端部底架及轨道车辆的制作方法



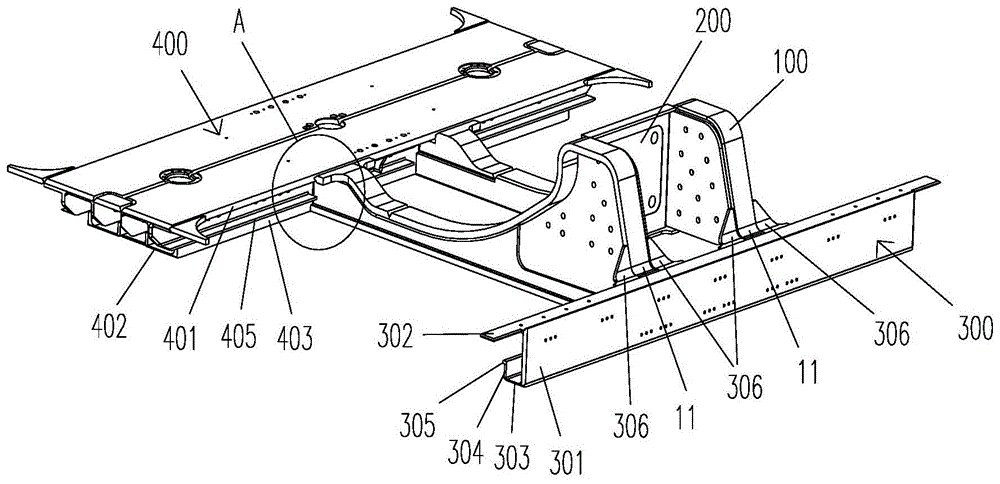
本发明涉及轨道车辆技术领域,尤其涉及一种端部底架及轨道车辆。
背景技术:
目前,在跨座式单轨列车的研发设计过程中,由于转向架的行走轮和导向轮空间限制区域比常规轨道车辆的空间限制区域超出较多,而且车辆维修方案对车体空间的限制要求,导致车体底架结构设计空间严重不足。现有常规轨道车辆的端部底架结构无法同时满足车钩安装的空间接口要求和转向架空间限制区域要求,而且也不能满足转向架不下车而直接换轮的车辆检修要求。
技术实现要素:
本发明旨在至少解决现有技术中存在的技术问题之一。
为此,本发明提出一种端部底架,减小了牵引梁所占用的结构空间,能够同时满足车钩安装的空间接口要求和转向架空间限制区域要求。
本发明还提出一种轨道车辆。
根据本发明第一方面实施例的端部底架,包括:
牵引梁,包括两个间隔相对设置的牵引梁腹板,各所述牵引梁腹板的上侧分别连接有上翻边,两个所述上翻边相背设置;各所述牵引梁腹板的下侧分别连接有下翻边,两个所述下翻边相背设置;各所述牵引梁腹板的外侧分别设有第一补强板,所述第一补强板连接在所述上翻边与所述下翻边之间,以使所述牵引梁腹板、所述上翻边、所述第一补强板和所述下翻边之间围合形成承载腔室;所述牵引梁腹板的第一端、所述上翻边的第一端、所述第一补强板的第一端以及所述下翻边的第一端之间形成缓冲梁接口;各所述上翻边的第二端分别连接有连接件,所述连接件分别与所述第一补强板的上侧、所述牵引梁腹板的上侧连接,所述牵引梁腹板的第二端、所述下翻边的第二端、所述第一补强板的第二端以及所述连接件之间形成枕梁接口;
车钩安装座,所述车钩安装座安装在两个所述牵引梁腹板之间;
缓冲梁,所述缓冲梁与所述缓冲梁接口相连;
枕梁,所述枕梁与所述枕梁接口相连。
根据本发明的一个实施例,所述连接件包括翻边连接部、腹板连接部和枕梁连接部,所述翻边连接部包括沿所述牵引梁腹板的延伸方向依次连接的第一连接板、第二连接板、第三连接板和第四连接板,所述第一连接板与所述上翻边的第二端相连;所述腹板连接部设置于所述翻边连接部沿长度方向延伸的一侧,所述腹板连接部的上侧与所述翻边连接部的下表面相连,所述腹板连接部的下侧与所述牵引梁腹板的上侧相连;所述枕梁连接部与所述第四连接板相连,所述腹板连接部的上侧与所述枕梁连接部的下表面相连;所述第一补强板的上侧分别与所述翻边连接部的下表面、所述枕梁连接部的下表面相连。
根据本发明的一个实施例,所述第一连接板为水平设置的平板,所述第二连接板、所述第三连接板和所述第四连接板分别为弧形板。
根据本发明的一个实施例,所述下翻边为水平设置的平板;所述上翻边包括第一水平板、第一弧形板、倾斜板、第二弧形板、第二水平板、第三弧形板、第四弧形板和第五弧形板,所述第一水平板、所述第一弧形板、所述倾斜板、所述第二弧形板、所述第二水平板、所述第三弧形板、所述第四弧形板和所述第五弧形板从左到右依次连接;所述第二水平板的设置位置分别高于所述第二弧形板和所述第三弧形板的设置位置,所述第二弧形板、所述倾斜板、所述第一弧形板和所述第一水平板从上至下依次设置,所述第三弧形板、所述第四弧形板和所述第五弧形板从上至下依次设置。
