用于车辆天窗的驱动装置的制作方法



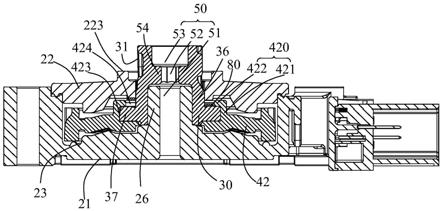
[0001]
本发明涉及驱动技术领域,具体涉及一种用于车辆天窗的驱动装置。
背景技术:
[0002]
目前,车辆天窗的开合主要通过驱动装置进行调整。驱动装置一般包括电机以及通过传动机构与电机的输出轴连接的输出齿轮,车辆天窗上一般固定连接有与所述齿轮配合的用于将转动运动转化为平移运动的机构。当电机转动时,传动机构在电机的驱动下使得齿轮转动,进而驱动天窗滑动,以打开或者关闭天窗开口。然而,当车辆遇到紧急情况而突然断电的情况下,电机无法正常工作,天窗无法被打开,车辆内的人员不能通过天窗进行紧急逃生,存在极大的安全隐患。
技术实现要素:
[0003]
有鉴于此,本发明旨在提供一种可以解决上述问题的用于车辆天窗的驱动装置。
[0004]
为此,本发明一方面提供一种用于车辆天窗的驱动装置,包括电机、与所述电机连接的传动机构、以及在所述传动机构的驱动下转动的输出轴,所述输出轴在其输出端的周缘上一体形成有若干齿,所述若干齿用于驱动所述天窗往复移动,所述输出轴内设有沿轴向贯穿所述输出轴的通孔,所述通孔包括依次连通的第一凹孔、中间孔和第二凹孔,其中第一凹孔邻近所述输出轴的输入端,所述中间孔为非圆形孔,所述第二凹孔邻近所述输出轴的输出端,所述第二凹孔与所述中间孔的形状和/或尺寸不同、和/或被构造在不同的部件上,且至少第一凹孔和第二凹孔的其中之一的横向尺寸不小于中间孔的最小横向尺寸。
[0005]
在一些实施例中,所述中间孔邻近所述输出轴的输入端设置或者邻近所述输出轴的输出端设置。
[0006]
在一些实施例中,所述第二凹孔的横向尺寸大于或者小于所述中间孔的横向尺寸。
[0007]
在一些实施例中,所述中间孔为选自以下组中的一个:
[0008]
1)所述中间孔一体形成于所述输出轴内;
[0009]
2)所述驱动装置还包括驱动件,所述驱动件防转动地收容于所述输出轴内,所述中间孔一体形成于所述驱动件内。
[0010]
在一些实施例中,所述驱动装置还包括驱动件,所述输出轴内形成有用于收容所述驱动件的中间收容孔,所述驱动件的外周壁和所述中间收容孔的孔壁的至少其中之一呈非圆状,所述中间孔一体形成于所述驱动件内。
[0011]
在一些实施例中,所述输出轴内还形成有用于与所述驱动件抵顶的限位面,所述限位面为选自以下组中的一个:
[0012]
1)所述限位面形成于所述中间收容孔与所述第一凹孔的交界处;
[0013]
2)所述限位面形成于所述中间收容孔与所述第二凹孔的交界处;
[0014]
3)所述输出轴内一体形成有过渡孔,所述过渡孔位于所述中间收容孔与所述第一
凹孔、或者所述中间收容孔与所述第二凹孔之间,所述限位面形成于所述过渡孔与所述中间收容孔的交界处。
[0015]
在一些实施例中,所述驱动装置还包括壳体,所述壳体包括支撑件,所述输出轴与所述支撑件可转动地连接,所述支撑件为选自以下组中的一个:
[0016]
1)所述支撑件为支撑轴,所述输出轴内一体形成有用于收容所述支撑轴的端部收容孔,所述第一凹孔一体形成于所述支撑轴内并沿轴向贯穿所述支撑轴。
[0017]
2)所述支撑件为套筒,所述套筒包括沿轴向延伸的贯穿孔,所述输出轴收容于所述贯穿孔内,所述第一凹孔和所述第二凹孔均一体形成于所述输出轴内。
[0018]
在一些实施例中,所述支撑件的与所述输出轴相对的表面和/或所述输出轴的与所述支撑件相对的表面内凹形成有用于容纳溶剂的溶剂槽。
