一种中压模块及其地铁转向架自动定位压紧装置的制作方法



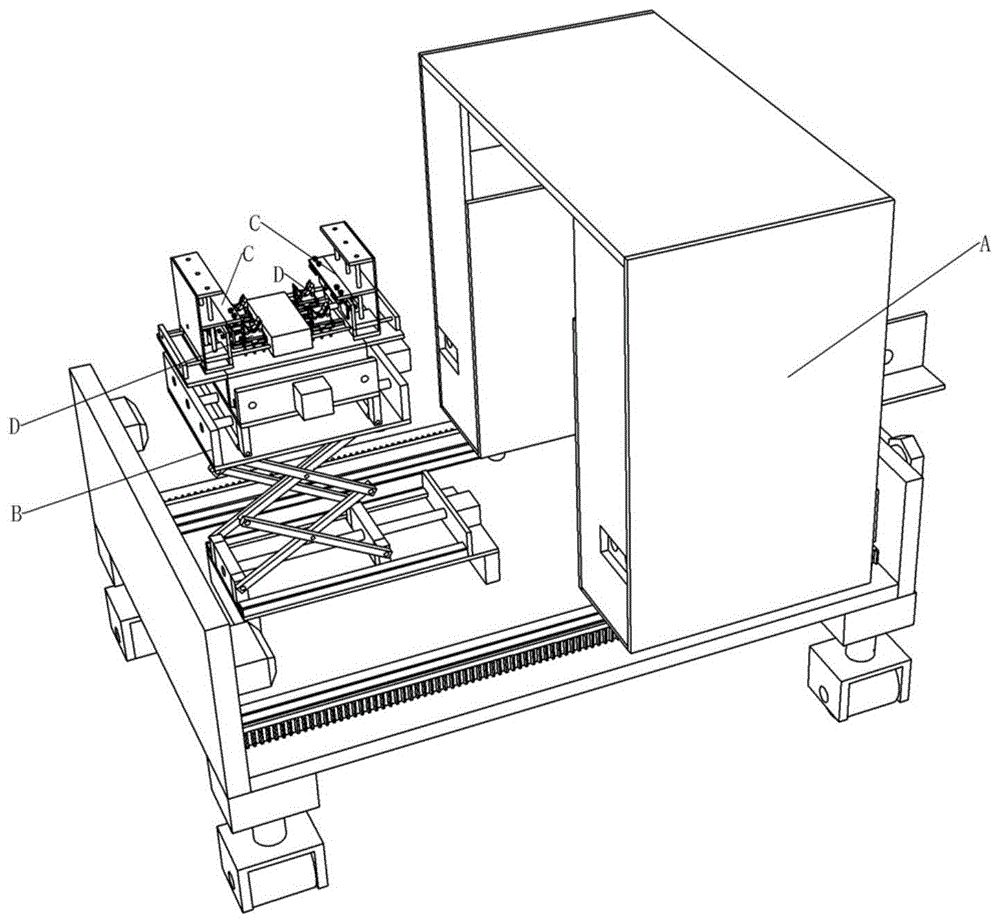
本发明涉及地铁检修技术,特别是涉及一种地铁转向架自动定位压紧装置。
背景技术:
在地铁检修中,对转向架进行检修是必经工序。目前的操作方式是采用工装安放转向架,然后利用工装上的结构对转向架进行定位、压紧或夹紧。对于转向架一般需要进行两端对中定位、两端下压定位、中间下压定位,通过这几个定位点定位后能够相对精确地确定转向架的位置,从而为后续的自动化、智能化检修及拆机提供基础。
目前的工装对中定位一般采用两端同步移动进行夹紧,但是由于转向架放置的误差因素,大概率会出现向一端偏移的问题,此时采用两端同步移动的对中方式就会导致一端已经压紧转向架、但是另一端却没有压紧,造成较大的定位误差,严重影响后续操作的自动化,因此目前这一步无法脱离人工。
另外在对转向架两端的下压压紧定位一般会采用两端贴紧定位完成后再进行,一旦两端侧面定位出现偏差,两端的下压压紧定位一定会出现偏差,而且一般两端的下压定位时联动的,一旦转向架存在上下不平、上翘等问题,那么势必造成两端下压定位存在更大的误差。对于中间下压定位,由于需要采用由上至下下压的方式,因此需要将转向架起吊后穿过中间下压定位装置的龙门,这显然会大大增加难度,操作性极低。当然可以采用每个定位点单独定位的方式,但是这样成本很高,而且不采用联动方式会造成结构复杂、控制系统复杂等问题。
对此发明人设计了一种地铁转向架自动定位压紧装置,其能够通过联动的方式实现转向架两端侧面、两端下压、中间下压的定位和压紧,同时通过龙门可移动的设计大大方便了整个转向架的吊装、定位。
技术实现要素:
有鉴于现有技术的上述缺陷,本发明所要解决的技术问题是提供一种中压模块及其地铁转向架自动定位压紧装置,其中压模块能够相对于定位台移动,从而方便转向架的吊装。
为实现上述目的,本发明提供了一种中压模块,包括龙门,龙门包括龙门组件、龙门顶板、中压座板,所述龙门组件有两个,两个龙门组件顶部分别与龙门顶板两端装配;中压座板的两端与两个龙门组件上的中压螺杆通过螺纹旋合装配,所述中压座板与中压限位轴卡合、可轴向滑动装配,所述中压限位轴一端与中压板装配、另一端穿过中压座板后与中压螺母装配固定,所述中压螺母不能穿过中压座板,所述中压限位轴位于中压座板、中压板之间的部分上套装有中压弹簧,所述中压弹簧用于对中压板施加阻碍其向中压座板移动的弹力,所述中压板上安装有中压触发板,所述中压座板上安装有中压行程开关,所述中压板向中压座板移动后可触发压行程开关,中压行程开关被触发后会向工控机输入信号,工控机判断为中压板下压到位;
所述底座齿条与行走齿轮啮合并构成齿轮齿条传动机构,所述行走齿轮套装在行走齿轴一端上,行走齿轴另一端穿过第一龙门横板后与第二离合盘装配固定,所述第二离合盘装入第二离合筒内且初始状态时与第二离合筒内侧端面压紧,从而使得第二离合筒与第二离合盘不可相对圆周转动,所述第二离合筒安装在离合轴一端上,所述离合轴另一端上安装有第一离合筒;
所述第一离合筒内部中空且其内部可轴向滑动地安装有第一离合盘,所述第一离合盘安装在中压螺杆底部,初始状态时第一离合盘与第一离合筒的内侧端面不接触,此时第一离合筒无法带动第一离合盘圆周转动;在第二离合盘与第二离合筒的内侧端面分离后,第一离合盘与第一离合筒压紧,从而使得第一离合盘与第一离合筒不可相对圆周转动,此时离合轴可驱动中压螺杆圆周转动。
优选地,还包括底座,底座上分别安装有两块相互平行的第一底座立板、第二底座立板,所述底座底部安装有万向轮,万向轮用于支撑底座且可带动底座移动;所述第一底座立板上安装有换向推块,所述换向推块用于驱动换向滑块移动;
所述底座与定位台的定位底板装配固定,所述第二底座立板与底座滑轴卡合、可轴向滑动装配,所述底座滑轴一端与底座推板装配固定、另一端穿出第二底座立板后与底座螺母装配,所述底座螺母不能穿过第二底座立板,所述底座滑轴位于第二底座立板和底座推板之间的部分上套装有底座弹簧,所述底座弹簧用于对底座推板施加阻碍底座弹簧向第二底座立板移动的弹力;
所述第二底座立板上安装有底座行程开关,所述底座的触发端正对底座推板,底座推板向第二底座立板移动后可触发底座行程开关,底座行程开关被触发后向工控机输入信号,工控机判断为龙门处于远离定位台一端;所述底座上安装有底座导轨、底座齿条。
优选地,所述龙门组件包括第一龙门侧板、第一龙门立板,第一龙门立板有两块且分别安装在第一龙门侧板两侧,两块第一龙门立板、第一龙门侧板顶部分别与龙门装配固定,两块第一龙门立板远离第一龙门侧板一侧分别与第二龙门侧板装配固定,两块第一龙门立板、第一龙门侧板、第二龙门侧板之间由上至下依次安装有第五龙门横板、第四龙门横板、第三龙门横板、第六龙门横板、第七龙门横板、第二龙门横板、第一龙门横板,所述第六龙门横板、第七龙门横板、分别安装在第三龙门侧板上,所述第三龙门侧板安装在第二龙门侧板上;所述第一龙门横板底部安装有龙门行走轴,所述龙门行走轴上可圆周转动地套装有龙门行走轮;
所述离合轴分别穿过第二龙门横板、换向滑块的换向通槽、换向升降块、第七龙门横板、离合升降齿轮后与第一离合筒装配固定,所述第二龙门横板、第七龙门横板分别与离合轴可圆周转动和可轴向滑动装配,所述换向升降块与离合轴可圆周转动、不可轴向移动装配;
所述第二离合筒与离合推力球轴承的座圈压紧或装配,所述推力球轴承的轴圈与离合弹簧一端压紧或装配,所述离合弹簧另一端与第二龙门横板压紧。