根据本发明的一个实施例,所述第一补强板包括从左到右依次连接的第一连接部、第二连接部和第三连接部,所述第一连接部的下侧与所述下翻边相连,所述第一连接部的上侧与所述上翻边间隔设置;所述第二连接部的下侧与所述下翻边相连,所述第二连接部的上侧与所述第五弧形板相连;所述第三连接部的下侧与所述下翻边相连,所述第三连接部的上侧与所述连接件相连。
根据本发明的一个实施例,在所述承载腔室的内部设有第二补强板,所述第二补强板连接在所述第五弧形板与所述下翻边之间,所述第二补强板与所述牵引梁腹板间隔设置,所述第二补强板与所述第一补强板间隔设置;所述第二补强板的长度小于所述第二连接部的长度。
根据本发明的一个实施例,所述枕梁包括上顶板、下底板和枕梁端板,所述上顶板与所述下底板从上至下平行设置,所述枕梁端板的上端与所述上顶板的下表面垂直连接,所述枕梁端板的下端与所述下底板朝向所述牵引梁的一端连接;所述牵引梁腹板的第二端、所述下翻边的第二端、所述第一补强板的第二端和所述腹板连接部的端部分别与所述枕梁端板的外侧面连接;所述枕梁连接部的端面与所述上顶板的端面对接。
根据本发明的一个实施例,各所述下翻边的下表面分别设有牵引梁插接板,所述枕梁端板的外侧面下端设有第一插接翻边,所述牵引梁插接板的第一端上表面与所述第一插接翻边的下表面连接。
根据本发明的一个实施例,所述缓冲梁包括缓冲梁端板、缓冲梁插接板、缓冲梁支撑板和缓冲梁连接板,所述缓冲梁插接板垂直连接在所述缓冲梁端板朝向所述牵引梁的一侧上端,所述缓冲梁支撑板垂直连接在所述缓冲梁端板朝向所述牵引梁的一侧下端,所述缓冲梁连接板垂直连接在所述缓冲梁支撑板远离所述缓冲梁端板的一侧上表面;所述牵引梁腹板的第一端与所述缓冲梁端板连接,所述上翻边的第一端的端面与所述缓冲梁插接板的端面对接,所述下翻边的第一端与所述缓冲梁支撑板连接;在所述缓冲梁连接板朝向所述牵引梁的一侧上端设有第二插接翻边,在所述第一补强板的第一端设有与所述第二插接翻边相适配的插接槽,所述第二插接翻边与所述插接槽相插接。
根据本发明的一个实施例,各所述上翻边第一端的左右两侧分别设有连接筋板,各所述连接筋板分别与所述缓冲梁插接板的端面对接。
根据本发明的一个实施例,所述车钩安装座包括第一安装板、第二安装板和第三安装板,所述第一安装板和所述第二安装板分别与两个所述牵引梁腹板对应连接,所述第三安装板垂直连接在所述第一安装板和所述第二安装板之间;所述第一安装板和所述第二安装板上分别设有多个第一安装孔,各所述牵引梁腹板上分别设有与所述第一安装孔相对应的第二安装孔;所述第三安装板的上端设有第一筋板,所述第一筋板的下表面分别与第一安装板、所述第二安装板相连;所述第三安装板的下端设有第二筋板,所述第二筋板的上表面分别与第一安装板、所述第二安装板相连;在所述第一筋板和所述第二筋板之间设有第三筋板,所述第三筋板设置于所述第三安装板上背向所述缓冲梁接口的一侧,所述第三筋板的两端分别与所述第一安装板、所述第二安装板对应连接;所述第三安装板上设有多个车钩安装孔。
根据本发明第二方面实施例的轨道车辆,包括上述实施例的端部底架。
本发明实施例中的上述一个或多个技术方案,至少具有如下技术效果之一:
