解耦式电动助力制动装置的制作方法



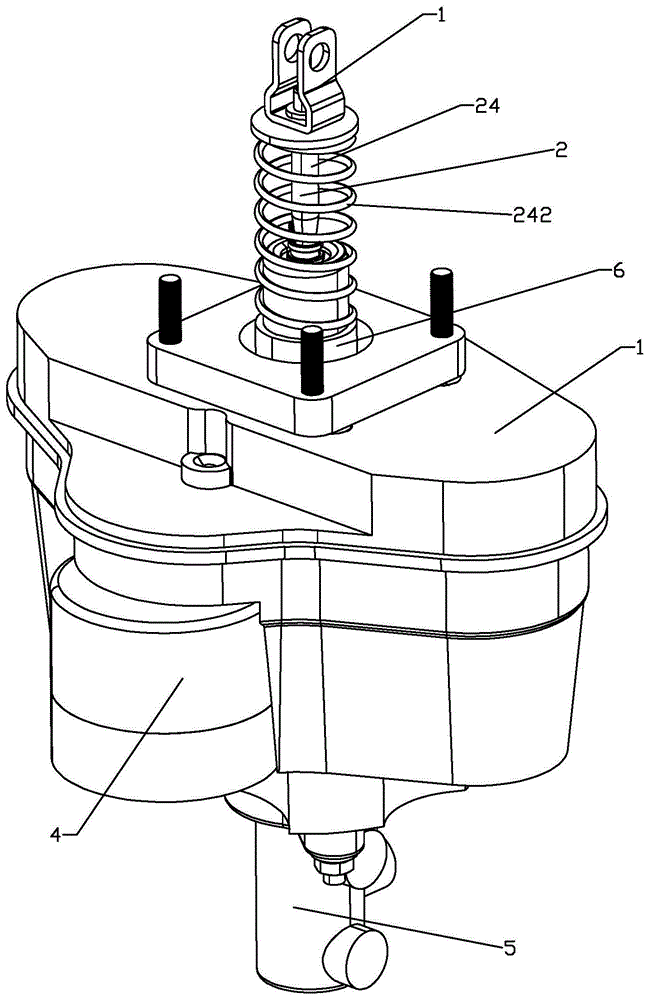
本实用新型涉及汽车制动领域,具体涉及一种解耦式电动助力制动装置。
背景技术:
传统内燃机汽车的制动系统大多采用真空助力装置来协助驾驶者产生足够的制动力,而真空源来自于发动机或机械真空泵。对于新能源汽车(燃料电池汽车和纯电动车)来说,没有发动机来提供真空动力源来提供制动助力,仅由人力所产生的制动力是无法满足行车制动的需求。电动助力制动装置可以很好的满足这种需求。
近几年,各大汽车及零部件厂商相继推出了相似的电动助力制动装置。现有的电动助力制动装置包括壳体及设置于壳体的踏杆总成、传感总成、电动助力器和制动泵总成,踏杆总成一端位于壳体外作为供驾驶者踩踏的踩踏端,另一端位于壳体内作为动作感应端,位于壳体内的传感总成通过感应动作感应端的踩踏深度控制电动助力器驱动制动泵总成的制动泵顶杆推入制动泵总成对应深度。
解耦的电动助力制动装置,一般直接采用缸体弹簧模拟踏板感,无制动压力对人体的反馈,进而影响踩踏力度的控制,踩踏力度过大或者过小均会影响驾驶体验。同时,现有的电动助力器能够提供的驱动力有限,无法使制动泵总成快速、稳定的进行制动,而且,壳体长度由于电动助力器与制动泵总成之间的传动结构长度过长,导致电动助力制动装置的结构过于臃肿,占据汽车内部过多空间。
技术实现要素:
针对现有技术存在的不足,本实用新型的目的在于提供一种模拟传统汽车脚踏刹车的踏感,提高驾驶制动时具有舒适踏板感的解耦式电动助力制动装置。
为实现上述目的,本实用新型提供了如下技术方案:包括壳体及设置于壳体内的解耦制动系统,所述的解耦制动系统包括踏杆总成、传感总成、电动助力器和制动泵总成,所述的踏杆总成一端位于壳体外作为与踏板联动的踩踏端,另一端位于壳体内作为轴向移动的动作感应端,位于壳体内的所述的传感总成通过感应动作感应端的踩踏深度控制电动助力器驱动制动泵总成的制动泵顶杆推入制动泵总成对应深度,构成踏杆总成与制动泵总成的解耦配合,其特征在于:还包括固定于壳体的第一缸体和第二缸体,所述的第一缸体内沿踩踏方向设置有第一活塞腔,所述的踏杆总成延伸至第一缸体内并设置有沿第一活塞腔移动的第一活塞,所述的第一活塞将第一活塞腔分隔为靠近踩踏端的第一腔及远离踩踏端的第二腔,所述的第二缸体位于第一缸体的侧面,所述的第二缸体沿平行于踩踏方向的方向设置有第二活塞腔,所述的第二活塞腔内设置有沿第二活塞腔移动的第二活塞,所述的第二活塞将第二活塞腔分隔为第三腔和第四腔,所述的第一缸体与第二缸体之间设置有联通第二腔和第三腔且截面积小于第一活塞腔的阻尼通道,所述的第二腔和第三腔内填充有液压油,所述的第二缸体设置有将第二活塞从第四腔向第三腔复位的复位件,所述的电动助力器与制动泵总成的制动泵顶杆之间设置有减速传动总成。
