统安装需求,在安装板5上进行车钩安装孔51以及减重孔12的开设,其中减重孔12难也同时作为检查孔来使用,根据实际检查部位所需进行选择和设定。
作为本发明实施例的一种具体实施方式,请参阅图2、图4和图5,下盖板4自枕梁63至端梁62向斜下方倾斜设置。本实施例中,下盖板4的一端与枕梁63相连,另一端逐渐向下倾斜延伸至中隔板3的中部下方,配合中隔板3以及立板2围合成用于容纳安装板5的空间,并通过上述构件实现与安装板5的各个边缘的固定连接。下盖板4向斜下方延伸的设置方式,不仅可以为底架6下方省出更多的空间,避免与转向架之间发生相对位置干涉,同时也便于其他部件的布设,保证留有较大的维修操作空间。
为了提高下盖板4与上盖板1以及立板2之间连接的可靠性,在下盖板4与上盖板1之间设置了板面沿上下方向设置的第一补强板71,第一补强板71的上边缘与上盖板1固接,下边缘与下盖板4固接,两侧边分别与立板2的内侧板面相连,第一补强板71的设置能够对上盖板1和下盖板4的相对位置进行限定,在下盖板4两侧与立板2连接的同时,还将下盖板4与上盖板1相连,以保证下盖板4的位置稳定性,实现对安装板5的有效承托。
进一步的,为了实现轻量化,第一补强板71上贯穿设置有第一孔711,第一孔711位于第一补强板71的中部,第一孔711靠近上盖板1的一侧设置,以便保证第一补强板71的下边缘与下盖板4之间的连接强度。第一孔711的两侧对称设有第二孔712,第二孔712的面积大于第一孔711的面积,第二孔712的设置不仅可以实现减重,还可以实现管线的贯穿布设。对第二孔712的边缘位置进行圆弧倒角,以避免第二孔712对管线造成刮伤。
作为本发明实施例的一种具体实施方式,请参阅图2、图4和图5,下盖板4的延伸端设有垂直于安装板5的板面设置且与安装板5的下端面相连的连接部41。本实施例中,安装板5的板面沿上下方向设置,连接部41的设置可以为安装板5的下边缘提供可靠的安装平面,具有可靠的承托效果。安装板5在后续受到车钩拉力时,能够将力分散至中隔板3、下盖板4以及立板2上,实现整个牵引梁构架的均匀受力,实现了均匀承受荷载的效果。
进一步的,为了避免下盖板4与其他外部构件之间发生摩擦影响下盖板4与安装板5的连接强度,在连接部41下方设置了防磨垫层411,该垫层可以采用普通的平钢板或者花纹钢板,能够对连接部41的底面进行保护,进而保证下盖板4的整体完整性,保证结构的使用性能。
进一步的,下盖板4根据实际需求进行凸起的弧度的设计,一方面可以配合安装板5的空间布置,同时能有效的增大下盖板4的下方空间,为转向架转向提供了可靠的保障。相比直接向下方倾斜的形式,设有向上凸起的弧度相当于对下盖板4进行起拱设置,在安装板5受到车钩的拉力时,具有起拱设置的下盖板4结合第一补强板71的综合作用,能够承受更大的拉伸力,避免各部件之间拉力过大造成的断裂,有效的提高了结构的整体强度,保证了牵引梁牵引动作的稳定性和可靠性。
作为本发明实施例的一种具体实施方式,请参阅图3和图5,中隔板3与安装板5相连的一端设有向下弯折的凸起31,凸起31设有用于与安装板5相连的平面,中隔板3与上盖板1相连的一端与上盖板1之间设有锐角夹角。
本实施例中,中隔板3用于与安装板5相连的部位向下弯折形成凸起31,一方面可以配合车钩的实际高度所需,尽量减小安装板5高度的作用,由于安装板5具有较大厚度,在不改变厚度的前提下,减小安装板5的高度便于实现车体的轻量化。另一方面,当安装板5受到车钩的牵引时,安装板5受到端梁62一侧的拉力,此时安装板5对中隔板3具有向上顶撑的作用,中隔板3与端梁62抵接的一端形成顶撑,同时与上盖板1之间具有锐角夹角,也能够实现可靠的顶撑作用,在中隔板3与上盖板1的底面相互固接的基础上进一步提高了上盖板1与中隔板3之间的连接可靠性。
中隔板3与上盖板1之间还设有第二补强板72,第二补强板72的板面垂直于车体的走向设置。第二补强板72将中隔板3与上盖板1进行连接,保证了中隔板3的折弯形状的稳定性,进而保证安装板5安装位置的准确性,以实现与车钩之间的精准连接。第二补强板72上设有第三孔721,第三孔721设有两个,两个第三孔721在第二补强板72上对称设置,能够减小第二补强板72的重量,保证轻量化设计所需,还能够为管线的穿设预留较大的空间。