优选地,所述换向升降块一侧上安装有换向升降滑块,换向升降滑块与换向升降滑槽卡合、可滑动装配,所述换向升降滑槽设置在换向立板上,所述换向立板安装在第二龙门横板上。
优选地,所述换向滑块两端分别与第一滑块端板、第二滑块端板装配固定,所述第一滑块端板、第二滑块端板分别与滑块短轴一端、滑块导向筒一端装配固定,所述滑块短轴另一端与滑块推板装配固定,所述滑块导向筒套装在滑块导向轴上且与之可轴向滑动装配,所述滑块导向轴安装在滑块轴板上,滑块轴板安装在第二龙门横板上,所述滑块轴板、第二滑块端板之间套装有滑块弹簧,滑块弹簧用于对换向滑块产生向滑块推板推动的弹力;
所述换向滑块上设置有换向斜面,所述换向升降块上设置有升降斜面,所述换向斜面与升降斜面贴合,所述换向斜面由靠近第二滑块端板一端向靠近第一滑块端板一端向上倾斜设置;
所述第一龙门立板与滑块推板对应处设置有贯穿的推板驱动槽,换向推块可穿过推板驱动槽从而驱动滑块推板克服滑块弹簧的弹力向滑块轴板移动;所述换向升降块与换向推力球轴承的座圈贴紧或装配,所述换向推力球轴承的轴圈套装固定在离合轴上,所述离合升降齿轮与离合动力齿啮合传动。
优选地,所述离合动力齿套装固定在离合动力轴上,所述离合动力轴与第六龙门横板、第七龙门横板可圆周转动且不可轴向移动装配,所述离合动力轴上套装固定有龙门蜗轮,所述龙门蜗轮与龙门蜗杆部分啮合并构成蜗轮蜗杆传动结构,所述龙门蜗杆部分设置在龙门动力轴上,所述龙门动力轴分别与第二龙门立板、至少一块第一龙门立板可圆周转动且不可轴向移动装配,龙门动力轴一端穿出其中一块第一龙门立板后与第一龙门斜齿轮装配固定,所述第一龙门斜齿轮与第二龙门斜齿轮啮合传动,所述第二龙门斜齿轮套装固定在龙门电机轴上,所述龙门电机轴装入龙门电机内,所述龙门电机轴的两端分别与至少一块龙门轴板可圆周转动装配,所述龙门轴板安装在龙门电机板上,所述龙门电机板安装在两个龙门组件的其中一块龙门立板上。
优选地,所述中压螺杆分别与第五龙门横板、第四龙门横板可圆周转动且不可轴向移动装配,中压螺杆顶部穿出第五龙门横板后穿过中压座板且与中压座板通过螺纹旋合装配。
优选地,所述第一底座立板还与气缸的伸缩轴可轴向滑动装配,气缸的伸缩轴穿过第一底座立板后其端面与龙门的侧面贴合或贴紧。
优选地,所述中压座板上还安装有中压限位板,所述中压限位板用于限制中压触发板向中压座板移动的最大位移量,中压螺杆顶部与中压轴承装配,中压轴承安装在龙门顶板上。
本发明还公开了一种地铁转向架自动定位压紧装置,其应用有上述中压模块。
本发明的有益效果是:
1、本发明的定位台能够实现侧端定位机构的两轴微调,从而在吊装转向架时通过两轴微调增加转向架的初始定位精度。另外将下压机构安装在侧端定位机构上可以确保两端侧面定位与两端下压定位的精度,从而降低定位误差,为后续的自动化操作提供基础。
2、本发明的侧端定位机构通过两块侧端压板反向同步移动能够快速地实现对转向架两端侧面的定位,而且由于设置了过载让位组件,在一端的侧端压板与转向架压紧时,另一端的侧端压板还能继续移动,从而确保对转向架两端侧面的高精度定位。
3、本发明的中压模块能够通过沿着中压滑轨携带龙门相对于定位台移动,从而解决龙门影响转向架吊装在定位台上的问题。另外通过中压电机实现龙门的行走、中压座板的上下移动,且只能在龙门达到定位位置后才能驱动中压座板下移,从而避免误操作且提高定位精度。
4、本发明的下压机构自带过载让位功能,从而可以既能够实现两端联动以进行快速定位,又能够实现两端不同步移动以探测转向架是否存在起翘的问题。
5、本发明的轮轴定位机构能够实现轮轴的定位,从而为后续轮轴的检修、拆卸提供定位数据。
6、本发明的过载让位组件能够同时实现两根侧端齿条的同步反向移动、单一过载后异步移动,从而既能够快速地实现转向架两端侧面的定位,又能在转向架两端位置偏移较大时实现两端的精确定位。
附图说明
图1-图5是本发明的结构示意图。其中图5是中压螺杆a240轴线所在中心面处剖视图。
图6是本发明的底座a110部分结构示意图。
图7-图14是定位台的结构示意图。
图15-图17是侧端定位机构的结构示意图。其中图17是下压螺杆轴线所在中心面处剖视图。
图18-图26是过载让位组件的结构示意图。其中图19是侧端联动轴c260轴线所在中心面处剖视图;图23是侧端动力轴c250轴线所在中心面处剖视图。
图27-图30是轮轴定位机构轴线所在中心面处剖视图。其中图29、图30分别是轮轴限位轴d230、触发滑轴d240轴线所在中心面处剖视图。
图31-图38是中压模块的结构示意图。
图39是中压限位轴a820轴线所在中心面处剖视图。
具体实施方式
下面将结合本发明实施例中的附图,对本发明实施例中的技术方案进行清楚、完整地描述。
在本发明的描述中,需要理解的是,术语“上”、“下”、“前”、“后”、“左”、“右”、“顶”、“底”、“内”、“外”等指示的方位或位置关系为基于附图所示的方位或位置关系,仅是为了便于描述本发明和简化描述,而不是指示或暗示所指的装置或元件必须具有特定的方位、以特定的方位构造和操作,因此不能理解为对本发明的限制。
参见图1-图39,本实施例的转向架100上安装有轮轴110,轮轴110上套装有钢轮120,而转向架100的顶部安装有连杆130。
参见图1-图39,本实施例的地铁转向架自动定位压紧装置,包括:
定位台b,用于安装、定位转向架100;
侧端定位机构c,用于定位、夹紧转向架100两端;
下压机构,用于通过下压板下压、定位转向架100两端;