[0019]
在一些实施例中,所述传动机构包括与所述电机的电机轴连接的蜗杆、以及与所述蜗杆啮合的蜗轮,所述蜗轮与所述输出轴之间设有连接结构,所述连接结构为选自以下组中的一个:
[0020]
1)所述连接结构包括在轴向上卡接配合的凸起和卡槽,所述输出轴的位于输入端的轴向端面和所述蜗轮的一轴向端面的其中之一形成所述凸起,其中之另一形成所述卡槽;
[0021]
2)所述连接结构包括在周向上卡接配合的凸块和凹槽,所述输出轴的外周壁和所述蜗轮的一内周壁的其中之一形成所述凸块,其中之另一形成所述凹槽。
[0022]
在一些实施例中,所述驱动装置还包括壳体和波形垫圈,所述传动机构包括与所述输出轴连接的蜗轮,所述壳体内形成一第一收容腔,用于收容所述蜗轮,所述波形垫圈布置于所述壳体的一轴向端面与所述蜗轮和/或所述输出轴的轴向端面之间,所述波形垫圈为选自以下组中的一个:
[0023]
1)所述波形垫圈包括若干沿周向交替连接的峰部和谷部,所述峰部和谷部均呈曲面状;
[0024]
2)所述波形垫圈包括若干沿周向交替连接的凹部和凸部,若干凹部的端面位于同一水平面,若干凸部的端面位于同一水平面
[0025]
在一些实施例中,所述输出轴采用粉末冶金制成。
[0026]
在一些实施例中,所述输出轴在其高度的大致1/2~1/4的位置处沿径向向内突出形成一环形凸起,所述中间孔形成于所述环形凸起内。在一些实施例中,所述输出轴在其高度的沿轴向自上而下的方向上的大致1/2~1/4的位置处沿径向向内突出形成一环形凸起。在另一些实施例中,所述输出轴在其高度的沿轴向自下而上的方向上的大致1/2~1/4的位置处沿径向向内突出形成一环形凸起。
[0027]
在一些实施例中,驱动装置还包括壳体,所述输出轴的环形凸起的轴向底端与所述壳体的轴向顶端大致处于同一水平面。
[0028]
在一些实施例中,所述输出轴的纵向截面大致呈h形。
[0029]
本发明通过提供一种一体形成齿的输出轴,可有效减少装配工序,且传动过程也更稳定。此外,由于本发明的中间孔为非圆形孔,因此当车辆遇到紧急情况例如落水的时候,车内人员可将与中间孔配合的应急工具插入中间孔内,然后手动转动应急棒,进而通过中间孔转动输出轴,从而手动打开天窗,实现逃生。
附图说明
[0030]
图1是本发明第一实施例的用于车辆天窗的驱动装置的立体图。
[0031]
图2是图1所示驱动装置的分解图。
[0032]
图3是图1所示驱动装置的剖视图。
[0033]
图4是图2所示驱动装置的输出轴的立体图。
[0034]
图5是本发明第二实施例的用于车辆天窗的驱动装置的剖视图。
[0035]
图6是本发明第三实施例的用于车辆天窗的驱动装置的立体图。
[0036]
图7是图6所示驱动装置的分解图。
[0037]
图8是图6所示驱动装置的剖视图。
[0038]
图9是图6所示驱动装置的输出轴的立体图。
[0039]
图10是本发明第四实施例的用于车辆天窗的驱动装置的立体图。
[0040]
图11是图10所示驱动装置的分解图。
[0041]
图12是图10所示驱动装置的剖视图。
[0042]
图13是图10所示驱动装置的输出轴的立体图。
[0043]
图14是本发明第五实施例的用于车辆天窗的驱动装置的立体图。
[0044]
图15是图14所示驱动装置的另一角度的立体图。
[0045]
图16是图15所示驱动装置的分解图。
[0046]
图17是图15所示驱动装置的剖视图。
