轮轴径向装置及具有其的副构架径向转向架的制作方法



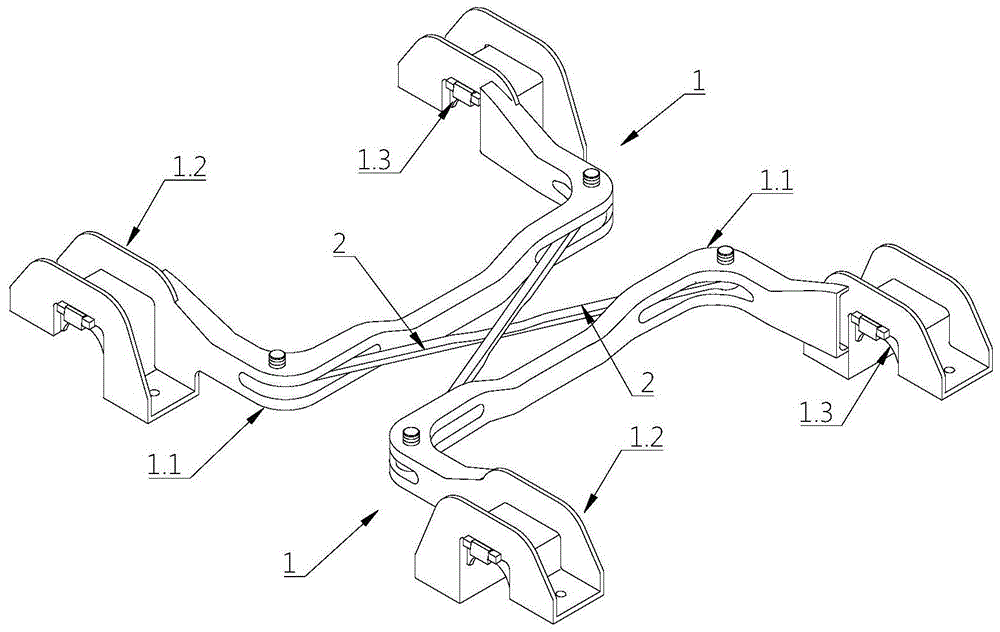
本实用新型涉及一种转向架,特别是指一种轮轴径向装置及具有其的副构架径向转向架。
背景技术:
铁路货车副构架径向转向架运行时,其轮轴(压装好轴承的轮对)径向装置对转向架的轮轴起运行导向定位作用。轮轴径向装置由两件呈u形的副构架和两件连接杆组成,其中的副构架通常为整体铸钢或整体焊接件,连接杆为两端带圆销孔的二力杆件。副构架的u形开口两端头设有与转向架轮轴端轴承外圈组装相匹配的承载鞍面结构,副构架的构架体两侧分别设置可供圆销组装的圆销孔。两件副构架沿轨道平行方向呈前后对称布置,连接杆两端通过圆销分别与前后两副构架体左右侧的圆销孔连接,两连接杆呈前后、左右交叉布置。副构架与交叉连接杆通过圆销连接后,形成一个完整的轮轴径向装置。
转向架落成组装后,该轮轴径向装置前后两副构架的四个端头导框鞍面分别落座于转向架前后两条轮对轴端的四件轴承外圈上,从而形成轮轴径向装置对转向架前后轮轴的组装定位。转向架直行时,由于连接杆的交叉连接作用,前后副构架沿轨道平行(以下简称纵向)和垂直方向(以下简称横向)的相对位移受到约束,增大了轮轴定位刚度,提高了轮轴的抗蛇形运行能力;转向架过曲线时,通过交叉连接杆可趋动前后两副构架在水平面内作相对转动,从而提高前后轮轴的曲线过轨能力。
以上所述为副构架自导向转向架的轮轴径向装置基本结构组成与工作原理。为实现轮轴径向装置与轮轴的落成组装,轮轴径向装置前后两副构架两端导框的轴承鞍面中心距尺寸必须与轮轴两端的轴承中心距尺寸匹配。现有的轮轴径向装置的承载鞍面结构与副构架体通过螺栓、铆接方式固定成一体,或直接铸造、焊接成一体,其后通过对整件副构架两端鞍面结构进行精密机加工成型。此种结构存在以下弊端:
1)转向架轮轴的轴承通过压装固定于车轴两端,受车轴的加工精度影响,轴承与轮对压装后,轮轴两端轴承中心距的实际尺寸变化范围较大,由于副构架两端的承载鞍及轴承鞍面与副构架的构架体固定成一整体,为保证副构架与轮轴两端的轴承对位组装,要求副构架、承载鞍有很高的制造加工和组装精度。
2)为提高副构架与轮轴的匹配组装合格率,须提高与副构架匹配组装的轮轴尺寸精度,由此,提高轮对及轮轴的制造经济成本。
此外,现有的轮轴径向装置在副构架中央横梁体靠近其横向对称中心两侧设置两个垂向通孔,用于安装连接杆圆销,连接杆两端及副构架的圆销孔通常分别压装有对副构架体和连接杆起防护作用的衬套,用一根圆销同时穿过副构架和连接杆衬套将连接杆与副构架连成一体。此种结构存在以下不足:1)由于连接杆支撑于副构架的中央横梁上,为防止转向架运行时在副构架横梁与纵向转臂的弯角处形成疲劳裂损,要求加大副构架纵向转臂以及纵向转臂与横梁弯角的结构强度,由此,将在很大程度上增加副构架的材料重量,在增加制造成本的同时,也因重量大给副构架组装落车带来不便。2)副构架与连接杆组装时,同一根圆销需同时穿过副构架和连接杆的衬套孔,为消除连接杆与副构架之间的连接间隙,圆销与副构架及连接杆的衬套孔通常为过盈量配合,组装时,连接杆和副构架圆销孔的对位要求高,给圆销组装带来不便。
技术实现要素:
本实用新型的目的在于提供一种能够降低制造及组装精度要求的轮轴径向装置及具有其的副构架径向转向架。