中压模块a,用于通过中压板a810下压、定位转向架100的中间部分。
参见图1-图14、图31-图38,所述中压模块a、定位台b均安装在底座a110上,所述底座a110上分别安装有两块相互平行的第一底座立板a120、第二底座立板a130,所述底座a110底部安装有万向轮a410,万向轮a410用于支撑底座a110且可以带动底座a110移动;所述第一底座立板a120上安装有换向推块a121,所述换向推块a121用于驱动换向滑块a740移动。
所述底座a110与定位台b的定位底板b110装配固定,所述第二底座立板a130与底座滑轴a220卡合、可轴向滑动装配,所述底座滑轴a220一端与底座推板a140装配固定、另一端穿出第二底座立板a130后与底座螺母a221装配,所述底座螺母a221不能穿过第二底座立板a130,所述底座滑轴a220位于第二底座立板a130和底座推板a140之间的部分上套装有底座弹簧a610,所述底座弹簧a610用于对底座推板a140施加阻碍底座弹簧a610向第二底座立板a130移动的弹力。所述第二底座立板a130上安装有底座行程开关a510,所述底座行程开关a510的触发端正对底座推板a140,底座推板a140向第二底座立板a130移动后能够触发底座行程开关a510,底座行程开关a510被触发后向工控机输入信号,工控机判断为龙门a300处于远离定位台b一端。所述底座a110上安装有底座导轨a210、底座齿条a420。
所述中压模块a包括龙门a300,龙门a300包括龙门组件、龙门顶板a360,所述龙门组件有两个,两个龙门组件顶部分别与龙门顶板a360两端装配,所述龙门组件包括第一龙门侧板a311、第一龙门立板a371,第一龙门立板a371有两块且分别安装在第一龙门侧板a311两侧,两块第一龙门立板a371、第一龙门侧板a311顶部分别与龙门顶板a360装配固定,两块第一龙门立板a371远离第一龙门侧板a311一侧分别与第二龙门侧板a312装配固定,两块第一龙门立板a371、第一龙门侧板a311、第二龙门侧板a312之间由上至下依次安装有第五龙门横板a325、第四龙门横板a324、第三龙门横板a323、第六龙门横板a326、第七龙门横板a327、第二龙门横板a322、第一龙门横板a321,所述第六龙门横板a326、第七龙门横板a327、分别安装在第三龙门侧板a313上,所述第三龙门侧板a313安装在第二龙门侧板a312上;所述第一龙门横板a321底部安装有龙门行走轴a440,所述龙门行走轴a440上可圆周转动地套装有龙门行走轮a441;所述底座齿条a420与行走齿轮a421啮合并构成齿轮齿条传动机构,所述行走齿轮a421套装在行走齿轴a270一端上,行走齿轴a270另一端穿过第一龙门横板a321后与第二离合盘a481装配固定,所述第二离合盘a481装入第二离合筒a480内且初始状态时与第二离合筒a480内侧端面压紧,从而实现第二离合筒a480与第二离合盘a481不可相对圆周转动,所述第二离合筒a480安装在离合轴a260一端上,所述离合轴a260另一端上安装有第一离合筒a470,所述离合轴a260分别穿过第二龙门横板a322、换向滑块a740的换向通槽a742、换向升降块a350、第七龙门横板a327、离合升降齿轮a451后与第一离合筒a470装配固定,所述第二龙门横板a322、第七龙门横板a327分别与离合轴a260可圆周转动和可轴向滑动装配,所述换向升降块a350与离合轴a260可圆周转动、不可轴向移动装配。所述换向升降块a350一侧上安装有换向升降滑块a351,换向升降滑块a351与换向升降滑槽a341卡合、可滑动装配,所述换向升降滑槽a341设置在换向立板a340上,所述换向立板a340安装在第二龙门横板a322上,所述第二离合筒a480与离合推力球轴承a482的座圈压紧或装配,所述推力球轴承a482的轴圈与离合弹簧a620一端压紧或装配,所述离合弹簧a620另一端与第二龙门横板a322压紧,本实施例中离合弹簧a620套装在离合轴a260上。离合弹簧a620用于对第二离合筒a480施加向第二离合盘a481推动的弹力,从而使得初始状态时第二离合筒a480内侧端面保持与第二离合盘a481压紧。
所述换向滑块a740两端分别与第一滑块端板a730、第二滑块端板a750装配固定,所述第一滑块端板a730、第二滑块端板a750分别与滑块短轴a720一端、滑块导向筒a760一端装配固定,所述滑块短轴a720另一端与滑块推板a710装配固定,所述滑块导向筒a760套装在滑块导向轴a770上且与之可轴向滑动装配,所述滑块导向轴a770安装在滑块轴板a780上,滑块轴板a780安装在第二龙门横板a322上,所述滑块轴板a780、第二滑块端板a750之间套装有滑块弹簧a630,滑块弹簧a630用于对换向滑块a740产生向滑块推板a710推动的弹力。所述换向滑块a740上设置有换向斜面a741,所述换向升降块a350上设置有升降斜面a352,所述换向斜面a741与升降斜面a352贴合,所述换向斜面a741由靠近第二滑块端板a750一端向靠近第一滑块端板a730一端向上倾斜设置。所述第一龙门立板a371与滑块推板a710对应处设置有贯穿的推板驱动槽a3711,使用时,换向推块a121可以穿过推板驱动槽a3711从而驱动滑块推板a710克服滑块弹簧a630的弹力向滑块轴板a780移动。