本发明实施例的端部底架,通过在两个牵引梁腹板之间设置车钩安装座,用于满足车钩安装的空间接口要求,通过在牵引梁腹板的上侧设置上翻边,在牵引梁腹板的下侧设置下翻边,在牵引梁腹板的外侧设置第一补强板,使第一补强板连接在上翻边与下翻边之间,从而使牵引梁腹板、上翻边、第一补强板和下翻边之间围合形成承载腔室,进而提高了牵引梁的结构强度;通过在牵引梁腹板的第一端、上翻边的第一端、第一补强板的第一端以及下翻边的第一端之间形成缓冲梁接口,用于实现牵引梁与缓冲梁的连接;通过在上翻边的第二端设置连接件,使该连接件分别与第一补强板的上侧、牵引梁腹板的上侧连接,使牵引梁腹板的第二端、下翻边的第二端、第一补强板的第二端以及连接件之间形成枕梁接口,用于实现牵引梁与枕梁的连接。由此,本发明实施例的端部底架,牵引梁的结构更加紧凑,从而减小了牵引梁所占用的结构空间,能够同时满足跨座式单轨列车对车钩安装的空间接口要求和转向架空间限制区域要求,同时还满足了跨座式单轨列车中转向架不下车而直接换轮的车辆检修要求,节约了车辆检修成本。
本发明实施例的轨道车辆,包括上述实施例的端部底架。由于该轨道车辆设置有上述实施例的端部底架,使得该轨道车辆具有上述端部底架的全部优点,进而提高了该轨道车辆的使用性能。
本发明的附加方面和优点将在下面的描述中部分给出,部分将从下面的描述中变得明显,或通过本发明的实践了解到。
附图说明
图1是本发明实施例提供的端部底架的第一方向轴测图;
图2是图1中局部a的放大结构图;
图3是本发明实施例提供的端部底架的第二方向轴测图;
图4是图3中局部b的放大结构图;
图5是本发明实施例提供的端部底架的第三方向轴测图;
图6是图5中局部c的放大结构图;
图7是本发明实施例中牵引梁的结构示意图;
图8是本发明实施例中两个牵引梁腹板的轴测图;
图9是本发明实施例中第一补强板的安装示意图;
图10是图9的a-a向剖视图;
图11是本发明实施例中第二补强板的安装示意图;
图12是本发明实施例中连接件的第一方向轴测图;
图13是本发明实施例中连接件的第二方向轴测图;
图14是本发明实施例中牵引梁腹板与车钩安装座的安装示意图;
图15是本发明实施例中车钩安装座的结构示意图。
附图标记:
100:牵引梁;1:牵引梁腹板;10:第二安装孔;11:上翻边;12:下翻边;13:第一补强板;14:承载腔室;15:缓冲梁接口;16:枕梁接口;17:第二补强板;18:缺口;19:牵引梁插接板;111:第一水平板;112:第一弧形板;113:倾斜板;114:第二弧形板;115:第二水平板;116:第三弧形板;117:第四弧形板;118:第五弧形板;131:第一连接部;132:第二连接部;133:第三连接部;3:连接件;31:翻边连接部;32:腹板连接部;33:枕梁连接部;311:第一连接板;312:第二连接板;313:第三连接板;314:第四连接板;4:安装腔室;
200:车钩安装座;20:第一安装孔;21:第一安装板;22:第二安装板;23:第三安装板;230:车钩安装孔;231:第一筋板;232:第二筋板;233:第三筋板;
300:缓冲梁;301:缓冲梁端板;302:缓冲梁插接板;303:缓冲梁支撑板;304:缓冲梁连接板;305:第二插接翻边;306:连接筋板;
400:枕梁;401:上顶板;402:下底板;403:枕梁端板;404:第一插接翻边;405:加强筋板。
具体实施方式
下面结合附图和实施例对本发明的实施方式作进一步详细描述。以下实施例用于说明本发明,但不能用来限制本发明的范围。
在本发明实施例的描述中,需要说明的是,术语“中心”、“纵向”、“横向”、“上”、“下”、“前”、“后”、“左”、“右”、“竖直”、“水平”、“顶”、“底”、“内”、“外”等指示的方位或位置关系为基于附图所示的方位或位置关系,仅是为了便于描述本发明实施例和简化描述,而不是指示或暗示所指的装置或元件必须具有特定的方位、以特定的方位构造和操作,因此不能理解为对本发明实施例的限制。此外,术语“第一”、“第二”、“第三”仅用于描述目的,而不能理解为指示或暗示相对重要性。