为实现上述目的,本实用新型所设计的轮轴径向装置,包括成对设置的两个副构架和连接在二者之间的两个连接杆;每个所述副构架包括一个构架体、两个导框和两个承载鞍;所述构架体呈u形,由一个中央横梁和两个纵向转臂构成;两个所述导框设置在构架体的两端,其上分别设置有开口向下的承载鞍安装槽;所述承载鞍呈鞍形,其上部设置有对接平台,下部设置有用于安装轮轴轴承的轴承安装槽;所述承载鞍安装于导框的承载鞍安装槽内,其对接平台与承载鞍安装槽的底面在垂向形成面与面的接触配合,同时对接平台与承载鞍安装槽之间还设置有卡槽式限位结构,使承载鞍在横向和纵向只能相对导框进行小距离的位移或转动。
根据限位凹槽具体位置,所述卡槽式限位结构可采用如下两种结构之一:
1)所述对接平台上设置有两块平行的限位侧板,两块所述限位侧板与对接平台的顶部平面形成限位凹槽;所述承载鞍安装槽的底部两侧卡在限位凹槽内,并与限位侧板构成间隙配合,从而形成第一方向上的限位;同时,所述承载鞍安装槽在每块限位侧板的两边分别设置有一个限位凸台,每块所述限位侧板卡在其两边的限位凸台之间,并与后者间隙配合,从而形成第二方向上的限位;所述第一方向为转向架横向或纵向,所述第二方向为转向架纵向或横向,二者相互垂直。
2)所述承载鞍安装槽的底面上设置有两块平行的限位侧板,两块所述限位侧板与承载鞍安装槽的底面形成限位凹槽;所述对接平台卡在限位凹槽内,且其两侧与限位侧板构成间隙配合,从而形成第一方向上的限位;同时,所述对接平台在每块限位侧板的两边分别设置有一个限位凸台,每块所述限位侧板卡在其两边的限位凸台之间,并与后者间隙配合,从而形成第二方向上的限位;所述第一方向为转向架的横向或纵向,所述第二方向为转向架的纵向或横向,且所述第一方向与第二方向相互垂直。
优选地,两个所述连接杆呈x形交叉布置,每个所述连接杆的两端分别通过联结圆销与构架体相连。
优选地,所述联结圆销安装于所述构架体的纵向转臂与中央横梁的过渡弯角处。相比将连接杆支撑于中央横梁中部的现有设计,将连接杆通过联结圆销设置在过渡弯角处具有以下两方面的优点:一方面改善了构架体弯角复杂截面的应力条件,便于构架体实现轻量化设计,以及因轻量化带来的机构组装便利化;另一方面,由于将联结圆销联结点由内向外转移,相应增加连接杆的杆体长度,由此也增加轮轴径向装置在整个水平面内的框架柔度,使组装轮轴径向装置的转向架及车辆具有更好的曲线线路通过适应性能。
优选地,所述联结圆销的外侧套设有一个弹性衬套,所述弹性衬套先套装在联结圆销上,再与后者作为整体压装于构架体及连接杆上的圆销安装孔内;安装完成后,所述弹性衬套在内圆面与联结圆销形成过盈配合,在外圆面同时与连接杆和构架体形成过盈配合。弹性衬套及联结圆销可采用压装方式安装,具体方法如下:压装前,弹性衬套的内孔直径大于联结圆销的外径,联结圆销可先行自由穿过弹性衬套孔,并在联结圆销端头安装轴端卡环以防止联结圆销与弹性衬套分离;其后,将弹性衬套连同联结圆销作为整体压装进构架体及连接杆的圆销安装孔,由于弹性衬套为弹性件,压装时连接杆的圆销安装孔与构架体的圆销安装孔的对位要求容易实现,压装后,弹性衬套内孔收缩,弹性衬套与联结圆销形成事实的过盈配合,使构架体与连接杆实现无间隙连接。弹性衬套的作用是保护构架体与连接杆的圆销安装孔无磨耗,对比现有的在构架体及连接杆的圆销安装孔分别独立设置弹性衬套的方式,该方案采用与联结圆销一同压装的整件式弹性衬套进行压装,对连接件构架体及连接杆的圆销安装孔对位要求相对较低,同时,弹性衬套与联结圆销同时装拆,降低了轮轴径向装置的组装与拆卸难度。