所述换向升降块a350与换向推力球轴承a490的座圈贴紧或装配,所述换向推力球轴承a490的轴圈套装固定在离合轴a260上;所述换向升降块a350升降时,不会影响离合轴a260的圆周转动但能够带动离合轴a260轴向同步升降。所述离合升降齿轮a451与离合动力齿a452啮合传动,所述离合动力齿a452套装固定在离合动力轴a250上,所述离合动力轴a250与第六龙门横板a326、第七龙门横板a327可圆周转动且不可轴向移动装配,所述离合动力轴a250上套装固定有龙门蜗轮a461,所述龙门蜗轮a461与龙门蜗杆部分a462啮合并构成蜗轮蜗杆传动结构,所述龙门蜗杆部分a462设置在龙门动力轴a230上,所述龙门动力轴a230分别与第二龙门立板a372、至少一块第一龙门立板a371可圆周转动且不可轴向移动装配,龙门动力轴a230一端穿出其中一块第一龙门立板a371后与第一龙门斜齿轮a431装配固定,所述第一龙门斜齿轮a431与第二龙门斜齿轮a432啮合传动,所述第二龙门斜齿轮a432套装固定在龙门电机轴a521上,所述龙门电机轴a521装入龙门电机a520内且龙门电机a520启动后能够驱动龙门电机轴a521圆周转动,所述龙门电机a520为双轴电机,所述龙门电机轴a521的两端分别与至少一块龙门轴板a381可圆周转动装配,所述龙门轴板a381安装在龙门电机板a380上,所述龙门电机板a380安装在两个龙门组件的其中一块龙门立板a371上。
所述第一离合筒a470内部中空且其内部可轴向滑动地安装有第一离合盘a471,所述第一离合盘a471安装在中压螺杆a240底部,初始状态时第一离合盘a471与第一离合筒a470的内侧端面不接触,此时第一离合筒a470无法带动第一离合盘a471圆周转动。在第二离合盘a481与第二离合筒a480的内侧端面分离后,第一离合盘a471与第一离合筒a470压紧,从而使得第一离合盘a471与第一离合筒a470不可相对圆周转动,此时离合轴a260能够驱动中压螺杆a240圆周转动。所述中压螺杆a240分别与第五龙门横板a325、第四龙门横板a324可圆周转动且不可轴向移动装配,中压螺杆a240顶部穿出第五龙门横板a325后穿过中压座板a330且与中压座板a330通过螺纹旋合装配,所述中压座板a330与中压限位轴a820卡合、可轴向滑动装配,所述中压限位轴a820一端与中压板a810装配、另一端穿过中压座板a330后与中压螺母a821装配固定,所述中压螺母a821不能穿过中压座板a330,所述中压限位轴a820位于中压座板a330、中压板a810之间的部分上套装有中压弹簧a640,所述中压弹簧a640用于对中压板a810施加阻碍其向中压座板a330移动的弹力,所述中压板a810上安装有中压触发板a811,所述中压座板a330上安装有中压行程开关a530、中压限位板a331,所述中压板a810向中压座板a330移动后能够触发压行程开关a530,中压行程开关a530被触发后会向工控机输入信号,工控机判断为中压板a810下压到位。所述中压限位板a331用于限制中压触发板a811向中压座板a330移动的最大位移量。中压螺杆a240顶部与中压轴承a710装配,中压轴承a710安装在龙门顶板a360上。
初始状态时,第二离合盘a481与第二离合筒a480的内侧端面压紧,第一离合筒a470与第一离合盘a471分离,此时龙门a300位于远离定位台b一端,此时底座行程开关被触发。转向架在定位台b上安装完成且分别通过侧端定位机构c、轮轴定位机构d进行两端及轮轴定位后,启动龙门电机a520,龙门电机a520驱动离合轴a260圆周转动,离合轴a260带动行走齿轴a270圆周转动,行走齿轴a270带动行走齿轮a421圆周转动,行走齿轮a421沿着底座齿条a420移动,直到龙门侧面与第一底座立板a120贴紧。此时中压板a810位于转向架100中间位于两根连杆a130之间的部分上方且换向推块a121穿过推板驱动槽a3711后推动滑块推板a710、换向滑块a740向滑块轴板a780移动,从而驱动升降滑块a350带动离合轴a260上移直到第一离合盘a471与第一离合筒a470的内侧端面压紧,此时第二离合盘a481与第二离合筒a480的内侧端面分离。龙门电机a520继续驱动离合轴a260圆周转动,离合轴a260带动中压螺杆a240圆周转动,中压螺杆a240通过螺纹驱动中压座板a330沿着其轴向下移,直到中压板a810压紧在转向架100位于两根连杆a130之间的部分上,最后触发中压行程开关a530,中压行程开关a530向工控机输入信号,工控机控制龙门电机停止运行,此时判断为转向架100中间部分被压紧、定位。
优选地,所述第一底座立板a120还与气缸(未画出)的伸缩轴可轴向滑动装配,气缸的伸缩轴穿过第一底座立板a120后其端面与龙门a300的侧面贴合或贴紧。在需要移开中压模块时,龙门电机a520反转从而驱动中中压座板a330上移复位,然后气缸进气驱动伸缩轴伸长,伸缩轴推动龙门a300向第二底座立板a130移动,从而使得换向推块a121退出推板驱动槽a3711,以使得换向滑块a740通过滑块弹簧a630的弹力复位,最终使得第二离合筒a480的内侧端面与第二离合盘a481贴紧,从而恢复至初始状态。
参见图1-图30,所述定位台b包括升降机构、定位顶板b140、侧端定位机构c、轮轴定位机构d,所述升降机构包括定位底板b110,定位底板b110上分别安装有两块相互平行的升降立板b131、两块相互平行的升降侧板b120,两块升降立板b131分别与升降螺杆b220可圆周转动、不可轴向移动装配,且升降螺杆b220一端穿出其中一块升降立板b131后通过联轴器与升降电机b310的输出轴连接固定,升降电机b310安装在定位底板b110上。