[0047]
图18是图16所示驱动装置的输出轴的立体图。
[0048]
图19是图18所示输出轴的另一角度的立体图。
具体实施方式
[0049]
以下将结合附图以及具体实施方式对本发明进行详细说明,以使得本发明的技术方案及其有益效果更为清晰明了。可以理解,附图仅提供参考与说明用,并非用来对本发明加以限制,附图中显示的尺寸仅仅是为了便于清晰描述,而并不限定比例关系。
[0050]
参考图1至图4,本发明第一实施例的用于车辆天窗的驱动装置100包括电机10、与所述电机10连接的传动机构、用于收容所述传动机构的壳体20、以及与所述传动机构连接的输出轴30。当电机10工作时,所述传动机构驱动所述输出轴30转动。本发明的输出轴30在其输出端的周缘上一体形成有若干齿31,用于驱动天窗往复移动,从而打开或者关闭天窗。通过在输出轴30上一体形成齿31,可减少装配工序,且传动过程也更稳定。
[0051]
本实施例中,所述传动机构包括与所述电机10的转轴11连接的蜗杆41、以及与所述蜗杆41啮合的蜗轮42,所述输出轴30与所述蜗轮42抗扭地连接。可以理解地,在其他实施例中,传动机构也可以由其他传动部件构成,其只要能实现将电机10的转矩传递至所述输出轴30,优选兼具减速的功能即可。
[0052]
本实施例中,所述壳体20包括可拆卸连接的基座21和盖板22,基座21和盖板22之间形成一第一收容腔23,用于收容所述蜗轮42。本实施例中,所述基座21还包括一用于收容所述蜗杆41的第二收容腔24,所述第二收容腔24的轴线与所述第一收容腔23的轴线垂直。所述第二收容腔24在一侧设有开口25,用于连通所述第二收容腔24和所述第一收容腔23,从而使得蜗杆41和蜗轮42啮合成为可能。
[0053]
本发明的输出轴30内设有沿轴向贯穿所述输出轴30的通孔50。所述通孔50包括依次连通的第一凹孔51、中间孔52和第二凹孔53,其中第一凹孔51邻近所述输出轴30的输入端并自驱动装置100的轴向下端沿轴向向上凹入,第二凹孔53邻近所述输出轴30的输出端并自驱动装置100的轴向上端沿轴向向下凹入。所述第二凹孔53与所述中间孔52的形状和/或尺寸不同、和/或被构造在不同的部件上。本实施例中,所述第一凹孔51和所述第二凹孔53均为圆形孔。所述中间孔52为非圆形孔。在其他实施例中,第一凹孔和/或第二凹孔也可以为非圆形孔,例如方形孔等。至少第一凹孔51和第二凹孔53的其中之一的横向尺寸不小于中间孔52的最小横向尺寸,使得可与中间孔52配合的轴可以经由中间孔52的至少一端插入中间孔52内。当车辆遇到紧急情况例如落水的时候,车内人员可将与中间孔52配合的应急工具,例如棱柱状的轴插入所述中间孔52内,然后手动转动应急棒,进而通过所述中间孔52转动所述输出轴30,从而手动打开天窗,实现逃生。为了方便描述中间孔52与其他孔的尺寸关系,本实施例中,将中间孔52的最小横向尺寸定义为中间孔52的孔径,将第一凹孔51和第二凹孔53的横向尺寸定义为第一凹孔51和第二凹孔53的孔径,因此,本文所述的孔径并非作为圆形孔的尺寸限制而也可以指非圆形孔的尺寸。
[0054]
第一凹孔51或者第二凹孔53的孔径优选大于中间孔52的孔径,从而在输出轴30内形成台阶,如此,在制造输出轴30的过程中,更有利于输出轴30与模具的分离,脱模更容易。优选地,所述输出轴30采用粉末冶金的方式一体制成。更优地,所述第一凹孔51和第二凹孔53的孔径均大于中间孔52的孔径,从而允许应急工具可以从中间孔52的两端插入中间孔52内,操作者选择更自由,操作更加快捷、方便。