通过采用上述技术方案,①与踏板联动的踩踏端向制动主泵方向移动,在移动过程中,第一活塞逐渐将液压油从第二腔通过阻尼通道向第三腔输送,由于阻尼通道的截面积小于第一活塞腔,故在输送过程中会形成类似传统汽车脚踏刹车的阻尼回馈,且踩踏速率越快阻尼回馈越大,同时复位件在第二活塞受到液压推力时产生了柔和的反向推力,从而使所模拟的踏感十分逼真,辅助驾驶员控制踩踏力度,提高驾驶体验,在踩踏结束后,复位件将第二活塞从第四腔向第三腔复位,从而使液压油能够回流至第二腔,以准备进行下一次踏感模拟,此外,将第二缸体排布于第一缸体的侧面,在保证第一缸体具有足够的踩踏深度的同时有效缩短踏感模拟器的长度,并合理利用壳体内的剩余空间,使结构更为精简、紧凑;②减速传动总成有效降低电动助力器的速率并提高驱动力,使制动泵总成快速、稳定的进行制动;③踏杆总成与制动泵总成的解耦配合,为具有能量回收功能的应用而设置。
本实用新型进一步设置为:所述的复位件为位于第四腔的缸体弹簧,所述的缸体弹簧压缩于第二活塞与第二活塞腔的腔壁之间。
通过采用上述技术方案合理利用第四腔的空间用于安装作为复位件的缸体弹簧,使结构更为紧凑,并能够提供持续、稳定的踏板力和复位力。
本实用新型进一步设置为:所述的减速传动总成包括主齿轮、减速齿轮组、推顶座及驱动螺杆,所述的电动助力器驱动主齿轮旋转,所述的驱动螺杆的数量两个并与主齿轮呈v形排布,所述的驱动螺杆设置有同步转动的传动齿轮,所述的减速齿轮组的数量为两个并分别位于主齿轮与两个驱动螺杆之间,所述的减速齿轮组包括同步转动的第一减速齿轮及第二减速齿轮,所述的第一减速齿轮与主齿轮相啮合且直径大于主齿轮,所述第二减速齿轮与传动齿轮相啮合且直径小于传动齿轮,所述的推顶座分别设置有与各驱动螺杆螺纹配合的配合部分,并在驱动螺杆旋转时沿螺杆轴向制动泵顶杆移动构成与制动泵顶杆的推顶配合。
通过采用上述技术方案,由主齿轮、减速齿轮组、传动齿轮组成的减速齿轮系统,通过多次减速,大大增加从主齿轮处所输出的扭矩,并配合与驱动螺杆螺纹配合的推顶座,将旋转扭矩转化直线驱动力的同时并大幅增加直线驱动力的大小,并提供稳定的传动,从而保证制动泵总成快速、稳定的进行制动,其次,将主齿轮、减速齿轮组、驱动螺杆v形排布,合理利用壳体内相对与踩踏方向垂直的横向两侧,从而缩短壳体相对踩踏方向的长度,使结构更为紧凑。
本实用新型进一步设置为:所述的主齿轮、第一减速齿轮、第二减速齿轮及传动齿轮均为斜齿轮。
通过采用上述技术方案,传动总成的各齿轮均采用斜齿轮,相较传统齿轮,斜齿轮因传动平稳,冲击、振动和噪声较小等特点,故十分适合电动助力制动装置这种重载的应用场合,保证大驱动力的稳定输出。
本实用新型进一步设置为:所述的驱动螺杆套设有将推顶座向远离制动泵总成方向复位的制动复位弹簧。
通过采用上述技术方案,增设制动复位弹簧,在制动动作结束后及时将推顶座进行复位。
本实用新型进一步设置为:所述的传感总成包括感应块及直线位置传感器,所述的感应块安装于动作感应端,所述的直线位置传感器固定于壳体并通过感应块检测动作感应端踩踏深度及踩踏速率。
通过采用上述技术方案,传统的传感器通过检测与踏杆总成外周啮合的齿轮转速来推断动作感应端的相对移动距离,在踏杆总成使用一定时长后,其位置会产生偏移,进而使检测的相对移动距离与实际距离产生数据偏差,现调整为直线位置传感器,由直线位置传感器配合感应块检测踏杆总成绝对移动距离,从而避免受到因踏杆总成位置偏移所产生数据偏差。
本实用新型进一步设置为:所述的踏杆总成包括沿踩踏方向依次联动设置的踩踏联动杆和活塞顶杆,所述的踩踏端设置于踩踏联动杆,所述的动作感应端及第一活塞设置于活塞顶杆,所述的活塞顶杆穿过第二腔并延伸至第一缸体外,所述的活塞顶杆穿出第二腔的部分与第一缸体的缸壁之间呈活动密封配合。