两块相互平行的升降侧板b120内侧为升降滑槽b121,升降滑槽b121与升降动力板b132两侧的升降滑块b1321卡合可滑动装配,所述升降动力板b132套装在升降螺杆b220外且与之通过螺纹旋合装配;所述升降动力板b132通过第一升降销b211与第一升降杆b410一端铰接,第一升降杆b410中间部分通过第三升降销b213与第二升降杆b420的中间部分铰接、顶部通过第五升降销b215与另一第一升降杆b410一端铰接;所述第二升降杆b420一端通过第二升降销b212与其中一块升降立板b131铰接、另一端通过第四升降销b214与另一第二升降杆b420一端铰接;
位于最上方的第一升降杆b410、第二升降杆b420分别通过第六升降销b216与不同的定位顶板块b141铰接,定位顶板块b141安装在定位顶板b140上。位于定位顶板块b141、升降动力板b132和升降立板b131之间的第一升降杆b410首尾通过不同的第五升降销b215逐一铰接;位于定位顶板块b141、升降动力板b132和升降立板b131之间的第二升降杆b420首尾通过不同的第四升降销b214逐一铰接;而每根对应的第一升降杆b410、第二升降杆b420的中间部分均通过第三升降销b213铰接。这种设计使得升降电机驱动升降螺杆转动时,能够带动升降动力板沿着升降螺杆的轴向移动,从而使得第一升降杆b410、第二升降杆b420之间进行收展,也就可以实现定位顶板b140的升降。
所述定位顶板b140上安装有两块相互平行的第一定位立板b151,两块第一定位立板b151之间安装有第一定位侧移板b161,两块第一定位立板b151分别与第一定位导向轴b230两端装配且两块第一定位立板b151还分别与第一定位螺杆b240可圆周转动且不可轴向移动装配,所述第一定位导向轴b230、第一定位螺杆b240分别穿过第一定位侧移板b161,且第一定位导向轴b230与第一定位侧移板b161卡合可轴向滑动装配,所述第一定位螺杆b240与第一定位侧移板b161通过螺纹旋合装配,第一定位螺杆b240与第一定位电机b320的输出轴通过联轴器连接固定,所述第一定位电机b320启动后能够驱动第一定位螺杆b240圆周转动,从而驱动第一定位侧移板b161沿着第一定位螺杆b240轴向移动。所述第一定位侧移板b161一端安装在第一定位架板b160上、第一定位侧移板b161另一端通过第一滚筒轴b251与第一滚筒b250可圆周转动装配,所述第一滚筒b250套装在第一滚筒轴b251上,第一滚筒轴b251安装在第一定位侧移板b161上。
所述第一定位架板b160顶部安装有两块相互平行的第二定位立板b162,两块第二定位立板b162之间安装有第二定位侧移板b171,所述第二定位侧移板b171安装在第二定位架板b170上;两块第二定位立板b162分别与第二定位导向轴b270、第二定位螺杆b271装配,所述第二定位螺杆b271分别与两块第二定位立板b162可圆周转动、不可轴向移动装配;所述第二定位导向轴b270、第二定位螺杆b271穿过第二定位侧移板b171,且第二定位导向轴b270与第二定位侧移板b171卡合、可轴向滑动装配,所述第二定位螺杆b271与第二定位侧移板b171通过螺纹旋合装配,所述第二定位侧移板b171一端穿出其中一块第二定位立板b162后与第二定位电机b330的输出轴通过联轴器连接,所述第二定位电机b330启动后能够驱动第二定位螺杆b271圆周转动,从而驱动第二定位侧移板b171沿着其轴向移动。所述第二定位侧移板b171上安装有第二滚筒轴b261,所述第二滚筒轴b261上可圆周转动地套装有第二滚筒b260。
使用时,第一定位电机b320启动,从而驱动第一定位架板b160沿着第一定位螺杆b240的轴向移动,而第一滚筒b250在定位顶板b140上滚动,从而既能够支撑第一定位架板b160,又能够降低第一定位侧移板b161与定位顶板的摩擦力。同理,第二定位电机b330启动后能够驱动第二定位架板b170沿着第二定位螺杆b271轴向移动,而第二滚筒在第一定位架板b160上滚动。这样可以实现第二定位架板b170的两轴调节,加上升降机构可实现三轴调节,从而可以在装载、定位转向架时进行微调以增加粗略定位的精度,为后续的侧端定位机构c、下压机构、轮轴定位机构d、中压模块a的精确定位提供基础。
所述第二定位架板b170顶部安装有两块相互平行的第二定位立板b172,两块第二定位立板b172分别与第三定位导向轴b280装配固定,所述第三定位导向轴b280分别穿过侧端定位组件、过载让位组件,且侧端定位组件、过载让位组件可与第三定位导向轴b280相对轴向滑动。
所述侧端定位机构c包括两个侧端定位组件,所述侧端定位组件上安装有第一侧端立板c110、第二侧端立板c120,所述第一侧端立板c110、第二侧端立板c120底部分别安装在第一侧端横板c131上,所述第一侧端立板c110、第二侧端立板c120中间部分安装有第二侧端立板c132,所述第一侧端立板c110顶部安装有第四侧端横板c134;所述第二侧端立板c120与侧端限位轴c240卡合、可轴向滑动装配,所述侧端限位轴c240一端与侧端压板c140装配固定、另一端穿过第二侧端立板c120后与侧端螺母c241装配,所述侧端螺母c241不能穿过第二侧端立板c120,且侧端限位轴c240位于第二侧端立板c120和侧端压板c140之间的部分上套装有侧端弹簧c511,所述侧端弹簧c511用于对侧端压板c140施加阻碍其向第二侧端立板c120移动的弹力。所述第二侧端立板c120上安装有侧端行程开关c390,所述侧端行程开关c390的触发端与侧端压板c140正对,且侧端压板c140向第二侧端立板c120移动后能够触发侧端行程开关c390,侧端行程开关c390被触发后向工控机发送信号,工控机判断为对转向架100两端侧面的定位完成。