[0055]
本实施例中,所述中间孔52和所述第二凹孔53一体形成于所述输出轴30内,其中第二凹孔53自输出轴30的轴向顶端沿轴向向下凹入。具体地,所述输出轴30在大致中部位置(具体地,在其高度的沿轴向的方向上的大致1/2~1/4的位置处)沿径向向内突出形成一环形凸起54。所述中间孔52形成于所述环形凸起54内,所述第二凹孔53邻近所述环形凸起54的轴向顶端。换言之,本实施例中的输出轴30内一体形成有两个孔径不同的孔,且应急工具经由其中孔径较大的孔(即第二凹孔53)插入至孔径较小的孔(即中间孔52)以驱动输出轴30。如前所述,由于第二凹孔53的孔径大于所述中间孔52的孔径,因此,更有利于输出轴30的脱模。本实施例中,中间孔52的孔壁轮廓呈正六边形,第二凹孔53呈圆形。可以理解地,在其他实施例中,中间孔52的孔壁轮廓也可以呈其他非圆形形状,例如三角形、四边形、八边形、椭圆形或d形等。第二凹孔53的孔壁轮廓也可以呈其他形状,例如多边形等。具体到本实施方式中,所述输出轴在其高度的沿轴向自上而下的方向上的大致1/2~1/4的位置处沿径向向内突出形成一环形凸起。当然地,可以理解地,在其他实施方式中,所述输出轴在其高度的沿轴也可以向自下而上的方向上的大致1/2~1/4的位置处沿径向向内突出形成一环形凸起。本实施例中,所述输出轴30在其输入端还一体形成有端部收容孔36。所述端部收容孔36自输出轴30的轴向底端沿轴向向上凹入,且其孔壁轮廓优选呈圆形。本实施例中,所述端部收容孔36与所述中间孔52直接连通,即,所述端部收容孔36邻近所述环形凸起54的轴向底端。此外,所述端部收容孔36的孔径大于所述中间孔52的孔径,结合前述的第二凹孔53的孔径大于所述中间孔52的孔径,因此,所述输出轴30的纵向截面大致呈h形。换言之,本实施例中,所述输出轴30内总共一体形成有沿轴向贯穿其自身的三个孔:即沿轴向由下而上的依次连通的端部收容孔36、中间孔52以及第二凹孔53,且三个孔的中心轴线重合。
[0056]
本发明所述的轴向底端定义为邻近所述输出轴30的输入端的端面,轴向顶端定义为邻近所述输出轴30的输出端的端面。
[0057]
本实施例中,所述基座21在所述第一收容腔23的中央形成有一支撑件。具体地,所述支撑件为一支撑轴26。所述支撑轴26的外径略小于所述端部收容孔36的孔径并大于所述中间孔52的孔径,使得所述输出轴30可套设在所述支撑轴26上,并可相对支撑轴26转动。本实施例中,输出轴30的轴向底端抵顶在基座21上,轴向顶端贯穿盖板22,且其输出端的齿31位于盖板22之外,以便于传动。本实施例中,所述第一凹孔51一体形成于所述基座21内,并自所述基座21的轴向底端沿轴向向上凹入至贯穿所述支撑轴26。优选地,所述第一凹孔51也呈圆形,其轴向各区段的孔径一致。所述第一凹孔51直接邻近所述中间孔52的轴向下端,且其中心轴线与所述中间孔52以及所述第二凹孔53的中心轴线重合。优选地,所述第一凹孔51的孔径大于所述中间孔52的孔径,因此操作人员还可从输出轴30的输入端插入应急工具至中间孔52内,以转动输出轴30。还优选地,所述中间孔52邻近所述输出轴30的输出端布置,即所述第一凹孔51的深度大于所述第二凹孔53的深度,如此,可以增大支撑轴26与输出轴30之间的接触面积,提高输出轴30的转动稳定性。
[0058]