通过采用上述技术方案,将踏杆分为两部分,便于与踏板适配的同时提高组装便捷性,使结构更为合理,活塞顶杆延伸至第一缸体外,从而使动作感应端位于第一缸体外,传感总成能够通过感应动作感应端的踩踏深度控制电动助力器驱动制动泵总成的制动泵顶杆推入制动泵总成对应深度,也可采用物理接触的方式将制动泵顶杆推入制动泵总成。
本实用新型进一步设置为:所述的踩踏联动杆位于与活塞顶杆的连接处设置有球头,所述的活塞顶杆设置容置球头并构成踩踏联动杆和活塞顶杆联动的联动槽。
通过采用上述技术方案,由球头与联动槽所构成多维度联动配合,使联动更为顺畅,提高实用性。
本实用新型进一步设置为:所述的踩踏联动杆与第一缸体之间设置有将踩踏端向踩踏相反方向复位的踏杆弹簧。
通过采用上述技术方案,增设踏杆弹簧,进一步提高踩踏过程中的舒适度,并在踩踏结束后及时将踩踏端进行复位。
附图说明
图1为本实用新型具体实施方式的立体图;
图2为本实用新型具体实施方式的横向剖视图;
图3为本实用新型具体实施方式的纵向剖视图;
图4为本实用新型具体实施方式中电动助力器、制动泵总成及减速传动总成的立体图;
图5为本实用新型具体实施方式中踏杆总成、第一缸体及第二缸体的剖视图。
具体实施方式
下面将结合附图对本实用新型的技术方案进行清楚、完整地描述,显然,所描述的实施例是本实用新型一部分实施例,而不是全部的实施例。基于本实用新型中的实施例,本领域普通技术人员在没有做出创造性劳动前提下所获得的所有其他实施例,都属于本实用新型保护的范围。
在本实用新型的描述中,需要说明的是,术语“中心”、“上”、“下”、“左”、“右”、“竖直”、“水平”、“内”、“外”等指示的方位或位置关系为基于附图所示的方位或位置关系,仅是为了便于描述本实用新型和简化描述,而不是指示或暗示所指的装置或元件必须具有特定的方位、以特定的方位构造和操作,因此不能理解为对本实用新型的限制。此外,术语“第一”、“第二”、“第三”仅用于描述目的,而不能理解为指示或暗示相对重要性。
如图1—图5所示,本实用新型公开了一种解耦式电动助力制动装置,包括壳体1及设置于壳体1内的解耦制动系统,解耦制动系统包括踏杆总成2、传感总成3、电动助力器4和制动泵总成5,踏杆总成2一端位于壳体1外作为与踏板联动的踩踏端21,另一端位于壳体1内作为轴向移动的动作感应端22,位于壳体1内的传感总成3通过感应动作感应端22的踩踏深度控制电动助力器4驱动制动泵总成5的制动泵顶杆51推入制动泵总成5对应深度,构成踏杆总成2与制动泵总成5的解耦配合,还包括固定于壳体1的第一缸体6和第二缸体7,第一缸体6内沿踩踏方向设置有第一活塞腔61,踏杆总成2延伸至第一缸体6内并设置有沿第一活塞腔61移动的第一活塞23,第一活塞23将第一活塞腔61分隔为靠近踩踏端21的第一腔611及远离踩踏端21的第二腔612,第二缸体7位于第一缸体6的侧面,第二缸体7沿平行于踩踏方向的方向设置有第二活塞腔71,第二活塞腔71内设置有沿第二活塞腔71移动的第二活塞72,第二活塞72将第二活塞腔71分隔为第三腔711和第四腔712,第一缸体6与第二缸体7之间设置有联通第二腔612和第三腔711且截面积小于第一活塞腔61的阻尼通道62,第二腔612和第三腔711内填充有液压油,第二缸体7设置有将第二