所述第一侧端立板c110、第二侧端立板c120均可轴向滑动地套装在第三定位导向轴b280上,所述第二侧端立板c120还与侧端齿条c610一端装配固定,所述侧端齿条c610另一端穿过过载壳c160且与之可滑动装配,所述侧端齿条c610上设置有侧端滑块c611,所述侧端滑块c611与过载导向板c162卡合、可滑动装配,所述侧端滑块c611安装在过载壳c160上;过载壳c160顶部与转向架100底面贴合以支撑转向架100。
所述过载让位组件包括过载壳c160,所述过载壳c160内部为中空的过载安装腔c164,所述过载安装腔c164内安装有侧端齿轮c475,所述侧端齿轮c475与侧端齿条c610啮合并构成齿轮齿条传动机构,所述侧端齿轮c475套装在侧端动力轴c250上且与之通过螺纹旋合装配,所述侧端动力轴c250上还套装有过载从动齿轮c474,所述过载从动齿轮c474与过载主动齿轮c473啮合传动,所述过载主动齿轮c473套装固定在侧端联动轴c260上,所述侧端联动轴c260穿过齿条刹车架c710的刹车底板c711、联动轴架c163、过载底板c170后与第一动力齿c411装配,所述侧端联动轴c260分别与联动轴架c163、过载底板c170、刹车底板c711可圆周转动且不可轴向移动装配。所述第一动力齿c411与第二动力齿轮c412啮合传动,第二动力齿轮c412与第三动力齿轮c413啮合传动,所述第二动力齿轮c412、第三动力齿轮c413分别套装在动力中转轴c270、侧端电机轴c321上,所述动力中转轴c270、侧端电机轴c321分别与过载底板c170可圆周转动装配,所述侧端电机轴c321穿过过载底板c170后装入侧端电机c320内,侧端电机c320启动后能够驱动侧端电机轴c321圆周转动,所述侧端电机轴c321圆周转动时可通过第三动力齿轮c413、第二动力齿轮c412驱动第一动力齿c411圆周转动,从而驱动侧端联动轴c260圆周转动。
所述过载底板c170通过过载侧板c161与过载壳c160装配,所述联动轴架c163安装在过载底板c170上,所述侧端动力轴c250上不可相对圆周转动、可轴向滑动地套装有第一推力轴承c481,具体地第一推力轴承c481的轴圈套装在侧端动力轴c250上且与侧端齿轮c475的端面贴紧,所述第一推力轴承c481的座端与过载弹簧c530一端贴紧或装配,所述过载弹簧c530套装在侧端动力轴c250上且另一端与第三推力轴承c483的轴圈贴紧或装配,所述第三推力轴承c483的座圈与调节筒c630一端压紧或装配,所述调节筒c630另一端穿过联动轴架c163后与调节齿轮c476装配固定,调节筒c630与联动轴架c163通过螺纹旋合装配。调节筒c630与侧端动力轴c250可圆周转动、轴向移动装配。
所述调节齿轮c476与调节齿条c620啮合并构成齿轮齿条传动机构,所述调节齿条c620上设置有调节滑块c621,所述调节滑块c621与调节保持块c172卡合、可滑动装配,所述调节保持块c172安装在过载底板c170上,所述调节齿条c620上安装有调节螺纹板c622,调节螺纹板c622套装在调节螺杆c331上且与调节螺杆c331通过螺纹旋合装配;调节螺杆c331分别与两块调节轴板c171可圆周转动、不可轴向移动装配,两块调节轴板c171分别安装在过载侧板c161上,所述调节螺杆c331一端与调节电机c330的输出轴通过联轴器连接固定,所述调节电机c330启动后能够带动调节螺杆c331圆周转动,从而带动调节螺纹板c622同步移动,也就带动了调节齿条c620移动,最终带动调节齿轮c476圆周转动,以带动调节筒c630圆周转动,侧端动力轴c250圆周转动时能够通过螺纹使其与联动轴架c163在轴向上相对移动。从而调节调节筒c630对过载弹簧c530施加的预压力。从而调节侧端齿轮c475与侧端动力轴c250相对转动所需要的扭矩。
由于过载弹簧c530对第一推力轴承c481施加了轴向的推力,这就使得侧端齿轮c475与侧端动力轴c250之间发生相对转动需要一定的扭矩。在这个扭矩没有达到之前侧端齿轮c475与侧端动力轴c250会同步转动,此时侧端齿轮c475与侧端动力轴c250处于相对静止状态。一旦侧端齿轮c475不能转动,那么侧端动力轴c250与侧端齿轮c475会发生相对转动,从而通过螺纹驱动侧端齿轮c475沿着侧端动力轴c250轴向下移,最终使得侧端齿轮c475与与之啮合的侧端齿条c610分离,此时侧端齿轮c475与侧端动力轴c250旋合的螺纹达到端部,因此侧端齿轮c475下移至最大位移点且将过载弹簧c530压紧,过载弹簧c530存储弹力。一旦侧端动力轴c250反转时,侧端齿轮c475会上移复位,从而恢复至与侧端齿条c610啮合的状态,而恢复至初始状态后侧端动力轴c250与侧端齿轮c475旋合的螺纹达到端部,因此侧端齿轮c475上移至最大位移点。