作为本发明实施例的一种具体实施方式,请参阅图1至图3,中隔板3的一端设有上下贯通且开口朝向端梁62设置的第一开口32,另一端设有上下贯通且开口朝向上盖板1设置的第二开口33。
中隔板3设置在两侧立板2之间,且位于上盖板1的下方,中隔板3的端部与端梁62的内侧面焊接连接,且二者之间为抵接状态。中隔板3上的第一开口32一方面可以起到良好的减重作用,同时,还可以实现中隔板3与端梁62的内侧面的有效顶撑,当安装板5受到车钩位于端梁62一侧的拉力时,中隔板3具有向两侧伸张的趋势,第一开口32的设置可以时中隔板3与端梁62具有更可靠的顶撑效果。设置第一开口32后,中隔板3与端梁62之间形成类似筋板的效果,相比通过中隔板3的整个侧边与端梁62抵接,具有更好的顶撑稳定性,进而可以利用二者之间的抵接作用保证二者的连接强度,起到增大结构强度的作用。
进一步的,第一开口32的开口宽度小于第一开口32的内腔宽度,第一开口32的开口端设置了向内侧延伸的板体34,该板体34与中隔板3相连的位置具有弧形过渡,使第一开口32的外端向中心处收拢,一方面增大中隔板3与端梁62的连接面积,同时还可以提高抵接作用,保证中隔板3与端梁62之间可靠的顶撑效果。
第一开口32和第二开口33的设置在保证轻量化的同时,还为后续构件的焊接连接以及管线的布设提供了较大的操作空间,便于进行安装作业,可以有效的提高作业效率。第一开口32和第二开口33之间还设置了面积小于第一开口32和第二开口33设置的圆形的减重孔12,以便进一步减小中隔板3的整体重量,实现轻量化的效果。
作为本发明实施例的一种具体实施方式,请参阅图1,上盖板1与端梁62相连的一端还设有第三开口11,第三开口11的开口宽度小于第三开口11的内腔宽度。第三开口11的设置可以有效的减小上盖板1的自身重量,第三开口11与端梁62接触的部位向内侧收拢,便于提高上盖板1与端梁62之间的接触面积,提高二者连接的可靠性。进一步的,第三开口11自靠近枕梁63的一侧向靠近端梁62的一侧的开口宽度逐渐变大,使上盖板1位于第三开口11两侧的部分形成向外打开的支撑板的结构,便于增强上盖板1的整体强度。
作为本发明实施例的一种具体实施方式,请参阅图1至图3,立板2与端梁62之间设有两个板面沿水平方向设置的辅助加强板21,两个辅助加强板21分别位于两个立板2的外侧且与中隔板3内外对应。
本实施例中,辅助加强板21设置在立板2背离中隔板3的一侧,且与中隔板3的高度齐平,辅助加强板21和中隔板3分别于立板2的两侧面焊接连接。当安装板5受到车钩的拉力时,中隔板3很容易对立板2产生力的作用,辅助加强板21则通过与立板2之间的连接,能够有效的抵消中隔板3对立板2的影响,提高构件连接的整体稳定性。
作为本发明实施例的一种具体实施方式,上盖板1的两侧边沿分别向外凸出于两个立板2的外侧面,上盖板1的底面用于与底架6的横梁61相连,立板2的外侧面用于与横梁61的内端相连。
本实施例中,底架6上的横梁61位于上盖板1的下方两侧,横梁61的内端顶面能够形成对上盖板1的有效承托,保证上盖板1即使受力时,也能稳定的保持在该位置。另外,横梁61的内端还与立板2的外侧面相连,在立板2上边缘与上盖板1相连的同时,对立板2的外侧板面进行限位保证立板2稳定的处于竖直状态,保证结构的稳定可靠。
本发明还提供了一种底架前端结构,底架前端结构设有牵引梁构架。
在底架6上设置了具有上述结构的牵引梁构架,由于牵引梁构架的结构相比传统结构进行了极大的简化,有效的减小了牵引梁构架的整体重量,省去了安装座8连接时的繁琐工序,所以可以减小底架6的整体重量,提高牵引梁牵引过程中的结构稳定性。
本发明还提供了一种轨道车辆,轨道车辆设有底架前端结构。轨道车辆采用具有上述牵引梁构架的底架前端结构,在底架前端结构整体强度和结构稳定性的前提下,减小了底架前端结构的整体重量,对保证列车的稳定运行具有巨大的作用,有助于实现车辆的轻量化需求。
以上仅为本发明的较佳实施例而已,并不用以限制本发明,凡在本发明的精神和原则之内所作的任何修改、等同替换和改进等,均应包含在本发明的保护范围之内。
起点商标作为专业知识产权交易平台,可以帮助大家解决很多问题,如果大家想要了解更多知产交易信息请点击 【在线咨询】或添加微信 【19522093243】与客服一对一沟通,为大家解决相关问题。
此文章来源于网络,如有侵权,请联系删除