还可以在支撑轴26的与输出轴30相对的外表面,例如支撑轴26的外周壁上开设内凹的溶剂槽(图中未示出),用于容纳溶剂。溶剂可以为例如润滑油,以减少输出轴30与支撑轴26之间的转动摩擦,降低或者消除噪音。可替代地或者附加地,在其他实施例中,也可以在输出轴30的与支撑轴26相对的内表面上,例如端部收容孔36的周向孔壁上开设内凹的溶剂槽,用于容纳溶剂,以达到同样的或者更佳的润滑效果。溶剂槽的形状、数量以及排布可以根据具体需要进行变化而不受限制。例如,溶剂槽可以是一个沿周向分布的弧形槽,也可以是沿轴向和/或沿周向、等距地和/或不等距地间隔布置的多个凹形槽。
[0059]
本实施例中,所述蜗轮42与所述输出轴30之间设有连接结构,用于使输出轴30随蜗轮42同步转动。具体地,所述连接结构包括形成于所述蜗轮42的轴向顶端的凸起71,以及形成于所述输出轴30的轴向底端的卡槽72。通过凸起71和卡槽72的在轴向上的卡接配合,使得当蜗轮42转动时,输出轴30也跟着转动。所述凸起71优选呈长方体状,相应地,所述卡槽72的槽壁也优选呈长方体状,如此,不论蜗轮42正转还是反转,蜗轮42均可稳定地驱动输出轴30同步转动。为进一步提高蜗轮42和输出轴30的传动稳定性,优选在蜗轮42的轴向顶端形成多个沿周向间隔、且均匀分布的所述凸起71,相应地,所述输出轴30的轴向底端也形成多个沿周向间隔、且均匀分布的所述卡槽72。可以理解地,在其他实施例中,所述凸起71也可以形成于所述输出轴30的轴向顶端,所述卡槽72也可以形成于所述蜗轮42的轴向底端。
[0060]
本实施例中,所述输出轴30在其输入端沿径向向外延伸形成有一环形凸缘37,所述若干卡槽72形成于所述环形凸缘37的轴向端面。优选地,所述蜗轮42还形成有一卡环420。所述卡环420包括自所述输出轴30的轴向顶端沿轴向向上延伸而成的连接环421,以及自所述连接环421的顶端沿径向向内延伸而成的内环缘422。所述卡环420与所述输出轴30的轴向顶端形成一环形腔423,用于收容所述输出轴30的环形凸缘37。具体地,所述蜗轮42可以采用塑胶材质,并可以通过包覆成型的方式形成前述的包覆环形凸缘37的蜗轮42形状。通过将输出轴30的环形凸缘37布置于蜗轮42的环形腔423内,不仅能进一步提高二者的连接强度,进而提高二者的传动稳定性,而且还可以定位蜗轮42,使得蜗轮42的轴向两端与
壳体20之间保持一定间隙成为可能,进而减少蜗轮42的转动阻力,同时降低整个驱动装置100的振动和噪音。
[0061]
优选地,所述蜗轮42的内环缘422与所述输出轴30之间形成一环形槽424,所述环形槽424内布置一波形垫圈80。波形垫圈80位于所述环形凸缘37的轴向顶端和所述盖板22的轴向底端之间。本实施例中,所述波形垫圈80包括若干沿轴向突出的峰部81和沿轴向凹陷的谷部82,所述峰部81和谷部82沿周向交替布置,所述峰部81和谷部82均呈曲面状。通过波形垫圈80可以减缓输出轴30与壳体20之间的振动和冲击。此外,本实施例的盖板22的顶端还形成有一环形围墙223,所述输出轴30位于所述环形围墙223的中央并与所述环形围墙223间隔布置。
[0062]
装配时,可先将蜗杆41固定至电机的转轴11然后装入基座21的第二收容腔24内,并将一体连接有蜗轮42的输出轴30套入基座21的支撑轴26内,同时使得蜗轮42和蜗杆41啮合,然后装入波形垫圈80,再将盖板22套设在输出轴30外周并与基座21固定连接。本实施例中,由于前述的端部收容孔36、中间孔52以及第二凹孔53的高度关系,装配好后的输出轴30的环形凸起54的轴向底端与所述盖板22的轴向顶端大致处于同一水平面。