两个侧端定位组件的侧端齿条c610分别与不同的侧端齿轮c475啮合传动,也就是侧端动力轴c250有两根。这种设计使得其中一根侧端齿条c610移动到位而另一根侧端齿条移动未到位时,以移动到位的侧端齿条c610啮合的侧端齿轮轴向下移,直到与此侧端齿条c610分离,而另一个侧端齿轮继续驱动另一侧端齿条移动,直到另一侧端齿条移动到位(与之对应的侧端行程开关被触发)即可完成对转向架100两端的定位、压紧。而通过侧端电机的转速、各个齿轮齿条的参数、两个侧端行程开关的触发时间即可推算转向架两端相对于第二定位架板b170的位置,从而实现误差补偿以提高定位精度。
优选地,为了避免侧端齿轮c475与侧端齿条c610分离后,侧端齿条c610发生移动导致后续侧端齿轮上移复位时与侧端齿条c610的卡齿侧面贴紧使其无法上移。而且由于需要侧端定位组件将转向架两端侧面压紧,如果不对侧端齿条c610进行固定,那么很可能造成侧端齿条发生移动造成较大的定位误差。对此申请人设计了齿条刹车架c710,所述齿条刹车架c710包括刹车底板c711、刹车板c712,所述刹车底板c711底部安装有刹车滑轴c650,刹车滑轴c650底部套装刹车弹簧c640后穿过刹车轴板c661且与刹车轴板c661可轴向滑动装配,所述刹车轴板c661安装在刹车立板c660上,刹车立板c660安装在过载底板c170上。所述刹车弹簧c640用于对刹车底板c711施加阻碍其下移的弹力,从而使得初始状态时,刹车板c712始终位于侧端齿条c610的上方,此时端部齿条处于可以滑动的状态。
所述刹车底板c711位于侧端动力轴c250穿过处安装有第二推力轴承c482,所述第二推力轴承c482的座圈安装在刹车底板c711上,所述第二推力轴承c482的轴圈套装在侧端动力轴c250外且与之可圆周转动、轴向滑动装配。在侧端齿条c610移动到位后(与之对应的侧端定位组件对转向架完成定位、压紧),侧端动力轴c250继续转动,从而驱动侧端齿轮c475下移,侧端齿轮c475下移的过程中会使得第一推力轴承c481与第二推力轴承c482压紧,从而带动齿条刹车架c710下移,直到刹车板c712与侧端齿条c610顶部压紧,此时侧端齿轮c475与侧端齿条c610分离,且侧端齿轮c475下移至最大位移点。而刹车板c712与侧端齿条c610压紧后能够防止侧端齿条c610滑动。同时随着侧端动力轴c250的转动,由于侧端齿轮c475与侧端动力轴c250旋合的螺纹达到端部,因此侧端齿轮c475与侧端动力轴c250之间不再发生移动。优选地,所述侧端动力轴c250底部与轴承c420的内圈装配固定,轴承c420的外圈安装在过载底板c170上。在侧端动力轴c250反转时,侧端齿轮c475上移,过载弹簧c530、刹车弹簧c640通过自生弹力驱动第一推力轴承c481、刹车架c710复位。
所述下压机构包括第三侧端横板c133,所述第三侧端横板c133安装在第四侧端横板c134与第二侧端立板c120之间,且第三侧端横板c133套装在下压导向轴c210、下压螺杆c220上,所述下压导向轴c210与第三侧端横板c133卡合、可轴向滑动装配,所述下压螺杆c220与第三侧端横板c133通过螺纹旋合装配,所述下压导向轴c210的上下两端分别与第四侧端横板c134、第二侧端横板c132装配,所述下压螺杆c220的上下两端分别与第四侧端横板c134、第一侧端横板c131可圆周转动且不可轴向移动装配;所述下压螺杆c220上套装有第一下压伞齿轮c431,所述第一下压伞齿轮c431与第二下压伞齿轮c432啮合传动,所述第二下压伞齿轮c432套装在下压动力轴c290上且与之通过螺纹旋合装配,所述下压动力轴c290两端分别与第一侧端立板c110、第二侧端立板c120可圆周转动且不可轴向移动装配,所述下压动力轴c290上还套装有第一下压带轮c461、第一下压轴环c291、下压推力轴承c440、下压弹簧c520、第二下压轴环c450,所述第一下压带轮c461、第一下压轴环c291套装固定在下压动力轴c290上,所述第二下压伞齿轮c432、下压推力轴承c440与下压动力轴c290可轴向滑动且不可相对圆周转动装配,所述第二下压轴环c450安装在第一侧端立板c110上;初始状态时,所述第二下压伞齿轮c432的两端分别与第一下压轴环c291、下压推力轴承c440的座圈压紧,所述下压弹簧c520的两端分别与第二下压轴环c450、下压推力轴承c440的轴圈贴紧或装配。
第三侧端横板c133与下压限位轴c230卡合、可轴向滑动装配,所述下压限位轴c230一端与下压板c150装配、另一端穿过第三侧端横板c133后与下压螺母c231装配,下压螺母c231不能穿过第三侧端横板c133,所述下压限位轴c230位于下压板c150与第三侧端横板c133之间的部分上套装有下压缓冲弹簧c512,所述下压缓冲弹簧c512用于对下压板c150施加阻碍其向第三侧端横板c133移动的弹力,所述第三侧端横板c133上安装有下压行程开关c310,所述下压行程开关c310的触发端正对下压板c150,下压板c150向第三侧端横板c133移动后能够触发下压行程开关c310,下压行程开关被触发后会向工控机输入信号,从而判断为下压到位(对转向架下压定位且压紧转向架)。
所述第一下压带轮c461通过下压皮带c460与第二下压带轮c462连接并构成带传动机构,所述第二下压带轮c462套装在下压传动管c281上,所述下压传动管c281与第二侧端立板c120可圆周转动且不可轴向移动装配,所述下压传动管c281内部中空且套装在下压传动轴c280上,所述下压传动轴c280与下压传动管c281可轴向滑动且不可圆周转动装配,所述下压传动轴c280穿过过载壳c160且与之可圆周转动、不可轴向移动装配,所述下压传动轴c280位于过载安装腔c164内的部分上套装有第一下压传动伞齿轮c471,所述第一下压传动伞齿轮c471与第二下压传动伞齿轮c472啮合传动,所述第二下压传动伞齿轮c472套装在侧端联动轴c260上。