在本发明实施例的描述中,需要说明的是,除非另有明确的规定和限定,术语“相连”、“连接”应做广义理解,例如,可以是固定连接,也可以是可拆卸连接,或一体连接;可以是机械连接,也可以是电连接;可以是直接相连,也可以通过中间媒介间接相连。对于本领域的普通技术人员而言,可以具体情况理解上述术语在本发明实施例中的具体含义。
在本发明实施例中,除非另有明确的规定和限定,第一特征在第二特征“上”或“下”可以是第一和第二特征直接接触,或第一和第二特征通过中间媒介间接接触。而且,第一特征在第二特征“之上”、“上方”和“上面”可是第一特征在第二特征正上方或斜上方,或仅仅表示第一特征水平高度高于第二特征。第一特征在第二特征“之下”、“下方”和“下面”可以是第一特征在第二特征正下方或斜下方,或仅仅表示第一特征水平高度小于第二特征。
在本说明书的描述中,参考术语“一个实施例”、“一些实施例”、“示例”、“具体示例”、或“一些示例”等的描述意指结合该实施例或示例描述的具体特征、结构、材料或者特点包含于本发明实施例的至少一个实施例或示例中。在本说明书中,对上述术语的示意性表述不必须针对的是相同的实施例或示例。而且,描述的具体特征、结构、材料或者特点可以在任一个或多个实施例或示例中以合适的方式结合。此外,在不相互矛盾的情况下,本领域的技术人员可以将本说明书中描述的不同实施例或示例以及不同实施例或示例的特征进行结合和组合。
如图1至图15所示,本发明实施例提供一种端部底架,包括牵引梁100、车钩安装座200、缓冲梁300和枕梁400。
其中,牵引梁100包括两个间隔相对设置的牵引梁腹板1,两个牵引梁腹板1之间安装有车钩安装座200,用于满足车钩的安装要求。
其中,各牵引梁腹板1的上侧分别连接有上翻边11,两个上翻边11相背设置。各牵引梁腹板1的下侧分别连接有下翻边12,两个下翻边12相背设置。各牵引梁腹板1的外侧分别设有第一补强板13,该第一补强板13与牵引梁腹板1平行设置,该第一补强板13连接在上翻边11与下翻边12之间,以使牵引梁腹板1、上翻边11、第一补强板13和下翻边12之间能够围合形成承载腔室14,从而作为牵引梁的主要承载结构,有效提高了牵引梁的结构强度。
其中,牵引梁腹板1的第一端、上翻边11的第一端、第一补强板13的第一端以及下翻边12的第一端之间形成缓冲梁接口15,牵引梁100通过该缓冲梁接口15与缓冲梁300相连。
其中,各上翻边11的第二端分别连接有连接件3,该连接件3分别与第一补强板13的上侧、牵引梁腹板1的上侧连接,使得牵引梁腹板1的第二端、下翻边12的第二端、第一补强板13的第二端以及连接件3之间形成枕梁接口16,牵引梁100通过该枕梁接口16与枕梁400相连。
本发明实施例的端部底架,在满足牵引梁100结构强度要求的前提下,使牵引梁100的结构更加紧凑,从而有效减小了牵引梁100所占用的结构空间,使得该端部底架能够同时满足跨座式单轨列车对车钩安装的空间接口要求和转向架空间限制区域要求,同时还满足了跨座式单轨列车中转向架不下车而直接换轮的车辆检修要求,节约了车辆检修成本。