活塞72从第四腔712向第三腔711复位的复位件,电动助力器4与制动泵总成5的制动泵顶杆之间设置有减速传动总成8,①与踏板联动的踩踏端21向制动主泵方向移动,在移动过程中,第一活塞23逐渐将液压油从第二腔612通过阻尼通道62向第三腔711输送,由于阻尼通道62的截面积小于第一活塞腔61,故在输送过程中会形成类似传统汽车脚踏刹车的阻尼回馈,且踩踏速率越快阻尼回馈越大,同时复位件在第二活塞72受到液压推力时产生了柔和的反向推力,从而使所模拟的踏感十分逼真,辅助驾驶员控制踩踏力度,提高驾驶体验,在踩踏结束后,复位件将第二活塞72从第四腔712向第三腔711复位,从而使液压油能够回流至第二腔612,以准备进行下一次踏感模拟,此外,将第二缸体7排布于第一缸体6的侧面,在保证第一缸体6具有足够的踩踏深度的同时有效缩短踏感模拟器的长度,并合理利用壳体1内的剩余空间,使结构更为精简、紧凑;②减速传动总成8有效降低电动助力器4的速率并提高驱动力,使制动泵总成5快速、稳定的进行制动;③踏杆总成2与制动泵总成5的解耦配合,为具有能量回收功能的应用而设置。此外,第一活塞63及第二活塞72外周均设置有与活塞腔内壁密封配合的密封环631。
复位件为位于第四腔712的缸体弹簧73,缸体弹簧73压缩于第二活塞72与第二活塞腔71的腔壁之间,合理利用第四腔712的空间用于安装作为复位件的缸体弹簧73,使结构更为紧凑,并能够提供持续、稳定的踏板力和复位力。
减速传动总成8包括主齿轮81、减速齿轮组82、推顶座83及驱动螺杆84,电动助力器4驱动主齿轮81旋转,驱动螺杆84的数量两个并与主齿轮81呈v形排布,驱动螺杆84设置有同步转动的传动齿轮85,减速齿轮组82的数量为两个并分别位于主齿轮81与两个驱动螺杆84之间,减速齿轮组82包括同步转动的第一减速齿轮821及第二减速齿轮822,第一减速齿轮821与主齿轮81相啮合且直径大于主齿轮81,第二减速齿轮822与传动齿轮85相啮合且直径小于传动齿轮85,推顶座83分别设置有与各驱动螺杆84螺纹配合的配合部分831,并在驱动螺杆84旋转时沿螺杆轴向制动泵顶杆移动构成与制动泵顶杆的推顶配合,由主齿轮81、减速齿轮组82、传动齿轮85组成的减速齿轮系统,通过多次减速,大大增加从主齿轮81处所输出的扭矩,并配合与驱动螺杆84螺纹配合的推顶座83,将旋转扭矩转化直线驱动力的同时并大幅增加直线驱动力的大小,并提供稳定的传动,从而保证制动泵总成5快速、稳定的进行制动,其次,将主齿轮81、减速齿轮组82、驱动螺杆84v形排布,合理利用壳体1内相对与踩踏方向垂直的横向两侧,从而缩短壳体1相对踩踏方向的长度,使结构更为紧凑。
主齿轮81、第一减速齿轮821、第二减速齿轮822及传动齿轮85均为斜齿轮,传动总成的各齿轮均采用斜齿轮,相较传统齿轮,斜齿轮因传动平稳,冲击、振动和噪声较小等特点,故十分适合电动助力制动装置这种重载的应用场合,保证大驱动力的稳定输出,电动助力器4则包括电机及在电机驱动下旋转并与主齿轮81啮合的齿轮轴41,主齿轮81、第一减速齿轮821、第二减速齿轮822及传动齿轮85均设置有与壳体1转动配合的转动轴,该转动轴与壳体的接触部分设置有保证转动稳定性的轴承,电动助力器4带旋转传感器,对电动助力器4的运转进行检测和监控,可以检测推顶座83的位移。