使用时,下压机构随着侧端定位组件的移动而移动,同时随着侧端动力轴c250的转动,驱动下压传动轴c280转动,下压传动轴c280带动下压动力轴c290转动,下压动力轴c290带动下压螺杆圆周转动,从而带动第三侧端横板c133下移,直到下压板与转向架压紧。一旦转向架存在起翘的情况,会有一端的下压板先与转向架压紧到位,此时此端的下压动力轴c290继续转动,但是由于此端的第三侧端横板c133无法继续下移,因此就会使得第二下压伞齿轮c432不能转动,从而使得下压动力轴c290与第二下压伞齿轮c432发生相对移动以通过螺纹将第二下压伞齿轮c432向第二下压轴环c450移动,从而使得第一下压伞齿轮c431、第二下压伞齿轮c432分离,而第二下压伞齿轮c432会移动至第二下压轴环c450上的螺纹端部后就不再移动。另一侧的下压螺杆会继续转动,直到此侧的下压行程开关被触发。最终通过侧端电机c320旋转的圈数以及各个零部件的传动比,加上两个下压行程开关被触发的时间就能够推算转向架的起翘角度。从而进行进一步的误差补偿,提高定位精度以及压紧效果。
所述轮轴定位机构d包括定位活动板d110、定位固定板d120,所述定位固定板d120安装在定位座板d130上,所述定位固定板d120与轮轴限位轴d230卡合、可轴向滑动装配,所述轮轴限位轴d230一端套装轮轴侧边弹簧d410后与定位活动板d110装配,轮轴限位轴d230另一端穿出定位固定板d120后与轮轴螺母d231装配,轮轴螺母d231不能穿过定位固定板d120;所述定位固定板d120上还安装有轮轴行程开关d320,轮轴行程开关d320的触发端正对定位活动板d110,定位活动板d110向定位固定板d120移动后能够触发轮轴行程开关d320,轮轴行程开关d320被触发后会向工控机输入信号,工控机判断为定位活动板d110与钢轮120端面完成压紧定位。定位活动板d110、定位固定板d120上设置有能与轮轴110卡合装配的轮轴槽d101。
所述定位座板d130底部安装有定位座板块d131,所述定位座板块d131可轴向滑动地套装在轮轴导向轴d220上,轮轴导向轴d220两端分别与两块轮轴轴板d141装配,所述轮轴导向轴d220位于轮轴轴板d141和定位座板块d131之间的部分上套装有轮轴让位弹簧d420,所述轮轴让位弹簧d420用于对定位座板块d131施加阻碍其沿着轮轴导向轴d220移动的弹力。
所述轮轴轴板d141安装在轮轴升降板d140上,所述轮轴升降板d140底部分别与轮轴立轴d210、轮轴伸缩轴d311一端装配,所述轮轴立轴d210、轮轴伸缩轴d311另一端分别穿过第二定位架板b170且与之卡合、可轴向滑动装配,所述轮轴伸缩轴d311另一端装入推杆电机d310内,推杆电机d310启动后能够驱动轮轴伸缩轴d311轴向移动,从而带动轮轴升降板d140同步升降。
所述定位固定板d120内还设置有触发滑槽d121,所述触发滑槽d121与触发滑环d241卡合、可轴向滑动装配,所述触发滑环d241套装在触发滑轴d240上,所述触发滑轴d240一端进入轮轴槽d101内、另一端穿过轮轴限位环d122后与轮轴微动开关d330的触发端正对,所述轮轴限位环d122安装在触发滑槽d121内,且触发滑轴d240位于轮轴限位环d122和触发滑环d241之间的部分上套装有轮轴触发弹簧d430,所述轮轴触发弹簧d430用于对触发滑轴d240施加阻碍其向轮轴限位环d122移动的弹力。所述轮轴槽d101与轮轴110装配到位后能够驱动触发滑轴d240下移直到触发轮轴微动开关d330,轮轴微动开关d330被触发后会向工控机输送信号,工控机判断为轮轴与轮轴槽安装到位。
使用时,由于转向架的两端与第二定位架板b170之间存在偏移,因此两根轮轴与与之对应的轮轴定位机构d也会存在偏移,因此在轮轴定位时,推杆电机d310驱动轮轴伸缩轴d311上移,以带动轮轴升降板d140上移,上移过程中,轮轴110会逐渐装入轮轴槽d101内,但会存在偏移。此时,定位座板d130沿着轮轴导向轴d220移动以抵消偏移量,最终使得轮轴完全装入轮轴槽d101内。而轮轴装入轮轴槽内后会推动触发滑轴触发轮轴微动开关d330,从而使得工控机判断为轮轴定位到位。而在安装转向架时,使得一侧的钢轮120的内侧挤压定位活动板d110向定位固定板d120移动,直到轮轴行程开关被触发,此时工控机判断为钢轮内侧与轮轴定位机构定位到位。这种设计主要是能够实现对轮轴的灵活定位从而为后续的检修工序提供基础。
本发明未详述之处,均为本领域技术人员的公知技术。
以上详细描述了本发明的较佳具体实施例。应当理解,本领域的普通技术人员无需创造性劳动就可以根据本发明的构思作出诸多修改和变化。因此,凡本技术领域中技术人员依本发明的构思在现有技术的基础上通过逻辑分析、推理或者有限的实验可以得到的技术方案,皆应在由权利要求书所确定的保护范围内。
起点商标作为专业知识产权交易平台,可以帮助大家解决很多问题,如果大家想要了解更多知产交易信息请点击 【在线咨询】或添加微信 【19522093243】与客服一对一沟通,为大家解决相关问题。
此文章来源于网络,如有侵权,请联系删除