如图12和图13所示,在本发明的一些实施例中,连接件3包括翻边连接部31、腹板连接部32和枕梁连接部33。其中,翻边连接部31包括从左到右依次连接的第一连接板311、第二连接板312、第三连接板313和第四连接板314,第一连接板311与上翻边11的第二端相连,从而实现连接件3与上翻边11之间的连接固定。第一补强板13的上侧与翻边连接部31沿长度方向延伸的一侧下表面相连,从而实现连接件3与第一补强板13之间的连接固定。
其中,腹板连接部32为竖直向设置的连接板,腹板连接部32设置于翻边连接部31沿长度方向延伸的另一侧,并且腹板连接部32的上侧与翻边连接部31的下表面相连。腹板连接部32的下侧与牵引梁腹板1的上侧相连,从而实现连接件3与牵引梁腹板1之间的连接固定。
其中,枕梁连接部33与翻边连接部31的第四连接板314相连,腹板连接部32的上侧与枕梁连接部33的下表面相连。第一补强板13的上侧与枕梁连接部33的下表面相连,从而实现连接件3与第一补强板13之间的连接固定。也即,连接件3、牵引梁腹板1、下翻边12以及第一补强板13之间能够围合形成安装腔室4,便于实现牵引梁100与枕梁400之间的稳定、可靠安装。
具体来说,翻边连接部31的宽度与上翻边11的宽度相同,枕梁连接部33的宽度大于翻边连接部31的宽度,从而使枕梁连接部33沿宽度方向延伸的两端能够分别延伸至安装腔室4的外部,进而便于实现枕梁连接部33与枕梁400之间的稳定、可靠安装。
具体来说,腹板连接部32远离上翻边11的一端与牵引梁腹板1的第二端平齐,第一补强板13的第二端与牵引梁腹板1的第二端平齐,下翻边12的第二端与牵引梁腹板1的第二端平齐。而枕梁连接部33与牵引梁腹板1的第二端之间具有一定间隔,也即,牵引梁腹板1的第二端、下翻边12的第二端以及腹板连接部32远离上翻边11的一端均处于安装腔室4的外部。
具体来说,第一连接板311、第二连接板312、第三连接板313、第四连接板314和枕梁连接部33从下至上依次设置,其中第一连接板311为水平设置的平板,第二连接板312、第三连接板313和第四连接板314分别为弧形板,从而使翻边连接部31与枕梁连接部33之间连接后形成从左到右逐渐向上凸起的平滑过渡的结构,进而便于实现牵引梁100与枕梁400之间的稳定、可靠安装。
如图9所示,在本发明的一些实施例中,下翻边12为水平设置的平板。上翻边11包括第一水平板111、第一弧形板112、倾斜板113、第二弧形板114、第二水平板115、第三弧形板116、第四弧形板117和第五弧形板118。其中,第一水平板111、第一弧形板112、倾斜板113、第二弧形板114、第二水平板115、第三弧形板116、第四弧形板117和第五弧形板118从左到右依次连接。第二水平板115的设置位置分别高于第二弧形板114和第三弧形板116的设置位置,第二弧形板114、倾斜板113、第一弧形板112和第一水平板111从上至下依次设置,第三弧形板116、第四弧形板117和第五弧形板118从上至下依次设置,从而使上翻边11整体呈向上凸起的结构。也即,下翻边12、牵引梁腹板1和上翻边11之间能够呈“凸”字形结构,使得牵引梁100的结构更加紧凑,进一步减小了牵引梁100的占用空间。
其中,倾斜板113与第一水平板111之间呈120°~135°的夹角,使得倾斜板113具有较为陡峭的坡度,从而使得牵引梁100的结构更加紧凑,进一步减小了牵引梁100的占用空间。