[0063]
图5示出了本发明第二实施例的驱动装置200的剖视图。所述第二实施例与第一实施例似,其中间孔152一体地形成于输出轴130内,相同的部分在此不再赘述。所述第二实施例与第一实施例的主要区别在于输出轴130内的三个孔的尺寸关系不同。具体地,
[0064]
不同于第一实施例中的第二凹孔53的孔径大于中间孔52的孔径,本实施例中的第二凹孔153的孔径小于所述中间孔152的孔径。不过,由于第一凹孔151的孔径仍大于所述中间孔152的孔径,操作人员仍可经由输出轴130的输入端插入应急工具至中间孔152,从而转动输出轴130。此外,本实施例中,输出轴130内的端部收容孔136的深度大于中间孔152的深度,中间孔152的深度大于第二凹孔153的深度。换言之,本实施例中,输出轴130的纵向截面呈二级台阶状。
[0065]
图6至图9示出了本发明第三实施例的驱动装置300。所述第三实施例与第一实施例相似,其中间孔252一体地形成于输出轴230内,相同的部分在此不再赘述。所述第三实施例与第一实施例的主要区别在于输出轴230内的三个孔的尺寸关系有所改变。具体地,本实施例中的中间孔252与第二凹孔253之间的高度差变大,且所述中间孔252更靠近所述第二凹孔253,因此可增大应急工具与中间孔252的接触面积,提高传动稳定性。此外,从图8可以毫无疑问地确定,本实施例中的输出轴230的纵向截面也大致呈h形。与第一实施例相比,本实施例的齿231的轴向高度与输出轴230的轴向高度的比值更大。此外,本实施例中的蜗轮242上的凸起271呈锥状,输出轴230上的卡槽272的槽壁也呈锥状。
[0066]
图10至图13示出本发明第四实施例的驱动装置500。本实施例与第一实施例的相同之处在此不再赘述,不同之处主要在于本实施例中的中间孔452不再由输出轴430一体形成,而是由一装配至输出轴430内的驱动件460形成。
[0067]
具体地,本实施例中的驱动装置500还包括一驱动件460。所述输出轴430内形成有用于收容所述驱动件460的中间收容孔432,所述驱动件460防转动地收容于所述中间收容孔432内。所述中间孔452一体形成于所述驱动件460内。本实施例中,所述中间孔452的孔壁轮廓呈正六边形。由于驱动件460防转动地收容于输出轴430内,因此当将应急工具插入驱动件460的中间孔452内后,也同样可以驱动输出轴430转动。
[0068]
本实施例中,所述驱动件460大体呈长方体状,换言之,驱动件460的外周壁轮廓呈四边形。为提高驱动件460与输出轴430之间的传动稳定性,优选所述中间收容孔432的孔壁轮廓与驱动件460的外周壁轮廓一样,即中间收容孔432的孔壁轮廓也呈四边形。可以理解地,在其他实施例中,驱动件460的外周壁和中间收容孔432的孔壁也可以呈其他形状,例如中间收容孔432的孔壁轮廓也可以呈圆形,而对应的驱动件460的外周壁轮廓也可以呈三角形、五边形、八边形等非圆形形状,而同样可以通过驱动件460转动输出轴430。甚至还可以使得驱动件460的外周壁轮廓和中间收容孔432的孔壁轮廓均呈圆形并紧配,也是可行的。
[0069]