驱动螺杆84套设有将推顶座83向远离制动泵总成5方向复位的制动复位弹簧86,增设制动复位弹簧86,在制动动作结束后及时将推顶座83进行复位,在具体实施方式中,制动复位弹簧86压缩于推顶座83与轴承之间。
传感总成3包括感应块31及直线位置传感器32,感应块31安装于动作感应端22,直线位置传感器32固定于壳体1并通过感应块31检测动作感应端22踩踏深度及踩踏速率,传统的传感器通过检测与踏杆总成2外周啮合的齿轮转速来推断动作感应端22的相对移动距离,在踏杆总成2使用一定时长后,其位置会产生偏移,进而使检测的相对移动距离与实际距离产生数据偏差,现调整为直线位置传感器32,由直线位置传感器32配合感应块31检测踏杆总成2绝对移动距离,从而避免受到因踏杆总成2位置偏移所产生数据偏差,传感总成3还包括用于计算数据并根据数据控制电动助力器4的控制模块,该控制模块为多功能集成模块,已为现有的成熟技术,在此不再赘述,为了使结构更为紧凑且感应效果更好,第二缸体7的外侧壁作为直线位置传感器32的安装位置。
踏杆总成2包括沿踩踏方向依次联动设置的踩踏联动杆24和活塞顶杆25,踩踏端21设置于踩踏联动杆24,动作感应端22及第一活塞23设置于活塞顶杆25,活塞顶杆25穿过第二腔612并延伸至第一缸体6外,活塞顶杆25穿出第二腔612的部分与第一缸体6的缸壁之间呈活动密封配合,将踏杆分为两部分,便于与踏板适配的同时提高组装便捷性,使结构更为合理,活塞顶杆25延伸至第一缸体6外,从而使动作感应端22位于第一缸体6外,传感总成3能够通过感应动作感应端22的踩踏深度控制电动助力器4驱动制动泵总成的制动泵顶杆推入制动泵总成对应深度,也可采用物理接触的方式将制动泵顶杆推入制动泵总成。
活塞顶杆25可穿过推顶座83的中间通孔832,与制动泵总成5保持一定的距离,该距离可定义为解耦间隙。在电动式助力制动装置未通电状态下,活塞顶杆25顶住推顶座83,消除解耦间隙,产生一定的制动力,该举措可帮助在机电制动助力器的失效模式下,人力辅助的安全举措,产生一部分的制动力和减速度。
踩踏联动杆24位于与活塞顶杆25的连接处设置有球头241,活塞顶杆25设置容置球头241并构成踩踏联动杆24和活塞顶杆25联动的联动槽251,由球头241与联动槽251所构成多维度联动配合,使联动更为顺畅,提高实用性。
第一缸体6或第二缸体7设置有与第二腔612联通的加油装置63,增设加油装置63,在具体实施方式中设置于第一缸体6,用于将液压油注入缸体内,提高实用性。
第一缸体6或第二缸体7设置有与第二腔612联通的放气装置64,增设放气装置64,在具体实施方式中设置于第二缸体7,用于将液压油内的气体排出,提高实用性。
上述加油装置63和放气装置64均采用现有装置结构,未对其进行详述。
踩踏联动杆24与第一缸体6之间设置有将踩踏端21向踩踏相反方向复位的踏杆弹簧242,增设踏杆弹簧242,进一步提高踩踏过程中的舒适度,并在踩踏结束后及时将踩踏端21进行复位。
起点商标作为专业知识产权交易平台,可以帮助大家解决很多问题,如果大家想要了解更多知产交易信息请点击 【在线咨询】或添加微信 【19522093243】与客服一对一沟通,为大家解决相关问题。
此文章来源于网络,如有侵权,请联系删除