其中,第三弧形板116、第四弧形板117和第五弧形板118分别在下翻边12上的投影长度之和,远大于第一水平板111、第一弧形板112、倾斜板113和第二弧形板114分别在下翻边12上的投影长度之和,因此上翻边11向缓冲梁接口15一端的延伸较短,上翻边11向枕梁接口16一端的延伸较长,不仅使牵引梁100的结构更加紧凑,而且便于实现牵引梁100分别与缓冲梁300和枕梁400之间的稳定、可靠安装。
在本发明的一些实施例中,第一补强板13包括从左到右依次连接的第一连接部131、第二连接部132和第三连接部133,第一连接部131的下侧与下翻边12的上表面相连,第一连接部131的上侧与上翻边11间隔设置,使得第一连接部131与上翻边11之间形成开口结构。第二连接部132的下侧与下翻边12的上表面相连,第二连接部132的上侧与第五弧形板118的下表面相连,使得第二连接部132、下翻边12、牵引梁腹板1以及上翻边11之间能够围合形成承载腔室14。第三连接部133的下侧与下翻边12的上表面相连,第三连接部133的上侧与连接件3相连,使得第三连接部133、连接件3、牵引梁腹板1以及下翻边12之间能够围合形成安装腔室4。其中,第一补强板13的两端分别与下翻边12的两端对应平齐,便于实现牵引梁100分别与缓冲梁300和枕梁400之间的稳定、可靠安装。
在本发明的一些实施例中,在承载腔室14的内部还设有第二补强板17,第二补强板17位于第五弧形板118的中间位置处,并且第二补强板17的上下两侧分别与第五弧形板118的下表面、下翻边12的上表面相连。其中,第二补强板17与牵引梁腹板1间隔设置,第二补强板17与第一补强板13间隔设置,第二补强板17与第一补强板13平行设置,也即,第二补强板17能够将承载腔室14分隔为相互独立的两个腔室。其中,第二补强板17的长度小于第一补强板13的第二连接部132的长度。也即,通过设置第二补强板17,能够进一步提高了牵引梁100的结构强度。
在本发明的一些实施例中,在牵引梁腹板1的第一端下侧设有缺口18,其中下翻边12的第一端与该缺口18平齐,从而便于实现牵引梁100与缓冲梁300之间的插接配合。
如图1至图6所示,在本发明的一些实施例中,枕梁400包括上顶板401、下底板402和枕梁端板403,上顶板401与下底板402从上至下平行设置,枕梁端板403的上端与上顶板401的下表面垂直连接,枕梁端板403的下端与下底板402朝向牵引梁100一端的端面连接,从而使上顶板401的下表面与枕梁端板403的外侧面之间形成第一插接口。
其中,牵引梁100与枕梁400装配时,牵引梁腹板1的第二端、下翻边12的第二端、第一补强板13的第二端和腹板连接部32的端部分别设置于第一插接口中,并且牵引梁腹板1的第二端、下翻边12的第二端、第一补强板13的第二端和腹板连接部32的端部分别与枕梁端板403的外侧面固定连接。枕梁连接部33的端面与上顶板401的端面对接,从而实现了枕梁接口16与枕梁400之间的稳定、可靠安装。
具体来说,各下翻边12的下表面分别设有牵引梁插接板19,枕梁端板403的外侧面下端设有第一插接翻边404,牵引梁插接板19的第一端上表面与第一插接翻边404的下表面连接,进一步提高了牵引梁100与枕梁400装配的稳定性和可靠性。
其中,枕梁端板403的外侧面还设有加强筋板405,该加强筋板405沿枕梁端板403的长度方向延伸设置,能够进一步提高枕梁400的结构强度。