本实施例中,所述第二凹孔453一体形成于所述输出轴430内,且第二凹孔453的孔径大于所述中间孔452的孔径,因此,操作人员可从输出轴430的输出端插入应急工具至中间孔452内,以转动输出轴430。优选地,所述第二凹孔453的孔径小于所述中间收容孔432的最大孔径,从而在中间收容孔432与第二凹孔453的交界处形成一限位面433。具体地,所述输出轴430在其轴向顶端沿径向向内延伸形成一凸环434,所述第二凹孔453形成于所述凸环434内。所述输出轴430还自第一凹孔51的位于轴向顶端侧的孔壁沿径向向内延伸形成四个凸台435,四个凸台435围合形成所述中间收容孔432。本实施例中,所述中间收容孔432的对角线的长度大于第二凹孔453的孔径,中间收容孔432的相对的两孔壁之间的距离等于所述第二凹孔453的孔径。换言之,所述限位面433形成于所述中间收容孔432的四个角对应的凸环434的部分轴向底端。因此,当装配驱动件460至输出轴430内时,可将驱动件460从输出轴430的输入端装配至中间收容孔432内,直至所述驱动件460与所述限位面433抵顶,即完成驱动件460的装配,装配方便、准确。
[0070]
图14至图19示出了本发明第五实施例的驱动装置400。所述第五实施例的驱动装置400与第四实施例的驱动装置500的主要区别在于以下几点:
[0071]
首先,两实施例的中间孔的位置不同。具体地,本实施例中的中间孔352位于邻近所述输出轴330的输入端的位置。这样也可以理解为,所述第一凹孔351的高度小于所述第二凹孔353的高度。优选地,本实施例的所述第一凹孔351的孔径大于用于收容所述驱动件60的中间收容孔332的孔径,如此可形成台阶方便脱模。可以理解地,由于第一凹孔351的孔径大于中间收容孔332的孔径,因此所述第一凹孔351的孔径也大于所述驱动件60内的中间孔352的孔径,因此,操作者可经由输出轴330的输入端插入应急工具至中间孔352内,从而转动输出轴330。还优选地,所述第二凹孔353的孔径也大于所述中间孔352的孔径,因此操作者还可以经由输出轴330的输出端插入应急工具至中间孔352内,以转动输出轴330。
[0072]
其次,两实施例的限位面的形成方式不同。本实施例中,所述输出轴330自第二凹孔353的内壁沿径向向内延伸形成有环形凸台334,环形凸台334内形成一过渡孔335,即所述过渡孔335位于所述中间收容孔332与所述第二凹孔353之间。本实施中,所述第二凹孔353的孔径大于所述过渡孔335的孔径。限位面333形成于所述过渡孔335与所述中间收容孔332的交界处。具体地,本实施例中的所述过渡孔335为一圆孔。所述中间收容孔332的孔壁轮廓,优选如第四实施例所描述的那样,呈四边形。所述中间收容孔332的对角线的长度大于过渡孔335的孔径,中间收容孔332的相对的两孔壁之间的距离等于过渡孔335的孔径,换言之,本实施例中的限位面333形成于中间收容孔332的四个角对应的环形凸台334的部分轴向底端。
[0073]
可以理解地,在其他实施例中,过渡孔335也可以形成于中间收容孔332与第一凹
孔351之间。还可以理解地,在其他实施例中,输出轴330也可以不形成所述过渡孔335,而使得第一凹孔351和第二凹孔353的其中之一的孔径小于中间收容孔332的孔径,其中之另一的孔径大于中间收容孔332的孔径,从而在保证操作者可以从输出轴330的其中一端插入应急工具的同时,还形成限位面333,方便驱动件60的装配。
[0074]