优选地,所述承载鞍与轴承安装槽的两侧面间隙配合。
优选地,所述导框与构架体为一体式铸造加工件。
本实用新型同时提供了一种具有前述轮轴径向装置的副构架径向转向架,除轮轴径向装置采用前述设计外,其余部分采用现有设计,本领域技术人员可以根据需要合理选择。
与现有技术相比,本实用新型的有益效果在于:该轮轴径向装置采用承载鞍与构架体的分体式结构,组装时,承载鞍可相对构架体导框作小距离的横向位移和微小角度的相对转动,通过调整承载鞍横向与周向位置,使同一副构架的两个轴承安装槽鞍面的中心距与其下方轮对的轮轴轴承中心距一致,并使两鞍面与轮轴保持同轴线,保证轮轴径向装置与轮轴实现落车组装,从而降低制造及组装精度要求、提高匹配组装合格率。本实用新型降低了副构架径向转向架制造技术难度,提高了副构架径向转向架的制造、使用经济性,尤其适用于运行线距弯道多、曲线半径小的铁道车辆及转向架组装。
附图说明
图1为本实用新型实所设计的轮轴径向装置的立体示意图。
图2、图3分别为图1中轮轴径向装置的主视、俯视结构示意图。
图4为图2中i处的放大图。
图5~7分别为图1中导框、承载鞍及二者的安装结构的立体示意图。图8~10为另一种结构的立体示意图。
其中:副构架1、构架体1.1、中央横梁1.11、纵向转臂1.12、导框1.2、承载鞍安装槽1.21、承载鞍1.3、对接平台1.31、轴承安装槽1.32、限位侧板1.4、限位凹槽1.5、限位凸台1.6、连接杆2、联结圆销2.1、弹性衬套2.2、轴端卡环2.3、轮轴轴承3
具体实施方式
下面结合附图和具体实施例对本实用新型作进一步的详细说明。
实施例1
如图1~10所示,本实施例所设计的轮轴径向装置,轮轴径向装置由两个副构架1和两根连接杆2组成。其中:
两个副构架1沿转向架的横向与纵向呈对称布置。每件副构架1均包括一个构架体1.1、两个导框1.2和两个承载鞍1.3。构架体1.1在水平面上呈u形,由位于中部的一个中央横梁1.11和位于两侧的两个纵向转臂1.12构成。两个导框1.2设置在构架体1.1的两端外侧,其上分别设置有开口向下的承载鞍安装槽1.21。中央横梁1.11、纵向转臂1.12与两个导框1.2铸造为一个整体。
承载鞍1.3呈鞍形,其上部设置有对接平台1.31,下部设置有轴承安装槽1.32,轴承安装槽1.32具有与轴承外圆结构尺寸匹配的鞍面。承载鞍1.3安装于导框1.2的承载鞍安装槽1.21内,其对接平台1.31与承载鞍安装槽1.21的底面在垂向形成面与面的接触配合,同时对接平台1.31与承载鞍安装槽1.21之间还设置有卡槽式限位结构。
如图5~7所示,卡槽式限位结构具体为:对接平台1.31的两侧设置有两块平行的限位侧板1.4,两块限位侧板1.4与对接平台1.31的顶部平面形成限位凹槽1.5;承载鞍安装槽1.21的底部两侧卡在限位凹槽1.5内,并与限位侧板1.4构成间隙配合,从而形成第一方向上的限位;同时,承载鞍安装槽1.21在每块限位侧板1.4的两边分别设置有一个限位凸台1.6,每块限位侧板1.4卡在其两边的限位凸台1.6之间,并与后者间隙配合,从而形成第二方向上的限位;第一方向为转向架横向或纵向,第二方向为转向架纵向或横向,二者相互垂直。卡槽式限位结构也可以采用如图8~10所示的结构(限位凸台和限位侧板的形状位置有所不同)。