如图1至图6所示,在本发明的一些实施例中,缓冲梁300包括缓冲梁端板301、缓冲梁插接板302、缓冲梁支撑板303和缓冲梁连接板304,缓冲梁插接板302垂直连接在缓冲梁端板301朝向牵引梁100的一侧上端,缓冲梁支撑板303垂直连接在缓冲梁端板301朝向牵引梁100的一侧下端,也即,缓冲梁插接板302和缓冲梁支撑板303从上至下平行设置。
其中,缓冲梁连接板304垂直连接在缓冲梁支撑板303远离缓冲梁端板301的一侧上表面,从而使缓冲梁插接板302、缓冲梁端板301、缓冲梁支撑板303和缓冲梁连接板304之间形成第二插接口。
其中,牵引梁腹板1的第一端设置于第二插接口中,并且牵引梁腹板1的第一端与缓冲梁端板301连接。上翻边11的第一端的端面与缓冲梁插接板302的端面对接。缓冲梁连接板304设置于牵引梁腹板1第一端下侧的缺口18中。下翻边12的第一端与缓冲梁支撑板303连接。在缓冲梁连接板304朝向牵引梁1的一侧上端设有第二插接翻边305,在第一补强板13的第一端设有与第二插接翻边305相适配的插接槽,第二插接翻边305与插接槽插接配合,由此,实现了缓冲梁接口15与缓冲梁300之间的稳定、可靠安装。
具体来说,各上翻边11第一端的左右两侧分别设有连接筋板306,连接筋板306的形状与上翻边11第一端的形状相适配,各连接筋板306分别与缓冲梁插接板302的端面对接,进一步提高了牵引梁100与缓冲梁300装配的稳定性和可靠性。
如图14至图15所示,在本发明的一些实施例中,车钩安装座200包括第一安装板21、第二安装板22和第三安装板23,第一安装板21和第二安装板22相互平行,第一安装板21和第二安装板22分别与两个牵引梁腹板1对应连接,第三安装板23垂直连接在第一安装板21和第二安装板22之间。
其中,第一安装板21和所述第二安装板22上分别设有多个供安装件穿过的第一安装孔20,各牵引梁腹板1上分别设有与第一安装孔20相对应的第二安装孔10,便于通过安装件实现牵引梁腹板1与车钩安装座200之间的安装固定。
其中,第三安装板23的上端设有第一筋板231,第一筋板231的下表面分别与第一安装板21、第二安装板22相连。第三安装板23的下端设有第二筋板232,第二筋板232的上表面分别与第一安装板21、第二安装板22相连。在第一筋板231和第二筋板232之间设有第三筋板233,第三筋板233设置于第三安装板23上背向缓冲梁接口15的一侧,第三筋板233的两端分别与第一安装板21、第二安装板22对应连接。通过设置第一筋板231、第二筋板232和第三筋板233,能够提高车钩安装座200的结构强度。其中,第三安装板23上设有多个车钩安装孔230,用于安装车钩。
本发明实施例还提供一种轨道车辆,包括上述实施例的端部底架。由于该轨道车辆设置有上述实施例的端部底架,使得该轨道车辆具有上述端部底架的全部优点,进而提高了该轨道车辆的使用性能。
以上实施方式仅用于说明本发明,而非对本发明的限制。尽管参照实施例对本发明进行了详细说明,本领域的普通技术人员应当理解,对本发明的技术方案进行各种组合、修改或者等同替换,都不脱离本发明技术方案的精神和范围,均应涵盖在本发明的权利要求范围中。
起点商标作为专业知识产权交易平台,可以帮助大家解决很多问题,如果大家想要了解更多知产交易信息请点击 【在线咨询】或添加微信 【19522093243】与客服一对一沟通,为大家解决相关问题。
此文章来源于网络,如有侵权,请联系删除