再者,两实施例的第一凹孔和第二凹孔的形成方式不同。本实施例中的第一凹孔351和第二凹孔353均一体形成于所述输出轴330内。换言之,本实施例不再采用第四实施例中的插入输出轴30内的支撑轴26作为支撑件,而是采用一套设在输出轴330外周的套筒326。所述套筒326包括沿轴向延伸的贯穿孔327,所述输出轴330收容于所述贯穿孔327内,并可相对套筒326转动。具体地,所述基座321的中央一体形成所述套筒326。所述输出轴330的轴向顶端贯穿所述贯穿孔327,且其输出端的齿331突出于所述套筒326,以进行传动。优选地,所述套筒326突出于基座321的轴向顶端,从而增大套筒326与输出轴330之间的接触面积,提高输出轴330的转动稳定性。还优选地,所述盖板322上也对应所述贯穿孔327形成另一贯穿孔328,所述输出轴330的轴向底端收容于所述另一贯穿孔328内,以进一步提高输出轴330的转动稳定性。与第四实施例中的溶剂槽的布置方式不同,本实施例中的用于容纳溶剂的溶剂槽可被布置在输出轴330的外周壁和/或套筒326的内周壁上。
[0075]
此外,两实施例的输出轴与蜗轮之间的连接结构不同。本实施例中的连接结构包括形成于所述输出轴330的外周壁上的凸块371,以及形成于蜗轮342的内周壁的凹槽372。通过凸块371和凹槽372的在周向上的卡接配合,使得当蜗轮342转动时,输出轴330也跟着转动。本实施例中,所述凸块371呈立方体状,所述凹槽372的槽壁呈u形。如此,不论蜗轮342正转还是反转,均可稳定地驱动输出轴330同步转动。为进一步提高蜗轮342和输出轴330的传动稳定性,优选在蜗轮342的外周壁上形成多个沿周向间隔、均匀分布的所述凸块371,相应地,所述蜗轮342的内周壁上也形成多个沿周向间隔、均匀分布的所述凹槽372。可以理解地,在其他实施例中,所述凹槽372也可以形成于所述输出轴330的外周壁,所述凸块371也可以形成于所述蜗轮342的内周壁。
[0076]
最后,两实施例的波形垫圈380的结构不相同。本实施例中,所述波形垫圈380包括若干沿周向交替连接的凹部381和凸部382,若干凹部381的端面均呈平面状并位于同一水平面,若干凸部382的端面均呈平面状并位于同一水平面。本实施例中,所述凹部381的轴向底端与所述盖板322的轴向顶端抵顶,所述凸部382的轴向顶端与所述蜗轮342的轴向底端抵顶,以缓冲蜗轮342与壳体320之间的振动和冲击。优选地,所述输出轴330的凸块371的轴向底端与所述蜗轮342的轴向底端齐平,所述波形垫圈380的凸部382的轴向顶端还与所述凸块371的轴向底端抵顶,以同时缓冲蜗轮342、输出轴330与壳体320之间的振动和冲击。还优选地,所述凸块371的高度小于所述凹槽372的高度,因此,仅需要使所述蜗轮342的轴向顶端与所述基座321的轴向底端抵顶,而输出轴330可以不与基座321进行抵顶,从而减少对输出轴330的磨损。
[0077]
以上所述仅为本发明较佳的具体实施方式,本发明的保护范围不限于以上列举的实施例,任何熟悉本技术领域的技术人员在本发明披露的技术范围内,可显而易见地得到的技术方案的简单变化或等效替换均落入本发明的保护范围内。
起点商标作为专业知识产权交易平台,可以帮助大家解决很多问题,如果大家想要了解更多知产交易信息请点击 【在线咨询】或添加微信 【19522093243】与客服一对一沟通,为大家解决相关问题。
此文章来源于网络,如有侵权,请联系删除
相关标签: 孔径分布



tips