上述卡槽式限位结构形成对承载鞍1.3横向和纵向(相对于轨道方向)的限位,同时在横向两侧各留有装配间隙n,纵向两侧各留有装配间隙m,使承载鞍1.3在横向和纵向能相对导框1.2进行小距离的位移或转动,进而使同一副构架1的两个轴承安装槽1.32鞍面的中心距与其下方轮对的轮轴轴承3中心距一致,并使两鞍面与轮轴保持同轴线,保证轮轴径向装置与轮轴实现落车组装。装配间隙n、m通常不超过0.4mm,具体取值应合理设置,即:在保证构架体1.1连同承载鞍1.3能与轮轴两端轴承对位落车的前提下,尽量减小承载鞍1.3相对于导框1.2的可移动和转动位移,以满足轮轴径向装置对转向架轮轴运行的精确导向定位。
两件连接杆2x形呈交叉布置,并且在空间上彼此独立无干涉。如图4所示,连接杆2的端部通过联结圆销2.1和弹性衬套2.2安装在构架体1.1的纵向转臂1.12和中央横梁1.11的过渡弯角处。弹性衬套2.2采用可采用工程塑料制造,从构架体1.1的上圆销安装孔插入,穿过连接杆2的圆销安装孔及构架体1.1的下圆销安装孔,将构架体1.1与连接杆2连成一体。弹性衬套2.2内安装有联结圆销2.1、联结圆销2.1下部轴端安装有轴端卡环2.3,使联结圆销2.1与弹性衬套2.2二者沿轴向连成一体,以防止联结圆销2.1轴向窜动。
联结圆销2.1、弹性衬套2.2及轴端卡环2.3的安装部骤为:1)首先将联结圆销2.1插装入弹性衬套2.2内,并在联结圆销2.1轴端安装轴端卡环2.3进行限位,此时,联结圆销2.1与弹性衬套2.2为小间隙配合,联结圆销2.1与弹性衬套2.2二者沿轴向无法相互窜动松脱;2)随后将弹性衬套2.2连同联结圆销2.1及轴端卡环2.3一起压装进构架体1.1及连接杆2的圆销安装孔内,完成构架体1.1与连接杆2的销连接组装。
组装完成后,弹性衬套2.2外圆柱面与构架体1.1及连接杆2的圆销安装孔为过盈配合,由于弹性衬套2.2为弹性材料,在连接杆2的圆销安装孔与构架体1.1的圆销安装孔的轴线重合度不高条件下,弹性衬套2.2压装仍可完成,由此降低了衬套及联结圆销2.1的组装工艺要求。同时,弹性衬套2.2内孔经压装收缩与联结圆销2.1由间隙配合变为有预紧力的过盈配合,构架体1.1与连接杆2之间形成事实上无间隙销轴连接,有效地缓解连接杆2与构架体1.1之间的连接冲击,提高了轮轴径向装置的使用寿命和工作性能。此外,通过对联结圆销2.1上方与下方施加压力或敲打,可实现联结圆销2.1与弹性衬套2.2同步组装、拆卸,极大方便于轮轴径向装置及构架体1.1径向转向架的维护拆装。
实施例2
本实施例提供了一种副构架径向转向架,其轮轴径向装置采用实施例1,其余部分采用现有设计,本领域技术人员可以根据需要合理选择。
起点商标作为专业知识产权交易平台,可以帮助大家解决很多问题,如果大家想要了解更多知产交易信息请点击 【在线咨询】或添加微信 【19522093243】与客服一对一沟通,为大家解决相关问题。
此文章来源于网络,如有侵权,请联系删除


